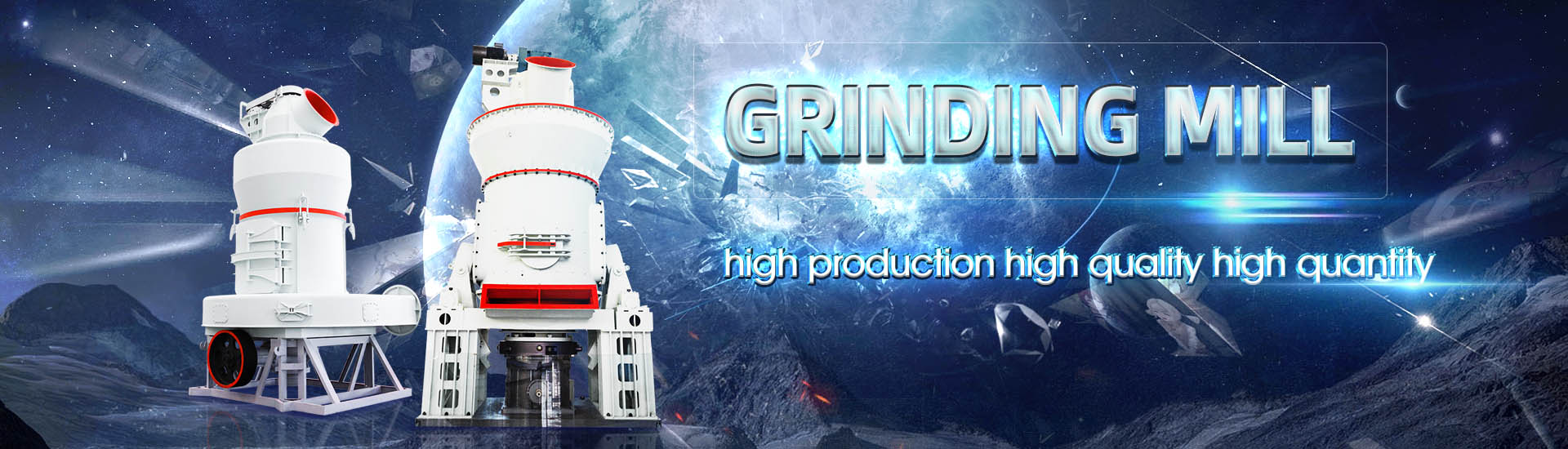
Alumina ash, overhaul slag, aluminum electrolyte deep processing projects
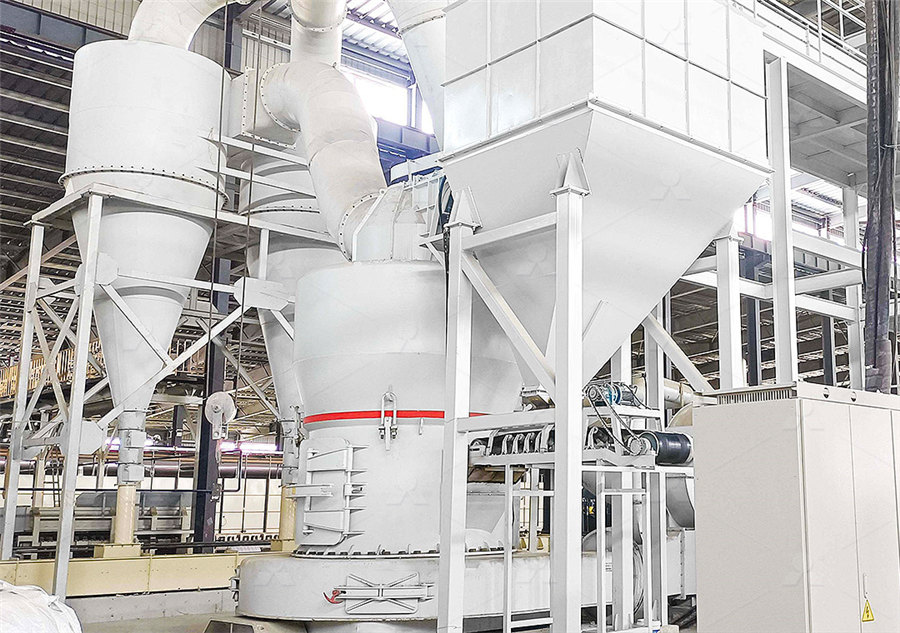
2023 the 7th International Conference on Energy and
2023年8月1日 The dissolution behaviors of overhaul slag were fitted by a mass transfer 2023年4月25日 This article analyzes and summarizes the composition and hazards of the Research Progress of Electrolytic Aluminum Overhaul Slag Disposal2024年2月1日 The electrolytic aluminum industry generates a large amount lithium (Li) Efficient lithium recovery from electrolytic aluminum slag via an 2022年12月12日 In this paper, the first ultrahigh pressure contact molding technology was Comprehensive performance study of aluminum ash and calcium
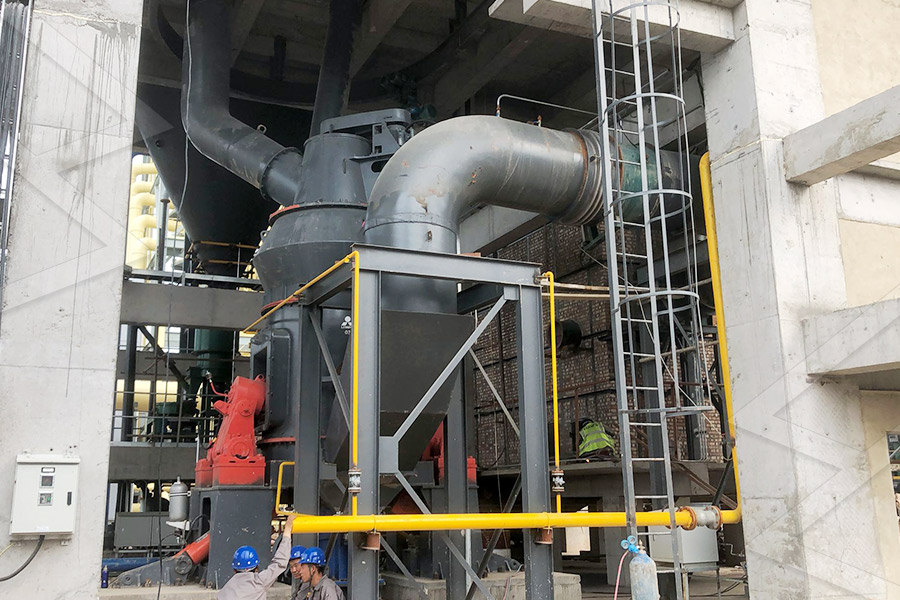
Cleaner Process for the Selective Extraction of Lithium
2024年7月24日 The lithium was selectively recovered and enriched from spent aluminum electrolyte slag by using calcium salt roasting transformation followed by HBL121solvent extraction The new process realizes a high leaching Aluminium ash and slag are produced from molten slag cooling in the electrolytic aluminium Recycling and Utilization of the Electrolytic Aluminium Ash and Slag2016年10月24日 In this paper, the development of aluminum electrolysis control systems is Progress in Aluminum Electrolysis Control and Future Direction for 2019年2月1日 Aluminum ash is an industrial waste residue produced during alumina Preparation of Alumina from Aluminum Ash by Sintering with
.jpg)
Fundamental Research on the Densification of Alumina
2022年1月3日 Ferrotitanium slag was used as a sintering aid to prepare highperformance alumina (Al2O3) ceramics by pressureless sintering at different temperatures The bulk density, apparent porosity, bending strength, and hardness of the 99 wt% Al2O3 ceramics after sintering at 1420 °C were 391 g/cm3, 016%, 38937 (± 761) MPa, and 1564 (± 016) GPa On the 2024年1月1日 Semantic Scholar extracted view of "Efficient lithium recovery from electrolytic aluminum slag via an environmentally friendly process: Leaching behavior and Green and efficient separation of fluorine from spent aluminum electrolyte by aluminum sulfate solution: Leaching behavior and mechanism Lingqi Meng Tianxiang Hao +5 Efficient lithium recovery from electrolytic aluminum slag via an In Fig 41, the numbers 150200250 on the graphs of equilibrium relate to caustic soda concentrations in Na 2 CO 3A/C denotes aluminate ion concentration as Al 2 O 3 (A)/caustic soda concentration as Na 2 CO 3 (C) A typical Bayer