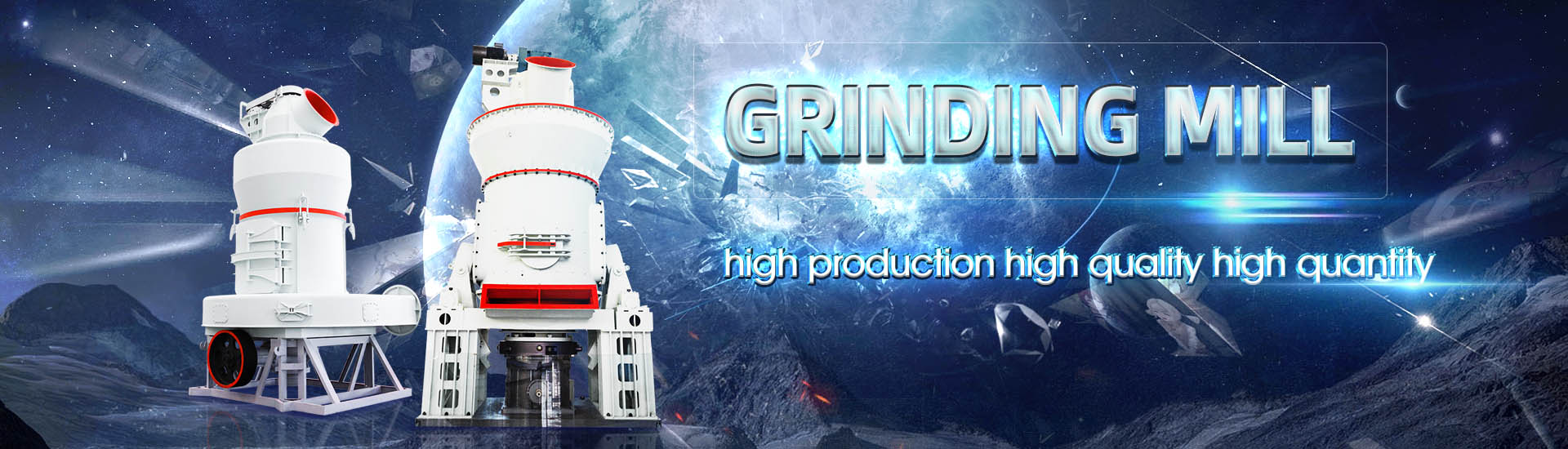
Reasons for coal blocking in the hopper of coal mill entrance
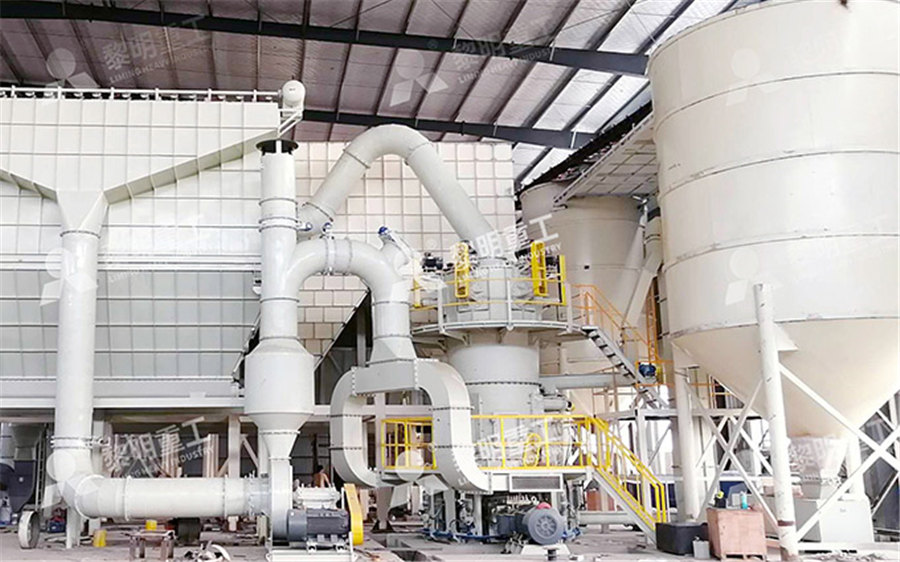
Prevent Material Blockages Martin Eng
This causes buildup in chutes and hoppers, contributing to bridging and ratholing, reducing or stopping material flow In addition to the reduction in profitability, material obstructions can pose a safety risk for workers when they attempt to The experimental results show that it can effectively detect the coal blocking and coal breaking faults of the coal feeder and the coal mill, effectively reduce the system false alarm rate, Research and Application of Coal Blockage Early Warning 2020年9月25日 Coal blockage is one of the main reasons for coal mill malfunction It is highly essential to accurately detect the critical blockage in coal mills to ensure a safe and stable Early Warning of Critical Blockage in Coal Mills Based on Stacked The experimental results show that it can effectively detect the coal blocking and coal breaking faults of the coal feeder and the coal mill, effectively reduce the system false alarmResearch and Application of Coal Blockage Early Warning
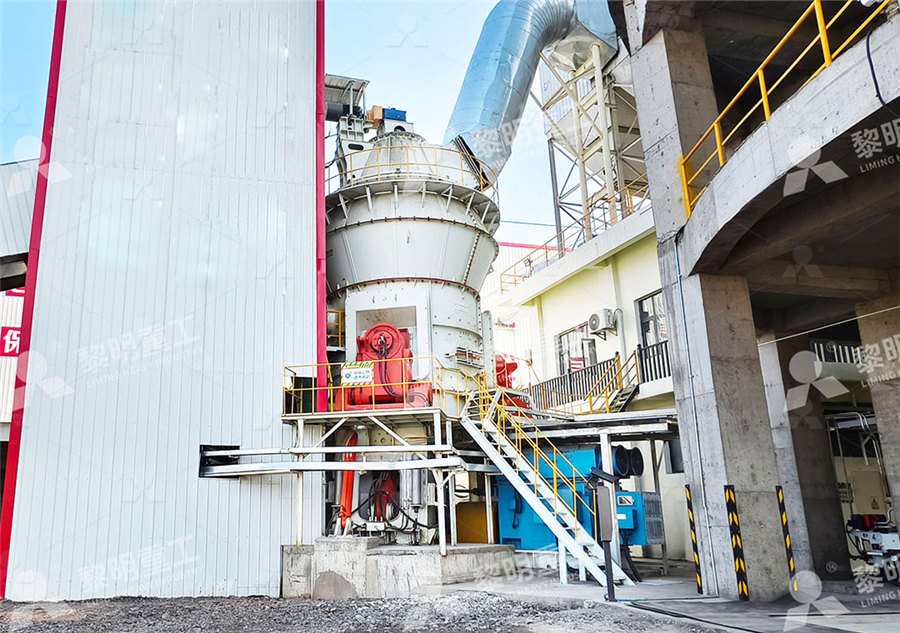
Experimental study on coal blockage removal based on pulverized
2022年10月1日 They found that coal powder aggregation and adhesion and pore throats' bridging and blocking are the main reasons for the channeling capacity injury of the proppant This paper aims to find a useful technology to prevent the coal antiblocking [Method] The paper studied the coal blocking reasons and same antiblocking technologies, such as hyperbolic Research on the Prevention of Coal Blocking in Power Plant Raw 2015年11月1日 Coal mills are bottleneck in coal–fired power generation process due to difficulty in developing efficient controls and faults occurring inside the mills In this paper, a dynamic A unified thermomechanical model for coal mill operation2020年7月11日 This paper aims to find a useful technology to prevent the coal antiblocking [Method] The paper studied the coal blocking reasons and same anti Research on the Prevention of Coal Blocking in Power Plant Raw
