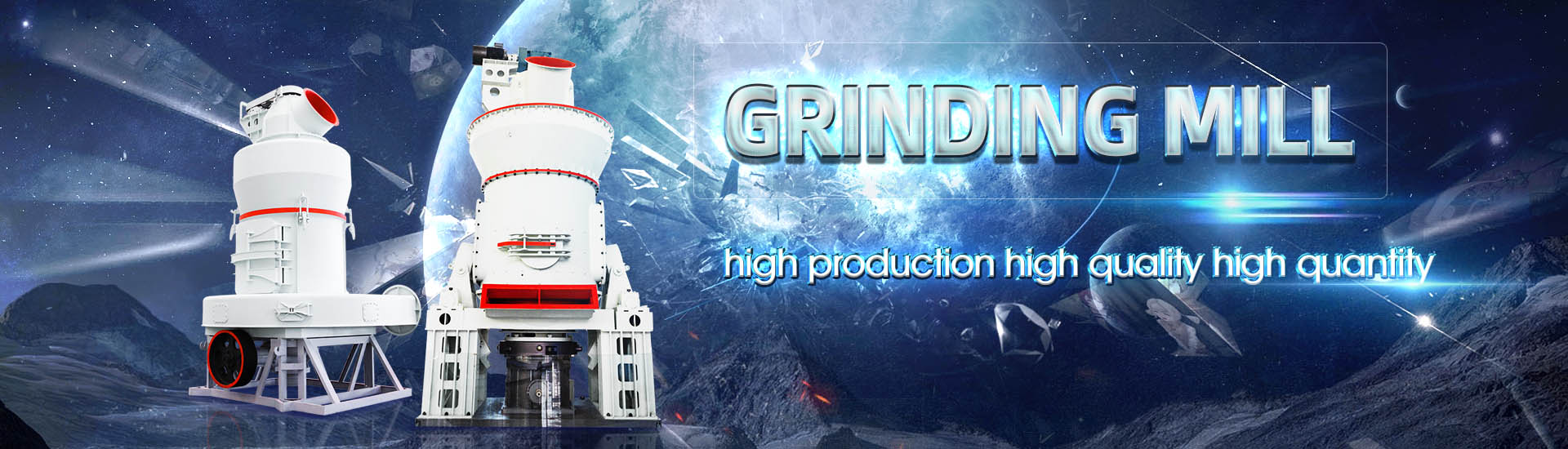
Working principle of coal slime ore grinding mill
.jpg)
Effect of grinding methods on slime dissociation characteristics
4 天之前 Its working principle is that the particles are irradiated by a laser beam to capture the highresolution image of the scattered light, and then the two shape parameters of AR and Rn are extracted by the complex image analysis software provided by Occhio2018年8月17日 Rod mills are more suitable for breaking up large pieces of ore due to the heavy weight of the rods Examples include large pieces of rock, Grinding Mills — Types, Working Principle Applications2023年7月20日 Moist grinding, a special grinding method, is used to prepare pellets for smelting According to the grinding medium features, ore grinding is mainly classified into ball grinding Ore Grinding SpringerLinkvertical roller grinding mills for grinding: • Coal • Cement raw material • Clinker / granulated slag • Industrial minerals, and • Ores The core elements of these plants are the Loesche vertical PROCESS OPTIMISATION FOR LOESCHE GRINDING PLANTS
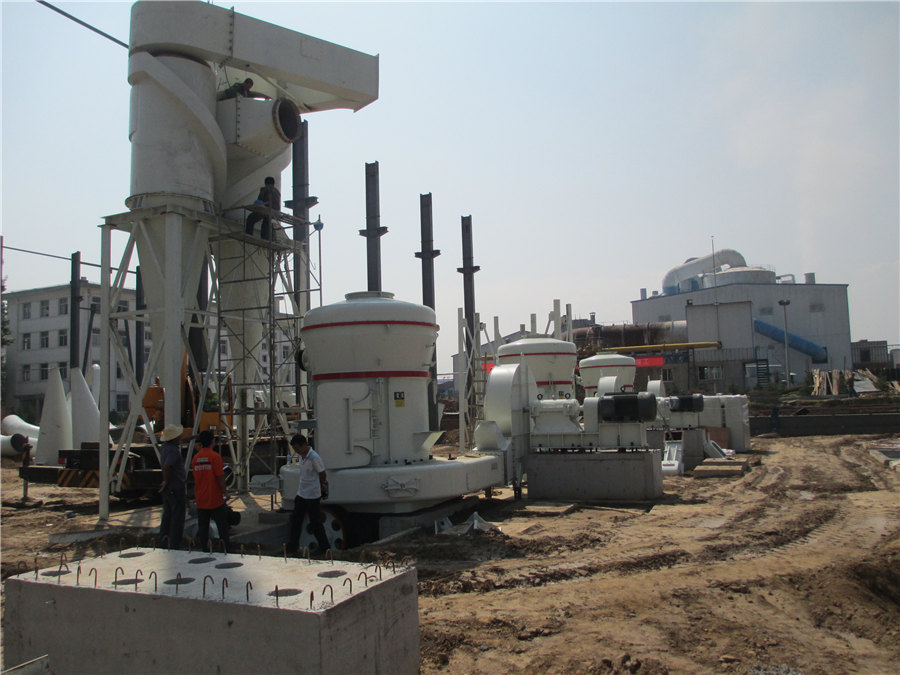
ISAMILL FINE GRINDING TECHNOLOGY AND ITS INDUSTRIAL
Fine grinding, in particular in the zinc retreatment circuit requiring a milled product P80 of 7 micron, is essential to treat the ores from the Mount Isa Mines deposits2024年11月1日 To fill this gap, this study aims not only to explore dissociation characteristics and particle shape properties resulting from the grinding of coking coal in a planetary ball mill Effect of grinding methods on slime dissociation characteristics It is performed in cylindrical steel vessels that contain a charge of loose crushing bodies—the grinding medium—which is free to move inside the mill, thus comminuting the ore particles Grinding Mill an overview ScienceDirect TopicsWorking principle: the motor drives the grinding table to rotate through the reducer, the material falls into the center of the grinding table from the feed inlet through the air lock feeder, and the Roller Mill Springer
.jpg)
Research of iron ore grinding in a verticalrollermill
