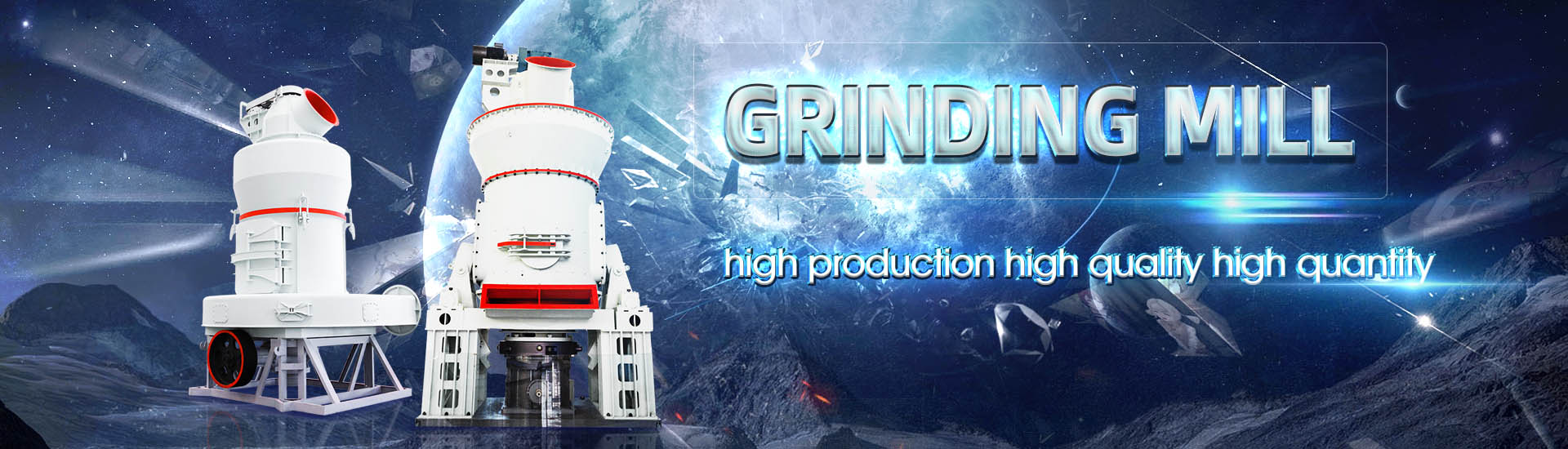
How to control the dust of ore mill and powder equipment
.jpg)
Dust Control in Mines: Methods, Sources, Solutions Oizom
Mining companies are responsible for monitoring and controlling their dust emissions because dust is produced at every stage of the mining process: mine construction, extraction, processing, storage, and transportation Government agencies in the United States, Canada, and the European Union define and regulate 展开Mention of any company or product does not constitute endorsement by the National Institute for Occupational Safety and Health (NIOSH) In addition, citations to Web sites external to NIOSHDust Control Handbook for Industrial Minerals Mining and 2023年12月1日 Establishing a mechanized, automated, and intelligent dust control system, and developing highefficiency, lowenergy consumption dust removal equipment are the main A review of dust control/removal methods in metal mines in ChinaAll powder handling and processing within a manufacturing process has the potential to generate dust in the atmosphere of the facility where the powder handling equipment is housed Minimizing dust levels well below hazardous Dust Control for Powder Handling Sterling Systems
.jpg)
Dust control handbook for industrial minerals mining and processing
The handbook describes both dustgenerating processes and the control strategies necessary to enable mine operators to reduce worker dust exposure Implementation of the engineering 2023年10月18日 A dust control strategy for a powder and bulk application will include containment and capture; dust collection and filtration; and housekeeping and administrative controls Containment and capture Where possible, dust Dust collection basics for powder and bulk solid 2020年11月1日 Minimizing dust in and around bulkmaterialhandling systems is most effective when less dust is allowed to escape from your materialhandling system This article provides information on design strategies and Mitigate Dust Hazards With Good Equipment and 2023年12月1日 In recent years, the control and removal methods for dust pollution in metal mines mainly focused on six aspects: (1) ventilation and dust removal technology, (2) sealed A review of dust control/removal methods in metal mines in China
.jpg)
Mineral Dust Emissions at Metalliferous Mine Sites
