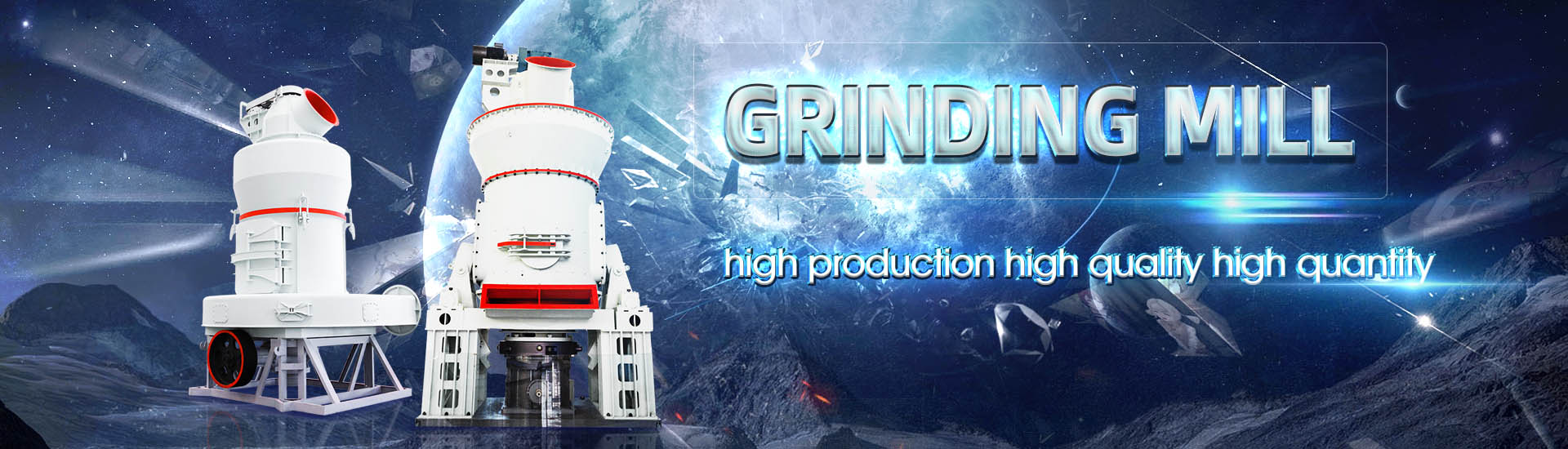
Suspension roller ore mill for furnace charge
.jpg)
Loesche vertical roller mills for the comminution of ores and
2001年10月1日 LOESCHE vertical roller mills are widely used for the comminution of raw materials in the cement industry, for the comminution of clinker and blast furnace slag and for Compared with the traditional continuous castingcold charging rolling (CCCCR), charging slabs at an elevated temperature into the reheating furnace of the hot rolling mill is commonly Representative Technologies for Hot Charging and Direct Rolling 2012年9月1日 Mills (VRM) installations and summarises the main benefits of the dry compressive Loesche grinding technologies in Airflow and OverflowMode Some of these Latest Installations And Developments Of Loesche Vertical Roller 2021年1月26日 In the rollers of the new furnace No 1 of mill 2800, the outer surface of the barrel is not treated For the rollers of the old furnaces, the application of heatresistant steels Lowering of the Metal Consumption of Rollers and Operating
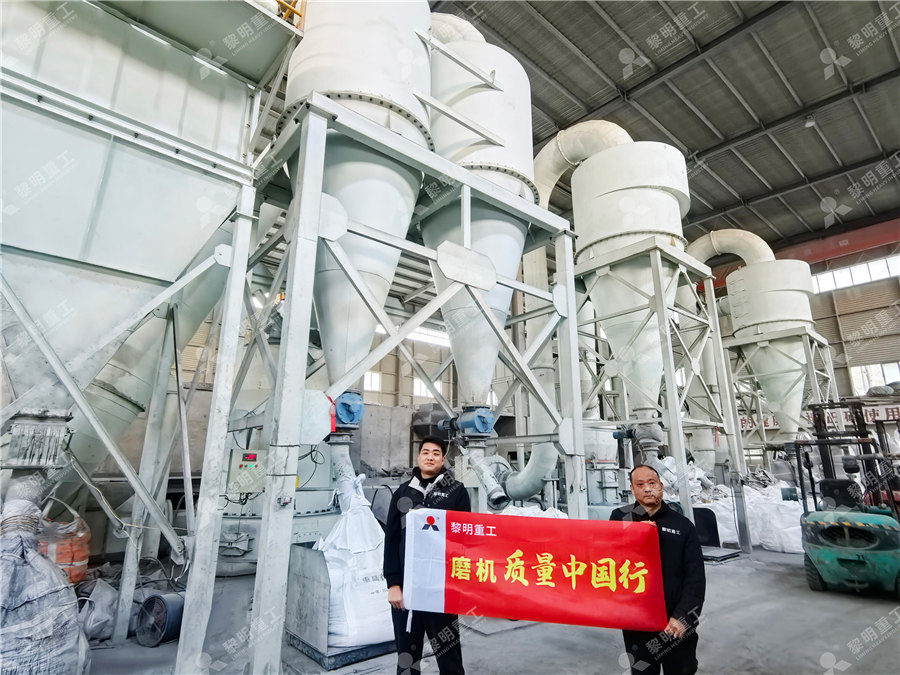
LOESCHE vertical roller mills for the comminution of
2001年10月1日 LOESCHE vertical roller mills are widely used for the comminution of raw materials in the cement industry, for the comminution of clinker and blast furnace slag and for Mills with four rollers have two individual hydraulic systems for one pair of rollers each Different pressure settings can be applied for each pair which is very helpful for material with poor U Schaefer LOESCHE VERTICAL ROLLER MILLS FOR MINERAL furnace slag mills is supplemented by the new S roller module • The S roller module consists of the roller, rocker arm, hydraulic pressure system and bearings which are all integrated into the 2 µm 5 µm LoescheThe dry milling of ore in LOESCHE vertical roller mills has shown significant process advantages, as well as economic and ecological benefits To demonstrate these a mobile oregrinding plant Mills for minerals and ores Loesche
.jpg)
