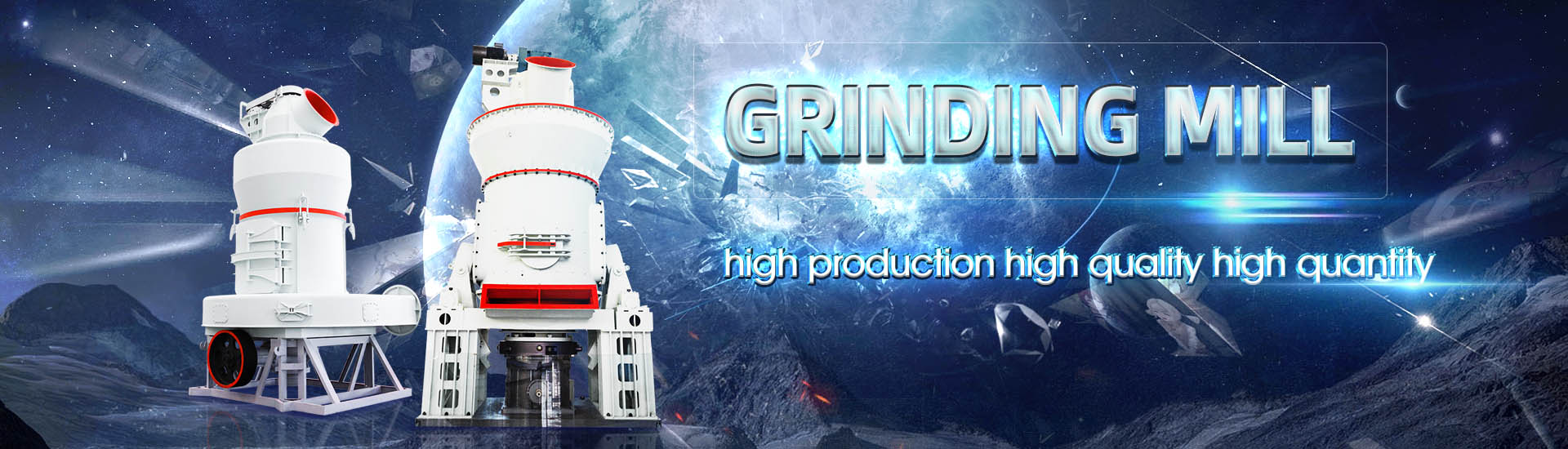
2 6x13 ball mill output
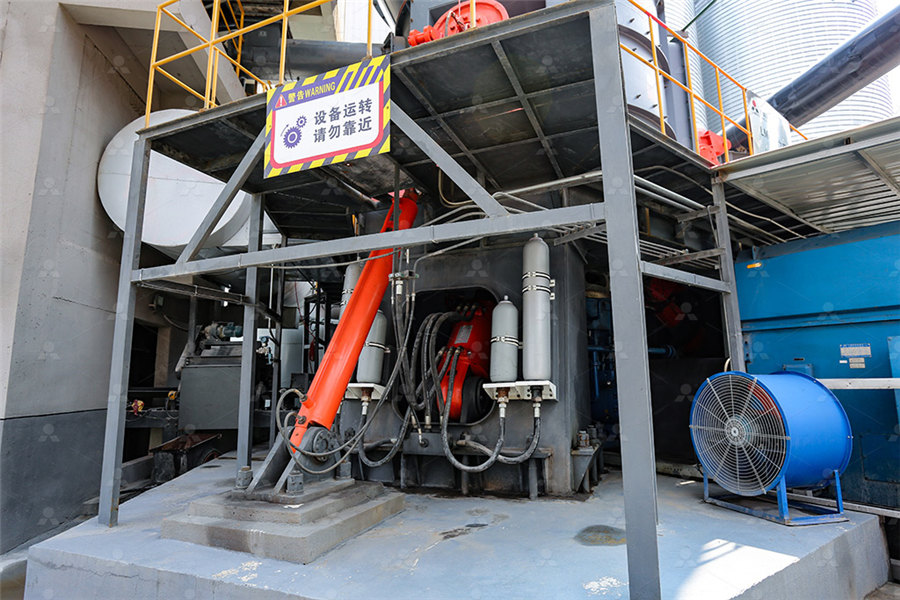
Calculate and Select Ball Mill Ball Size for Optimum Grinding
2013年8月3日 In Grinding, selecting (calculate) the correct or optimum ball size that allows for the best and optimum/ideal or target grind size to be achieved by your ball mill is an important MILLING/SOLID MILLING/BALL NOSE/9192 Back EXOCARB CBNLNSXB Maximum Performance CBN Ball Mills for Hardened Steels over 55Rc EDP: R02 x 3MM x R02 x 3MM x 4MM EXOMAX CBN OSG USA, Inc2023年10月1日 The Bond ball mill work index is an expression of the material’s resistance to ground and a measure of the grinding efficiency The test is a standardized methodology that ends when a circulating load of 250% is obtained In this paper, a new method based on the Population Balance Model (PBM) is proposed and validated to estimate the results Estimation methodology for Bond ball mill work index experiment output small stage ball grinding provides a comparative analysis of a wide range of ore processing steps and requires 515% energy in a selfgrinding mill [3] 1 Figure 2 Ball mill process control system using ACS (Adaptable Control System) Figure 2 shows that the input and output signals depend mainly on the mill and the hydrocyclone SomeControl of ball mill operation depending on ball load and ore
.jpg)
High Efficiency and Large Output Cement Ball Mill
Motor: The motor is the power source that drives the mill; Bearings: These components support the mill shell and allow it to rotate; Lining plates: The mill shell interior is often lined with replaceable plates to protect it from wear due 2015年6月19日 The basic parameters used in ball mill design (power calculations), rod mill or any tumbling mill sizing are; material to be ground, characteristics, Bond Work Index, bulk density, specific density, desired mill tonnage capacity DTPH, operating % solids or pulp density, feed size as F80 and maximum ‘chunk size’, product size as P80 and maximum and finally the type of Ball Mill Design/Power Calculation 911MetallurgistAnalysis of the efficiency of the grinding process in closed circuit ball mills Valery I Telichenko1, Rashid R Sharapov1*, Svetlana YLozovaya2 and Vladimir ISkel1 1Moscow State University of Civil Engineering, Moscow, Russia 2Belgorod State Technological University named after VG Shukhov, Belgorod, Russia Abstract Ball mills for fine grinding cement clinker and additives areAnalysis of the efficiency of the process in closed circuit ball mills2016年2月14日 Do you need a quick estimation of a ball mill's capacity or a simple method to estimate how much can a ball mill of a given size (diameter/lenght) grind for 911 Metallurgist is a trusted resource for practical insights, solutions, and support in mineral processing engineering, helping industry professionals succeed with proven expertise Small Ball Mill Capacity Small Ball Mill Capacity Sizing Table 911Metallurgist
