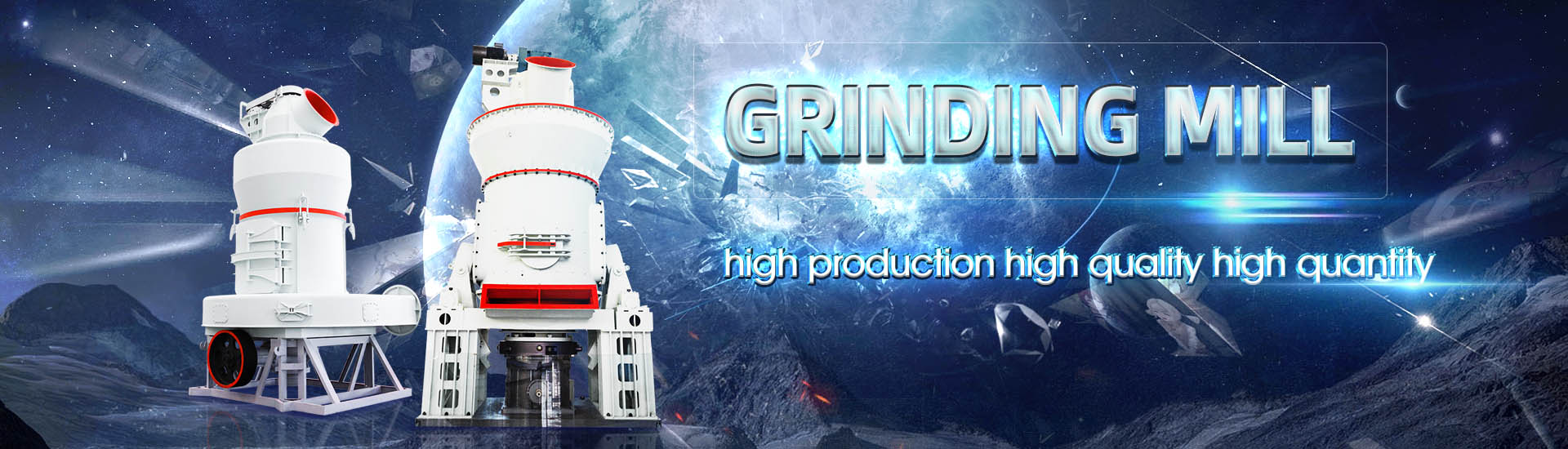
The purpose of material grinding in cement production
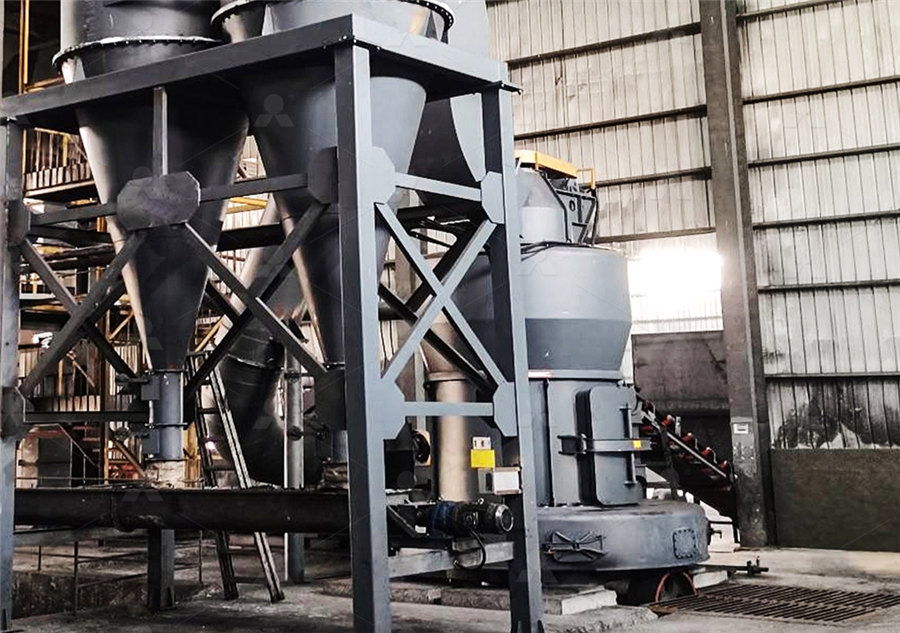
Grinding in Cement Manufacturing: Key Process, Types of Mills,
Grinding plays a pivotal role in the cement manufacturing process, transforming raw materials into a fine powder suitable for creating cement It’s a crucial step that directly impacts the physical properties of the final product, including strength, durability, and workability2023年8月21日 How does the grinding process contribute to the production of highquality cement? The quality of cement depends on its reactive properties and particle size grinding helps to reduce the size of the clinker particles and Grinding process is a critical stage in cement productionHighly energy intensive unit operation of size reduction in cement industry is intended to provide a homogeneous and super fine (30004000 Blain) cement Grinding operation is monitored for Cement Grinding Cement Plant Optimization2023年10月19日 Clinker grinders are an important part of the cement manufacturing process They are used to grind clinker into a fine powder and are typically located at the end of the cooler in a cement plant Clinker is a nodular Understanding the Role of Clinker Grinding in Cement
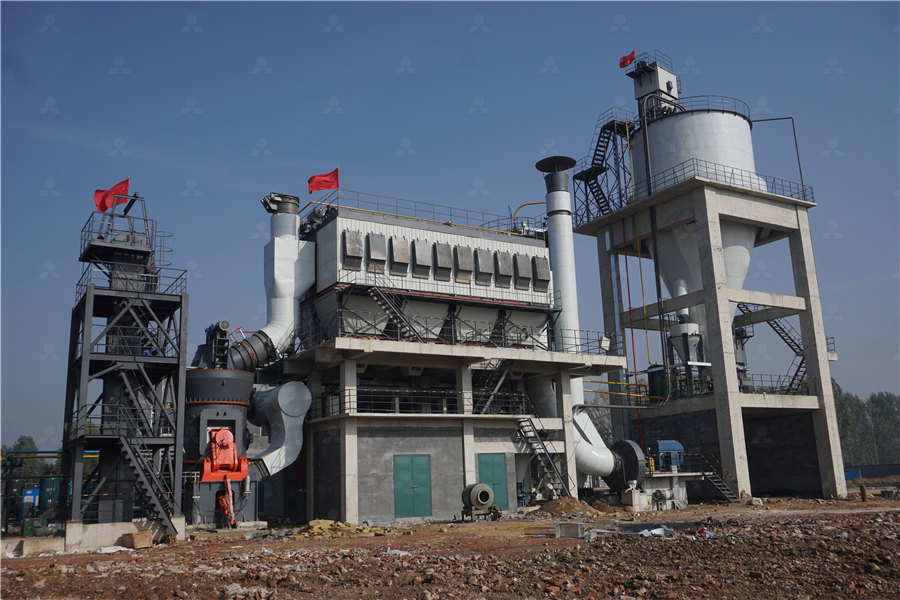
Overview of cement grinding: fundamentals, additives,
2017年5月19日 Grinding is an essential operation in cement production given that it permits to obtain fine powder which reacts quickly with water, sets in few hours and hardens over a period of weeksIn raw grinding, a ball mill with a high efficiency separator is used to achieve uniform particle size in raw mix for the next stages of the manufacturing process At the Cement Grinding Stage, 90 – 95% of the clinker is mixed with gypsum Cement Grinding Unit Process High Quality Cement 2019年1月3日 Clinker grinding technology is the most energyintensive process in cement manufacturing Traditionally, it was treated as "low on technology" and "high on energy" as grinding circuits use more than 60 per cent of total energy Clinker grinding technology in cement manufacturing2004年11月1日 There is potential to optimise conventional cement clinker grinding circuits and in the last decade significant progress has been achieved The increasing demand for “finer Cement grinding optimisation ScienceDirect
