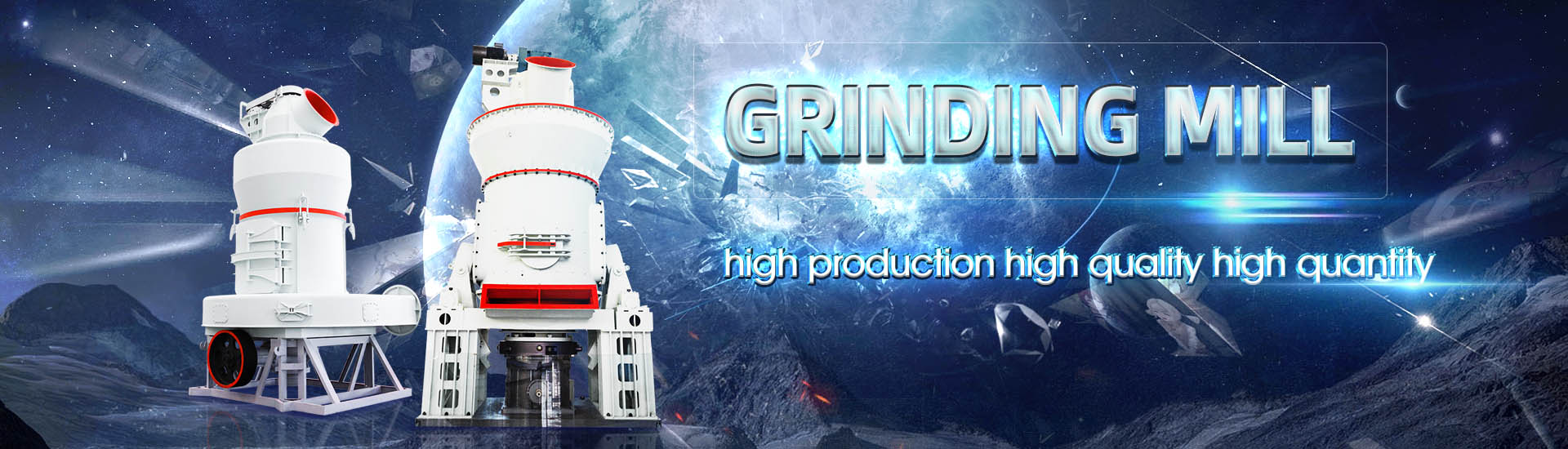
Aluminum smelting electrolyte waste slag grinding mechanical moving knife
.jpg)
Efficient lithium recovery from electrolytic aluminum slag via an
2024年2月1日 The electrolytic aluminum industry generates a large amount lithium (Li)containing electrolytic aluminum slag (EAS) annually, and this can result in severe 2023年5月20日 Spent carbon anode (SCA) discharged from the aluminum electrolysis industry is an unavoidable solid waste with an estimated production of 700 kilotons in 2021, which has Regeneration of raw materials for aluminum electrolysis from 2022年4月13日 Here we propose a solidstate electrolysis (SSE) process using molten salts for upcycling aluminium scrap The SSE produces aluminium with a purity comparable to that of A solidstate electrolysis process for upcycling aluminium scrap2020年8月1日 Here, we discuss the influence of different processing parameters on electrolytic refining of aluminum alloy and investigate the mechanism of extracting Al from coarse AlSi Recovery of aluminum from waste aluminum alloy by low
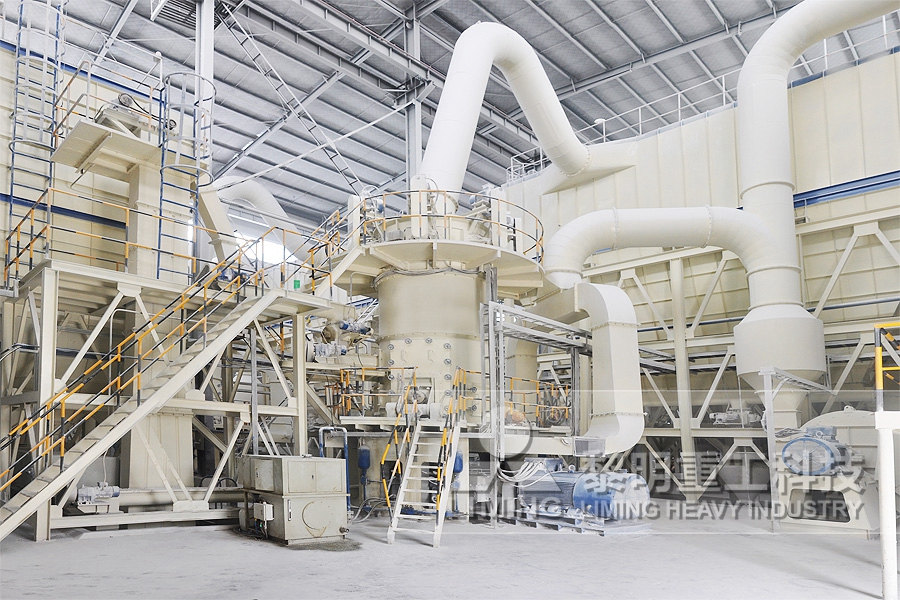
The recycling of carbonrich solid wastes from aluminum
2024年5月23日 Here, we review carbonrich solid wastes with focus on sources and hazards, detoxification, separation, recovery, recycling and disposal Treatment techniques include 2023年4月25日 This article analyzes and summarizes the composition and hazards of the overhaul slag and the current development status of domestic and international electrolytic Research Progress of Electrolytic Aluminum Overhaul Slag Disposal2014年5月1日 Additionally, aluminum smelters use carbon anodes in their electrolysis cells because carbon is a reasonably good electrical conductor and can withstand the corrosive (PDF) The Aluminum Smelting Process and InnovativeThere are three ways for extracting Aluminum, primary source from aluminum ores (bauxite ore), secondary source from aluminum scrap and white dross, tertiary source from black dross and Recovery of Aluminum from Industrial Waste (Slag) by Melting and
.jpg)
A comprehensive review of aluminium electrolysis and the waste
2023年4月13日 Aluminium is produced by electrolysis using alumina (Al2O3) as raw material and cryolite (Na3AlF6) as electrolyte In this HallHéroult process, the energy consumption is 2024年7月24日 The lithium was selectively recovered and enriched from spent aluminum electrolyte slag by using calcium salt roasting transformation followed by HBL121solvent Cleaner Process for the Selective Extraction of Lithium from Spent Kvande and Drabløs JOEM Volume 56, Number 5S, May 2014 Volume 56, Number 5S, May 2014 (The Aluminum Smelting Process and Innovative Alternative 2014年5月1日 The beginnings of human civilization can be traced to the Jiahu settlement, China (ca 7000–5700 BC, 500 inhabitants) However, if we are to accept the view of historians, who generally clock (PDF) The Aluminum Smelting Process ResearchGate