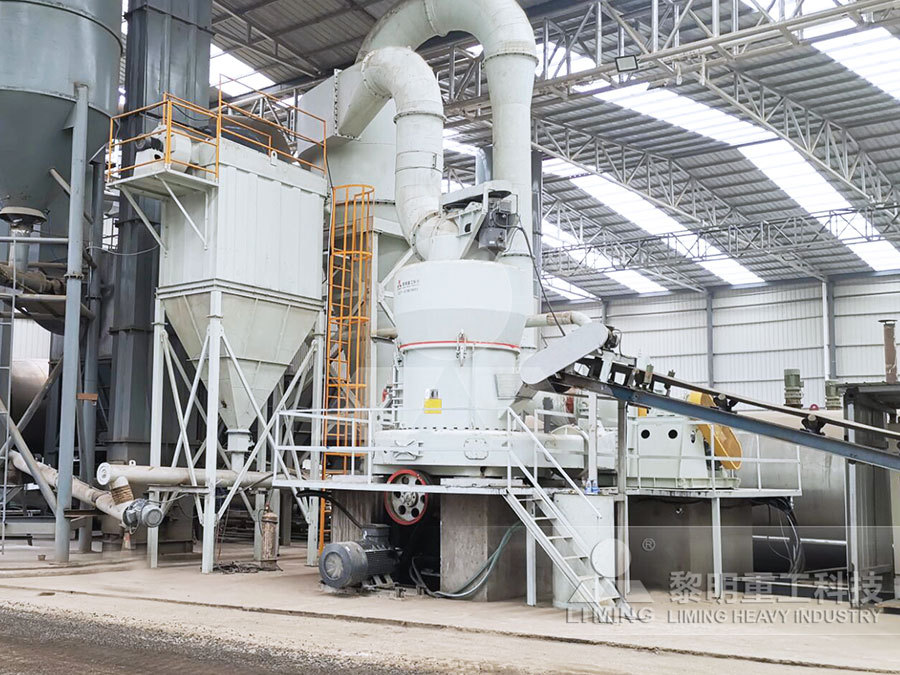
Research on Initial Prevention of Spontaneous Combustion in Coal
2022年2月1日 The reason may be that the flow field in the hightemperature area of the coal bunker gradually increased and took away more heat after CO 2 injection for a period of time, 2020年1月1日 Coal blockage is one of the main reasons for coal mill malfunction It is highly essential to accurately detect the critical blockage in coal mills to ensure a safe and stable operation of the unitEarly Warning of Critical Blockage in Coal Mills Coal blockage is one of the main reasons for coal mill malfunction It is highly essential to accurately detect the critical blockage in coal mills to ensure a safe and stable operation of theEarly Warning of Critical Blockage in Coal Mills Based on Stacked 2020年7月11日 Key words: coal blocking /; rotary blockage clearing machine /; coal bunker /; coal dropping pipe /; hyperbolic coal hopper; Abstract: [Introduction] Coal blocking of pulverizing system is a big problem in power plant, especially for coal bunker At present, there are many types of antiblocking coal technologies on the market, but there are different opinions on the Research on the Prevention of Coal Blocking in Power Plant Raw Coal
.jpg)
Reasons and Prevention of the Bag Dust Collector Catching Fire
2021年6月22日 The main design parameters and equipment selection for the above reasons are unreasonable We talked about this problem in the early stage In many systems, the original coal bunkers and coal feeders have been modified to prevent coal blocking and material suspension The consequences of coal blocking and material suspension are too serious 4Coal blockage is one of the main reasons for coal mill malfunction It is highly essential to accurately detect the critical blockage in coal mills to ensure a safe and stable operation of the unitThe monitoring indicator of coal mill under normal condition2009年9月20日 A control