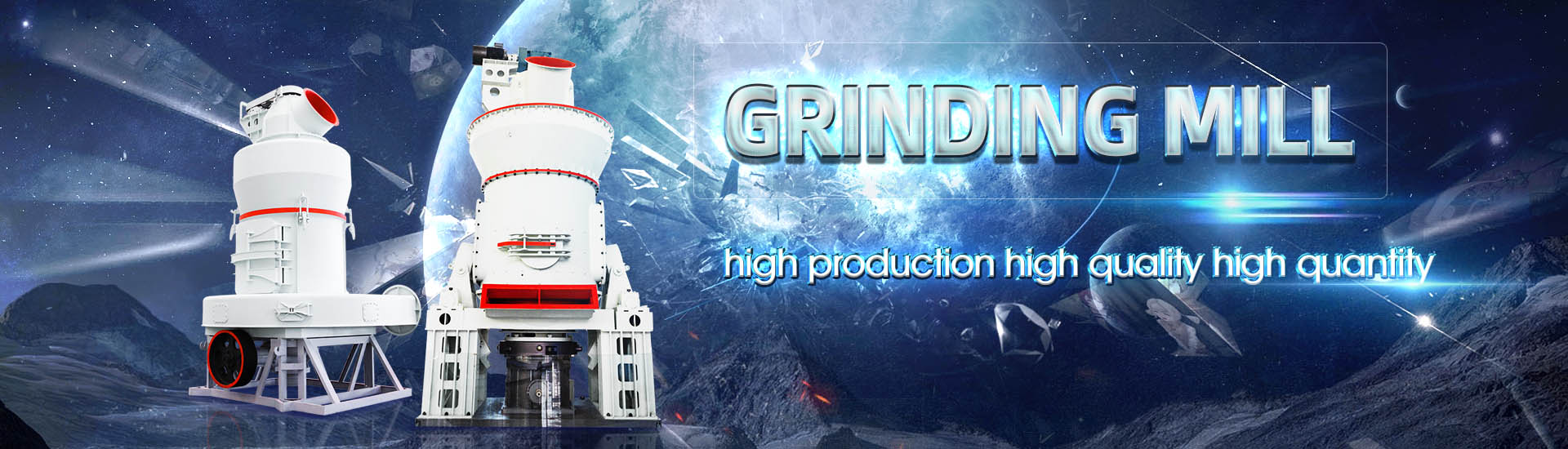
Gear clearance adjustment in grinding production line
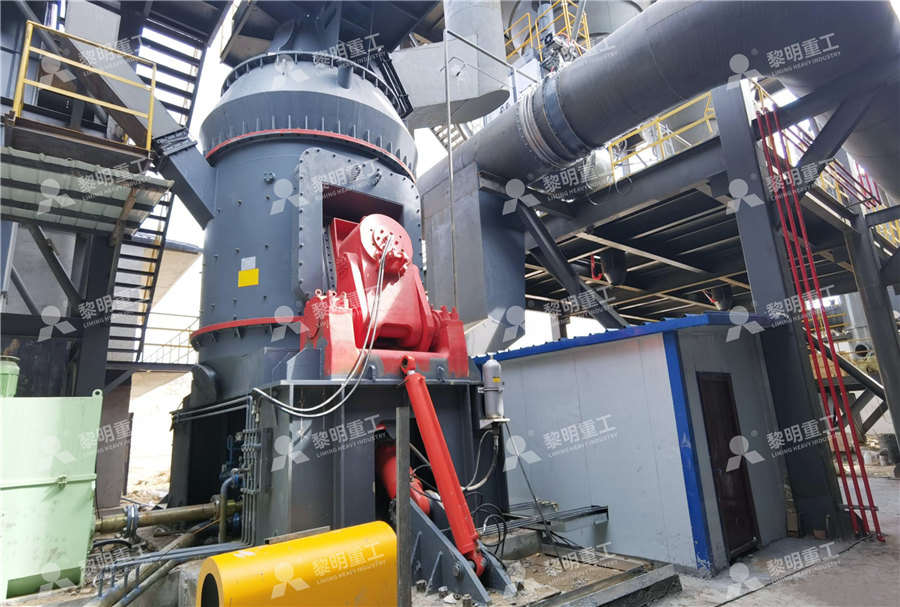
Process Adjustment and Monitoring in the Gear Grinding Process
This case study about gear grinding process has two purposes We indicate the effectiveness of using process adjustments with different parameters depending on machining positions for decreasing process variations2015年10月16日 With the help of this method, it is easy to control and adjust the process so that no defects are produced due to insufficient cooling or a worn grinding wheel The method also Effective Methods for Checking Grinding Quality GearThis paper proposes a quantitative correction method based on the grinding error of a cycloidal gear This method allows the error in machinetool grinding settings to be quickly and Quantitative correction method for the grinding errors of cycloidal This research shows whether feedback adjustment is effective for the process and then shows appropriate control characteristics, other than quality characteristics, for the use of T 2Q Process Adjustment and Monitoring in the Gear Grinding Process
.jpg)
A novel correction method to attain even grinding allowance in
2022年5月1日 In this paper, a novel method for designing the conical skiving cutter with a predefined grinding allowance of skived gear by modifying the normal rack is firstly proposed The To achieve an optimal working condition, one needs to understand the relationship of grinding parameters like chip thickness, surface speed, specific material removal rate and the Optimization of Generation Gear Grinding Process Gear 2022年5月11日 This research shows whether feedback adjustment is effective for the process and then shows appropriate control characteristics, other than quality characteristics, for the Process Adjustment and Monitoring in the Gear Grinding Process2021年1月5日 This investigation shows how the condition of abrasive tools and workpiece quality are evaluated by means of process near acoustic emission sensor application and In‐process evaluation of continuous generating gear grinding for
.jpg)
A novel correction method to attain even grinding allowance in
2022年5月1日 In practical applications, uneven gear profile deviations caused by the asymmetric cutting edge of a skiving cutter affect gear profile accuracy and finishing cost Therefore, this grinding wheel is also showing a rapid increase among highprecision gear processing methods for mass production such as honing, carbide skiving hobbing, etc Mitsubishi Heavy Industries, Latest Technologies for HighPrecision, HighEfficiency Gear 2010年5月1日 In our comparison of continuous generating grinding to the discontinuous profile grinding, special attention was given to the application of dressable grinding worms for gear diameters up to 1,000 mm and modules between 6 and 10 Fig 9: Gear