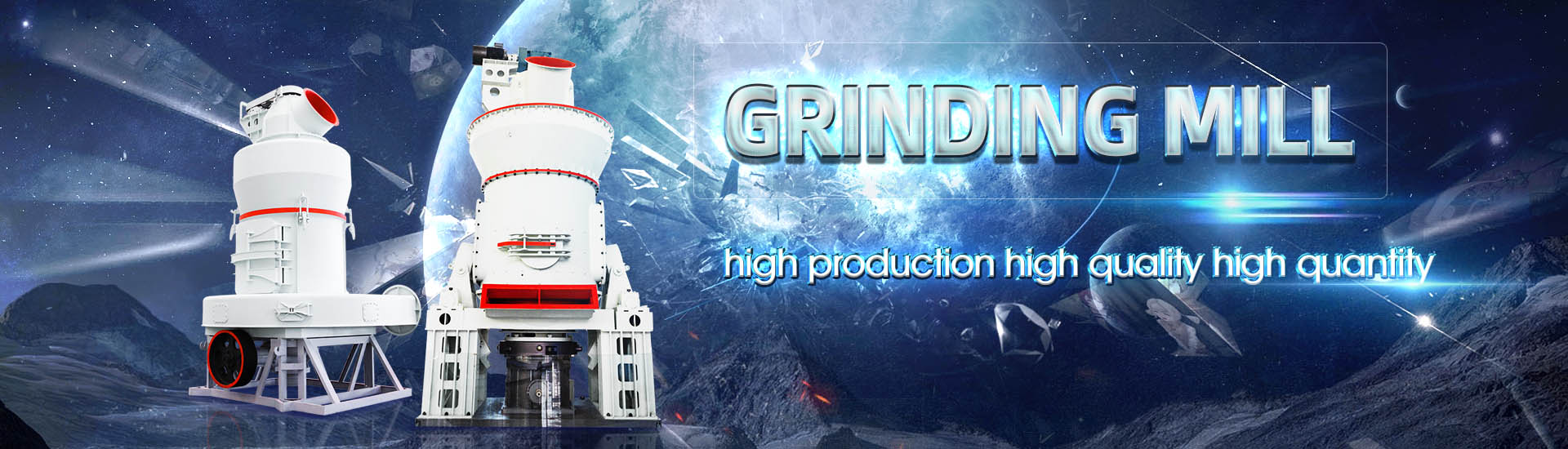
Process flow of cement plant
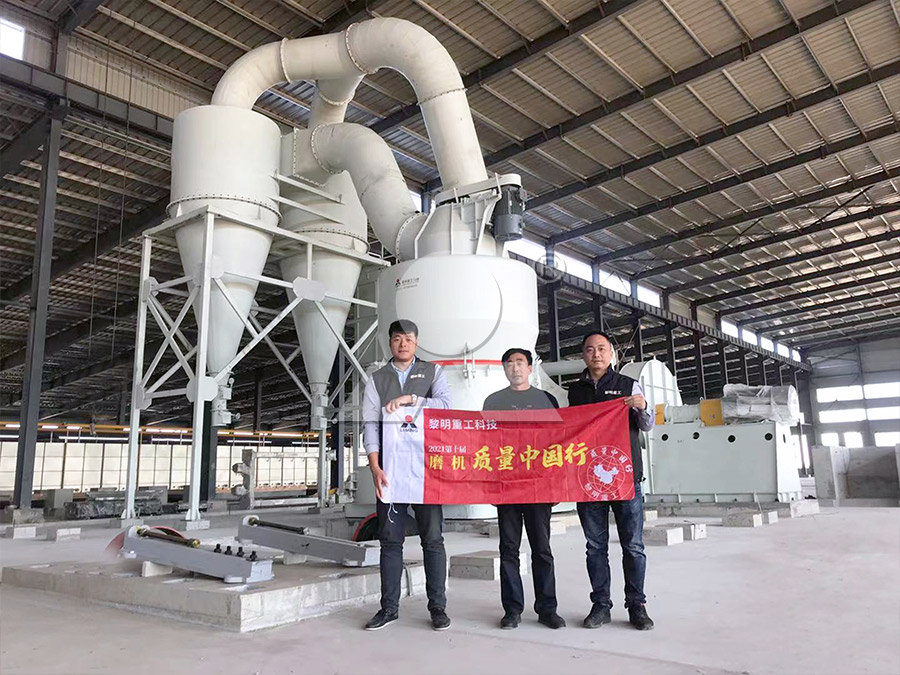
Process Flow Diagram of the Cement Plant ResearchGate
This is the ReadMe file of a SuperPro Designer example that simulates a cement manufacturing plant where cement clinker is produced by mixing clay and limestone First, clay and limestone are© 20082024 ResearchGate GmbH All rights reserved Terms; Privacy; IP ResearchGateProcess flow diagram for the cement manufacturing process, showing electricity and heat consumption or inputs [39] The paper presented herein investigates the effects of usingProcess flow diagram for the cement manufacturing Download scientific diagram Cement Manufacturing Process Flowsheet (Flow Chart) from publication: Cement Manufacturing – Process Modeling and TechnoEconomic Assessment (TEA) usingCement Manufacturing Process Flowsheet (Flow Chart)
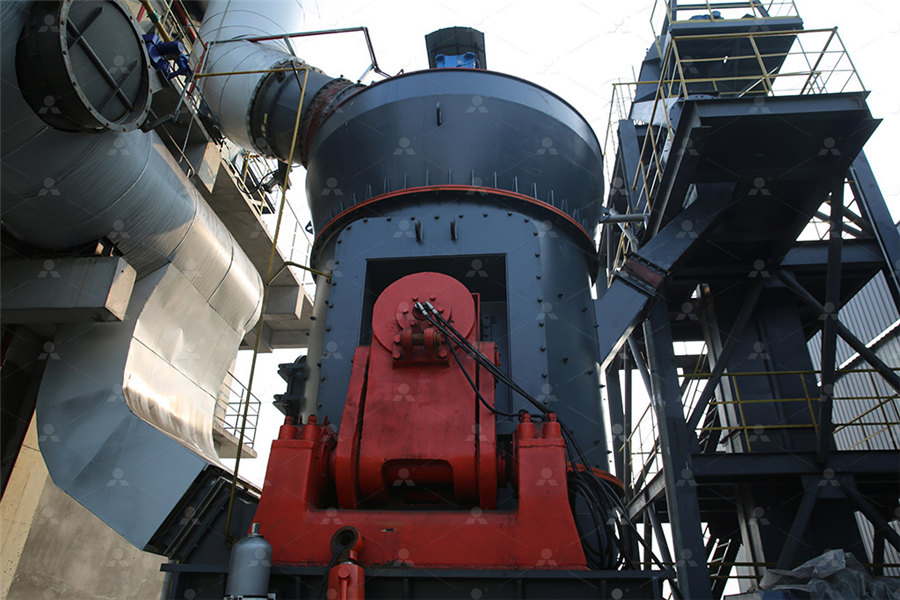
How Cement is Made Cement Manufacturing Process
There are six main stages of the cement manufacturing process The raw cement ingredients needed for cement production are limestone (calcium), sand and clay (silicon, aluminum, iron), 2018年8月28日 Production of cement completes after passing of raw materials from the following six phases These are; Cement uses raw materials that cover calcium, silicon, iron and aluminum Such raw materials are limestone, clay Cement Manufacturing Process The Engineering The Cement Plant Operations Handbook is a concise, practical guide to cement manufacturing and is the standard reference used by plant operations personnel worldwide Providing a The Cement Plant Operations Handbook International Cement Cement Plant: The Manufacturing Process worldcementassociation 1 Limestone (CaCO3) is taken from a quarry 2 4 3 The limestone is fed into a crusher and then stored until needed The Cement Plant: The Manufacturing Process 4 5 World Cement
