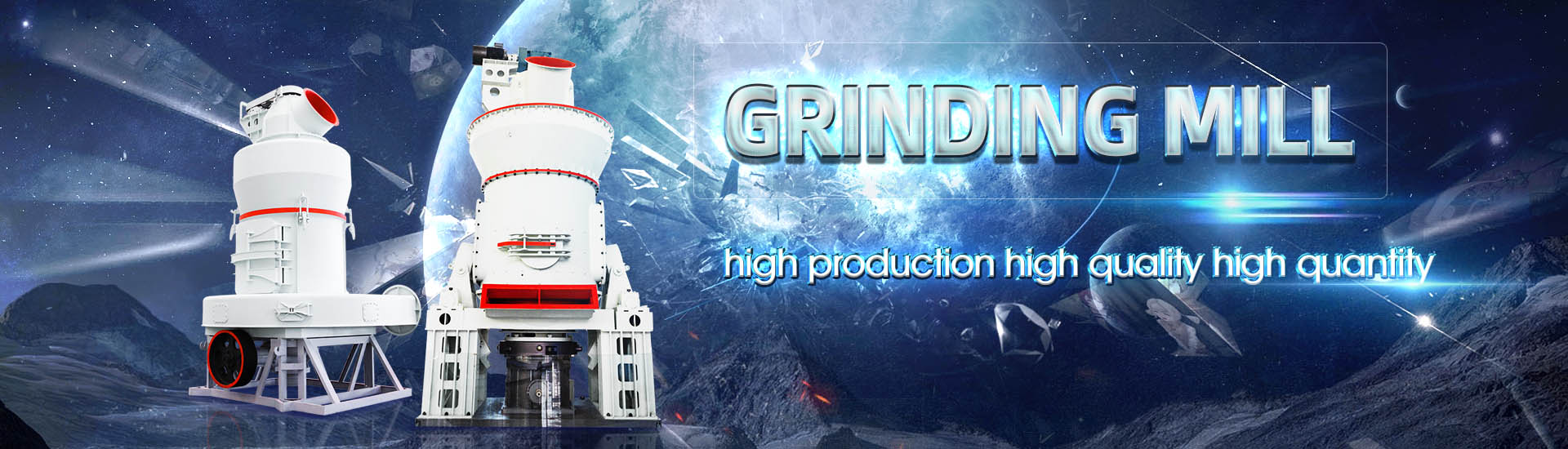
roasted spodumene grinding mill mad ore grinding mill
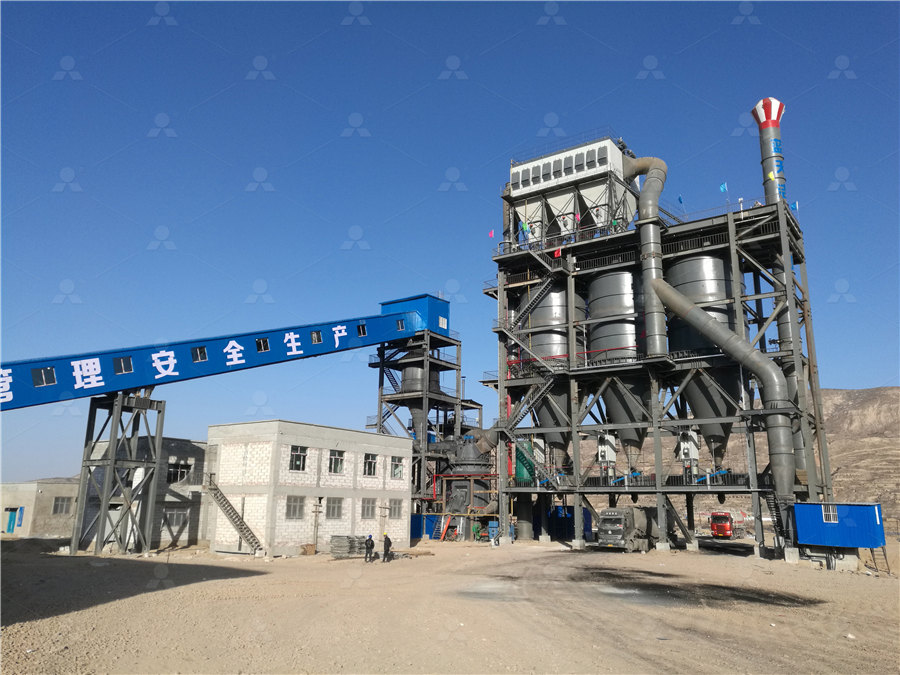
Aspects of Spodumene Lithium Extraction Techniques MDPI
2024年9月30日 The calcination decrepitation reaction of spodumene with limestone (roasting process) involves three distinct steps : (i) decomposition of limestone at temperatures ranging 2023年11月7日 Crushing and Grinding Equipment: Spodumene ore is typically crushed and ground to reduce its size and prepare it for further processing Crushing equipment includes Spodumene Processing And Production Equipment2024年7月9日 Lithium ore grinding mills are the devices used to grind lithium ore into fine powder SBM's lithium ore grinding machines are mainly divided into four categories: Lithium Ore Grinding Mills SBM Ultrafine Powder TechnologyLithium ore vertical mill process flow: The roasted spodumene (βspodumene) is cooled by grate cooler, crushed, and then sent to the raw material warehouse by the conveying equipment, Spodumene grinding for lithium extraction choose lithium ore
.jpg)
Mechanochemical Extraction of Lithium from αSpodumene at
2024年2月3日 Lithium extraction was performed through a mechanochemical reaction between αspodumene and various solid leaching agents (with 50% excess of stoichiometry) in a steel 2022年10月31日 This work investigates the energy efficiency of different grinding circuits used for upgrading the lithium content in the finer fraction of the calcined spodumene oreLithium deportment by size of a calcined spodumene ore2023年12月27日 To produce battery chemical inputs, spodumene is mined, ground and acidroasted The resulting solution undergoes concentrating, refining, and converting (CRC) into Hard Rock Spodumene Lithium Processing Saltworks Technologies2018年8月19日 The grinding mill, DMS flotation cells, tailings and concentrate thickeners, and filter are larger than in the DMS + Flotation since the whole ore is treated by flotation The Flowsheet Development for Benefication of Lithium Minerals from
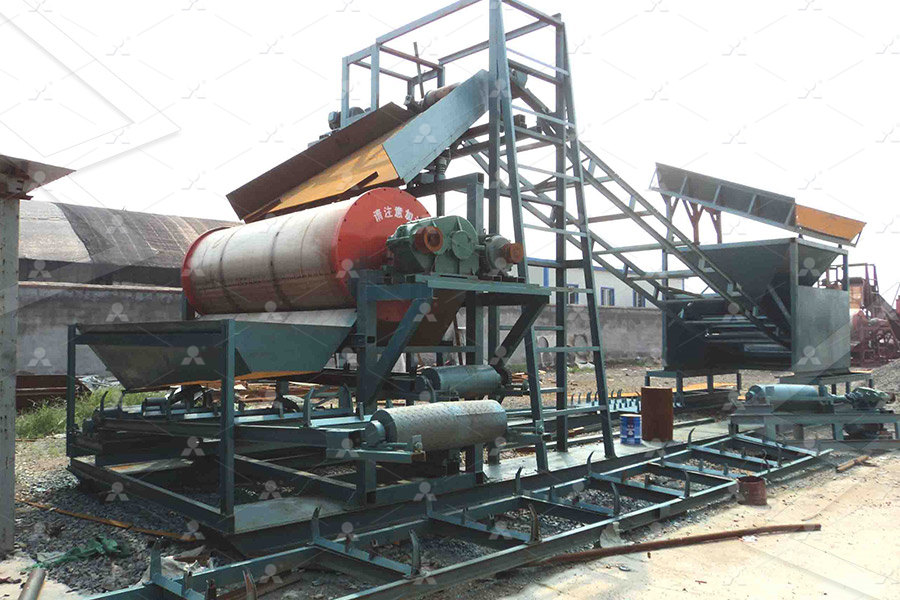