2016年10月19日 This review considers aspects of mineral dust related to the mining of metalliferous ores including: (a) sources of mineral dust at mine sites (ie land clearing, drilling For water spray or misting systems to be effective in controlling/suppressing airborne dust, the mist curtain efficiency and energy need to be matched to suit the product flow rate, the processIron Ore 2015 Conference ResearchGate3 Dust explosion and prevention, Institution of Chemical Engineers, 2002, ISBN 4 BS EN 14491:2006: Dust explosion prevention systems 5 BS EN 61241 Part 10: Electrical equipment for use in combustible dust atmospheres 6 BSEN 14797 Explosion venting devices 7 BSEN 14373 Explosion suppression devices and systems Web Prevention of dust explosions in the food industry HSEExplore our Powder Milling Equipment and why Hammer Milling is the choice when you need to precisely control the particle size reduction process Explore our Powder Milling Equipment and why Hammer Milling is the Altering the Fitzpatrick Powder Milling Equipment
.jpg)
Iron Ore: From Mining to Processing to Dust Control
Proper dust control for mining and processing iron ore has a system that targets each source and cause of fugitive dust Benetech’s patented MaxZone ® Modular Skirtboard, and Belt Support System seals your iron ore load zone to reduce 2017年4月24日 Grinding stone into powder is something you might need to do for all sorts of reasons The process of assaying ore samples for mineral content usually requires that stone be ground down to a fine powder Other reasons for grinding it might also include the production of ingredients for chemicals, dyes or building materials Although most types of stone are very How To Grind Stone Into Powder Sciencing2024年1月11日 With a ball mill 1 To pulverize crushed coals in a ball mill, you start by feeding the mill with crushed coal Then the grinding media crushes and grinds the coal in the rotating chamber 2 Airflow carries the pulverized coal out of the ball mill 3 Next, you'll need to use the mill classifier to separate the fine coal particles from the airflowHow to Process Coal into Pulverized Coal in 5 Steps?equipment and pipes are also important to eliminate static charges, which are a source of ignition Dust explosion risks may be even more serious in plant rooms containing the milling machinery than in the machinery housing itself The hazard arises from bad housekeeping, which allows dust to accumulate on ledges, ceiling beams, and other Back to Basics Hammer Milling and Jet Milling Fundamentals
.jpg)
A guide to SAG Mill management
2024年5月17日 A SAG (SemiAutogenous Grinding) mill is a giant rotating cylinder filled with grinding media and the ore being reduced As the mill rotates, the grinding media lifts and the impact crushes the feed material SAG mill control refers to the practice of managing the mill load, which is the amount of material inside the mill at any given timeThe mineral powder grinding mill is a commonly used grinding equipment In the mineral powder production line, a large amount of dust will be generated during the production process which