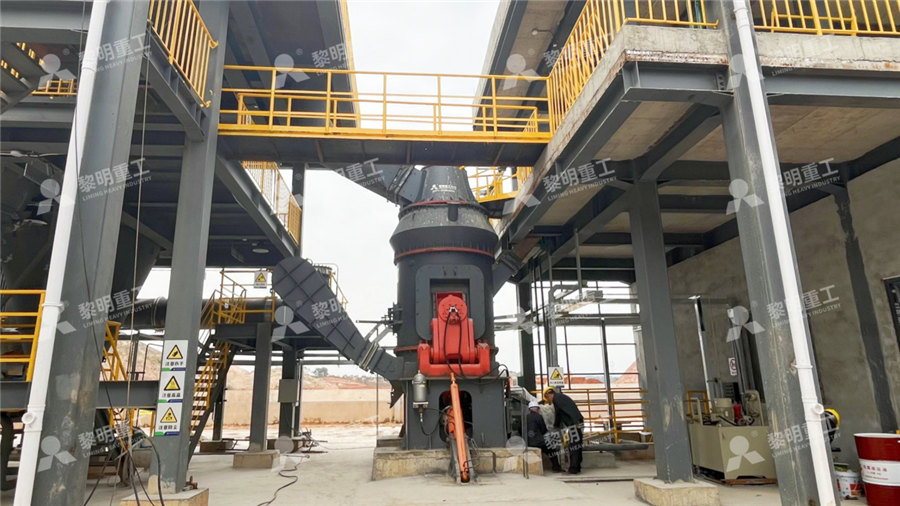
(PDF) Control of ball mill operation depending on ball load and
2023年12月12日 PDF Ball mills are used for the second stage of ore grinding in mining operations by proportioning ore piles and rolling energy were considered as the most important model output variables2012年12月1日 Mod 1 Mod 2 Mod 1 Mod 2 Mod 1 Mod 2 Mod 1 Mod 2 Mod 1 Mod 2 Regression 1354 216 5 4 271 054 452 675 439 412 Residual 365 046 6 7 061 007 – – – –(PDF) Optimization of inmill ball loading and slurry solids 2019年10月19日 Ball mills are extensively used in the size reduction process of different ores and minerals The fill level inside a ball mill is a crucial parameter which needs to be monitored regularly for optimal operation of the ball mill In this paper, a vibration monitoringbased method is proposed and tested for estimating the fill level inside a laboratoryscale ball mill A vibration Monitoring the fill level of a ball mill using vibration sensing and 2013年7月15日 PDF The ball mill in closed circuit with hydrocyclones is an industry standard, and well known methodologies exist for equipment sizing, selection and (PDF) Energy Efficient Ball Mill Circuit – Equipment Sizing

System dynamics model of output of ball mill
2021年2月15日 of double inlet and double outlet ball mill output system is established, and SPSS is used to fit the model data with the real data The fitting degree is above 08, Download Table Ball mill characteristics and test conditions Mill Diameter, D (cm) 204 Length, L (cm) 166 Volume, V (cm 3 ) 5,423 Operational speed, Ν (rpm) 66 from publication Ball mill characteristics and test conditions Mill This document provides instructions for installing a 16x22ft, 2800kW ball mill It outlines 8 key steps: 1) Prepare the foundation and install the trunnion bearing sole plates 2) Assemble and mount the trunnion bearings onto the sole 16' X 22' Ball Mill Installation ManualInternational Journal of Advances in Mechanical and Civil Engineering, ISSN: 23942827 Volume2, Issue5, Oct2015 Increasing Output Of Cement Grinding In Ball MillCase Study 5 INCREASING OUTPUT OF CEMENT GRINDING IN BALL MILLCASE STUDY 1MOHAN SINGH PANWAR, 2AJAY KUMAR BANSAL, 3HEMANI PALIWAL 1Student, 2Guide, 3External GuideINCREASING OUTPUT OF CEMENT GRINDING IN BALL MILL

6 Reasons Why Output of Ball Mill Decreases