oriented model was then developed by Fan (1994) and Fan and Rees (1994) In 2009, coal flow and outlet temperature of mill were modelled using mass and heat balance equations for startup Modeling and Parameter Identification of Coal MillA simple energy balance model of the coal mill is derived in (Odgaard and Mataji 2006), this model is based on a more detailed model found in (Rees and Fan 2003)In this model the coal mill is seen as one body with the mass m mThe following variables are defined: T(t) is the temperature in the coal dust flow in the mill, ṁ PA (t) is the primary air mass flow, T PA (t) is Coal Mill an overview ScienceDirect Topics
.jpg)
Mill Training Manual Alstom PDF Coal Mill (Grinding)
Mill Training Manual Alstom Free download as PDF File (pdf), Text File (txt) or read online for freecoal quality is poor, causing units 1 and 2 to frequently block coal, causing the unit to derating and requiring more time and energy for cleaning coal The number of SR (FLM Blocking Coal) that has been carried out by the Operator is as follows : 1) 5) 9) 2) 6) 10) ANALYSIS OF CONTROL SYSTEM MODIFICATIONS ON COAL The reasons for this concentration on one type of firing system were that it was safe, and cheaper than either of the alternatives shown in Figure 9, both of which involved storage of the ground product in a hopper These示tems either use the mill sweeping gas to take the coal from the hopper (semiindirect firing), or take the dedusted mill COAL PREPARATION AND FIRING INFINITY FOR CEMENT EQUIPMENT2012年11月17日 20 131Fineness Fineness is an indicator of the quality of the pulverizer action Specifically, fineness is a measurement of the percentage of a coal sample that passes through a set of test sieves usually designated at 50, Coal mill pulverizer in thermal power plants PPT
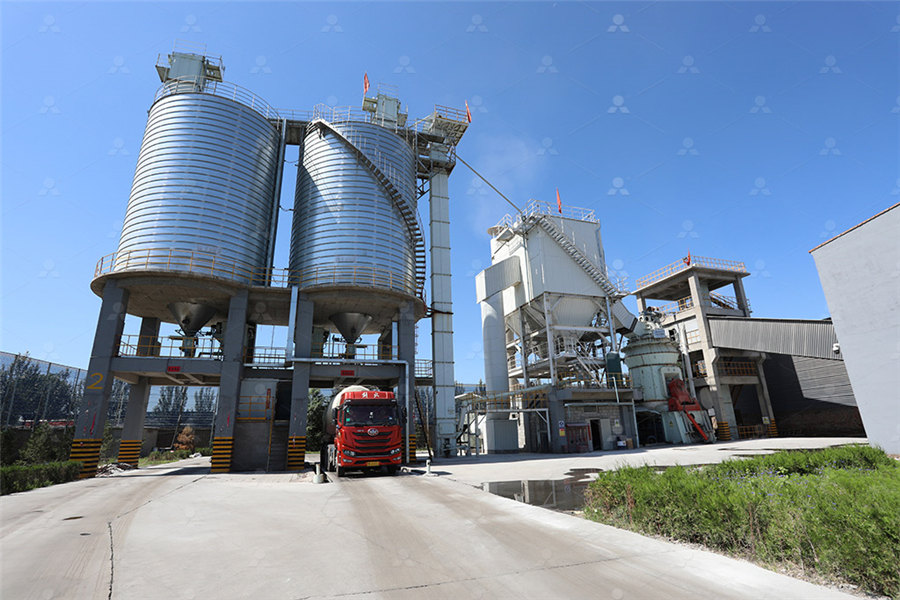
IMPROVING THE UNLOADING OF QUEENSLAND COAL
