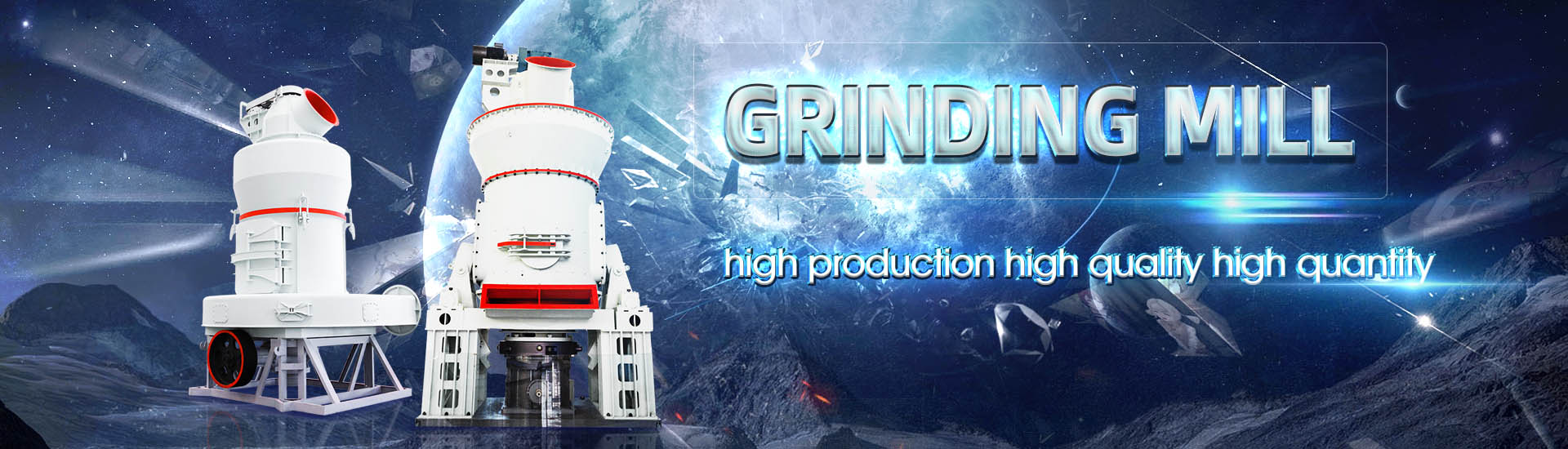
A cement crushing mill with a diameter of 3.2 meters x 3.0 meters needs an induced draft fan.
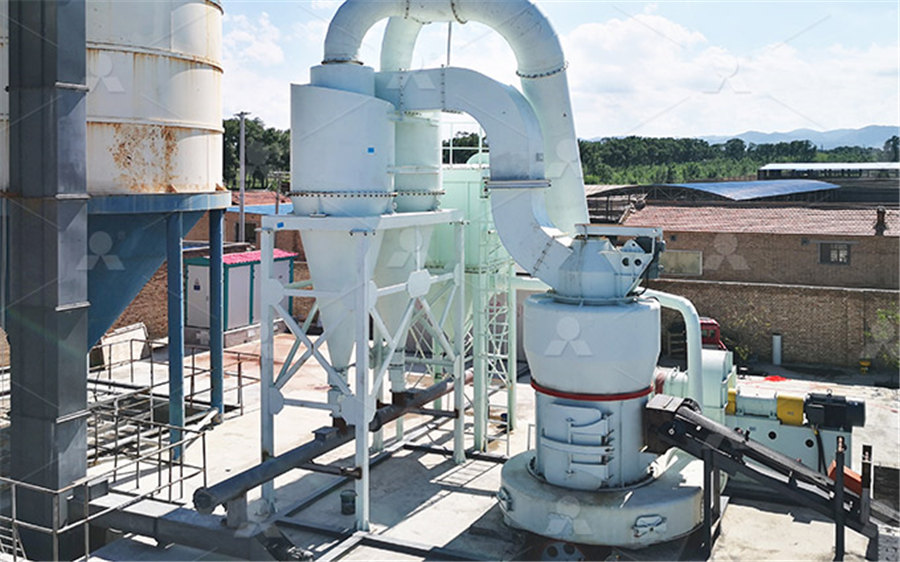
Complete Lecture about Crushers in Cement Industry
Size reduction is performed in crushers and grinding mills Crushing is comminution in the coarse range, whereas grinding refers to comminution in the fine range The technique of size In this paper, the specific electrical energy (CEES) of the cement crusher has been modeled and optimized as a function of feed flow, separator speed and air flow using the experimental Cement Industrial Process: Modeling and Optimization of the Ball mills and grinding tools Cement ball mills are typically twochamber mills (Figure 2), where the first chamber has larger media with lifting liners installed, providing the coarse grinding BALL MILLS Ball mill optimisation Holzinger Consulting2022年8月1日 Ball mills are designed according to the input grain size, production rate, environmental restrictions, and spatial installation restrictions The ball mill understudy has, as Failure analysis of a ball mill located in a cement’s production line
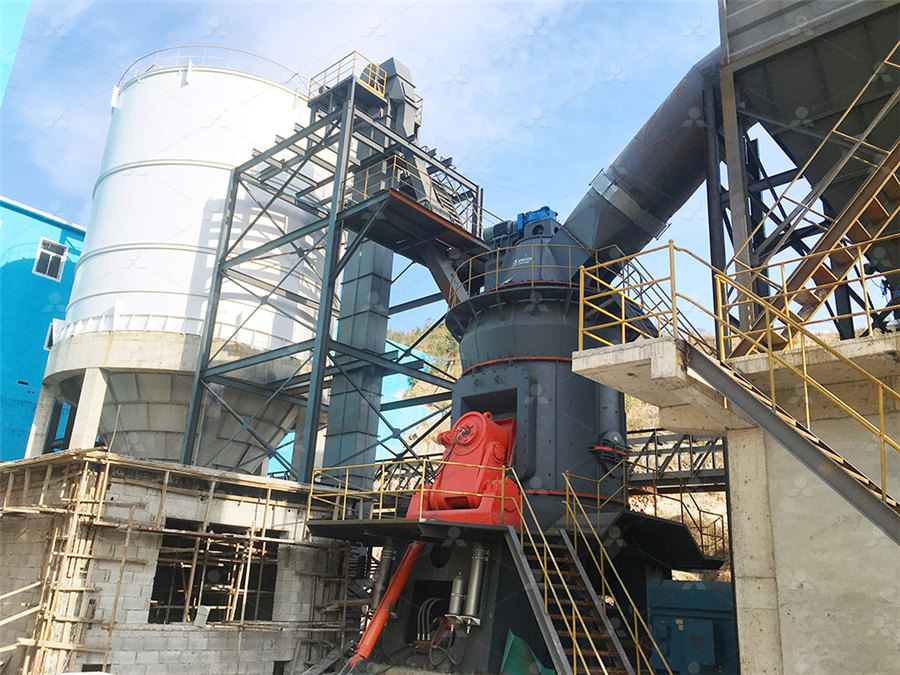
Energy and exergy analyses for a cement ball mill of a new
2020年5月1日 In this work, a cement ball mill (CBM) of a new generation cement plant is considered as a case study in order to study its efficiency based on both first and second laws 2021年1月1日 This paper discusses a range of available methods for measuring and calculating mill filling and introduces a new technique for accurately measuring filling that eliminates the An improved method for grinding mill filling measurement and This document discusses crushing and grading processes used in mining and cement production It describes several types of machines used for crushing hard materials, including jaw Crushing Screening of Hard Materials PDF Bearing In a cement plant, crushing is the primary sizereduction process carried out under the action of external mechanical forces Generally, three levels of crushing are recognized: coarse (top Everything you need to know about cement Materials Preparation
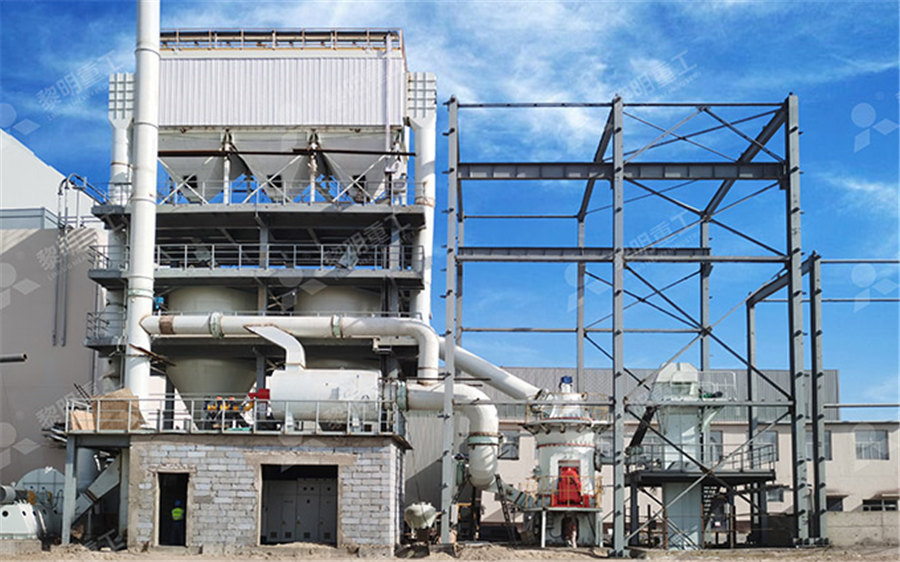
Optimization of A Fully AirSwept Dry Grinding Cement Raw Meal
