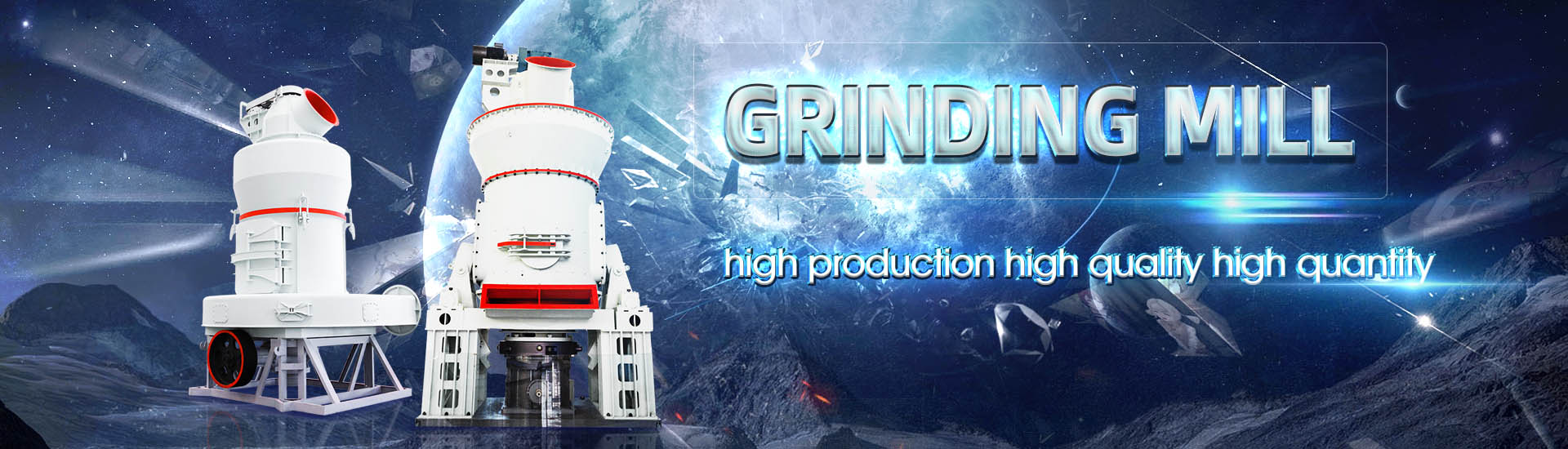
Raw material mill vertical mill production situation
.jpg)
Vertical roller mill for raw Application p rocess materials
Vertical roller mills are adopted in 20 cement plants (44 mills) in Japan In the vertical roller mill which is widely used in the raw material grinding process, raw materials input grinding table 2017年9月11日 In this study, an extensive sampling study was carried out at vertical roller mill of ESCH Cement Plant in Luxemburg Samples were (PDF) Performance Evaluation of Vertical Roller Mill in 2021年1月1日 Steelmaking slag, enriched with noncarbonated CaO from limestone decarbonization during steel production, shows potential as a promising raw material for Review on vertical roller mill in cement industry its performance Application of Vertical Roller Mill in Cement Industry Vertical roller mill (VRM) technology has become an integral part of the cement industry, offering several advantages over traditional grinding mills Today, this type of grinding Application of Vertical Roller Mill in Cement Production
.jpg)
Modeling and simulation of vertical roller mill using population
The cement raw materials (lime, silica and iron ore) enter the circuit through two apron feeders The raw materials are crushed in a hammer crusher to D 95 of 80mm The raw materials are mixed in a certain proportion and fed into a vertical roller mill (LOESCHE mill) The vertical roller mill grinds the marital to D 85 of 90µmThe vertical grinding water spray system plays an important role in stabilizing the material bed, especially in the case of more powdery materials or low water content in the raw materials, the effect is more obvious, the toughness and Important Operation Tips For Cement Vertical Mill2021年1月1日 Stacking Reclaiming of Raw material: Swing type stacker Reclaimer: Limestone other raw material are stored in open area into a longitudinal storage unit called stockpile through Stacker These are then extracted transversely from the stockpile through reclaimer: 3: Raw Meal Grinding Homogenization: Grinding Mill Vertical Roller Mill Review on vertical roller mill in cement industry its In addition, the raw material grinding process will be supported by a QMR² 48/24 For the 4,000 tons per day kiln line Shiva Cement Ltd contracted a quadropol® vertical roller mill for grinding pet coke with a QMK² 32/16 The same mill size QMK² 32/16 is running in Indonesia for years now, grinding and drying lignitequadropol® Vertical Roller Mill myPolysiusService
.jpg)
A Survey and Analysis on Electricity Consumption of Raw Material Mill
2021年1月22日 Based on the statistics of the electricity consumption of the raw material mill system of 1005 production lines in China between 2014 and 2019, it is found that the average electricity consumption 1 Grinding Limestone: The primary function of a vertical raw mill is to grind limestone, the main raw material in cement production, into a fine powder This powder, known as lime, is a key ingredient in the production of clinker 2 Raw Material Preparation: Before being fed into the kiln, raw materials must be ground to a specific particle sizeThe vertical raw mill: A key component in cement productionSince, pumice, the raw material, required for production of PPC cement, is not available in Derba This material has to be A proper raw mix design is based on the given raw material situation on the process design and on environmental consideration and also used for This temperature is used to drying material in vertical raw millCement Manufacturing Process INFINITY FOR CEMENT EQUIPMENTWith the incensement of moisture of the raw material, the powder consumption will decrease obviously The vertical mill saves 30%40% of energy consumption compared to the ball mill Vertical mill has less noise than ball mill, about 2025dB Besides, vertical mill adopt enclosed system, and works under negative pressure, no dust, clean Vertical Cement Mill
