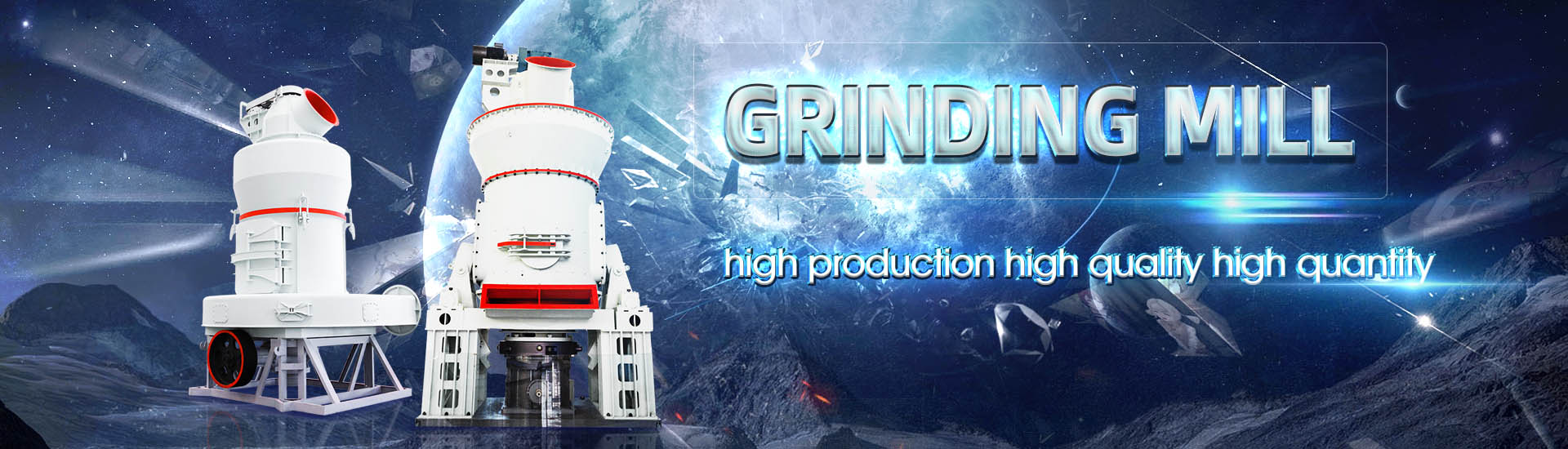
What are the grinding machines for processing calcite minerals
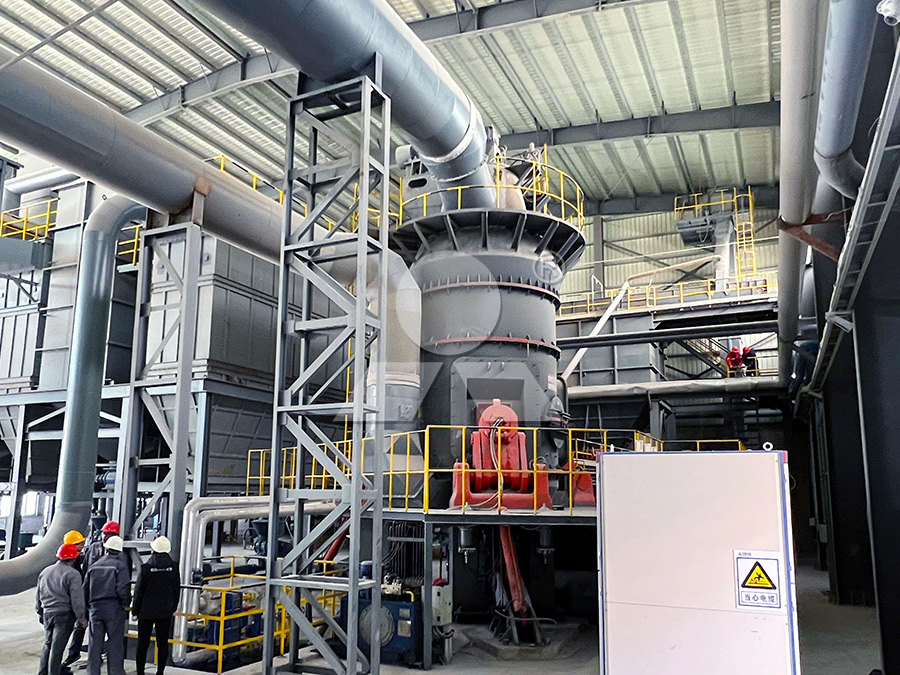
3 Incredible Flows to Win Calcite Processing (Without Failing)
There are three main technologies in calcite processing: crushing, sand making, and milling, and crushing is the primary stage Calcite has a Mohs hardness of 3 It is easily broken, often breaking into small square pieces along its cleavage 展开2020年12月22日 So the equipment configuration for calcite grinding includes: ⑴ C6X Jaw Crusher C6X Jaw Crusher has the characteristics of large feed range, high operating strength, and strong durability, which is suitable for processingWhat kind of grinding mill can be used for process 2024年10月14日 Remark: For conversion from millimeter to mesh, please refer to mm to mesh Process 3: Calcinating dolomite rock The crushed dolomite is calcined in a rotary kiln, which is used for producing refractory materials, How to Process Dolomite Rock and What Is It Used 2023年4月26日 Calcite grinding process Calcite belongs to the type of ore that is easy to grind Calcite grinding powder generally requires the fineness of the finished product to be small 1 Process flow of calcite grinding Grinding: The 3 Incredible Flows to Win Calcite Processing (Without
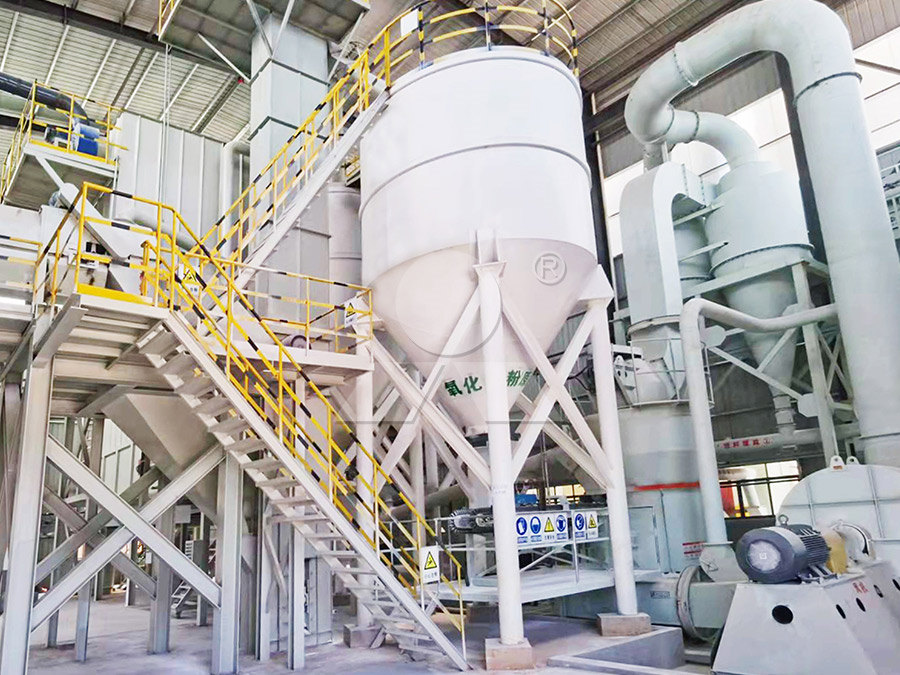
SIZE REDUCTION BY GRINDING METHODS
2017年3月4日 In the field of extractive metallurgy, mineral processing is the process of separating commercially valuable minerals from their ores Mineral processing involves two major categories of processing2023年4月21日 Calcite ball mills have several uses in the building materials, chemicals, and mineral processing industries, as well as for grinding a wide range of ores and other materials In addition, according to the different loads used in the mine, there are two types of ball mills: screen type and overflow typeCalcite Processing SBM Mill Crusher2021年7月7日 YGM Raymond Mill is mainly suitable for grinding and processing mineral materials such as metallurgy, building materials, chemicals, mining, etc It can grind quartz, feldspar, calcite, talc, barite, fluorite, etc materials that Mohs