Literature Review and Thermodynamic Modelling of Roasting
Spodumene is naturally present in the stable αmonoclinic (highly packed crystal structure) form with high grindability and hence the mineral is difficult to leach without pretreatment It is made spodumene concentrates after roasting and acid roasting operations A concentrate with at least 6% Li2O (approximately 75% spodumene) is suitable for roasting Roasting is performed at Hard Rock Lithium Processing SGSGrinding Mills: Ball Mill Rod Mill Design PartsCommon types of grinding mills include Ball Mills and Rod Mills This includes all rotating mills with heavy grinding media loads This article focuses on ball and rod mills excluding SAG and AG Grinding Mills 911Metallurgist2023年7月20日 Therefore, the rod mill is mostly used for coarse grinding of the previous period of ball mill, or grinding of brittle materials and materials against overcrushing, such as tungsten and tin ore before gravity separation; and (3) autogenous mill – it refers to the materials which themselves are collided and ground mutually to be crushed when the grinding mill rotates, and Ore Grinding SpringerLink
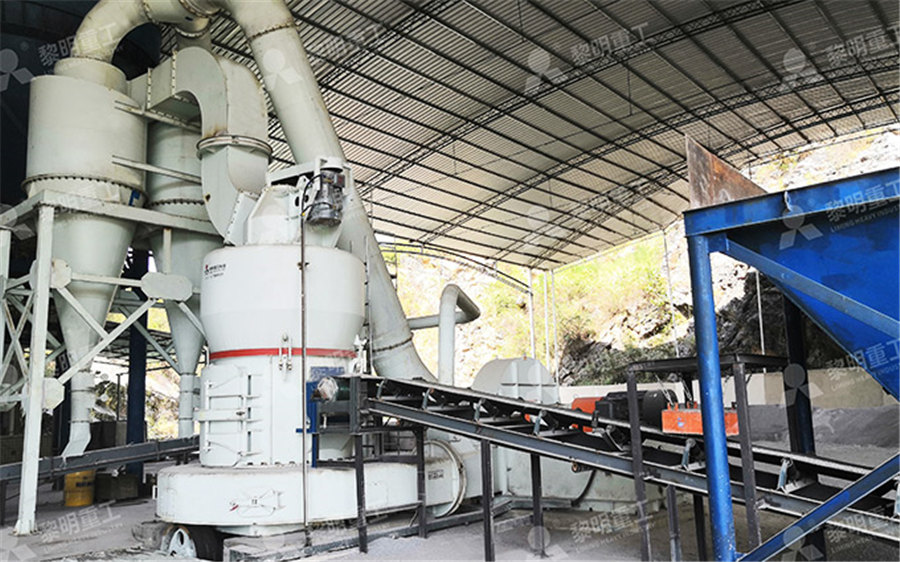
(PDF) Estimation of Grinding Time for Desired Particle Size
The present work was used to find the total grinding retention time of each ore in the mill Based on the total retention time of each ore, the optimum grinding time for each ore was identified to obtain the desired P80 passing particle size with acceptable hematite liberation2024年3月21日 The Significance of Grinding in Lithium Ore Processing: Grinding stands as an indispensable process in lithium ore processing, playing a pivotal role in liberating lithiumbearing minerals from the surrounding gangue materialBy reducing the ore particles to a finely ground state, grinding sets the stage for subsequent beneficiation processes, including flotation, Lithium Ore Grinding MillsThe working principle of ball mill for grinding spodumene lepidolite Ball mill is the key equipment for grinding spodumene lepidolite after crushing process