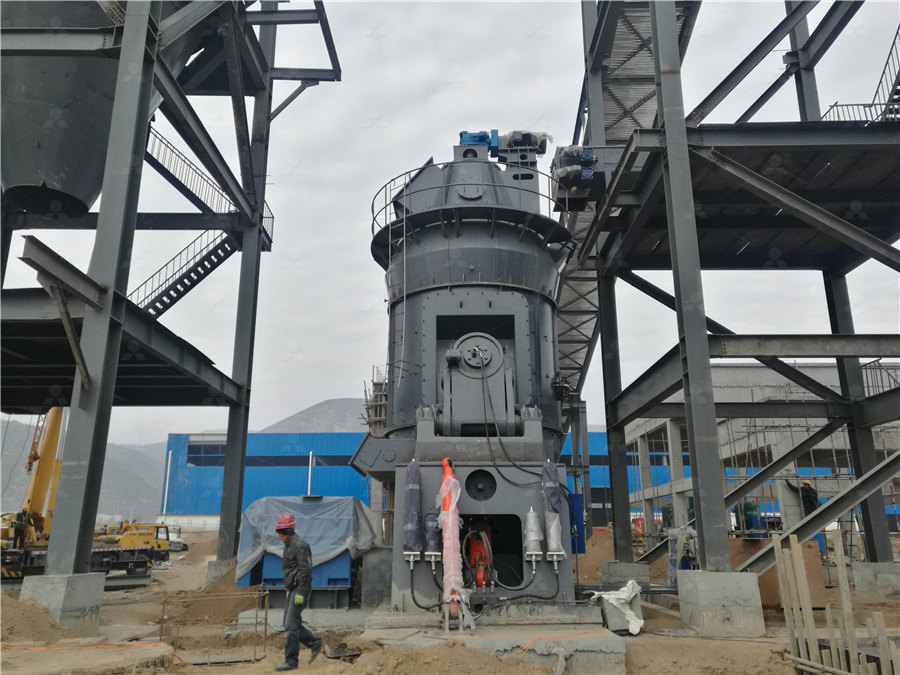
The Cement Manufacturing Process Thermo Fisher
2023年12月20日 Cement manufacturing is a complex process that begins with mining and then grinding raw materials that include limestone and clay, to a fine powder, called raw meal, which is then heated to a sintering temperature as Kiln Process Thermochemical Reactions Process Reactions Temperature ºC free water evaporates 20 100 Drying/ Preheat crystallization waterCement ManufacturingDownload scientific diagram Process flow diagram for the cement manufacturing process, showing electricity and heat consumption or inputs [39] from publication: Energy Savings Associated with Process flow diagram for the cement 2021年3月9日 In this study the process flow diagram for the cement production was simulated using Aspen HYSYS 88 software to achieve high energy optimization and optimum cement flow rate by varying the flow rate of calcium Simulation and Optimization of an Integrated Process
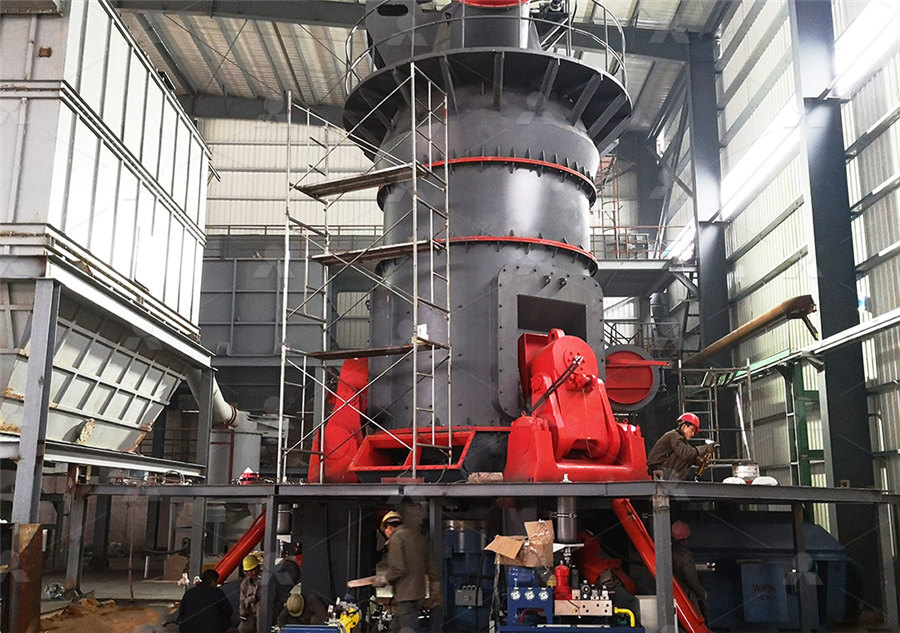
Typical cement manufacturing process flow diagram [4]
Download scientific diagram Typical cement manufacturing process flow diagram [4] from publication: Model Development for CO2 Capture in the Cement Industry Climate change has become a Choose an optimal location for the cement plant Design the layout of the cement factory Acquire the necessary equipment Construct the factory and install the equipment Recruit and train staff to operate the plant What is the process for making concrete? The concrete manufacturing process includes: Batching, where all required ingredients StepbyStep Guide to the Manufacturing of Cement2023年12月20日 The Cement Manufacturing Process flow chart sums up where in the process each type of technology is making a difference Cement operators also use these analysis systems to analyze and adjust the coal mix instream, which enables the plant to reduce energy consumption by using exactly the amount