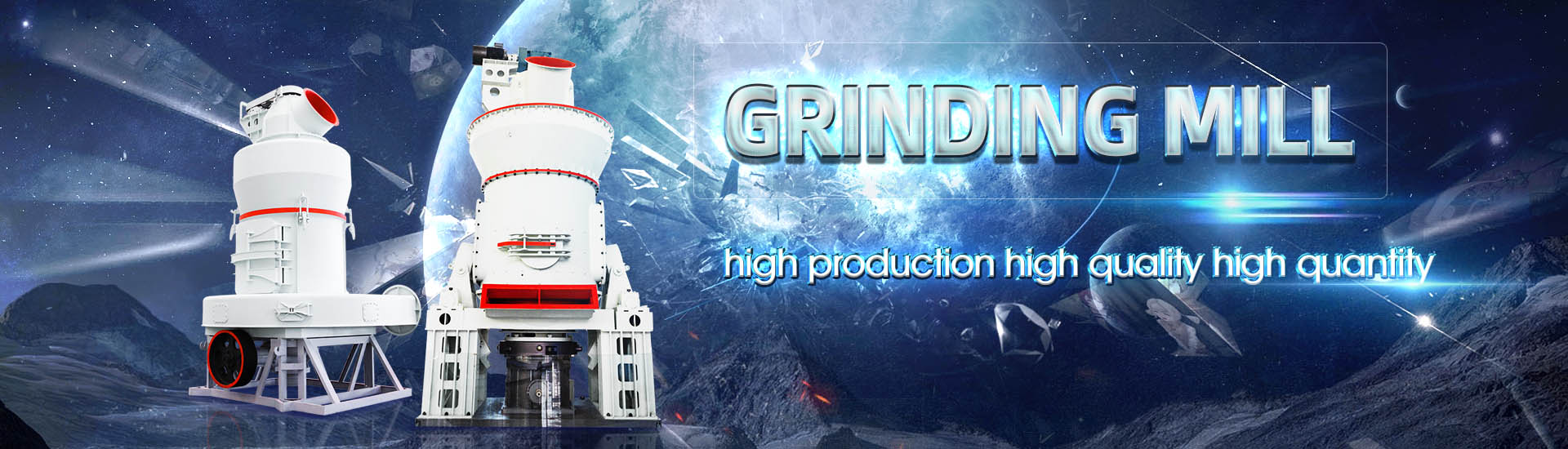
How to process clinker into cement
.jpg)
Cement Clinker Manufacturing Process with Reactions
The main raw materials (limestone, clay chalk or basalt) are quarried from natural rocks They are crushed and transferred to preblending storage where other substances (such as sand, iron ore, bauxite, shale, slag, fly ash) are added to get the desired chemical composition 展开The clinker keeps cooling and a ball mill grinds it with gypsum or other ingredients into fine cement—about 150 billion grains per pound Blending in higher ratios of limestone or SCMs can reduce a plant’s carbon footprint by up to 10%How Cement is Made Portland Cement AssociationMinimizing CO 2 emissions during cement and clinker production might be achieved through different strategies such as optimizing the process, reducing the clinker volume in cement, and Clinker Production an overview ScienceDirect TopicsFormation of a sulfate melt phase The decomposition products react with lime to form intermediate compounds which in turn form other compounds as clinkering proceeds In wetprocess kilns, and their derivatives, water must first be driven Clinker: reactions in the kiln Understanding Cement
.jpg)
Clinker Grinding Techniques in Cement Manufacturing
2023年10月19日 Clinker grinders are an important part of the cement manufacturing process They are used to grind clinker into a fine powder and are typically located at the end of the cooler in a cement plant Clinker is a nodular Cement production and concrete as building material The properties of concrete make it a primary building material where reliability and durability are required Depending on the application ~ Process characteristics of clinker and cement production SINTEFThe cement clinker manufacturing process traditionally involves intimate mixing and the subsequent heat treatment of a blend of calcareous rock, such as chalk or limestone, and Cement Clinker Production an overview ScienceDirect TopicsWith this process, we manufactured cement and clinker from industrial and laboratory raw mixes, which had to be rectified by adding kaolinite in compliance with the different cement indicators (LSF, SM, AM)Cement and Clinker Production by Indirect
.jpg)
Portland Cement Clinker SpringerLink
2014年1月1日 The main goal of the clinkering process is to produce the material of designed phase composition, which is called Portland cement clinker Under the action of high 2023年12月20日 Excess free lime, for example, results in undesirable effects such as volume expansion, increased setting time or reduced strength Several laboratory and online systems can be employed to ensure process control in The Cement Manufacturing Process Thermo Fisher Clinker: reactions in the kiln