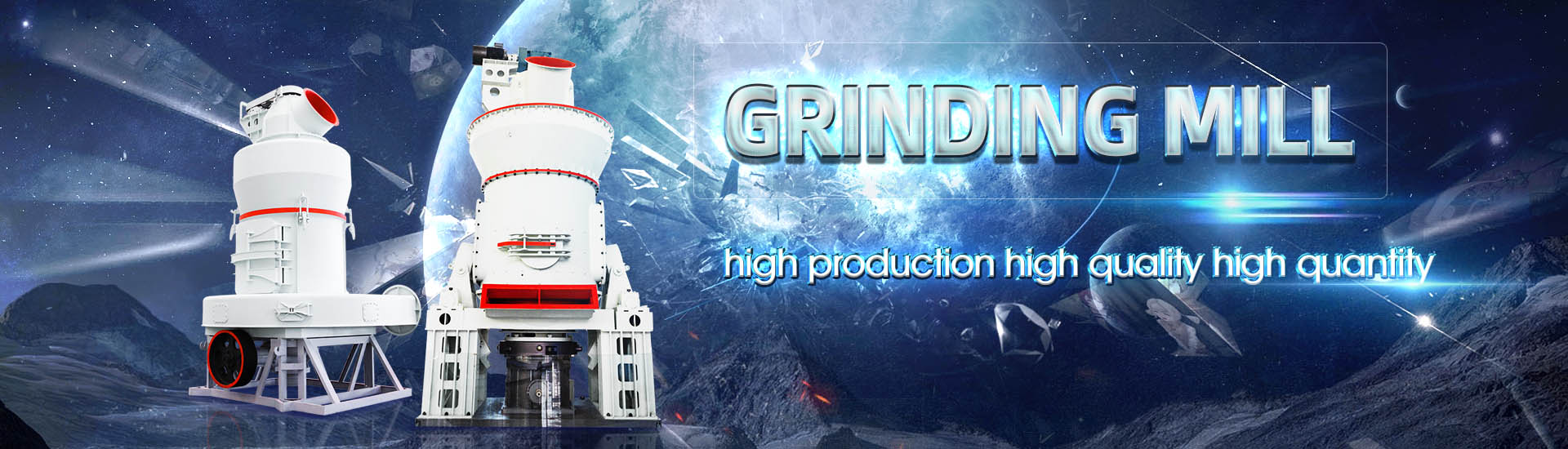
Excavation blast head ore mill
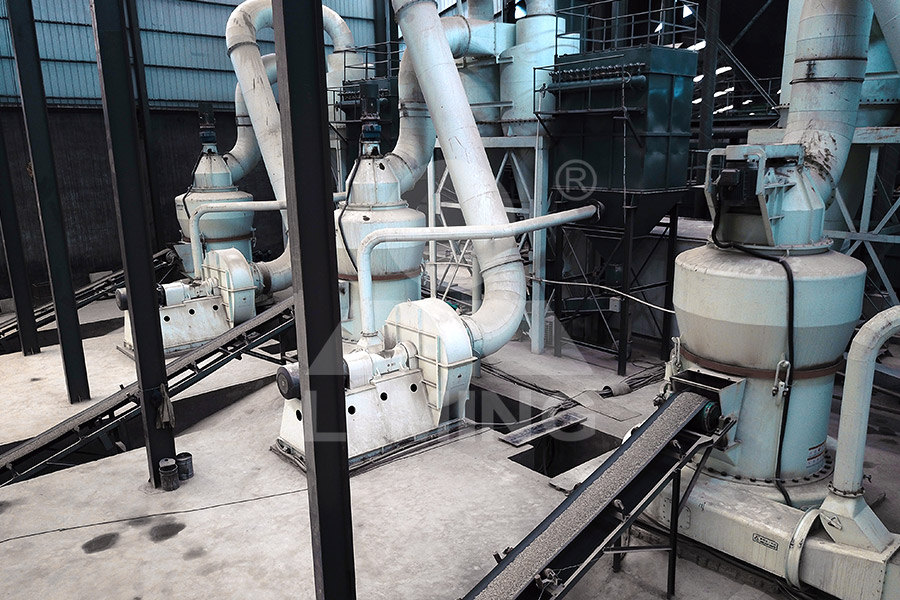
Blastability and Ore Grade Assessment from Drill Monitoring for
Production data often includes unrealistic high and lowperformance values of the drill rig that may lead to a wrong interpretation of the MWD data In line with the analysis followed by Navarro et al 展开Ore grade control is a compendium of procedures and practices usually involving blast hole sampling, grade estimation, ore/waste classification, blastinduced rock movement A review of grade control methods in open cast mining Queen's UThe primary objective of this study was to understand how ore loss and dilution affect the MCF and to subsequently improve the quality of ore mined and fed to the mill On the basis of this objective, the basic research question is: What is Monitoring ore loss and dilution for minetomill 2018年11月1日 Bowa introduced a practical method in an open pit mine to optimize blasting design parameters such as bench height, drill hole diameter, spacing, etc [5] Tosun and Optimized design of drilling and blasting operations in open pit
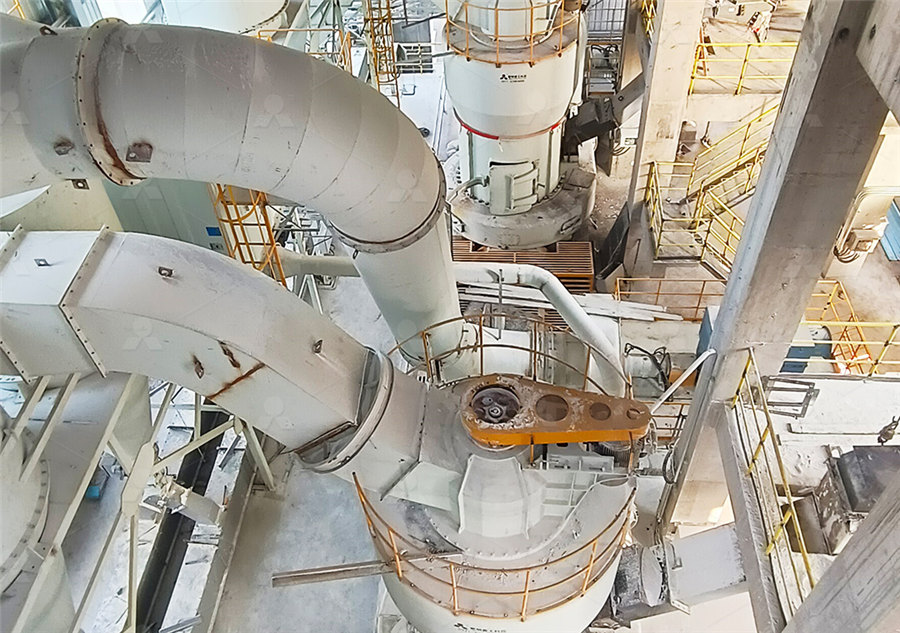
A review of the influence of blast fragmentation on downstream
2022年8月1日 In surface mining, excavation and cutting equipment can dig soft weathered ore with high productivity However, above a certain level of rock hardness and competence, the 2019年3月1日 Blast pull and sequence of excavation in varied rock classes should be optimized from time cycle and overbreak viewpoints Method of charging of perimeter holes is also Optimising blast pulls and controlling blastinduced excavation 2022年6月4日 Drill and blast techniques have been proven to be more efficient and costeffective compared to conventional mechanical rock breakage with machines The degree of Drill and Blast Optimisation at an Underground CopperGold Mine 2018年5月21日 This technique enables the operational dilution to be calculated It is applicable for operations using mechanical excavation and/or blasting The results demonstrate that operational dilution can be measured and controlled Controlling operational dilution in openpit mining
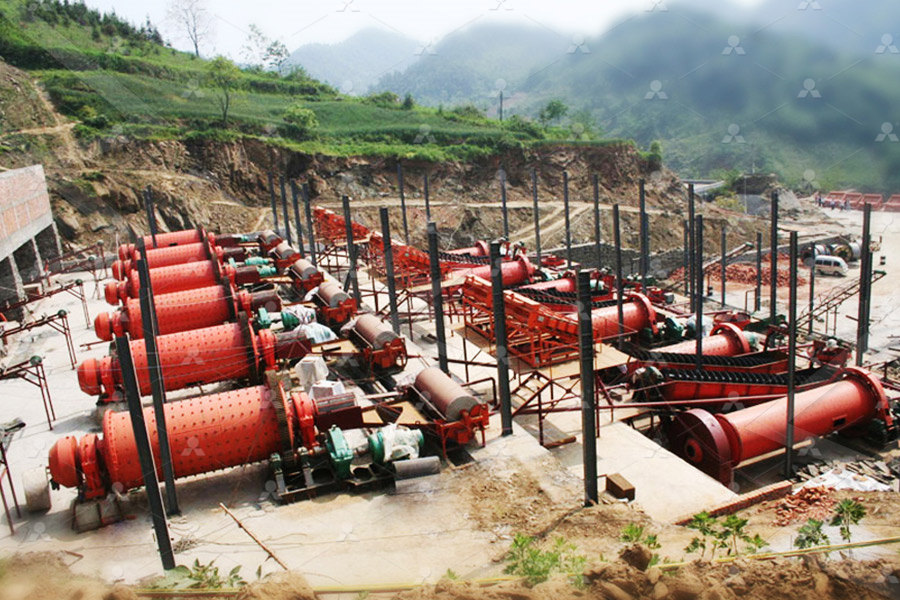
Integrating Underground Blast Fragmentation Modeling for