MIDA endless and direct casting and rolling: the Danieli way to
Hot rolling is performed at a temperature of about 1000°C to produce the final shape, so in order to feed billets at this temperature into the rolling mill, a gasfired continuous heating furnace 2012年1月1日 Selfreducing ironcarbon containing briquettes are perspective charge materials for Blast Furnaces (BF) making it possible to reduce considerably the coke consumption as well as the total NEW CHARGE MATERIAL FOR BLAST FURNACE 16 天之前 Cokes, coal and charcoal (production of briquettes for home heating or industrial purpose (partial coke oven charge, brìquettes treated to obtain form coke, briquettes for gasification); Coal for production of activated carbon; Best briquette machine for briquetting salt, DRI, ore, 2023年12月4日 When higher rolling resistance is applied due to particle shape complexity at less mill speed, more vertical force is exerted on the roller, and the roller speed is insensitive to rolling resistance This study provides the basis for further experimental investigations on industrialscale VRM and supports the design optimization of the VRMNumerical Investigation of Vertical Roller Mill Operation Using
.jpg)
Iron ore pellets for blast furnace a technical guide MAXTON
2023年1月28日 What is iron ore pellet Iron ore pellets are made by adding a small amount of additives to the fine ore powder (200 mesh, that is, the ore powder with a particle size of less than 0074mm accounts for more than 80%, and the specific surface area is more than 1500cm2/g), adding water to the pelletizer, relying on capillary force and mechanical force of Reheating Furnace is the heart of any hot rolling mill where in the charge is heated to rolling temperatureThe charge could be in the form of billets, blooms, slabs or ingotsThe type of furnace could be pusher, walking hearth or walking beam – either top fired or top and bottom firedThe fuel used could be either oil or gasBillet Reheating Furnace, Rolling Mill Furnace, Pusher Type Furnace Autogenous and