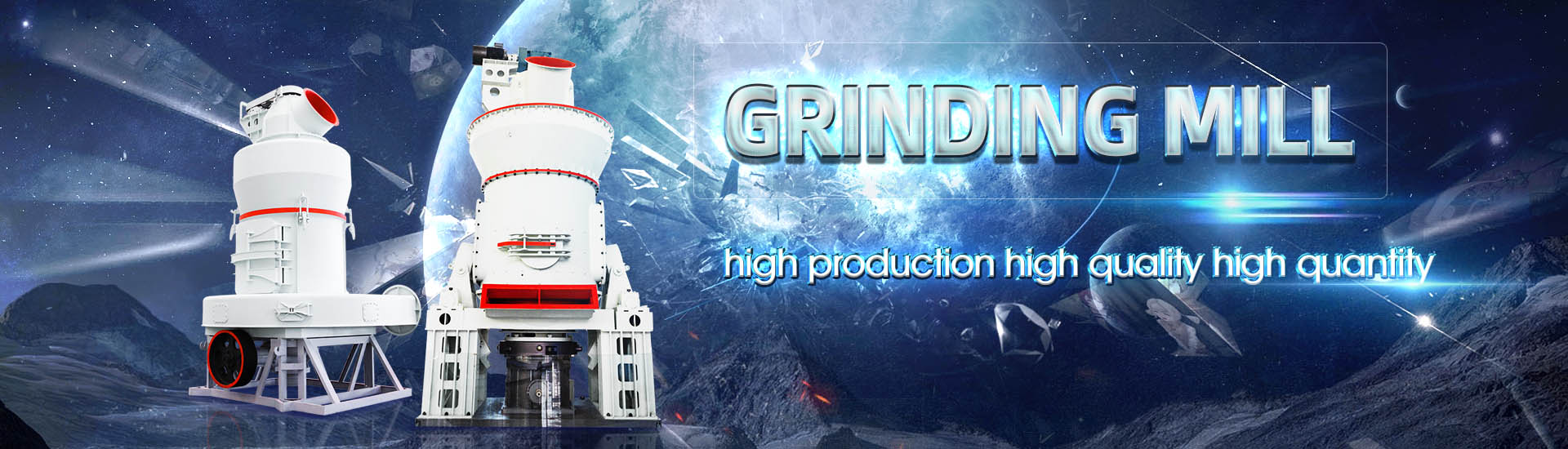
Cement plant uses limestone process flow
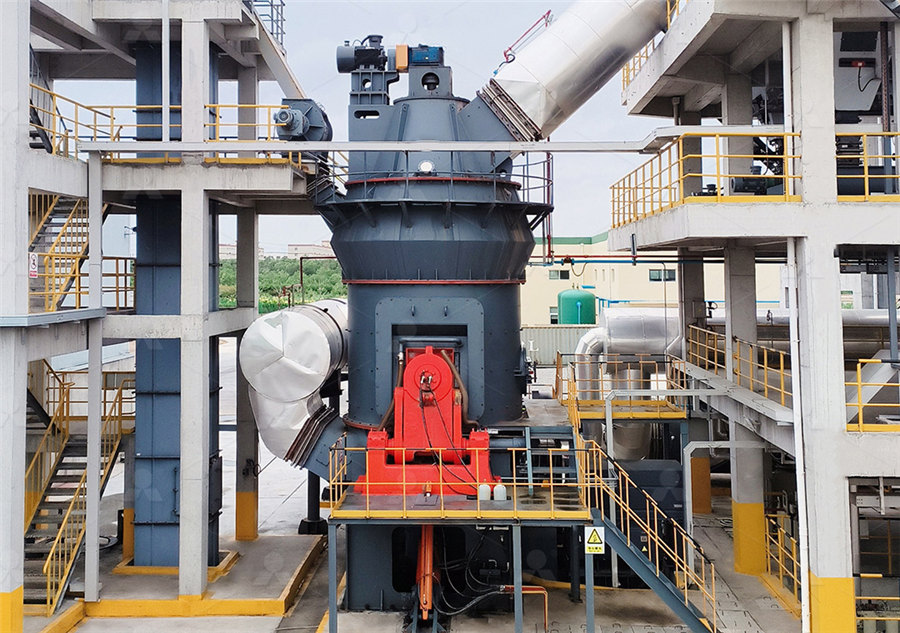
Limestone Quarrying and Processing: A LifeCycle Inventory
Process flow diagram for limestone processing operations Processing commences with transportation of the (raw) stone from the quarry to the processing facility, as depicted by Figure 2The crushed limestone and aggregates such as sand, clay and ironstone are blended together in a raw mill to a particle size of 90 micrometres, producing “kiln feed” Cement Plant: The Cement Plant: The Manufacturing Process 4 5 World Cement Cement plants basically consist of three manufacturing parts: (i) raw material and fuel supply preparation, (ii) clinker production (commonly named as the pyroprocessing part), and (iii Cement manufacturing from the quarrying of limestone to the 2024年9月15日 This paper proposes a new cement process (NCP) that uses natural gas to react with limestone to reduce CO 2 emissions and simultaneously produce highvalueadded Conceptual design and lifecycle environmental and economic
.jpg)
ZeroCAL: Eliminating Carbon Dioxide Emissions from Limestone’s
While there is a substantial demand for a finite albeit fastgrowing supply of renewable energy, electrification allows a means for decarbonizing cement production while using Ca(OH) 2 as a 2023年12月20日 Cement manufacturing is a complex process that begins with mining and then grinding raw materials that include limestone and clay, to a fine powder, called raw meal, which is then heated to a sintering temperature as The Cement Manufacturing Process Thermo Fisher Abstract—A long term production planning of limestone quarry is presented to supply consistent quantity and quality of limestone to a cement plant A case study from Indian cement industry Limestone Quarry Production Planning for Consistent Supply of Portland cement clinker was first made (in 1825) in a modified form of the traditional static lime kiln [2] [3] [4] The basic, eggcup shaped lime kiln was provided with a conical or beehive shaped extension to increase draught and Cement kiln Wikipedia
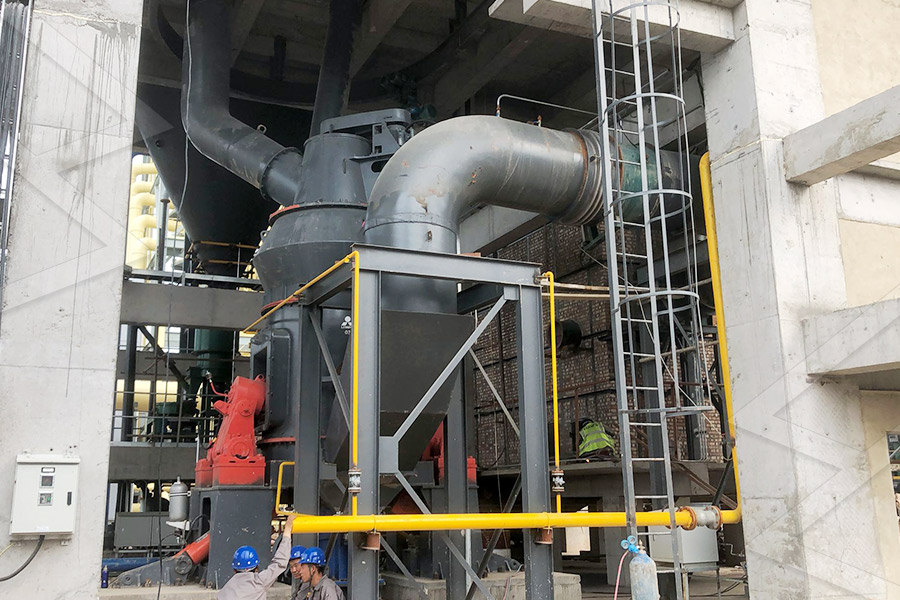
Cement Manufacturing Process and Its Environmental