2002年1月1日 Coals from some Queensland mines give varying degrees of problems with hangup in rail wagons during unloading at the ports Jackhammers are currently used at the ports to vibrate the wagons and It is kept at low temperature, limited to about 373 K, for reasons of safety against ignition and explosion in the mill and in the powdered coal transport pipeline between the mill and the burners The rest of the combustion air, which can be preheated to higher temperatures, is injected separately and admixed with the already ignited coal particleladen jet in the combustion Pulverised Coal Combustion an overview ScienceDirect Topics2020年9月25日 Coal mills have a significant influence on the reliability, efficiency, and safe operation of a coalfired power plant Coal blockage is one of the main reasons for coal mill malfunction It is highly essential to accurately detect the critical blockage in coal mills to ensure a safe and stable operation of the unit Taking advantage of unsupervised learning methods and Early Warning of Critical Blockage in Coal Mills Based on Stacked Mill Rejects from coal mill will drop into the Pyrite Hopper through the grid Oversize material will be retained on the grid A pneumatic cylinder operated Plate Valve on oversize material discharge chute will be provided, which will be operated automatically MRHS Mill Reject Handling System in Thermal Power Plant
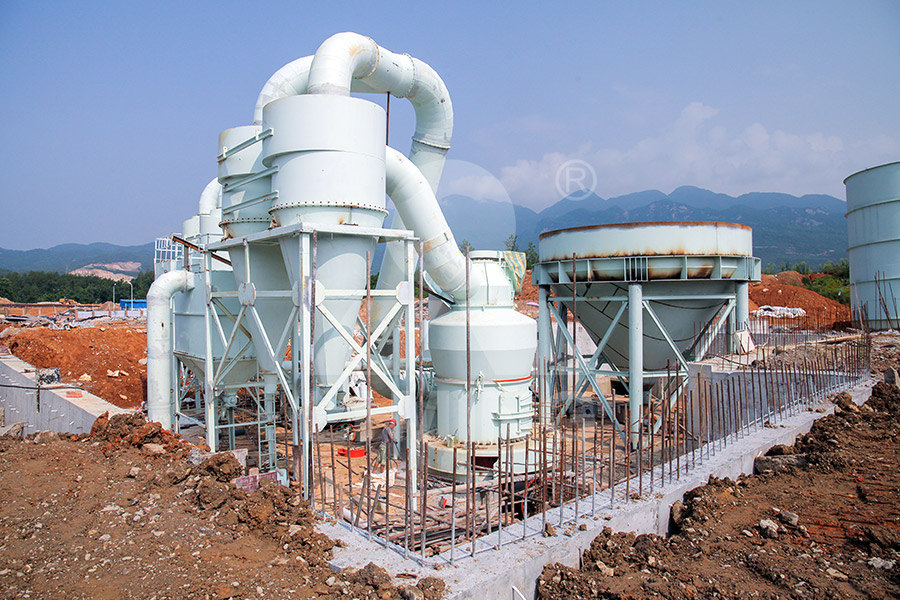
Coal Pulverization System: Explosion Prevention and Process
designing and operation of the coal process system 1 Hazard analysis of the process The process is shown as Figure 1 Raw coal is conveyed from the storehouse by a belt conveyer Then it is lifted to the entrance level of a vertical cylindrical mill by a bucket elevator, and an electromagnet is used to remove iron objects from the raw coalopened depends on the size of the hopper that is the time taken to unload the coal from the hopper is given to TP block and thus the coal will be transferred Here it is roughly taken as 10 seconds As long as the hopper gate is opened the jaw crusher will be running and the crushed coal will be transferred to bunker by conveyor 2Automated Coal Crushing and Conveyor System