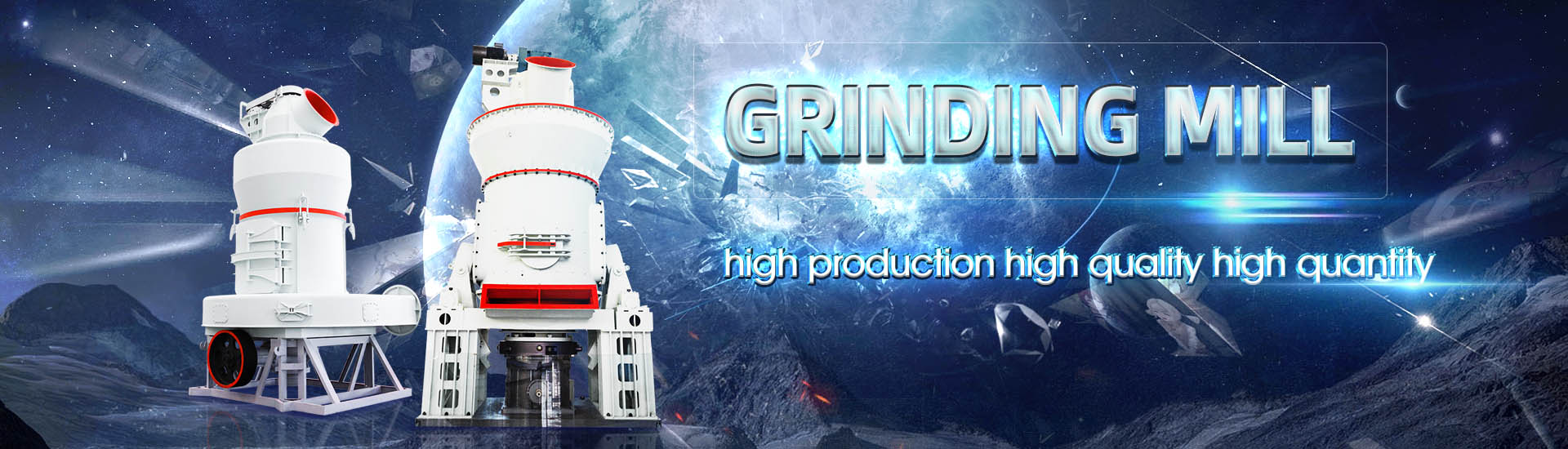
High fine Grinding technology
.jpg)
ISAMILL FINE GRINDING TECHNOLOGY AND ITS INDUSTRIAL
IsaMill is a major development in grinding technology jointly invented by Mount Isa Mines of Australia and Netzsch Feinmahltecknik GmbH of Germany for ultrafine and fine grinding duties in the minerals industry The IsaMill was introduced by MIM over a period of 9 years, as thereThe Metso HIGmill™ is an advanced, energyefficient fine and ultrafine grinding solution that utilizes proven technology With the tall, narrow, vertical body arrangement, grinding media is evenly distributed and mineral particles remain HIGmill high intensity grinding mill MetsoThree features of stirred mills that transform the economics of fine grinding are : the high intensity attrition grinding environment the ability to use fine grained media (eg 1 mm) to suit Fine Grinding as Enabling Technology – The IsaMillsolution for fine and ultra fine grinding Outotec HIGmills™ offer the unique possibility for online control and optimization of regrind product particle size This paper describes the basis of this Outotec HIGmills; A Fine Grinding Technology
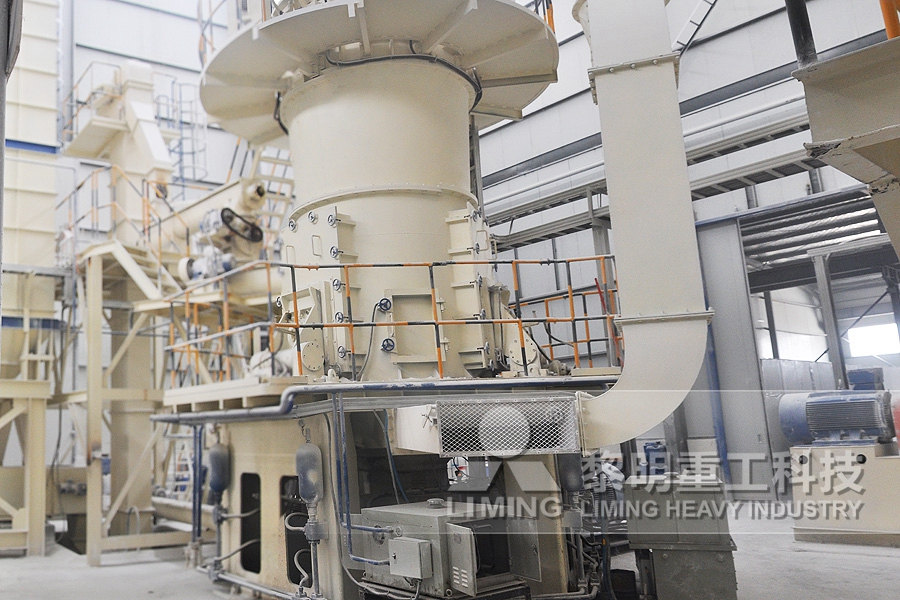
IsaMill™ Glencore Technology
The IsaMill™ has realworld success in 143 metalliferous installations across 23 countries It’s the world’s only horizontal finegrinding mill, so it avoids shortcircuits, is highly efficient and gives 2018年4月12日 It is shown that improved technology has yielded higher productivity and better quality across a diverse range of applications involving very large and very small products Modern grinding technology has learned Towards High Productivity in Precision Grinding MDPIIn principle, high energy can be supplied to quite fine media, making these devices attractive for ultrafine grinding applications By very careful matching of media size, powder size, and Ultrafine Grinding an overview ScienceDirect Topics2023年4月25日 So far, all countries in the world have invested in the research and development of optical ultraprecision grinding and polishing technology, and have developed more relatively mature highprecision grinding and polishing Ultraprecision grinding and polishing processing
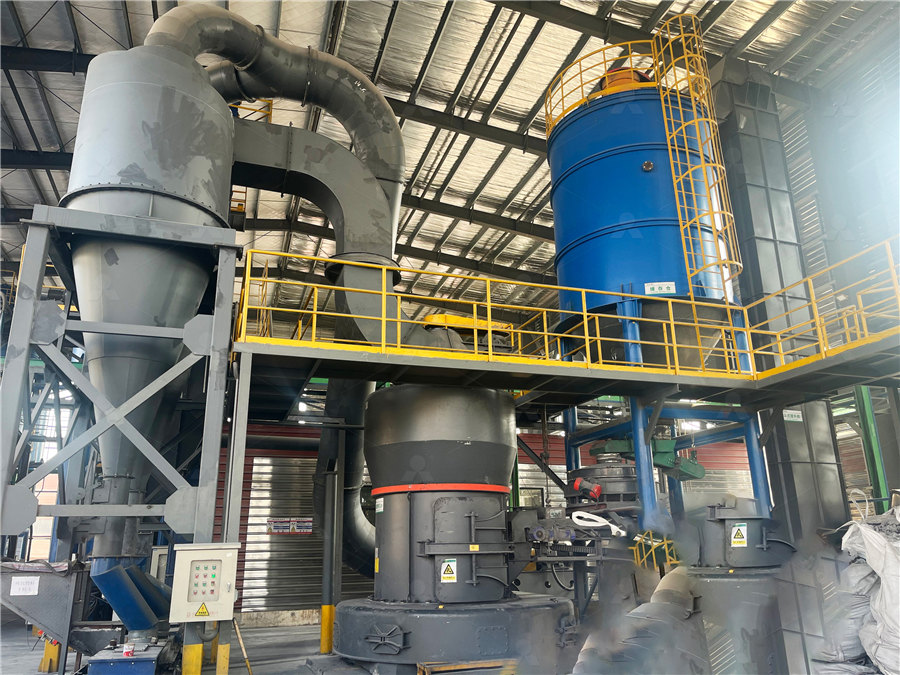
EnergyEfficient Advanced Ultrafine Grinding of
