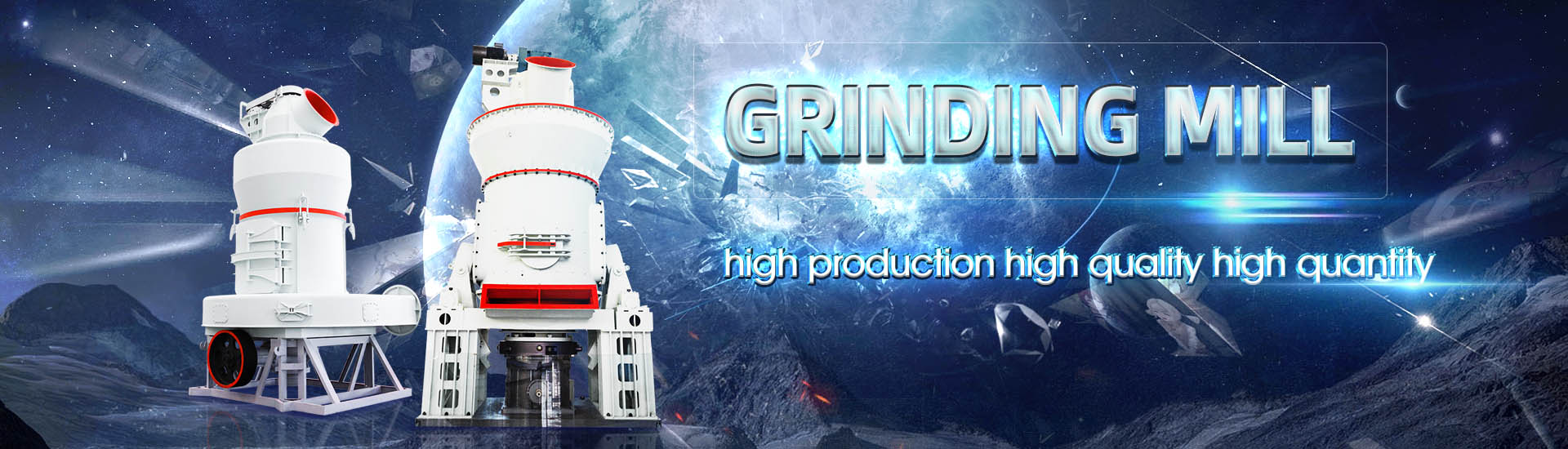
Drum grinding system machine operating procedures
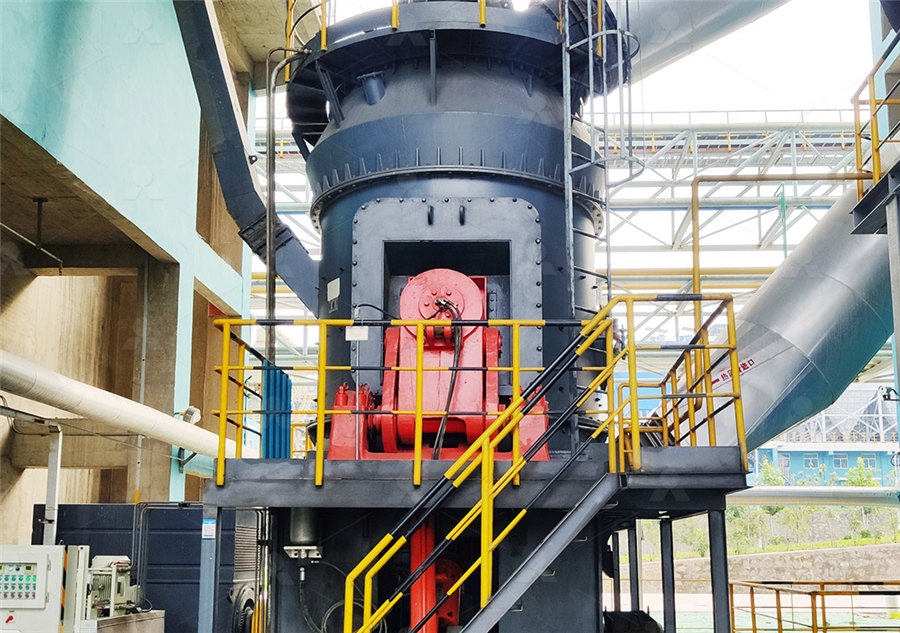
RETSCH TM 300 MANUAL Pdf Download ManualsLib
Operating the device 57 Preparing the grinding process 571 Filling the grinding balls Load the grinding drum with grinding balls • First fill the balls into the grinding drum, followed by the materialWORKSHOP MACHINES PEDESTAL GRINDER • Inspect the wheels before turning on the power Do not use wheels that are chipped or cracked • Stand to one side of the wheel when STANDARD OPERATING PROCEDURES for COMMON TOOL The machine is d ispatched completed with the exception of tabe,so as to protect the harden and ground slideways from d amage shipmentWhen installed,mounting the table as following INSTRUCTION MANUAL FOR PRECISION SURFACE GRINDER Grinding machines are often found between milling, shaping, drilling and even slotting machines, without any thought of the consequences of such planning In such cases, it is impossible to INSTRUCTION MANUAL FOR PRECISION SURFACE GRINDER
.jpg)
G32P(A)CNCmanual(Eng)A Sharp Industries
Grinding Machine We believe that this machine is capable of meeting your requirement and to make your product with best high precision quality This brochure is an operation and Vermeer horizontal grinders feature a patented hardfaced duplex drum designed for aggressive cutting performance The industryexclusive design features reversible hammers and tips, VERMEER HORIZONTAL GRINDERS2021年8月13日 A rotary drum is a carefully balanced system Proper alignment of the drum ensures that despite the constant rotation, heat stresses (where applicable) and static and Basic (But Essential) Rotary Drum Maintenance Processing During operation, keep hands a safe distance away and only use adjustment tools on lathe to maneuver work piece Know the location of start and stop switches or buttons and keep the STANDARD OPERATING PROCEDURE AVIT
.jpg)
Operating Instructions and Parts Manual Drum Sander
This manual is provided by JET covering the safe operation and maintenance procedures for a JET Model 2244 Pro3 Drum Sander This manual contains instructions on installation, safety Grinding is the process of removing metal by the application of abrasives which are bonded to form a rotating wheel When the moving abrasive particles contact the workpiece, they act as GRINDING MACHINES Carnegie Mellon University2024年7月21日 About Us Discover the story behind Artizono and our commitment to providing topquality machine tools; Shop Explore our extensive range of cuttingedge machine tools designed for precision and performance; Download Brochure Get a comprehensive overview of our products and services by downloading our latest brochureGrinding Machine Safety: Essential Tips for OperatorsDiscontinuous operated drum mills make, in addition to size reduction, homogenization of the material to be ground possible Drum mills have a horizontal grinding drum rotating around a fixed center of rotation Located in Drum mills by SIEBTECHNIK TEMA Comminution