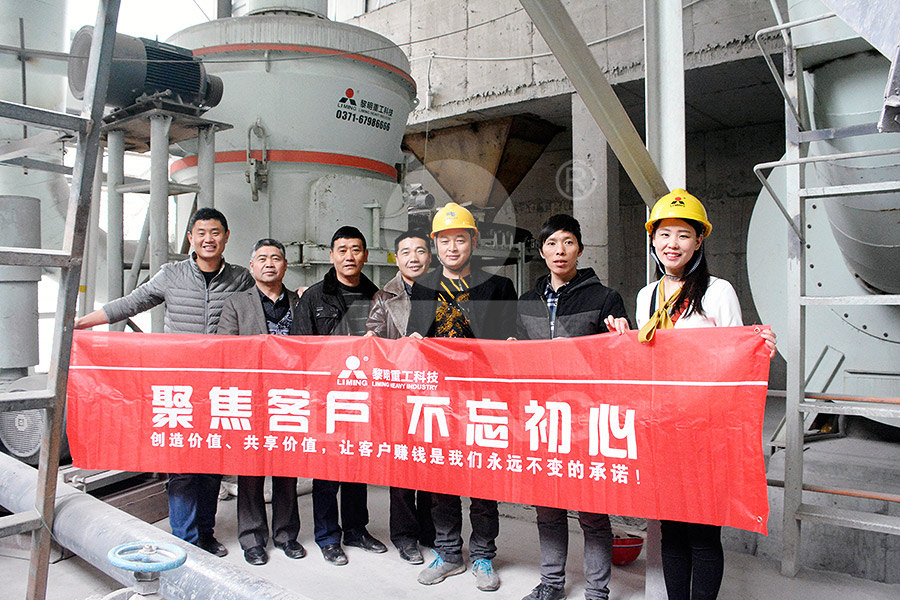
The recycling of carbonrich solid wastes from aluminum
2024年5月23日 This work was supported by the Key Research and Development Program of Yunnan Province, Joint Disposal and Comprehensive Utilization of Typical Hazardous Waste of Electrolytic Aluminum (No AA), Demonstration of Industrialization of Spent Anode Carbon Recovery Electrolyte Treatment and Conversion to Aluminum Fluoride and Alumina 2022年10月10日 One of the main electrolytic aluminum production costs is the consumption of carbon anodes, and carbon anode slag is a common hazardous waste in the aluminum industryRecovery of carbon and cryolite from spent carbon anode slag of AlKhwarizmi Engineering Journal AlKhwarizmi Engineering Journal, Vol 14, No 3, September, (2018) PP 81 91 Recovery of Aluminum from Industrial Waste (Slag) by Melting andRecovery of Aluminum from Industrial Waste (Slag) by Melting 2023年11月16日 A solution to improve the energy efficiency of aluminum smelting by preheating prebaked anodes is proposed The reduction of electricity consumption is calculated, and the advantages of the prebaked anode preheating technology are assessed Pilot tests of the anode preheating technology were prepared and conducted The results of mathematical modeling Improving the Energy Efficiency of Aluminum Smelting Using the
.jpg)
A Review of Secondary Aluminum Production and Its Byproducts
2021年7月30日 Secondary aluminum production is required for the conservation of the environment It can significantly reduce greenhouse gas emissions and energy consumption and reduce the consumption of alumina 2024年6月29日 Aluminum electrolyte is a necessity for aluminum reduction cells; however, its stock is rising every year due to several factors, resulting in the accumulation of solid waste Currently, it has become a favorable material for the resources of lithium, potassium, and fluoride In this study, the calcification roasting–twostage leaching process was introduced to extract Stepwise extraction of lithium and potassium and recovery of 2013年12月1日 According to the European Waste Catalogue and Hazardous Waste List, the slag resulted from electric arc furnace is part of the wastes from thermal processes category and it has the codes 10 02 01 Optimization of process for total recovery of aluminum from smelting Aluminum processing Smelting, Refining, Alloying: Although there are several methods of producing aluminum, only one is used commercially The Deville process, which involves direct reaction of metallic sodium with aluminum chloride, was the basis of aluminum production in the late 19th century, but it has been abandoned in favour of the more economical electrolytic Aluminum processing Smelting, Refining, Alloying Britannica
