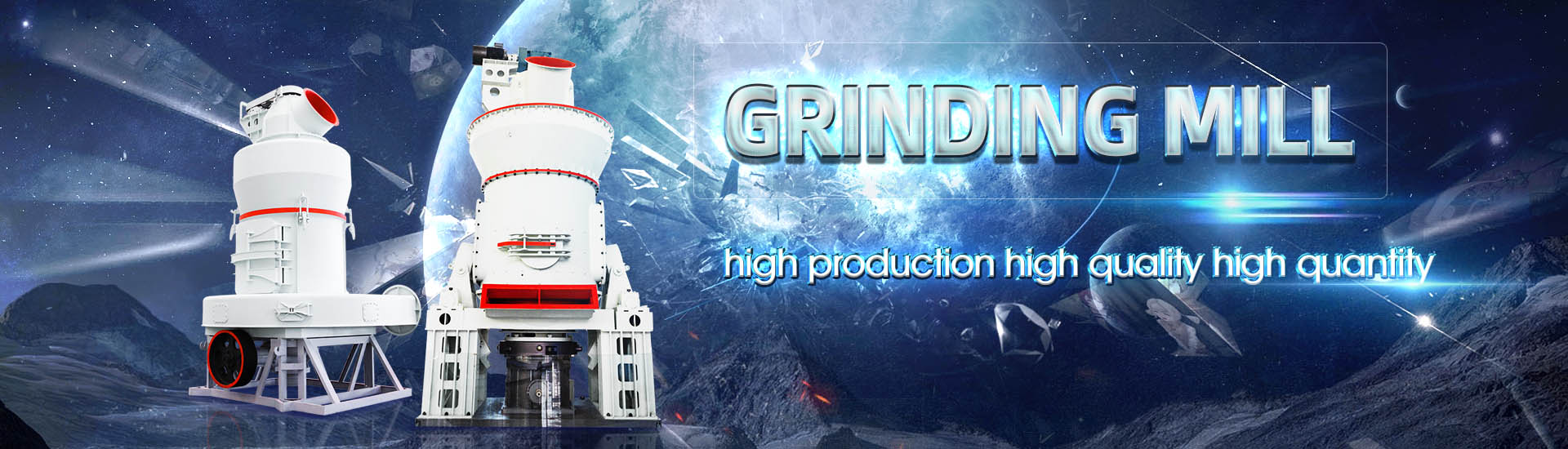
Lime rotary kiln process flow chart cement production line process flow chart
.jpg)
Stages in cement production flow chart [43] ResearchGate
This study presents new lightweight periclase‐magnesium alumina spinel refractories for the working lining of cement rotary kilns in which magnesium alumina spinel hollow spheres are This study presents new lightweight periclase‐magnesium alumina spinel 登录Rotary lime kilns are large steel tubes that are lined on the inside with refractory bricks They are slightly inclined from the horizontal and are slowly rotated on a set of riding rings Lime mud is 22 Lime Kiln Principles And Operations TAPPIThe heat and mass transfer modeling process in rotary kilns is summarized The commonly used correlations involving rotary kilns are categorized by application The solidwall heat exchange Rotary kiln process: An overview of physical mechanisms, models
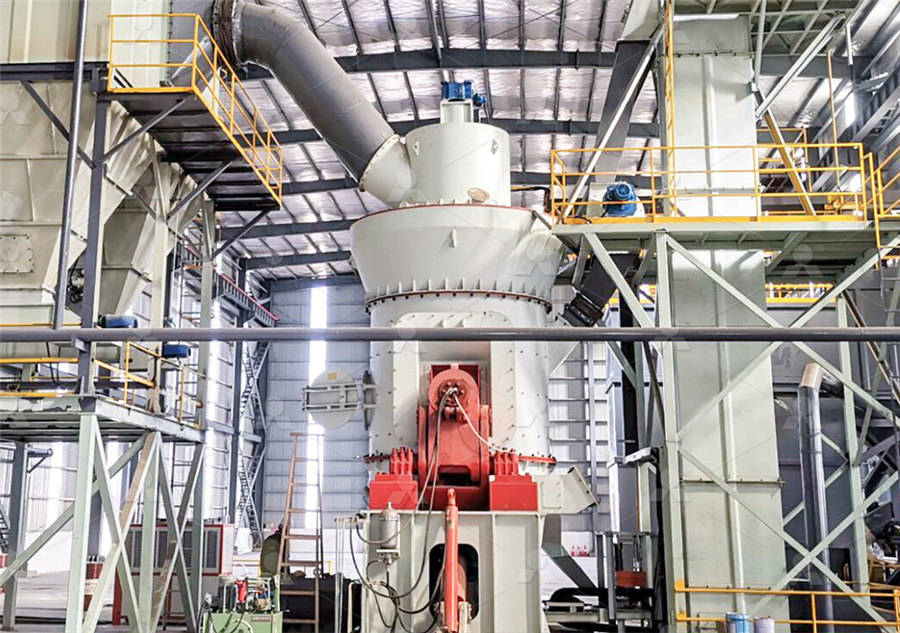
Process flow diagram for the cement manufacturing
Process flow diagram for the cement manufacturing process, showing electricity and heat consumption or inputs [39] The paper presented herein investigates the2023年2月25日 The rotary kiln is used in many solid processes, including drying, incineration, heating, cooling, humidification, calcination and reduction This widespread application can be Rotary kiln process: An overview of physical mechanisms, models A generalized material flow diagram for a lime manufacturing plant is given in Figure 11171 Note that some operations shown may not be performed in all plants The heart of a lime plant 1117 Lime Manufacturing US Environmental Protection AgencyIn the cement kiln, all the ingredients are heated to about 1400–1500 °C in huge horizontal cylindrical steel tubular vessel called rotary kiln, lined inside with special Refractory material Chapter 4 Cement Manufacturing and Process Control
.jpg)
22 Lime Kiln Principles and Operations TAPPI
Lime Kiln Principles And Operations Terry N Adams Technical Consultant Seattle WA Slide 2 Outline • Lime kiln equipment – flames, chains, refractories – product coolers, external mud The Cement Plant Operations Handbook is a concise, practical guide to cement manufacturing and is the standard reference used by plant operations personnel worldwide Providing a The Cement Plant Operations Handbook International Cement 1the introduction of the cement plant equipment We Henan Zhengzhou Mining Machinery Co,ltd,can provide complete set technology solutions and supporting production equipments of cement production line 1)Design capacity:150 Supply Cement Production Line Process Flow Chart Download scientific diagram Typical cement manufacturing process flow diagram [4] from publication: Model Development for CO2 Capture in the Cement Industry Climate change has become a Typical cement manufacturing process flow