2023年7月10日 The review concludes that stirred mills have significant potential for achieving the energyefficient ultrafine grinding of particles Stirred mills have unique designs and operations, which provide higher grinding efficiency, lower 2010年1月1日 The objective of ultraprecision grinding is to generate parts with high surface finish, high form accuracy and surface integrity for the electronic and optical industries as well Ultraprecision grinding ScienceDirect2023年8月29日 Superfine grinding is an emerging technology that reduces particle size and modifies surface properties (Hu et al, Citation 2012)It is a novel processing method that is capable of degrading the organization of plant Full article: Potentials of superfine grinding in quality For fine grinding applications it is often necessary to use an extra heavy hammer pattern to achieve the very fine finished products desired: in many cases, the rotor will be equipped with hammers on all 8 or all 12 sets of hammer pinsHigh Speed Hammermills For Fine Grinding: Part 4
.jpg)
Towards High Productivity in Precision Grinding MDPI
2018年4月12日 Applications in modern grinding technology range from highprecision kinematics for grinding very large lenses and reflectors through to medium size grinding machine Figure 14a shows a tool where fine diamond 2023年4月25日 Under the opportunity of 'Made in China 2025', in the field of ultraprecision, China has broken through many key bottleneck technologies, achieved many remarkable scientific research results, built a number of highlevel ultraprecision processing technology innovation platforms, talent growth platforms and application demonstration bases, and Ultraprecision grinding and polishing processing technology Proven technology for efficient grinding: High Pressure Grinding Rolls Optimise your results with a high pressure grinding roll, the most energyefficient way to process mining ores Suitable for industries including iron ore, precious metals, base metals and other, the HPGR’s ability to weaken rock structure provides metallurgical benefits downstream (ie enhanced kinetics for FLS High Pressure Grinding Rolls – Efficient grindingThe new generation of stirred mills like the IsaMill has fundamentally changed the economics of fine grinding This has made them enabling technology for several existing and planned operations, and has opened new fields of processing in hydrometallurgy These opportunities are made possible by the unique combination of features of stirred mills : • Very high intensity Fine Grinding as Enabling Technology – The IsaMill
