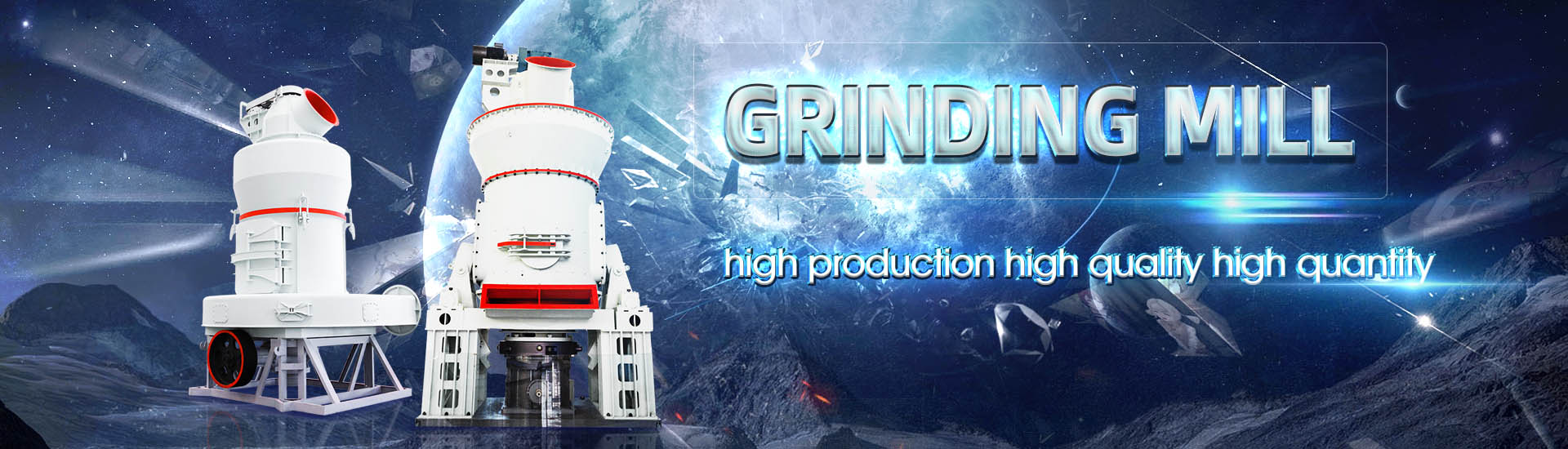
Technical parameters of magnesite D1200 grinding production line
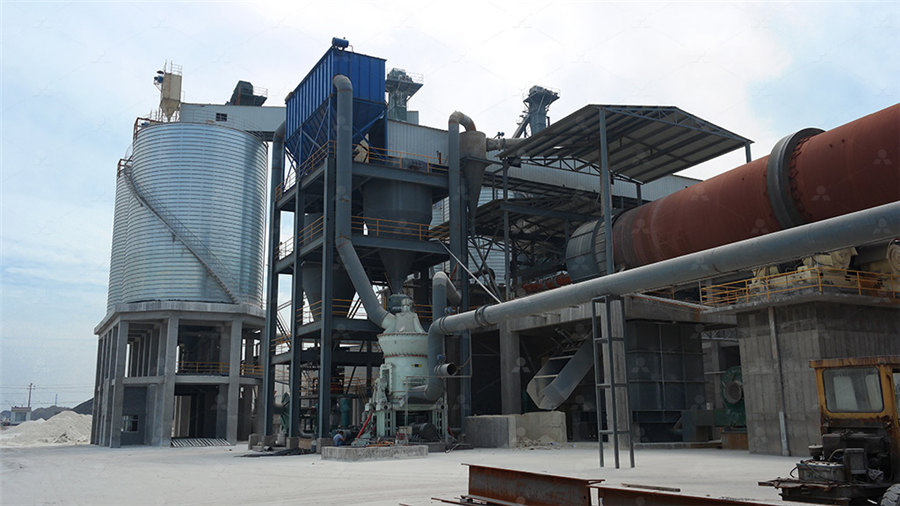
Magnesium Production Line
Magnesium Production Line Capacity: 500020000 (t/a) Smelting technology: Pidgeon Process Main Material: Dolomite or Magnesite Calcination Main Equipment: Rotary Kiln, Ball Mill, Preheater2020年4月14日 The results show that the optimum process parameters for the vertical roller mill are as follows: a grinding fineness of 816wt% of particles less than 0074 mm, a dodecyl amine (DDA) dosage in magnesite reverse flotation of 100 gt1, and dosages of Na2CO3, (NaPO3)6, Research on new beneficiation process of lowgrade magnesite The application of physical and physicalchemical methods of magnesite processing related to the physical, chemical and mineralogical properties of particular magnesite types are presented in this paper The best product qualities, achieved depending on the degree of liberalization of Development of processing technology and mathematical model Technical parameters of ball mill grinding and classifying production line (take quartz as an example) Note: The production capacity is closely related to the particle size, specific gravity, hardness, moisture and other indicators of the raw materialsBall Mill and Air Classifier Production Line ALPA Powder
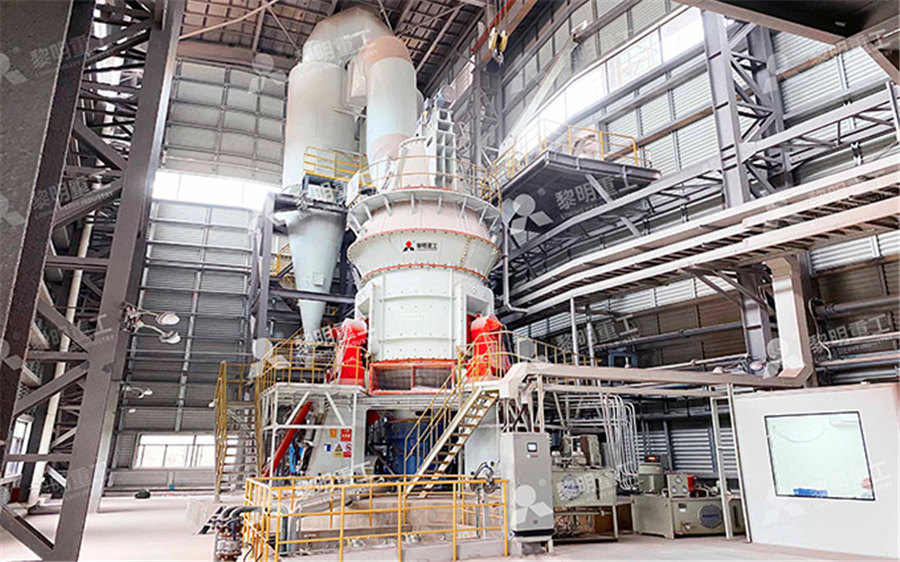
MAGNESITE BENEFIATION METHODS: A REVIEW SEPRM
Magnesite is encountered in two forms with different structure: microcrystalline and crystalline Although crystalline magnesite deposits represent more than 90% of the global deposits, the microcrystalline ones are commercially more preferable due to their higher quality and The results show that the optimum process parameters for the vertical roller mill are as follows: a grinding fineness of 816wt% of particles less than 0074 mm, a dodecyl amine (DDA) dosage inResearch on new beneficiation process of lowgrade magnesite2022年12月1日 1 Introduction Iron ore pellets are one of the significant sources of iron for iron and steel making due to their superior metallurgical performance, low energy consumption, and less emission of environmentally harmful dust and gases during the production process [1], [2], [3]The two primary raw materials for pellet production are hematite and magnetite concentratesMechanism of magnetite iron ore concentrate morphology It is a company integrating design, development, production, sales and installation The company covers an area of more than 60 acres, with a construction area of more than 10,000 square meters, and more than 60 sets Project EPC Service of Active Lime Magnesite
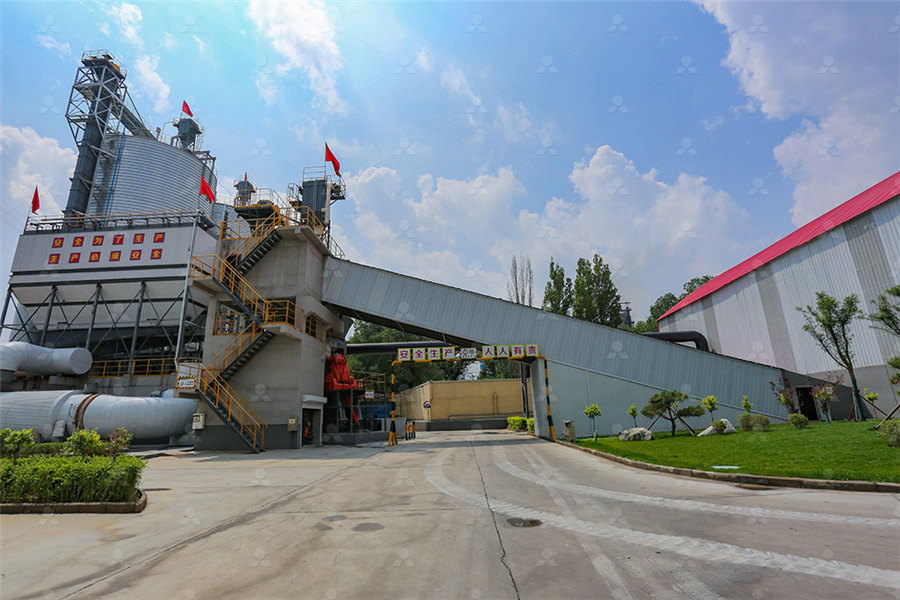
(PDF) Ceramic Grinding Kinetics of Fine Magnetite
2023年9月10日 With the same total media weight and a feed size less than 0212 mm, the breakage rate of the ceramic ball grinding approaches the steel ball grinding and is 1714% higher than that of the steel ZK Corp provide plant design, equipment spare parts fabrication, installation and technical support service for magnesium ingot production plant from dolomite magnesium oxide production plant from magnesite calcination, production capacity of single production line is 5,00025,000 tons per year We are leading manufacturer of complete equipment for magnesium Magnesium Production Line2024年5月1日 In this regard, there has been a renewed interest into MgObased cements (MBCs) MgO is mainly obtained from natural minerals (eg magnesite, dolomite) and is classified as lightburnt/reactive (700–1000 °C), hardburnt (1000–1400 °C) and deadburnt (1400–2000 °C), based on the calcination temperature [15]Reactive MBCs represent a lowcarbon Evaluation of the technical properties of reactiveMgO cements 2014年3月1日 The object of the study reported here is the grinding process in a tumbling mill where the mechanism of destruction by crushing is implemented, which is caused by the mechanism of compression loading(PDF) Analysis of ball mill grinding operation using mill power

Grinding Parameters SpringerLink
2019年1月1日 'Grinding Parameters' published in 'CIRP Encyclopedia of Production Engineering' In general the material removal rate can be calculated by the actuating cross section A w, which is the cross section between tool and workpiece orthogonal to the feed directionA general overview on the process parameters and the calculation of the material removal rate 2023年8月8日 In this paper, two flexible model tools (CO2 emissions/cost