of coal fuel required to meet the specific heating The Cement Manufacturing Process Thermo Fisher Scientific2014年6月10日 Evolution of the cement Process • Wet process easiest to control chemistry better for moist raw materials • Wet process high fuel requirements fuel needed to evaporate 30+% slurry water • Dry process kilns less fuel requirements • Preheater/Precalciner further enhance fuel efficiency allow for high production ratesCement manufacturing process PPT Free Download SlideShare
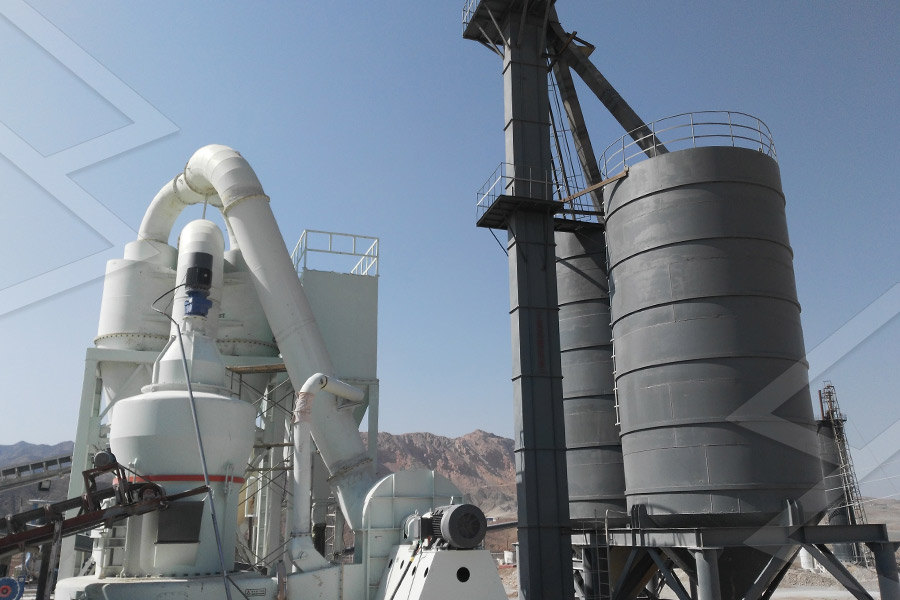
CEMENT PRODUCTION AND QUALITY CONTROL A Cement manufacturing Process
The whole process of cement manufacturing in Messebo Cement plant which consists of two separate Cement Production lines can be summarized into the following processes ;as can be seen in the process and Quality flow diagram below; 1 Quarrying and Crushing 2 Raw material Storage and Transportation 3 ProportioningDownload scientific diagram Process flow sheet of a CAP process integrated in a cement plant (adapted from [46]) from publication: CO2 Capture, Use, and Storage in the Cement Industry: State of Process flow sheet of a CAP process integrated in a cement plant 2023年9月5日 Process control experts in the cement industry need to be wellversed with the process flow, the chemical reactions, and the physical transformations that occur in a cement plant They need to understand the interdependencies between the various process parameters and how they affect the quality of the cement and the efficiency of the production processMastering Process Control Instrumentation in Cement Plants: A 2017年8月15日 Providing information on bulk materials handling (liquid and solid), plant systems engineering, specialty machine design, and process control engineering Industry focus for the following posts are bulk handling systems, ELiquid (EJuice) manufacturing equipment, Biomass, plastics and polymersThe Cement Manufacturing Process