Request PDF On Mar 15, 2015, Mathis Reichert and others published Research of iron ore grinding in a verticalrollermill Find, read and cite all the research you need on ResearchGate2017年10月3日 Share with Facebook; Share with Twitter; Share with Google+; Share with LinkedIn; Posted: October 3, 2017 Grinding Mills Types, Working Principle Applications The purpose of this article is to explain the usage of Grinding Mill Types, Working Principle 2024年9月26日 Baichy Machinery is a factory supplier of mining machinery, mainly focusing on stone crushers, powder grinding mills, and mineral beneficiation plantsWe can offer you a free design and completed solutions according to your project Baichy Heavy Industry has grown into a hightech mining equipment comprehensive enterprise, integrating RD, manufacturing, sales, What Is A Coal Slime Dewatering Screen? Baichy Heavy Industry2024年4月26日 The choice of grinding mill depends on factors such as the desired product size, capacity requirements, and energy consumption b Autogenous and SemiAutogenous Mills: In some cases, autogenous (AG) and semiautogenous (SAG) mills are used for grinding These mills utilize the ore itself as the grinding media, reducing the need for additional Iron Ore Processing: From Extraction to Manufacturing
[GYQ0R)ZQ]ESS4NJ.jpg)
(PDF) MPS mills for coal grinding ResearchGate
2014年1月1日 Two mill systems are employed for most coal grinding applications in the cement industry These are, on the one hand, vertical roller mills (VRM) that have achieved a share of almost 90% and, on ore fine grinding, and other fields Horizontal Cylinder Roller Mill As for the horizontal cylinder roller, its roller surface and roller have a horizontal layout It was developed by France and applied to production in 1993 The structure principle isshown inFigure 2 When working, the grinding material relies on theRoller Mill SpringerWorking principle and characteristics of vertical mill Working principle The working principle of a vertical mill involves the rotation of a grinding table with rollers attached to it Raw materials are fed into the table and ground between the rollers and table The ground materials are then blown by hot air through an outlet in the mill's Working principle and characteristics of vertical mill2015年8月7日 The centrifugal force (the central Hydrocyclone Working Principle) that is generated by this spin, forces the “bigger particles outwards towards the wall of the cyclone If you were able to do a cross section of a cyclone while it is operating, you could see that the ground rock will become finer the closer that you get to the centre of the cycloneHydrocyclone Working Principle 911Metallurgist
