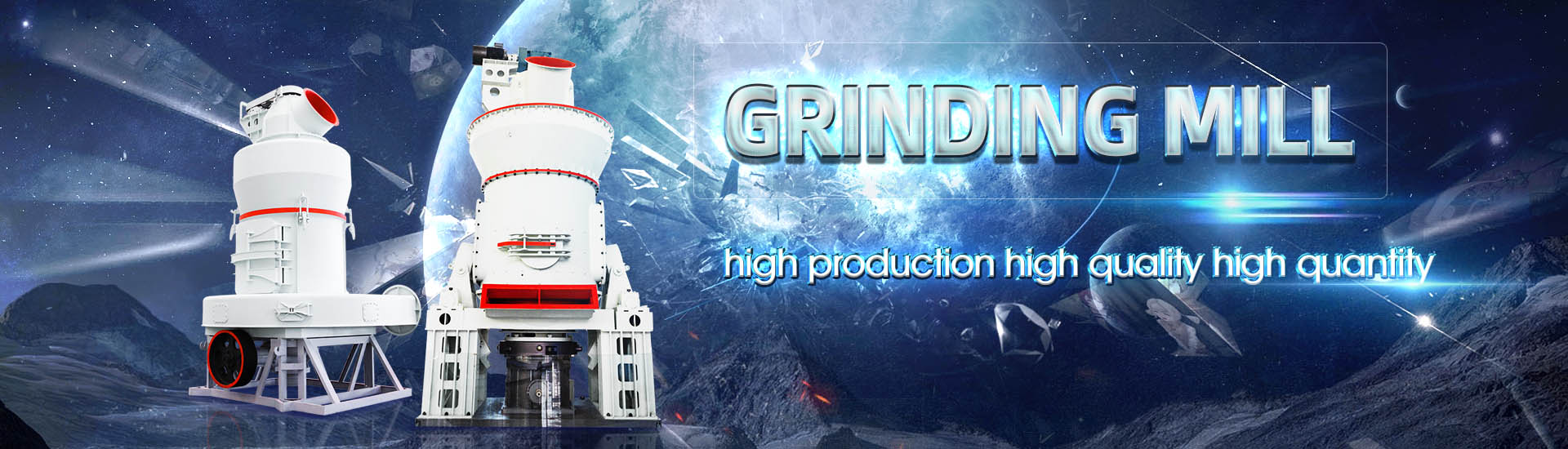
Typical faults of ore grinding mill
.jpg)
Analysis of the criticality of flaws found in trunnion of grinding ball
The grinding ball mills are equipments present in mining plants, being important in the ore comminution circuits Depending on numerous factors, such as, for example, inappropriate design, manufacturing, overloads, poor maintenance and inadequate operating procedures, 2023年10月27日 Grinding media play an important role in the comminution of mineral ores in A Review of the Grinding Media in Ball Mills for Mineral Processing The performance of a ball mill can be affected by a number of factors, including the type of ore Factors affecting ores grinding performance in ball millsIt is performed in cylindrical steel vessels that contain a charge of loose crushing bodies—the Grinding Mill an overview ScienceDirect Topics
.jpg)
STEPPING FORWARD: USING VARIABLE SPEED DRIVES FOR
to grind and crush ore is a new field being explored by main industrial players This paper Grinding of ore is one of the most important and power intensive operation in mining In order OVERVIEW OF GRINDING SYSTEMS AND MV DRIVE 2017年2月27日 Quality and performance of mill liners play a fundamental role to enhance Wear and Failure Analysis of SemiAutogenous Grinding Mill Liners2017年9月1日 The objective of this work is to assess the influence of fine grinding in ball mills Fine grinding: How mill type affects particle shape characteristics
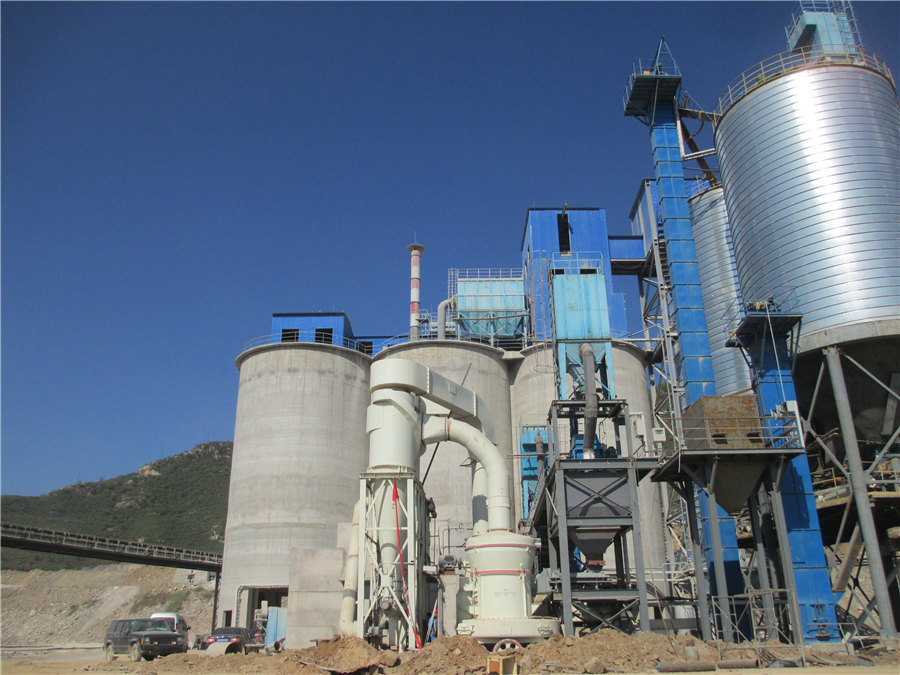
Ore Grinding SpringerLink
2023年7月20日 Grinding operation quality indices mainly include four aspects (1) Grinding Request PDF On Mar 15, 2015, Mathis Reichert and others published Research of iron ore grinding in a verticalrollermill Find, read and cite all the research you need on ResearchGateResearch of iron ore grinding in a verticalrollermillComminution, grindability, grinding, SAG mill, AG mill, milling, HPGR, work index, pilot plant INTRODUCTION The resistance of ore samples to breakage (or hardness) is measured through grindability testing 1Weight requested for the test, for typical ores (SG = 28g/cm3) Denser samples require more weight, proportional to the SGSAG Mill Testing