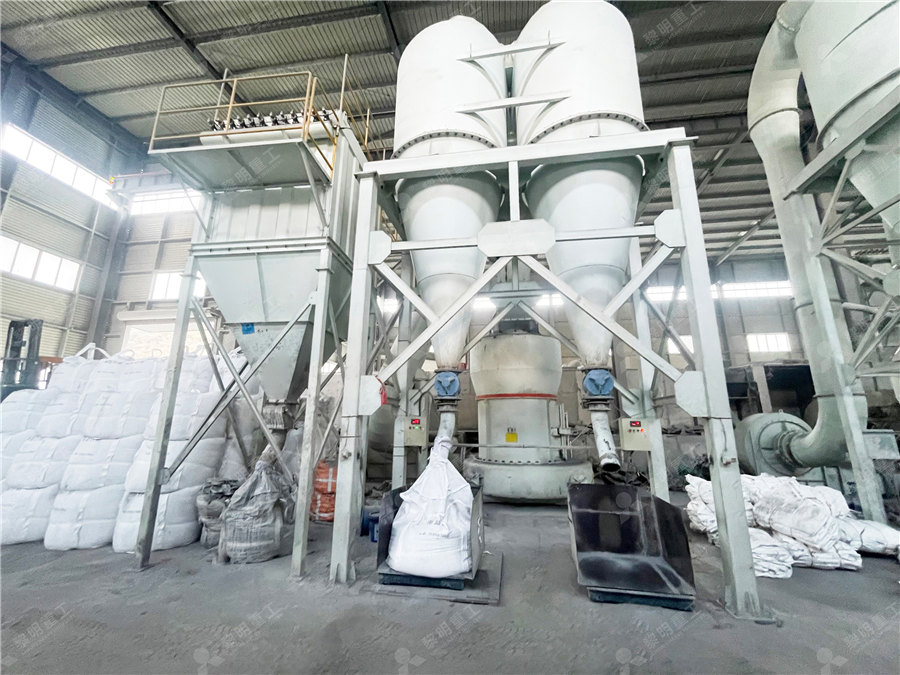
Cement manufacturing components of a cement
Cement manufacturing: components of a cement plant This page and the linked pages below summarize the cement manufacturing process from the perspective of the individual components of a cement plant the kiln, the cement mill etc 2012年4月30日 Plant Process Flow Diagram 2 Samanta et al [2] worked on the "automation of a cement process plant" with the aim of eliminating the challenges associated with the manual operation of the plant(PDF) Process Automation of Cement PlantDownload scientific diagram Cement Manufacturing Process Flowsheet (Flow Chart) from publication: Cement Manufacturing – Process Modeling and TechnoEconomic Assessment (TEA) using SuperPro Cement Manufacturing Process Flowsheet (Flow Chart)2015年9月17日 6 00 Limestone Quarry and Crushing plant The major raw material for cement production is limestone The limestone most suitable for cement production must have some ingredients in specified quantities ie, calcium carbonates, silica, alumina, iron,etc Belt Conveyors The quarried raw material is transported to the cement plant, using mechanical conveying Cement Production Process PPT SlideShare
.jpg)
Manufacturing process Lafarge
The cement manufacturing process starts from the mining of raw materials that are used in cement manufacturing, mainly limestone and clays A limestone quarry is inside the plant area and a clays quarry is as far from the plant area as 25 km2022年11月9日 Cement plant mainly consists of large duct with blowers (FD ID Fan) where conventional flow measurement is done with Differential pressure sensor as primary elements such as Averaging Pitot tube, Orifice, Aerofoil etc which are prone to clogg, insensitive to changes in flow velocity, and considerable pressure drop occurs with lower accuracy is now Advanced Air Process Gas Flow Monitoring in Cement Plants1971年8月17日 116 Portland