.jpg)
Comprehensive understanding of grinding aids
2014年6月1日 Grinding aids increase the productivity and costeffectiveness of cement production A comprehensive experimental test program and a variety of computer simulations were used to2014年10月15日 The objective of the study is to reveal these differences by means of conducting the industrial scale test studies around a cement grinding circuit for a given cement The influences and selection of grinding chemicals in cement strengths of a blended cement with a high slag content All the main cement characteristics are reported as follows: Table 1: Cement production properties Cement type CEM III/B 42,5 N Blaine 4500 cm2/g Recipe Clinker 33%, Gypsum 2%, Slag 65% Mill output 57 t/h Compressive strengths 2days 11 MPa 7days 30 MPa 28 days 43 MPaImprovement of cement performances through the use of grinding Among the major raw materials required for cement production, limestone, sandstone, and gypsum are abundantly available in Debra As it was observed from the preliminary geological survey of the raw materials study, [this study Cement Manufacturing Process INFINITY FOR
.jpg)
What is Cement Milling? ball mills supplier
The cement milling process is a critical step in cement production that involves grinding and blending materials to create the final product The purpose of cement milling is to achieve a specific particle size distribution (PSD) that allows the cement to 2017年5月19日 Grinding is an essential operation in cement production given that it permits to obtain fine powder which reacts quickly with water, sets in few hours and hardens over a period of weeks i Overview of cement grinding: fundamentals, additives, technologiesModern grinding and separating plant incorporating technological improvements is also used for