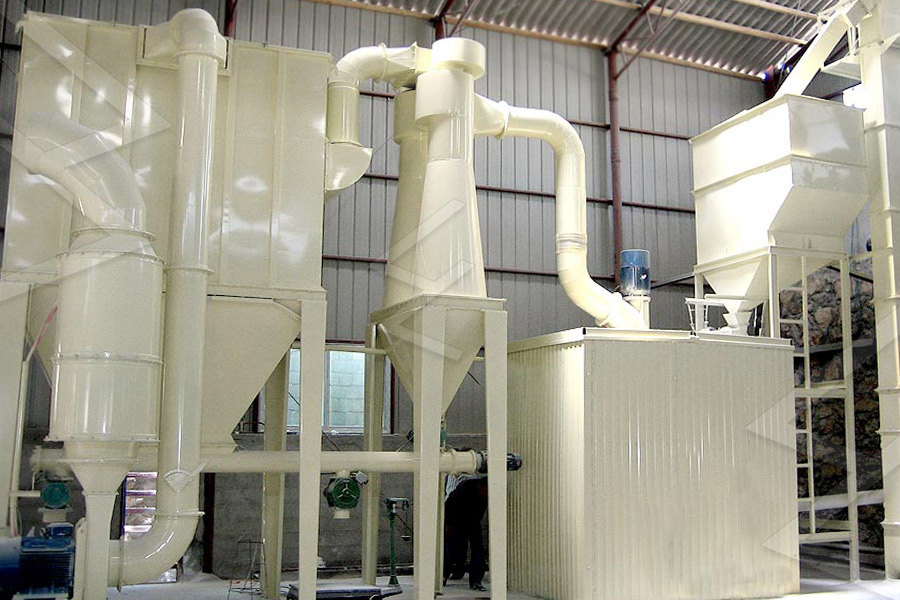
Roller Mill SpringerLink
2023年7月4日 Their working conditions are basically the same, while four rollers are the most commonlyused The Raymond mill is mainly used to grind coal, nonmetallic ore, glass, ceramics, cement, gypsum, pesticide, chemical fertilizer, and other materials The product particle size is 0045–0125 mm2021年5月5日 Grinding Machine Working Principle: In brief, we can say the working of the Grinding Machine is the Workpiece is fed against the rotating abrasive wheel The action of rubbing or friction generates between wok price and Grinding Machine: Definition, Parts, Working Principle, Operation No 1599, Pingzhuang West Road, Shanghai , China +86135 6414 3944 sales@jetmillmfgJet mill working principleIn the mill, the mixture of medium, ore, and water, known as the mill charge, is intimately mixed, the medium comminuting the particles by any of the above methods Apart from laboratory testing, grinding in mineral processing is a continuous process, material being fed at a controlled rate into one end of the mill and discharging at the other end after a suitable dwell (residence) timeGrinding Mill an overview ScienceDirect Topics
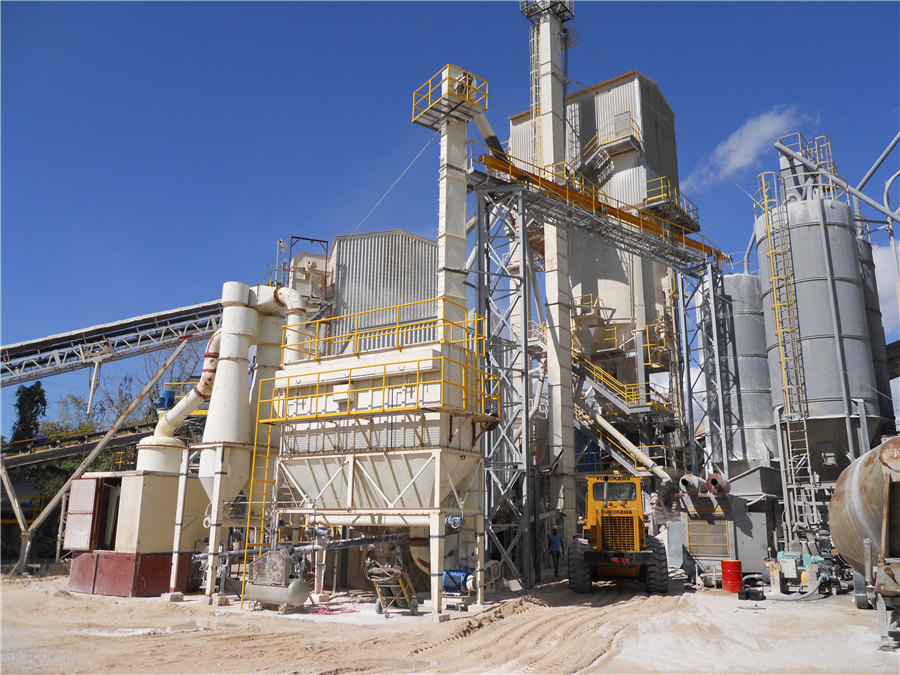
Grinding in Ball Mills: Modeling and Process Control
2012年6月1日 As the cylinder starts to rotate, the grinding balls inside the cylinder crush and grind the feed material, generating mechanical energy that aids in breaking bonds, activating the catalyst, and 2022年10月17日 Low speed: At low speed, the mass of balls will slide or roll up one over another and will not produce a significant amount of size reduction High Speed: At highspeed balls are thrown to the cylinder wall due to centrifugal force and no grinding will occur Normal speed: At Normal speed balls are carried almost to the top of the mill and then fall into a Ball Mill; Principle, Working, and Construction » PharmagudduDOVE Rod Mills are highly efficient grinding mills commonly used in minerals processing and particle size reduction through friction, attrition and compressive forces, designed to grind and blend various bulk material ranging from soft, fibrous to hard and brittle material