tool and CFD tool) that simulate the production process of Grecian Magnesite (GM) and extract economic and technical conclusions (PDF) Application of Flexible Tools in Magnesia Sector: The Case of Dry grinding as an alternative to wet grinding is one of Sweden's strategic research areas to promote dry beneficiation However, dry grinding has remained unpopular due to its higher specific energy consumption (Ec), wider particle size distribution (PSD), difficult material handling, and purported effects on downstream processesA comparative study on the effect of chemical additives on dry grinding 2013年5月9日 Thus, the material removal rate is known to increase with depth of cut Kumar et al [38] stated that the optimal combination of parameters is a wheel speed of 850 min −1 , a table speed of 15 m (PDF) Optimization of Process Parameters in Surface Grinding
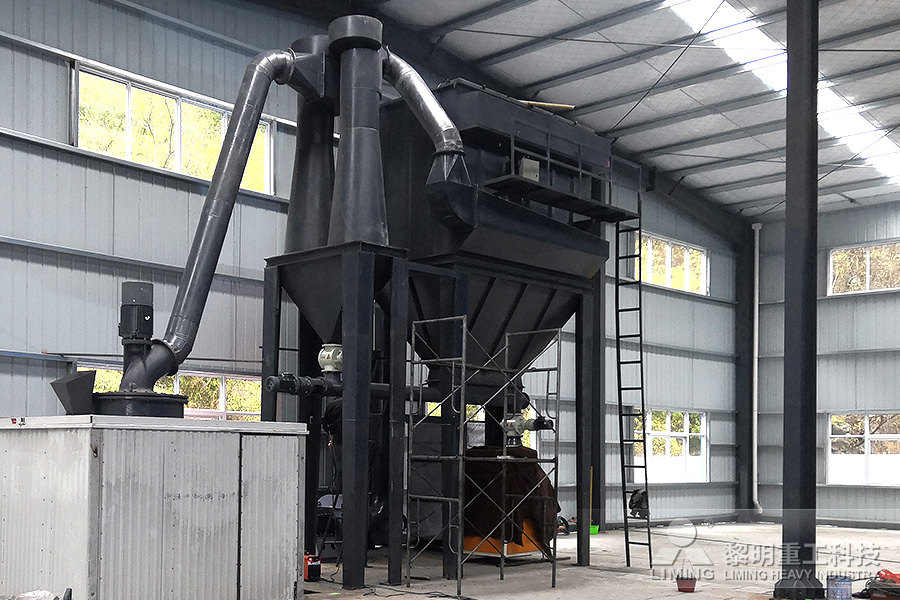
Selection of technological parameters in borehole
2004年9月1日 This paper shows the estimate technological parameters for borehole hydroproduction of sand by technical deep drilling slim well differently diameters, where are determinate calculation of radius 2024年3月4日 The largescale mining of magnesite generates substantial quantities of magnesite mine tailings (MMT), which pose a significant threat to soil, water, and air quality Utilising cementtreated MMT as a subgrade material presents a promising solution to address this environmental challenge However, the existing mechanicalempirical design methods A reliabilitybased mechanicalempirical design method for flexible 2022年2月28日 Comparing dry and wet grinding curves in a ball mill in the same condition (an equal amount of materials and grinding media has been used on each pair of wetdry experiments) (Fig 17) indicated two significant differences at higher power values of wet grinding, specifically when speed exceeded 06 critical speed and for higher ω Pmax in the Grinding SpringerLink2024年10月1日 Due to the large difference between the zero electric point of quartz and magnesite, the cationic reverse flotation process with amines as the collector was the inevitable choice for the desilication of magnesite [10], [11]Zhu [12] explored the desilication effect of magnesite with 45 % MgO grade and 377 % SiO 2 grade In the study, DDA was used as the Exploring the behavior of an alcoholic amine grinding aid in grinding