Using PLC and There are two types of impact: gravity impact and dynamic impact Coal dropped onto a hard surface such as a steel plate is an example of gravity impact Gravity impact is most often used to separate two materials which are having relatively different friability For example, inConstruction, Working and Maintenance of Crushers for Crushing Circa 1953, for the movement of coal from Mine to destinations that used large amounts of it, such as Coke Plants (either as independent operations or as part of an Integrated Steel Mill) I have a few questions 1) When hoppers were empty, where would they be routed too? Not the few hopper cars that would be in a local being delivered to coal dealers for example I'm asking Need further help understanding Coal Hopper Car Movements
.jpg)
In discussion: Coal Mill Safety Coal Mill Safety, Explosion and
In discussion: Coal Mill Safety At best, coal mill safety is not well understood and, at worst, it is ignored When it comes to coal mill systems, most cement plant operators just presume that the supplier of the equipment knows all of the standards and rules and is 100% capable of making a system that conforms to these and is therefore safeThis document discusses coal pulverization in power plants It covers various topics related to coal pulverizers including: Types of coal and reasons for pulverizing coal like improved efficiency and combustion control Two types Coal Mills in Thermal Power Plant PDF Mill 2020年6月29日 6 TYPES OF COAL PULVERIZER • Tube or ball mills: Lowspeed machines that grind the coal with steel balls in a rotating horizontal cylinder If the diameter of the cylinder is greater than the length of the classifications and working of mills in a power plantWhile renewable energy has undergone wide and rapid deployment, coal is still expected to be the main source of fuel for producing base load power in the near future This is because coal reserves are expected to last for the next century and its cost is still relatively cheap However, the emissions from coal combustion are a major environmental concernEffects of Mill Performance on Unburnt Carbon in Coalfired Boilers