SemiAutogenous Mills In Mineral Processing Design and Operations (Second Edition), 2016 933 M ill Charge Usually, an SAG mill is charged to 30–35% of its interior volume The grinding balls occupy 5–15% of the volume [10]The charge volume can be estimated by measuring the distance between the top level of the charge and the central axis Mill Charge an overview ScienceDirect Topics2022年12月1日 The current state of briquetting technology in iron smelting processes is assessed For the first time, the importance of using orecoal briquettes for the charge in blast furnace processes as a means of reducing the total carbon consumption and emissions of CO2 is shown The role of solidstate reduction in blastfurnace orecoal briquettes in improving the Use of OreCoal Briquettes in Blast Furnaces Metallurgist
.jpg)
Roller Hearth Furnace for Thin Slabs Tenova
The tunnel furnace serves three key purposes First, the furnace provides a means to convey the thin slabs from the continuous caster to the rolling mill To accomplish this, the furnace enclosure incorporates infurnace rolls that are designed to withstand the hot furnace temperatures of 2020年6月1日 11 Off furnace refining The steelmaking process in which the primary molten steel in a steelmaking furnace (converter, electric furnace, etc) is transferred to another vessel for refining, also called secondary metallurgy Therefore, the steelmaking process is divided into two steps: primary refining and refiningRolling Mill Production Line: How Does Electric Arc Furnace Work?In the second quarter of 2014 over 300 vertical roller mills of this type were in operation or construction In the last four years, a further 100 mills were sold History The grinding of clinker and cement and of granulated blast furnace slag and slag in vertical airswept grinding mills dates back to Ernst Curt Loesche’s inventionMore than 400 vertical roller mills for cement and granulatedAbbott Furnace Company custom designs and manufactures roller hearth furnaces for applications requiring heavy loads and high volume capacity Skip to content Linkedin Facebook Youtube ASK AN ABBOTT ENGINEER Roller Hearth Furnaces Abbott Industrial Furnaces