Cement Manufacturing 1161 Process Description17 Portland cement is a fine powder, gray or white in color, that consists of a mixture of hydraulic cement materials comprising primarily calcium silicates, aluminates and aluminoferrites More than 30 raw materials are known to be used in the manufacture of portland cement, and these116 Portland Cement Manufacturing US EPA2019年8月27日 The major raw materials used as a source of CaO for cement manufacturing are limestone, chalk, marl, etc These raw materials by virtue of their natural occurrence contains other mineral impurities eg, MgO, SiO 2, Al 2 O 3, Fe 2 O 3, alkali compounds, and sulfidesThese impurities play an important role to influence the cement manufacturing Cement Manufacturing and Process Control SpringerLink
.jpg)
Analysis of material flow and consumption in cement production process
2016年1月20日 The LN cement plant, located in the southwest of Shandong Province, was considered as a case study for the mass flow and balance analysis This cement plant operates on a dry process line with a fivestage suspension preheater and an inline precalciner The kiln is 4 m in diameter and 60 m in length2024年5月23日 The belt conveyor in cement plant operations is an essential component that significantly contributes to the efficiency, safety, and environmental sustainability of the cement manufacturing process By providing a seamless, reliable, and costeffective method for transporting materials, belt conveyors play a vital role in ensuring the smooth operation of Optimizing Material Flow with Belt Conveyor in Cement Plant2023年11月1日 Cement plant process technology and condition Power and fuel costs Availability of excess heat Availability of materials Space requirements Schematic flowsheet of a multistage grinding plant for the production of Portlandcements including 3 The cement plant of tomorrow ScienceDirectcement plants with wet process kilns is 305006, constitute the core of a portland cement plant Process flow diagram for portland cement manufacturing 1164 EMISSION FACTORS 11/21 Table 1161 Source Classification Code (SCC) for Portland Cement Manufacturing116 Portland Cement Manufacturing US Environmental