It is widely used in cement, silicate products, new building materials, refractory materials, chemical fertilizer, black and nonferrous metal oredressing, as well as glass ceramics ball mill for grinding spodumene lepidolite production procesA crushing plant delivered ore to a wet grinding mill for further size reduction The size of crushed ore (F 80) was 40 mm and the SG 28 t/m 3 The work index of the ore was determined as 122 kWh/t A wet ball mill 1 m × 1 m was chosen to grind the ore down to 200 micronsGrinding Mill an overview ScienceDirect Topics
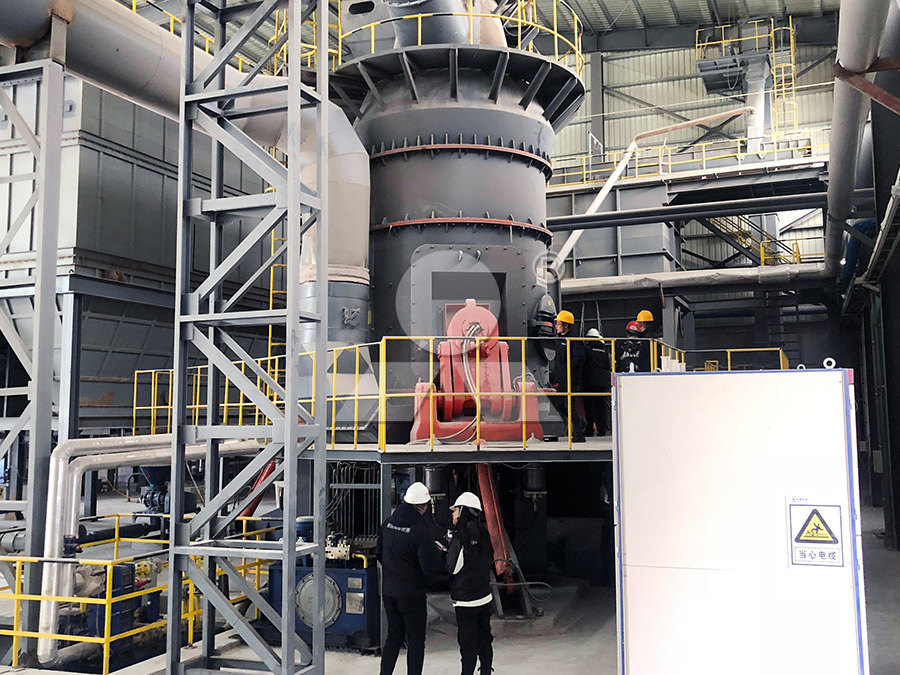
Green Battery Minerals How to Get Lithium from Spodumene
2023年4月7日 After the screening, qualified spodumene minerals are fed into the grinding and grading process The particle size of spodumene ore is ground to less than 015 mm to obtain a better flotation effect Spodumene grinding equipment you need Wettype ball mill: The ore Introduction The LM Vertical Grinding Mill , launched by SMMVIK Machinery, integrates five functions of crushing, grinding, powder selection, drying and material conveyingIt is characterized by centralized technological process, small occupational area, low investment, high efficiency, energy conservation and environment protectionLM Vertical Grinding Mill SMMVIK MachineryThe Autogenous Mill, also known as AG Mill, is a type of grinding mill used in the mining industry This machine uses ore and rock itself as grinding media to perform its job Unlike other types of mills that use steel balls or rods for grinding materials, the Autogenous Mill relies on the material being ground to break itself into smaller piecesUnderstanding the SAG Mill in Copper Ore Mining Process2012年6月1日 As the cylinder starts to rotate, the grinding balls inside the cylinder crush and grind the feed material, generating mechanical energy that aids in breaking bonds, activating the catalyst, and Grinding in Ball Mills: Modeling and Process Control
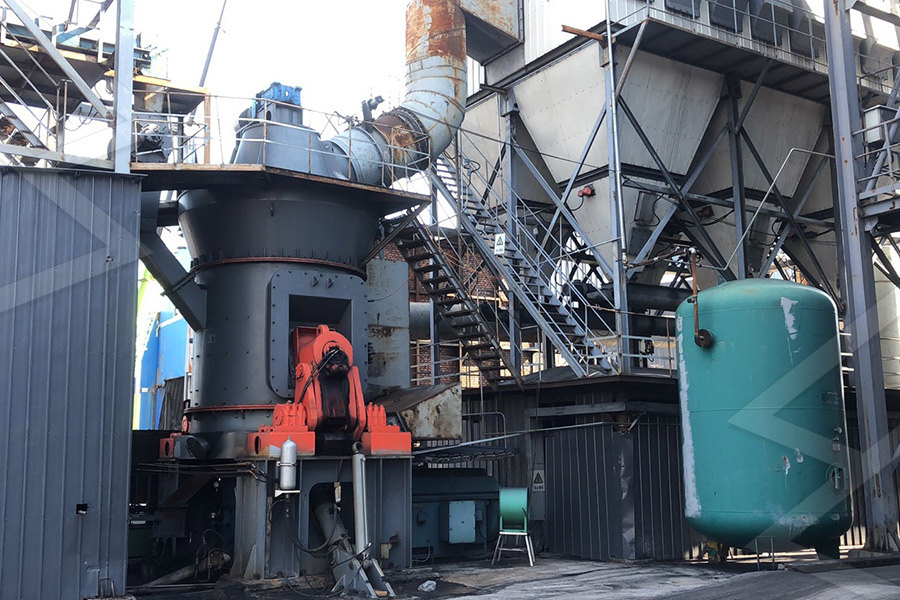
Closed Circuit Grinding VS Open Circuit Grinding
