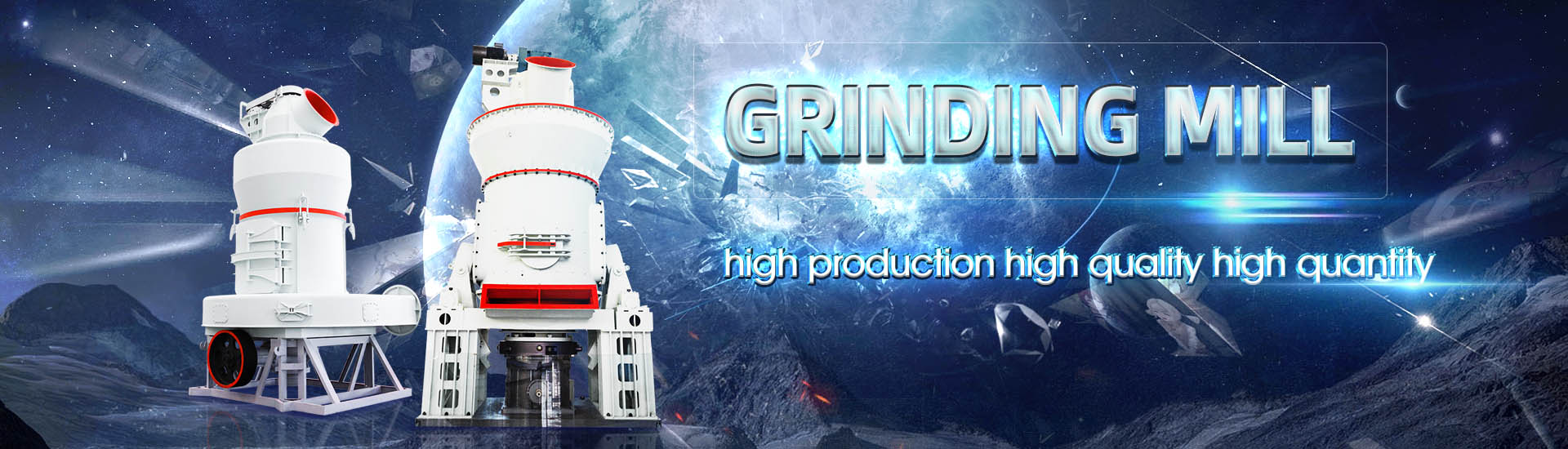
Sandstone ore grinding mill employee work summary
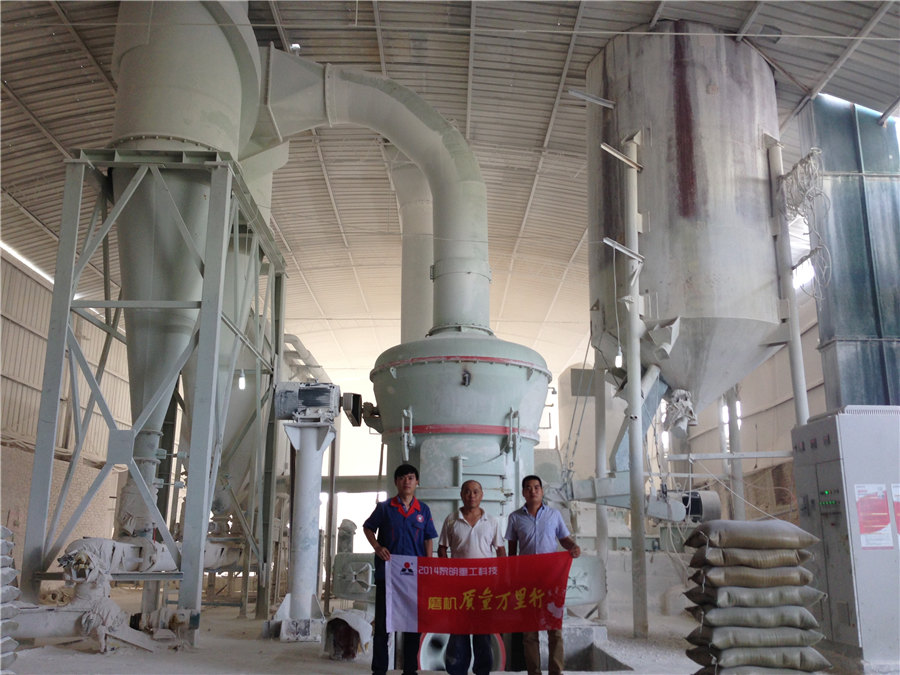
Ore Grinding SpringerLink
2023年7月20日 Ore grinding is a process to further reduce and disperse the ore particle size In the mineral processing industry, ore grinding is the particle size preparation before the separation of the crushed ore2024年9月6日 The sandstone crushing process offers several advantages: High Automation : The process is highly automated, reducing the need for manual intervention and minimizing The Crushing Process and Equipment for SandstoneNowadays, conducting grindability tests requiring only a few kilos of material on several samples, is a more typical approach to grinding mill design This paper summarises the requirements SAG Mill Testing Test Procedures to Characterize Ore Grindability2019年11月15日 The article presents a comparison of the use of a ball mill and an electromagnetic mill for the grinding sandstones, taking into account the obtained grain Sandstone grinding in electromagnetic mill – case study
.jpg)
Understanding the operation of grinding mills in the mining and
Grinding mills operate on the principle of breaking down ore particles into smaller sizes through the action of abrasion The primary types of grinding mills include ball mills, rod mills, 2017年10月3日 SemiAutogenous Mills/ SAG Mills (primary grinding mill) – these mills use grinding balls with forces of attrition, impact, and abrasion between grinding balls and ore Grinding Mill Types, Working Principle Applications2019年4月16日 The paper demonstrates why the Loesche VerticalRollerMill (VRM) is a serious alternative to conventional grinding technologies and where the limitations of the system are (PDF) LEARNING FROM OTHER INDUSTRIES; WHY THE VRM2024年5月17日 A SAG (SemiAutogenous Grinding) mill is a giant rotating cylinder filled with grinding media and the ore being reduced As the mill rotates, the grinding media lifts and the A guide to SAG Mill management
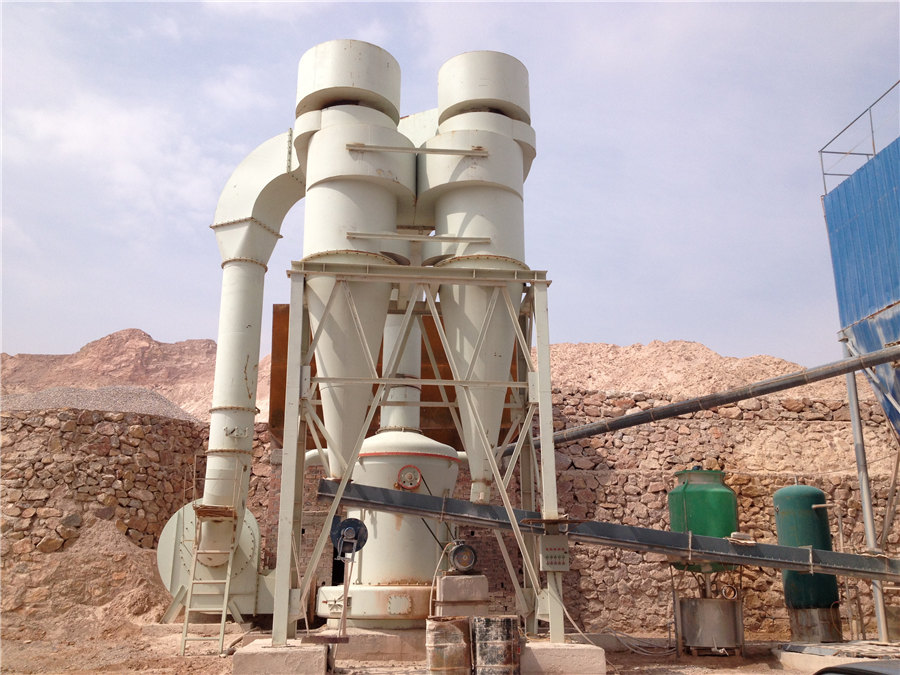
Grinding Mills — Types, Working Principle Applications
2018年8月17日 Extreme temperatures, impact velocity, mill load, grinding media, ore types, and applications are some of the factors to be considered while installing new liners2020年6月3日 Grinding mills are some of the most important equipment in mines, processing over a few thousand tons of ore every hour It is not uncommon to see these days that a single How grinding mill design changed over the last 30 yearsDSMAC sandstone crusher has many advantages according to other companies, so it’s right choice for you to choose DSMAC stone crushers for your sandstone crushing business As the important resource of nowadays industry production, ore minerals are required nearly in every business in the industrySandstone Ore Crushing Solutions DSMAC2013年4月16日 ABSTRACT In this study, ultrafine grinding of a refractory silver ore tailings was studied A laboratory scale pintype vertical stirred mill and ceramic beads were employed for the grinding testsInvestigation of some parameters affecting the Ultrafine grinding