This document discusses optimizing the production capacity of a fully airswept industrial scale twocompartment cement ball mill through simulation The mill has two compartments, with the 2019 The performance of a hammer mill fabricated in Uganda was evaluated and the optimal performance conditions were determined The evaluation was done with screen hole diameters (S) of 15, 20, and 30 mm, hammer tip speeds Design and Evaluation of Crushing Hammer mill2017年2月13日 The apparent difference in capacities between grinding mills (listed as being the same size) is due to the fact that there is no uniform method of designating the size of a mill, for example: a 5′ x 5′ Ball Mill has a working Ball Mills 911MetallurgistCyclone to homogenization silos by small induced draft (ID) fan under it Infrared measuring sensor with 3 0 c per second reaction time; Measuring range from 0 – 800 0 c and 500 – 1500 0 c; Coal Mill and Cement mill drying; Cement Manufacturing Process INFINITY FOR
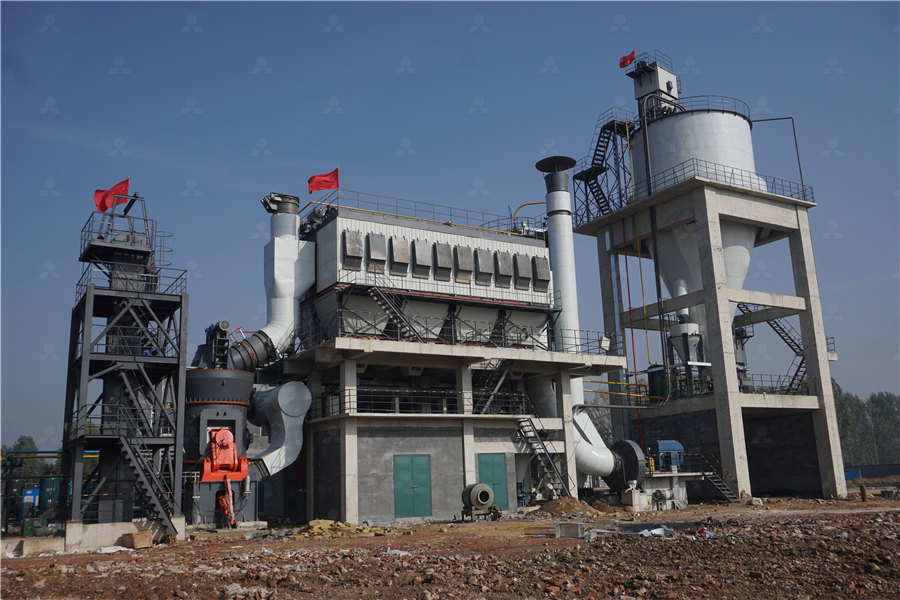
Energy and cement quality optimization of a cement grinding circuit
2018年7月1日 Among the industries, the nonmetallic industry was reported as the third largest energy user and accounted for about 12% of the global energy use [1]Within this portion, cement industry had the majority of the utilization with 85–12% [1], [2]US Energy Information Administration (EIA) [7] named cement industry as the most energy intensive among the The roller mill with a grinding table of 20 m and four externally mounted 10 m diameter x 04 grinding rollers, designed for a nominal throughput of 55 tph raw meal of less than 12% residue on 90 mm reached a throughput of 68 tph with specific power consumption of 1145 kWh/tEverything you need to know about cement Materials Preparation 2022年5月31日 Mineral crushing is the main source of energy consumption in mineral processing According to statistics, this consumption accounts for about 35–50% of the total cost of the mine (Curry et al, 2014), or even higherIt may also account for 18% of the global electrical energy consumption (NapierMunn, 2015)More efficient crushing equipment needs to be Analysis of vertical roller mill performance with changes in 2022年8月1日 The ball mill understudy has a length of 1307 m in its cylindrical geometry and a length between supports of 162 m (Fig 1 a,b)The formation of cracks in the middle span has been identified, generally spreading from the holes near the maintenance manhole, as shown in Fig 1 c Certified welders carry the repairing procedure using PERMA 622 electrodes [1]Failure analysis of a ball mill located in a cement’s production line