.jpg)
Highefficiency and energyconservation grinding technology using
2022年1月1日 A pilotscale grinding technology of ceramic medium stirred mill was proposed in this study Based on the specific productivity and grinding efficiency, the appropriate grinding parameters were ascertained as follows: material ball ratio of 07, ceramic ball medium size ratio (10 mm: 15 mm: 20 mm = 3:2:5), stirring speed of 110 rpm, grinding concentration of 50%, Fine grinding is also used when workpieces require both surfaces to have plane parallelism, but with more precision than can be achieved with doubledisk grinding Workpieces are placed in carriers that have teeth on the outside diameterSupfina Fine GrindingThe Metso HIGmill™ is an advanced, energyefficient fine and ultrafine grinding solution that utilizes proven technology With the tall, narrow, vertical body arrangement, grinding media is evenly distributed and mineral particles remain in constant contact, significantly increasing grinding efficiencyHIGmill high intensity grinding mill Metso2016年1月1日 Abrasive finefinishing technology is often applied as a final finishing process, abrasive finefinishing processes are lowefficiency processes compared to grinding However, the high ratio of energy u sl results in the improvement of the surface integrity characteristics such as surface roughness and residual stressAbrasive finefinishing technology ScienceDirect
.jpg)
The mechanisms of highefficiency grinding for micro/meso
2021年10月1日 To increase the process efficiency and reduce the costs, Zhang et al [9] used lasers to ablate grinding wheels to form micro/mesostructuresDeng and Xu [10] also introduced laser dressing of arcshaped resinbonded diamond grinding wheelsOther forms of highenergy beams (eg electron beam and ion beam) have also been used for dressing grinding wheels, 2010年1月1日 This may appear counterintuitive since ultraprecision grinding is often associated with low levels of materials removal However, ultraprecision grinding tends to employ grinding wheels having fine micrometer scale abrasives These fine wheels result in a high normal to tangential force ratioUltraprecision grinding ScienceDirectEnduron® high pressure grinding rolls (HPGR) can handle a wide variety of ores and particle sizes, from fine pellet feed all the way up to coarse grinding of 75mm copper, gold or iron ore When it