hardness is below 93 Processing of various nonflammable and explosive mineral materials with humidity below 6%What are the types of industrial grinding mills?Grinding mills or pulverizers are employed for this purpose Classification and Separation: The powdered calcite is classified by particle size using air classifiers or sieving machines Further processes such as flotation may be used to enhance the purity and separate calcite from other minerals and impurities Chemical Processing (if needed):How calcite is mined and processed
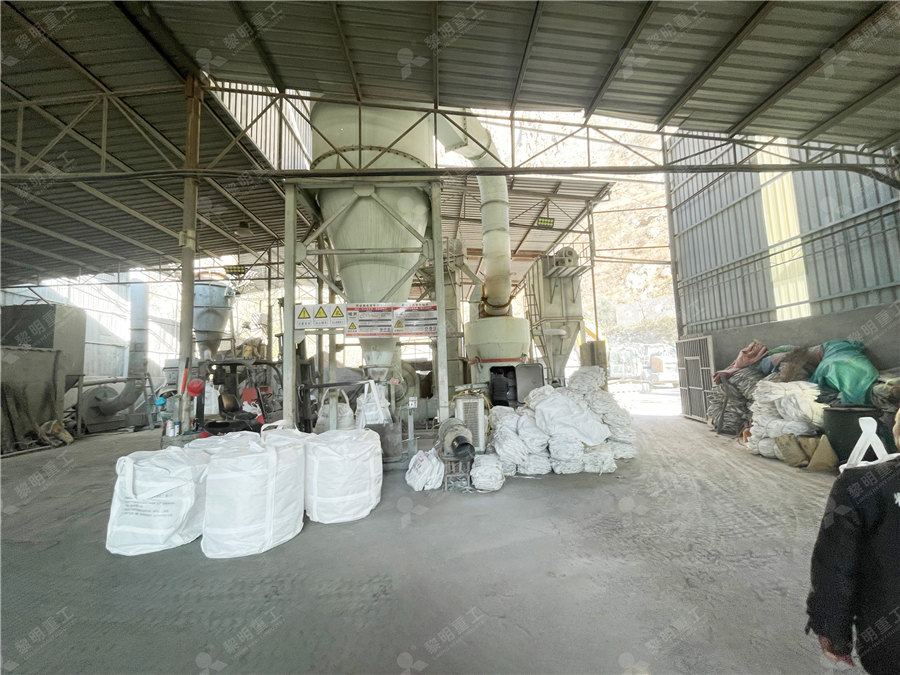
Calcite Mastery: From Hardness to Powder Processing Techniques
Calcite is a widely found mineral composed of calcium carbonate, Calcite processing mainly includes three steps: crushing, Shanghai CLIRIK Machinery Co,Ltd has dedicated itself to the ultrafine powder grinding machine industry for two decades Welcome to visit our factory in In the modern industrial landscape, the demand for ultrafine powders of minerals such as heavy calcium carbonate (CaCO3) and calcite is rapidly increasing These minerals are widely used in various industries, including paper, paint, plastThe ultrafine grinding mill for processing heavy calcium 2024年8月7日 Mineral processing involves key stages to extract valuable minerals from ores, including crushing to reduce ore size for further processing, grinding to further refine particle size and liberate minerals, classification to separate particles by size and density, and separation to isolate valuable minerals from waste materialsMineral Processing Equipment for Mining Industry2013年12月18日 Fine grinding, to P80 sizes as low as 7 μm, is becoming increasingly important as mines treat ores with smaller liberation sizes This grinding is typically done using stirred mills such as the Isamill or Stirred Media Detritor While fine grinding consumes less energy than primary grinding, it can still account for a substantial part of a mill’s energy budget Overall Energy Use of Fine Grinding in Mineral Processing
.jpg)
Mineral Processing Plants: What You Need to Know