Test Procedures to Characterize Ore Grindability2020年9月1日 Signalbased fault diagnosis method is widely used to evaluate the health of mechanical equipment In the operation process of the coal mill, there are many kinds of signals with high frequency, such as grinding current, vibration Research on fault diagnosis of coal mill system based on the
.jpg)
Research on fault diagnosis of coal mill system based on the
2020年9月1日 For modelbased fault diagnosis method, it first needs to establish a mathematical model of the coal mill Odgaard et al [2] used a simplified energy balance equation to monitor and diagnose abnormal energy flow in the coal mill Andersen et al [3] designed a Kalman filter to estimate the moisture entering and leaving the coal mill, thereby identifying whether the Speed also plays a role in ore grinding; too high of a speed can cause damage to the mill gears and other components, while too low of a speed can cause excessive wear on these same components It is important to find a balance between these two variables in order to achieve optimal grinding performanceFactors affecting ores grinding performance in ball mills2020年10月9日 This method simulates the particles size, mill power, and qualified particles quality of crushed particle, which reveal the grinding strength and energy consumption of the SAG mill In this paper Operation Analysis of a SAG Mill under Different Conditions Based on 2015年8月6日 It affects retention time and helps distribute the ore throughthe mill so each piece of rock will come in contact with the surface of the rods The % solids by volume of the rod mill discharge Rod mill grinding efficiencies have been shown to increase in the range of 5 to 15% with more dilute discharge slurry (ie, Ball Rod Mill Density – How Water Impacts Grinding
2FD{P}PC]854]XQ.jpg)
SBM Ore Ultrafine Grinding Mill
HGM ultrafine grinding mill can process nonmetallic ores with Mohs hardness less than 7 The equipment has stable operation, simple operation, long service life, low carbon and environmental protection There are 5 models of HGM ultrafine grinding mill, 9 most common grinding problems and how to fix them Most Common Grinding Process Related