2023年7月10日 The cement manufacturing process involves the extraction and processing of raw materials, such as limestone, clay, and shale, which are then heated in a kiln at high temperatures to form clinkerconstitute the core of a portland cement plant marl, seashells, aragonite, and an impure limestone known as "natural cement rock" Typically, these raw materials are obtained from openface quarries, but underground mines or dredging operations are Process flow diagram for portland cement manufacturing 1164 EMISSION FACTORS 11 116 Portland Cement Manufacturing US Environmental 2014年6月10日 This document discusses Portland cement and the cement manufacturing process It begins with an overview of what cement is and how it is used to make concrete It then describes the industrial process for manufacturing cement, involving grinding raw materials like limestone and clay at high temperatures in a kiln to form clinker, which is then pulverized with Cement manufacturing process PPT Free Download SlideShareClinker is the intermediate product used in the manufacturing of cement There are two primary processes used to manufacture clinker: the dry process and the wet process Our plants use the dry process, which is more energy efficient In the wet process, the raw materials are mixed with water to form slurry, which is fed into a kilnProduction Process CEMEX Philippines
.jpg)
Simulation and Optimization of an Integrated Process Flow Sheet
2021年3月9日 In this study the process flow diagram for the cement production was simulated using Aspen HYSYS 88 software to achieve high energy optimization and optimum cement flow rate by varying the flow rate of calcium oxide and silica in the clinker feed Central composite Design (CCD) of Response Surface Methodology was used to design the ten experiments for on its intended use Portland cement is used primarily to make concrete, mortar, and grout Types of Portland Cement • Type I For use when the special properties specified for any other type are not required • Type IA Airentraining cement for the same uses as A practical guide to improving cement manufacturing processes 2018年5月31日 This type of deposit cannot be utilized for