2019年4月25日 3 Not added the steel ball in time The grinding effect and output of the ball mill are restricted by the steel ball in the ball mill But the steel ball might have wears with the grinding and impact of the cylinder body, so it is necessary to add the steel ball timely, which can maximize the output of the ball mill 4Output: 10 t/h 20 t/h Ball mill is common used grinding plant in the industry, and it is key equipment used for milling after materials are crushed This machine can be can grind all kinds of ores and other materials, which Compare this product Remove from Ball mill, Ball grinding mill All industrial manufacturersRotational speed: 150 rpm 740 rpm Output: 200 kg/h 186,000 kg/h Motor power: 22 kW 1,250 kW overflow of the pulp from the discharge end The overflow type ball mill is a new type of ball mill equipment with simple structure and selfflow discharge of ore It Ball mill, Ball grinding mill All industrial manufacturers Page 2• De = 25 mFind: required maximum ball size – F80 – Maximum ball size (mm) Mill performance test Steps 1 Recording of related operational data 2 Air flow measurement 3 Crash stop and visual inspection in mill 4 Sampling in mill 5 Evaluation of test 1 Recording of related operational dataTube MillCement Separator Ball Mill Optimization
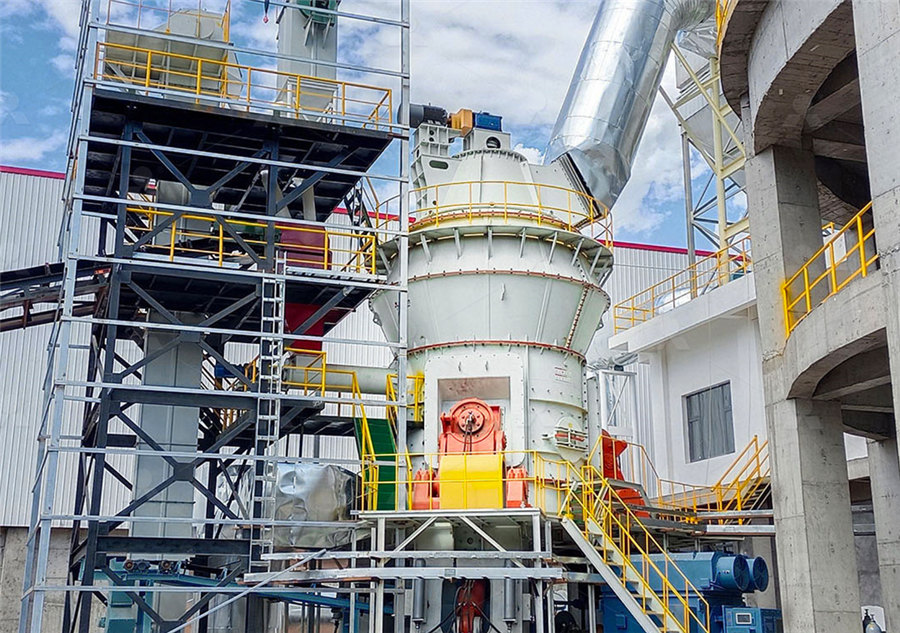
TECHNICAL SPECIFICATION OF WET BALL MILL EQUIPMENT
TECHNICAL SPECIFICATION OF WET BALL MILL EQUIPMENT (SUB ASSEMBLY OF FGD SYSTEM) 03 18032022 P V S BABU AMAN KHRK 02 02072021 P V S BABU AMAN KHRK 01 2007 420 mA output signals from transmitters/other control system shall be able to drive minimum 500 Ohms load resistance2023年12月28日 The safety factor is low, the service life is short, etc, and these will inevitably affect the continuous production of the ball mill Therefore, the overall performance of the ball mill is better 3 The ball mill is of good quality The better the quality of the ball mill, the more stable the performance of the ball mill will be during Factors Affect The Output and Quality of Ball Mills And How to 2017年2月13日 2) Ball milling – a ball mill with a diameter of 244 meters, inside new liners, grinding wet in open circuit When the grinding conditions differ from these specified conditions, efficiency factors (Rowland and Kjos, 1978) have Ball Mills 911MetallurgistBall mills can be divided into center drive ball mills and edge drive ball mills according to different transmission modes Φ46x13 125~130 149 242 4800 465 Φ46x14 140~150 145 255 the output of the closedcircuit production is relatively large, Center drive ball millBall millPRODUCTTongli Machinery
.jpg)
Ball Mills For Sale Machinery Equipment Co