However, reading an article or two is perhaps not the best way to get a clear picture of a complex process like cement production To get a more complete and integrated understanding of how cement is made, Reactions in the cement kiln clinkeringThe cyclone preheating system Phase IV: Calcination The calcination is the core phase of the cement making dry process The calcination of the preheated raw meal takes place in the rotary kiln of the cement plant The rotary kiln is a How Is Cement Produced in Cement Plants Cement
.jpg)
How Is Cement Made? StepbyStep Guide BigRentz
2023年12月7日 The newly formed clinker has unique chemical properties that impact the cement’s strength and other key properties Step 4: Grinding and Preparing the Cement After the production of the clinker, the next step is preparing the cement powder Grinders break down the clinker into a fine powderClinker is a nodular material produced in the kilning stage during the production of cement and is used as the binder in many cement products The lumps or nodules of clinker are usually of diameter 325 mm and dark grey in color It is produced by heating limestone and clay to the point of liquefaction at about 1400°C1500°C in the rotary kiln What is Cement Clinker? Composition, Types Uses2020年8月25日 The raw meal will be sent into cement kiln to calcine clinker The semidry process of cement also belongs to the dry process of cement, add certain water into raw meal powder to make raw meal ball, which will be sent into the vertical kiln to process cement clinkerCement Production Process Cement Manufacturing Process AGICO CEMENTThe process of cement clinker manufacturing involves intimate mixing and subsequent heat treatment of a blend of calcareous rocks, After cooling and storage, the clinker is ground into a fine cement powder and gypsum is added, as a source of calcium sulphate, Cement Clinker Production an overview ScienceDirect Topics
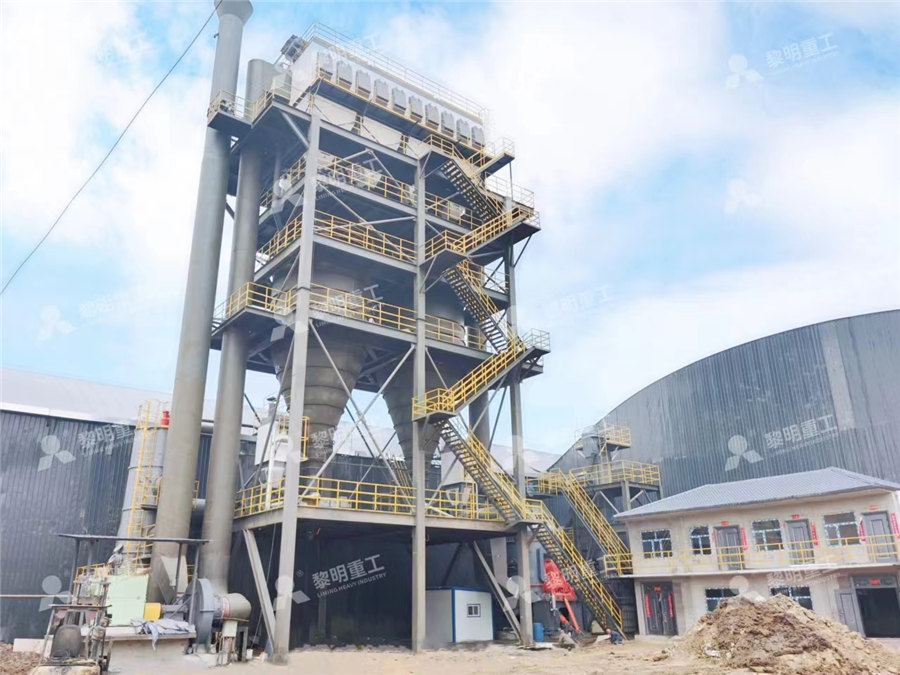
Clinker Production an overview ScienceDirect Topics
The kiln process is divided into the decomposition, transition, sintering and cooling zones The clinker is an intermediate product in cement production before adding additives to cement Its use as a raw material in cement clinker production allows the complete and highgrade recycling of Cement clinker is a type of substance formed during the cementmaking process It is created by heating a mixture of limestone and clay at extremely high temperatures in a kiln This pebblesized dark grey clinker, when ground into a fine powder, becomes cement and combined with other ingredients to form cement variantsCement Clinker: Types and Uses of Cement Clinker JK Cement2024年9月16日 It is collected as lumps or nodules appear in 3mm to 25mm in