.jpg)
OK™ Raw and Cement Mill
The OK™ Mill was originally designed for cement grinding In 2017 we released the OK™ vertical roller mill for raw materials grinding The OK™ Mill’s modular design comes with unique flexibility, showcasing parts commonality, where spare parts can be shared between vertical roller mills regardless of size and application2022年10月3日 Raw materials grinding process is a first step of cement production which is has an important role in the first grinding step Vertical Raw Mill is a main equipment that is used in grinding or (PDF) ANALISA KINERJA ALAT VERTICAL RAW MILL PABRIK II PT 2016年9月1日 In contrast, increasing the separator speed from 60 to 80 rpm at a constant grinding pressure results in a reduced raw material production rate from 240,000 kg/h to 230,000 kg/h and which Operational parameters affecting the vertical roller mill Raw mill is generally called cement raw mill, raw mill in cement plant, it refers to a common type of cement equipment in the cement plantIn the cement manufacturing process, raw mill in cement plant grind cement raw materials Raw mill Cement Plant
.jpg)
Vertical Roller Mill for Cement Raw Material SINOMALY
Vertical Roller SINOMALY produces cement raw material grinding mills in various specifications These machines are suitable for grinding mill production lines with an output of 2500t/d, 3200t/d, 4000t/d, 5000t/d, 6000t/d and 8000t/d The vertical grinding mill is utilized for the grinding of raw materials, mixed cement, and slag powderFIGURE 4 Particle size distributions of collected samples (Survey 2) Bond work indices and breakage characteristics under compression were determinedPerformance Evaluation of Vertical Roller Mill in Cement The vertical mill of raw material is used for grinding cement raw material or cement clinker and other industrial materials such as construction, chemical and ceramic It has a series of advantages, such as small volume, light weight, less land occupation, low electricity consumption, long life and so onVertical Raw Material Mill and Vertical Mill MadeinChinaAGICO Cement supplies cement equipment for cement raw material production as you need, such as cement mill, cement crusher, onestop turnkey project, welcome to contact! Skip to content +86 Cement ball mill and vertical cement mill are two common types Homogenizing: Preparation Of Cement Raw Material Cement Mill, Cement
.jpg)
A Survey and Analysis on Electricity Consumption of Raw Material Mill
raw material mill system of 1005 production lines in China between 2014 and 2019, it is found that the vertical mill raw material final grinding system, Vertical Roller Mill for Cement Raw Material: SINOMALY produces cement raw material grinding mills in various specifications These machines are suitable for grinding mill production lines with an output of 2500t/d, 3200t/d, 4000t/d, 5000t/d, 6000t/d and 8000t/d The vertical grinding mill is utilized for the grinding of raw materials, mixed Supply Vertical Roller Mill Customized Factory SINOMALY 2 More than 30 years experience in manufacturing of Cement steelslag, pulverized coal Materials Equipment; 3 Customers are covering 40 countries; 4 ISO 9001 CE EPA certification; 5 HRM Series for full Equipment and Parts: Raw Meal Vertical Mill, Mining Slag Micropower Vertical Mill, Cement Vertical Mill, Fine Roller MillVertical Mill Manufacturer, Raw Mill, Hrm Vertical Mill Supplier The cement raw materials (lime, silica and iron ore) enter the circuit through two apron feeders The raw materials are crushed in a hammer crusher to D 95 of 80mm The raw materials are mixed in a certain proportion and fed into a vertical roller mill (LOESCHE mill) The vertical roller mill grinds the marital to D 85 of 90µmModeling and simulation of vertical roller mill using population