comes to feed material characteristics, the specific ore type is not detected by an Enduron® HPGR, however ore hardness, size and bed compressibility are important Enduron® High Pressure Grinding Rolls (HPGR) WeirCreepfeed grinding (CFG) was a grinding process which was invented in Germany in the late 1950s by Edmund and Gerhard Lang Normal grinding is used primarily to finish surfaces, but CFG is used for high rates of material removal, competing with milling and turning as a manufacturing process choice CFG has grinding depth up to 6 mm (0236 inches) and Grinding (abrasive cutting) Wikipedia
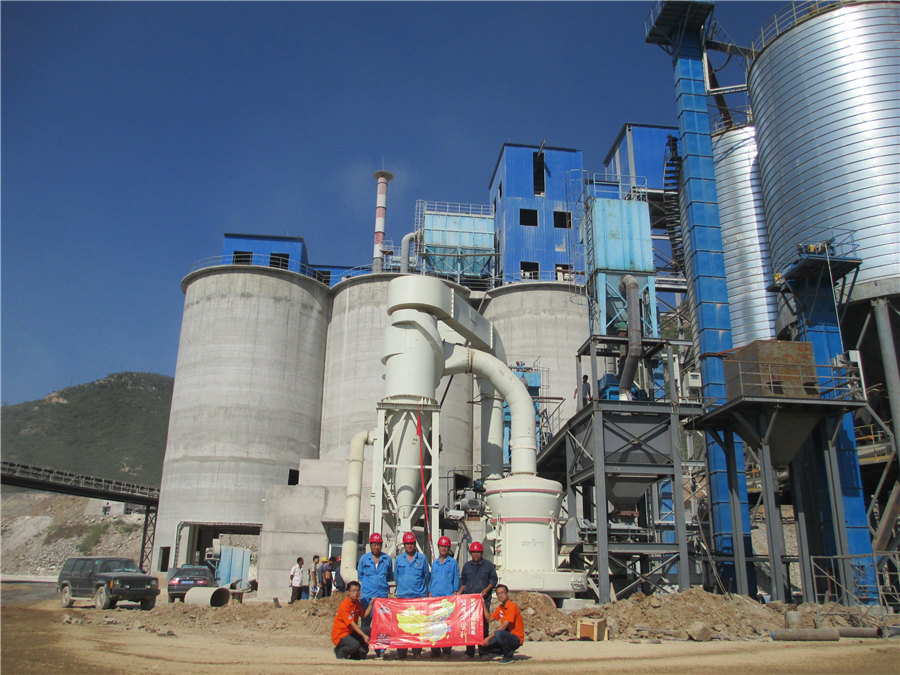
Effect of ultrafine grinding technology combined with high
2022年1月15日 Effect of ultrafine grinding technology combined with highpressure, Ultrafine grinding increases the antioxidant capacity of wheat bran Journal of Cereal Science, 57 (2013), pp 8490, 101016/jjcs201210002 View PDF View article View in Scopus Google ScholarFine grinding technology is performed by Melchiorre with the double side machines series ELC ELCs can cover all the main applications present in the high precision components industry ELC Machines Series APPLICATIONS Typical applications of fine grinding are: hydraulic pump components (rotors, stators, covers, blades)Melchiorre Fine Grinding, Lapping, Honing, PolishingIsaMill™ Technology Used in Efficient Grinding Circuits BD Burford1 and LW Clark2 High intensity stirred milling is now an industry accepted method to efficiently grind fine and coarse particles In particular, the IsaMill™, which was invented for, and transformed the fine grindingIsaMill Technology Used in Effecient Grinding Circuits2022年5月31日 Nanogrinding of SiC wafers with high flatness and low subsurface damage was proposed and nanogrinding experiments were carried out on an ultra precision grinding machine with fine diamond wheelsNovel VitrifiedBond UltraFine Grinding Technology for SiC
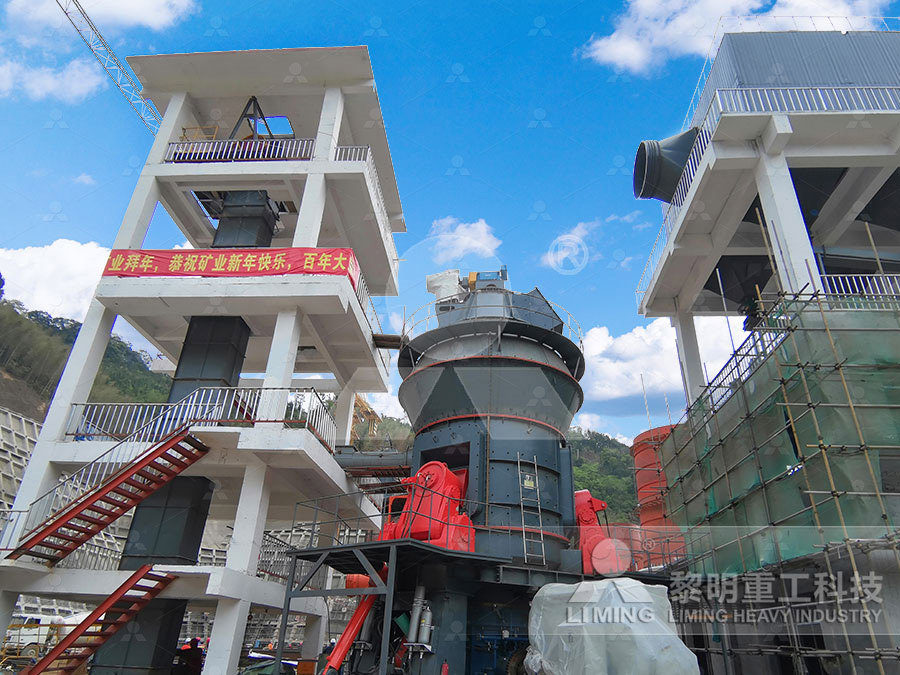
(PDF) A comprehensive review on the grinding process:
2022年6月24日 Grinding is a manufacturing process which significantly contributes in producing high precision and durable components required in numerous applications such as aerospace, defence and automobilesStirred media mills in the mining industry: Material grindability, energysize relationships, and operating conditions Lewis Taylor, Richard Greenwood, in Powder Technology, 2020 1 Introduction 