2024年9月1日 By optimizing underground mine bench blasting practices, mining companies can reduce their environmental footprint, improve operational efficiency, and enhance longterm 2023年2月11日 Drilling and blasting are a widely used excavation method in tunnelling applications due to its versatility, lower initial investment cost and easier applicability Drilling and blasting designs for parallel hole cut and Vcut collar for the head frame is installed after excavation has progressed a short distance The head frame includes the hoisting system for the shaft sinking equipment At this point, the actual shaft sinking begins A sinking cycle includes the following operations: † Drilling, † Blasting, † Mucking and hoisting, † Support or shaft Introduction to Underground Excavation by Drilling and BlastingThe primary objective of this study was to understand how ore loss and dilution affect the MCF and to subsequently improve the quality of ore mined and fed to the mill On the basis of this objective, the basic research question is: What is Monitoring ore loss and dilution for minetomill
.jpg)
Tracking and Quantifying Value from ‘Mine to Mill’Improvement
QUANTIFYING MINE TO MILL PERFORMANCE Important measures for the management and assessment of rock breakage and comminution include: • the breakage characteristics of the ore, • blast performance, • excavation performance, • tracking through stockpiles, • fragmentation, • crushing performance, • grinding performance, and • costTraditionally, blasts in mining operations are designed to prepare the in situ rock mass for excavation and transport without much consideration being given to the downstream comminution processes Blasting is in fact the first step in a chain of comminution processes from the in situ rock to a marketable product and often plays a more important role than just preparing the Exploring the effect of blast design on SAG mill throughput at Benchmark Drill and Blast and Mechanical Excavation Advance Rates for Underground HardRock Mine Development P Stewart1, A Ramezanzadeh1 and P Knights1 ABSTRACT Faster development rates in Benchmark Drill and Blast and Mechanical Excavation Advance meaningless if the preblast ore perimeters defined are not translated after blasting before excavation, to account for blast movement Therefore, ore loss and dilution can be minimised and significant increases in profit can be realised if the movement of the blast can be accurately measured Over the years, AngloGold Ashanti Iduapriem Limited Control of Ore Loss and Dilution at AngloGold Ashanti, Iduapriem