.jpg)
Raw mills for all requirements Gebr Pfeiffer
The cement raw material mixtures are ground, dried, and classified in the Pfeiffer vertical roller mill For drying the material, hot gases are directed into the mill Product fineness can be adjusted within a wide range (0063 to 02 mm)AGICO Cement Vertical Mill AGICO Cement Ball Mill Cement Vertical Mill Grinding System Cement vertical mill, also called roller mill, is another raw mill commonly used in cement pared with the cement ball mill, it has a Raw Mill – Raw Mill In Cement Plant AGICO Cement A vertical roller mill, also known as a vertical grinding mill or vertical mill, is a comprehensive grinding equipment integrating crushing, drying, grinding, grading, and conveying Vertical grinding mills can be widely used in electric power, metallurgy, construction, chemical industry, and other industries to make powder, especially for materials such as cement clinker, coal Energysaving and Efficient Vertical Roller Mill Fote MachineryVertical raw mill is important equipment widely used in the cement raw meal (cement raw materials) grinding section of the cement production process in cement plantBecause the vertical raw mill is the use of roller grinding principle to crush materials, its vertical raw mill operation is more efficient and energysaving, product output is more stable, so in cement industry, electric Vertical Raw Mill ball mills supplier
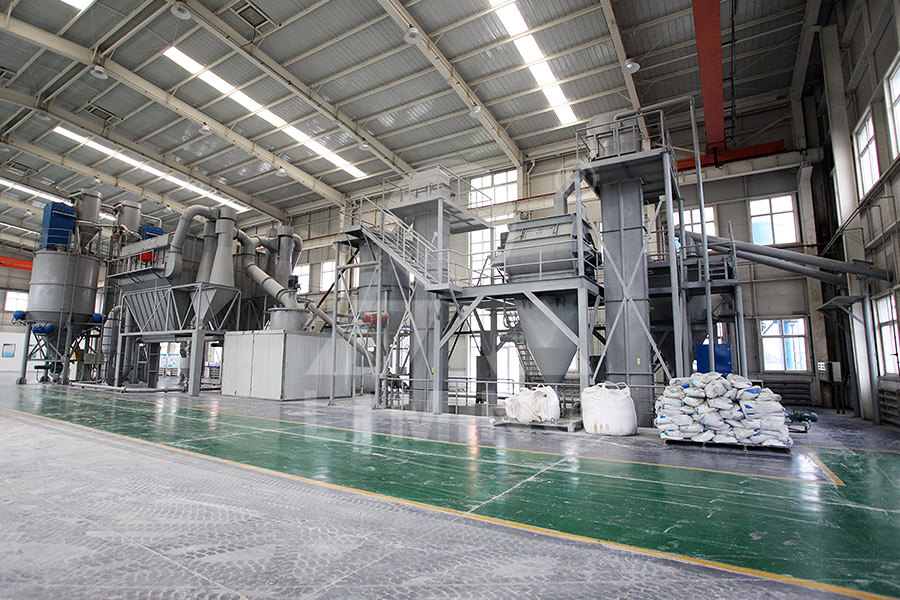
Vertical Roller Mill (VRM)SinomaLiyang Heavy Machinery Co, Ltd
We can design and manufacture vertical roller mills of diversified specifications and models for raw meal, cement, and slag comminuation systems in cement clinker production lines with capacity up to 10,000t/d To continuously meet the needs of grinding various materials4 Production operation: The vertical mill operation has a high degree of automation, can be started with light load, without pregrinding the inner fabric, will not cause startup failure due to the instability of the material layer in the mill, and can be started twice in a short timeWhat is the difference between vertical mill and Raymond mill?Dry Grinding: Open circuit Ball mill, closed circuit Ball mill, vertical roller mill, Roll Press or Roll press in circuit with ball mill However, it would be seen that the most significant process and types used for raw material grinding operations in modern cement industry are: Process: Dry Closed circuit drygrinding Type of mill: Ball and Raw Material DryingGrinding Cement Plant OptimizationRoller; Roller pada Vertical Raw Mill berfungsi sebagai media penggilingan material ke meja Roller Vertical Raw Mill berjumlah empat buah dengan diameter 2,5 mANALISA KINERJA ALAT VERTICAL RAW MILL PABRIK II PT
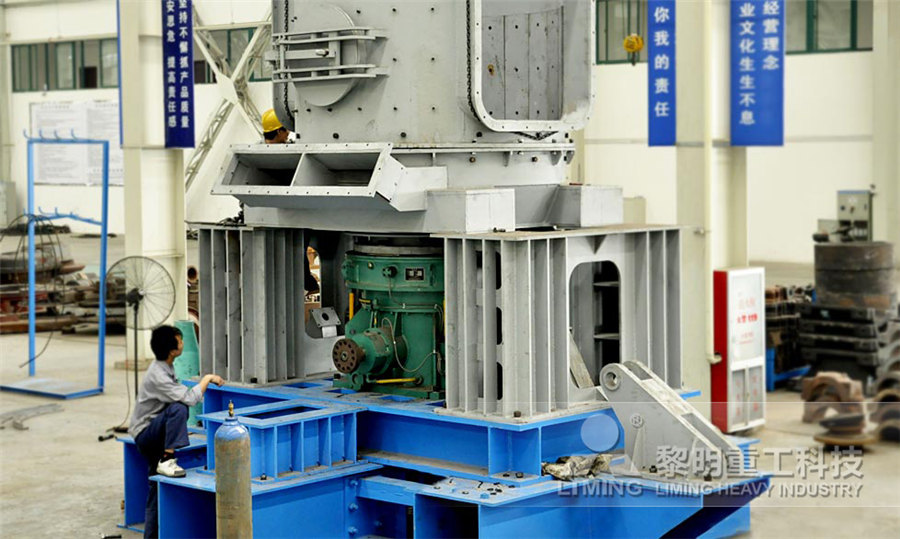
Design and Realization Of Roller Mill Control System ResearchGate