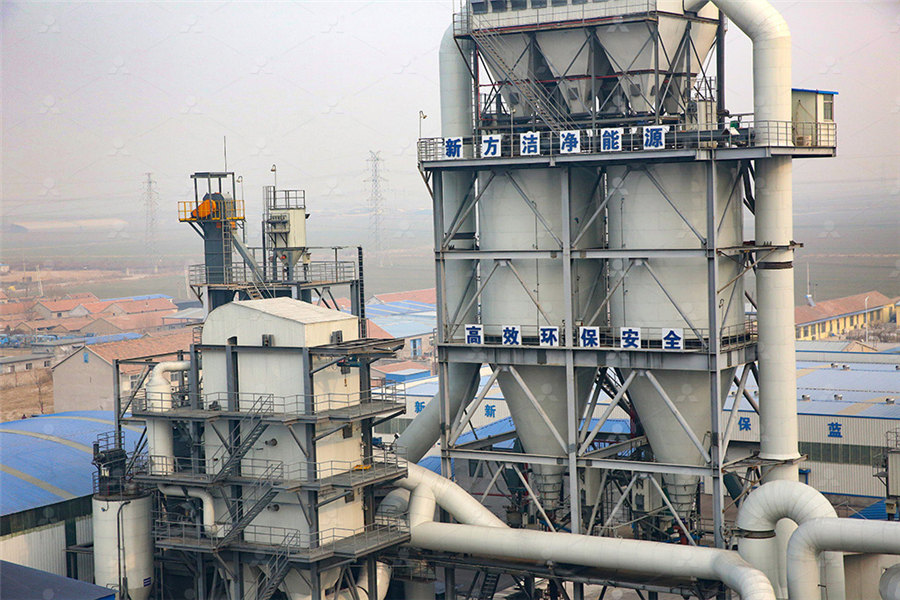
The Inferential predictive control method of coal mill IEEE
2016年1月18日 Next, the paper estimates the coal outlet mass flow of the coal mill by using extended Kalman filter (EKF), and the result is compared with the coal flow instruction Finally, we take the estimation of coal outlet mass flow as the new controlled variable and use inferential predictive control method to solve the coal mill control problems2021年3月31日 24 mill performance monitoring using non iso kinetic technique • dirty pitot testing to be carried out before and after mill overhaul • non iso kinetic sampling to be used for routine checking of fineness • pf fineness data to be trended mill wise • sample to be collected from each pipe in case of major degradationEffect of Coal Quality and Performance of Coal pulverisers / MillsFuel preparation for a pc boiler occurs in a mill, where coal is typically reduced to 70% through a 200mesh (74μm) screen Figure 2 shows a particlesize distribution from a bowlmill grinder typically used in power plants A typical utility specification for particle size distribution of the coal is that 70% of the mass should pass through a 200mesh screen, which is equivalent to 70% Pulverized Coal Boiler an overview ScienceDirect TopicsPulverizer throats that are too wide will have a correspondingly low vertical velocity jet, which contributes to coal rejects and fires Objectionable quantities of coal rejects are shown to the left Only Trace amounts of Coal should be discharged from the pulverizer No raw coal should be discharged through the tramp metal or “pyrite” chuteRaw Coal Spillage Or “Pyriting”
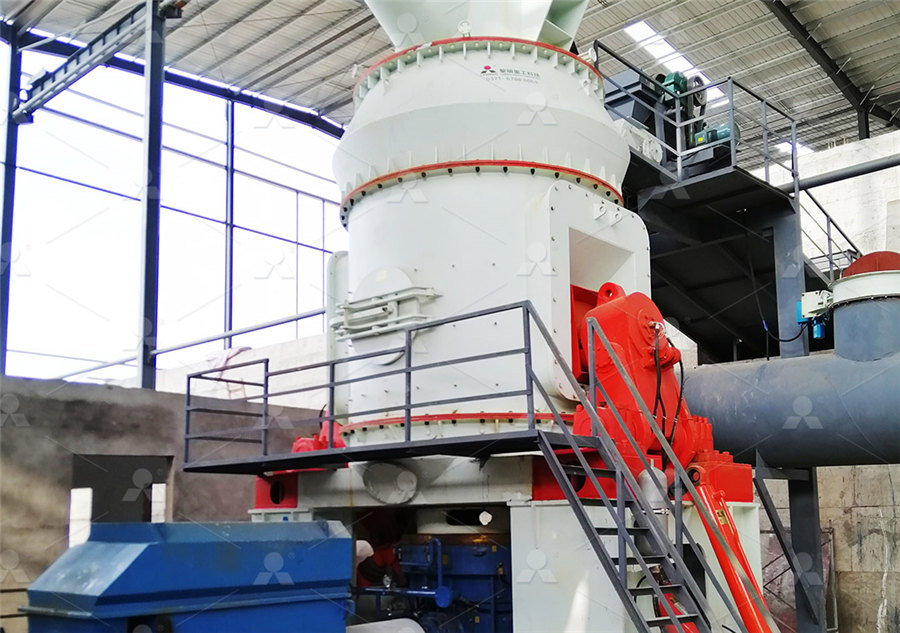
CFD Modeling of MPS Coal Mill for Improved Performance and Safety