process cycle with low temperature digestion is also shown Virtually each bauxite contains more or less amount of clay minerals, Chemical Processing of Bauxite: Alumina and Silica 2024年6月29日 Aluminum electrolyte is a necessity for aluminum reduction cells; however, its stock is rising every year due to several factors, resulting in the accumulation of solid waste Currently, it has become a favorable material for the resources of lithium, potassium, and fluoride In this study, the calcification roasting–twostage leaching process was introduced to extract Stepwise extraction of lithium and potassium and recovery of

Preparation of Alumina from Aluminum Ash by Sintering with
2019年2月1日 Aluminum ash is an industrial waste residue produced during alumina electrolysis and aluminum processing and casting In the experiment, alumina powder with a purity of 9897% was prepared by sintering with sodium hydroxide and the process conditions affecting the dissolution rate of Al 2 O 3 from aluminum ash were studied The best process conditions for 2023年9月1日 Lithium (Li)bearing aluminum electrolyte slag is an inevitable byproduct of the aluminum industry, and improper disposal or stacking it may lead to potential environmental hazards This study employed hydrometallurgical processes to selectively leach lithium from Licontaining aluminum electrolyte slag, using sodium carbonate solution as the leaching agent Clean Process for Selective Recovery of Lithium Carbonate from 2023年10月1日 Currently, the green resource utilization in the aluminum electrolysis industry mainly focuses on the solid waste treatment of aluminum electrolysis tank overhaul slag, the resource utilization of waste cathodes, and the recovery of electrolytic tank waste heat There are few reports on lithium recovery from waste aluminum electrolytes [16,17]A novel approach for ultrasonic assisted organic acid leaching of 2024年7月24日 Spent aluminum electrolyte slag is a byproduct produced during the electrolysis of aluminum and contains elements such as F, Al, Na, and Li It is a toxic and harmful substance with a stable and complex structure As a consequence of fluorine pollution and low lithium recovery efficiency in the traditional hydro metallurgy process, a novel cleaner production Cleaner Process for the Selective Extraction of Lithium from Spent
.jpg)
(PDF) Carbothermic reduction of alumina: A review of
