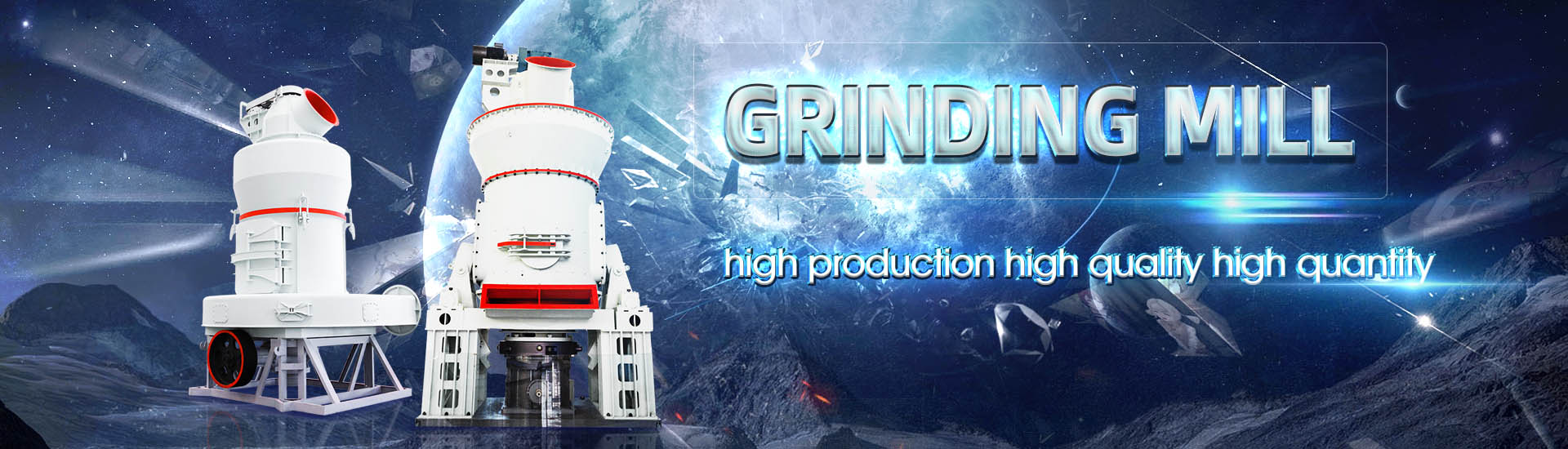
Dry grinding zinc smelting silo design
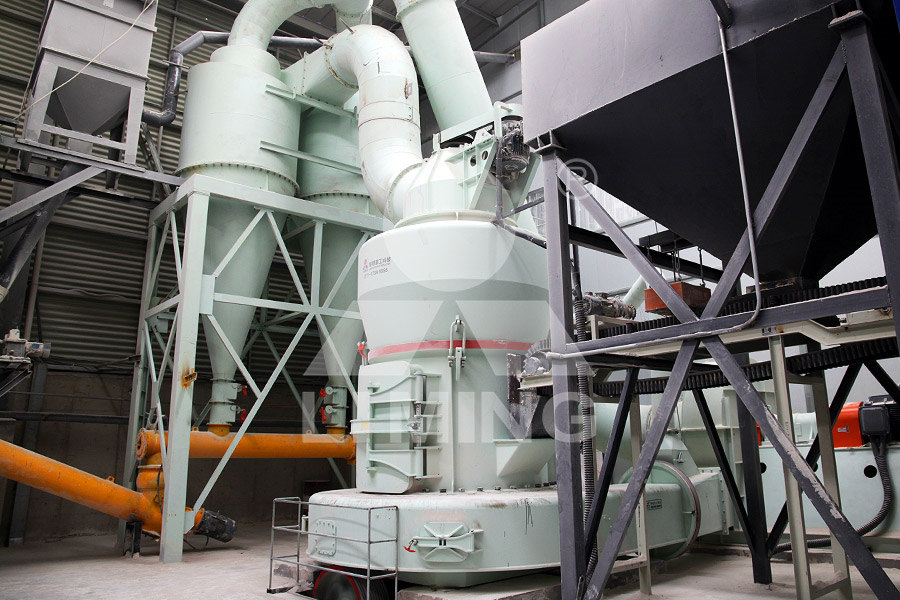
Calculation method to Design Hoppers and Silos Hopper and
The flow of powder in a hopper is linked to 3 properties : 1 The powder internal friction : how easy the powder particle can move from each other 2 The 展开2022年2月28日 This book introduces and explains all existing dry processing methods, drawing from larges studies about these techniques in both the academia and industrial sectors Dry Mineral Processing SpringerLink• Metal Extraction: Smelting is the primary method for extracting metals from their ores It allows for the separation of valuable metals from the host rock or mineral matrix in which they are Guide to Modern Smelting Processes CED Engineering1991年3月1日 In the present paper three examples will be presented in order to illustrate the range of application of silo design methods: the design of a silo for storage of moist limestone, (PDF) Examples of modern silo design ResearchGate
.jpg)
Basics of Silo Design Engineering BSCES Boston Society of Civil
2023年11月13日 In the following paragraphs, topics related to the design of silo structures will be discussed These topics include behavior of stored bulk solids, materialinduced loads, and This article presents methods for measuring fundamental bulk solids flow properties and explains how to use them to design hoppers, bins, and silos for reliable flow It expands on previous Designing Hoppers, Bins, and Silos for Reliable Flow AIChE2015年1月1日 In order to structurally design a silo, an engineer must determine all loads that are likely to be applied to it These include, among others, wind, seismic, external, and loads Silo Design Codes: Their Limits and Inconsistencies2017年9月26日 The following is an overview of a couple of particularly important areas of building codes that affect design and fabrication of industrial storage silos The storage silo is Building Codes and Bulk Storage Silo Design Powder Bulk Solids
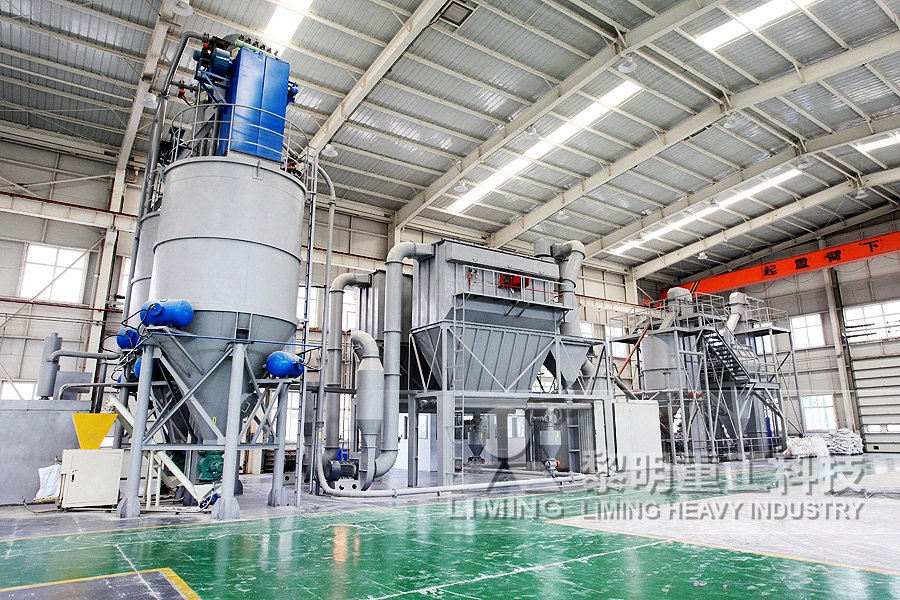
Bulk solids handling system design Processing Magazine
2016年11月28日 This article discusses critical design parameters required for a reliable storage vessel (such as a silo, bin, tote, intermediate bulk containers, hopper, bunker, stockpile 2024年3月2日 Fly ash silos are crucial components in the construction industry, especially in concrete production The design of these silos plays a critical role in ensuring efficient storage and handling of fly ash, a byproduct of coal Fly Ash Silo Design: Key Considerations for Efficient 4 