2024年8月15日 Understanding the four stages of mineral processing Mineral processing, also known as ore dressing or mineral beneficiation, typically consists of four key unit operations: comminution, sizing, concentration, and 2023年4月23日 It consumes most of the energy used in mineral processing plants with grinding using up to 50% of the provided energy Tumbling mills are an old technology that is still commonly used for grinding(PDF) Grinding Media in Ball MillsA ReviewIndustries Requiring Mineral Processing Equipment Various industries require machinery to process minerals for a plethora of applications Regardless of the type of business, all mineral processing equipment essentially works towards Which Machines Should You Use for Mineral 2023年8月8日 One mineral floats up in the medium and the other sinks to separate phosphorus minerals Applicable types: Carbonate phosphate rock Process 5: Magnetic separation Principle: According to the different magnetism of minerals, ferromagnetic minerals are separated from nonmagnetic minerals under the action of the magnetic fieldPhosphate Rock Processing: 6 Useful Ways and 4 Stages
.jpg)
Exceptional Barite Processing Methods and Machines
2023年3月20日 To fully dissociate useful barite minerals, ball mills are commonly used to grind barite rocks Generally, the grinding fineness of barite200 is 85~90%, and a twostage grinding process is often used In view of the differences in the properties of barite ores, the optimum grinding fineness needs to be determined experimentallyCalcite is rich in resources globally, and the highquality calcite resources with calcium carbonate content ≥97% are also large Therefore, at present, only performs simple washing and hand selection at the beginning of classification The processing flow for products below 400 mesh is like: raw orecrushinggrindingclassifyingcalcite grinding machine, calcite grinding mill, calcite processing plantmineral processing, art of treating crude ores and mineral products in order to separate the valuable minerals from the waste rock, or gangue It is the first process that most ores undergo after mining in order to provide a more concentrated material for the procedures of extractive metallurgyThe primary operations are comminution and