.jpg)
How Cement is Made Cement Manufacturing Process
Stage 2: Grinding, Proportioning, and Blending The crushed raw ingredients are made ready for the cementmaking process in the kiln by combining them with additives and grinding them to ensure a fine homogenous mixture The composition of cement is proportioned here depending on the desired properties of the cement Generally, limestone is 80%, and the remaining 20% 2016年1月20日 In each unit's material flow structure, the flow rate and flow direction are varied In the production process, material consumption needs to be investigated at every point, and a large number of measurements are taken To analyze the material flow of a cement production line, the material flow model of each unit should be establishedAnalysis of material flow and consumption in cement production process The lime rotary kiln production process is highly automated and can be effectively controlled using advanced instrumentation and control systems This allows for precise regulation of temperature, material flow, atmosphere, and other critical parameters, resulting in improved production efficiency and stabilityLime Rotary Kiln Roatry Kiln Manufacturer YingYong MachineryDownload scientific diagram Process flow diagram for the cement manufacturing process, showing electricity and heat consumption or inputs [39] from publication: Energy Savings Associated with Process flow diagram for the cement manufacturing process,
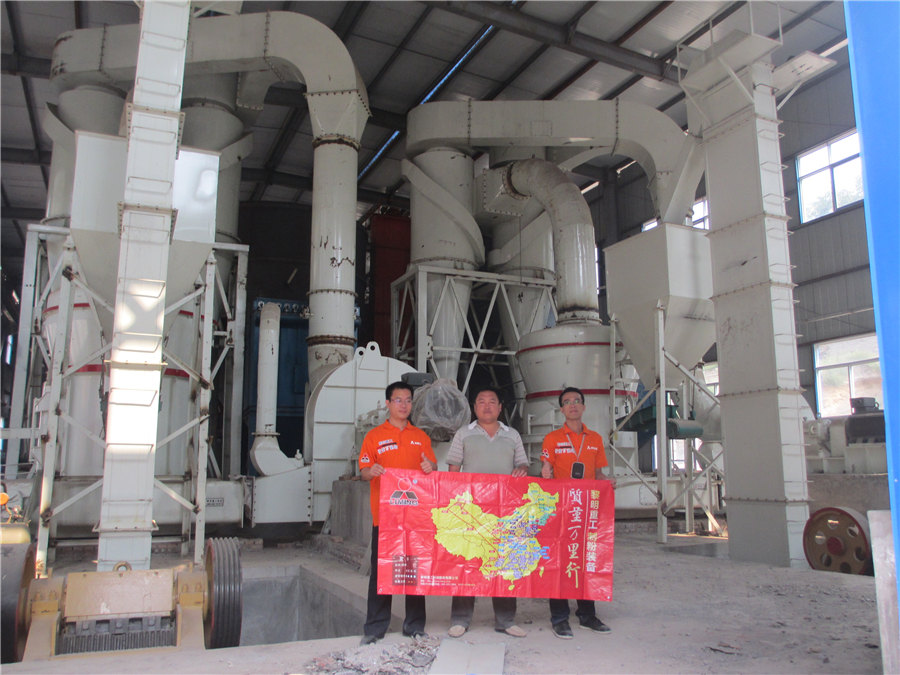
Lime Production Line Active Lime Production Line Cement
SOLUTION2: Lime Production Line With Vertical Kiln The vertical lime kiln is suitable for smallcapacity active lime production lines, lowcost, safe and environmentally friendly The vertical lime kiln uses the principle that the material’s own weight descends and the hot gas rises for heat exchange to burn lime We supply twin shaft lime kiln, double beam lime kiln, annular lime kiln 2012年8月30日 Cement Manufacturing Process Phase IV: Kiln Phase Kiln is a huge rotating furnace also called as the heart of cement making process Here, raw material is heated up to 1450 ⁰C This temperature begins a chemical reaction so called decarbonation In this reaction material (like limestone) releases the carbon dioxideCement Manufacturing Process Engineering IntroA generalized material flow diagram for a lime manufacturing plant is given in Figure 11171 Note that