Silo Design good principles In order to design properly a silo, several considerations must be kept in mind, related to the product to store, the material in which the silo will be built, and the safety of the installation Table 5 : Silo Calculation method to Design Hoppers and Silos2021年4月29日 Stephen Hall discusses the golden rules for design SOLID materials are stored and dispensed from bins For the purpose of this article that means bins, hoppers, and silos interchangeably Bins are vessels that contain Rules of Thumb: Solids Transfer Bins Silos

Dry Grinding for Roasting 911Metallurgist
2016年4月1日 There are two parallel dry grinding circuits prior to roasting Crushed ore is carried to the two circuits by the two reclaim conveyors located below the 911 Metallurgist is a trusted resource for practical insights, solutions, and support in mineral processing engineering, helping industry professionals succeed with proven expertise Dry Grinding for Roasting2016年6月6日 The use of the integral lift bar principle reduces the number of pieces and handling time This design is also convertible in the future to the patented “insert” concept as applicable See Figure 6 Total active patterns in this idealized case is only six excluding the trunnion liner and inner discharger SemiAutogenous Grinding (SAG) MillsSAG Mill Liner Design 911Metallurgist2023年11月1日 In this study, a novel dry capture process utilizing a mixed adsorbent of ZnO and CuS was proposed for the simultaneous removal of Hg⁰ and SO3 in flue gas from zinc smelting, addressing severe (PDF) PilotScale Experimental Investigation on Dry• Metal Extraction: Smelting is the primary method for extracting metals from their ores It allows for the separation of valuable metals from the host rock or mineral matrix in which they are naturally found Commonly extracted metals include iron, copper, aluminum, lead, zinc, nickel, and precious metals like gold and silverGuide to Modern Smelting Processes CED Engineering
.jpg)
Gold Ore Roasting Plant 911Metallurgist
2016年6月1日 One silo is provided for each dry grinding circuit Each silo has a 2,000ton live capacity providing a normal 6 hours of roaster feed The silo is designed as a massflow silo The hopper section of the silo is sufficiently steep and has a coefficient of friction that is sufficiently low to ensure that all the material is discharged2016年3月11日 In the crushing section, the ore as it comes from the mine is broken down dry to a size suitable for the wet grinding machines ; these can, if necessary, be 911 Metallurgist is a trusted resource for practical