.jpg)
Ultimate Guide – Aluminum Fabrication, Grinding,
2021年6月16日 Aluminum and aluminum alloys are among the most used metals in fabrication,construction, and in the creation of good all around you It is such a useful and versatile metal, but there are some special 2024年2月1日 Aluminum metal was produced using the cryolitealumina molten salt electrolysis method (Ishak et al, 2017)A large amount electrolytic aluminum slag (EAS) is generated during the electrolysis process, as the falling of carbon particles on the anode into the electrolysis cells and the accumulation of lithium fluorine result in energy consumption and electrolyte scrapping Efficient lithium recovery from electrolytic aluminum slag via an The History Of Aluminum Smelting The modern aluminum smelting technique traces its roots to 1886 An Ohio chemistry student named Charles Martin Hall discovered a process to separate aluminum from molten material At the same The Aluminum Smelting Process Explained HARBOR2023年3月12日 The aluminum electrolysis industry continually and unavoidably produces hazardous solid waste in the form of carbon anode slag Carbon anode slag poses a serious environmental pollution risk, and it must be disposed of in a harmless manner On the other hand, it contains a few valuable resources, as well In order for the aluminum electrolysis industry to Recovery of Carbon and Cryolite from Spent Carbon Anode Slag
.jpg)
The Aluminum Smelting Process : Journal of Occupational and
Despite this, more aluminum is produced today than all other nonferrous metals combined The total annual world production of primary aluminum was about 50 million metric tonnes in 2013, and in addition around 20 million tonnes was recycled One billion tonnes of aluminum has been produced in history, and 800,000 tonnes since 19802024年6月6日 Dive into the fascinating world of aluminum smelting Explore its rich history, intricate processes like the Bayer and HallHéroult methods, and discover the benefits, challenges, and future trends in this crucial industry Perfect for industry enthusiasts and those seeking consulting services on aluminum smeltingAluminum Smelting: History, Processes, and Future Outlook2024年4月17日 Recycling plays an important role in today's world due to its considerable contributions to mitigating energy concerns and environmental challenges One of them is dross recycling from aluminum (Al) cast houses Unlike other recyclable materials, dross has an abundance of components, including rare earth elements, heavy metals, ferrous, and recycled Aluminum dross: aluminum metal recovery and emerging Download Citation On Sep 1, 2023, Rui Xu and others published Clean Process for Selective Recovery of Lithium Carbonate from Waste LithiumBearing Aluminum Electrolyte Slag Find, read and cite Clean Process for Selective Recovery of Lithium Carbonate from Waste