grinding phosphate rock, chemical fertilisers, coal for power stations, limestone and other materials Advances include increases in the scale and automation of ball mills and development of high efficiency separators vertical roller mills and high pressure roll presses for both raw and The Cement Production ProcessSo next, we will have a detailed understanding of the clinker calcination and cement production process Cement Production Process The cement production processes mainly include raw material crushing and storage, raw material proportioning and grinding, clinker calcination, clinker grinding, cement packing, etc Portland cement is the most Cement Clinker Calcination in Cement Production Process AGICO Cement
.jpg)
Cement: History, Types, Manufacturing Process Science Info
2023年8月15日 Steps of Manufacturing Cements Extraction of Raw Materials The production of cement involves the utilization of a blend of raw materials, typically comprising calcium, silicon, iron, and aluminum The essential components necessary for this procedure encompass limestone, clay, and sand Limestone is frequently employed as a calcium source2024年11月23日 Cement Extraction, Processing, Manufacturing: Raw materials employed in the manufacture of cement are extracted by quarrying in the case of hard rocks such as limestones, slates, and some shales, with the aid of blasting when necessary Some deposits are mined by underground methods Softer rocks such as chalk and clay can be dug directly by Cement Extraction, Processing, Manufacturing Britannica2014年6月1日 Grinding aids are materials that are added to cement mixtures to improve the characteristics of the cement or increase the efficiency of the milling systems or both in the clinker grinding (finish Comprehensive understanding of grinding aids ResearchGate2018年8月1日 In fine grinding of cement in a ball mill, it is sometimes impractical to grind finer in a dry state Even though the chemical reactivity requires the material to be dry ground, it is sometimes Effect of Grinding Aids in Cement Grinding ResearchGate