insights, solutions, and support in mineral processing engineering, helping industry professionals succeed with proven expertise Crushing Plant Flowsheet Crushing Plant Flowsheet DesignLayout 911Metallurgist2016年12月15日 By keeping the level of the froth consistently equal to that of the overflow lip, the quantity of froth removed is controlled by the paddle design and the number of froth removal sweeps per minute Details of the number of concentrate collections per minute and timing of the sweeps can be found in EMC’s procedureFlotation: Principles and Applications in Mineral Processing2022年1月1日 Grinding is the final stage of comminution, performing size reduction at finer sizes than crushers Size reduction is achieved by a combination of impact breakage, abrasion, and attrition After grinding, the characteristics of the solid material is changed: the grain size, the grain surface and the grain minution and classification technologies of iron ore
.jpg)
(PDF) Examples of modern silo design ResearchGate
1991年3月1日 Silo design for flow provides the maximum hopper inclination angle to achieve mass flow, and the minimum outlet dimensions to avoid arching and ratholing for the basic hopper shapesMethods for Design of Hoppers Silos, Bins and Bunkers for Reliable Gravity Flow, for Pharmaceutical, Food, Mineral and Other Applications MSA Bradley , RJ Berry, RJ Farnish The Wolfson Centre for Bulk Solids Handling Technology University of Greenwich Chatham, UK bulksolidsMethods for Design of Hoppers University of Greenwich2021年9月3日 The silo design method applied above assumes the emptying state for the bulk solid in the hopper which prevails when the bulk solid in the silo has already been in motion In the emptying state (Fig 1028 ), the consolidation stress, σ 1 , in the lower part of the hopper is proportional to the local hopper diameter and therefore decreases linearly towards the outlet Silo Design for Flow SpringerLink2009年6月28日 Simplified slag phase relationships for zinc direct smelting (Stage 1 at 1250 °C) in a TSL furnace showing the Slagliquid area for typical smelting conditionsTop Submerged Lance Direct Zinc Smelting ResearchGate
.jpg)
Dry Grinding VS Wet Grinding 911Metallurgist