.jpg)
Ball Mill Design/Power Calculation 911Metallurgist
2015年6月19日 The basic parameters used in ball mill design (power calculations), rod mill or any tumbling mill sizing are; material to be ground, characteristics, Bond Work Index, bulk density, specific density, desired mill tonnage capacity DTPH, operating % solids or pulp density, feed size as F80 and maximum ‘chunk size’, product size as P80 and maximum and finally the type of 2022年9月24日 The diameter of a cement silo is mainly restricted by the transportation conditions, such as the limits of railroad vehicles, buildings, loading, bridges, and tunnels; Therefore, the diameter of the cement silo is less than or equal to 3 m Of course, if you have a sheet cement silo, you do not need to consider this problem The diameter of the Cement Silo Design Manufacturing Dry Mortar PlantClinker – 11 Finish mill – 12 Cement – 13 Quality control – 14 Packing and distribution – 15 Emission abatement (dust, NO x, SO 2, etc) – 16 Maintenance – 17 Process – 18 Materials analysis –19 Plant capacity summary – 20 Storage capacity 15 Cement plant construction and valuation 244 1 New plant construction – 2The Cement Plant Operations Handbook International Cement 2015年2月2日 As with any material, rock particles only break when the applied tensile stress exceeds the tensile strength of the rock However, in terms of comminution, the main interest is to derive reliable ways of assessing how a particular material breaks in a comminution device such as a crusher or a mill []In general, the breakage of rock particles is dependent on two factors: Comminution SpringerLink
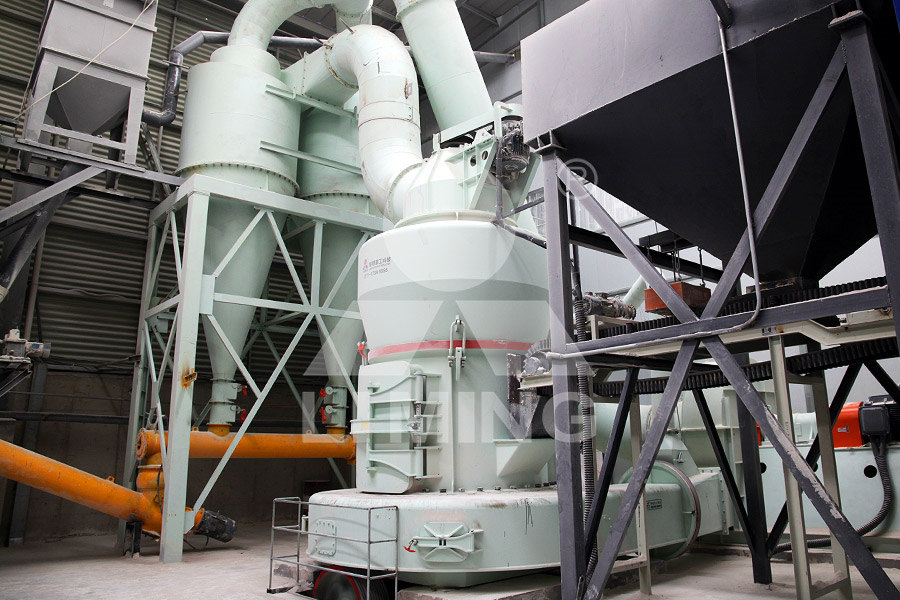
selection and purchasing guide of hammer crusher
