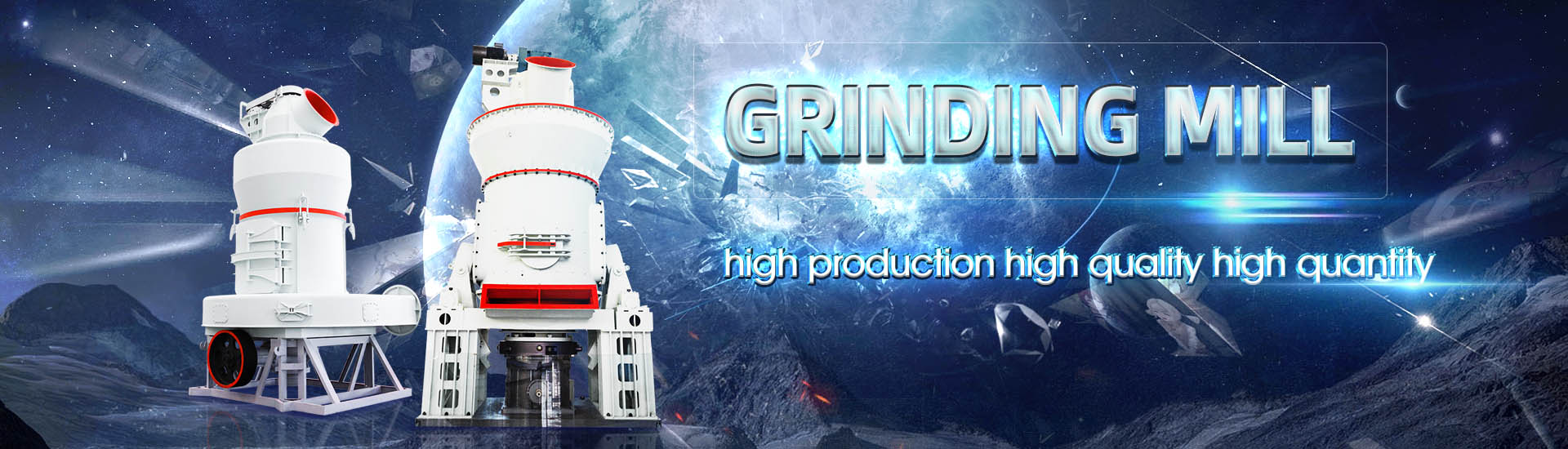
Ball consumption standard of cement ball mill
.jpg)
BALL MILLS Ball mill optimisation Holzinger Consulting
the ball mill had an average production rate of 190tph with a specific electrical energy consumption of 355kWh/t Its operational issues included: • oversized limestone • wornout lifting liners with liner thickness decreasing from 80 to 20mm • lowquality media Following Optimization of the Cement Ball Mill Operation Optimization addresses the grinding process, maintenance and product quality The objective is to achieve a more efficient operation and OPTIMIZATION OF CEMENT GRINDING OPERATION IN BALL MILLSOptimization of a ball charge for cement and raw mills with objective of optimizing the grinding efficiency The ball charge in first and particularly in the second compartment, will be adapted Ball charge optimization INFINITY FOR CEMENT EQUIPMENTball mills and combined grinding systems (pre‑grinder plus ball mill) are still widely used Which option to install depends on the local cement market, the product portfolio and raw materials, Thomas Holzinger, Holzinger Consulting, grinding system
.jpg)
Optimization of Cement Grinding Operation in Ball
The consumption of energy by the cement grinding operation amounts to one third of the total electrical energy used for the production of cement The optimization of this process would yield substantial benefits in terms of energy Table 7721 shows the improvement in the specific wear rate of grinding media in finish grinding mills, during the period from 1958 to 1971, relating to grinding of standard cement (Type I) Wear of high wear resistant grinding balls (59 Rc) in Grinding ball data INFINITY FOR CEMENT 2020年2月1日 Nowadays, ball mills are used widely in cement plants to grind clinker and gypsum to produce cement In this work, the energy and exergy analyses of a cement ball mill (CBM) were performed and Energy and exergy analyses for a cement ball mill of a new 2023年4月23日 the grinding media reduces energy and material consumption in a ball mill of cement clinkers was higher with cylpebs grinding media than with steel balls in a ball mill(PDF) Grinding Media in Ball MillsA Review
.jpg)
BALL MILL FLSmidth Cement