2017年5月25日 An examination of the literature shows, however, that the actual difference between the results of wet and dry milling are often very large; for example the power to drive a tube mill in which a given material is being wet ground may be as much as 30 % less than that of a similar mill dry grinding2017年9月26日 First and foremost are the building codes – the International Building Code, or IBC – that will determine the wind and seismic factors used in the design of the silo itself Regardless of how you design the silo structure, you will need to know the wind loads and seismic loads present on that silo before you can even begin Two silos of the Building Codes and Bulk Storage Silo Design Powder Bulk From Table 11 there is clearly an imbalance between regional mining and smelting activities, indicating considerable trade in the intermediate smelter feed or zinc concentrate THE ZINC SMELTING INDUSTRY The world primary zinc smelting industry employs five distinctive processes: The Extractive Metallurgy of Zinc Spectrum Series Volume 13 3The Extractive Metallurgy of Zinc AusIMM2016年4月12日 This reaction is a result of a differently acting “bed of pulp” and lack of grinding media “coating” Due to a common “swelling action” of dry material being ground, the grinding media level is often reduced to approximately 4042% of mill volume Dry grinding offers less steel consumption than its equivalent wet grinding counterpartDry Grinding Coke Grinding 911Metallurgist
.jpg)
(PDF) MPS mills for coal grinding ResearchGate
2014年1月1日 temporary storage of the pulverized coal in silos (for cement plants, design of a grinding system for solid fuels with Mill size Cement Steel Zinc smelting plant Total 112 2 1 3 125 2022年12月20日 Reliable bulk solids material flow from a bin or silo requires that the silo hopper is designed to create the correct flow pattern (funnel flow or mass flow) during discharge In funnel flow, material above the hopper outlet How feeder design impacts silo discharge Processing 2011年10月29日 It describes the major zinc ores and details several pyrometallurgical and hydrometallurgical extraction processes The key processes are roasting to produce zinc oxide from zinc sulfide ores, followed Extractive Metallurgy Presentation (Zinc) PPTAt temperatures typically used for smelting metals, zinc is a gas that will escape from a furnace, unless specific measures are taken to prevent it Zinc is extracted from the purified zinc sulfate solution by electrowinning, which is a specialized Zinc Smelting from Ore Wilfley
.jpg)
Silo design bulk solids