cement manufacturing process without blending with high grade limestone About 97 per cent of Limestone is used in Cement Industry, 3 per cent in other industries like Iron and Steel and Chemical Hence major consumer for limestone is cement industryThe Limestone Challenge Indian Cement ReviewThe crushed limestone and aggregates such as sand, clay and ironstone are blended together in a raw mill to a particle size of 90 micrometres, producing “kiln feed” Cement Plant: The Manufacturing Process worldcementassociation 1 Limestone (CaCO3) is taken from a quarry 2 4 3 The limestone is fed into a crusher and then stored until neededCement Plant: The Manufacturing Process 4 5 World Cement

Cement Production an overview ScienceDirect Topics
Uses of alternative fuels and raw materials in the cement industry as sustainable waste management options Alfonso Aranda UsónAna M LópezSabirónGermán FerreiraEva Llera Sastresa, in Renewable and Sustainable Energy Reviews, 2013 21 Worldwide production One of the wellknown characteristics of cement production is that cement plants are not uniformly 15 Cement plant construction and valuation 244 1 New plant construction – 2 Project management – 3 Cement plant investment costs – 4 Project phases – 5 Plant valuation Section B – Process calculations and miscellaneous data B1 Power 262 1 Specific power consumption 2 Power conservation – 3 Threephase power – 4The Cement Plant Operations Handbook International Cement Finally, during the cement grinding and distribution process, firstly the cooled clinker is ground with around 5% of gypsum and other 17 JRTE2020 cementitious materials to form the final cement Typical cement manufacturing process flow Our product process is supported by strict process and product quality control A passion for accuracy ensures that the line of operations in our plant is at par with strict local and international standards The process uses high grade limestone that in return gives us high grad Ordinary Portland Cement (OPC)Process :: Maruti Cement
.jpg)
The Cement Manufacturing Process