2016年10月12日 Stockpiling of ore ahead of the mill can aid in smoothing out some of the fluctuations although it must be stored in such a manner that no segregation occurs In operating a grinding circuit, like any other unit process, 2021年1月14日 Comparison of Ore Hardness Measurements for Grinding Mill Design for the Tenke Project John Starkey1, Principal Consulting Engineer David Meadows2, Manager Mineral Processing Development 1 Starkey Associates 344115 George St Oakville, ON L6J 0A2 PH: (416) 7357512Comparison of Ore Hardness Measurements for Grinding Mill from the ores The grinding of ore is a highly energyintensive process [1–4] In this process, the size of the particle obtained depends on the energy consumption of the ball mill The major challenge encountered in the process of iron ore grinding is to maintain the desired product particle size distribution (PSD) with sufficientEstimation of Grinding Time for Desired Particle Size DistributionSpodumene has a theoretical Li2O content of 803% Due to its high lithium content, spodumene is considered the most important lithium ore mineral A typical run of mine ore can contain 12% Li 2 O, while a typical spodumene concentrate suitable for lithium carbonate production contains 67% Li 2 O (75% 87% spodumene) Higher grade concentratesHard Rock Lithium Processing SGS
.jpg)
Population balance model approach to ball mill optimization in iron ore
3 BALL MILL MODEL The population balance model may be expressed by Equation (1): > @ ¦ i1 1 i b ij m j j i j i S Ht dt d H m t (1) where: S i (t) is the size discretized selection function for 2020年1月3日 Iron ores obtained from different sources differ in their chemical and physical properties These variations make the process of grinding a difficult task The work carried out in this context focuses on three different samples of iron ore, viz, high silica high alumina, low silica high alumina, and low silica low alumina The grinding process for all the three iron ores is Estimation of Grinding Time for Desired Particle Size Distribution 2016年11月7日 In Fig 13 is shown a large ball