2011年6月26日 New processes and novel concepts were developed, under the ENEXAL project, for the vacuumassisted carbothermal reduction of alumina showing that this could provide an energy saving of 21%, GHGs 2021年11月1日 Dissolution behavior of overhaul slag from aluminum reduction cell in a cryolitebased molten Abstract The crusting/agglomerating behavior and heat transfer process upon feeding of smeltinggrade alumina into aluminum electrolyte were investigated using a suspended weighing device Mineral Processing and Extractive Improved CFD modeling of full dissolution of alumina particles in 2023年10月1日 Cryolitealumina (Na 3 AlF 6Al 2 O 3) molten salt electrolysis is the only modern method for the industrial production of metallic aluminum (Ishak et al, 2017)Under the influence of direct current, Al 2 O 3 dissolved in the molten salt is reduced to monolithic aluminum at the cathode (Haraldsson and Johansson, 2020)As the blood of the electrolytic cell, the electrolyte Efficient extraction and recovery of lithium from waste aluminum 2018年11月29日 For existing coalfired power plants, current methods of utilizing ash and slag waste may be considered in addressing new environmental and economic risks However, for new power sources, environmental considerations are much more important in selecting the coalcombustion technology Technology based on a circulating fluidized bed is sometimes cited as Processing Ash and Slag Wastes from Thermal Power Stations Part 2
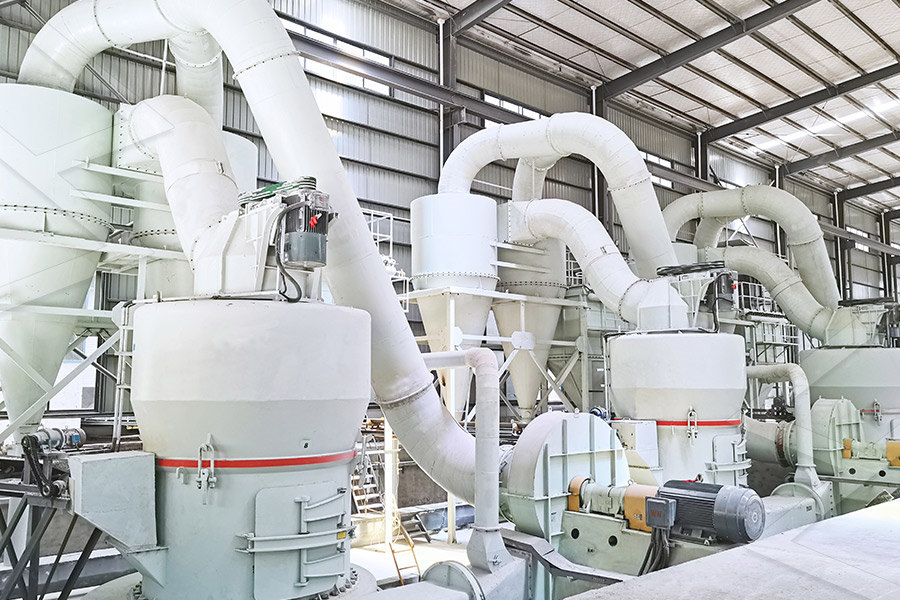
A Review of Secondary Aluminum Production and
2021年7月30日 On the other hand, due to the maturity of micron alumina production technology, micron alumina has relatively low energy consumption and emissions in the production process, reducing the waste of 2018年12月17日 A sintering–CO2 decomposition process for preparation of pseudoboehmite is proposed for clean valorization of highalumina fly ash The effects of different synthesis conditions on the crystal structure and textual properties of the pseudoboehmite were studied systematically The results showed that the main product was NaAlCO3(OH)2 when the Preparation and Properties of Pseudoboehmite Obtained from 2023年1月30日 The present article is focused on extraction alumina from high alumina fly ash using an improved hydrochemical method with highefficiency alkali circulation and mild reaction conditions The alumina leaching behavior and corresponding reaction mechanism of the process were systematically investigated The results revealed that the alumina extraction efficiency A HighEfficiency Alkali Circulation Process for Alumina Extraction 2024年5月23日 16 Million metric tons of spent carbon electrodes modify carbonrich solid wastes from aluminum electrolysis are produced annually, threatening ecosystems by cyanide and fluoride pollution Here, we review carbonrich solid wastes with focus on sources and hazards, detoxification, separation, recovery, recycling and disposal Treatment techniques The recycling of carbonrich solid wastes from aluminum