not only endangers the health of operators, but also easily causes environmental pollution Therefore, solving the dust problem of grinding equipment has How To Deal With The Dust Problem In The Grinding Process Of Mention of any company or product does not constitute endorsement by the National Institute for Occupational Safety and Health (NIOSH) In addition, citations to Web sites external to NIOSHDust Control Handbook for Industrial Minerals Mining and Most of these dust control measures really only treat the “symptoms” of dust generation and are considered as “protection” methods (ie they do not deal with the root causes of the problem)Iron Ore 2015 Conference ResearchGate
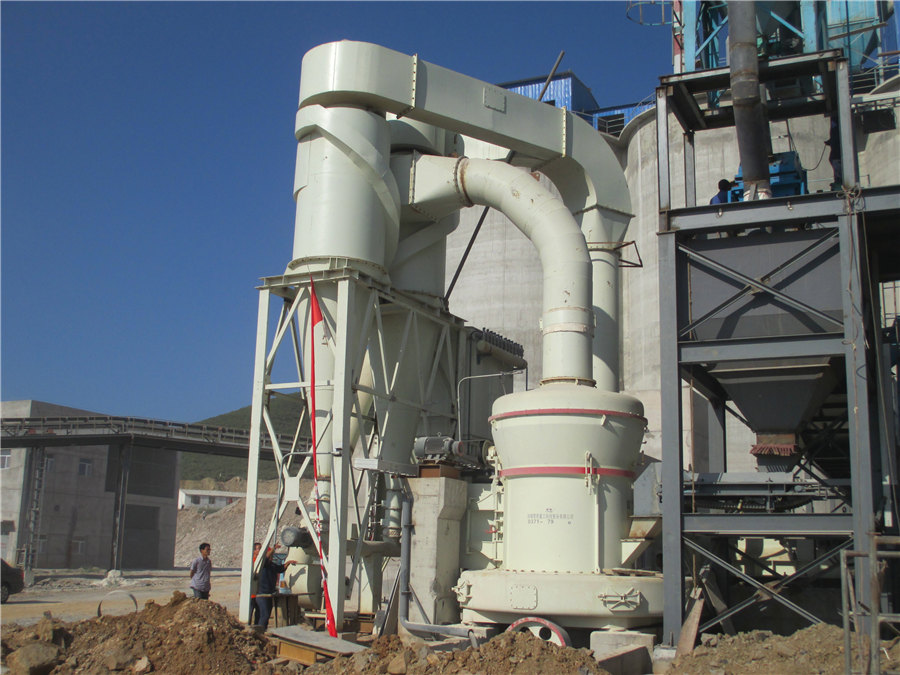
Dust collection basics for powder and bulk solid
2023年10月18日 Elements of dust control A dust control strategy for a powder and bulk application will include containment and capture; dust collection and filtration; and housekeeping and administrative controls Containment and Coal dust explosions are among the severe hazards in industries using coal, posing significant risks to personnel and infrastructure These explosions occur when fine coal particles become airborne and come into contact with a heat source in an enclosed environment, leading to a rapid combustion event Given the catastrophic potential of such incidents, robust measures for coal Coal Dust Explosion Protection: Ensuring Safety in industries using 2022年1月11日 ABSTRACT Resuspension of iron ore dust presents a constant hazard in the working environment within steel production plants Herein, the optimal operating parameters for maximum dust suppression efficiencies through a water mist generator and a conventional sprinkler for particulate matter (PM) originating from an iron ore pile measuring about 2 m in Suppression Efficiency for Dust from an Iron Ore Pile Using a 2016年2月29日 Sometime, the selection, design and operation of any process are complex and needs a special study In this way, improvements in the understanding of the processes have developed better equipments, efficiency and productivity Special operations have sophisticated instruments dedicated to control and give more realistic information about the Gold Extraction Recovery Processes 911Metallurgist
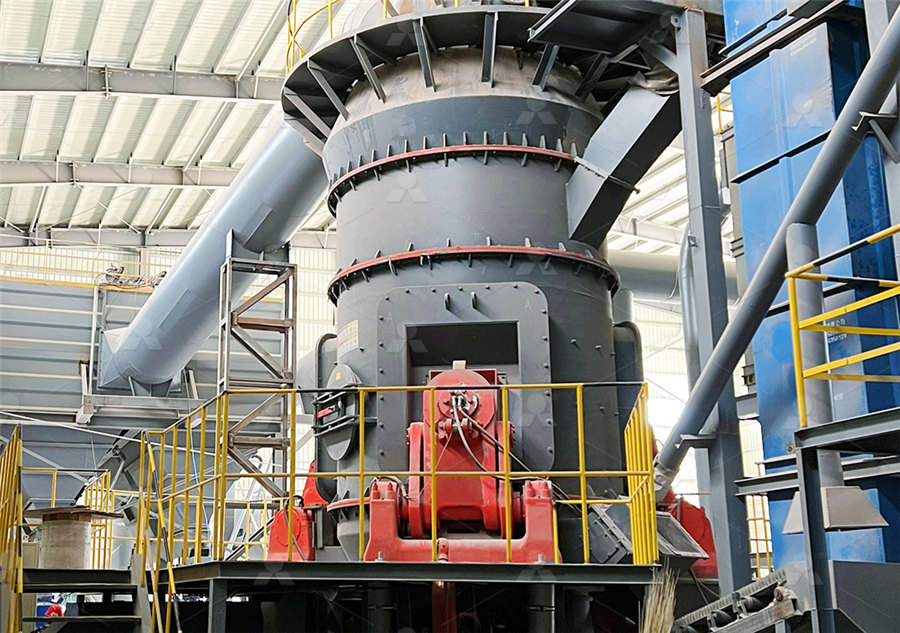
Roller mills: Precisely reducing particle size with greater efficiency