2017年8月15日 Cement is used in mortar (to bind together bricks or stones) and concrete (bulk rocklike building material made from cement, aggregate, sand, and water) By modifying the raw material mix and the temperatures utilized in manufacturing, compositional variations can be achieved to produce cements with different properties2024年1月11日 Limestone Sand Making Plant Flow Limestone enters the primary jaw crusher for coarse crushing The crushed material enters a belt conveyor and goes to a fine jaw crusher(impact crusher or hammer crusher) for further crushing After crushing, the material enters a vibrating screen to separate two types of stonesLimestone Crushing And SandMaking Plant Eastman Rock Limestone powder is widely used in electric power, metallurgy, cement, chemical industry, building materials, coatings, papermaking, rubber, medicine, food, and other fields, and has broad market prospects The process flow of the limestone grinding production line mainly includes the following steps:Limestone Grinding Mill Plant TAYMACHINERYThe major raw materials used in the manufacture of cement are Calcium, Silicon, Iron and Aluminum These minerals are used in different form as per the availability of the minerals Table shows the raw materials for Portland cement manufacture The mixing procedure of the manufacture of cement is done in 2 methods, Dry process; Wet process; a Manufacture of Cement Materials and Manufacturing Process of
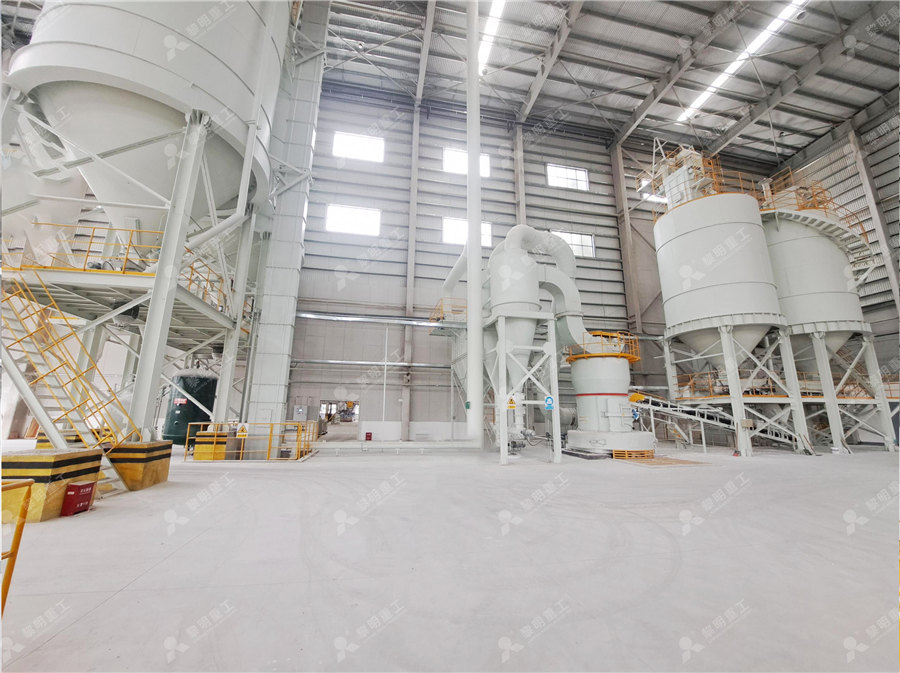
The Use of Limestone in Portland Cement: A StateoftheArt
2003年6月5日 Required water:cement ratio to achieve a slump of 60 to 70 mm in concretes made with different cements Cement E contained a limestone not conforming to the EN 1971 criteria2015年9月17日 6 00 Limestone Quarry and Crushing plant The major raw material for cement production is limestone The limestone most suitable for cement production must have some ingredients in specified quantities ie, calcium carbonates, silica, alumina, iron,etc Belt Conveyors The quarried raw material is transported to the cement plant, using mechanical conveying Cement Production Process PPT SlideShareLimestone (calcite, CaCO3) is an abundant and costeffective source of calcium oxide (CaO) for cement and lime production However, the thermochemical decomposition of limestone (∼800 °C, 1 