2009年1月1日 This book details advances in the production of steam and the utilization of all types of fuels Section 1 covers Steam Fundamentals including thermodynamics, fluid mechanics, heat transfer Coal Mill PPT Free download as Powerpoint Presentation (ppt / pptx), PDF File (pdf), Text File (txt) or view presentation slides online The document provides an overview of coal mill operation, protections, and interlocks It discusses coal combustion theory, coal properties, coal mill components and operation, and troubleshooting The coal mill grinds coal into fine particles for Coal Mill PDF Combustion ChemistryFrom the coal yard, the coal is transfer to the mill bunkers through conveyor belt The bunkers are sized for an effective capacity of twelve (12) hours at BMCR with design coal Each mill bunker has one hopper, connected to the feeders Mills operate when the bunker coal gate valves are opened, coal is allowed to flow to the gravimetric feedersAnalysis of the Coal Milling Operations to the Boiler Parameters2023年3月16日 Closed coal bunkers emerged as a novel form of coal storage for coalfired power stations Nevertheless, heat builds continually in the storage process because of the constant oxidation of coal Research on the Combustion Characteristics of Coal
.jpg)
Operational parameters affecting the vertical roller mill
2016年9月1日 Cement production is one of the most energyintensive manufacturing industries, and the milling circuit of cement plants consumes around 4% of a year's global electrical energy production2020年5月13日 The dry coal is then transferred to the pulverising mill to pulverise the coal The primary air is supplied to the mill to carry the pulverised coal to the burner where the secondary air is mixed to have complete Coal Handling Plant Layout Thermal Power 2012年12月7日 1 COAL HANDLING PLANT OBJECTIVE: Coal Handling Plant is a plant which handles the coal from its receipt from Coal mines to transporting it to Boiler and store in Bunkers It also processes the raw coal to make it suitable for Boiler operation A typical coal handling plant in any power plant shall have the following processes in sequence depending on the capacity Chp in presentation PPT SlideShareVertical Coal Mill (VCM) is equipment for grinding and pulverizing coal into micron size Rotary kilns then use the powders as fuel burners The VCM has a housing section equipped with a lining The layout of the coal mill with a rotary classifier