Problem – Chatter Grinding is a crucial process in manufacturing and it is important to ensure that it is done accurately and efficiently However, there are a number of potential faults that can occur during grinding, such as feed lines or spirals on the workpiece, scratching, burning, and Common Grinding Problems : Causes and Methods of Correction2020年4月7日 Inside the coal mill, the grinding part is composed of a groove type grinding plate and How to obtain a large number of typical fault samples is the key p oint to solve the fault diagnosis of Modeling of Coal Mill System Used for Fault Simulation2013年8月3日 In Grinding, selecting (calculate) the correct or optimum ball size that allows for the best and optimum/ideal or target grind size to be achieved by your ball mill is an important thing for a Mineral Processing Engineer AKA Calculate and Select Ball Mill Ball Size for Optimum
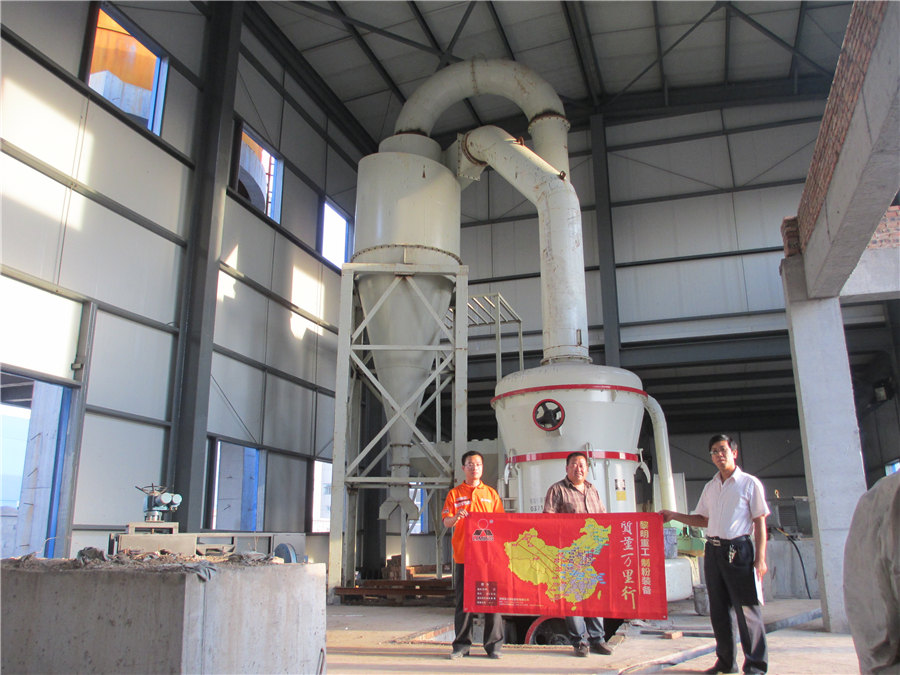
Inventory Of Common Faults And Solutions Of Mining
Fault 3: Mining ball mill has an insufficient grinding capacity Reason: This is a common problem mining ball mills face, resulting in low productivity and low ore processing efficiency One reason may be the improper design of the grinding 2018年8月8日 One of the most effective methods of grinding Portland cement is the use of an electromagnetic mill, which has proven its advantage in creating clinkerless binders [2], regulating the kinetics of (PDF) Grinding Kinetics Adjustment of Copper Ore 2023年7月20日 Therefore, the rod mill is mostly used for coarse grinding of the previous period of ball mill, or grinding of brittle materials and materials against overcrushing, such as tungsten and tin ore before gravity separation; and (3) autogenous mill – it refers to the materials which themselves are collided and ground mutually to be crushed when the grinding mill rotates, and Ore Grinding SpringerLinkHowever, ore below the pay limit adds variation to the mill grade as increased mill throughput will be required to make up for the loss of gold, and that impacts on the recovery in the plant It is against these perspectives and findings of this study that the MCF should be seen as a method that identify the real problems underground and when these are addressed, the profitability of Monitoring ore loss and dilution for minetomill integration in