and bore grinding machine ZP10B with quick runout alignment device DressingGrinding Large Module Gears Gear Solutions Magazine Your 2024年11月5日 31 Form Grinding When using a form grinding machine for gear modification, the conventional method is to use a diamond roller to dress the grinding wheel, and then the grinding wheel grinds the gear to complete the modification []One of the disadvantages of this method is that if you want to get different gear profiles, you must use different diamond wheels HighSpeed and LowNoise Gear Finishing by Gear Grinding and
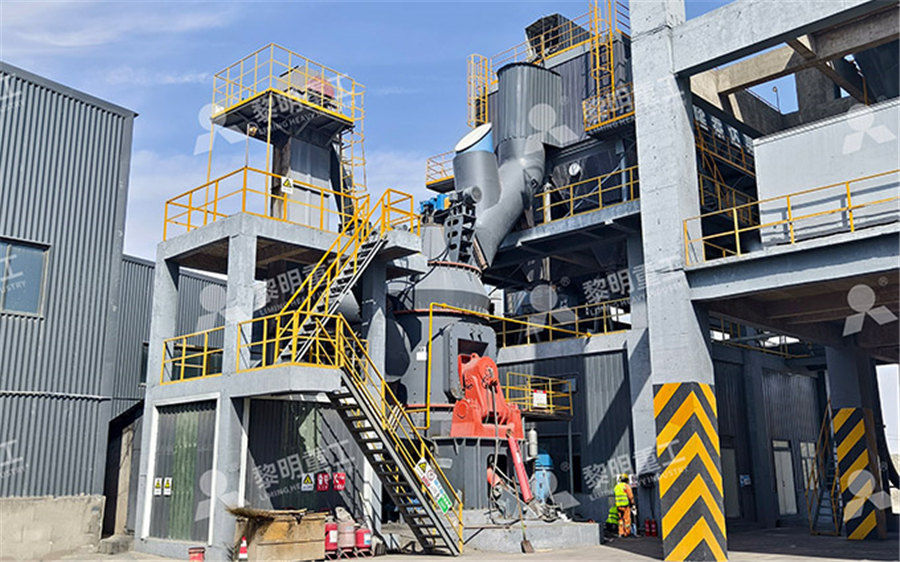
Effective Methods for Checking Grinding Quality
2015年10月16日 Reducing the speed of the grinding process will most likely yield highquality products, but the productivity goes down It is vital to the component lifetime and safety that possible defective parts are picked out of 2011年12月8日 The grinding stock is removed on the convex flanks and the concave flanks in two separate passes, which can be accomplished in a “uproll > convex, downroll > concave” grinding In cases of large bevel gear grinding with high amounts of stock removal, the single side grinding can be viewed as an advantage that contributed to high Cyclocut Bevel Gear Production2019年1月1日 There is a linecontact between tool and workpiece The flexibility of these processes is decreased Discontinuous Profile Grinding With discontinuous profile grinding, the tooth flanks of a gear can be either ground separately or joint depending on the number and setup of the grinding wheels, Fig 4 (Abler et al 2004)Gear Grinding SpringerLink2016年1月27日 4 Gear Grinding 41 What is a Gear Grinder? Gear grinders are finishing machines that use a grinding wheel rotating at high speed to grind the surface of the gear (workpiece) teeth Gear grinders can be broadly divided into continuously generation grinders and profile grindersIntroduction to Machine Tools Used in Gear Processing YANMAR
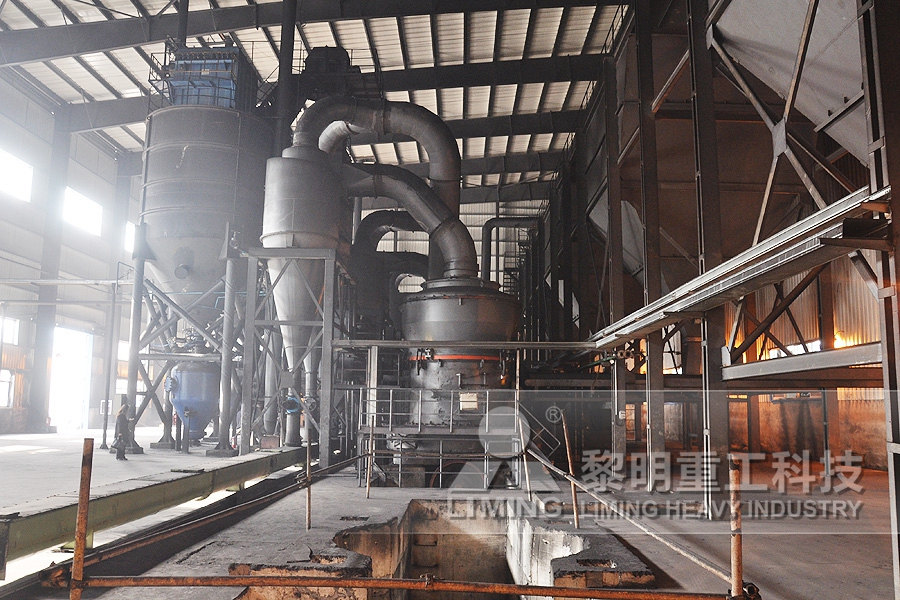
Latest Technologies for HighPrecision, HighEfficiency Gear Grinding
(MHI) has a product line that suits needs for mass production gear grinding consisting of the ZE series gear grinding machine for external gears and the ZI series gear grinding machine for internal gears We have further improved the efficiency and accuracy of the ZE series gear grinding machine for mass production of external gears in response Grinding Wheel Runout Clearance at Tooth Grinding Gear blanks with eon grinding small and medium production runs • NILES meets your requirements with a full line of automaticgrind'ers with gear diameter capacities from liZ' to 158"Gear Grinding Fundamentals Sep/Oct 1989 Gear Technologygrinding wheel ground 40 workpieces between dressing cycles According to the graph, the variation on both the right and left flanks is 2 μm or less, which means that the machine