mill, designed for the dry grinding of limestone, dolomite, quartz, refractory and similar materials; this type of mill being made in a series of sizes having diameters ranging from about 26 in to 108 in, with the corresponding lengths of drum ranging from about 15 in to 55 inGrinding Mills Common Types 911Metallurgist2023年3月1日 Traditional finegrinding mills in mineral processing rely on the use of steel medium for particle size reduction The IsaMill (a horizontal stirred mill with a 3,000L net chamber volume and a Study on the unequalprobability comminution of spodumene
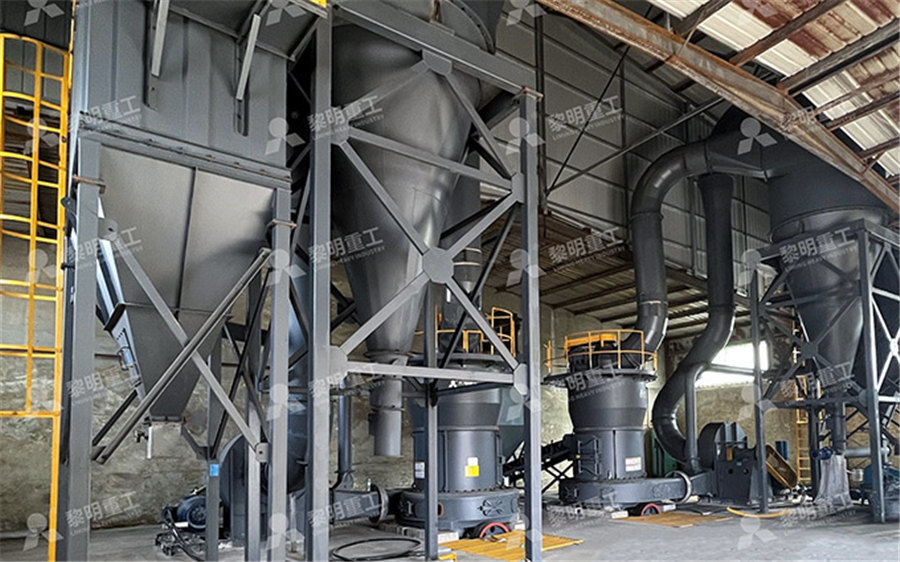
FLOOR MOUNTED LABORATORY GRINDING MILL
Our Laboratory Grinding Mill comes standard with a 1 HP motor and optional variable speed drive ranging from 1 to 100 RPM Chilean mills were used at the Golden Cycle up to a few years ago for grinding roasted ore Cyanidation and concentration of gold and silver ores Related Products 05 TO 15 TPH SMALL SCALE MINER’S BALL MILL Grinding mill is an industrial grinding mill used to grind solid stones into fine powder Stable hardness 1), gypsum (MOH's hardness 2) to hard potash feldspar (MOH's hardness 6), quartzite (MOH's hardness 7), our mill is the ideal choice for ore processing, which can process hundreds of ore materials Dolomite Marble Calcite Potash Grinding MillIndustrial Grinding Mill, Ultrafine Grinding Mill 2017年5月8日 A lifter mill of 6 ft diameter, revolving at 187 rpm, is grinding coal The body of the mill is divided into two sections: one section, 75 ft long, being charged with 5 tons of steel balls, of 2 in average diameter, and the Grinding Mill Power 911MetallurgistGrinding Mills Barry A Wills, James A Finch FRSC, FCIM, PEng, in Wills' Mineral Processing Technology (Eighth Edition), 2016 71 Introduction Grinding is the last stage in the comminution process where particles are reduced in size by a combination of impact and abrasion, either dry, or more commonly, in suspension in waterGrinding Mill an overview ScienceDirect Topics
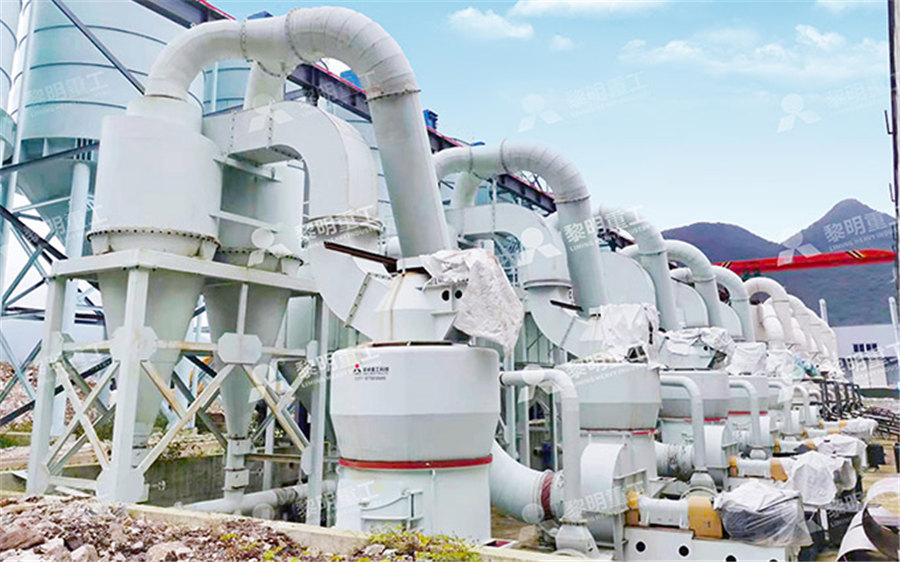