(PDF) Advancements in Cement Technology: A
2023年12月1日 Concrete made of cement is the most adaptive material for construction purpose Design and Preparation of such a concrete mix with good strength and durability has been always the need of the dayThe major raw materials used in the manufacture of cement are Calcium, Silicon, Iron and Aluminum These minerals are used in different form as per the availability of the minerals Table shows the raw materials for Portland cement Manufacture of Cement Materials and Manufacturing 1 The basics of cement manufacture – 2 History of cement manufacture – 3 Portland cement in today’s world 2 Raw materials management system – 22 Concrete problems 16 1 Raw materials – 2 Raw mix – 3 Reserves – 4 Crushing – 5 Drying – 6 Preblending – 7 Storage and handling 3 Raw milling and blending 3The Cement Plant Operations Handbook International Cement 2021年4月2日 1111 Chemical Compositions Four main compounds make up Portland cement They include tetracalcium aluminoferrites (4CaOAl 2 O 3 Fe 2 O 3), tricalcium aluminates (3CaOAl 2 O 3), dicalcium silicates (2CaOSiO 2), and tricalcium silicates (3CaOSiO 2) (Demis et al 2014)These compounds are abbreviated as C 3 S, C 2 S, C 3 A, and C 4 AF, Introduction to the Principles of Cement and Concrete Composites
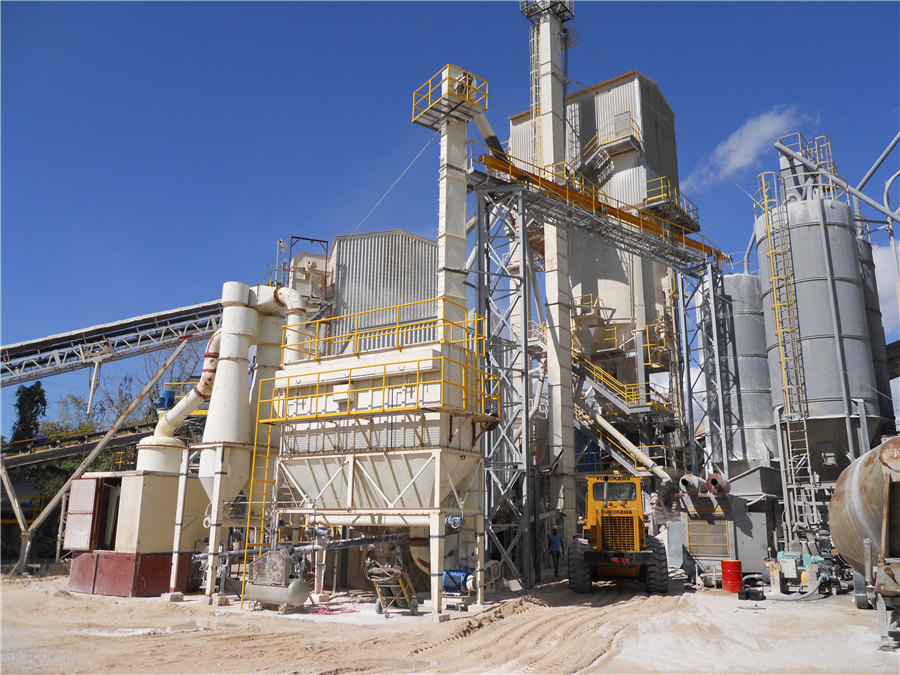
What are the Roles of Gypsum in Cement Production
Gypsum can be used as a raw material, mineralizer, retarder and activator in cement plants Among the components, SO 2 is used to balance the sulfuralkali ratio in the calcining of clinker and improve the calcining operation and the service life of refractory materials Roles of gypsum: 1 As a raw material, it can be used in the production of CSA cement, slaggypsum cement, During the cement manufacturing process, upon the cooling of clinker, a small amount of gypsum is introduced during the final grinding process Gypsum is added to control the “setting of cement” If not added, the cement will set immediately after What is the purpose of adding gypsum in cement?2016年10月5日 In this chapter an introduction