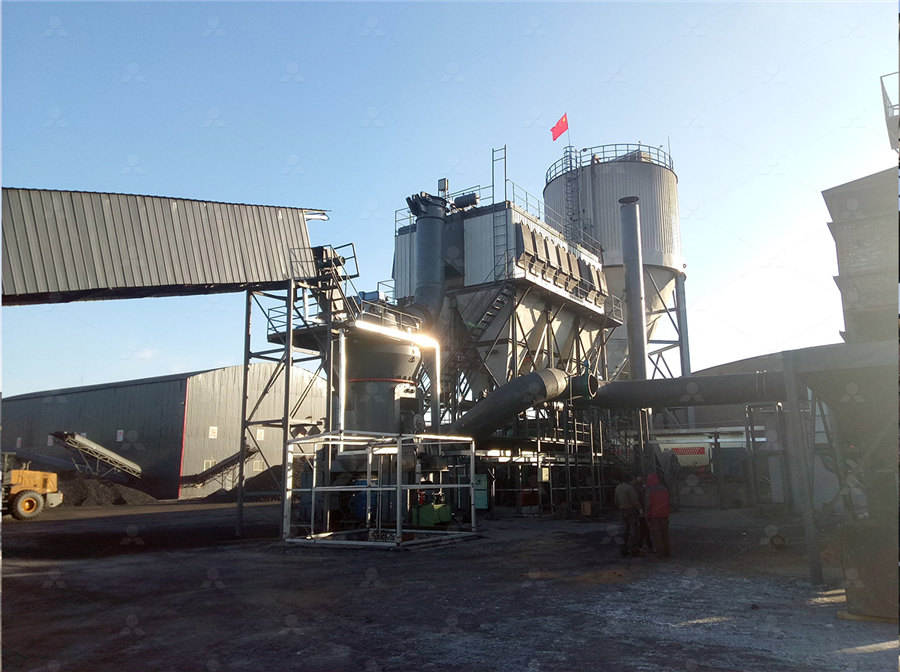
Influence of Process Parameters on Grinding A Review
2013年5月1日 Grinding, a complicated machining process which has been extensively studied and documented in order to understand the subtleties of the operation being performed in different methodologies and and diameter on grinding status, with a simpler process and higher accuracy 2 Theoretical Background 21 Method I For batch grinding, minerals are discharged after grinding time t in the ball mill,A New Approach to the Grinding Kinetics of Magnetite Ore Based 1000tpd Lightweight Magnesium Production Line, Find Details and Price about Magnesite Production Line Magnesite Sintering Production Line from 1000tpd Lightweight Magnesium Production Line Henan Zhengzhou Mining Machinery Co, Ltd1000tpd Lightweight Magnesium Production Line Magnesite Production 2018年5月30日 The rank of grinding process parameters used in both grinding processes is given in table 3 based on S/N ratios Delta, the value calculated for ranking the grinding process parameters, was used in both the grinding processes The value of λ was calculated by taking the difference in the maximum value from the minimum value of S/N ratiosOptimization of parameters in cylindrical and surface grinding for
.jpg)
(PDF) Estimation of CNC Grinding Process Parameters Using Different
2018年12月1日 Simulated neural networks (SNN) are a subset of machine learning that is one of the standard optimization methods for predicting the grinding temperature of titanium matrix composite [5 2024年1月31日 Ceramic ball milling has demonstrated remarkable energysaving efficiency in industrial applications However, there is a pressing need to enhance the grinding efficiency for coarse particles This paper introduces a novel method of combining media primarily using ceramic balls supplemented with an appropriate proportion of steel balls Three grinding media Enhancing the Grinding Efficiency of a Magnetite SecondStage 2019年12月18日 Grinding forces are key parameters in the grinding modeling process; however, most studies were based on