Understanding the operation of grinding mills in the mining and
1 Grindability: The grindability of the ore affects the efficiency of the grinding mill Harder ores require more energy and longer grinding times, which can impact the mill's performance and operational costs 2 Media andliner Wear: The condition of the grinding media and liners affects the mill's efficiency2020年5月28日 The feed samples of X, Y, and Z iron ores were ground in the BBM (ball mill refers to a BBM of size 300 mm × 300 mm with smooth liners) to identify the PSD, BWI, and RT of each ore Grinding experiments were conducted according to Bond’s standard test procedure []For each iron ore sample, the RT taken to produce 250% circulating load in the BBM was Investigation on Iron Ore Grinding based on Particle Size Distribution 2024年11月21日 The grinding and grading stage of lithium ore is to ensure that lithium minerals are fully dissociated from gangue mineral monomers Therefore, lithium ore extraction is inseparable from ore grinding, and the common equipment for lithium ore grinding is ball mill Onestage closedcircuit grinding and grading process can be adopted, and the onestage Ball Mill Is Indispensable For Lithium Ore Processing2016年6月6日 One of the most important was the severe stressing which took place at the connection of the mill shell and the trunnion bearing end plates, which is further aggravated by the considerable distortion of the shell and the bearing journals due to the dynamic load effect of the rotating mill with a heavy mass of ore and pulp being lifted and dropped as the grinding SAG Mill Grinding Circuit Design 911Metallurgist
.jpg)
A Review of the Grinding Media in Ball Mills for Mineral
2023年10月27日 The ball mill is a rotating cylindrical vessel with grinding media inside, which is responsible for breaking the ore particles Grinding media play an important role in the comminution of mineral ores in these mills This work reviews the application of balls in mineral processing as a function of the materials used to manufacture them and the mass loss, as 2022年5月23日 Grinding