microns The roller mill’s ability to reduce materials to a uniform particle size provides more control of product characteristics and minimizes waste, as shown in Figure 1 The mill’s controlled reduction action requires less energy than other grinding methods, improving production efficiency and saving energy dollars2017年3月4日 Ball mills are used for wet grinding iron ore, g old/copper ore, nickel ore and other ores, as wel l as lime/limestone for flue gas desulphurisat ion systems, coal and other raw materials Rod mill :SIZE REDUCTION BY GRINDING METHODS ResearchGateHowever, ore below the pay limit adds variation to the mill grade as increased mill throughput will be required to make up for the loss of gold, and that impacts on the recovery in the plant It is against these perspectives and findings of this study that the MCF should be seen as a method that identify the real problems underground and when these are addressed, the profitability of Monitoring ore loss and dilution for minetomill integration in As the size of the industry is large, pollution control is a costly proposition Major pollution sources and types in iron and steel industry are presented How to Control Air Pollution in Iron and Steel Industry: There are emissions to the atmosphere in the form of dust, fume and steam, acid emissions, fugitive emissions and toxic gasesHow to Control Pollution in Iron and Steel Industry?
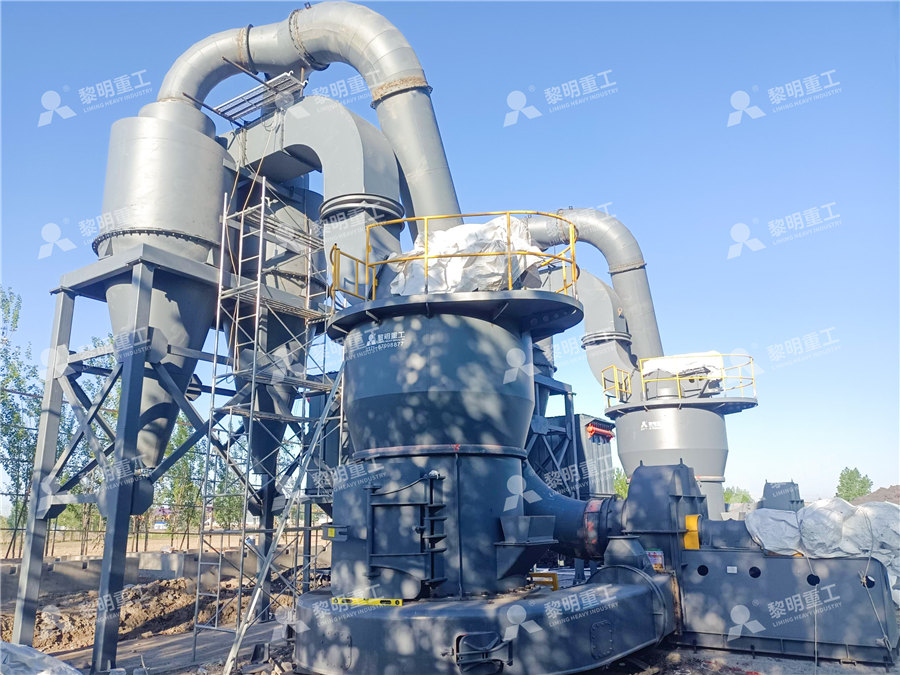
What is Raymond Mill? How Does It Work? alwepo
2024年9月4日 To mitigate this risk, proper ventilation and dust control measures, such as dust collection systems, should be in place to minimize the dispersion of particles into the air Operators are typically required to wear personal protective equipment, including dust masks and safety goggles, to reduce their exposure to airborne particles 22015年8月6日 There are three mill slurry characteristics which you should note The % fines in the rod mill feed For the purposes of rod mill performance analysis, “fines” can be arbitrarily defined as particles finer than 75 microns (200 mesh) Rod mill feeds which contain less than approximately 10% fines are good candidates for fines addition testworkBall Rod Mill Density – How Water Impacts GrindingGoogle's service, offered free of charge, instantly translates words, phrases, and web pages between English and over 100 other languagesGoogle Translate Automation: Modern ore powder production equipment is equipped with advanced automation systems, which improve operational efficiency and reduce labor costs Energy Efficiency: Innovations in mill design and technology have led to more energyefficient equipment, reducing the overall energy consumption of the processAdvancements in ore powder production process equipment:
.jpg)
Powder Processing Equipment Systems Qlar