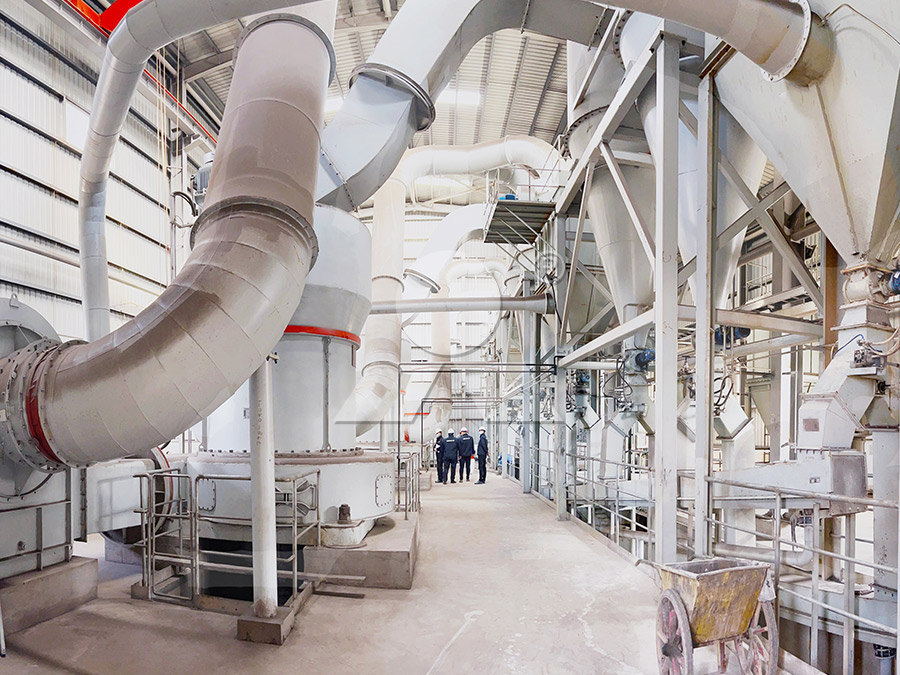
Progress in Aluminum Electrolysis Control and Future Direction
2016年10月24日 The industrial aluminum reduction cell is an electrochemistry reactor that operates under high temperatures and highly corrosive conditions However, these conditions have restricted the measurement of key control parameters, making the control of aluminum reduction cells a difficult problem in the industry Because aluminum electrolysis control 2014年12月5日 The dissolution process of alumina in a threedimensional 300 kA aluminum reduction cell was modeled and simulated employing our custom code A twoparticle phase population balance model (TPPBM) was proposed by dividing solid phase into two groups consisting of small and large size alumina particles separately A CFDTPPBM coupled model CFD simulation of dissolution process of alumina in an aluminum 2015年5月1日 The Reynolds numbers for alumina sedimentation were in the range of (788 × 107)(756 × 103) that indicated the Stockesian regime The values were significantly lower than those calculated in Ref [39] for both agglomerated and nonagglomerated alumina particles settling, which were in the range of 34–25458 for the size range from 40 μm (non Analysis and modeling of alumina dissolution based on heat and 2022年11月2日 To prepare highpurity aluminum by ionic liquidbased electrolytic aluminum deposition, primary aluminum (about 99% purity) is used as the anode, which is immersed in the ionic liquid electrolyte The refinement of aluminum is achieved via an electrolytic reaction at lower temperatures (25–80°C), and highpurity aluminum is produced on the cathodeIonic liquids as electrolytes in aluminum electrolysis
.jpg)
Review A review on fly ash highvalue synthesis utilization and its
2024年3月1日 Fly ash possessing an alumina content exceeding 30% is categorized as highaluminum fly ash (Wang et al, 2020a; Yao et al, 2014), while fly ash with an alumina content below 271% which is the average alumina content in Chinese fly ashis denoted as lowaluminum fly ash (Yang et al, 2019b; Zhan et al, 2022; Zhao et al, 2022)2024年11月15日 So, when sintering ash and slag waste from Almaty TPP2 on a threecomponent charge of the composition CaO:SiO 2 = 