Mainly used in size reduction of Coal/ Coke, Feldspar, Quartz minerals, Tungsten Tin ore, production of Rod Mills Grinding Mills DOVE2024年6月17日 Time and energy savings: A custom hammer mill can crush or grind materials more efficiently than standard equipment, saving your company time and energy Cost savings: Investing in a custom hammer mill can also save money over time compared to the cost of using toll grinding services to have materials crushed by a third partyUnderstanding Hammer Mill Operation Pulva
.jpg)
Raymond Mill: Working Principle Parts Powder Raymond Mill
Raymond Mill Features High Grinding Efficiency The new generation of Raymond Mill has made a lot of improvements These improvements effectively ensure the stable and efficient production Lower Energy Consumption Under ideal conditions, a Raymond Mill consumes less energy than other ordinary millsLocation: Gold, Platinum, Coal, Base metals, Chrome, Minerals processing plants Typical Dewatering Applications: Dewatering dredger stream Location: Water dam dredging, Sand mining by dredging Slimes Dam Building: This is a variant of the dewatering cyclone, where the underflow is used to build the tailings dam wallIntroduction to Cyclones AusIMM2019年10月17日 In this post, we're going to learn more about rod mill We'll cover it from two aspects: 1 Working principle 2 Structure Let's dive right in! 1 Working Principle of Rod Mill Rod mill is a common equipment for grinding operation in mineral concentrator, which is mainly suitable for rough grinding operationThe Working Principle and Structure of Rod MillThe MPS ZGM coal mill is a type of coal mill that operates at a speed of 50300r/min This equipment is used to prepare and process auxiliary materials for blast furnace ironmaking It provides suitable coal powder for the blast furnace ironmaking systemMPS ZGM Coal MillGrinding Equipment YingYong Machinery
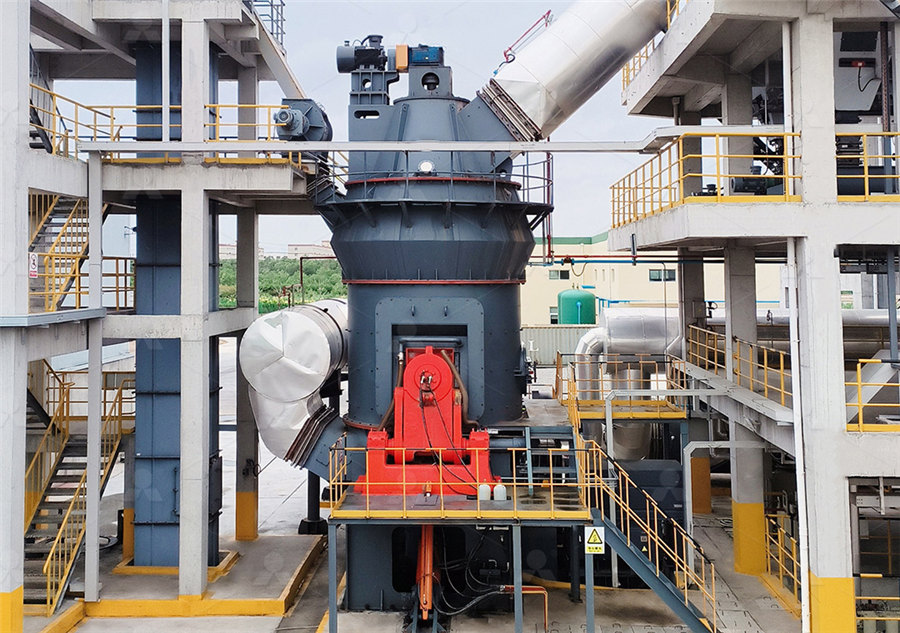
Air Swept Coal Mill Cement Plant Equipment Coal