of widely applied energyefficient grinding technologies in cement grinding and description of the operating principles of the related equip‐ ments and comparisons over each other in terms of grinding efficiency, specific energy consumption, production capacity and cement quality are given A case study per‐ formed on a EnergyEfficient Technologies in Cement Grinding2019年1月3日 Clinker grinding technology is the most energyintensive process in cement manufacturing Traditionally, it was treated as "low on technology" and "high on energy" as grinding circuits use more than 60 per cent of total energy consumed and account for most of the manufacturing cost Since the increasing energy cost started burning the benefits significantly, Clinker grinding technology in cement manufacturing
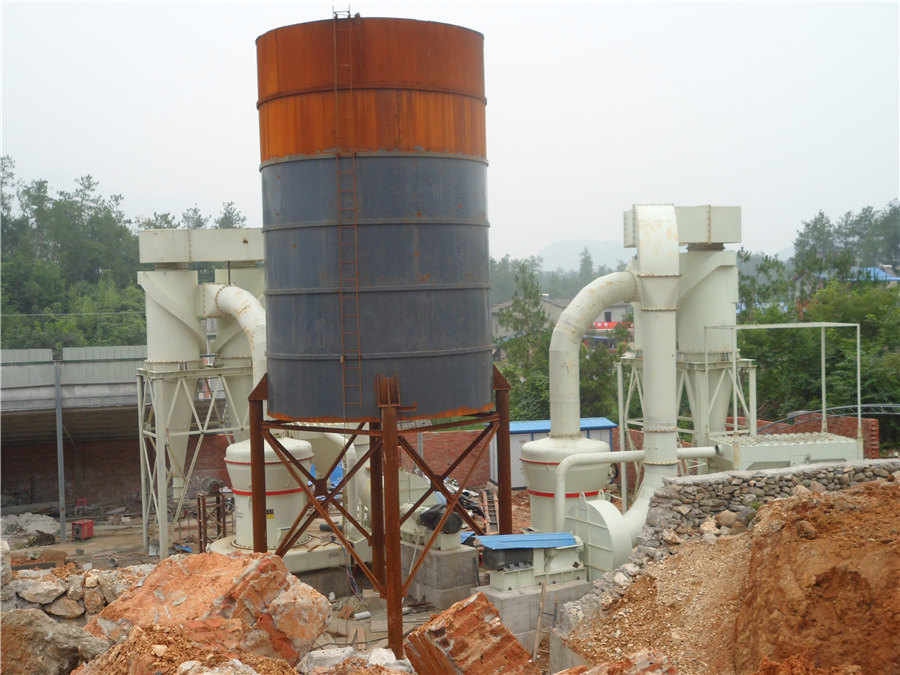
Manufacturing the cement kiln Understanding Cement
Articles like this one can provide a lot of useful material However, reading an article or two is perhaps not the best way to get a clear picture of a complex process like cement production To get a more complete and integrated understanding of how cement is made, do have a look at the Understanding Cement book or ebook2023年8月23日 The production process of a cement ball mill involves raw material preparation, grinding, linearization, clinker grinding, and the eventual storage and distribution of the finished cement product This process is integral to the production of cement, a vital building material that plays a central role in construction and infrastructure development around the worldWhat Are the Parts of a Cement Mills? Cement Ball Mill Production The production of cement is rather complex process which includes a high amount of raw materials (eg, limestone, marl, clay, and iron ore), heat, electricity and different fuels (petroleum coke IDENTIFYING ENVIRONMENTAL IMPACTS OF CEMENT PRODUCTION 2015年8月1日 The results show that approximately 248t, 469t, and 341t of materials are required to produce a ton of the product in raw material preparation, clinker production, and cement grinding stages (PDF) Analysis of material flow and consumption in