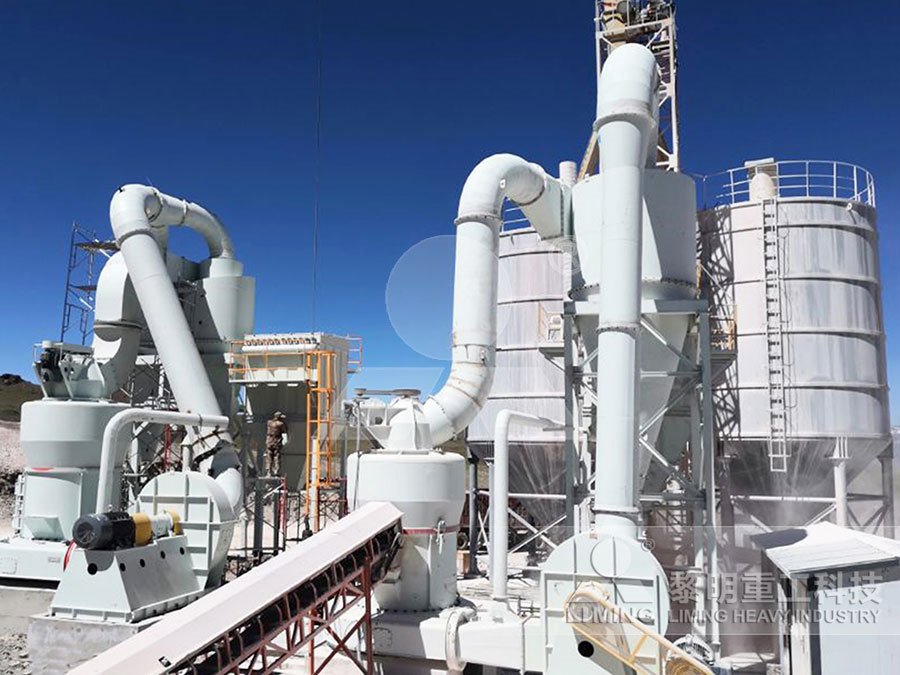
Advances in the Safe Disposal and Comprehensive Utilization
2021年11月1日 Advances in the Safe Disposal and Comprehensive Utilization of Spent Carbon Anode From Aluminum Electrolysis: Prospects for Extraction and Application of Carbon Resources From Hazardous Waste2024年2月3日 Effective monitoring and precise control of electrolyte and thesis, College of Engineering and Mineral Resources, Department of Mechanical and Aerospace Bao J, SkyllasKazacos M, Welch B, Mahmoud M, Arkhipov A, Ahli N (2023) Studies on Power Modulation of Aluminum Smelting Cells Based on a Discretized Mass and Predicting Electrolyte and Liquidus Temperatures of Aluminium Smelting 2022年1月1日 Aluminum black dross is produced by the secondary smelting process of aluminum Aluminum black dross is classified as hazardous waste because it is reactive with water and produces substances and (PDF) Utilization of hazardous waste of black dross 2020年2月1日 Salt slag treatment plants: There are companies that take and treat salt slag from secondary smelters, the available processes are summarised by Tsakiridis [37] Some secondary smelters internally recycle salt slag [53] , first by removing more available aluminium, and separating the salt from the oxide by washing and recrystallisationThe aluminium industry: A review on stateoftheart technologies
.jpg)
Studies on Power Modulation of Aluminum Smelting Cells Based
2023年1月4日 Dynamic models for aluminum smelting cells have been proposed to describe the average cell conditions, [34,35,36,37,38,39,40,41,42,43,44,45] but the assumptions of cell spatial homogeneity is becoming questionable due to the trends in large modern cell designs, which includes increasing anode size per line current, decreasing electrolyte volume per line current, 2018年10月1日 For instance, the production of alumina with a purity of more than 97% from a solid waste cake produced at an aluminum factory in Egypt by dissolving the waste in sodium hydroxide solution, precipitating aluminum hydroxide from sodium aluminate solution by CO 2 injection, followed by heat treatment at 600–1000 °C to produce gamma and alphaalumina Hazardous aluminum dross characterization and recycling 2021年10月1日 Aluminum electrolysis of China, solid waste, such as waste aluminum electrolyte, has been largely idled and caused serious environmental pollution In this paper, a novel approach is developed for achieving the separation/recovery of lithium from spent lithiumcontaining aluminum electrolyte by a sodium carbonate roasting–acid leaching processA novel approach for lithium recovery from waste lithium 2020年6月3日 Smelting slag is a typical hazardous waste generated in the smelting and metallurgy industry 1,2 Slag contains high concentrations of heavy metals, such as Cu, Zn, Cr and Ni, which are harmful if Highpurity recycling of hematite and Zn/Cu mixture from waste smelting