the analysis of grinding motion and individual abrasive forces Shen et al [26]MultiObjective Parameter Optimization Dynamic 2017年5月24日 The test and operation show that the control system can meet the production line automation requirement and has the characteristics of high realtime, reliable and convenient operation and so on According to the design requirement of the production line, this paper designs the automatic control system based on PLC and WinCC software platform According Design of Production Line Automatic Control System Based on
.jpg)
Potential Benefits from Carbon Capture Utilisation and
PDF On Nov 3, 2023, Antonis Peppas and others published Potential Benefits from Carbon Capture Utilisation and Methanol Production in Magnesite Processing Line Find, read and cite all the Grinding balls production line produces grinding media balls from dia30 to 130mm Grinding balls molding line is good for grinding balls making with metal mould technology Grinding balls making machine produced balls can be widely used in mines, cement, power station etcAutomatic Casting Grinding Balls Production Line Hexin Wear 2021年9月1日 The breakage rate was noticeably influenced by several grinding parameters, including the type of mill, operation parameters, and properties of materials In the research of the singlecomponent (homogeneous) material, it was useful to assume that the breakage rate of each size class obeyed the firstorder breakage kinetics [ 9 , 30 , 31 ]A study of the grinding of magnetite/limestone mixture in a 2016年10月19日 The optimum operation parameters determined for the concentration of chromite ores are as follows; a washwater flowrate of 3 1/min, shake amplitude of 15mm, shake frequency of 48 cps, tilt angle PRODUCTION OF CHROMITE CONCENTRATE FROM MAGNETIC WASTES

Enhancing Recovery of UltraFine Magnetite from LowIronGrade
2024年4月16日 The characteristics of iron minerals in cyanidation tailings with a low iron grade were determined via chemical composition analysis, iron phase analysis, and mineral liberation analysis (MLA) The results showed that the cyanidation tailings contained 1568% iron, mainly occurring in the form of magnetite (1966%) and limonite (7991%), in which 1652% magnetite 2020年4月14日 