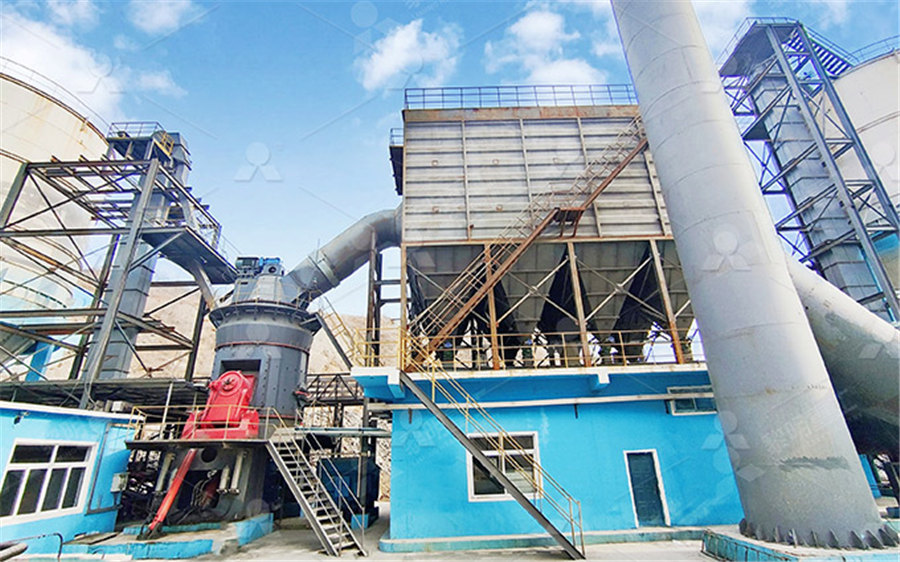
Coprocessing of Grinding Sludge as Alternative Raw
Ordinary cement raw meal and grinding sludge analysis: The ordinary cement raw meal was collected from a Thailand’s local cement plant in, 2007 The chemical compositions of the ordinary cement raw meal were analyzed by Thermo 2022年4月6日 6 Grinding of Clinker: • Cooled clinker is ground along with 3 5 % gypsum in a cement grinding mill (ball mill / VRM/ Roll press combined with a ball mill) to a fine powder, known as cement 7 Storage of Cement: • The ground cement is stored in cement silos (having different compartments) from where it is fed to packer machines 8From raw materials to 8 steps of cement manufacturing, read2021年12月6日 In the production of Portland cement, grinding aids are added in small amounts in the range of 001 to 010% by weight of cement, according to the PNEN 1971 standard They allow a larger specific surface area to be obtained by the material in a shorter grinding time, which reduces energy consumptionThe Effect of Various Grinding Aids on the Properties of Cement Clinker is a nodular material produced in the kilning stage during the production of cement and is used as the binder in many cement products The lumps or nodules of clinker are usually of diameter 325 mm and dark grey in color It is produced by heating limestone and clay to the point of liquefaction at about 1400°C1500°C in the rotary kiln What is Cement Clinker? Composition, Types Uses
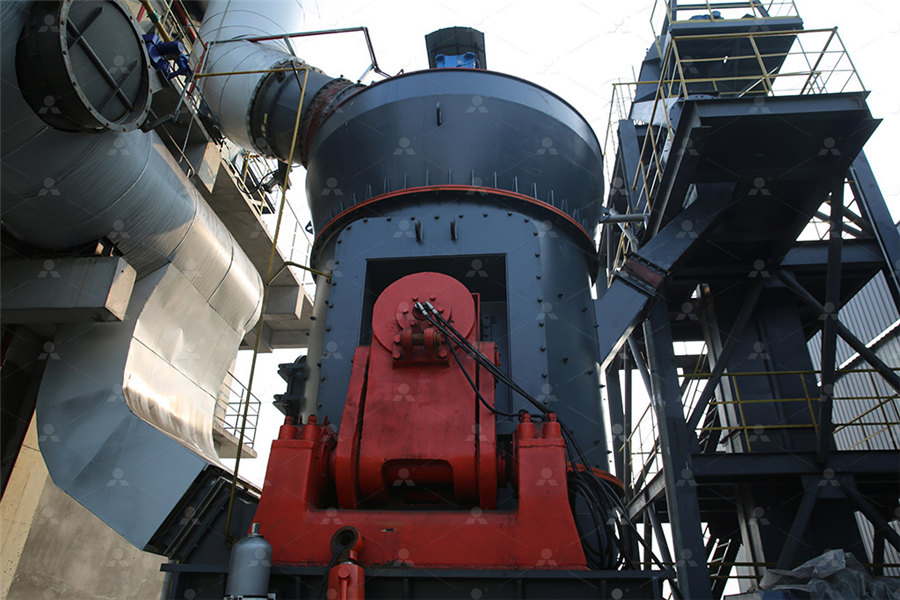
A study of different grinding aids for lowenergy cement clinker production
2023年10月23日 The cement properties of the mortar samples produced by separate ultrafine grinding do not essentially differ from those of a reference material, provided that there is no significant difference 2023年1月1日 Grinding aids are materials that are added to cement mixtures to improve the characteristics of the cement or increase the efficiency of the milling systems or both in the clinker grinding (finish (PDF) EFFECTS