Efficient Recycling of Valuable Metals from Waste Copper Slag by
2022年6月21日 In this work, an innovative and carbonfree smelting reduction process is proposed to recycle valuable metals from waste copper slag using secondary aluminum dross as a reductant Experimental and thermodynamic investigations were carried out to understand the reaction and separation process and its correlation with smelting temperature, modified 2023年8月2日 Request PDF Sustainable Recovery of Fluorine from Waste Aluminum Electrolyte by Sulfuric Acid Baking The highvalue, green and harmless purification of aluminum electrolysis comprehensive Sustainable Recovery of Fluorine from Waste Aluminum Electrolyte 2024年1月23日 Copper smelting slag discharged from mining and highaluminum fly ash generated during the combustion of coal for energy production are two typical bulk solid wastes, which are necessary to carry out harmless and resourceful treatment This research proposed an ecofriendly and economical method for the coconsumption of copper smelting slag and high Preparation of Cementitious Materials from Mechanochemically 2023年6月2日 The effects of LiF, MgF2 and KF additions to the electrolyte on current efficiency were investigated during aluminium electrolysis using base NaF−AlF3−Al2O3 system with a cryolite ratio of 25 Efficient extraction and recovery of lithium from waste aluminum
.jpg)
Research Progress of Electrolytic Aluminum Overhaul Slag Disposal
2023年4月25日 As the main solid waste of the electrolytic aluminum industry, overhaul slag contains a large amount of hazardous 2013(5):2327 LI N, LI R X, XIE G, et al Separation of carbon and electrolyte in waste cathodes of aluminum electrolysis by flotation method[J] Light Metals, 2013(5):2327 doi: 103969/jissn10021752201305 2018年5月1日 Gallium is a rare metal with a low melting point that blends easily with most elements to form lowmelting alloys (Moskalyk, 2003)Due to this property, gallium and gallium compounds are commonly used in the industry and medical fields (Gupta et al, 2007), for example, radioactive gallium (Ga) is used in nuclear medicine to detect and localize malignant Gallium recovery from aluminum smelting slag via a novel 2022年9月25日 Iron in CSS mainly exists in the form of complex iron oxides such as iron olivine rather than magnetite or hematite, which is difficult to be recovered efficiently by traditional