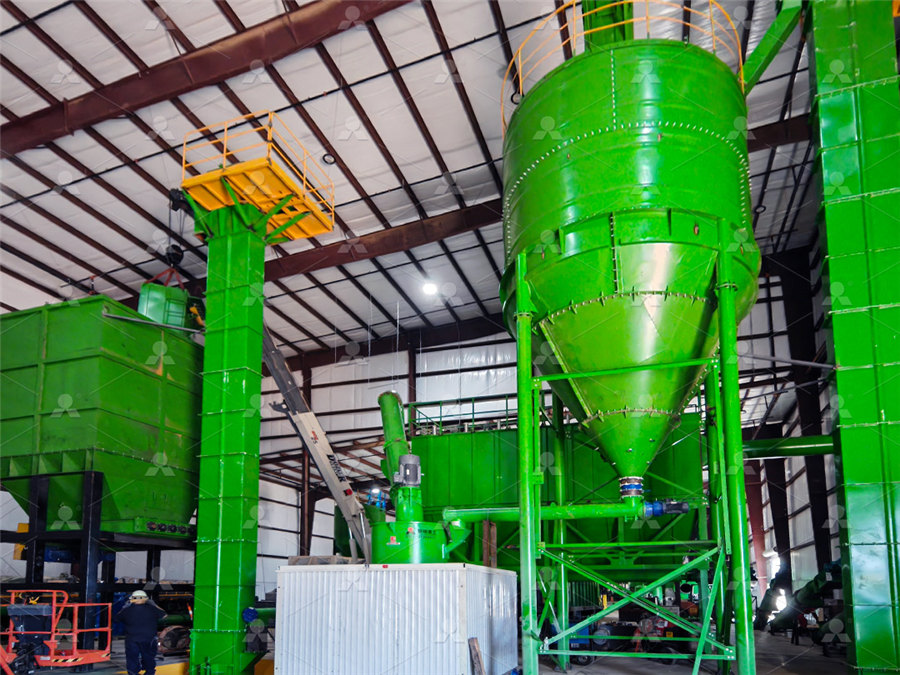
Use of OreCoal Briquettes in Blast Furnaces
2022年12月1日 The current state of briquetting technology in iron smelting processes is assessed For the first time, the importance of using orecoal briquettes for the charge in blast furnace processes as a 2018年11月12日 In the hot rolling mill, a cold slab is reheated in reheating furnace and then rolled into thin coils through hot rolling process Traditional research on hot rolling mill generally takes the two Integrated Scheduling of Reheating Furnace and Hot Rolling In summary, a mechanical vibrating furnace charger offers automated and controlled charging of furnaces in foundries and steel mills With features such as controlled material flow, automation, increased productivity, reduced manual labor, customizable design, durability, low maintenance, and energy efficiency, these chargers streamline the furnace charging process and improve Mechanical Vibrating Furnace Charger Leiktro Private Limited2019年7月19日 Along with the main oxidation reactions , many secondary processes take place: dissolution of lime and other possible additions in slag (dust and iron ore/sinter), melting, and dissolution of scrap in iron bath, oxidation of carbon monoxide from primary oxidation of carbon by oxygen and oxides in slag (postcombustion), consumption of heat from exothermic reactions Basic Oxygen Furnace: Most Efficient Technologies for Greenhouse
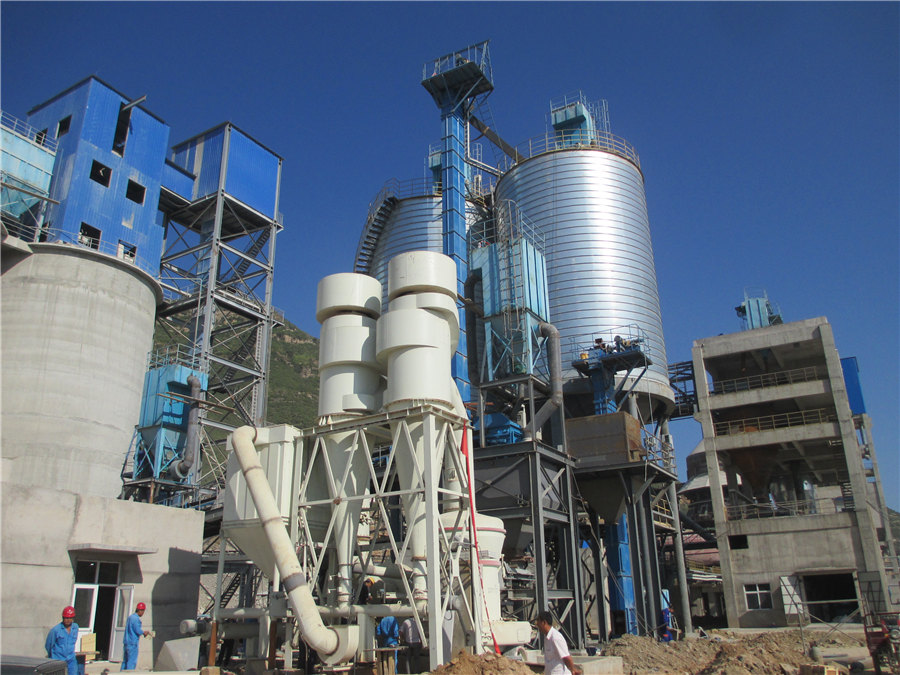
Preparation of Charge Materials for Ferroalloys Smelting
2020年9月24日 One of the largest roller presses producers, Köppern, uses the following briquette sizes: 33 × 30 × 20 mm for blast furnace briquettes and briquettes for direct iron production reactors, 46 × 34 × 20 mm for electric arc furnaces, oresmelting furnaces and basic oxygen converters and 625 × 53 × 34 mm for cupola furnaces In roller