some operations shown may not be performed in all plants The heart of a lime plant is the kiln The prevalent type of kiln is the rotary kiln, accounting for about 90 percent of all lime production in the United States1117 Lime Manufacturing US EPA2023年12月26日 As we all know, the dryprocess cement production line is commonly used in the cement industry The new type of dryprocess cement production process includes four main sections: Prehomogenization of raw materials, homogenization of raw materials, clinker firing, cement grinding, etc Raw material conveying system The raw material, including limestone, 6 Cement Equipment For Dryprocess Cement Production Line
.jpg)
Cement Production Line,Cement Machine,Rotary
5000 Tons/Day New Type Dry Process Cement Production Line Pengfei 5000t/d dry process cement production line is excellent in saving energy It adopts various high efficient cement equipment and devices It is designed with a smooth and 3Limestone Calcination Limestone in the preheater will be preheated by the hot air, then it will be discharged to rotary kiln through chute that connecting preheater and kiln, it will stay in the kiln for 152 hours for calcination, during lime Lime Production Line AGICO Cement Plant2015年8月1日 Cement production, which is highly dependent on the availability of natural resources, will face severe resource constraints in the future This is especially true for the cement industry in ChinaAnalysis of material flow and consumption in 2016年4月15日 Mujumdar et al presented the integrated model for cement rotary kiln, calciner, cooler and preheater, and developed a simulation software titled RoCKS [25] However, they did not make any comparisons with experimental data Söğüt et al performed an exergy analysis on the cement production line [26]Thermal energy analysis of a lime production process: Rotary kiln

Cement Manufacturing Process The Engineering Community
2018年8月28日 CEMENT MANUFACTURING PROCESS PHASES Production of cement completes after passing of raw materials from the following six phases Rotary kiln The series of After explaining the complete process of cement making, flow chart would be like that flow chart present the summary of whole process as shown belowThe cement production process 1 The Quarry: The cement production process begins with the extraction of limestone and clay from the quarry 2 Crusher and PreBlending: The material is then crushed to reduce particle sizes and blended to reduce variability in composition 3 Raw Mill and Kiln: Raw materials and additives areA practical guide to improving cement manufacturing processes 2013年5月11日 Categories Civil Engineering