provides stable grinding precision even in highvolume gear production Moreover, ZE series grinders can finish approximately 8,000 gears per grinding wheel becauseGear Grinding Processing Developed for High Precision Gear in Generating Gear Grinding Matthias Ophey and Dr Jan Reimann One process for hard finishing gears is generating gear grinding Due to its high process efficiency, generating gear grinding has replaced other grinding processes such as profile grinding in batch production of small and middlesized gears Yet despite the wide industrialPrediction of Surface Zone Changes in Generating Gear Grinding
.jpg)
Gear Top Clearance XinLan Technology Co, Ltd
4 Calculation and Adjustment of Gear Top Clearance Accurate calculation and adjustment of gear top clearance are crucial in achieving optimal performance: Measurement techniques: Gear top clearance can be measured using methods such as the feeler gauge method or optical measurement methods, ensuring precise and reliable results2014年5月15日 Figure 17 and Figure 18 depict how tooth twist—or bias—is opposite when comparing profile grinding to generating grinding with a threaded grinding worm Machine Modern gear grinding machines of the KAPP KX Topological Gear Grinding Methodsthree locations across the face width of the gear Controlling Grinding Twist TCG grinding takes place on modern existing continuous generating gear grinding machines that possess the necessary kinematics to control twist Modification to the gear’s base pitch can serve to compensate for any resulting twist, or serve to create aTwist Control Grinding Gear TechnologyKeywords: Gear Grinding, Internal Gear, Threaded Grinding Wheel, Axial Stroke ABSTRACT tool component The internal gear grinding machine, ZI20A is the first of its kind that is applicable for mass production of internal gears It is suitable for grinding planetary gears, heattreated internal or external gears at high speeds withPROCESS ANALYSIS FOR INTERNAL GEAR GRINDING Nidec
.jpg)
Gear Grinding SpringerLink
2018年3月20日 There is a linecontact between tool and workpiece The flexibility of these processes is decreased Discontinuous Profile Grinding With discontinuous profile grinding, the tooth flanks of a gear can be either ground separately or joint depending on the number and setup of the grinding wheels, Fig 4 (Abler et al 2004)Gear grinding comes with unique production challenges today Customers often request higher and faster speeds for continuous generation gear grinding They also struggle to find a balance between productivity and quality requirements While many applications are utilizing gears in their less equipment, the quality and productionMaking Room for Productivity and Quality Requirements in Gear Grinding2 Profile equation of cycloidal gear with grinding settings as variables 21 Grinding motion analysis of cycloidal gear The grinding