.jpg)
Fine Grinding as Enabling Technology – The IsaMill
mill detritor (SMD) ore) as grinding media These features distinguish stirred mills as fundamentally different from both ball mills and Tower Mills, as demonstrated by Tables 1 and 2 Table 1 : Typical Power Intensities of different Grinding Devices Table 1: Power Intensity of Different Grinding Devices Ball Mill is a 56m D x 64m L @ 26MW2017年9月1日 With the continual depletion of high grade simple ore bodies, more complex, finely disseminated ore bodies are being processed, which has led to an increase in the prevalence of fine grinding (Sinnott et al, 2006)This has been evident in the platinum group element (PGE) industry in South Africa, where the Bushveld Complex hosts 70% of global Fine grinding: How mill type affects particle shape characteristics The present work was used to find the total grinding retention time of each ore in the mill Based on the total retention time of each ore, the optimum grinding time for each ore was identified to obtain the desired P80 passing particle size with acceptable hematite liberation(PDF) Estimation of Grinding Time for Desired Particle Size 2022年7月26日 into the grinding disc for regrinding The coal mill faults, such as abnormal loading and mill vibration, etc, increase the unit consumption of coal pulverizing, and the output of grinding coal can not be guaranteed, which has a negative influence on the operation of the pulverizing system [1] Therefore,Fault Diagnosis of Coal Mill Based on Kernel Extreme Learning
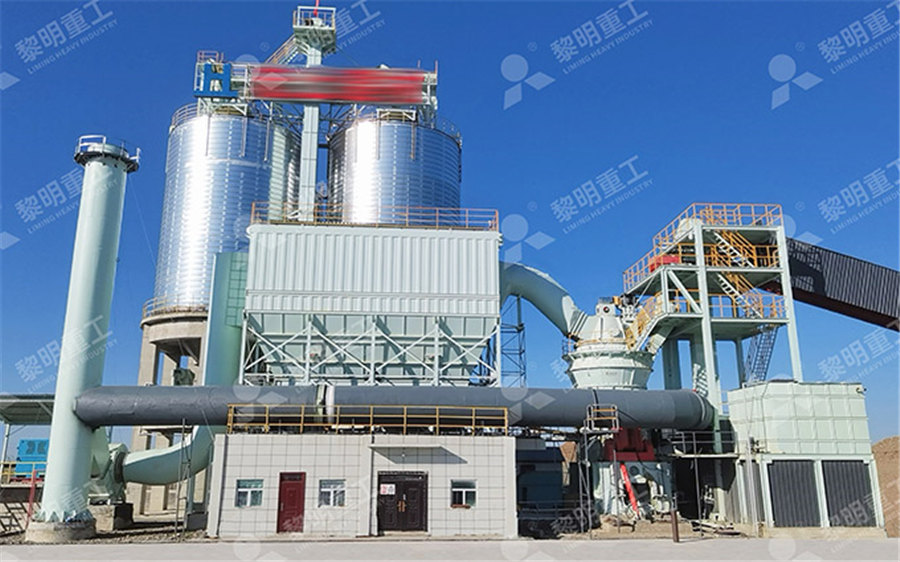
Optimization of stirred mill parameters for fine grinding of PGE
Optimization of stirred mill parameters for fine grinding of PGE bearing chromite ore, Particulate Science and Technology, DOI: 101080/2020 To link to this article: https://doi The iron ore material, together with a large amount of water, enters the mill at the inlet end The ore is crushed and grinded to a fine powder inside the mill, in a process where larger ore lumps are grinding smaller ones At the outlet end, ore