11 Fine grinding in the mining industry It has been estimated that approximately 2% of the world's energy usage is applied to mineral comminution, and around a quarter of this is Ultrafine Grinding an overview ScienceDirect Topics2012年4月5日 Outotec has expanded its Grinding mill product family and now offers Outotec® High Intensity Grinding Mill (Outotec® HIGmill) for fine, ultra fine and regrind milling applications Outotec holds an exclusive rights agreement to provide process development, sales, and lifecycle support of the well proven technology from Swiss Tower Mills Minerals Ltd (STM) in the Outotec® High Intensity Grinding Mill Metso2024年1月23日 It’s often the first step in a multistage grinding process and is followed by finer, more precise grinding techniques HighSpeed Grinding Highspeed grinding involves using a grinding wheel that rotates at a much higher What is Grinding: Definition, Process, Types
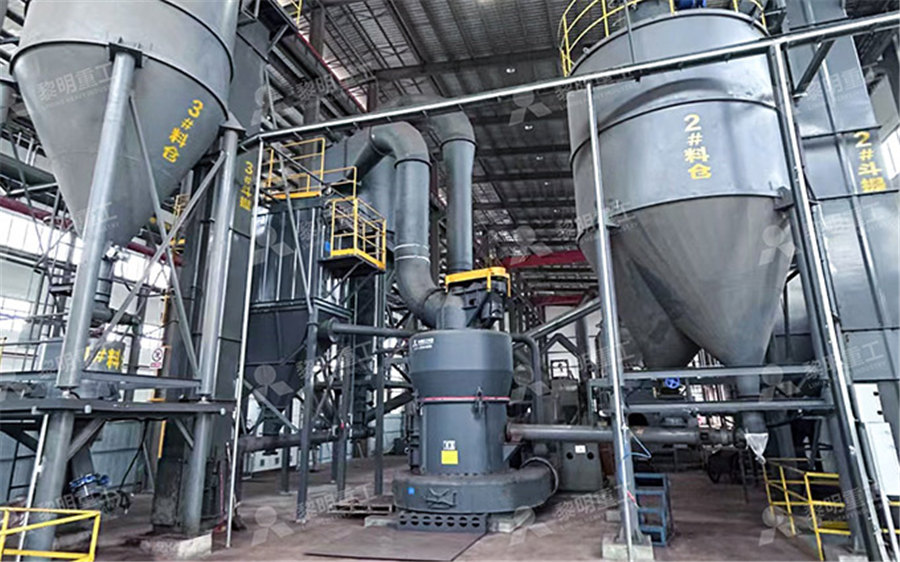
HIGH PRESSURE GRINDING; HOW HIGH CAN YOU
2019年2月5日 High Pressure Grinding Roll ("HPGR") technology could provide solutions in operations where even a very fine grind is required, by applying closed circuit arrangements with air classificationHammermills are commonly used for grinding a broad range of materials including those used in the production of pet foods and aquaculture feeds Since most pets and species of fish, crustaceans, and shellfish have a very short digestive tract, they require a finely ground, highly processed feed in order to realize good feed utilizationHigh Speed Hammermills For Fine Grinding: Part 1 Introduction2023年2月22日 In order to meet the manufacturing requirements of modern space remote sensors for highprecision freeform optical parts, the grinding technology and its application were studied The objective of this paper was to improve the application effect of traditional grinding technology in the processing of hard and brittle materials, and then apply it in specific fields Application of the Improved Grinding Technology to Freeform Enduron® high pressure grinding rolls (HPGR) can handle a wide variety of ores and particle sizes from fine pellet feed all the way up to coarse grinding of 75mm magnetite iron ore When it comes to feed material characteristics, the specific ore type is not detected by an Enduron® HPGR, however ore hardness, size and bed compressibility are important considerationsOur Dynamic HPGR Technology for Mineral Grinding Weir