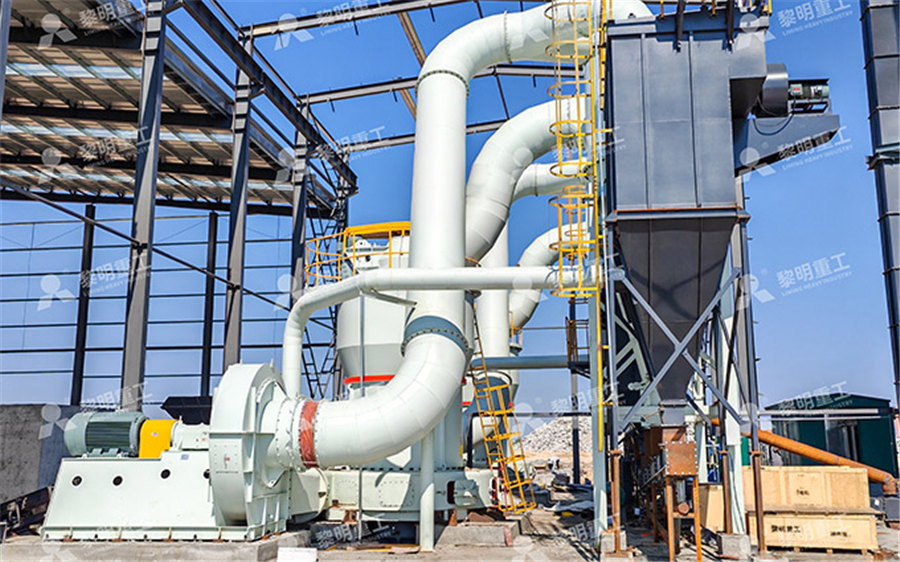
Cement Manufacturing Process and Its Environmental Impact
2023年7月10日 Cement manufacturing is a significant industrial activity that plays a vital role in the construction sector However, the process of cement production is associated with various environmental The use of fossil fuels such as coal, natural gas, and oil is common in cement production, both as a fuel for the kiln and as a source of heat for other parts of the process which leads to CO2 emitted by combustionHowever chemical reactions happening in the kiln (calcination) are also responsible for up to 60% of the total of emissions of the cement production process [PCA]Cement Production Demystified: StepbyStep Process and 2017年10月20日 1 Introduction Nowadays, cement manufacturing is an energyintensive industry The energy costs of cement industry are about 40% of the product cost that indicates that this sector is one of the biggest CO 2 emitter The global anthropogenic CO 2 emission of cement industry is approximately 5% []The International Energy Agency reported in 2011 that Heat Integration in a Cement Production IntechOpenThe 6 Main Process Fans in Cement factory IF YOU WORK IN A CEMENT PLANT AND YOU NEED COURSES AND MANUALS LIKE THIS MANUAL AND BOOKS AND It is considered as the ‘lung’ of the clinker burning system Without the aid of induced draft fan, the gas flow and combustion of In addition to these key process fans, cement industry also has The 6 Main Process Fans in Cement factory
.jpg)
Cement Production Process Cement Manufacturing Process AGICO CEMENT