This reduces the energy consumption of the mill ventilation fan and keeps your energy costs down Cement grinding – taking on the tough tasks Cement ball mills have to achieve the desired grinding fineness with maximum grinding efficiency and minimal wear and tear Our ball mill is based on standard modules and the2020年7月2日 A comprehensive investigation was conducted to delineate the effect of ball size distribution, mill speed, and their interactions on power draw, charge motion, and balls segregation in a (PDF) Effects of Ball Size Distribution and Mill Speed and Their online live calculators for grinding calculations, Ball mill, tube mill, critical speed, Degree of filling balls, Arm of gravity, mill net and gross powerball mill calculations, grinding media filling degree, ball size, mill Ball Charge Ball mills for cement grinding usually operate with a filling degree between 25 and 35 % The The power consumption of the mill shaft is calculated as the product of the grindability and the product capacity P shaft = w x M P shaf t – mill shaft Process Training Ball Mill INFINITY FOR CEMENT EQUIPMENT
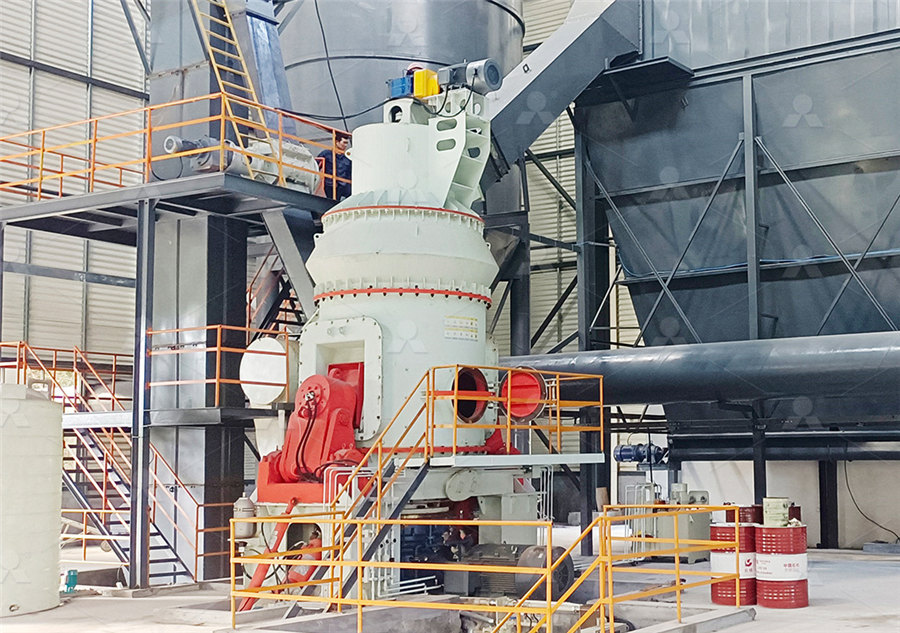
Cement grinding Vertical roller mills VS ball mills
Vertical roller mills and ball mills represent two clearly distinct technologies However, with proper adjustments to the operational parameters of the vertical roller mill almost identical cement properties can be achieved by the two mills that satisfy the cement user’s demandsNevertheless, the two types of mills have their distinctive merits2017年4月29日 In the previous discussion the fact was established that the work done by a ball when it strikes at the end of its parabolic path is proportional to its weight and velocity; then, since the velocity may be considered as constant for all the balls in the mill, the work done by a ball is proportional to its weight Since the amount of ore crushed varies as the work done upon it, it Grinding Media Wear Rate Calculation in Ball Mill2021年6月29日 Nowadays, ball mills are widely used in cement plants to grind clinker and gypsum to produce cement The research focuses on the mill speed as well as air classifier speed effect on the two Effects of Mill Speed and Air Classifier Speed on Types of cement mills There are basically 4 types of cement mills in use today: Ball Mill (BM) Ball Mill (BM): predominant despite higher energy consumption partly because of historical reason but partly also because it still offers Improvements in New Existing Cement Grinding
.jpg)