Previous Post Next Post Contents1 selection and purchasing guide of hammer crusher 11 12 when to use Hammer Crusher ?13 Hammer crusher crushing concept14 Hammer Crusher classifications :15 11 Advantages and 2021年1月1日 India is the world's second largest producer of cement and produces more than 8 per cent of global capacity Due to the rapidly growing demand in various sectors such as defense, housing, commercial and industrial construction, government initiative such as smart cities PMAY, cement production in India is expected to touch 550–600 million tones per Review on vertical roller mill in cement industry its performance Roller mills are now operated with throughput capacities of more than 500 tons per hour of cement raw mix (Loeschemill, Polysius double roller mill, Pfeif ferMPSmill, SKET/ZABroller mill) The working principle of roller mills is based on two to four grinding rollers with shafts carried on hinged arms and riding on a horizontal grinding table or grinding bowlRoller mills INFINITY FOR CEMENT EQUIPMENT2020年5月1日 Cement industry consumes a huge amount of electrical energy that is about 100 kWh/t (kWh per ton (10 3 kg) of cement) [16]In a cement plant, about twothirds of the total electrical energy is used for particle size reduction of raw materials and clinker [17]There is a diverse range of options to decrease the production expenses as well as CO 2 emissions that Energy and exergy analyses for a cement ball mill of a new
.jpg)
(PDF) The latest innovative technology for vertical roller mills
2014年4月1日 Two mill systems are employed for most coal grinding applications in the cement industry These are, on the one hand, vertical roller mills (VRM) that have achieved a share of almost 90% and, on 2016年1月1日 For open circuit grinding [34,35], there is no disagreement with the calculation of the circulating load and classification efficiency, both of which 2 can be characterized relatively accuratelyAnalysis of the efficiency of the grinding process in closed circuit 2015年11月1日 Several configurations of deep mixing have been applied in the field including (a) Group column type improvement, (b) Wall type improvement, (c) Grid type improvement, and (d) Block type improvement(PDF) Deep Mixing Columns A Review ResearchGate2016年7月8日 Industrial Internship Training Report 201516 1 Index SNo Title Page no 1 Acknowledgement 2 2 Introduction 3 3 About DCM Shriram cement works 4 4 Cement 5 5 Crushing plant 7 6 Raw mill 12 7 Kiln section 18 8 Electrostatic precipitator 22 9 Clinker cooler and coalsection 24 10 Cement mill 26 11 Packaging plant 28 12 Quality control 29 13 Report on Cement manufacturing process PDF SlideShare