Articles, Civil Engineering Articles for Mobile, Concrete Technology, PowerPoint Presentations Tags acc cement, cement, cement concrete, cement in concrete, cement manufacture, cement manufacture process, cement manufacturers, cement manufacturers in india, Cement Manufacturing, cement manufacturing process, Cement Manufacturing Process Simplified Flow Chart2019年8月26日 The new dryprocess cement production line technology was developed in the 1950s So far, in Japan, Germany and other developed countries, the production rate of new dryprocess cement clinker with suspension preheating and pre New dry process cement production line process LCDRI CN
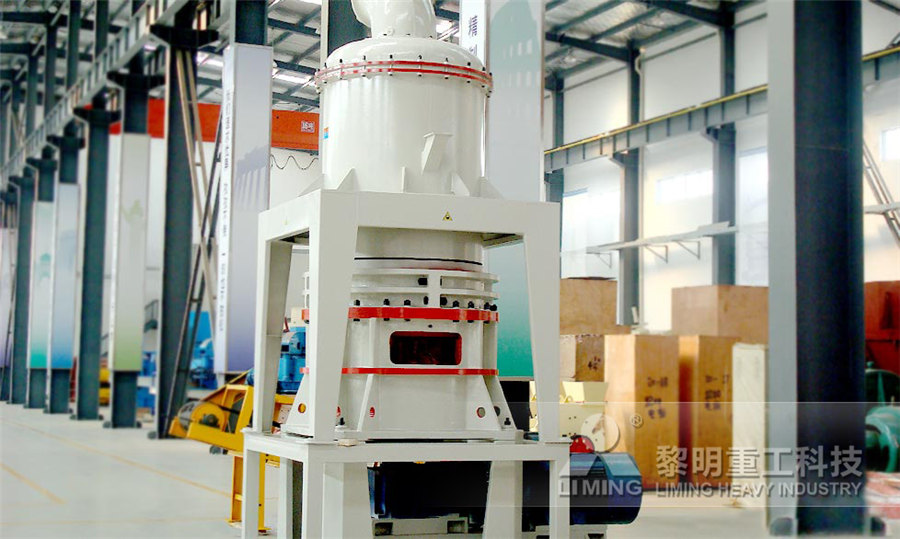
Rotary kiln process: An overview of physical mechanisms, models
2023年2月25日 The angle of repose is an intrinsic characteristic of a given material; it depends principally on: particle size, rotational speed of the kiln (Fig 2), and surface condition of the kiln wallMore specifically, this angle characterizes the flow properties of “solid particles” in the kiln; it is often assumed to be constant but may vary along the length of the kiln, in correlation with The burning process is carried out in the rotary kiln while the raw materials are rotated at 12rpm at its longitudinal axis The rotary kiln is made up of steel tubes having the diameter of 2530 meter and the length differs from 90120meterManufacture of Cement Materials and Manufacturing Process of Download scientific diagram Cement Manufacturing Process Flowsheet (Flow Chart) from publication: Cement Manufacturing – Process Modeling and TechnoEconomic Assessment (TEA) using SuperPro Cement Manufacturing Process Flowsheet (Flow Chart)A generalized material flow diagram for a lime manufacturing plant is given in Figure 11171 Note that some operations shown may not be performed in all plants The heart of a lime plant is the kiln The prevalent type of kiln is the rotary kiln, accounting for about 90 percent of all lime production in the United States1117 Lime Manufacturing US Environmental Protection Agency
.jpg)
How Is Cement Produced in Cement Plants Cement
The cyclone preheating system Phase IV: Calcination The calcination is the core phase of the cement making dry process The calcination of the preheated raw meal takes place in the rotary kiln of the cement plant The rotary kiln is a 2024年5月14日 Cement manufacturing process is a reliable bonding material It is obtained by burning calcareous material (lime) and argillaceous material (clay) and then grinding, types of cement The cement manufacturing process was first produced by Joseph Aspidin, a mason from England As its