A comparison of wear rates of ball mill grinding
2016年1月1日 The wear of balls used during a grinding process is considered one of the losses that cause an increase in the operating cost allocated to the ball mill [21]However, particle size distribution is again a problem, and roll presses are now increasingly popular as a "pregrind" process, with the cement finished in a single chamber ball mill This gives good cement performance, and reduces energy consumption by 2040% compared with a standard ball mill systemCement mill WikipediaBall mill is the cement crushing equipment in the cement plant Compared with open circuit ball mill, the closedcircuit ball mill has high efficiency, Then there will be an increase in production, a decrease in power consumption and abrasion, while the content of particles larger than 64 μm will also increase significantlyBall Mill In Cement Plant Cement Ball Mill AGICO Cement2023年10月27日 The ball mill is a rotating cylindrical vessel with grinding media inside, which is responsible for breaking the ore particles Grinding media play an important role in the comminution of mineral ores in these mills This work reviews the application of balls in mineral processing as a function of the materials used to manufacture them and the mass loss, as A Review of the Grinding Media in Ball Mills for Mineral
.jpg)
Ball charge optimization INFINITY FOR CEMENT EQUIPMENT
Previous Post Next Post Contents1 Ball charge optimization2 1 How to use the BP21 2 Description of the main indicators used in this BP2101 The residue on 2mm/4mm before partition wall2102 Material filling level and ball charge expansion211 Cement mill specific power 1st compartment 212 Raw mill specific power 1st compartment Ball charge 2020年7月24日 The energy consumption of grinding is the subject of many studies, especially in the case of ball mills for grinding clinkers [8, 9], fuels [10], iron ore [11], hematite ore [12], sulfide ore [13 Determination of granulometrical composition of the clinker 2022年11月1日 In the context of fullscale continuous cement ball milling, there is no exact rule for ball selection; rather, the cement industry designs the mixture of ball sizes and BSD on the basis of their experience along with recommendations from the mill machine suppliers (eg, FLSmidth, 2012, FLSmidth, 2014) and (empirical) Bond’s approach (Bond, 1958), in which top Impact of ball