.jpg)
BOND'S WORK INDEX: WHAT IT IS AND WHAT IT
It is commonly known that one must run the Bond ball mill work index test such you pick a closing Grindability and grinding characteristics of ores, Mining Technology, AIME, March, Pages 122 Ore Design Parameters Ore Grade % FeT 322 Drop Weight Index (DWi) Ore SG kWh/m3 111 340 Concentrate SG Bulk Density t/m3 430 201 Bond ball mill work index (BBWi) Bond abrasion Index (BAi) kWh/t 172 030 Bond rod mill work index (BRWi) Bond crushing work index (BCWi) kWh/t kWh/t 177 206 MPa MPa 148 355 Point Load Index (PLI) Unconfined (PDF) Reducing Grinding Energy and Cost Magnetite Iron Ore 2018年8月8日 One of the most effective methods of grinding Portland cement is the use of an electromagnetic mill, which has proven its advantage in creating clinkerless binders [2], regulating the kinetics of (PDF) Grinding Kinetics Adjustment of Copper Ore Grinding in 2019年11月15日 Sandstone grinding in electromagnetic mill Comparisons were made with the results from ball mill grinding experiments The aim of this work was to verify the usefulness of highenergy Sandstone grinding in electromagnetic mill – case study
.jpg)
Comparison of Ore Hardness Measurements for Grinding Mill
2021年1月14日 standard Bond crushing, and rod mill work indices, abrasion indices and by Dawson for Bond Ball Mill Work Index tests using crushed feed, and Standard Autogenous Grinding Design (SAGDesign) Tests, patented by Outokumpu (See reference 8 below) The comparison of these results gives context to how the various measurements relate to each2023年5月14日 The size of the grindstones depended on the intended use Diameters ranged from a few inches to seven feet, sometimes more, and thicknesses from two or three inches to sixteen inches, but rarely larger (Figures 5, 6, and 7) Large grinding stones were cut from the coarse sandstone while smaller ones were made from the finegrainedOhio’s Sandstone: Once the Source of the World’s Finest Grinding 2019年4月16日 Conference: Applying a Successful Technology from the Cement Industry: Advantages of Grinding Ore in a VerticalRollerMill; At: Antalya, Türkey(PDF) LEARNING FROM OTHER INDUSTRIES; WHY THE VRMI can't find consistent guidance on what mining boosts work with sandstone, however I know Honed 6 works, but what about the Quarrymaster aura and invisible level boosts like the Gargoyle familiar? To be clear, I'm referring to the sandstone deposits to make fine sand, NOT the crystal or red sandstoneOptimal sandstone mining setup? : r/runescape Reddit
.jpg)
Study on leaching systems and recovery for PALUA–PARONG low