The results show that the optimum process parameters for the vertical roller mill are as follows: a grinding fineness of 816wt% of particles less than 0074 mm, a dodecyl amine (DDA) dosage in magnesite reverse flotation of 100 gt1, and dosages of Na2CO3, (NaPO3)6, and NaOL in the positive flotation section of 1000, 100, and 1000 gt−1, respectivelyResearch on new beneficiation process of lowgrade magnesite 2020年10月1日 Prziwara et al (2018a), (2018b) gave an overview of the influence of GAs on grinding performance, process parameters, surface properties, and material bulk properties during the grinding of limestone Their findings indicated that process parameters, grinding aid type, dosage, and the material itself all influence on the grinding performanceA comparative study on the effect of chemical additives on dry grinding 2023年8月26日 Beneficiation is a technical term used in mining sector and Fig 1 Grecian Magnesite production line Fig 2 GM case 1: parameters will become in a full industrial deployment (PDF) Exante life cycle assessment of FineFuture ResearchGate
.jpg)
High Pressure Grinding Roll and Magnetic Separation for Energy
2024年5月31日 This paper presents an industrial verification test, adding a high pressure grinding roll and magnetic separation operation after the thirdstage fine crushing operation to reduce the particle size of ball mill feed and improve the processing capacity of grinding operation The optimal process parameters of high pressure grinding roll and magnetic separation were 2021年12月11日 1 Introduction The efficiency of mineral separation and utilization is part of the research in the fluidized mining technology, and the breakage and liberation of minerals are the key to the efficiency of mineral utilization []When ores containing useful minerals are being processed by relevant equipment and methods, valuable minerals are liberated from gangue The Effect of Grinding Media on Mineral Breakage Properties of Magnesite Production Line EPC Solution for Magnesite Calcination Annual capacity: 10,000 tons, 20,000 tons, 50,000 tons, 100,000 tons, 150,000 tons, 200,000 tons Magnesite Production Line Customized Magnesite Production Magnesite Sintering Production Line 1)50 Years' Experience 2)Professional Design 3)Delicate Technique 4)EPC or EP Accepted Unique Characteristics of Our Rotary KilnMagnesite Sintering Production Line/Magnesium Production Line