size distribution, compartment configuration, and Proven Technology: The technology behind ball mills is wellestablished and widely understood This means that there is a wealth of knowledge and experience available for troubleshooting and optimizing ball mill operations Disadvantages of Ball Mills: Higher Energy Consumption: Ball mills are known for their higher energy consumption compared Vertical roller mill vs ball mill for cement grinding: Comparison
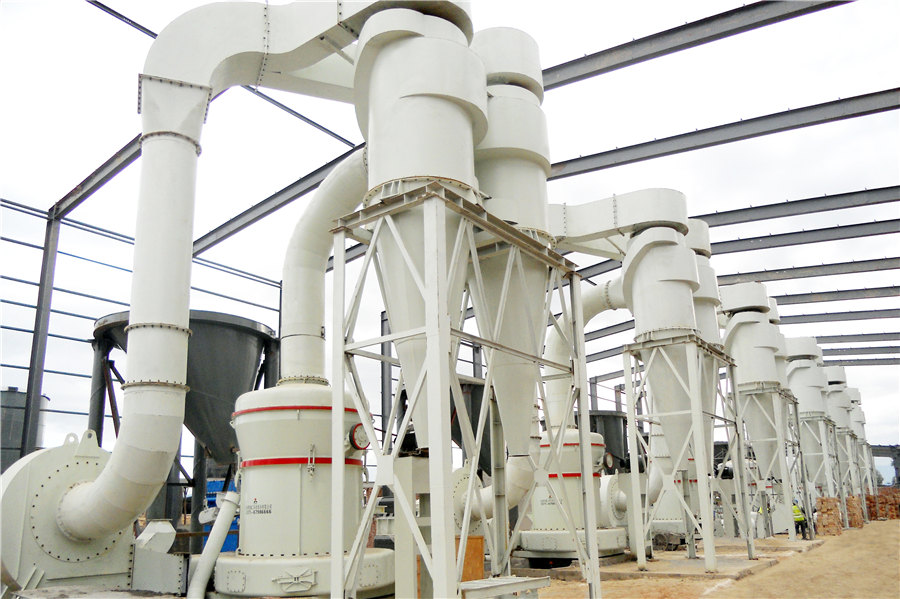
Ball Mills 911Metallurgist
2017年2月13日 BallRod Mills of the grate discharge type are made by adding the improved type of grates to a standard BallRod Mill They have vast applications within different branches of industry such as for example the ore Cement Separator Ball Mill Optimization Evaluation of mill test standard reference – Size reduction along mill axisSieve residues and Blaine value in front of the diaphragms Power consumption of mill went down Improvement Cement Separator Ball Mill Optimization2024年1月5日 Closedcircuit ball mill grinding plant Advantage: Lower power consumption than an open circuit ball mill High cement fineness achievable Cement fineness can be controlled with separator adjustment Disadvantage: Cement ball mill process calculation pdf PPTBALL MILL INSPECTION PROCEDURES record mill power consumption at counter KWh; Adjust control loop parameters if required Information on: Available information at the CCR; Please can you send me information about cement mill Loading Reply Anjireddy March 21, 2020 at 7:56 amBALL MILL INSPECTION PROCEDURES INFINITY FOR CEMENT EQUIPMENT
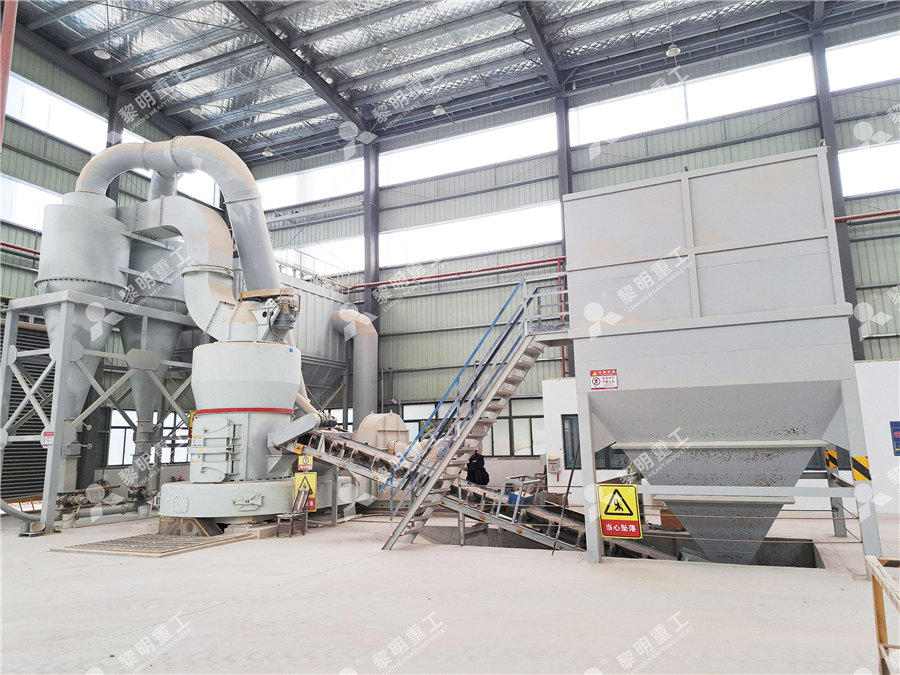
Bond´s work index estimation using nonstandard ball mills
2023年9月18日 Operating conditions of nonstandard mills were matched to standard Bond ball mill operating conditions based on: (a) the filling volume for each mill used, (b) the ore density and (c) the critical2013年8月1日 Apart from these cost factors, one of the major unsolved problems in the optimal design of ball mills concerns the equilibrium media size distribution in the mill, which is determined by the rate at which makeup media is added to the mill, as well as the rate at which these grinding media are consumed (Austin and Klimpel, 1985)Reliable prediction of grinding media Consumption of steel grinding media in mills – A review2022年2月8日 Request PDF Study of steel