The introduction of hot air helps to improve the drying effect of coal powder and carries coal powder into the coal mill shell during the coal grinding process Coal Powder Conveying System The pulverized coal conveying system is used to 911 Metallurgist can enter the scene and see what you have become blind to We can fix issues in ways you never thought possible Our fresh eyes will open new opportunities for your plant Each mineral processing plant has varied ore types, mining equipment, (crusher, ball mill, flotation, tailings), and management (operating) philosophyThe evaluation and prioritization of variables Metallurgists Mineral Processing Engineers 911Metallurgist2020年6月8日 The internal working principle of Raymond Mill is as follows: the crushed materials are continuously and uniformly fed into the grinding chamber of the host machine for grinding The powder after grinding is carried away by What is the working principle of Raymond Mill?1 Grindability: The grindability of the ore affects the efficiency of the grinding mill Harder ores require more energy and longer grinding times, which can impact the mill's performance and operational costs 2 Media andliner Wear: The condition of the grinding media and liners affects the mill's efficiencyUnderstanding the operation of grinding mills in the mining and
.jpg)
Gravity Spiral Concentrator Working Principle 911Metallurgist
2016年3月26日 The Humphreys Spiral has been successfully applied to recovery of chromite from chrome sands, rutile, ilmenite, and zircon from sand deposits, tantalum minerals and lepidolite from their ores, gravity concentration of base metal ores and in the cleaning of fine coal How it works: Pulp is introduced at the top of the spiral and flows downwardIt suitable for huge capacity producing, widely used in grinding nonflammable and nonexplosive materials under 7(the Moh’s hardness) Such as quartz, feldspar, calcite, talcum, barite, fluorite, iron ore, copper ore quartz, especially for slag, cement clinker, zircon sand, fly ash and carborundum, coal, etcVertical Roller Mill SBM Ultrafine Powder TechnologyCoal Mill Applied Materials: Coal, cement, ore, calcite, cement clinker, dolomite, clay, barite, etc in cement industry, building materials, thermal power, The thicker particles will be returned to the grinding bin through the return screw of the discharge device for regrinding Working Principle of Coal Mill Structural Advantages of Coal Mill with Industrial Solutions Fote Machinery(FTM)2019年7月24日 The coarsegrain chute and the ore sand chute are mainly used for the sand ore of gold, platinum and tin and other rare metal ore, such as monazite, zircon and other sand ore The slime chute is often used for some ore gravity separation,like tungsten ore and tin ore 4 Centrifugal Gravity Separation:Comprehensive Guide of Gravity Separation Method