OF VARIOUS GRINDING AIDS DOSAGE ON2023年5月27日 Step 3: Cement raw material homogenization and fine grinding The cement raw materials (limestone, clay, etc) are sent to the batching station for homogenization, and then the homogenized raw materials are sent to a ball mill for fine grinding according to a certain feeding amount to obtain raw meals Step 4: Clinker calcination2 Major Roles of Limestone in Cement Manufacturing2021年11月15日 It includes from mining to the production of clinker in cement kiln, excluded the blending and grinding of clinker and other raw material for cement production Valderrama et al (2012) Spain: It includes raw materials extraction to cement production, including waste from refuse as secondary materials and alternative fuelsA review of the effectiveness of Life Cycle Assessment for gauging
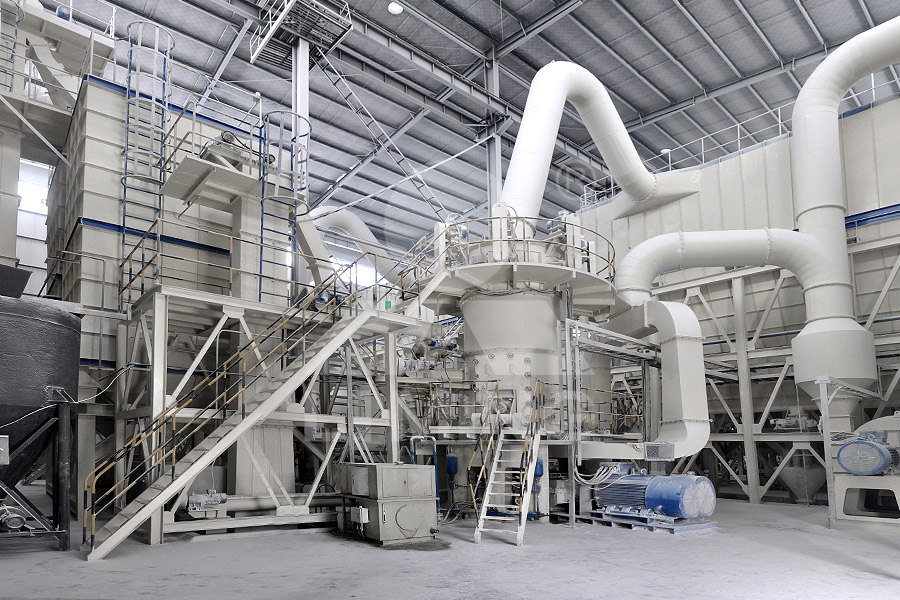
Uses of Gypsum in Cement BricknBolt
2024年8月20日 In 2024–2025, cement production is estimated to increase by around 491 MT, of which the cement industry alone will need 196–246 MT Gypsum is an important element that has many uses in cement, read on to For example, in the dry process of cement production, the raw meal is ground into powders, while in other cement production methods, slurry, spherical, and massive raw meals are also commonly seen However, no matter what form Cement Raw Meal Homogenization Process in The 2003年6月5日 Required water:cement ratio to achieve a slump of 60 to 70 mm in concretes made with different cements Cement E contained a limestone not conforming to the EN 1971 criteriaThe Use of Limestone in Portland Cement: A State 2015年12月9日 Raw materials are used to produce the main cement elements (Mohsen, 2015) • Quarry The process of obtaining raw materials for cement manufacturing involves mining and quarrying natural materials (PDF) Cement Manufacturing ResearchGate
.jpg)
How Cement is Made Cement Manufacturing Process