Silo design, flow, bridging, feeding p 1/6 BSE bulk solids engineering Kogelerbos 10 tel +31 53 434 45 66 NL7543 GT Enschede post@bulksolids Silo design Avoiding flow problems through adequate design To avoid problems in silos concerning flow, product ageing or decay, silo design is necessary The design of a silo is based on the most reliable design criteria for silos are available In the present chapter the well known design procedure due to Jenike [101,102] is described, which is based on the bulk solid’s properties The expense to measure bulk solid properties that are necessary for silo design for flow is normally small compared to the costs which arise due to 10 Silo design for flow Springer911 Metallurgist can enter the scene and see what you have become blind to We can fix issues in ways you never thought possible Our fresh eyes will open new opportunities for your plant Each mineral processing plant has varied ore types, mining equipment, (crusher, ball mill, flotation, tailings), and management (operating) philosophyThe evaluation and prioritization of variables Metallurgists Mineral Processing Engineers 911MetallurgistZinc ores typically contain three to eleven percent zinc, along with cadmium, copper, lead, silver, and iron Beneficiation, or the concentration of the zinc in the recovered ore, is accomplished at or near the mine by crushing, grinding, and flotation Once concentrated, the zinc ore is transferred to smelters for the production of zinc or BACKGROUND REPORT PRIMARY ZINC SMELTING Prepared for
.jpg)
MEKA SCREENING PLANT FOR ZINC REFINERY AND SMELTER
Zinc and lead ores are mined in key mining sites of Hakkari, Siirt, Şırnak, and smelting and refining of zinclead and other minor metals at processing operation at Siirt Industrial Zone Plant Design Criteria • Material to be processed is ZnPb Ore with a solid density of 34 tons/m³ • Feed material size : 0600 mm2020年11月27日 To avoid problems in silos concerning flow, product ageing or decay, silo design is necessary The design of a silo is based on the most economical case: gravity flow Wall friction, internal friction and bridging properties determine the applicable hopper angle and opening diameterSilo design: avoiding flow problems through adequate design2024年3月20日 Zinc oxide is used in chemical, pharmaceutical and metallurgical industries In the zinc oxide processing production line, zinc oxide rotary kiln is an important production equipment for calcining zinc processing, its appearance is similar to a large furnace, it is composed of preheater, rotary kiln, cooler and other combination of roasting system, the Zinc Oxide Rotary Kiln Project In Shandong AGICO CEMENT2016年2月29日 In general, slag from smelting process arises from extraneous materials such as rust and oxides; oxidation of elements in the charge (eg iron, copper, zinc); residues from fuels; fluxes employed in the process (silica, Gold Smelting Refining Process 911Metallurgist