with a small enough lump size passes through aStructural Analysis and Condition Monitoring of Grinding Mills: A 2016年6月6日 One of the most important was the severe stressing which took place at the connection of the mill shell and the trunnion bearing end plates, which is further aggravated by the considerable distortion of the shell and the SAG Mill Grinding Circuit Design 911MetallurgistTable 1 Typical Mill Grinds and Power Intensities Type of Mill Typical Lower Grind Size P80 µm Power Intensity kW/m3 Ball Mill 75 20 Tower Mill 20 40 UFG Mill 5 280 Two basic types of UFG mills are available, the vertical stirred mill and the horizontal stirred mill Both use rotating stirrers within a stationary mill shell to impart kineticUltra Fine Grinding A Practical Alternative to Oxidative
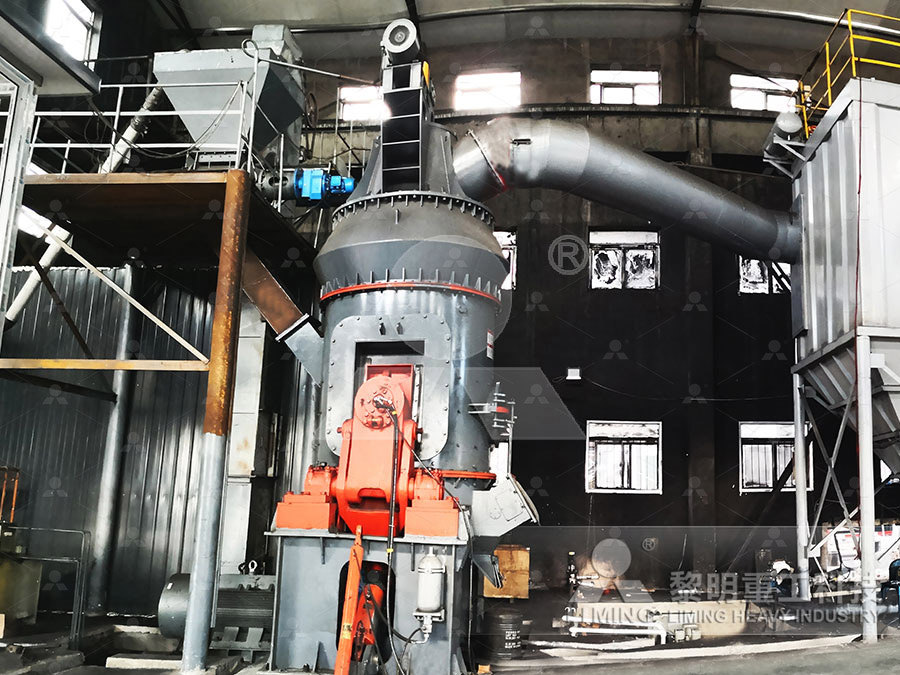
OVERVIEW OF GRINDING SYSTEMS AND MV DRIVE
Operation of Grinding mill [1] Fig 31 shows the cross section of grinding mill having internal steel liners with lifters for lifting the loadDECEMBER 2011 n IEEE INDUSTRIAL ELECTRONICS MAGAZINE 13 FIGURE 2 – An oregrinding mill FIGURE 3 – Fabrication of a phase voltage wave of a cycloconverter output power to drive an induction or synchronous motor Figure 2 shows a typical oregrinding mill [4] that is coupled to the motor(PDF) OreGrinding Cycloconverter Drive Operation and Fault: Typical mine has ore processing units at site for grinding of ore This operation is done at site for making product cost effective After grinding and processing, only useful material is transported for further processing Grinding of ore is one of the most power intensive operation in mining For grinding of ore, various mills areOVERVIEW OF MV DRIVE TECHNOLOGIES IN MINES AND FUTURE 2016年1月1日 In wet grinding practice, highstress abrasion occurs over a small region when ore particles are trapped between the grinding balls and the mill liner, and the load is sufficient to fracture A comparison of wear rates of ball mill grinding media
43.jpg)
A Review of the Grinding Media in Ball Mills for Mineral Processing