diameter The cement clinker is produced by heating clay and limestone together at a temperature range of 1400 to 1500 degrees Celsius When ground finely and mixed with gypsum, cement is manufactured Cement Clinker Types Cement clinker is categorised into 5 different types and is Cement Clinker: Its Types, Uses and Composition2022年9月21日 Global cement production has reached 39 billion tons However, the clinkerization process, which is the basis of cement production, is responsible for an approximate annual global CO2 emission of Cement and Clinker Production by Indirect
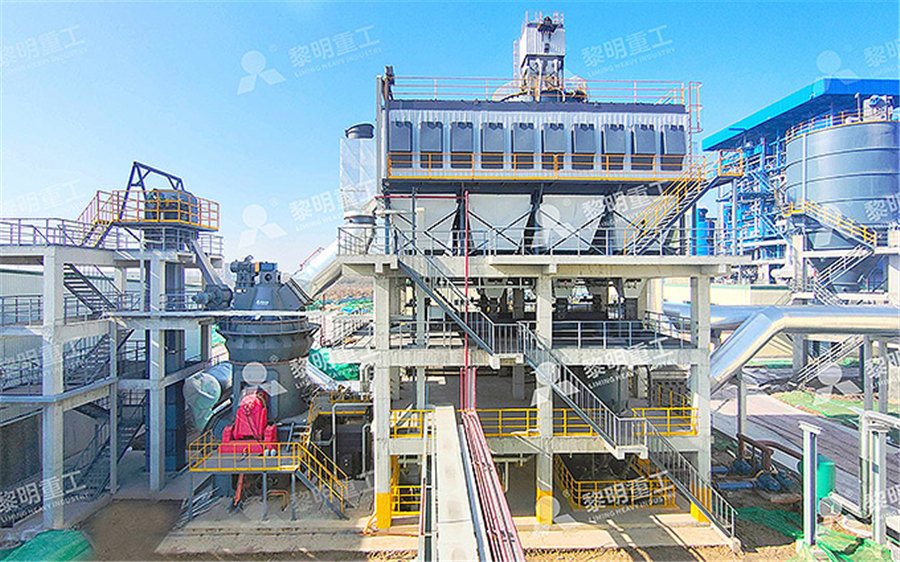
Manufacturing the cement kiln Understanding
Wet process kilns The original rotary cement kilns were called 'wet process' kilns In their basic form they were relatively simple compared with modern developments The raw meal was supplied at ambient temperature in the form 2024年9月5日 The Manufacturing Process of Cement Now, let’s explore the steps involved in the cement production process in more detail: 1 The ball mill pulverizes the clinker and gypsum into a fine powder The last product is of A Comprehensive Guide to the Cement Manufacturing Portland cement clinker overview Portland cement clinker is a dark grey nodular material made by heating ground limestone and clay at a temperature of about 1400 °C 1500 °C The nodules are ground up to a fine powder to produce cement, with a small amount of gypsum added to control the setting properties This page gives a thumbnail sketchPortland cement clinker overview Understanding CementThe process of clinkerization signifies conversion of raw meal into clinker minerals mainly consisting of C4AF(Aluminoferite), C3A(Aluminite), C2S(Belite) and C3S (Alite Alternative fuels like petcoke, rubber tyres, wood chips, etc have been introduced to economize cement making process PrecalcinerKiln Important Operational parameters Clinkerization Cement Plant Optimization
.jpg)
Clinkering Process in Portland Cement Manufacturing
2019年11月17日 This transformation is called clinkering and is analyzed as now generally practiced in cement making from the raw material to the resulting clinker Cement manufacturing may be divided into two general kinds of processing: (a) crushing and grinding, and (b) turning, this is accomplished by means of a variety of operations, including excavation The cement clinker calcination is an important step in the cement production process It mainly occurs in cement kiln and can be roughly divided into six reaction stages, namely drying, preheating, chemical decomposition, exothermic reaction, sintering and coolingCement Clinker Calcination in Cement Production Process AGICO Cement would be a length of 135 m and a diameter of 25 m, with a speed of approximately 