bar) to produce lime (CaO) results in substantial carbon dioxide (CO2(g)) emissions and energy use, ie, ∼1 tonne [t] of CO2 and ∼14 MWh per t of CaO produced Here, we describe a new ZeroCAL: Eliminating Carbon Dioxide Emissions from Limestone’s 2023年11月1日 Assuming an average limestone quality in a cement plant and an average recycled Schematic flowsheet of a multistage grinding plant for the production of Portlandcements He, SG Nodeland, T Cantero, Pilot demonstrationreporting on CO 2 capture from a cement plant using hollow fiber process, Energy Procedia 114 The cement plant of tomorrow ScienceDirect
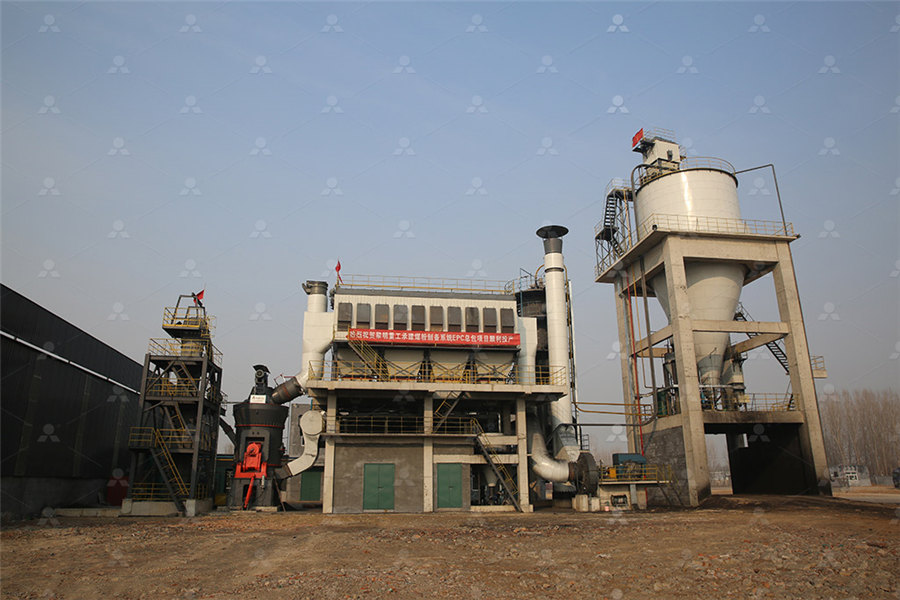
CEMENT PLANT Project Report Manufacturing
2018年1月15日 We can modify the project capacity and project cost as per your requirement If you need any customized project report and BANKABLE project reports as per your requirement, Click here to CONTACT US Or Call us at +91 2023年5月27日 In which industry is limestone mainly used? The answer is the cement industry Limestone plays two major roles in the cement manufacturing process, one is used as a raw material for cement clinker, and the other is 2 Major Roles of Limestone in Cement ManufacturingManufacturing process flow 1 Quarrying and Crushing The quarry (where the mining activity is performed) is located 07 km away from the plant and has the main raw materials such as Limestone and shale that is estimated to last for 100 years, the other raw materials (Iron ore, silica sand, gypsum and Pozzolana (pumice) ) are brought from nearbyManufacturing process flow 1 Quarrying and Crushing Messebo Cementelectricity use A process flow diagram for the calcination process or cement clinker burning process for the plant is shown in Fig 1 22 Process Design for the Capture System using Aspen Hysys Flue gas from Ashaka Cement Plant is usually emitted through the stack into the atmosphere at a temperature of 180ºC The flue gas prior toTechnical Evaluation of SelexolBased CO Capture Process for a Cement Plant
.jpg)
(PDF) Process Automation of Cement Plant ResearchGate