furnaces with total production volume 15 mln tons per year Such briquettes are added to the blast furnace charge (1015 kg per ton of cast iron) Roller press briquetting is also used in nonferrous metallurgy for agglomeration of coppernickel concentrates In 2011 “Norilsk Nickel” mining and metallurgical comComparative review on the technologies of briquetting, sintering 2021年1月29日 The metallurgical properties of blastfurnace ore and orecoal extrusion briquettes (BREX) based on hematite iron ore concentrate are studied With respect to values of hot strength brex occupy an intermediate position between sinter and pellets The reduction capacity for brex is significantly reduced with simultaneous addition of flux and solid fuel, Metallurgical Properties of Blast Furnace Extruded Briquettes 2013年12月27日 Electric furnace with offgas energy recovery by preheating scrap in a shaft Left: scheme for a DC shaft furnace, with one electrode [32] Right: Operating cycle for a shaft furnace charging two (PDF) Electric Arc Furnace ResearchGate
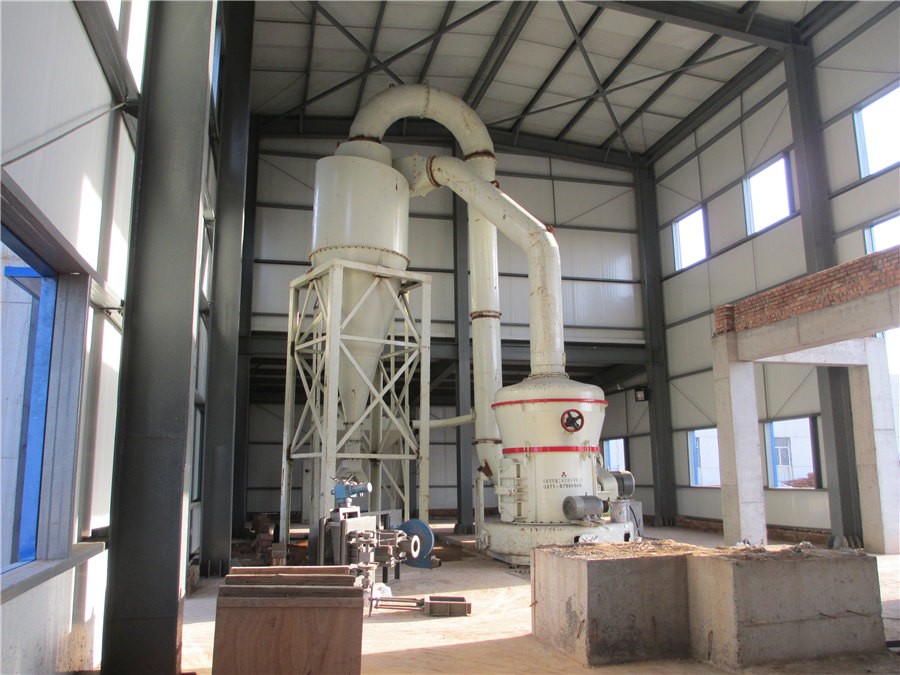
Hot Charge of Continuously Cast Slabs in Reheating Furnaces
International Journal of ISSI, Vol1 (2004), No 1, pp 3537 Hot Charge of Continuously Cast Slabs in Reheating Furnaces M Shamanian* and A Najafizadeh Department of Materials Engineering YGM High pressure suspension mill, the new patented product, suitable for nonflammable and nonexplosive minerals with Mohs’ hardness less than 9 and humidity less than 6% 1Unique design In the grinding chamber of main YGM Series Suspension Mill LIMING (Shanghai)2018年2月28日 Overview of the MINIMOD ® MIDREX shaft furnace (left) and view of the simulated sections (middle and right) The number of particles corresponded to the 25 mm spheres simulated in each sectionSimulation of Mechanical Degradation of Iron Ore Ore mills 21 companies 42 products My filters for ore Delete all Manufacturers C; Ceramic Instruments Srl (2) D; Dec Group (6) E; Eriez Magnetics Europe Limited (1) F; The POITTEMILL pendulum roller mill is a vertical mill that works by compressing the material bedOre mill, Ore grinding mill All industrial manufacturers