concentration, but there are other Mineral processing Metallurgy, Crushing Grinding Britannica2024年5月23日 Millennia ago, many pyramids in Egypt and Latin America were constructed using calcite minerals like limestone as fundamental building materials With the United Nations predicting that 68% of the world's population will reside in urban areas by 2050, there is a growing demand for infrastructure services in housing, transportation, energy, and more, to Calcite: A Key Ingredient in Efficient Cement Manufacturing
.jpg)
Copper Mining and Processing: Processing Copper Ores
Copper processing is a complicated process that begins with mining of the ore (less than 1% copper) and ends with sheets of 9999% pure copper called cathodes, which will ultimately be made into products for everyday useThe most common types of ore, copper oxide and copper sulfide, undergo two different processes, hydrometallurgy and pyrometallurgy, respectively, calcite milling equipment image, micronizer jet mill and coal grinding mill process for power plant of cost products raymond mill vertical roller mill ball mill cement clinker grinding plant coke grinder equipment crushing Micronizer Grinding Machines For Minerals Crusher MillsAs the minerals industry is required to process increasingly complex, finelygrained ores, stirred mills are replacing ball mills for regrind applications in flotation circuits Stirred mills are able to produce fine grind sizes in an energy efficient manner and without additional size classification Laboratory grinding trials were conducted using two highspeed stirred mills; one vertical and Ultrafine grinding for improved mineral liberation in flotation 5 Ball mills are used for wet grinding iron ore, gold/copper ore, nickel ore and other ores, as well as lime/limestone for flue gas desulphurisation systems, coal and other raw materialsSIZE REDUCTION BY GRINDING METHODS By ResearchGate
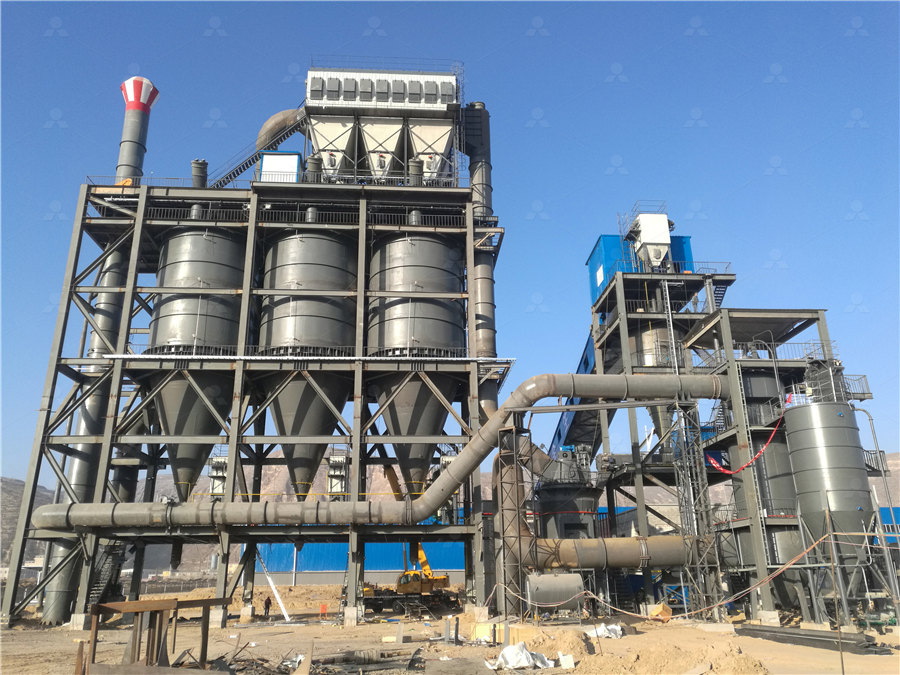
Calcite Processing Equipment, Process Flow, Cases