experiments were conducted in a laboratoryscale stirred mill on a lowgrade PGE bearing chromite ore HighPressure Grinding Rolls (HPGR) product of −1 mm was used as feed material to Modeling and application of stirred mill for the coarse grinding 2023年10月27日 The ball mill is a rotating cylindrical vessel with grinding media inside, which is responsible for breaking the ore particles Grinding media play an important role in the comminution of mineral A Review of the Grinding Media in Ball Mills for Mineral ProcessingWith the development of new energy industry, the demand for lithium salt is increasing Spodumene is the main lithium source, and lithium extraction process from spodumene is the key technology in lithium salt production industry The chemical property of natural spodumene is stable, and the chemical index control of direct lithium extraction is more stable than that of News Which Spodumene Ginding Mill Is Selected For Spodumene
.jpg)
Grinding equipment for spodumene and spodumene
The ore is then crushed into small pieces and fed into the mill through a feed chute The crusher then breaks down the rocks into small pieces which are then ground by the hammer mill How can grinding mills be used in the mining process? Mills for grinding spodumene and Lepidolite are used extensively in the mining process2020年10月18日 An iron ore concentrate sample was ground separately in a pilotscale HPGR mill in multiple passes and a dry opencircuit ball mill to increase the specific surface area of particlesThe effects of iron ore concentrate grinding methods (HPGR and 2017年1月17日 Other process activities, such as spraying the ore with water for dust control or the fact that runofmine ore moisture is approximately 2%5% are not generally considered (Bleiwas, 2012a)Breaking down energy consumption in industrial 2022年11月1日 Mild steel and ceramic laboratory ball mills were used to grind 600 g sulfide ore charges The mild steel ball mill generated approximately 46 g of iron fines (08% of the ore charge mass) when The effects of dry grinding and chemical conditioning during grinding