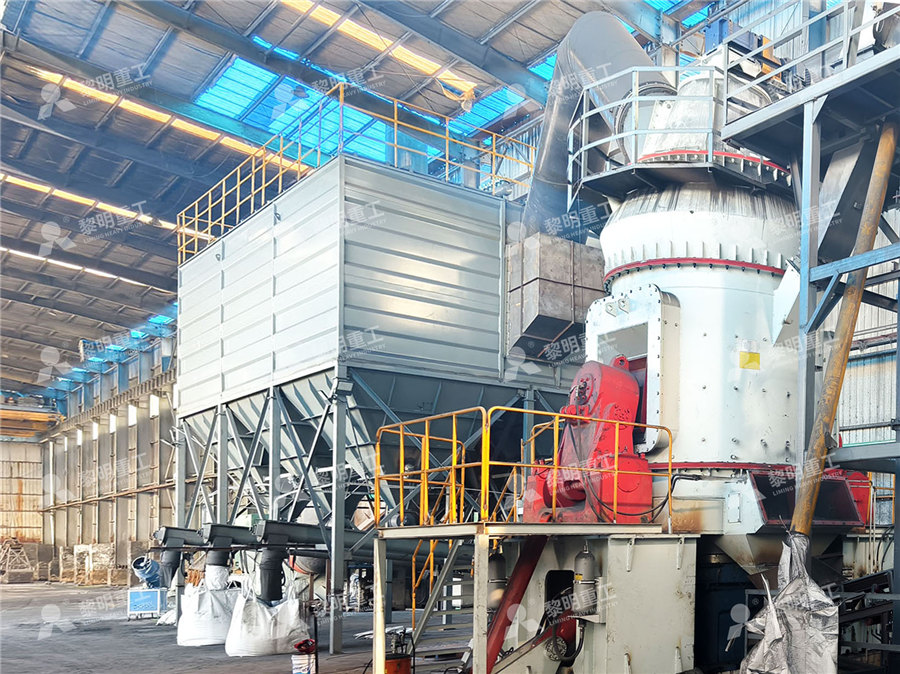
Grinding Mill an overview ScienceDirect Topics
The principle objective for controlling grinding mill operation is to produce a product having an acceptable and constant size distribution at optimum cost A crushing plant delivered ore to a wet grinding mill for further size With increased fineness grows the overall circulation rate of coal in the mill, coal retention time and the Ball Mill Grinding Process Handbook Free download as PDF File (pdf), Text File (txt) or read online for free This document provides guidance on ball mill grinding processes It covers topics such as ball mill design including length to diameter ratios, percent loading, critical speed, and internals evaluation Methods for assessing ball charge, wear rates, and liner management are Ball Mill Grinding Process Handbook2017年2月20日 All Grinding Mill Ball Mill Manufacturers understand the object of the grinding process is a mechanical reduction in size of crushable material 911 Metallurgist is a trusted resource for practical insights, solutions, and support in mineral processing engineering, helping industry professionals succeed with proven expertise Grinding Mill Design Ball Mill Grinding Mill Design Ball Mill Manufacturer 911Metallurgistvertical roller grinding mills for grinding: • Coal • Cement raw material • Clinker / granulated slag • Industrial minerals, and • Ores The core elements of these plants are the Loesche vertical mills for drygrinding the abovementioned grinding stock Loesche has PROCESS OPTIMISATION FOR LOESCHE GRINDING PLANTS
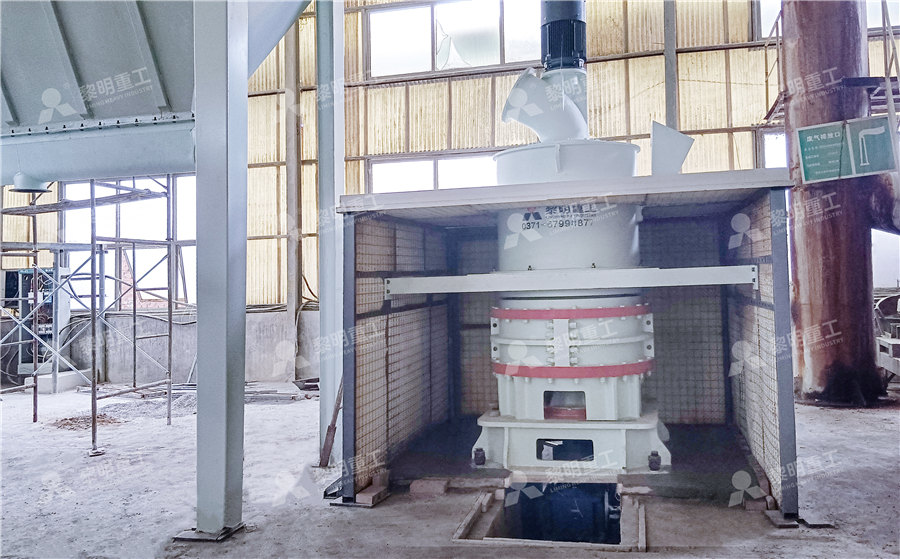
Operation Analysis of a SAG Mill under Different
2020年10月9日 working principle, and particle movement laws of a SAG mill from multiple angles, and studied the influence of these factors on speed, lining board, fill level ratio, and steel ball diameter of Coarse Powder Grinding Mill is engaging in crushing various rocks and stones with comprehensive strength not higher than 320 MPA into coarse powder and small particles It is widely used in metallurgy, mining, chemical, cement, coal, sandmaking, construction, refractory materials, and