The Kek Cone Mill provides a gentle, low energy form of size reduction and eliminates traditional milling problems including noise, dust, and heat generation The gentle grinding action is capable of control within fine limits while maintaining a close particle size distribution with minimal fines generation Kek Cone Mills2024年4月30日 Introduction: The mineral ore processing industry is a sector that can generate pollutants in the form of dust during the production, commonly known as respirable dust(PDF) Risk Assessment of Respirable Dust Exposure to Workers in 2021年5月31日 The nature of the ore blending problem is due to uncertainty and the uneven distribution of minerals in geology The benefits of ore blending are extending the ore reserve base by utilization of (PDF) A Method of Ore Blending Based on the Quality of few locations the ore is processed without fine grinding, and the resultant tailings are transported in a nearly dry form to a waste disposal area The specific radioactivity of uranium mill tailings is low About 15% of the total radioactivity which was originally contained in the ore is retained in the yellowcake produced by the millManagement of wastes from uranium mines and mills
.jpg)
How to Control Dust in Crushing Plant 911Metallurgist
2020年11月8日 On Ray installations this method was employed on all dust control systems with the exception of the sample mill exhaust system, where diversified control was advantageous Exhaust System Installations Opinions vary among the authorities in the field of dust control regarding the size of exhaust systems2024年8月7日 Key types include Jaw Crushers, which handle large rocks and ores through compressive force; Cone Crushers, which provide finer output for hard materials; and Impact Crushers, which use highspeed impacts to process softer ores Grinding Equipment: After crushing, grinding refines ore into a fine powder to liberate valuable mineralsMineral Processing Equipment for Mining Industry2021年11月3日 Phosphate Rock Processing Process Phosphate ore processing and production processes mainly include three processes: crushing, grinding, and beneficiation In the crushing process, the threestage closedcircuit crushing is more modern and suitable for the crushing of highhardness phosphate orePhosphate Mineral Powder Grinding Mill SBM Ultrafine Powder 2023年7月15日 An integrated steel plant plays an important role in India’s economic growth with a positive impact on country’s GDP The contribution of iron and steel sector towards India’s GDP is around 2% which is quite high []India is the second largest producer of crude steel after China with a market share of almost 6% []India has produced around 1112 million tons in 2019 [] to Utilization of Some of Major Steel Plant Wastes to Produce
.jpg)
MeasurementControl for Crushing and Screening Process