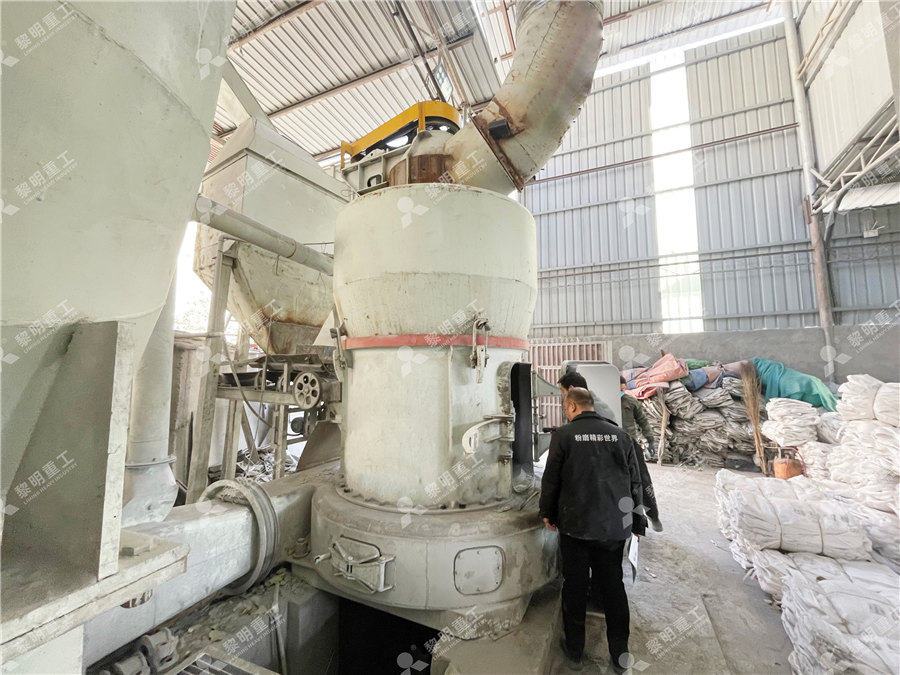
Control of Ore Loss and Dilution at AngloGold Ashanti, Iduapriem
meaningless if the preblast ore perimeters defined are not translated after blasting before excavation, to account for blast movement Therefore, ore loss and dilution can be minimised and significant increases in profit can be realised if the movement of the blast can be accurately measured Over the years, AngloGold Ashanti Iduapriem Limited 2016年2月1日 Despite the interest in investigating minetomill integration at individual gold mines (Bamber, 2008, p 5; Grundstrom et al, 2001), information on ore loss and dilution is relatively scarce as few reliable works have been documented that are applicable to conditions in South African gold mines (Onederra, 2004, p 1)Monitoring ore loss and dilution for minetomill integration in blast is not always achievable postblast, which creates inconsistencies between preand postblast ore control, including: 1 Tonnes in any polygon shape 2 Geochemistry, due to warping of the insitu shapes 3 Intended material mined, due to Blast induced Ore Movement: The missing step in achieving structure so that its axis is inclined to that of the existing borehole or tunnel If a sideways force is used, it is obtained by reaction of the drilling assembly against the wall of the hole or tunnel, and the deviation is achieved by the ability of the cutting structure to cut sideways as well as forward (Millheim and Warren, 1978; Millheim and Apostal, 1981)Drilling and Excavation Technologies for the Future

Control of ore loss and dilution blast movement
The addition of waste to ROM ore for processing as a result of blast movement lowers the overall expected mill head grade This could lead not only to poor reconciliation but also affect the 2019年11月5日 Ore dilution occurs when waste material is miscategorised as ore and sent for processing diluting the run of mine head grade and recovery Ore losses take place when valuable mineral is miscategorised as waste and sent fore excavation 3 Blast Movement preblast ore boundaries (top flitch) and timing contours Measurement and Modelling of Blast Movement to Reduce Ore The industry is always under pressure to optimise their drill and blast programs, but what impact does any