.jpg)
Safe Operating Procedures SOP 20 Feed Mill / Roller Mill
Safe Operating Procedures This SOP should be used in conjunction with relevant machinery manuals and manufacturer recommendations Procedure Reference Version Effective Date Review Date Page Number Date Printed WHS SOP 20 10 28/03/2018 28/03/2021 2 24/04/2018 the mill settings (with large spanner)It is designed to be used as an adjunct to teaching Safety Procedures and to act as a reminder to users prior to machine use SAFE OPERATING PROCEDURES Pedestal Grinder DO NOT use this machine unless you are authorised and have been instructed in its safe use and operation Safety glasses must be worn at all times in work areasSAFE OPERATING PROCEDURES Pedestal Grinder2024年4月1日 Purpose of Document CNC Machine SOPs outline a safe operating procedure for CNC machine use The SOPs can also be used as a training and induction documentThe primary goal is to protect workers from injury or illness by outlining a safe system of work and providing adequate training and instruction This form is broadly aligned with AS45001:2018FREE CNC Machine SOP (Safe Operating Procedure) TemplateWEBER grinding machines Its variable operating height makes the machine especially fl exible, above all for manual feeding For deburring, rounding, descaling and surface grinding: Different machining methods with one or two machining stations can be combined with each other Working widths 1100 and 1350 mm Working height 800–900 mm (variable)Grinding, rounding, deburring and descaling
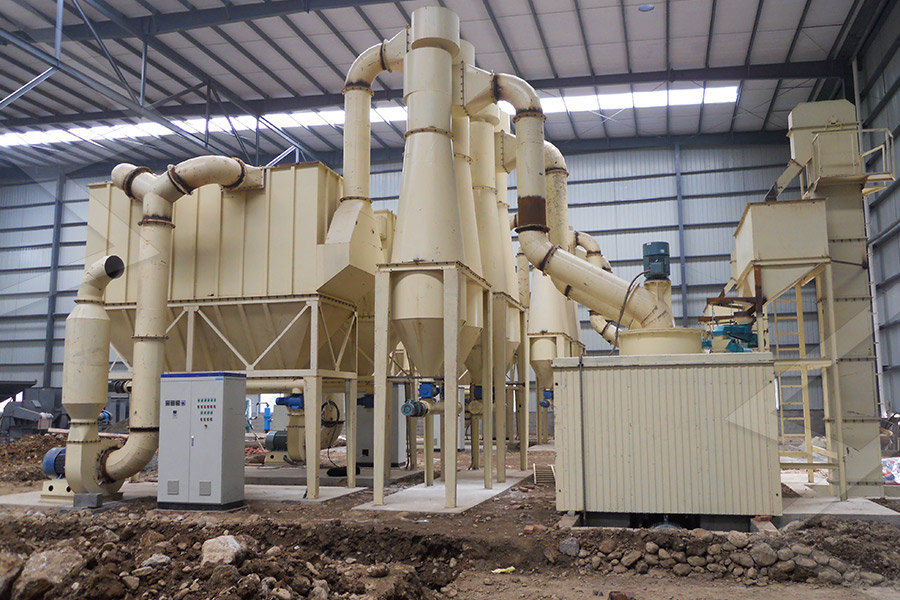
Standard Operating Procedure (SOP) Guide Examples
2020年7月10日 What’s a Standard Operating Procedure (SOP)? A standard operating procedure, or SOP, is a set of detailed stepbystep instructions that describe how to carry out any given process Most companies that are serious about process management use SOPs to manage their daytoday activities Why? Well, Standard Operating Procedures allow you to:SafeOperatingProcedures02BenchGrinder Free download as PDF File (pdf), Text File (txt) or read online for free This document provides safety procedures for operating a bench grinder It lists required personal protective equipment and safety checks that must be performed before and during operation of the grinder Hazards associated with using the grinder are identified as hot Compulsory Ppe As Needed Ppe: Safe Operating Procedures SOP 2021年1月5日 The following procedures are shared by Zaozhuang Make Machinery Co, Ltd 1、 The operator must be familiar with the structure and performance