Machinery and Equipment Company buys and sells used Ball Mills our inventory and request a quote Buy Equipment; Sell Equipment; Can't Find? Financing ; Upcoming Auctions; Contact Us +1 (415) 4673400 Mill Type Overview Three types of mill design are common The Overflow Discharge mill is best suited for fine grinding to 75 – 106 microns; The Diaphram or Grate Discharge mill keeps coarse particles within the mill for additional grinding and typically used for grinds to 150 – 250 microns; The CenterPeriphery Discharge mill has feed reporting from both ends and the product AMIT 135: Lesson 7 Ball Mills Circuits – Mining Mill Operator 2013年8月3日 In Grinding, selecting (calculate) the correct or optimum ball size that allows for the best and optimum/ideal or target grind size to be achieved by your ball mill is an important thing for a Mineral Processing Engineer AKA Metallurgist to do Often, the ball used in ball mills is oversize “just in case” Well, this safety factor can cost you much in recovery and/or mill liner Calculate and Select Ball Mill Ball Size for Optimum GrindingJ Control Theory Appl 2013 11 (3) 454–462 DOI 101007/s1176801312103 Intelligent optimal control system for ball mill grinding process Dayong ZHAO 1†, Tianyou CHAI,2 1State Key Laboratory of Synthetical Automation for Process Industries, Northeastern University, Shenyang Liaoning , China;Intelligent optimal control system for ball mill grinding process
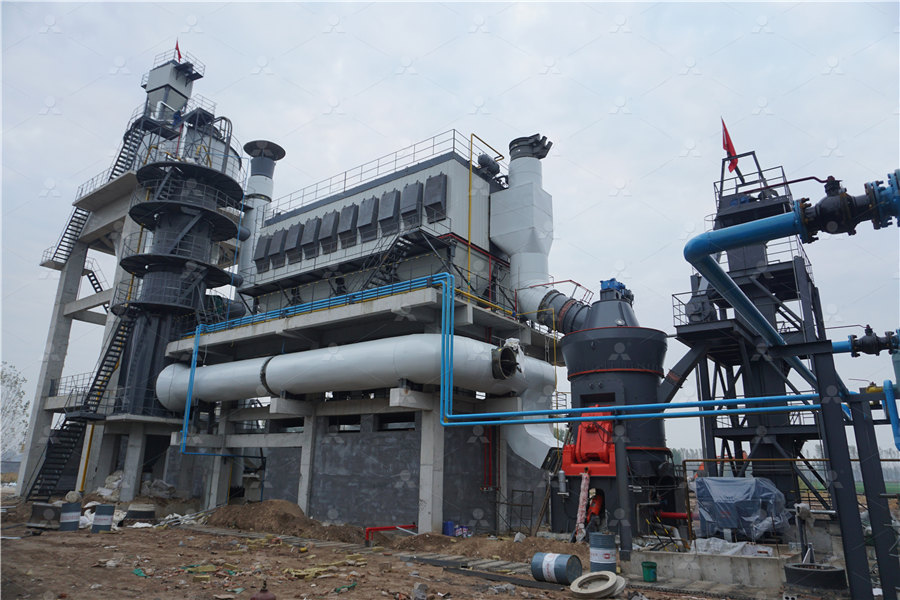
(PDF) Performance optimization of an industrial ball mill for
2017年1月1日 An increase of over 10% in mill throughput was achieved by removing the ball scats from a single stage SAG mill These scats are non spherical ball fragments resulting from uneven wear of balls 2023年2月15日 A beneficiation plant in Singapore loads balls into a ϕ 1500mm×3000mm wet grid type ball mill, determines the filling rate ϕ = 50%, and selects cast steel grinding balls δ = 45 t/m 3 The ball mill processes the mediumhard ore 1 See Table 1 for the sieving analysis results of all the ore samples from a ball mill Table 1Method of Steel Grinding Ball Proportioning and Example2015年10月15日 A) Total Apparent Volumetric Charge Filling – including balls and excess slurry on top of the ball charge, plus the interstitial voids in between the balls – expressed as a percentage of the net internal mill volume (inside liners) B) Overflow Discharge Mills operating at low ball fillings – slurry may accumulate on top of the ball charge; causing, the Total Charge Calculate Ball Mill Grinding Capacity 911MetallurgistChemical process industries are running under severe constraints, and it is essential to maintain the endproduct quality under disturbances Maintaining the product quality in the cement grinding process in the presence of clinker Predictive Controller Design for a Cement Ball Mill
.jpg)
Grinding in Ball Mills: Modeling and Process Control