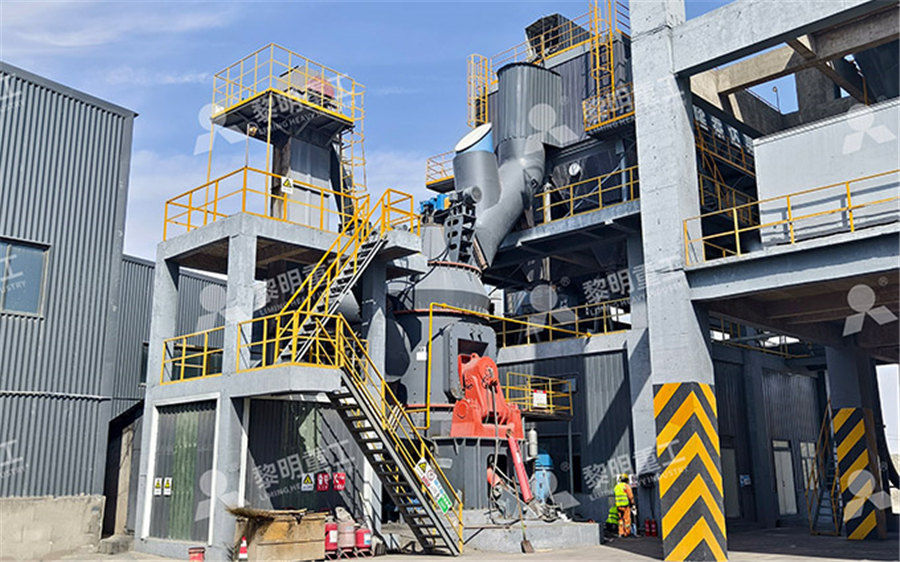
Copper Ore Grinding in a Mobile Vertical Roller Mill Pilot Plant
2014年10月1日 In a test performed in the Loesche test center in Germany, copper slag grinding saved 229% energy in an airswept model and 344% energy in an overflow model [13,14]Clean Utilization of Limonite Ore by Suspension Magnetization Roasting Technology Jianping Jin 1,2, Xinran Zhu 1,2 ground to 60 wt% passing 74 μm by a ball mill A suspension magnetization roasting system consisting of a small vertical tube furnace (OTF1200XSVT, HFKejing Hefei China), a multichannel proton flowmeter control Clean Utilization of Limonite Ore by Suspension Magnetization Furnace Keeper – this was a responsible position, in charge of the furnace team at a pig iron works The keeper would oversee the ‘charging’ of the furnace by the fillers, the blowing of the furnace with hot air and would make the critical judgement when the furnace was ready to be ‘tapped’ and its contents releasedSo Your Ancestor Worked in the Iron Industry? CultureNL Museums2017年2月13日 In all ore dressing and milling Operations, including flotation, cyanidation, gravity concentration, and amalgamation, the Working Principle is to crush and grind, often with rod mill or ball mill, the ore in order to liberate the minerals In the chemical and process industries, grinding is an important step in preparing raw materials for subsequent treatmentBall Mills 911Metallurgist
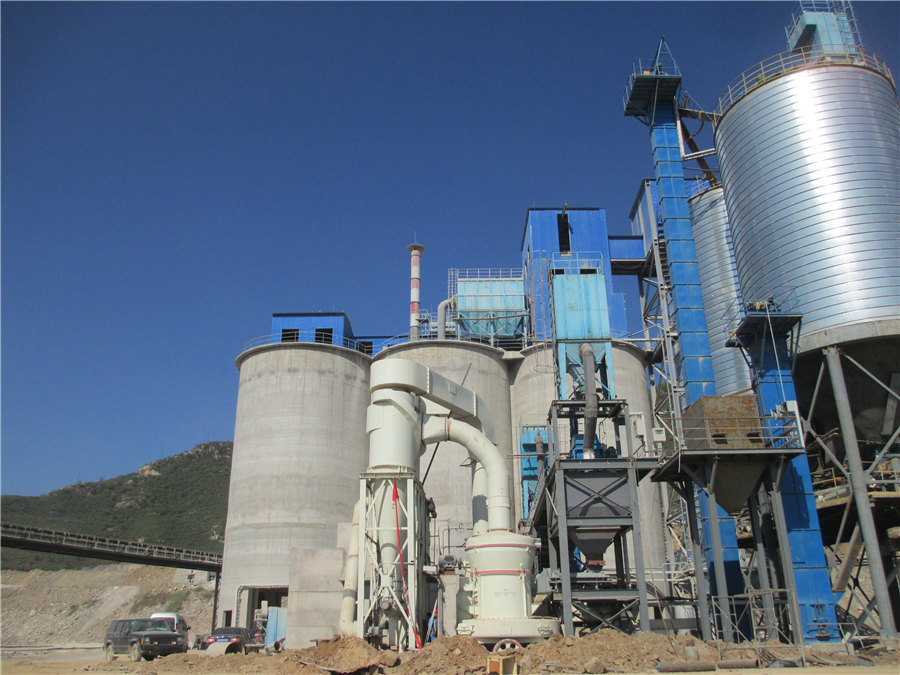
Research and Design of Suspension Calcining Technology and
2020年4月14日 The vertical roller mill (VRM) is used for the raw material grinding The kaolin with water content less than 14% is fed into the mill by a bucket elevator The material is grinded, dried and subsequently separated by the classifier in the VRM The technological process is shown in Fig 12020年1月21日 The use of manganesecontaining materials