2020年1月1日 From the energy economic view point (Durupt and Blanvillain 2010) the power consumption for crushing ore particle from size of 25 mm to 10 mm is only about 035 kWh/t because PaluaParong uranium sandstone ore belongs to the mediumhard type (BTI, Breaker Technology, 2019), the Bond work index for crushing this ore is ω 1 = 1271 kWh/t (Noakes The ball mill grindability test is used for describing ore hardness and it is so widespread that the Bond Work Index generated from the test is often referred to as an ore characteristicBond Ball Mill Grindability Test Summary ResearchGate2020年4月1日 Mill liners and grinding media (balls or rod) sizes along with ore residence time and circulating load all have impact on mill efficiency Power consumption is largely impacted by the grindability index as determined by Grinding Mills: How they Work Neumann 2015年3月15日 For the grinding tests, a Loesche mill LM45 (table diameter 045 m) is used (Fig 2a) This pilot scale mill is a special development for ore grinding, which is reflected by several features The mill has four rollers, which are able to stress the particle bed with grinding pressures of up to 5000 kN/m 2Research of iron ore grinding in a verticalrollermill
.jpg)
(PDF) Geometallurgical Studies on Gold Ore for Enhanced
2019年6月30日 The Bond Ball Mill Work Indices of the blends tested were between 164 kWh/t and 96 kWh/t and a blend ratio of 85% fresh and 15% weathered was found to have a Bond Ball Work Index almost equal to 2018年12月24日 The SMC and Bond ball work index experiments as well as the Morrell model indicated that the order of the specific energy consumption of comminution was “Jaw crusher + HPGR mill + ball mill EVALUATION OF THE ALTERNATIVES FOR GOLD ORE GRINDING 2018年1月1日 The article concerns issues related to the copper ore ball mill grinding process, operating at different technological parameters The aim of the study was to investigate the influence of various An assessment of influence of selected characteristics of feed on 2022年10月12日 A complex ore, such as Palabora, requires grindability measurements be made at three size classes, such as the three Bond work indices A simple ore, such as El Soldado, can be reliably modelled A Statistical Comparison of Bond Ball Mill Grindability Work Index
.jpg)
Grinding Mills and Their Types – IspatGuru
2015年4月9日 The mill is normally used for grinding of ores Lining of the cylinder plays very important role It protects the mill from abrasions and at the same time it helps in lifting of the material from the bottom of cylinder The types of lining are The grinding requirements for conglomerate ores are usually finer and vary more A grind of 50% passing 0074 mm (200 mesh) is not uncommon, and for some ores much finer grinding may be desirable A few ores, such as those produced from the intrusive Rossing type of deposit, leach at much coarser sizes (95%, —17 mm) 422CRUSHING AND GRINDING 1 Introduction ORE PREPARATIONLining is a special finish on the inner surface of the ore grinding mill protecting it from mechanical and physical damage which is very important for the labour protection of employees of mining and processing enterprises BGF Rubber Rubber Lining for Ore Grinding Mills and Mining and Concentrate or whole ore feed from the grinding circuit is further ground to a particle size of less than 10 μm to physically liberate gold using either a vertical or horizontal stirred mill Ultra fine grinding circuit for whole ore and