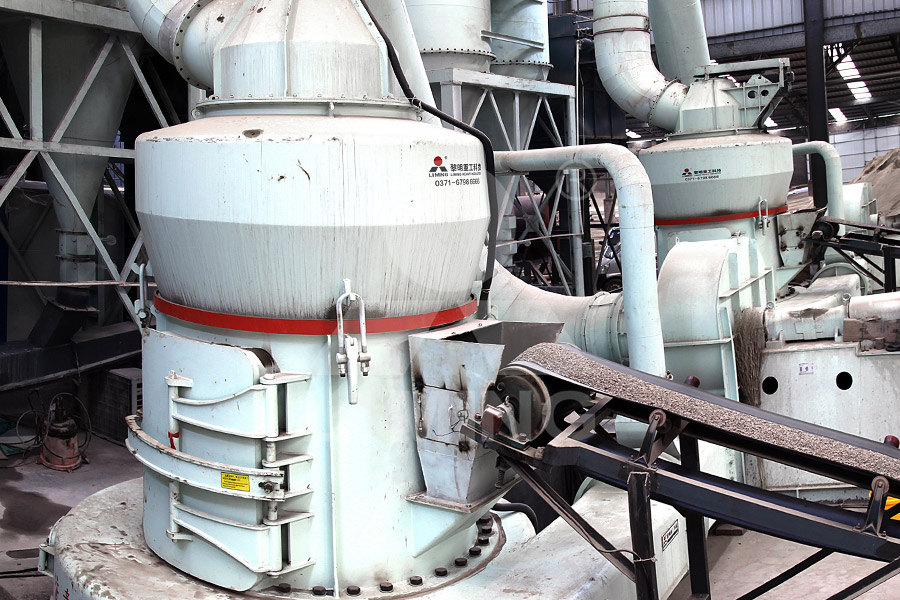
Consumption of steel grinding media in mills – A review
2013年8月1日 In the case of sulphide ores, such results could be explained by the galvanic interactions taking place between the ore and the grinding media during wet grinding (Yuan et al, 1996, Deshpande and 2017年7月20日 Where in conventional rod and ball mill plants there are usually 3 to 4 stages of crushing followed by 1 to 3 stages of grinding, depending on ore fineness and hardness, primary autogenous plants require only one stage of crushing followed by 1 to 2 stages of grindingAutogenous Grinding Semi Autogenous Grinding Circuits2016年5月10日 In the handling of wet, sticky ores such as encountered in tropical areas having distinct dry and rainy seasons, the crushing plant is a section of the mill which must be planned very carefully Unless this is done, crushing becomes a constant source of trouble resulting in lost production and high milling cost In some areas rainfall is high for prolonged periodsCrushing and Grinding Wet Sticky Ore 911Metallurgist2018年8月17日 Extreme temperatures, impact velocity, mill load, grinding media, ore types, and applications are some of the factors to be considered while installing new linersGrinding Mills — Types, Working Principle Applications
.jpg)
Zimbabwe 2 Million TPA Spodumene Ore Beneficiation Process
2023年7月14日 02 Spodumene ore grinding and classifying process To improve the working efficiency of grinding equipment, crushed products should be sent into the screening machine for screening before into ball mill machine The products under the screen can enter the ball mill for grinding processRefractory Gold Ores S Ellis Kalgoorlie Consolidated Gold Mines Kalgoorlie, WA Abstract Since early 2001, Kalgoorlie Consolidated Gold Mines (KCGM) has successfully operated an ultra fine grinding (UFG) circuit to supplement its roaster capacity for the treatment of the refractory gold flotation concentrate A second UFG mill was installed inUltra Fine Grinding A Practical Alternative to Oxidative