beneficiation methods (Li et al, 2021)In order to separate iron from CSS, it is necessary to convert the complex iron oxide into metal iron or ferric oxide, and then recover it through Extraction and separation of copper and iron from copper smelting slag 2016年12月2日 Air–water models have been widely applied as substitutes for CO2–cryolite systems in the study of the complex bubble dynamics and bubbledriven flow that occurs in the molten electrolyte phase in the aluminum electrolytic process, but the detailed difference between the two systems has not been studied This paper makes a numerical comparison between the Numerical Modeling of Flow Dynamics in The Aluminum Smelting
.jpg)
Recovery of Aluminum from Industrial Waste (Slag) by Melting
Slag of aluminum is a residue which results during the melting process of primary and secondary aluminum production Salt slag of aluminum is hazardous solid waste according to the European Catalogue for Hazardous Wastes Hence, recovery of aluminum not only saves the environment, but also has advantages of financial and economicJOEM Volume 56, Number 5S, May 2014 The Aluminum Smelting Process The principal technological change was in preparation of the carbon anode from petroleum coke and pitch The anode is slowly The Aluminum Smelting Process ResearchGateAluminium smelting is the process of extracting aluminium from its oxide, alumina, generally by the HallHéroult processAlumina is extracted from the ore bauxite by means of the Bayer process at an alumina refinery This is an electrolytic process, so an aluminium smelter uses huge amounts of electric power; smelters tend to be located close to large power stations, often Aluminium smelting Wikipedia2018年4月8日 The main waste of secondary Al production is the nonmetallic residue coming from scrap smelting It is often termed “salt cake” or “salt slag” and contains 5–7% of residual metallic aluminum, 15–30% aluminum oxide, 30–55% sodium chloride, 15–30% potassium chloride and, depending on the initial scrap type, carbides, nitrides, sulfides, and phosphides [ Preparation and Melting of Scrap in Aluminum Recycling: A Review
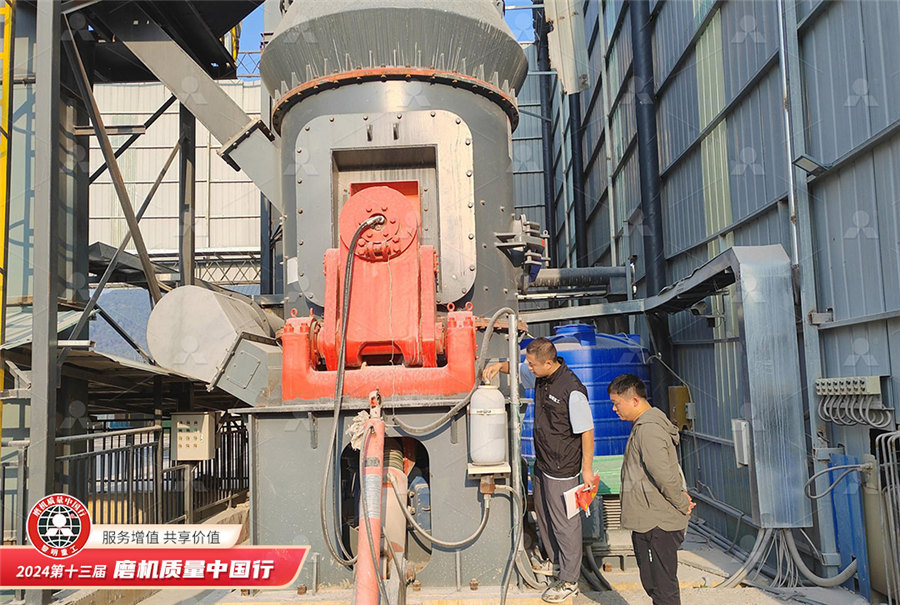
Guide to Modern Smelting Processes CED Engineering
Guide to Modern Smelting Processes – T09002 3 • Environmental Impact: Smelting processes can have environmental consequences, including emissions of greenhouse gases and other pollutants Modern smelting endeavors to mitigate these impacts through cleaner technologies and sustainable2019年4月17日 Aluminium is produced by electrolysis using alumina (Al2O3) as raw material and cryolite (Na3AlF6) as electrolyte In this HallHéroult process, the energy consumption is relatively large, and Sustainable wastetreatment procedure for the spent potlining