20 revolutions per minute Such a mill would normally have a load of approximately 90 tons of grinding media, graduated from 90 mm to 60 mm in the first chamber, 50 mm to 15 mm in the second chamber and 15 mm down in the final chamberAn Introduction to Clinker Grinding and Cement Storage2014年1月1日 Portland cement clinker burning, 22 The phase systems important for cement chemistry, 23 The clinkering process in industrial mixes, It has insignificant effect on clinkering process and clinker properties, The transformation of the rhombohedral into monoclinic plane at 1050 °C is continuousPortland Cement Clinker SpringerLink
.jpg)
Quality Composition of cement clinker
Production of clinker in a reducing atmosphere in a cement kiln can seriously degrade the quality of clinker and the cement produced from the clinker However, an industrial cement kiln is tolerant of reducing conditions without these adverse effects manifesting themselves, provided that the clinker falls into the cooler at a temperature above 1250°C and is cooled in airAlthough the dry process is the most modern and popular way to manufacture cement, some kilns in the United States use a wet process The two processes are essentially alike except in the wet process, the raw materials are ground The Fundamentals Of How Cement Is MadeCement kilns are an essential component of the cement manufacturing process, playing a crucial role in producing the clinker that is ground into cement These massive, rotating cylindrical vessels are designed to withstand extreme Comprehensive Guide to Cement Kilns: Processes, 2024年3月1日 Cement plants have used new grinding equipment, dryprocess instead of the wetprocess kiln, modern clinker kilns, and multistage preheaters that can save energy [1] The use of blends with renewable fuel and fossil fuel [ 2 ] or the use of solar calcination reactors [ 3 ] can reduce emissions and save energy in cement manufacturingToward smart and sustainable cement manufacturing process:
.jpg)
How cement is made Heidelberg Materials
Clinker grinding After burning, the clinker is cooled down and stored in clinker silos From there the clinker is conveyed to ball mills or roller presses, in which it is ground down to very fine cement, with the addition of gypsum and anhydrite, as well as other additives, depending on the use to which the cement is to be putThis results in the production of cement clinker, an intermediate product in the manufacturing process The cement clinker emerges from the kiln, is cooled, and then finely ground to produce the powder we know as cement The fuels combusted to heat the kiln account for about 40% of cementmanufacturing emissionsHow cement and concrete are made Cement Association of 2024年8月23日 ICR explores the details