2023年10月27日 The ball mill is a rotating cylindrical vessel with grinding media inside, which is responsible for breaking the ore particles Grinding media play an important role in the comminution of mineral 2017年7月20日 ABC closed circuit, AutogenousBallMillCrusher Another similar technique is the ABC open circuit where the crusher product feeds the ball mill rather than the autogenous mill Crusher product is typical feed to a ball mill using large diameter balls but not much grinding of 2025 mm ore can be accomplished in an autogenous millAutogenous Grinding Semi Autogenous Grinding CircuitsThis mill accepts grinding set weights of up to 30 kg, the largest grinding jar has a volume of 2,000 ml chemical industry, etc, it has two ore grinding Compare this product Remove from comparison tool ball grinding mill horizontal for ore ball grinding mill Final grain size: 74 µm Ore mill, Ore grinding mill All industrial manufacturersperformance of a large diameter sag mill is shown in Figure 4 page I208 The top size data has been plotted in both raw and smoothed form It clearly shows that as top size increases the mill weight increases as the mill finds it increasingly difficult to break down the bigger rocks Power responds to the increased mill weight by also increasingI203 I204 INTRODUCTION SMC Testing
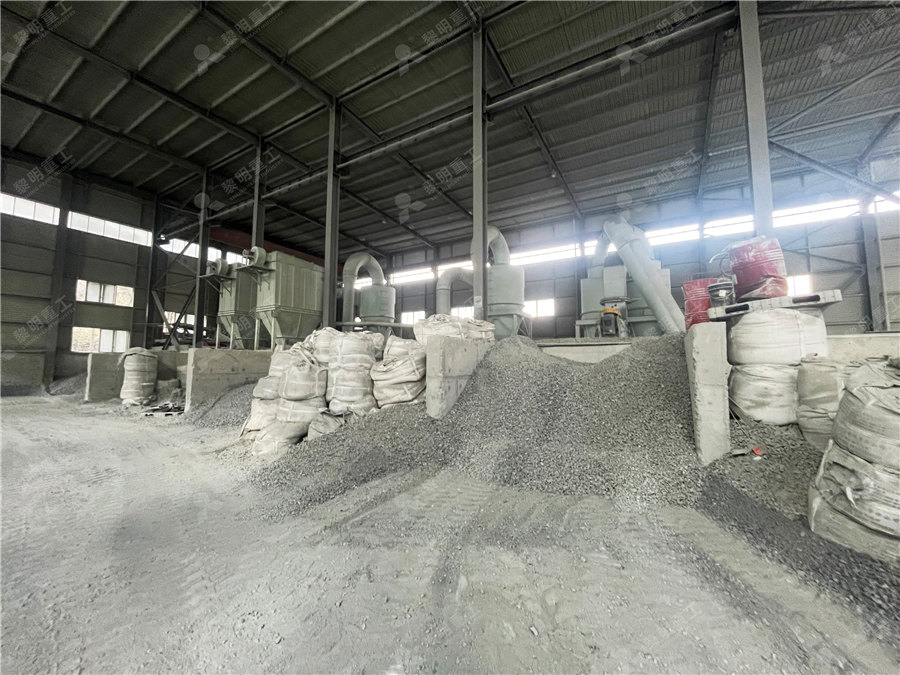
SAG Mill Testing Test Procedures to Characterize Ore
Comminution, grindability, grinding, SAG mill, AG mill, milling, HPGR, work index, pilot plant INTRODUCTION The resistance of ore samples to breakage (or hardness) is measured through grindability testing 1Weight requested for the test, for typical ores (SG = 28g/cm3) Denser samples require more weight, proportional to the SGThe second primary function of a liner is to transfer rotary motion of the mill to the grinding media and charge After all, it is the interface between the mill and the grinding charge Although work on the grinding action in mills was published 100 years ago (White 1905 and Davis 1919), the firstThe Selection and Design of Mill Liners 911 Metallurgist2017年2月20日 All Grinding Mill Ball Mill Manufacturers understand the object of the grinding process is a mechanical reduction in size of crushable material When choosing primary autogenous grinding, run of mine ore up to 200300 mm in size