Stage of Cement Manufacture There are six main stages of the cement manufacturing process Stage 1: Raw Material Extraction/Quarry The raw cement ingredients needed for cement production are limestone (calcium), sand and clay (silicon, aluminum, iron), shale, fly ash, mill scale, and bauxite The ore rocks are quarried and crushed into smaller pieces of about 6 inchesThe purpose of the training is to Identify and understands necessary known and unknown information towards the completed cycle of the grinding system, whether is a ball or vertical mill Throughout the course the lectures are supplemented with exercises and case studies, allowing the participants to relate the course material to their cement grinding facility and as a result CEMENT GRINDING COURSE The Cement InstituteThey calculated the material efficiency and waste recycling rates for each stage and production unit The results showed that approximately 248, 469, and 341 tons of materials are required to produce one ton of product in the raw material preparation, clinker production, and cement grinding stages, respectivelyAnalysis of Material Flow and Consumption in Cement Production Learn about our cement grinding process and plant stages for high quality cement Amrit Support About Amrit Support; Services; Activities; Corporate Annual Return FY 202021; FY 202122; FY 202223; The cement mill grinds all materials Cement Grinding Unit Process High Quality Cement Grinding
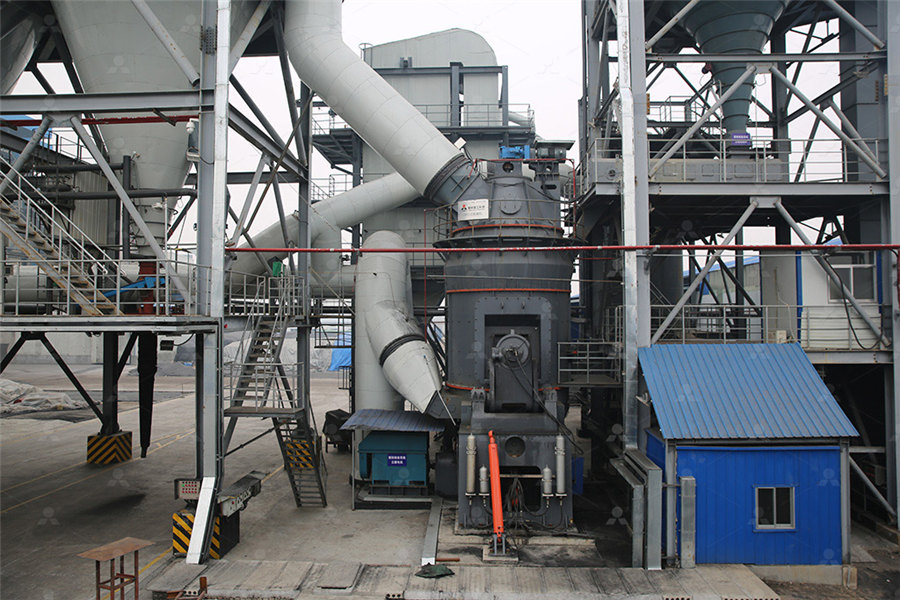
Cement Roller Press Roller Press In Cement Plant Roller Press
Semifinishing grinding system: after ground by cement roller press, materials are divided into three parts through an air classifier: coarse, medium and fine, in which the coarse material is returned to the roller press for regrinding, the medium material is put into a ball mill for further grinding, and the fine material is directly discharged as the finished cement product2022年6月30日 Moreover, common materials used in cement production are limestone, shells, chalk, shale, clay, slate, blast furnace slag, silica sand, and iron ore Extraction and Processing of Raw Materials Cement manufacturing demands naturally occurring rocks and The Manufacturing Process of Cement in Factory