of the grinding process, which is a critical stage in cement manufacturing, which significantly impacts the final product’s quality and characteristics By finely grinding raw materials into clinker and mixing them with gypsum, cement manufacturers ensure the fineness and uniformity essential for strong and durable cementFrom Clinker to Cement Indian Cement Review2023年7月3日 To understand clinker better, we need to dive into the cement manufacturing process From quarrying raw materials to the final grinding, each stage is crucial in determining the quality of clinker We’ll take a closer look at how limestone, clay, and other additives are processed and heated in the kiln to produce clinkerWhat is clinker? The Crucial Element for Building a Solid Future
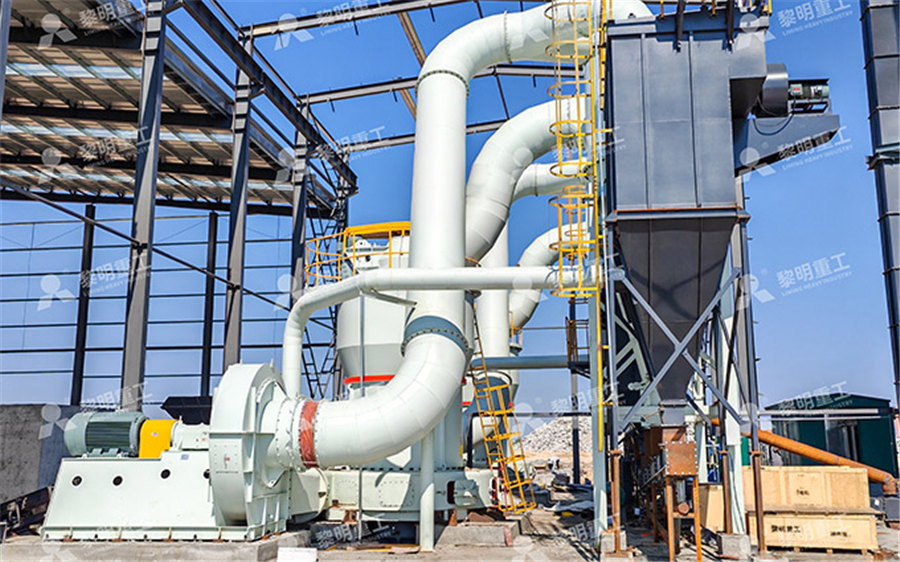
Production Process CEMEX Philippines
Clinker is the intermediate product used in the manufacturing of cement There are two primary processes used to manufacture clinker: the dry process and the wet process Our plants use the dry process, which is more energy efficient In the wet process, the raw materials are mixed with water to form slurry, which is fed into a kilnInstead, it serves as a precursor to cement Clinker is ground into a fine powder to produce cement, which is then mixed with other materials to create various construction products During the production process, clinker is exposed to extreme heat, reaching temperatures of around 1450 degrees Celsius Cement vs Clinker What's the Difference? This vs ThatDiscover the detailed steps of the cement manufacturing process in India The hot clinker from kiln discharge is cooled very quickly/ quenched in air with the help of efficient coolers Heidelberg Cement offers insights into modern techniques and industryleading practices mycem Cement Who Are We;Know All About Cement Manufacturing Process in India mycem cementEverything you need to know about clinker/cement Grinding Your choice must take into account the effect of porosity will have on throughput and the separator cement mill, dry process raw mill, wet process raw mill Diaphragm location: Everything you need to know about clinker/cement
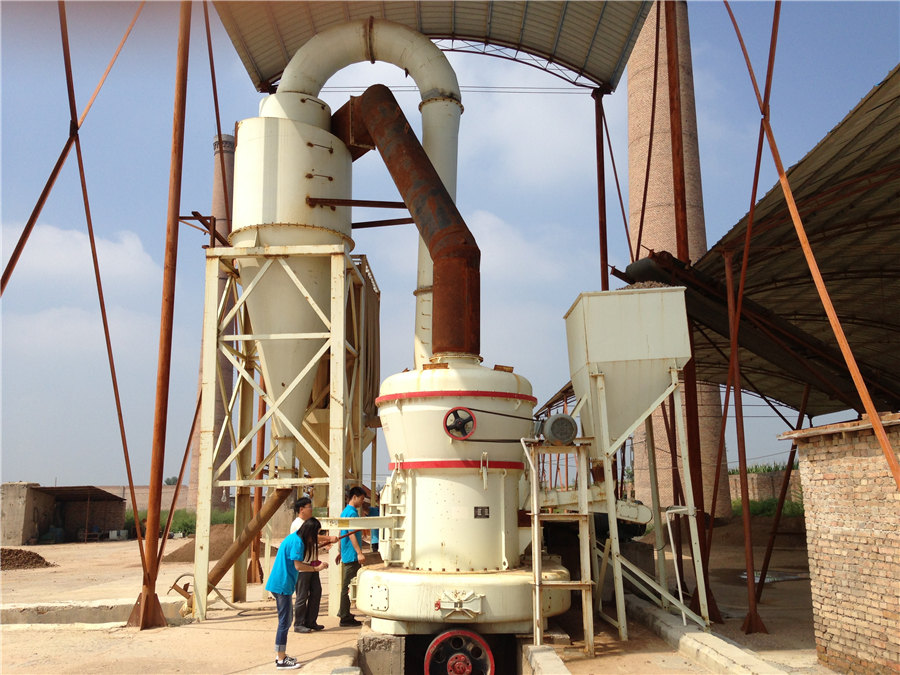
What is Cement Clinker? Composition, Types Uses
Sulfate Resistant Clinker – The composition of this type of clinker is alite 76%, belite 5%, tricalcium aluminate 2%, tetra calcium aluminoferrite 16%, and free calcium oxide 1% In recent years the production of this type of clinker has 2020年1月27日 6 steps of the cement manufacturing process When we talked about the manufacturing of cement, anyone who knows the cement manufacturing process slightly will mention “two grinding and one calcination”, Cement Manufacturing Process: 6 StepsTo Make The