(PDF) Assessment of the Performance of Grinding
2021年2月9日 It had been reported by the management that BGM grinding circuit was designed to produce final product size of 125 μm, which had not been achieved for a long period of time under both, low to 1 Grindability: The grindability of the ore affects the efficiency of the grinding mill Harder ores require more energy and longer grinding times, which can impact the mill's performance and operational costs 2 Media andliner Wear: The condition of the grinding media and liners affects the mill's efficiencyUnderstanding the operation of grinding mills in the mining and 2014年10月1日 Request PDF Copper Ore Grinding in a Mobile Vertical Roller Mill Pilot Plant In addition, they indicate that the Bond ball mill work index is equal to 153 kWh/ton, Copper Ore Grinding in a Mobile Vertical Roller Mill Pilot PlantThe Autogenous Mill, also known as AG Mill, is a type of grinding mill used in the mining industry This machine uses ore and rock itself as grinding media to perform its job Unlike other types of mills that use steel balls or rods for grinding materials, the Autogenous Mill relies on the material being ground to break itself into smaller piecesUnderstanding the SAG Mill in Copper Ore Mining Process
.jpg)
Processing of Magnetite Iron Ores–Comparing Grinding Options
Ore grade Drop weight index (DWi) % FeT 322 kWh/m3 111 Ore specific gravity 340 Concentrate specific gravity 430 t/m3 201 kWh/t 172 Bond rod mill work index (BRWi) kWh/t 177 Bond crushing work index (BCWi) Bulk density Bond ball mill work index (BBWi) Bond abrasion index (BAi) 03 kWh/t 206 Point load index (PLI) MPa 148 Unconfined compressive SAG MILL TESTING AN OVERVIEW OF THE TEST PROCEDURES AVAILABLE TO CHARACTERIZE ORE GRINDABILITY AUTHOR: FO VERRET, G CHIASSON AND A MCKEN SGS KEYWORDS Comminution, grindability, grinding, SAG mill, AG mill, milling, HPGR, work index, pilot plant INTRODUCTION The resistance of ore samples to breakage (or hardness) is SAG Mill Testing Test Procedures to Characterize Ore EFFECTS OF MILL ROTATIONAL SPEED ON THE BATCH GRINDING KINETICS OF A UG2 PLATINUM ORE By DINEO MOKGANYETJI MAKGOALE Submitted in accordance with the requirements for the degree of MAGISTER TECHNOLOGIAE in the subject ENGINEERING: CHEMICAL at the UNIVERSITY OF SOUTH AFRICA SUPERVISOR: Prof FRANCOIS EFFECTS OF MILL ROTATIONAL SPEED ON THE BATCH GRINDING KINETICS OF Overall, ball size and shape are important factors to consider when choosing a mill for ore grinding However, other factors such as mill design and the type of ore being processed also play a role in how well the ball milling process works Effect of media type on ore grinding performanceFactors affecting ores grinding performance in ball mills