color resembled a variety of sandstone found in Portland, he named it Portland CEMENT MANUFACTURING PROCESS ! TYPES OF CEMENT, FLOW CHART 2021年3月9日 In this study the process flow diagram for the cement production was simulated using Aspen HYSYS 88 software to achieve high energy optimization and optimum cement flow rate by varying the flow Simulation and Optimization of an Integrated Process Flow Sheet Cement and Concrete Testing Laboratory (VCCTL) 7 Calorimetry – 8 Burnability – 9 Grindability – 10 Physical testing – 11 Process control analysis – 12 Chromate passivation – 13 Cement quality – 14 Setting time – 15 ASTM cement types and specifications – 16 European EN 197 cement specification – 17 Composite cementsThe Cement Plant Operations Handbook International Cement
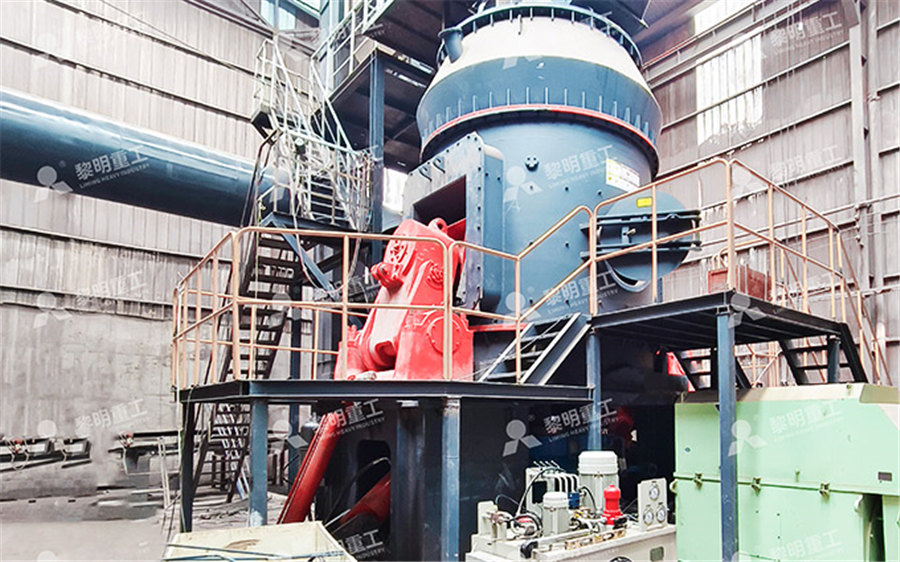
Production Line of Active Lime Rotary Kiln MadeinChina
The active lime production line follows a meticulous process flow, ensuring the production of superior quality active limestone It consists of three main components: limestone crushing, limestone preheating and decomposition, and lime calcination In the first stage, limestone is crushed into small particles to facilitate the subsequent processes2021年3月9日 In this study the process flow diagram for the cement production was simulated using Aspen HYSYS 88 software to achieve high energy optimization and optimum cement flow rate by varying the flow rate of calcium oxide and silica in the clinker feed Central composite Design (CCD) of Response Surface Methodology was used to design the ten experiments for Simulation and Optimization of an Integrated Process Flow Sheet 2014年6月10日 Cement manufacturing process Download as a PDF or view online for free History of Portland Cement • First rotary kiln designed to produce Portland cement patented in 1885 by Frederick Ransome Fuel, Feed, Kiln Speed, Gas Flow • Kiln Temperatures Burning Zone • Kiln Stability • Chemistry • Instrumentation 35Cement manufacturing process PPT Free Download SlideShare1971年8月17日 States The balance of domestic cement production is primarily masonry cement Both of these materials are produced in portland cement manufacturing plants A diagram of the process, which encompasses production of both portland and masonry cement, is shown in Figure 1161 As shown116 Portland Cement Manufacturing US EPA
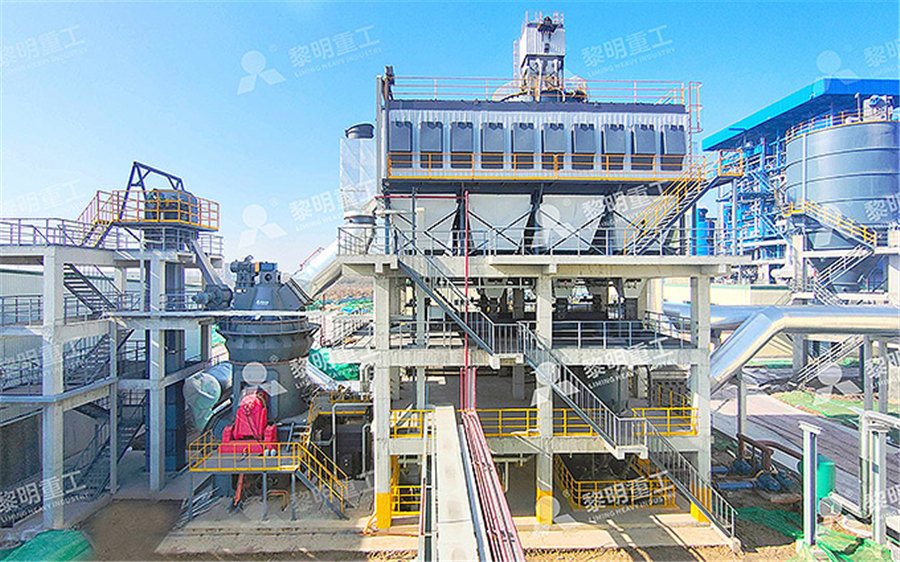
Cement Making Process Cement Production