Calcite is the mineral component of limestone which is used primarily as construction aggregates, and in production of lime and cement Limestone also is used in a variety of commercial applications including: road construction, 2023年8月25日 3 Mineral Deposits: Calcite can be associated with various types of mineral deposits In hydrothermal veins, where hot fluids circulate through fractures in rocks, calcite can precipitate along with other minerals Calcite can also be present in ore deposits, especially those related to metallic ores like lead, zinc, and copperCalcite : Properties, Formation, Occurrence and Uses Areas2020年9月7日 The progress of processing powder size is called grinding The final powder size can reach from 05 mm to 0005 mm There are also several grinding mill machine: Raymond mill, High pressure grinding mill, and Micro powder grinding mill etc However, in most case, a small crusher is needed in the grinding mill machineWhat is the difference between crushing and grinding?2023年2月15日 4 Grinding: Next, talc ore is sent to a Raymond mill and superfine mill for fine grinding and ultrafine grinding to obtain the final talcum powders 5 Classifying: Finally, the talcum powders are classified by a spiral classifier Qualified talc powders are packaged as the final product, while the others return the milling machine for regrindingHow to Process Talc (the Softest Mineral)? FTM Machinery
.jpg)
The effects on the grinding parameters of chemical, morphological
2022年1月1日 1 Introduction Calcite, in other words, calcium carbonate (CaCO 3), is a glassy shimmer, transparent, easily breakable, large crystal marble mineralIts Mohs hardness is 3 and specific gravity is in the range of 26–28 It is micronized by grinding then classification processes are applied, and offered to the user as natural ground or ground and coated calcite according Solid minerals can either be native elements like gold, silver, etc, or compounds like calcium carbonate (calcite), calcium silicate (wollastonite), aluminum silicate hydrate (kaolinite), etc The last group of solid minerals in the form of simple or complex compounds is of particular relevance for cement manufactureBasics of mineral resources for cement production2016年4月12日 Flotation reagents are added to the conditioner and the “SubA” Flotation Machine, keeping them out of the