BOND'S WORK INDEX: WHAT IT IS AND WHAT IT ISN'T
1 A grindability measurement made in a laboratory work index apparatus, such as a ball mill work index (WiBM) or a rod mill work index (WiRM) 3 An operating work index (WiO): A measurement of a specific energy consumption and size reduction in an operating plant 4 A generic work index that represents an intrinsic ore breakage characteristic This step involves the material being retained inside the mill for a specific time (with or without grinding balls) which is calculated by applying Bond’s work index to the process calculation This index takes into account the material ore The six main steps of iron ore processing Multotec2009年1月1日 Also, equipment like ball mill is used at the final stages of grinding Among the comminution and grinding equipment, HPGR is increasingly utilized as tertiary crusher or primary mill because of Processing of Magnetite Iron Ores–Comparing Grinding Options1985年6月1日 PDF The relative significance of corrosive and abrasive wear in ore grinding is discussed Laboratory marked ball wear tests were carried out with Find, read and cite all the research you (PDF) Corrosive and abrasive wear in ore grinding ResearchGate
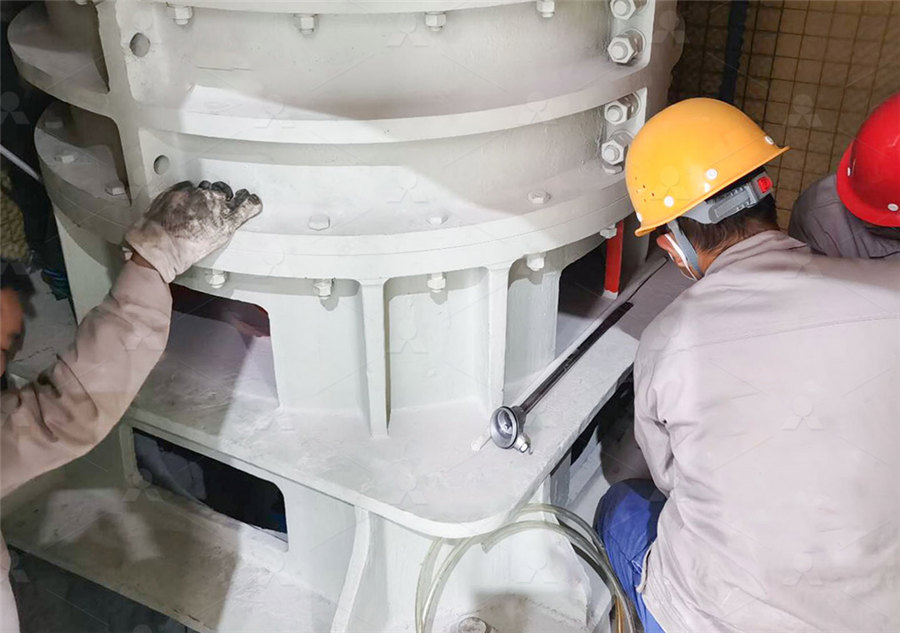
Copper ore grinding in a mobile vertical roller mill pilot plant
2015年3月10日 DOI: 101016/JMINPRO201410002 Corpus ID: ; Copper ore grinding in a mobile vertical roller mill pilot plant @article{Altun2015CopperOG, title={Copper ore grinding in a mobile vertical roller mill pilot plant}, author={Deniz Altun and Carsten Gerold and Hakan Benzer and Okay Altun and Namık A Aydogan}, journal={International Journal of Bond work index reduction In applications where HPGR is followed by tumbling mills, the induced micro cracks generally result in a reduction of the Bond Work Index For most ores this reduction is in the range of 10 – 25% This directly translates to either an increased throughput of the grinding circuit or a reducedEnduron High Pressure Grinding Rolls Weir Group2019年2月5日 High Pressure Grinding Rolls (“HPGR”) is applied in all stages of iron ore size reduction, from coarse ore grinding down to pellet feed preparationCONSIDERATIONS FOR MULTISTAGE HPGR GRINDING IN IRON ORE GRINDINGThe mining industry will be faced with new challenges as the need to develop lower grade ore Table 22 Summary of Grinding Media Wear Rates Table 46 Summary Bond Ball Mill Work Indices for Cone Crusher and HPGR Product A PilotScale Examination of a Novel High Pressure Grinding Roll
.jpg)
Crushing Plant Flowsheet DesignLayout 911Metallurgist
2016年3月11日 In the crushing section, the ore as it comes from the mine is broken down dry to a size suitable for the wet grinding machines ; these can, if necessary, be made to take lumps of 2in size, but they work much more efficiently if their feed is ½ in or less