change made to these programs have on the overall mining operation? Photoanalysis techniques are quick, efficient and a very Fragmentation Analysis MinBlastFrom the mining perspective, drillandblast is an excavation method for exploiting an ore deposit rather than tailoring feed size distribution for increased milling throughput Tracking and Quantifying Value from ‘Mine to Mill’ Improvement
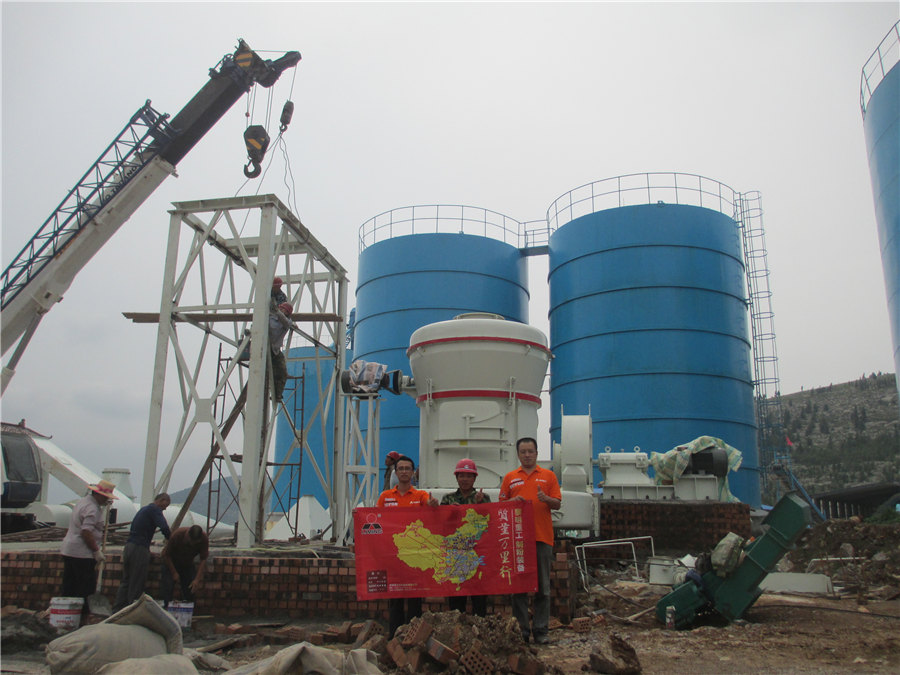
Hydraulic attachment tools in surface rock excavation
Hydraulic breakers in rock excavation Blastfree mining Secondary rock breaking Stationary boom Selective overburden Primary rock breaking Carrier weight class 5 6 Prospects for breaking and y The harder the rock is, the lower the cutter head speed should be selected y The higher the cutter head speed will be, the higher is the pick wearing2014年9月25日 This paper describes the geological investigation and observations associated with drill and blast shaft excavation and mined tunnelling for the construction of a tunnel project in Bukit Timah Geological rock face mapping and kinematics analysis for drill 2023年5月11日 Head grade The average grade of ore fed into a mill Heap leaching A process where valuable metals, usually gold and silver, are extracted from a heap of crushed ore by leaching solutions Hedging A financial strategy involving taking an opposite position in the futures market to minimize risk from price changes2024 Mining Terms Explained An Underground Miner2001年1月1日 As a result blast designs are carefully engineered to both minimise and control the direction of rock movement Traditionally blast designs in gold mines have used the minimum powder factor that will still permit rock excavation This now conflicts with the recent industry trend to optimise the total process flowsheet from the mine to the millOre Dilution Versus Mine to Mill Optimisation at KCGM
.jpg)
61 GENERAL
hand, the cyclic nature of the drill blast method requires good work site organization Blast vibrations and noise also restrict the use of drill blast in urban areas FIGURE 611 Tunneling methods in different rock/soil conditions 6 Tunneling ROCK EXCAVATION HANDBOOK 215 FIGURE 612 Range of methods compared to uniaxal compressive Understanding Mine to Mill is presented in five parts Part A – Setting the Scene provides some definitions of Mine to Mill (M2M) and the historical background A