2; Na 2 O:(Al 2 O 3 +Fe 2 O 3) = 1 at a duration of 60 min and a temperature of 1200 °C, alumina extraction was 8368 %, under the same conditions, alumina extraction of 8707 % was obtained during sintering of ash and slag Studies of the sintering method of ash and slag waste for the 2023年4月13日 Aluminium is produced by electrolysis using alumina (Al2O3) as raw material and cryolite (Na3AlF6) as electrolyte In this HallHéroult process, the energy consumption is relatively large, and A comprehensive review of aluminium electrolysis and the waste electrolyte (specific gravity 21) Periodically, this aluminum is siphoned off by vacuum into crucibles To replace the alumina consumed in the reaction, more alumina must be added Today, computercontrolled devices called point feeders automatically inject the alumina powder through the top surface crust of solidified electrolyte Pots may eachChapter 2 Production and Processing of Aluminum The
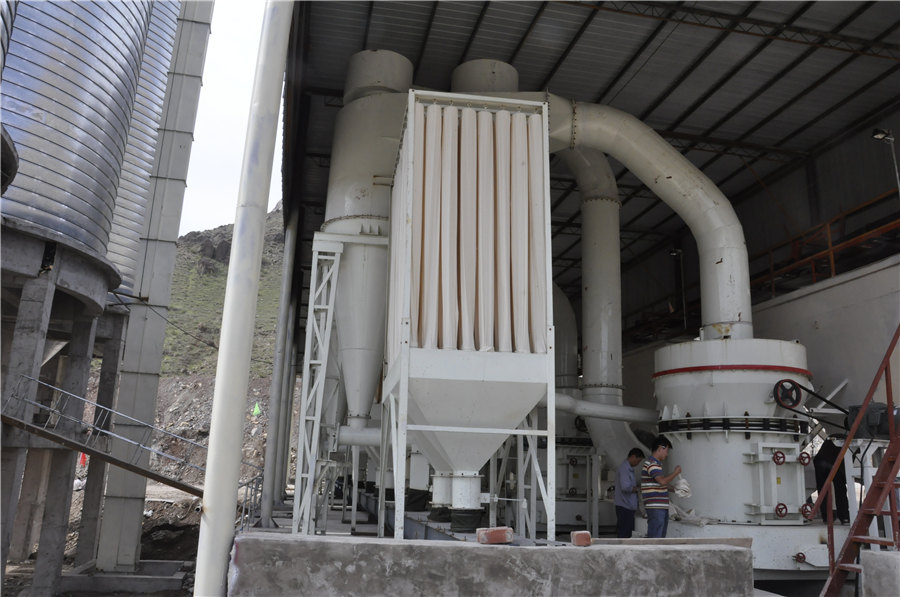
A Review of Secondary Aluminum Production and Its Byproducts
2021年7月30日 The aluminum metal and molten salt flux are tapped after the process, where the cooled flux along with the mixture of nonmetallic components is called salt slag or salt cake54 Salt slag contains 5–7 wt% residual aluminum metal, 15–30 wt% aluminum oxide, 30–55 wt% sodium chloride, and 15–30 wt% potassium chloride and, depending upon the 2021年10月26日 The liquidus temperature for primary crystallization of cryolite in the system Na3AlF6AlF3LiFCaF2MgF2 was determined by thermal analysis The data were fitted to an empirical equation, valid (PDF) Modeling of the Aluminium Electrolysis Process: Feeding and 2022年8月19日 According to the CaO–SiO 2 –MgO–Al 2 O 3 phase diagram with different alumina content (10–25 wt%), as shown in Fig 41With the increase of Al 2 O 3 content, the high melting point phase spinel (MgO Al 2 O 3) area expandsWhen the basicity is about 10–12 (this is the common basicity range of blast furnace slag) with suitable content of MgO and Al 2 O 3, HighTemperature Physicochemical Properties of High Alumina Slag 2023年4月1日 Comparing with other materials, the aluminum industry is energy intensive with a notable difference between primary and secondary production (174–186 MJ/kg and 10–20 MJ/kg, respectively) (Abdulkadir et al, 2015)The reason by which secondary aluminum production consumes much less energy is because its raw material is aluminum scrap and primary Synthesis strategies of alumina from aluminum saline slags
.jpg)
Prospects of Aluminum Chloride Electrolysis under Modern Conditions