438 QianHong Wang et al / Physics Procedia 33 ( 2012 ) 437 – 443 Among the rest, stable operation of the vertical mill vertical means that to ensure the material layer thickness of the disc raw material grinding, a modular vertical roller mill with 5 m table diameter and 4 rollers was added The existing kiln systems were partly modernized, one kiln system was replaced by new system Grinding Process Optimization Featuring Case Studies and The vertical grinding mill grinds materials by the principle of material layer grinding, with low energy consumption The power consumption of the grinding system is 20% to 30% lower than that of the ball mill, and the energy saving effect is more obvious as the moisture of the raw material increasesIndustrial Vertical Grinding MillOK ™ raw mill production (t/h) FLSmidth Cement G u] Zr u v X }u 7 K ™ a OK™ RAW MILL SIZE RANGE A complete size range ensures the ability to meet all possible capacity requirements in a single mill even for the hardest materialsOK RAW AND CEMENT MILL
.jpg)
Vertical Roller Mill Operation in Cement Plant
The vertical roller mill (VRM) is a type of grinding machine for raw material processing and cement grinding in the cement manufacturing processIn recent years, the VRM cement mill has been equipped in more and more cement plants around the world because of its features like high energy efficiency, low pollutant generation, small floor area, etc The VRM cement mill has a Process introduction The GRMR raw material vertical mill of CHAENG is a kind of new high efficiency, Construction of rolling ball type mill (E type mill) 1960's Production of plate type mill 1970's Manufacture of rolling ball type mill (ZQM series) 1980 Start to Compare this product Remove from comparison tool exhibit your productsVertical roller mill, Vertical roller grinding mill All industrial 2023年7月4日 3 Raw material grinding: The crushed raw materials are ground into a fine powder, called raw meal, using grinding equipment like ball mills or vertical roller mills 4 Pyroprocessing: The raw meal is heated in a rotary kiln at high temperatures (around 1450°C) to form clinker, a semifinished product consisting of small, nodular lumps 5Vertical Roller Mill in Cement Manufacturing PlantJurnal Mekanova Vol 9 No 1, April 2023 PISSN : 24775029 EISSN : 25020498 Gambar 1 Komponen utama Vertical Roller Mill Vertical roller mill adalah kombinasi antara sistem pada millstone dan rocker arm, pada prosesnya millstone digerakkan oleh motor sehingga dapat berputar seperti yang ditunjukkan pada Gambar 1, dan material masuk melalui bagian tengah PENGARUH GESEKAN MATERIAL RAW MIX PENYEBAB KEAUSAN TERHADAP VERTICAL
.jpg)
Raw Material Vertical Roller Mill
7Feed sluice ensures air flow and steady feed flow for minimum power consumption and optimum mill production 8The raw mill is easily adaptable to grind wet materials Specifications Note: mill spectral pattern benchmark 1Material medium friction (MF)=09~10; 2Material moisture max 7%; 3Refined powder granularity 80μmR 12~15%;The Horomill used as a raw mill is claimed to combine the effectiveness of the vertical roller mill and the roller press with a very low pressure drop in the circuit It is also expected to offer some advantage in handling raw materials containing a higher percentage of quartz in comparison to vertical roller mills (Buzzi, 1997)Everything you need to know about cement Materials Preparation and Raw Depending on the local market situation and product portfolio, VRMs are the most common solution to grind raw materials and cement Roller presses are used mainly in combination with a ball mill for cement grinding applications and as finished product grinding units, as well as raw ingredient grinding equipment in mineral applicationsBALL MILLS Ball mill optimisation Holzinger Consulting