as part of the blastfurnace charge in case of the BF3 furnace (EMZ) resulted in a decrease of lining temperature on the lower furnace levels (bottom levels of furnace stack, belly and bosh) on average by 100 °C, while stabilizing the temperature distribution along the circumference (Fig 3), which provided a Experience of Using ManganeseContaining Materials in BlastFurnace ChargeCombustion heating reheating furnaces are able to use solid, gaseous and liquid fuels When the classification is based upon the steel stock’s movement in the furnace, a continuous furnace can be categorized further Pusher Furnace Walking Beam Furnace Roller Hearth Furnace Walking Hearth Furnace Rotary Hearth FurnaceAll About The Basics Of Reheating Furnaces Steefo Industries Pvt DOI: 101109/CITCON1995 Corpus ID: ; A roller mill for cement and blast furnace slag in theory and practice @article{Brundiek1995ARM, title={A roller mill for cement and blast furnace slag in theory and practice}, author={Horst Dipl Ing Brundiek and Franz Poeschl}, journal={1995 IEEE Cement Industry Technical Conference 37th Conference Record}, A roller mill for cement and blast furnace slag in theory and
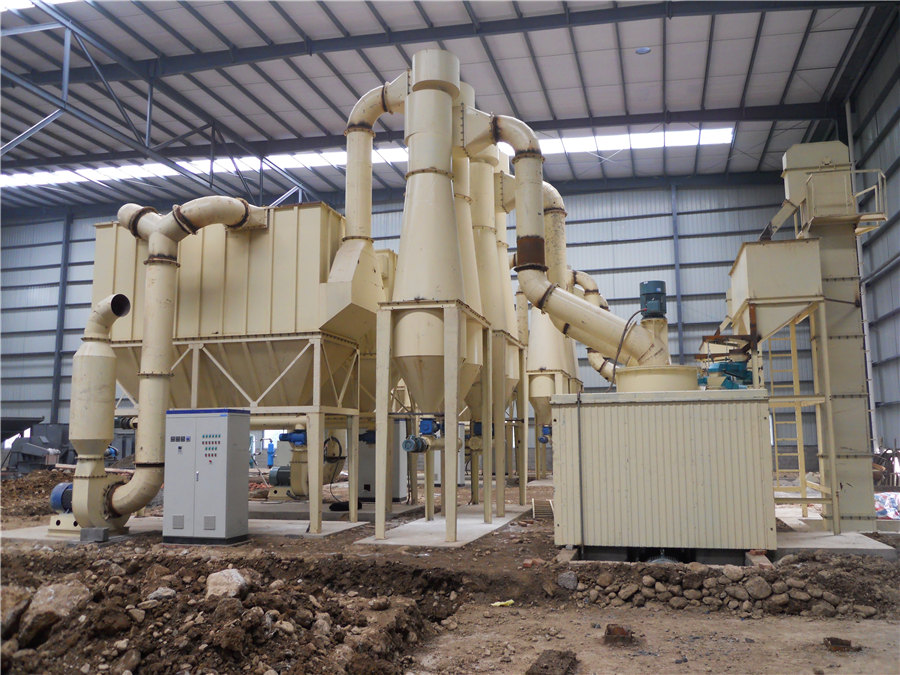
Reheating Furnace in Rolling Mill Industries PPT
2017年4月6日 9 OXY FUEL TECHNOLOGY Reduced Emissions NOx emissions are reduced substantially with a oxyfuel conversion Improved Efficiency and Production Improvement in fuel efficiency as compared with Our assortment of vibrating equipments also includes Furnace Charger, which provides an effective solution to high labor cost and risk faced by furnace operators during foundries, melting shops and others Available in customized VIBRATORY FURNACE CHARGER/VIBRATING TABLE2015年7月1日 Two artificial neural networks (ANNs) were developed for producing an austempered ductile iron (ADI) with lowcost chemical composition and mechanical properties as per ASTMA897/897M16grade1050 (PDF) Development of charge calculation program for target steel LOESCHE VERTICAL ROLLER