extracted raw materials are crushed and then ground into a fine powder This process increases their surface area and facilitates chemical reactions and grinding parameters can affect the formation of the clinker as well as the grinding of the clinker into cement What are the main ingredients of cement? Lime, clay and shale are some of Cement Ingredients: chemical composition of cement JK Cement2023年6月6日 Clinker Cooling – After leaving the kiln, the clinker is extremely hot Manufacturers must cool the clinker rapidly to ensure its physical properties They use air or water in specialized cooling units called clinker coolers Clinker Grinding – Cement machines such as ball mills or vertical rollers mills grind the cooled clinker into a powderCement Clinker: Production, Composition, Types, and Impact
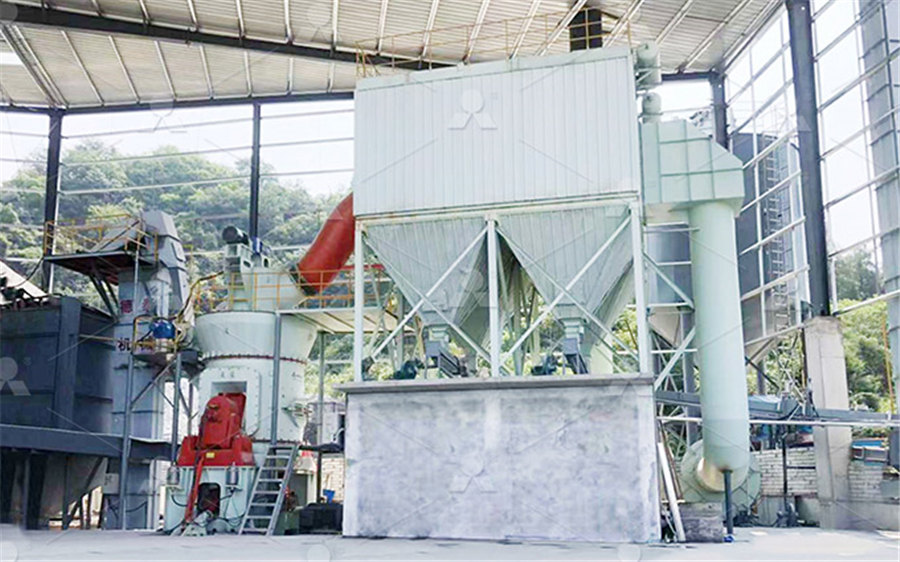
Manufacture of Cement Materials and Manufacturing Process of
Each process is explained chemical reactions for manufacture of Portland Cement Cement is a greenish grey colored powder, made of calcined mixtures of clay and limestone When mixed with water becomes a hard and strong building material The history of cement goes back into Roman Empire The modern day cement1971年8月17日 116 Portland Cement Manufacturing 1161 Process Description17 Portland cement is a fine powder, gray or white in color, that consists of a mixture of hydraulic cement materials comprising primarily calcium silicates, aluminates and aluminoferrites More than 30 raw materials are known to be used in the manufacture of portland cement, and these116 Portland Cement Manufacturing US EPAProcess heat overview Clinker, and clinker substitutes, are the active components that confer cement its binding properties Producing traditional cement clinker is an extremely energy and CO 2 intensive process In the EU, 90% of clinker is now made via the more energy efficient dry clinkermaking process (2) Older, less efficient wetDeep decarbonisation of industry: The cement sector EuropaPortland cement PC Aïtcin, in Science and Technology of Concrete Admixtures, 2016 Abstract Portland cement is at the same time the fruit of simple technology and a complex science It consist in firing at 1450 °C very simple pulverized raw materials having a very specific composition to produce an intermediate product called Portland cement clinker or simply clinkerPortland Cement Clinker an overview ScienceDirect Topics
.jpg)
Everything you need to know about Clinker Coolers
In cement manufacturing, formation of clinker nodules occurs at the entrance to the hottest part of the kiln with a material temperature of around 1280°C The clinker is preferably in the form of 10mm to 25mm size nodules that exit from the front end of the kiln into the cooler