.jpg)
(PDF) Ultrafine grinding of inorganic nonmetallic materials using
2020年8月20日 Ultrafine grinding is a technology, which can be used to process inorganic nonmetallic materials High quality surfaces with a low roughness, and high flatness are achievable in a low processing Fine grinding in the continuous range down to the nano range of low to medium viscosity liquids KREISIT ® MillingBeads Specially designed for the wet grinding technology of our machines Ideal for use in the paint, The consequence is a poor grinding and a too high temperature is introduced into the grinding stockFine Grinding with KREISBASKETMILL®Fine grinding lies at the heart of many processing applications, The Bepex Pulvocron defines fine grinding for food and industrial applications which rely on a consistently onspec fineground powder High speed impact fractures material into powder When a Fine Grinding Machines and Micronizing Equipment Bepex2024年4月25日 Grinding is a key technology for the resourcesaving and lowemission mobility of the future Examples of this include electric drives, which place the highest demands on the precision and surface properties of transmissions and engine components, or brake discs with reduced fine dust and hard coatings that are difficult to machineEMAG at the GrindingHub 2024 – Grinding technology for the
G[R.jpg)
IsaMill™ Glencore Technology
In short, IsaMill™ reduces the energy cost, media cost and capital cost of finegrinding The IsaMill™ is used extensively in base metals, PGM, gold processing and magnetite grinding applications And the power capacity of an IsaMill™ ranges from 75kW to 38mW IsaMill™ is the realworld specification of choice in: mainstream grinding2021年11月1日 A pilotscale grinding technology of ceramic medium stirred mill was proposed in this study Based on the specific productivity and grinding efficiency, the appropriate grinding parameters were Highefficiency and energyconservation grinding technology 2020年10月1日 Grinding is a key technology of highadded value sectors including aerospace, automotive, and energy generation [6], which has a direct impact on the accuracy, performance and the surface integrity of the workpiece [7]However, in addition to many factors such as the size precision requirements of the parts, parameter selection, blank type, processing method, Intelligent technology in grinding process driven by data: A 2004年12月10日 Whereas the state of the art of fine grinding technology for brittle materials is very high, thermoplastic, elastic, or fibrous materials cannot yet be ground as efficiently as brittle materials The production of finest powders of viscoelastic and plastic materials is often very energy consuming and therefore costintensive or even not possible at ambient temperaturesOptimised technologies for cryogenic grinding ScienceDirect
.jpg)
The Recent Technology and its Evaluation for Fine Grinding with High
DOI: 104164/SPTJ36484 Corpus ID: ; The Recent Technology and its Evaluation for Fine Grinding with Highoutput and Lowenergyconsumption @article{Ito1999TheRT, title={The Recent Technology and its Evaluation for Fine Grinding with Highoutput and Lowenergyconsumption}, author={Mitsuhiro Ito}, journal={Journal of The Society of Powder Technology, 2024年7月10日 Taking heavy calcium carbonate for coating industry as an example, its production process mainly includes: cleaning and impurity removal, coarse crushing, fine crushing, screening, grinding and grading, material collection, surface treatment, packaging, etc 2 Heavy calcium carbonate grinding technology and equipmentHeavy calcium carbonate grinding, surface modification technology Tip Speed Fine Grinding and Tough to Grind Materials For fine grinding aquaculture feeds, a high tip speed is required Normal tip speeds for fine grinding and fibrous materials are obtained on 44" Feed Manufacturing Technology; 4 Evaluating High Speed Hammermills For Fine Grinding: Part 3 Feed Fine grinding is easily automated; Fast High removal rate using super abrasive diamond and CBN (3 – 20 times faster than lapping) Possible saving of premachining steps; Fine grinding benefits from long intervals between resharpening; Fine grinding has high flexibility; Automated solutions; Clean Fine grinding benefits from the recycling of What is Single Double Side Fine Grinding? Lapmaster Wolters
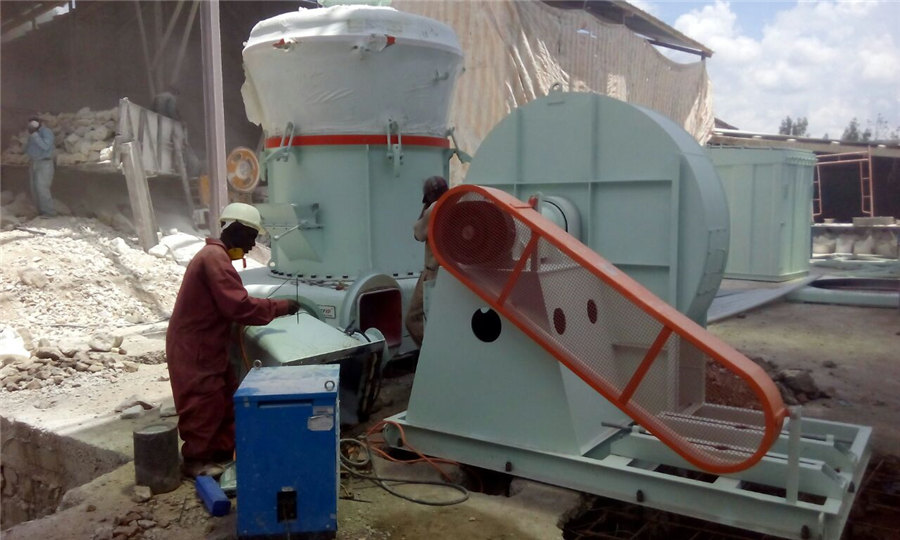
HighSpeed and LowNoise Gear Finishing by Gear Grinding and
2024年11月5日 31 Form Grinding When using a form grinding machine for gear modification, the conventional method is to use a diamond roller to dress the grinding wheel, and then the grinding wheel grinds the gear to complete the modification []One of the disadvantages of this method is that if you want to get different gear profiles, you must use different diamond wheels