2012年6月1日 PDF The paper presents an overview of the current methodology and practice in modeling and control of the grinding process in industrial ball mills Find, read and cite all the research you 2013年4月1日 For a closed circuit ball mill flowsheet as represented in Figure 2, a simplified relationship (Equation 1) for relative capacity at different circulating load and classification efficiencies was Closed circuit ball mill – Basics revisited Request PDFDry and wet ball mills have the same basic components, but there are some structural differences: 1 Partition The dry ball mill is doublewall or three partitions The wet ball mill is singlewall partition 2 Feeding device Dry ball mill: drum feeder, feed hopper, combined feeder Wet ball mill: feed hopper, combined feederBALL MILL FOR ALL YOUR NEEDS FTM Machinery2023年2月15日 High temperature of the ball mill will affact the efficiency 3 For every 1% increase in moisture, the output of the ball mill will be reduced by 8% 10% 4 when the moisture is greater than 5%, the ball mill will be unable to perform the grinding operation 5 The bearing of the ball mill is overheated and the motor is overloaded Reasons17 Signs of Problems with Ball Mills: Quickly Remove Hidden Troubles

15 x 21 batch ball mill Custom Laboratory and Pilot Plant
2018年8月15日 Mill Type: 15 inch diameter by 21 inches long, 304 stainless steel batch ball mill Total Mill Volume: 155 Gallons Mill Operating Speed: 51 RPM Mill Ball Charge: 250 pounds of chrome steel grinding balls (Not Included with Mill) FOUNDATION The mill foundation must be rigid to eliminate vibration and any tendency to sway With suitable2020年8月10日 Make the base The wooden base will serve as the support for the ball mill It can be made by resting the wooden platform on top of the two 1”x10”x4” (254cm x 254 cm x 1016 cm) pieces of woodHow to Make a Ball Mill: 12 Steps (with Pictures) wikiHow2017年7月26日 The finer you crush, the higher your ball mill tonnage and capacity will be 911 Metallurgist is a trusted resource for practical insights, solutions, As a result, the mill output will increase with this reduced size to approximately 77,000 tons per day The gain in production compared to the 13,000 micrometer feed will be:How Ball Mill Ore Feed Size Affects Tonnage CapacityBall mills and grinding tools Cement ball mills are typically twochamber mills (Figure 2), where the first chamber has larger media with lifting liners installed, providing the coarse grinding stage, whereas, in the second chamber, medium and fine grinding is carried out with smaller media and classifying linersBALL MILLS Ball mill optimisation Holzinger Consulting
.jpg)
Energy and exergy analyses for a cement ball mill of a new
2020年5月1日 Cement industry consumes a huge amount of electrical energy that is about 100 kWh/t (kWh per ton (10 3 kg) of cement) [16]In a cement plant, about twothirds of the total electrical energy is used for particle size reduction of raw materials and clinker [17]There is a diverse range of options to decrease the production expenses as well as CO 2 emissions that