2020年8月25日 Before you send inquiry Please provide us with project information as much as possible: For a complete project: the material availability, the required output capacity, the process technology, your budgetary and financing status, the estimated starting time, etc For singular machinery: the model, the capacity, your budgetary information, other requirements, etcDownload CAD block in DWG General plan of the cement manufacturing process it is a vertical grinding system (65357 KB)Cement plant in AutoCAD Download CAD free (65357 KB) Bibliocad2015年8月1日 This cement plant operates on a dry process line with a fi vestage suspension preheater and an inline precalciner The kiln is 4 m in diameter and 60 m in lengthAnalysis of material flow and consumption in cement production processA development of this process is the 'precalciner' kiln Most new cement plant is of this type The principle is similar to that of the dry process preheater system but with the major addition of another burner, or precalciner With the additional Manufacturing the cement kiln Understanding
.jpg)
Chapter 4 Cement Manufacturing and Process Control
Cement Manufacturing and Process Control 41 Cement Manufacturing: Basic Process and Operation To design the Refractory for the lining of different equipments in a cement plant, it is necessary to understand the total operational process of a cement plant in depth It is necessary to know the conditions prevailing in different equipments and theAGICO supplies cyclone preheaters for the new dry process of cement manufacturing Project Cases; Solutions Menu Toggle Factory Scales Menu Toggle Mini Cement Plant Hot Sale; Cement Plant 700 ~ 2000tpd; Cement Cement Plant Cyclone PreheaterLearn about our cement grinding process and plant stages for high quality cement Learn about our cement grinding process and plant stages for high quality cement Amrit Support About Amrit Support; Services; Activities; Corporate Annual Return FY 202021; FY 202122; FY 202223;Cement