grinding and desliming sections Flotation density will vary between 20 and 30% solids, depending upon the degree of grinding required to liberate the impurities and to meet the kiln feed specifications FLOTATION OF CALCITECalcite Processing by Flotation for BeneficiationA dedicated grinding mill production line for calcite processing is a sophisticated solution that caters to the specific needs of the mineral processing industry With its ability to produce highquality calcite powder efficiently and sustainably, such a production line is a valuable investment for businesses involved in the calcite supply chainThe grinding mill production line for calcite processing
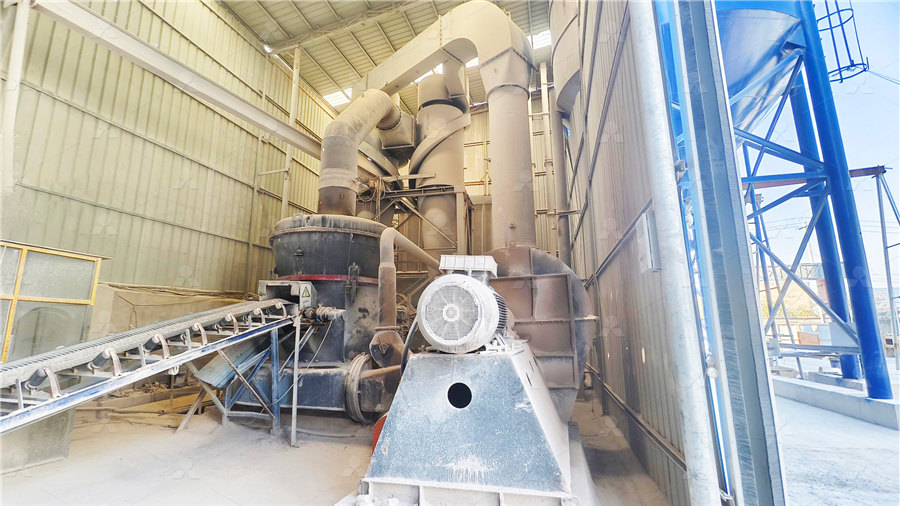
Raymond Mill TAYMACHINERY
The Raymond mill is a versatile and reliable grinding machine, suitable for producing fine powders for a wide range of industrial applications Its efficiency, ease of maintenance, and ability to handle various materials make it a Calcite with the 3 mohs hardness belongs to the easy grinding mineral To make full use of the calcite, grinding and further processing are necessary Processed calcite serves in varying industries calcite grinding machine is generally Calcite Grinding Mill/ Calcite Crusher/ Calcite 2017年5月30日 Coarseore dry sampling of the type found in primary and secondary crushing systems prior to processing, often requires sampling large flow rates containing 911 Metallurgist is a trusted resource for practical insights, solutions, and support in mineral processing engineering, helping industry professionals succeed with proven expertise Mineral Processing Plant Mineral Processing Plant Sample Equipment 911MetallurgistThe Raymond mill is a versatile and reliable grinding machine, suitable for producing fine powders for a wide range of industrial applications Its efficiency, ease of maintenance, and ability to handle various materials make it a valuable asset in many industries [Introduction]: Raymond Mill has a strong performance of becoming a complete set with a production system Raymond Mill TAYMACHINERY
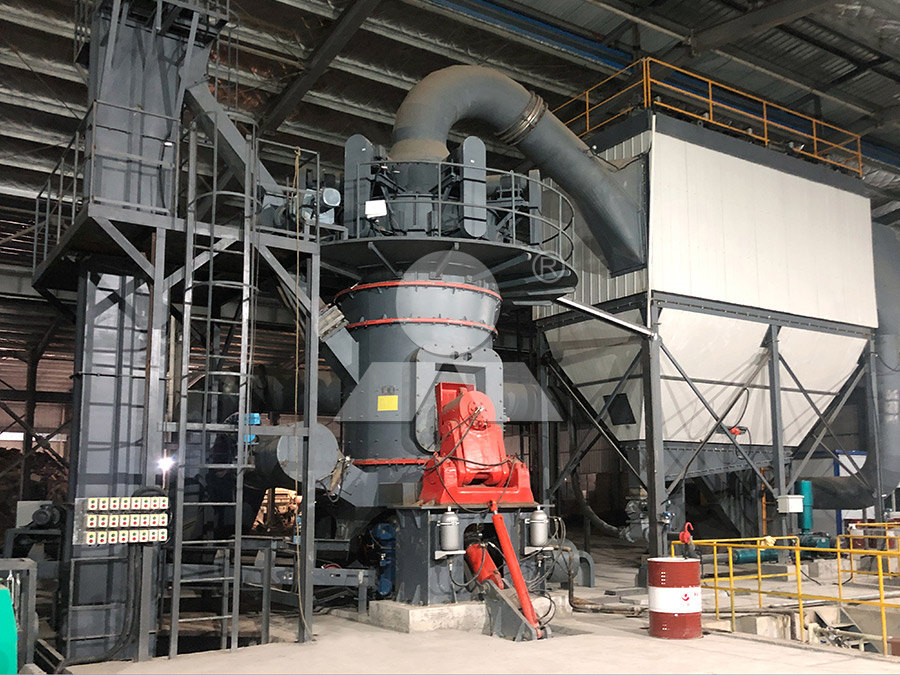
Calcite Processing: 3 Incredible Technologies You Should Try