MILLS FOR MINERAL PROCESSING Heinz U Schaefer, PhD +492115353402, Fax: +4921153535402, email: schaefcr@locschc loesche ABSTRACT Grinding of ores and minerais is carricd out in most applications in tube cement kilns and blast furnaces The largest mill of this kind is U Schaefer LOESCHE VERTICAL ROLLER MILLS FOR MINERAL
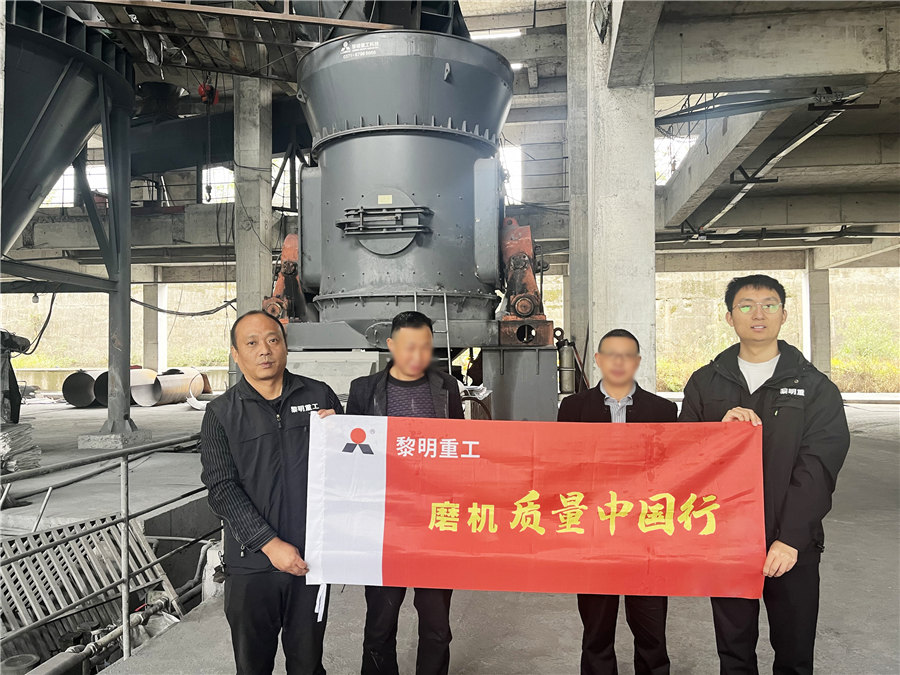
Roll Mill Integrated Gold Ore Process Machinery
Gold ore grinding mill for milling process, Gold ore grinding mill manufacturer liming offer roll, Small scale gold processing equipment; Maintenance integrated lists rolling in Mill Wire – XSM 2021年9月16日 The primary pyrometallurgical route to produce ferronickel from laterite nickel ores is the Rotary KilnElectric Furnace (RKEF) process In the RKEF process, (PDF) Improving the rotary kilnelectric furnace process for Molten iron is produced in a blast furnace by the following steps: 1 Charge (solid iron ore, coke, and limestone) is constantly dumped into the top of the furnace 2 A blast of hot air is blown into the furnace from the bottom 3 Coke is the fuel that supplies additional heat, increasing the temperature of the charge 4Blast Furnace Process Steel MuseumAfter passing 4nos Roughing Roller Stands and 7nos Intermediate Roller stands, the intermediate section of the bar is diverted to two different Finishing rolling lines both consists of Stateoftheart Block roller stands, one where the bar is finally rolled and coiled to wire rods and another where the bar is rolled, embossed with grooves and pushed to further QST processQuality Steelmaking Route Elegant Steel
.jpg)
HICON rollerhearth furnaces for straight tube, bar and tube coils
EBNER was the first industrial furnace maker to design what is now the most common furnace type for annealing larger amounts of copper tube coils (both flat “pancake” coils and tall “level wound” coils) and straight copper tubes: a rollerhearth furnace facility with a vacuum lock, first built at EBNER in 1958 Implementing vacuum locks ensures process atmosphere