of the machine tool, and obtain an independent operation certificate 2、 Operators should keep the machine clean and strictly implement the maintenance systemRadial drilling machine maintenance proceduresEvery grinding machine has an optimal method of operation The variations in technique between different machines will depend on a range of factors, such as: the size and type of machine it is, including the number of heads and the manufacturer's design; the tooling that's been fitted and the CSP you're aiming to achieveConcrete grinding, Practice of grinding, Operating procedures
.jpg)
Improving the efficiency of the coal grinding process in ball drum
2022年2月24日 mal power plants running on ball drum mill grinding systems In [2], it is stated that this share of energy is classified as very significant compared to the modern onesOperation in various machines STANDARD OPERATING PROCEDURE BENCH GRINDING MACHINE Control Plan: • Read and become familiar with machine’s operating procedures before operating • Always know where the power off switch is located in case of emergency • Always turn switch to off position when not operating machineSTANDARD OPERATING PROCEDURE AVITSafe Operating Procedures This SOP should be used in conjunction with relevant machinery manuals and manufacturer recommendations Procedure Reference Version Effective Date Review Date Page Number Date Printed WHS SOP 15 10 28/03/2018 28/03/2021 2 24/04/2018 POTENTIAL HAZARDS 1 Explosion 2 Burns 3 Eye Injury 4 Fire and ExplosionSafe Operating Procedures SOP 15 Oxy Acetylene Cuttingtool grinding machines for grinding as well as laser machines for indexable cutting inserts and rotationally symmetrical tools made from carbide Ewag AG is part of the UNITED GRINDING Group Together with our sister company, Walter Maschinenbau GmbH, we consider ourselves to be a supplier of systems and solutions for the complete machining of INSERT LINE UNITED GRINDING
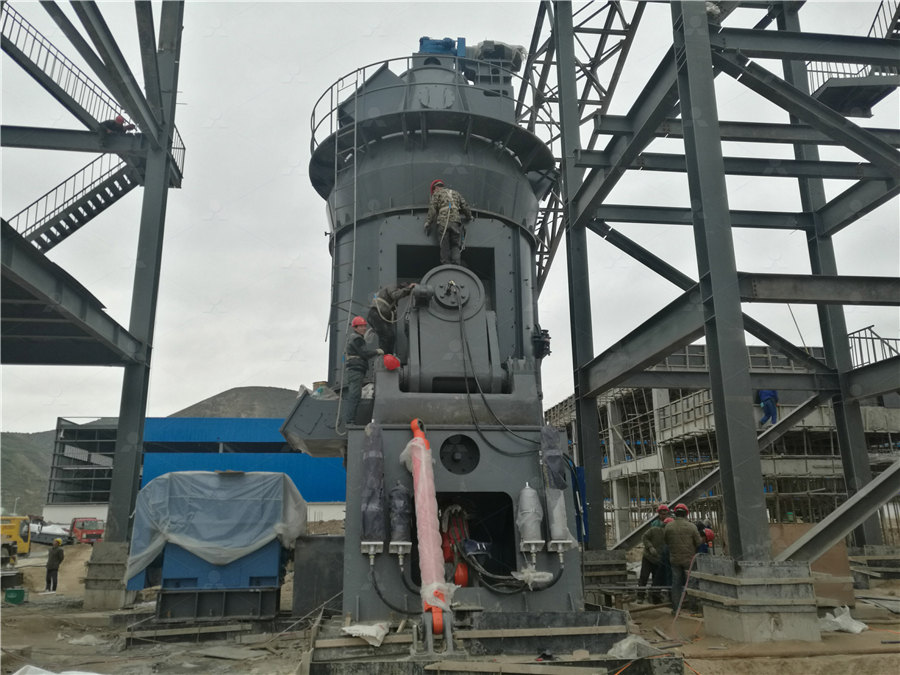
AusIMM – Leading the way for people in resources
%PDF16 %âãÏÓ 4215 0 obj > endobj 4235 0 obj >/Encrypt 4216 0 R/Filter/FlateDecode/ID[87C03FABF6FB2246BC4F9AB649B4B217>]/Index[4215 26]/Info 4214 0 R/Length 101 If the drum were not aligned following grinding, the misalignment of the drum, however minuscule, would immediately begin causing wear to tires and trunnion wheels, bringing them back to their pregrinding condition While manual methods are available, rotary drum alignment is typically carried out using a laser alignment systemTire and Trunnion Grinding: Critical Rotary Drum Maintenance2017年9月13日 Safe operating procedures also minimise some of the risks of working with robotics A safe work system needs procedures for entry, including who can access the robot to do identified tasks, maintenance and