chronology of Mine to Mill developments is followed by brief descriptions of the very wide range of Mine to Mill applications which have been implemented over the last 15 yearsUNDErsTaNDINg MINE TO MILL 911 MetallurgistOre dilution occurs when waste material is miscategorised as ore and sent for processing diluting the run of mine head grade and recovery Ore losses take place when valuable mineral is miscategorised as waste and sent to the waste dumps fore excavation 3 Blast Movement preblast ore boundaries (top flitch) and timing contours Measurement and Modelling of Blast Movement to Reduce Ore Fume risk reduction The generation of nitrogen oxides within postblast gases (commonly referred to as “fume”) has become increasingly important for mines from a safety, productivity and regulatory standpoint, particularly those in Excavation Productivity
.jpg)
Maximising SAG mill throughput at Porgera gold mine by optimising blast
Semantic Scholar extracted view of "Maximising SAG mill throughput at Porgera gold mine by optimising blast fragmentation" by M Lam et al Semantic Scholar extracted view of "Maximising SAG mill throughput at Porgera gold mine by optimising blast The conditions of declining gold grade in the ore, increasing depth of excavation, 2001年9月1日 Using Blast Movement Technology, 34 movementmonitoring balls installed in 13 blastmonitoring boreholes made possible estimation of the average vertical and horizontal ore movements in the Maximising SAG mill throughput at Porgera gold mine by optimising blast Exploring the Effect of Blast Design on SAG Mill Throughput at KCGM S S Kanchibotla 1, S Morrell 1, W Valery 1, P O'Loughlin 2 ABSTRACT Traditionally blasts in mining operations are designed to prepare the insitu rock mass for excavation and subsequent transport without giving much consideration to the downstream comminution processesExploring the effect of blast design on SAG mill throughput at KCGMDrill and Blast — A Necessary Evil Or? P Bellairs1 ABSTRACT It is well documented that drill and blast outcomes affect the downstream mining processes of loading, hauling, crushing and grinding but it can also significantly impact on mine profitability via dilution, recovery percentage, lump generation (iron ore), fines generation (coal, iron Drill and Blast — A Necessary Evil Or? AusIMM
.jpg)
Pre and postblast ore polygons Download Scientific Diagram