Computation of charging media for a double compartment cement ball mill
2024年1月26日 The speed of Oseparator fan controls the fineness of cement to be separated and the coarser particles are sent back to ball mill Cement ball mill is a well known machine to grind raw material (hard clinker) into grey powder: Inner diameter of mill = 42 m Length of drum = 1525–10 = 1425 mBowl diameter at the discharge x Gape; Bowl diameter at the feed end x Gape; Bowl circumference at the feed end x Gape; Maximum diameter at the head x Gape Diagram of a gyratory crusher [image: 135516)] Gyratory Crushing AMIT 135: Lesson 5 Crushing – Mining Mill Operator PDF On Dec 18, 2015, Hanafi A Radwan and others published DESIGN AND EVALUATE OF A SMALL HAMMER MILL Find, read and cite all the research you need on ResearchGateDESIGN AND EVALUATE OF A SMALL HAMMER 2023年7月10日 Cement manufacturing is a significant industrial activity that plays a vital role in the construction sector However, the process of cement production is associated with various environmental Cement Manufacturing Process and Its Environmental
.jpg)
Effect of grinding media on the milling efficiency of a ball mill
2022年1月1日 The size of grinding media is the primary factor that affects the overall milling efficiency of a ball mill (eg power consumption and particle size breakage)Question: OR A crushing mill reduces limestone from a mean particle size of 45mm to a product having size co2 as per the following table: Size (mm) 125 75 50 25 15 075 040 020 Percent 05 75 450 190 160 80 30 10 And in doing so requires 21 kJ/kg of the material crushedSolved OR A crushing mill reduces limestone from a mean CheggLimestone is a sedimentary rock composed primarily of calcium carbonate (CaCO3) It forms in a variety of marine environments and is often used in the construction industry as a building material or as an aggregate for concreteAbout the limestone crusher used in cement plant2023年12月4日 Cleary simulated the industrialscale ball mill of 5 m diameter using DEM to predict the motion of particles, power, torque, and liner wear by varying the mill speed and material parameters Influence of mill speed and contact properties on power draw and the effect of particle shape on charge motion were predictedNumerical Investigation of Vertical Roller Mill Operation Using