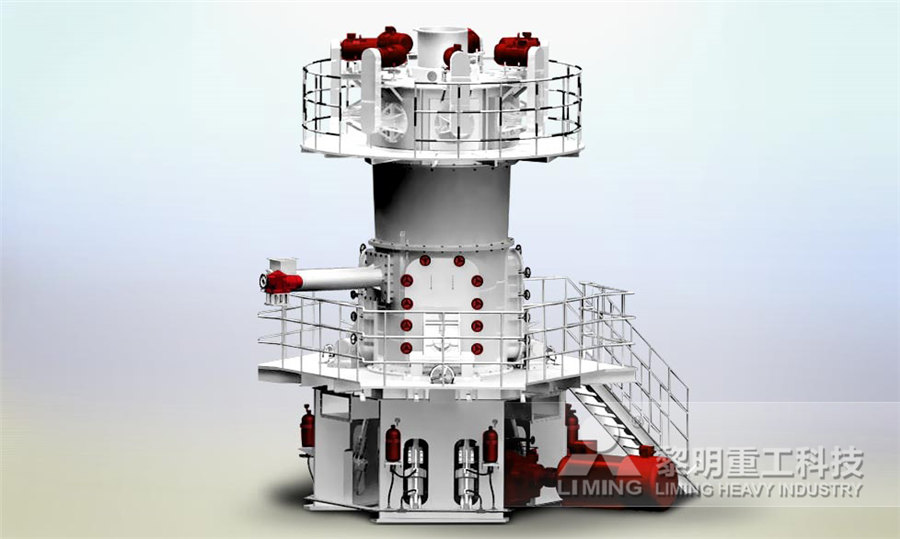
Flotation data for the design of process plants Part 1 AusIMM
Flotation data for the design of process plants Part 1 – testing and design procedures R C Dunne*1, G S Lane2, G D Richmond3 and J Dioses2 This paper discusses the methods used in the design of flotation plants, including benchscale batch and locked cycle tests and pilot plant trials The methods used to establish appropriateRailcar and Bulk Truck Unloading Systems Silo Filling Systems: Whether unloading multiple railcars per day, or periodically unloading a single truckload, National Bulk Equipment silo filling systems provide reliable, repeatable, and Bulk Material Storage Silos National Bulk Equipment, 2024年1月17日 Selecting a dependable steel silo supplier ensures highquality manufacturing, professional design services, timely delivery, and ongoing support When comparing manufacturers, assess: Expertise Experience – Long, proven track record building all types of steel silos; Custom Design Capabilities – Engineers silos specific to your needsChoosing the Right Steel Silo Design for Your Storage Needs2018年5月9日 3 Common forms • Silos are generally circular in cross section, although different forms, such as square or rectangular cross sections are commonly adopted for shallow bins or bunkers • When calculating the size of a silo of a specified capacity, the unit weight of the material should not be overestimated and too small a value should not be assumed for the Design of silo PPT SlideShare
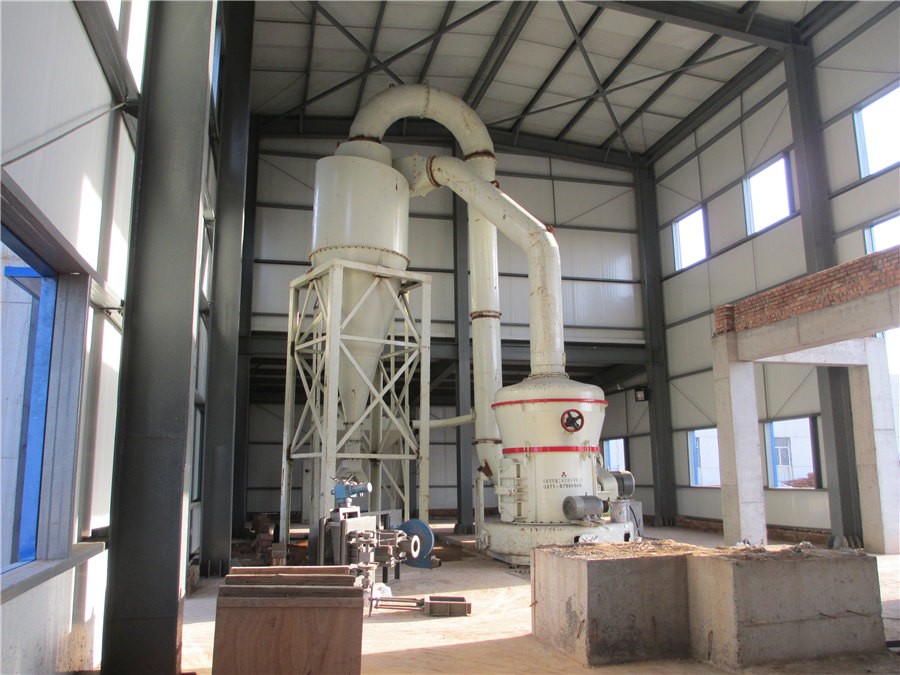
Silos Design Limits Jenike Johanson
2013年7月3日 The most modern and complete silo design code in use today was adopted by the European Committee for Standardization (CEN) in 2005 The formal designation for the English version of this code is British Standard BS EN 19914:2006 “Eurocode 1 – Actions on structures – Part 4: Silos and Tanks”2022年2月25日 Superposition Effects of Zinc Smelting Atmospheric Deposition on Soil Heavy Metal Pollution Under Geochemical AnomalySuperposition Effects of Zinc Smelting Atmospheric Deposition 2018年7月18日 Hydrometallurgical recovery of zinc from electric arc furnace dust was investigated on a laboratory scale, using aqueous sodium hydroxide solution as a leaching agentZinc Recovery from Steelmaking Dust by Hydrometallurgical Methods2015年12月31日 In order to structurally design a silo, an engineer must determine all loads that are likely to be applied to it These include, among others, wind, seismic, external, and loads induced by the Silo Design Codes: Their Limits and Inconsistencies