2022年7月6日 Grinding: The crushed calcite (≤30mm) is lifted to the silo by the elevator and sent to the grinding chamber of the mill for grinding Under the action of the grinding roller and ring, the 2016年1月17日 In mineral processing, the reduction of minerals by crushing and grinding may be regarded as having one or other of two main objectives: the attainment of a size appropriate for the direct industrial application of the mineral, eg barytes, sand, aggregate; or the release of metallic or ore inclusions from an unwanted matrix with a view to maximum separationCrushing Mineral Processing 911Metallurgist2016年11月10日 Reverting now to the study of the grinding tests by use of the dimensionless equation (52), it is found that Gross has, given figures for the values of “Rittinger’s Constant” for galena, sphalerite, pyrite and calcite, as determined by use of a laboratory ball mill, run under specified conditions, and also figures for the Rittinger’s constant as determined by the use of a Grinding Process 911Metallurgist2021年12月20日 The way in which minerals separate when processed is referred to as cleavage, and calcite’s cleavage is rated as perfect in three directions The term “calcite” refers to the crystalline structures that make up calcium carbonate Manufacturing processes break these crystals along three planes, resulting in blocklike fragmentsCalcium Carbonate Manufacturing Process and Equipment
.jpg)
Essential Guide to Mineral Processing Equipment Flyability
Mineral processing is a form of extractive metallurgy that separates valuable minerals from the ore into a concentrated, marketable product Mineral processing is also known as mineral dressing Mineral processing is conducted at the site of the mine and is a highly mechanical process, with oversight from a central control roomMineral processing, also known as ore dressing, involves the separation of valuable minerals from waste material through methods like crushing, grinding, and flotation This essential process increases the metal concentration for more efficient extraction and refining in industries such as mining and metallurgyMineral Processing: Technology Basics Vaia