process for a cycloidal gear can be realized by simulating the planetary transmission of the cycloidpin gear During the transmission of the cycloidpin gear, the pin gear is fixed, and the cycloidal gear makes aQuantitative correction method for the grinding errors of 2024年2月16日 Gear tooth profile grinding, also known as form grinding, is a finishing method used in gear manufacturing It involves the use of vitrified bonded grinding wheels to modify or correct the profile of gear teeth, often after heat treatment The grinding wheel runs between two opposing teeth, grinding both surfaces at the same timeFour Tips to Optimize Quality and Reduce Cycle Time in Gear
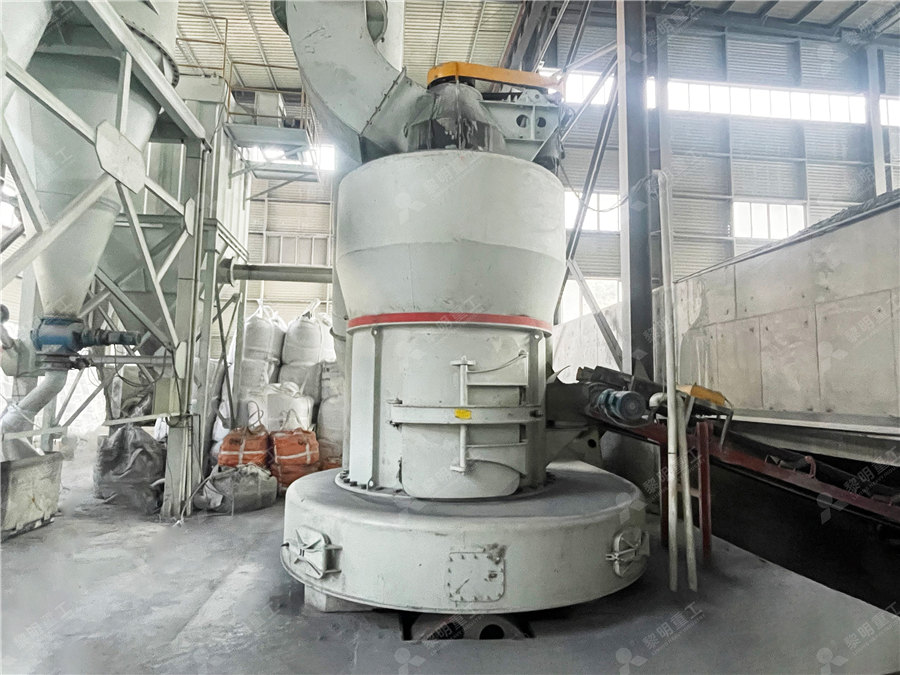
Gear Grinding Fundamentals Sep/Oct 1989 Gear Technology
Grinding Wheel Runout Clearance at Tooth Grinding Gear blanks with eon grinding small and medium production runs • NILES meets your requirements with a full line of automaticgrind'ers with gear diameter capacities from liZ' to 158"Process Adjustment and Monitoring in the Gear Grinding Process Kota Goto*, Fumiko Ogawa and Hironobu Kawamura 1 Nagoya Institute of Technology, Nagoya, Aichi, 4660061,Japan * Abstract: When a process demonstrates complex cause andeffect relationships, process adjustments are often used, such as automatic process Process Adjustment and Monitoring in the Gear Grinding in Generating Gear Grinding Matthias Ophey and Dr Jan Reimann One process for hard finishing gears is generating gear grinding Due to its high process efficiency, generating gear grinding has replaced other grinding processes such as profile grinding in batch production of small and middlesized gears Yet despite the wide industrialPrediction of Surface Zone Changes in Generating Gear Grinding2015年3月1日 One process for hard finishing gears is generating gear grinding Due to its high process efficiency, generating gear grinding has replaced other grinding processes such as profile grinding in batch production of small and Prediction of Surface Zone Changes in Generating
.jpg)
11 Steps of Gear Processing You Must Know
2023年8月25日 ordinary turning → gear hobbing → shaping → shaving → hard turning → geargrinding machining → honing → drilling → bore grinding → welding → measurement It is crucial to utilize the appropriate clamping Roller Adjustment Technology™ is an innovative technology ensuring efficient and consistent grinding operation, via detecting real time operation of the roller mechanisms by its ELS (Electronic Control System) The Roller Adjustment Technology™ consists of secondary subsystems and sensors below: Feed Roll Capacitance Sensor Spreading Paddle Roller Adjustment Technology Alapalain Generating Gear Grinding Matthias Ophey and Dr Jan Reimann One process for hard finishing gears is generating gear grinding Due to its high process efficiency, generating gear grinding has