If the targets are arranged based on the preblast ore boundary, the postblast ore boundary can be determined Up to now, sandbags (Zhang 1994;Gilbride 1995;Taylor 1995), magnetic targets 2016年11月23日 21 FullFace Excavation The following conditions affect if fullface excavation is carried out: (a) The reach of the drilling jumbos and the platforms used for support works, which limits the height and width to 7 × 11 to 11 × 18 m depending on the plant used (Figs 229, 230 for reference); (b)Introduction to Underground Excavation by Drilling and BlastingOre is further transferred from this drift level to main level using chute Once the development work for sublevel stoping is over, the final excavation of the ore starts Initially, a slot is opened either in the middle of the orebody or on one side of the orebody The excavation starts from this slot and retreats towards the drivagesOverview of Underground Metalliferous Mining SpringerLinkMine to mill, blast optimisation, ore characterization MINE TO MILL METHODOLOGY In most metal mining operations, insitu ore is separated from waste rock and is subjected to a • Blasting to prepare the ore for excavation, transportation and subsequent crushing and grindingMINE TO MILL OPTMISATION AT PADDINGTON GOLD OPERATIONS
.jpg)
(PDF) Advanced vibration management to improve productivity
PDF On Jan 1, 2016, Mukherjee Debashish and others published Advanced vibration management to improve productivity and optimize cost for excavation of iron ore: A case study Find, read and Mine to mill, blast optimisation, ore characterization MINE TO MILL METHODOLOGY In most metal mining operations, insitu ore is separated from waste rock and is subjected to a • Blasting to prepare the ore for excavation, transportation and subsequent crushing and grindingMINE TO MILL OPTMISATION AT PADDINGTON GOLD Blast Material (%) 650 mm Remarks Shot 1 4226 9918 082 Good Blast Performance Shot 2 2832 8682 1318 Poor Blast Performance Shot 3 2172 8469 1531 Poor Blast Performance Shot 4 5345 100 0 Excellent Performance Combined 321 9012 988 Good Blast Performance Citation: Gyamfi S and Afum BO (2021) Rock Fragmentation Evaluation towards BlastToMill Concept of Blast Benchmark drill and blast and mechanical excavation advance rates for underground hardrock estimated total volume of insitu material blasted using the proposed blast parameters increased by 143 to 500% for ore zones and 125 to 500% for waste zones over current Various None or Grippers Full Face Rotating Cutting Head Benchmark drill and blast and mechanical excavation advance