ball recharge and consumption in a wet cement industrial mill via a population balance model A population balance model is applied to a steel ball mill Experimental Study of steel ball recharge and consumption in a wet cement 2024年1月26日 Approximately 65–75 % of the total power consumption is used in grinding process Generally, ball mills are utilized for grinding the raw material into finished product The schematic view of cement ball mill is shown in Fig 2 Download: Download highres image (305KB) Download: Download fullsize image;Computation of charging media for a double compartment cement ball mill
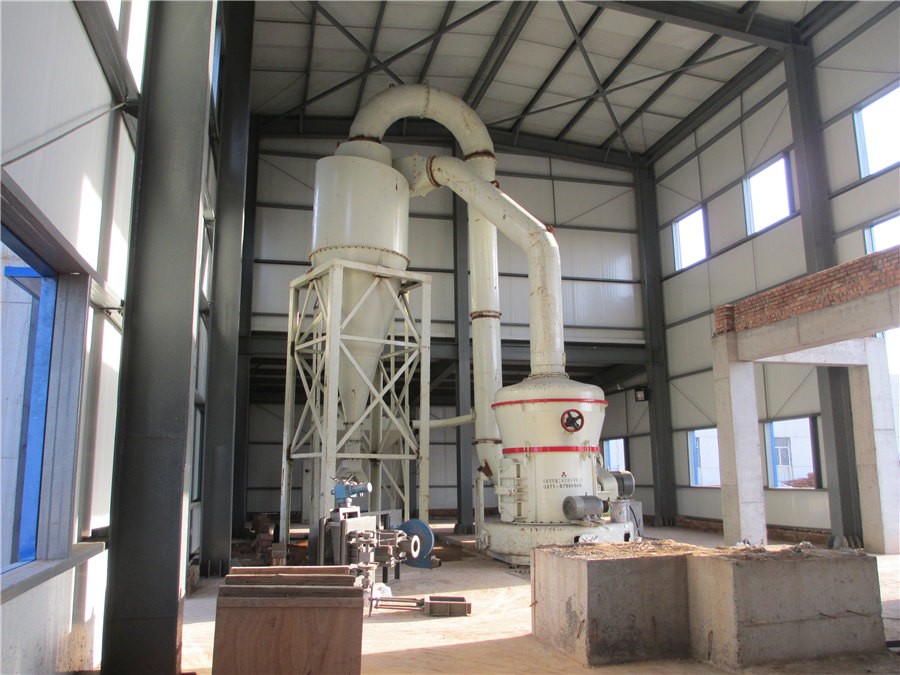
Ball mill for cement grinding
An inefficient ball mill is a major expense and could even cost you product quality The best ball mills enable you to achieve the desired fineness quickly and efficiently, with minimum energy expenditure and low maintenance With more than 4000 references worldwide, the FLSmidth ball mill is proven to do just that2013年8月3日 In Grinding, selecting (calculate) the correct or optimum ball size that allows for the best and optimum/ideal or target grind size to be achieved by your ball mill is an important thing for a Mineral Processing Engineer AKA Metallurgist to do Often, the ball used in ball mills is oversize “just in case” Well, this safety factor can cost you much in recovery and/or mill liner Calculate and Select Ball Mill Ball Size for Optimum Grinding2023年2月15日 What should we do to solve those problems? 1 First of all, it is necessary to do analyses including changes of nature of the ore, whether the amount of ore, water, sand and overflow size are normal Then do the 17 Signs of Problems with Ball Mills: Quickly 2020年11月5日 We compare 3 cement milling and cement mill processes, including cement ball mill, vertical roller mill, and rod mill Find your answer here! Skip to content +86 info@ In general the grinding efficiency 3 Necessary Cement Milling Comparison Ball Mill,
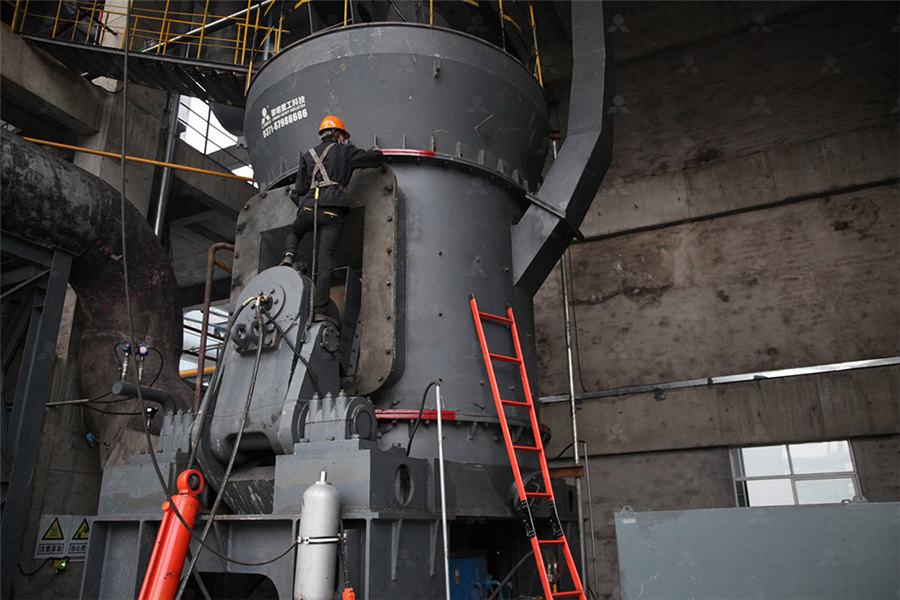
Energy and exergy analyses for a cement ball mill of a new