replaced other grinding processes such as profile grinding in batch production of small and middlesized gears Yet despite the wide industrialPrediction of Surface Zone Changes in Generating Gear Grinding2023年10月15日 Continuous generating gear grinding, sometimes referred to as CGG grinding, is one of several types of gear grinding, and it’s commonly used in highproduction applications It is a threadedwheel process that uses a largediameter grinding wheel with a thread preformed on the outside diameter, similar to a hobbing tool6 tips to optimize throughput in the CGG grinding process Gear
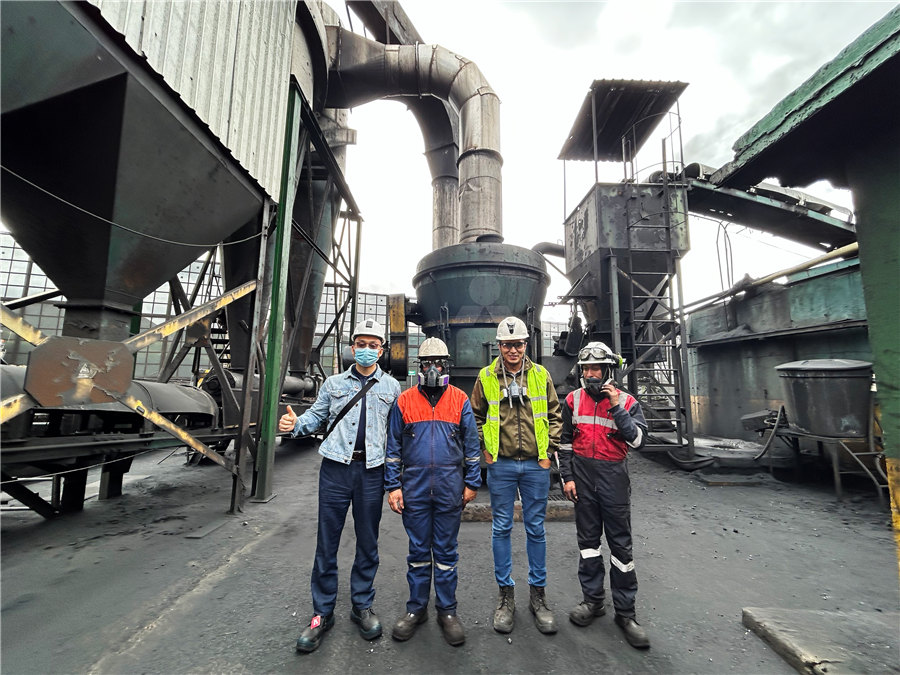
Gear Mesh Misalignment
2006年6月1日 These gear pairs were part of a large test program of the Army and NASA [1] and have subsequently been analyzed and tested at The Ohio State University [2] Figure 1 shows the transverse view of the helical gear pair with the superimposed line of action that is tangent to the base circles of the respective gears2020年10月1日 Most grinding machines and abrasive tools companies have not collected the grinding data during production and processing to achieve the “reuse” of the grinding processing data Some enterprises regard production practice data as enterprise secrets, which can only be circulated within the enterprise, and cannot realize the sharing and optimization of processing Intelligent technology in grinding process driven by data: A Over the last 15 years, gear skiving has established itself as a highly productive gear cutting process for the production of internal gears and gears with near interference contours As with all processes with crossed axes, gear skiving generally results in a pronounced natural twist when gears with lead crowning or other flank modifications are produced In practical applications, Gear skiving with minimum twist errors Forschung im 2007年12月1日 It does not seem practical to use segmented grinding wheels, which is why in the past a grinding method was never developed for Coniflex gears Even with a single grinding wheel that duplicated the enveloping internal cone surface of the cutting edges, a major obstacle occurs with respect to the dressing removal and the compensation thereofStraight Bevel Gears on Phoenix Machines Using Coniflex Tools Gear
.jpg)
Guidelines for Modern Bevel Gear Grinding
2008年8月1日 Figure 5—Surface structure after grinding (left conventional, right MicroPulse) Grinding Wheel Specifications and Performance Keys to efficient grinding are the abrasive material and the abrasive bond Recommended for Also, specify that the manufacturing process is to include grinding or lapping Controlling the accuracy of the gear assembly Specify adequate shaft parallelism and perpendicularity of the gear housing (box or structure) The features Mounting Accuracy of Gears KHK2008年2月1日 This gear pair has been tested, both at NASA [17] and