2021年6月25日 The advantages of electrolysis of aluminum chloride in comparison with alumina–cryolite melts, namely, a lower temperature of the process, a lower potential of AlCl 3 decomposition, the inertness of carbon anode to chlorine, provide savings at this process stage However, the electrolysis of aluminum chloride applies higher requirements onto the quality of Coal fly ash (CFA), an industrial byproduct of hightemperature combustion of coal in coalfired power plants, is one of the most complex and largest amounts of industrial solid wastes generated in China It is widely recognized that CFA should be considered as a potential alumina resource to substitute bauxite In this review, the features of highalumina fly ash and aluminum recovery Aluminum extraction technologies from high aluminum fly ash De GruyterAmong them, alumina accounts for more than 70%, which has a high recycling value Aluminum ash is divided into primary aluminum ash, secondary aluminum ash, cathode carbon block, anode carbon slag, electrolytic cell impermeable material, refractory, aluminum alloy factory dust collection, aluminum processing sludge, etcAluminum Ash Processing Aluminum Ash Recovery Aluminum Ash 2024年10月9日 So, when sintering ash and slag waste from Almaty TPP2 on a threecomponent charge of the composition CaO:SiO2=2; Na2O:(Al2O3+Fe2O3)=1 at a duration of 60 minutes and a temperature of 1200 ºC, alumina extraction was 8368 %, under the same conditions, alumina extraction of 8707 % was obtained during sintering of ash and slag waste STUDIES OF THE SINTERING METHOD OF ASH AND SLAG WASTE
.jpg)
A novel approach for extracting lithium from overhaul slag by low
2024年2月1日 Overhaul slag, as one of the main hazardous solid wastes generated in the electrolytic aluminum, has high research value [12]The electrolytic cell lining is eroded by continuous chemical corrosion of hightemperature molten metal and salt, resulting in expansion and peeling off, leading to low production efficiency and degradation of performance [13]2024年4月17日 Recycling plays an important role in today's world due to its considerable contributions to mitigating energy concerns and environmental challenges One of them is dross recycling from aluminum (Al) cast houses Unlike other recyclable materials, dross has an abundance of components, including rare earth elements, heavy metals, ferrous, and recycled Aluminum dross: aluminum metal recovery and emerging 2020年7月5日 Experiments were conducted to investigate the process of aluminum