2012年4月30日 Plant Process Flow Diagram 2 Normally there are various types of lime stone quarry so the qualit y of limestone does not dry process cement plant situated at Jayanthipuram, Andhra 2016年1月20日 All cement types contain approximately 4–5% gypsum to control the setting time of the product Other mineral components such as slag, power plant fly ash, limestone, and other materials are used to replace clinker to produce blended cement The process of cement grinding is shown in supplementary materialAnalysis of material flow and consumption in cement production process Download scientific diagram Process flow sheet of a CAP process integrated in a cement plant (adapted from [46]) from publication: CO2 Capture, Use, and Storage in the Cement Industry: State of Process flow sheet of a CAP process integrated in a cement plant 2021年3月9日 In this study the process flow diagram for the cement production was simulated using Aspen HYSYS 88 software to achieve high energy optimization and optimum cement flow rate by varying the flow Simulation and Optimization of an Integrated Process Flow Sheet
.jpg)
Cement Industry in Sri Lanka JRTE
2020年1月2日 The flow diagram of a typical cement manufacturing process is shown in Fig 1 [3] Finally produced cement is transported in bags (packages) or as a bulk powder Table 1 shows the cement manufacturing subprocesses ongoing in Sri Lanka [2] Fig 1 Cement manufacturing process flow diagram [3] Table 1 Sri Lanka’s Cement Manufacturing sub 2015年12月9日 Raw materials are used to produce the main cement elements (Mohsen, 2015) • Quarry The process of obtaining raw materials for cement manufacturing involves mining and quarrying natural materials (PDF) Cement Manufacturing ResearchGate2024年9月10日 The dry process is the most commonly used Cement manufacturing process today due to its energy efficiency Here is a stepbystep procedure for the dry process of Cement manufacture: Quarrying and Cement Manufacturing Process: Know Extraction, How can I start a cement manufacturing plant? Starting a cement factory involves several crucial steps: Determine the scale of production and type of cement to be produced Choose an optimal location for the cement plant Design the layout StepbyStep Guide to the Manufacturing of Cement
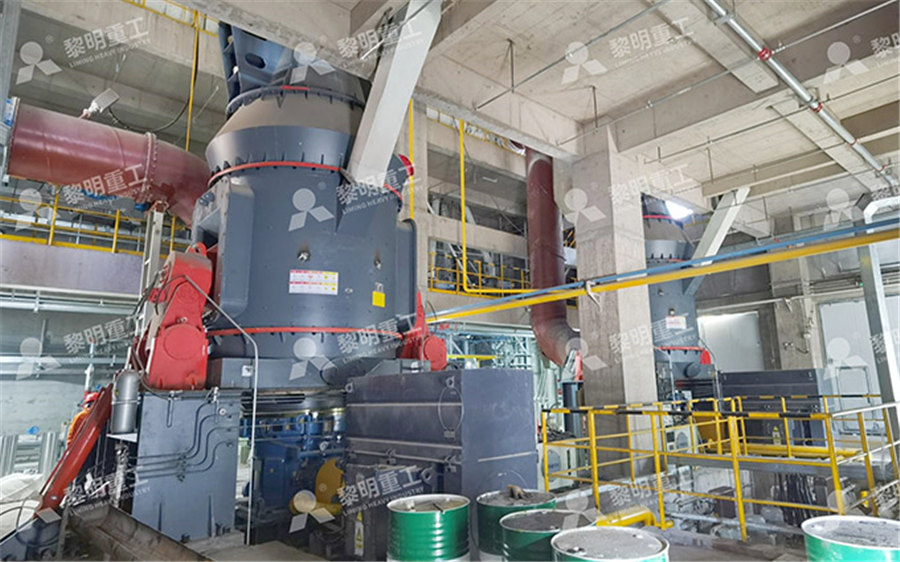