.jpg)
Design, Fabrication and Testing of a Double Roll Crusher
crushing limestone was 60% while that of kaolin was 80% Keywords: Double roll, crushing, Particle size, design analysis, solid mineral 1 Introduction Crushing” and “grinding” have been in use since the beginning of human existence The old ways of crushing is stressful, less efficient,2024年7月17日 Crushing is a multistage process that includes primary crushing, secondary crushing, and tertiary crushing Different types of crushing equipment are used at each stage to meet various crushing requirements Primary crushing breaks down large raw materials into mediumsized pieces for easier handling in subsequent processesTypes of Crushers: Choosing the Right One for Each StageMOMCQ1 Free download as Word Doc (doc / docx), PDF File (pdf), Text File (txt) or read online for free This document contains 47 multiple choice questions related to mechanical operations and size reduction processes Some key topics covered include: Pebble mills are used for grinding in paint, pigment and cosmetic industries to avoid iron contaminationMo MCQ 1 PDF Mill (Grinding) Materials2020年9月14日 Raw Mill; Preheater fan; Coal Mill; Cement Mill; Go back to Contents Table ↑ 53 Variable Speed Drives (VSD) In the last 25 years, variable speed drives (VSD) have been used more frequently in the cement industry The essentials of electrical systems in cement plants EEP
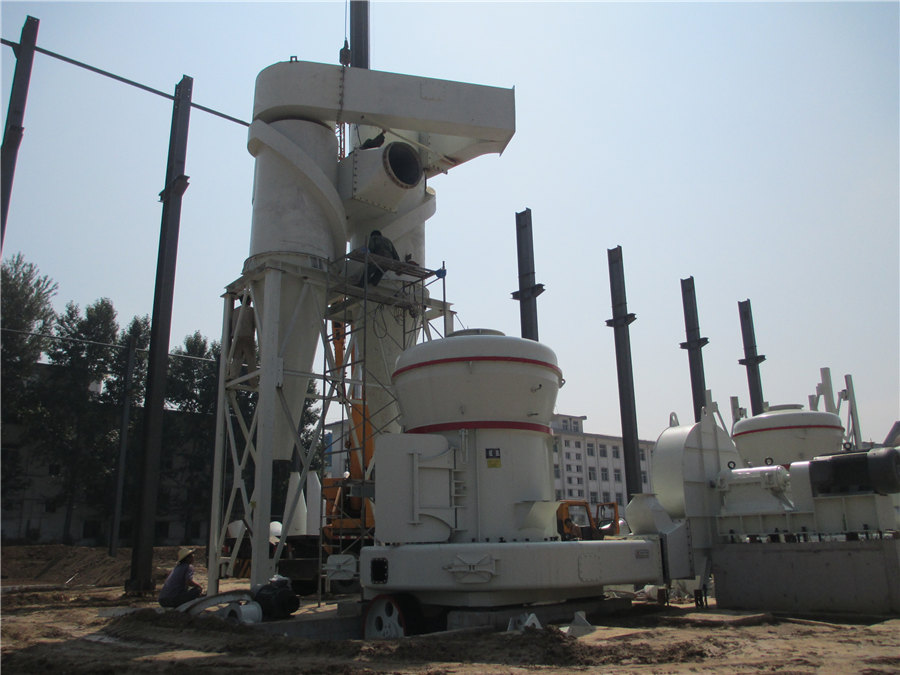
Concrete Cylinder Calculator
2024年6月30日 Let's say we need to make 10 concrete cylinder specimens for compressive strength testing of a new cement brand, and we decide to use concrete cylinders measuring 4 inches in diameter and 8 inches in heightWe 2019年9月1日 1 Introduction As one of typical coalfired industrial furnaces and kilns, cement kiln has the characteristics of high consumption of energy and resource as well as the large pollutant emission (Zhang et al, 2015)China has been the world's largest cement producer since 1985, accounting for about 60% of global production in 2014 (Chen et al, 2015; Long et al, Field measurements on particle size distributions and emission 2022年11月1日 Hence, N 1 and N 2 were taken as 05 and 02, respectively, along with N 3 = 02 Here, subscript T is the test condition in