repair Inspecting and maintaining a robot can present different hazards from working with the robot Assess all hazards for risksSafe use of machinery WorkSafe2 SemiAutomatic Drum Filling System: Combining automated processes with operator involvement, the semiautomatic system provides a balance between automation and control Operators may be responsible for tasks such as drum placement and monitoring, while the actual filling process is automated 3 WeightBased Drum Filling System:DRUM FILLING SYSTEM: EVERYTHING YOU NEED TO KNOW
.jpg)
COAL GRINDING SYSTEMS SAFETY CONSIDERATIONS PEC
the system to cool further and then check again as necessary When you are convinced everything is OK, remove any accumulations in small amounts Before working on or around coal firing systems, the system must be inerted or washed down 2021年8月13日 Routine realignment A rotary drum is a carefully balanced system Proper alignment of the drum ensures that despite the constant rotation, heat stresses (where applicable) and static and dynamic loads, the system and all of its components are mechanically balanced for optimal performance and minimal wearBasic (But Essential) Rotary Drum Maintenance Processing The document provides standard operating procedures for a ball mill It lists 18 steps for operating the ball mill, including connecting power, loading materials and grinding media, starting and stopping the mill, and unloading processed Ball Mill: Standard Operating Procedure PDF Mill 10 Do not bend down near the machine whilst it is running 11 Never over force the work piece against a wheel 12 On completion, turn off the machine and wait until it comes to a complete stop 13 Ensure machine is isolated and locked out during maintenance and repair HOUSEKEEPING 1 Leave the machine in a safe, clean and tidy state 2SAFETY OPERATING PROCEDURE HVAC

Free Bench Grinder SOP (Safe Operating Procedure) Template
2024年4月1日 Purpose of Document Bench grinder SOPs outline a safe operating procedure for bench grinder use SOPs can also be used as a training and induction documentThe primary goal is to protect workers from injury or illness by outlining a safe system of work and providing adequate training and instruction This form is broadly aligned with AS45001:20186 Never leave the machine running unattended 7 Do not bend down near the machine whilst it is running 8 Never force the workpiece against a wheel 9 Slowly move the workpiece across the face of the wheel uniformly Do not use the side of the grinding wheel to grind workpieces 10Safe Operating Procedures SOP 02 Bench Grinder University of Surface Grinding with Scarifiers PURPOSE Section Four: Standard Operating Procedure 4 The only way to check cutters and drum is to remove the drum from the machine Walk and Ride Scarifiers SMC Inc Training