The comparison data between the wet process cement production line and the new dry process cement production line shows that with the same rotary kiln size (diameter), the production capacity of the cement kiln which adopts the pre Lime rotary kiln has many advantages in the calcination of lime, it is also known as the lime kiln, and is a professional, strong calcining equipment, Its main advantages include great production capacity, no noise, low energy Lime Rotary Kiln Limestone Rotary Kiln Capacity: Download scientific diagram Process Flow Diagram of the Cement Plant from publication: In this study, heat loss from rotary kiln was examinedProcess Flow Diagram of the Cement PlantFig 41 Flow sheet of cement manufacturing process 4 Cement Manufacturing andfiProcess Control 63 43 Fuel Different fuels like coal, gas, etc are used as the source of heat energy to carry out the reactions inside the cement rotary kiln The fuel cost is about 50% of the total energy cost and 10% of the total cost for cement productionChapter 4 Cement Manufacturing and Process Control
.jpg)
Improved Process Modeling for a Lime Rotary Kiln Using Equilibrium
2012年3月1日 This article discusses the impact of oxygen (O2) enrichment on rotary kiln lump lime production A predictive simulation tool is utilized to investigate the effect of O2 enrichment on the products, byproducts of the production process, and input substitution possibilities Finally, this section explains costs of production and economies of scale 21 PRODUCTION PROCESS, INPUTS, AND OUTPUTS The production of lime begins with the Lime Production: Industry Profile2016年4月1日 Thus, rotary kiln energetic and exergetic analyses are useful tools to reach cement production process improvements Energetic analysis is based on the first law of thermodynamics and allows one Thermal energy analysis of a lime production process: Rotary kiln Lime production line refers to the whole process of active lime produce During all the lime production process, the rotary kiln production process is the most advanced one Our production process adopt the rotary kiln with the vertical preheater and vertical cooler for the limestone calcination to achieve the production requirements of energy Active Lime Production Line

The Cement Manufacturing Process
2017年8月15日 The materials reach temperatures of 2500°F to well above 3000°F in the kiln Rotary kilns are divided into two groups, dryprocess and wetprocess, depending on how the raw materials are prepared In wetprocess kilns, raw materials are fed into the kiln as a slurry with a moisture content of 30 to 40 percent2013年1月1日 In this study the process flow diagram for the cement production was This article describes an improved process model for simulation of the manufacturing process of lime in a rotary kilnModelling the cement process and cement clinker quality