at The Ohio State University and has been shown to be an extremely low noise gear set The modifications applied to this gear pair will be 178 micron of circular lead crown and 178 micron of circular profile crown as shown in Figure 3Microgeometry and Bias in Helical Gear Noise ExcitationsThe spectrum of topics ranges from process and tool design in line with requirements to the manufacturing of individual gear geometries and measures for continuous quality assurance In addition, aspects of digitalization and the improvement of sustainability in gear production and application will be presentedAachen Conference on Gear Production (ACGP)
.jpg)
Guidelines for Modern Bevel Gear Grinding August 2008 Gear
Modern Bevel Gear Grinding Dr Hermann J Stadtfeld Management Summary This paper acknowledges the wide variety of manufacturing processes—especially in grinding— utilized in the production of bevel gears and that gear designers and engineers cannot always be expected to have an informed understanding of them2023年5月23日 A gear grinding wheel is one of the most important and expensive elements of the gear grinding system based on a CNC machine tool Various gear grinding wheels are used, including costly ones: highly porous, solgel corundum, monocorundum [1, 2], cubic boron nitride wheels [], etcThe case study proposed makes it possible to evaluate the technical Just in Time Gear Grinding Wheel Dressing SpringerLink2018年5月15日 Figure 8: Water soluble coolant system for gear grinding Small Changes = Big Improvement The many small changes add up to a new stateoftheart in gear grinding With the emphasis on reliability and consistent productivity, the ZE16C and 26C represent the newest developments in gear grindingContinuous improvement in generating gear grinding2022年5月12日 How to improve the dressing method has become a key technology for highprecision flex and circular rigid splines with involute tooth profile in gear form grinding, where the machining precision mainly depends on dressing accuracy of the grinding wheel Based on the geometric principle (ie, a spatial straight line changes to quadric conical surface by A highprecision fitting and dressing method for the flex and
.jpg)
Putting Teeth into Gear Inspection
2011年8月5日 The Optiv line of multisensor measuring systems from Brown Sharpe can dimensionally inspect 2D and 3D features of a microgear to the tightest production tolerances (Figure 3) Figure 3: The Leica TProbe, a wireless probe, Gear fabrication methods have been typically classified into three main categories: generation, forming, and form cutting Gear forming creates gears without using cutting tools (ie casting, forging, powder metallurgy, 3D printing) Gear form cutting involves tools that are used to create the gear profile (ie gear milling, broaching, and EDM)Gear Manufacturing: Definition, Processes, and Materials