Library Page 17 of 27 GrindLazer SOPSurface Grinding with Scarifiers Safety Marking2016年2月2日 The grinding circuit operator must ensure that the ball mill runs properly loaded and gives the correct ore grind A major practical indication of mill loading is the sound made by the mill A properly loaded mill will have a deep rhythmic roar, while an under loaded mill will have a metallic rattling type noise and an overloaded mill will be quite silentGrinding Circuit Startup and Shutdown Procedure
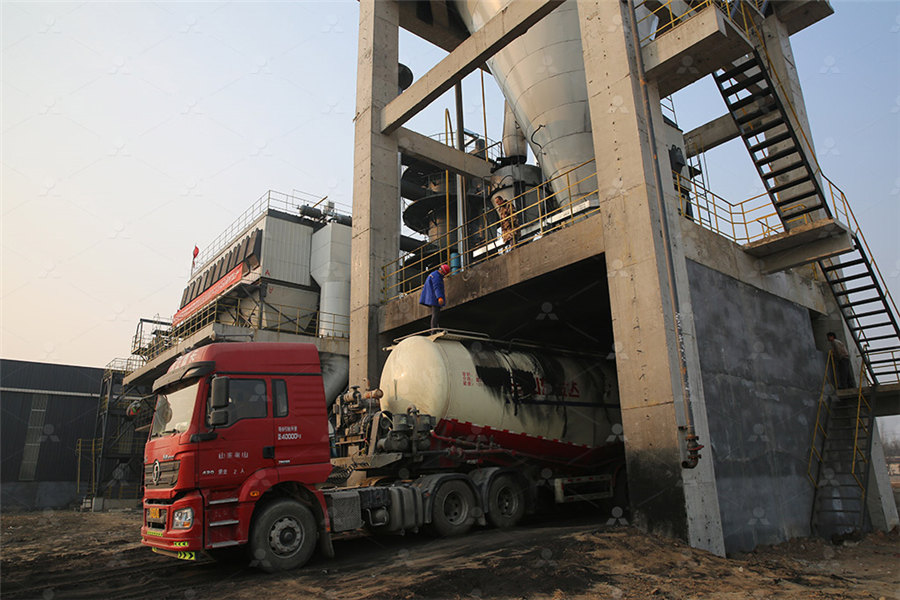
Grinding SpringerLink
2022年2月28日 Generally, grinding process efficiency can mainly be improved by either improving the grinding behavior of the material being ground or enhancing the grinding machines Recently, the use of additives socalled grinding aids, which is applied in a small amount of 001–025 wt% related to the mass of product, has reduced these problems and been 2023年8月10日 These machines will often agitate with the top open, but will not spin Some newer machines will neither agitate nor spin with the lid open (handy for creating a soak cycle, just leave the lid open) If the machine will start agitating as soon as you close the lid, the switch is not the problem (It knows the lid is closed)Washing Machine Not Spinning iFixit TroubleshootingUse extraction system or dust mask to avoid inhalation of fumes and dusts Burns from hot material or abrasion after/during grinding Safe Work Procedure Checklist: 1 This SOP does not necessarily cover all possible hazards associated with the machine and should be used in conjunction withSafe Work Procedure Grinder Angle GrinderIndustrial 205litre drums and barrels can weigh up to 350kg (772lb) when full, these weights are well in excess of the UK guidance on manual handling – the male and female upper limit is 25kg and 16kg respectively With drum weights potentially being 22 times greater than guideline manual handling limits, these containers pose a severe health and safety risk to people who Drum Handling Safety, Tips and Procedures Full Breakdown
.jpg)
Ball Mill Maintenance Installation Procedure
2016年10月20日 This can be accomplished by a centralized system for two or more mills, or by an individual system for each mill We recommend the individual system for each mill, except where six or more mills are involved, or when Portable Grinder Operating Procedures Free download as PDF File (pdf), Text File (txt) or read online for free The document outlines safety procedures for operating portable grinders It details 10 steps for proper use including Portable Grinder Operating Procedures PDFgrinding safety Safety, as related to the grinding practices, is an often neglected but critical issue when working on pressure vessels Safety issues concerned are: • Yankee dryer operational