.jpg)
Research and Application of Coal Blockage Early Warning
Abstract: This paper introduces the mechanismbased fault diagnosis model of the main equipment of the milling system, and adopts the trend state detection and failure mode recognition methods according to the detection data for comprehensive diagnosis The experimental results show that it can effectively detect the coal blocking and coal breaking faults of the coal feeder 2020年11月25日 Dried coal of BRXL lignite emits a smaller amt of NOx than that of BRXL lignite However, the dried degree of BRXL lignite is closely related to R90 fineness Dried coal with optimal moisture content yields least NOx emissions When deep or middle staged combustion was adopted, the application of multistaged combustion is conducive to NOx rednA Control Strategy of the Air Flow Rate of CoalFired Utility Boilers 2020年4月2日 Milling system in coal power plant purposely to process the raw coal to become as pulverise fuel before enter to the boiler furnace Pulverise fuel enter to the boiler furnace through pulverise Analysis of the Coal Milling Operations to the Boiler Parameters2021年11月4日 Test methods for grindability and abrasion testing: Full scale ring and ball mill, Hardgrove mill [30,31], BCURAroll mill, Rotating electrode ball wear tester [32], Dropweight test machine [28 Technique to Investigate Pulverizing and Abrasive Performance of Coals
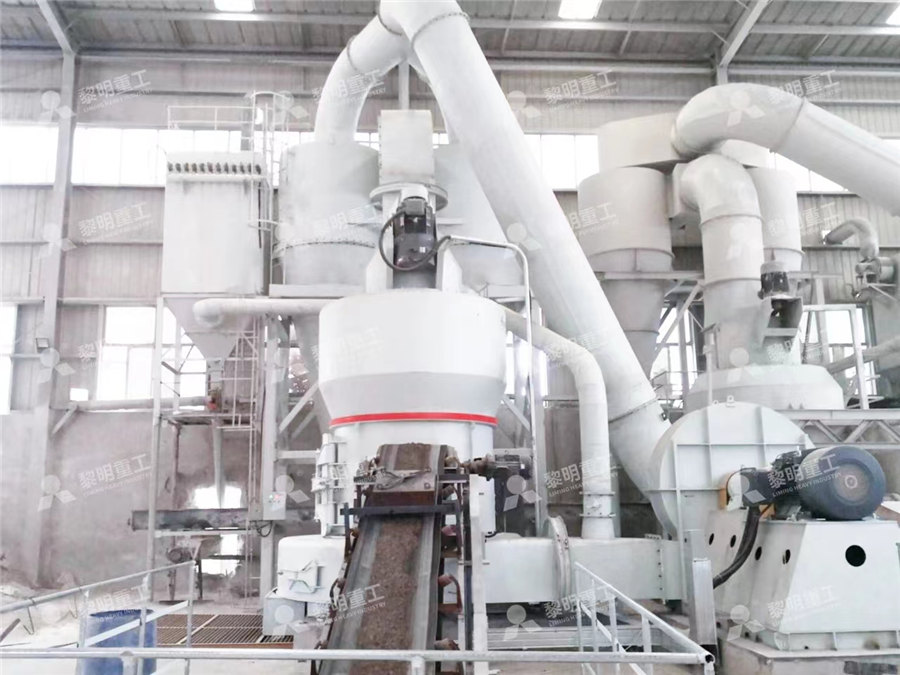
The Origin and Classification of Coal SpringerLink
2019年4月18日 Such coals are softer, friable materials Coals from the Mesozoic are found largely in the USA, CIS, Footnote 1 China, South America, and other countries in the Far East (Thomas 2002) They are usually hard coals, although brown coal (lignite) also occurs Coals from the Tertiary (Paleogene and Neogene) are mainly brown coals