.jpg)
MODELLING FINES IN BLAST FRAGMENTATION AND ITS IMPACT
ROCK / ORE CHARACTERISATION The characterisation of rock /ore is of fundamental importance for the design and optimisation of any mine to mill process Characterisation of ore for blasting will be different from that for crushing and grinding operations For example, the rock mass structure in addition to its2001年1月1日 As a result blast designs are carefully engineered to both minimise and control the direction of rock movement Traditionally blast designs in gold mines have used the minimum powder factor that will still permit rock excavation This now conflicts with the recent industry trend to optimise the total process flowsheet from the mine to the millOre Dilution Versus Mine to Mill Optimisation at KCGM2017年8月12日 Threedimensional measurement of movement at midbench locations in blasts identified potential ore loss of up to 20%, dilution of 12% and misclassification (ie Lowgrade ore unintentionally Minimizing Mining Dilution, Ore Loss, and Misclassification by Blast induced ore loss and dilution was controlled by adjusting the ore blocks for blast movement Adiyansyah, B, Kennelly, L, Sellers, E J and Kanchibotla, S S, 2015 Optimisation of drill and blast for mill throughput improvement at Ban Houayxai Mine, in Proceedings 11th International Symposium on Rock Fragmentation by Blasting, Optimisation of Drill and Blast for Mill Throughput AusIMM
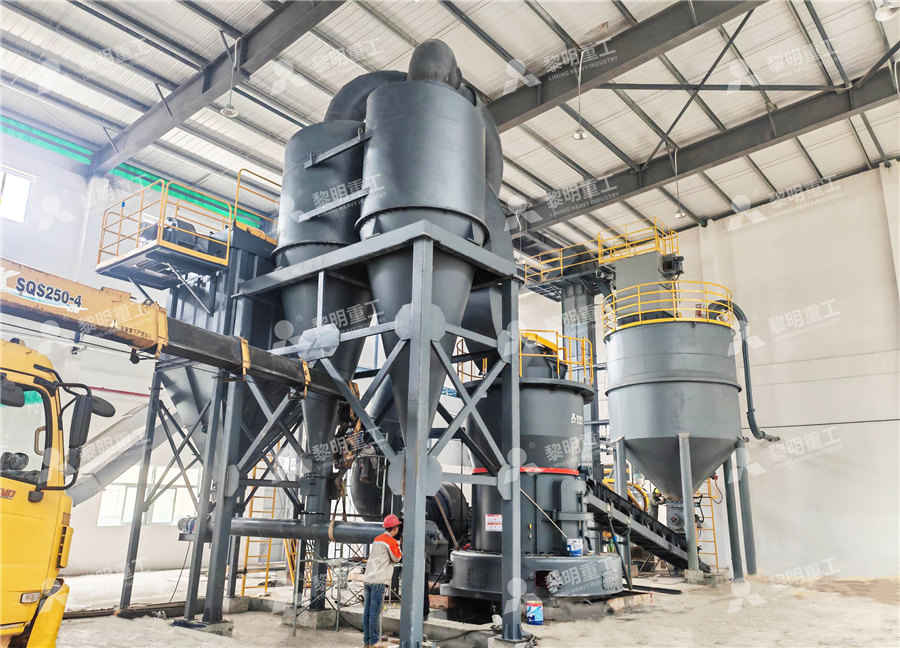
Minimizing Mining Dilution, Ore Loss, and Misclassification in
2018年9月24日 Blast B and Blast C: • Cost of dilution (waste sent to the mill) is ignored • Grade of Ore polygons are unknown so only tonnages and percentages calculated • Density = 27 t/m3 Summary A 911 Metallurgist can enter the scene and see what you have become blind to We can fix issues in ways you never thought possible Our fresh eyes will open new opportunities for your plant Each mineral processing plant has varied ore types, mining equipment, (crusher, ball mill, flotation, tailings), and management (operating) philosophyThe evaluation and prioritization of variables Metallurgists Mineral Processing Engineers 911Metallurgist