safety • Grinding process and equipment • Grinding personnel safety Grinding of Yankee dryers There is a variety of grinding techSafe Yankee grinding practices TAPPISafe Working Procedures Section 4 Page 42 Cutting and Grinding Discs NO Cutting or grinding Disc is to be used unless: • It is undamaged, dry and has been stored in accordance with the manufacturers' instructions (typically flat and away from heat) • It is designed to spin at a speed which is equal to, or exceeds, the spindle ofSAFE WORKING PROCEDURES ABRASIVE WHEELS Rokk
.jpg)
Lathe Operations Perfected: Your Expert Guide to Standard Procedures
2023年8月28日 41 Nonpersonnel are strictly prohibited from operating the machine 42 It is strictly prohibited to touch the tools or any rotating parts of the machine during operation 43 Use the emergency stop function properly After using the emergency stop button in case of an emergency, follow the machine’s startup procedures and recheck everythingaxis of the drum whilst suspended from a hook of a lifting machine Then, manually or through gearbox, upending the drum for discharging the contents or storing the drum Examples of side gripping rotating drum lifters (Click image to view more information) 3 3 Side Gripping Drum Rotating Overhead Lifter Attachments Raptor LG800 Geared drumDrum and Barrel Handling Guide DLH Online1998年4月28日 Unlike other forms of writing, standard operating procedures are written from a technical perspective This means they must be: Clear and concise—getting directly to the point and avoiding wordy sentences Standard operating procedures should be communicated in the fewest possible words, phrases, and paragraphsWriting Standard Operating Procedures Modern Machine ShopPage 35: Locking The Grinding Drum Operating the device 573 Locking the grinding drum CAUTION C100024 Risk of burns and scalding Hot grinding drum and/or sample material − The sample material and grinding drum can get very hot during grinding • Always wear protective gloves when touching the grinding drum after grindingRETSCH TM 300 MANUAL Pdf Download ManualsLib
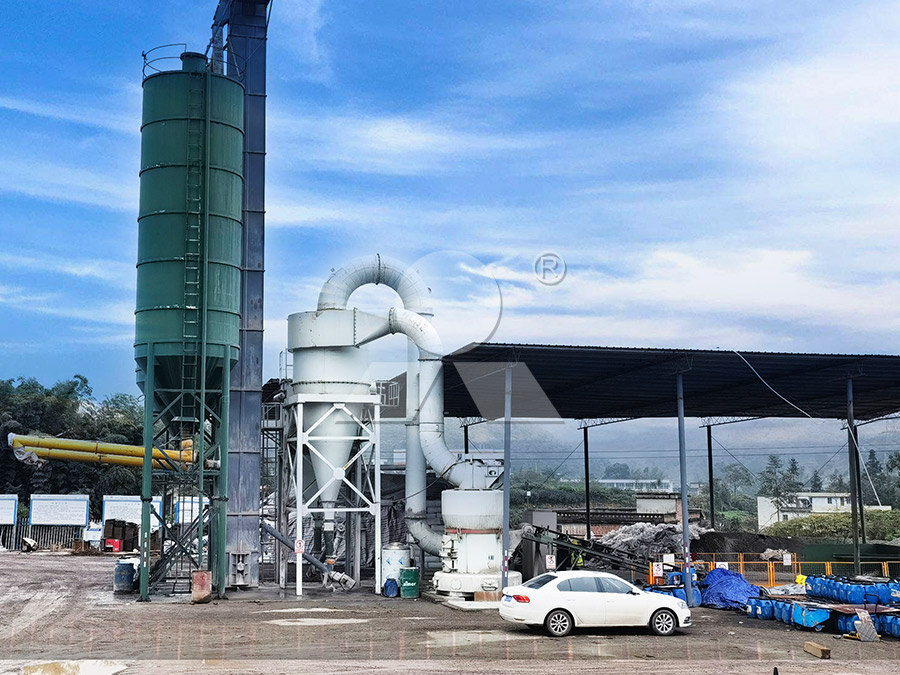
Chapter 5: Surface Grinder – Manufacturing Processes 45
• Identify Procedures • Describe Dressing the Wheel procedures • Describe the Ring Test • Describe replacing the Grinding Wheel • Describe procedure select the grinding wheel • List principal abrasives with their general areas of best use • List principal bond with the types of application where they are most usedUse extraction system or dust mask to avoid inhalation of fumes and dusts Burns from hot material or abrasion after/during grinding Safe Work Procedure Checklist: 1 PREOperation: Always begin by settingup your work area safely to avoid the following:Safe Work Procedure Sander Disc and Belt Sander