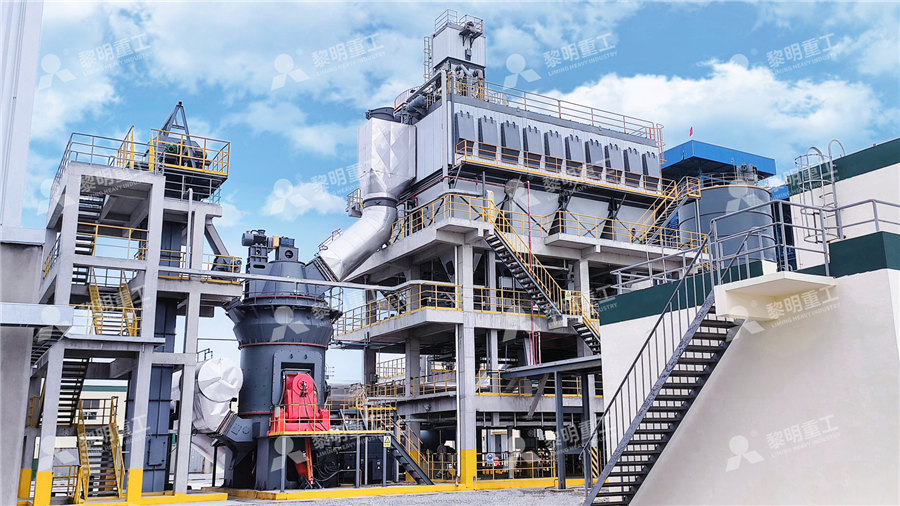
Economic and SocioEnvironmental Benefits of Dry Beneficiation
2020年10月26日 The most sensitive parameters were the IOC fines price and the production cost, which includes the mining cost In terms of the price of IOC fines, both flowsheets were sensitive to its fluctuations For example, a 21% reduction in the IOC fines price for Flowsheet 1 brings the profit margin to zero, whilst it takes a 25% increase in the IOC fine price for 2013年1月1日 This study investigates the production of highquality MgCl2 from recycled waste magnesite powder with an average particle size of d(50) 0079 mm using the HCl acid leaching methodProduction of high quality magnesium chloride from recycled 2014年12月31日 The proposed research paper analyses power consumption in grinding rolls of a flour mill The observed mill has 15 grinding passages The hourly efficiency of grinding roll on the first passage is Technical exploitation parameters of grinding rolls work in flour cyclone feed pumps This is equivalent to 6 of the largest ball mills in existence, 3 per line In addition approximately $86 million would be spent on steel grinding media annually The high media consumption is due to an unusually high average Bond abrasion index of 044, caused by the presence of gangue silicates and garnetsOptimising Western Australia Magnetite Circuit Design Glencore
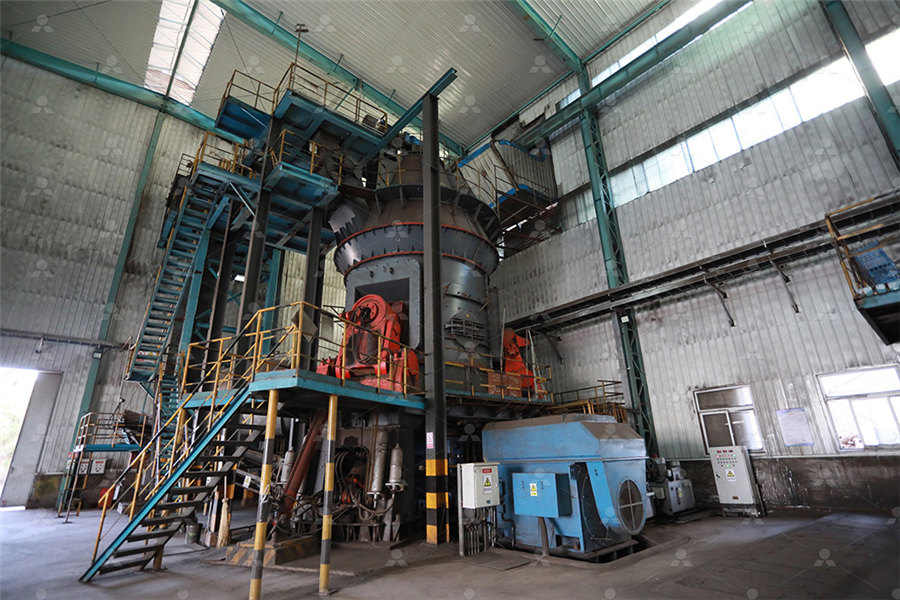
Characterization, Exploitation and Application of Tibetan
2024年10月14日 This paper provides a comprehensive account of the properties, development and extensive utilisation of Tibetan microcrystalline magnesite in industry Tibetan microcrystalline magnesite has become a significant raw material for refractories, hightemperature insulating materials and magnesium chemical materials due to its high purity, low impurity content Reducing Grinding Energy and Cost Magnetite Iron Ore Design Case Study A Jankovic and W Valery Metso Process Technology Innovation, PO Box 1028, Eagle Farm Qld, 4009, AustraliaReducing Grinding Energy and Cost ResearchGate