is fed to the mill Typical grinding mill size of feed: coarse (1″ to 2″); medium (¼” to Grinding Mill Design Ball Mill Manufacturer 911Metallurgist2017年8月5日 The installed power in the primary mill is generally much greater than in conventional circuits Since the semiautogenous or autogenous mill is dependent at least in part, if not entirely, on the ore to grind itself, a small change in ore grinding characteristics can produce a relatively large change in the grinding capacity of the millHow to Control a SAG Grinding Mill Circuit 911Metallurgist
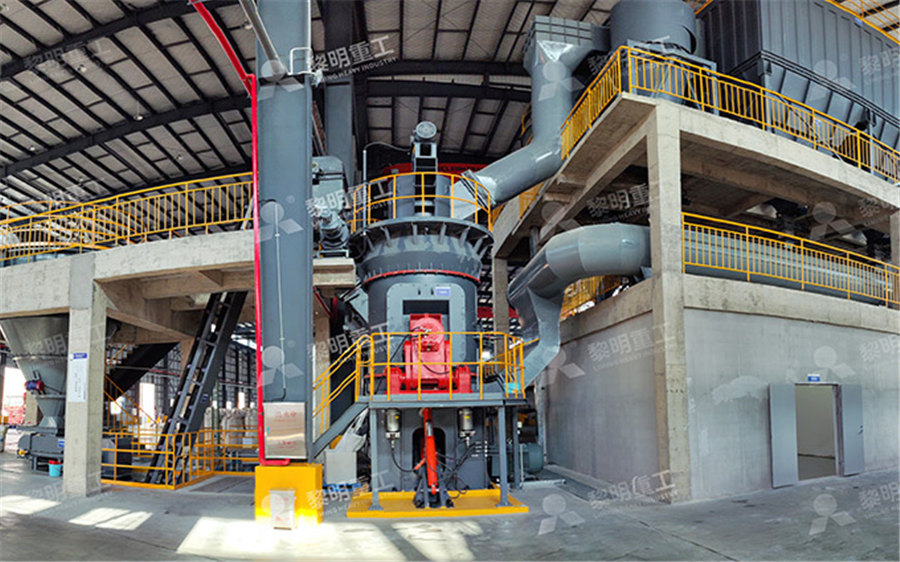
Design of a typical Autogenous Mill: PartI ResearchGate
2013年12月23日 [Show full abstract] grinding mills are classified often into five major groups: (1) impact mills, (2) ball media mills, (3) air jet mills, (4) roller mills, and (5) shearing attrition mills from 2024年5月17日 A SAG (SemiAutogenous Grinding) mill is a giant rotating cylinder filled with grinding media and the ore being reduced As the mill rotates, the grinding media lifts and the impact crushes the feed material SAG mill control refers to the practice of managing the mill load, which is the amount of material inside the mill at any given timeA guide to SAG Mill management2013年4月1日 A simple and novel nonlinear model of a runofmine ore grinding mill circuit, developed for process control and estimation purposes, is validatedAnalysis and validation of a runofmine ore grinding mill circuit 2023年6月7日 The maximum particle size of the lump ore fed into autogenous mill is 300–350 mm In the grinding mill, the ore blocks sized >100 mm function as grinding medium The ore particles smaller than 80 mm but bigger than 20 mm have poor grindability and they cannot be easily ground by big lump ore, so such material is usually called “hardto Autogenous Mill SpringerLink
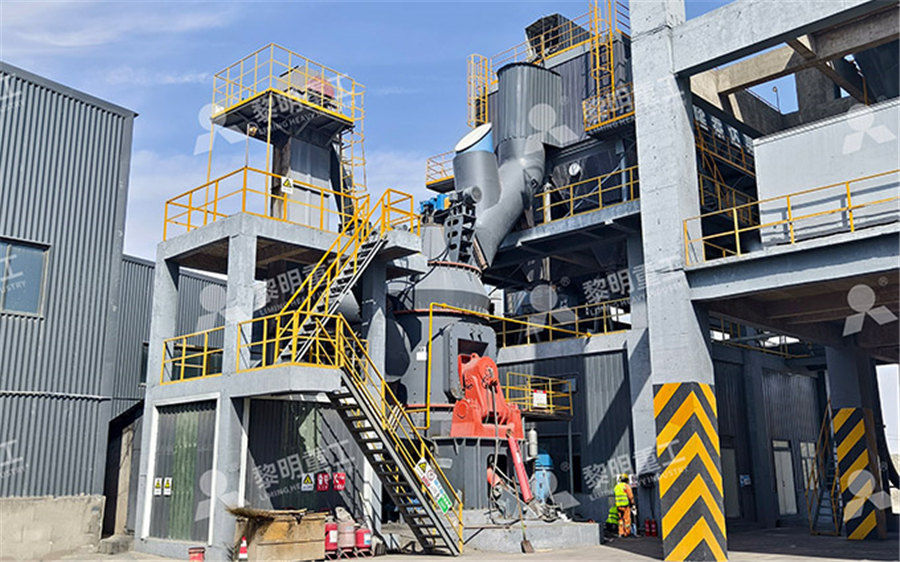
Semi Autogenous Grinding Mill ScienceDirect Topics
An autogenous mill of ID 67 m and an effective grinding length of 21 m was fed with ore of SG 38 to 20% of its volume The mill was operated continuously 24 hours per day at 1200 t per day and 75% of the critical speed The solids in the mill charge were at 80% solids Estimate:1