and lithium extraction from highalumina coal fly ash (HCFA) generated from coalfired power plants located in northern China The presence of mullite and other aluminosilicates lead to low reactivity of coal fly ash An activation pretreatment that destroys an inert composition of coal is necessary The Activation Pretreatment and Leaching Process of HighAlumina2023年11月9日 The process of extracting aluminum with sulfuric acid from highalumina fly ash activated by roasting with Na2CO3 and NaOH as raw materials ware studied The results revealed that the aluminum in fly ash activated by sodium carbonate reached 932% under the optimum conditions (30% H2SO4, 90°C, 120 min, and liquidtosolid ratio was 5:1) Kinetics of aluminum extraction from roasting activated fly ash by
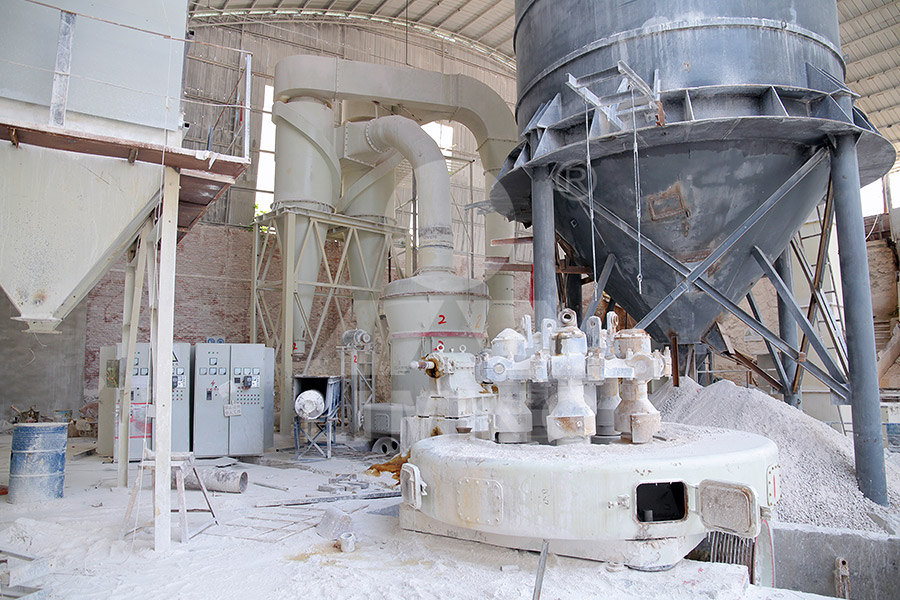
Comprehensive Extraction of Silica and Alumina from Coal Fly Ash
2023年11月30日 Coal fly ash (CFA) is an increasingly prevalent byproduct that necessitates more resourceful and ecofriendly processing methods Extracting aluminum from CFA is a crucial aspect of promoting sustainable development in the alumina industry In this paper, a technique for comprehensive extraction of silica and alumina from circulating fluidized bedbased CFA is 2017年11月22日 A method is developed for processing saline aluminumcontaining slag based on leaching and electrolysis of solid residue after leaching in molten fluoride with preparation of a deoxidizing alloy for steel Saline solution is evaporated with preparation of a covering and/or coveringrefining flux In the course of pilot plant tests, optimum process conditions are Comprehensive Processing of Saline AluminumContaining Slag2020年12月1日 The rapid development of the electrolytic aluminum industry in China and the increasing demand for aluminum products have led to the development of many lowgrade bauxite mines with an average Li 2 O content of at least 058% (Wang et al, 2013)Due to the use of this lowgrade bauxite in the electrolytic aluminum process, the content of lithium in the Novel process for the extraction of lithium carbonate from spent 2013年6月15日 The fly ash with alumina composition from 45 to 55 % has been found in China in last 10 years, which attracts great attention from Chinese government and related alumina industry Chinese government and its stateowned enterprises have successfully extracted the Al as alloy product from the highalumina fly ash However, to recycle the calcium silicate slag as Thermal activation on calcium silicate slag from highalumina fly ash