2023年6月3日 It mainly includes crushing process control, crushing appliance fault diagnosis, and automatic distributing control Crushing Process Control To ensure the continuous, stable, and safe operation of the ore crushing production process, it is necessary to monitor the running state and parameters of key equipment (such as crusher and belt conveyor) in real time for Mode 1 Reject Excess Dust In Mode 1, the dust bin with an auger dust spillover, the discharge port is used to automatically reject what the vane feeder does not take away (ie, the dust the plant does not use as a percentage of dust being How to Control Dust During Production2016年10月28日 Sintering is an agglomeration process that fuses iron ore fines, fluxes, recycled products, slagforming elements and coke The purpose of sintering is to obtain a product with suitable Iron Ore Sintering: Raw Materials and Granulation ResearchGateThe mills were typically enclosed in buildings with the equipment arranged in levels, the variety of processes that have been used to mill ore (again) There are 4 Dorr Continuous Thickeners used The cyanide solution is precipitated by means of zinc dust discharged from an endless belt into a cone The cyanide and zinc combine Winning the Metal: Ore Mills of the West Western Mining History
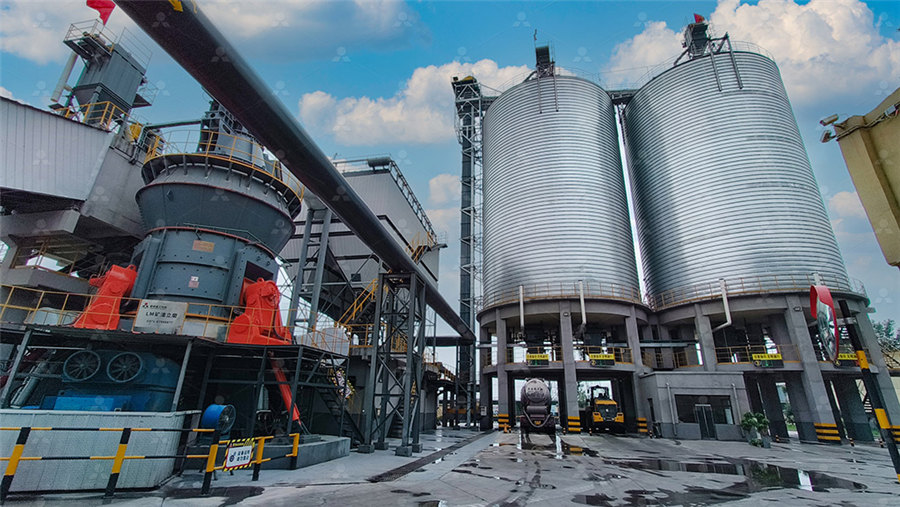
A review of dust control/removal methods in metal mines in China
2023年12月1日 The main harm of dust in metal mines to human health is pneumoconiosis To track the incidence rate of occupational diseases, the National Health Commission of the People's Republic of China conducts statistics on the incidence rate of occupational diseases every year Fig 2 shows the number and proportion of new occupational diseases and pneumoconiosis in 2012年6月1日 The feed material is typically composed of the BFRs and the catalyst, both in powder form As the cylinder starts to rotate, the grinding balls inside the cylinder crush and grind the feed Grinding in Ball Mills: Modeling and Process Control2011年1月1日 Grade control programs aim to deliver economic tonnes to the mill via accurate definition of ore and waste The foundation of a successful program is high quality sampling supported by geology and Design of grade control sampling programs for underground gold mines2020年1月12日 This paper also illustrates design analysis and the best selection of a dust collection system for various kinds of manufacturing industries who are facing dust emission and unable to control as Design analysis of Dust collection system ResearchGate
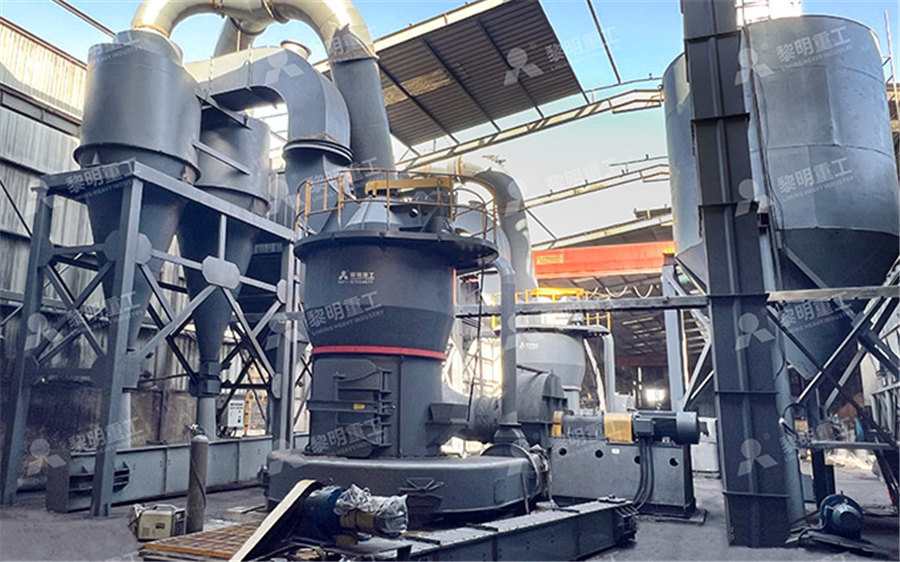
(PDF) Control of ball mill operation depending on ball load and ore
2023年12月12日 In addition, the ore properties are one of the important parameters for the optimal utilizing of the ball mill Ore can have various properties, such as hardness, density, moisture content, etc