ceramic industriesCoarse Powder Grinding Mill SBM Ultrafine Powder TechnologyThe coal vertical mill, also referred to as the vertical roller coal mill, is an advanced equipment developed by our company It combines modern technology with our extensive experience in powder manufacturing This coal pulverizer efficiently integrates coal grinding and drying, providing highperformance and energysaving featuresHighEfficiency Vertical Coal Mill Enhancing Coal PulverizationThe VRM technology was introduced in the mid'90s for grinding clinker and slag by LOESCHE (Schaefer, 2001) Fig 1 illustrates the grinding parts of a Loesche vertical roller mill The grinding material is comminuted in the Loesche roller grinding mill between the rotating horizontal grinding track and stationary grinding rollersModeling and simulation of vertical roller mill using population
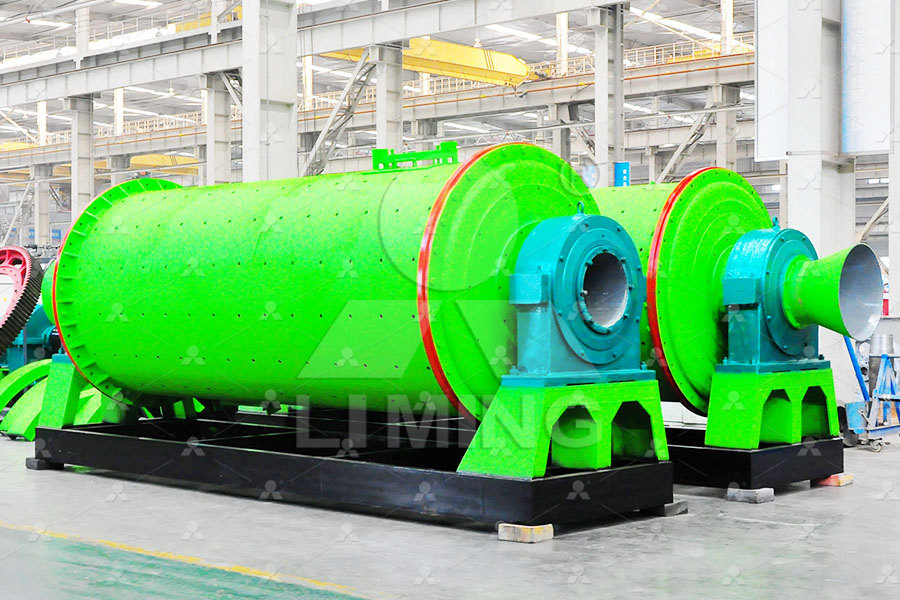
Impact Crusher Working Principle 911Metallurgist
2015年6月23日 Starting from the base working principle that compression is the forcing of two surfaces towards one another to crush the material caught between themImpact crushing can be of two variations: gravity and dynamic An example of gravity impact would be dropping a rock onto a steel plate (similar to what goes on into an Autogenous Mill)Pharmaceuticals: The attritor mill is used for grinding and dispersing pharmaceutical powders and suspensions, producing fine particles with a narrow size distribution The attritor mill has revolutionized the world of grinding with its unique working principle and many advantages over traditional grinding millsWhat is The Working Principle of Attritor Mill? ball mills supplierBall Mill Working Principle High energy ball milling is a type of powder grinding mill used to grind ores and other materials to 25 mesh or extremely fine powders, mainly used in the mineral processing industry, both in open or closed circuitsBall Mill JXSC Mineral2014年12月22日 What makes the ball mill so popular machine around the world is its incredibly simple but highly efficient working principle It works on the impact principle First, the materials that need to be reduced in size are loaded into the rotating barrel of the ball mill which is composed of grinding balls, also known as grinding mediaThe Working Principle Of A Ball Mill Sherlocksau Blog