BASIC CEMENT PLANT LAYOUT – Process Cement Forum The Cement
2020年7月4日 Map Key 00 Limestone Quarry and Crushing plant 01 Limestone Stockpile 02 Additives Hopper 03 Additives Storage 04 Process Cement Forum Last Post by lisa 5 years ago 2 and drying plants, finishing mills, and raw mills through water injection Through ESPs, the dustladen gas is made to flow through a chamber usually 2019年8月27日 The major raw materials used as a source of CaO for cement manufacturing are limestone, chalk, marl, etc These raw materials by virtue of their natural occurrence contains other mineral impurities eg, MgO, SiO 2, Al 2 O 3, Fe 2 O 3, alkali compounds, and sulfidesThese impurities play an important role to influence the cement manufacturing Cement Manufacturing and Process Control SpringerLink2015年8月1日 This cement plant operates on a dry process line with a fi vestage suspension preheater and an inline precalciner The kiln is 4 m in diameter and 60 m in lengthAnalysis of material flow and consumption in cement production processThe cement sector faces a unique challenge in decarbonizing operations because the CO2 emitted originates from the use of fossil fuels in the hightemperature calcination step (∼40% emissions Stages in cement production flow chart [43] ResearchGate
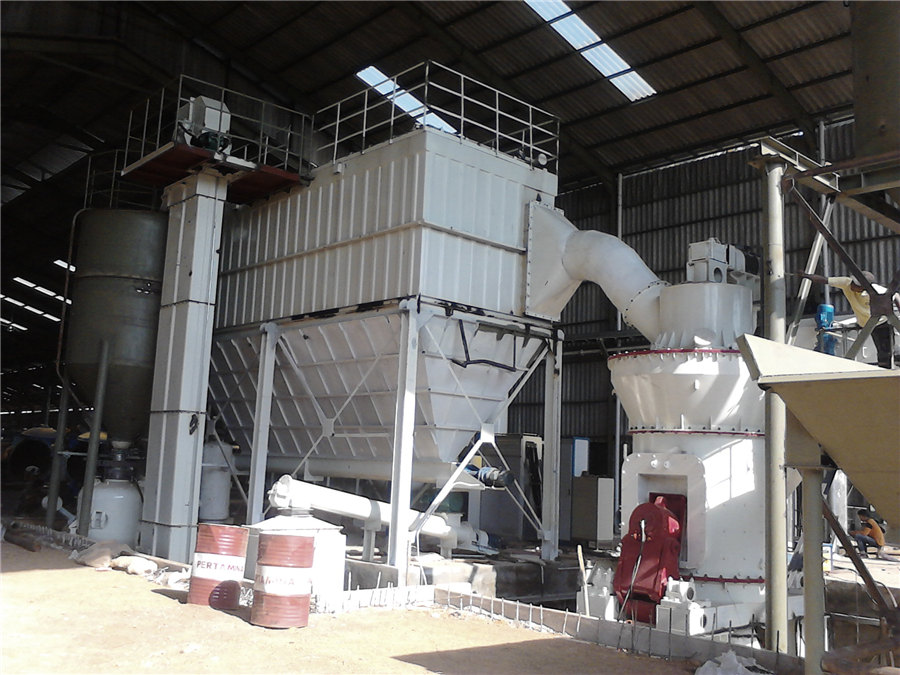
ShapedByConcrete – How Cement is Made
During this process, cement manufacturers have been a leader in the use of alternative fuels to reduce waste going to landfills In fact, alternatives fuels now represent more than 15% of total cement plant energy consumption in the USDownload scientific diagram Process Flow Diagram of the Cement Plant from publication: First, clay and limestone are crushed, ground, and mixed in specific proportionsProcess Flow Diagram of the Cement Plant ResearchGate2023年12月20日 Accurate cement production also depends on belt scale systems to monitor output and inventory or regulate product loadout, as well as tramp metal detectors to protect equipment and keep the operation running smoothly The Cement Manufacturing Process flow chart sums up where in the process each type of technology is making a differenceThe Cement Manufacturing Process Thermo Fisher Scientific