2020年5月1日 The primary ball charge pattern and the design ball charge pattern that is introduced by KHD Company (Cement ball mill’s manufacture Company) are presented in Table 6 It can be observed in this table that the amount of current ball charge is about 14% less than the amount of design ball charge, so it could reduce the CBM’s efficiency2023年8月23日 A cement mill is a fundamental component of the cement manufacturing process, playing a vital role in breaking down and grinding cement clinker into fine powder This finely ground powder, when mixed with other materials, produces the building material we commonly know as cement To achieve this crucial transformation, a cement mill comprises What Are the Parts of a Cement Mills? Cement Ball Mill Differences between cement ball mills and vertical cement mills, including their grinding mechanisms, energy consumption and cost Tell you when choosing the right type of mill for your needs The energy consumption of a ball mill is typically very high, especially in Difference between a Cement Ball Mill and Vertical Cement MillConventionally multicompartment ball mills are used in finish grinding of cement However, they are relatively inefficient at size reduction and have high energy consumption, so it is increasingly common to find grinding technologies such as High Pressure Grinding Rolls (HPGR), vertical mills and Horomill in cement plantsHorizontal roller mill (Horomill ) application versus hybrid HPGR/ball
.jpg)
A study on the specific rate of breakage of cement materials in a
2003年3月1日 Among these, ball size which is a critical parameter that affects the performance of a mill, has been the subject of many studies Deniz (2003 Deniz ( , 2012a investigated the grinding kinetics of 2023年10月23日 When blended by ball mill, the AluminaZirconia particles were changed into 977 μm, showing that the ball mill to refine powder particles while reducing the risk of agglomeration(PDF) A study of different grinding aids for lowenergy cement 2015年1月27日 The use of highpressure grinding rolls (HPGR) prior to ball mills has become a common practice in cement clinker grinding due to significant energy savings in comparison to ball milling aloneBallMill Grinding Kinetics of Cement Clinker Comminuted in the Adjusting mill parameters: Finetuning mill parameters such as mill speed, ball charge, filling ratio, and grinding media size can have a substantial impact on the grinding efficiency of the mill For example, a 10% increase in mill speed can result in up to 10% higher production rate, while optimizing the ball charge can lead to a 510% reduction in energy consumptionCement Mill Optimization: Practical Strategies for Enhanced