the laboratory mill D is the diameter of the ball mill J is the ball filling ratio, which is defined as the fraction of the mill volume filled by ballsImpact of ball size distribution, compartment configuration, and Cement Mill Ball Mill Dynamics Free download as Word Doc (doc / docx), PDF File (pdf), Text File (txt) or read online for free The document summarizes key aspects of ball mill fundamentals: 1) Ball mills reduce materials through comminution mechanisms like fracture, chipping, and abrasion caused by ball movement inside the rotating millCement Mill Ball Mill Dynamics PDF Mill (Grinding) Heat

Crushing and Grinding Calculations by Bond PDF Mill
Crushing and Grinding Calculations by Bond Free download as PDF File (pdf), Text File (txt) or read online for free This document presents equations for calculating particle size reduction in crushing and grinding processes It begins with an overview of the three main theories of comminution: Rittinger's theory which states work input is proportional to new surface area; 2021年8月13日 In this paper, a DEM model was applied to a copper mining gyratory crusher to perform a comprehensive analysis of the loads in the mantle, the crushing torque, and crushing power(PDF) Torque Analysis of a Gyratory Crusher with thethe energy used is in the form of fuel for the production of cement clinker and electricity for grinding the raw materials and finished cement Thermal energy accounts for about 20–25% of the cement production cost [10] The typical electrical energy consumption of a modern cement plant is about 110–120 kWh per ton of cement [11]Cement Industrial Process: Modeling and Optimization of the o x (41) though of course this is of no practical use for plant operations [D(x, 0) is the fraction by mass inferior to x; S(y) the selection function for material of size y at time t; B(x, y) the cumulative breakage distribution, ie the fraction finer than y in the breakage product of size x, and x maximum the largestKINETICS OF GRINDING
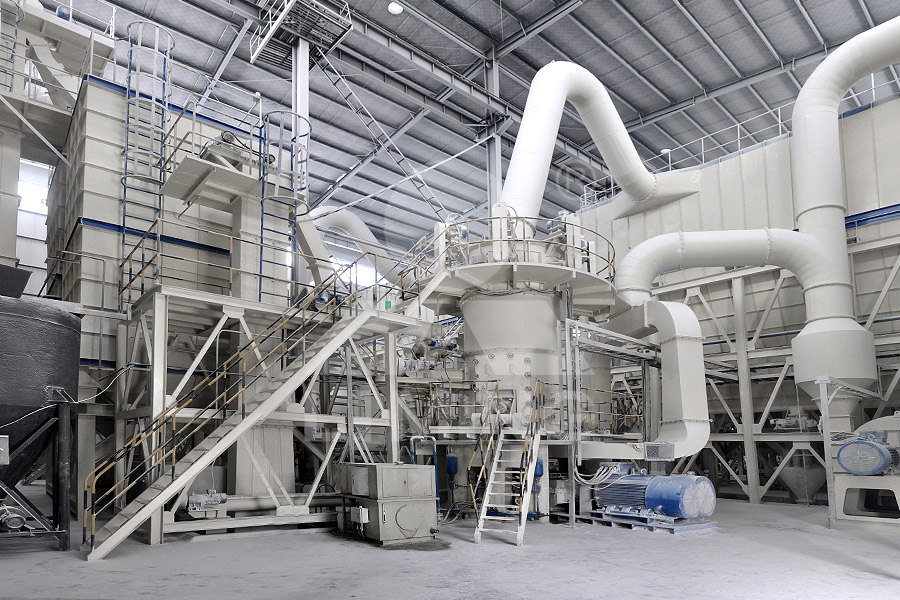
(PDF) Design, construction and performance evaluation of a
2018年7月19日 The detailed design procedure for a hammer mill machine is presented The system designed is a modification to the conventional hammer mill with a circular bottom casing and a semicircular screen