Grinding Unit Process High Quality Cement Grinding Plant2020年9月26日 Cement Manufacturing Process: ement is a material which is used to bind other materials together Binding means it has an effect of gluing the substances Coriolis Flow Transmitter Working November 6, 2020 Instruments Boiler Drum Level Control November 3, 2020 Instruments Deluge Valve System WorkingCement Manufacturing Process Chemical Engineering World
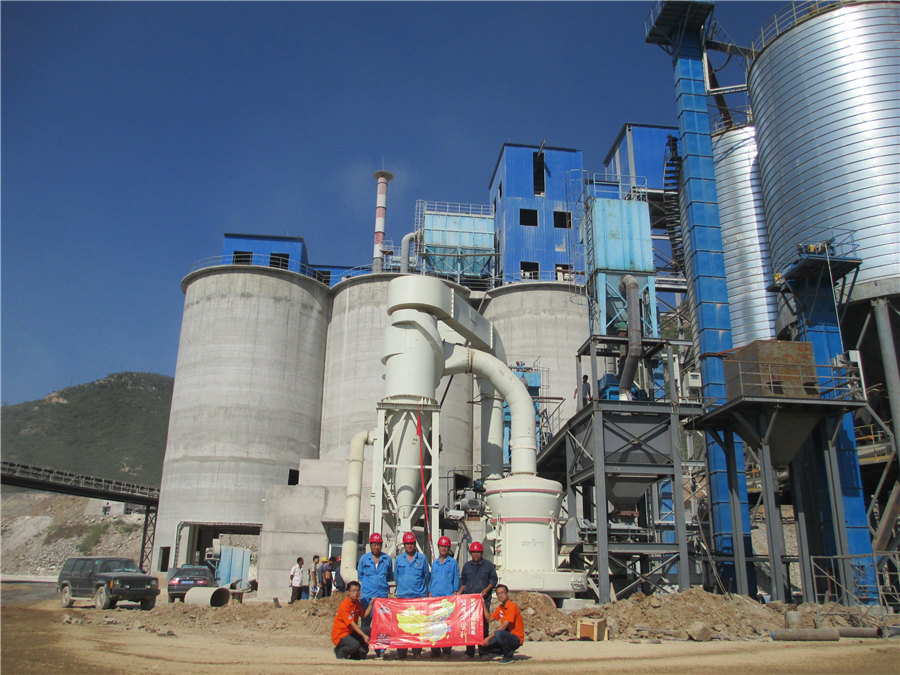
Cement processing equipment Qlar
For a new plant, this approach delivers many relevant savings Your specialist partner every step of the way With more than 80+ years of experience working with the world’s leading cement producers, we have the deep application knowhow you can count on to tailor plantwide solutions to meet your most exacting needsPROCESS CALCULATIONS AND FLOW DIAGRAMS PROCESS SELECTION AND EQUIPMENT SIZING ANALYSIS OF OPTIMUM MATERIAL STORAGE REQUIREMENTS DEVELOPMENT OF COSTEFFECTIVE ENGINEERING SOLUTIONS be installed in the St Mary’s Cement plant as part of the plant upgrade project Votorantim North America St PROCESS ENGINEERING FOR THE CEMENT LIME INDUSTRIES While each cement plant may differ in layout, equipment, and appearance, the general process of manufacturing portland cement is the same: crushed limestone and sand are mixed with ground clay, shale, iron ore, fly ash and alternative raw materials The clinker comes out of the kiln redhot with a consistency like a lava flowHow Cement is Made Portland Cement Association2020年2月15日 The cement production in the MCC plant is based on the dry process technology, and according to the preliminary energy audit, the thermal energy consumption in MCC is about 35 GJ per ton of produced clinker The main source of energy in the plant is the coal that is obtained from Tanzania (Tancoal) and from Malawi (both, Mchenga and Erland)Parametric Studies of Cement Production Processes John 2020
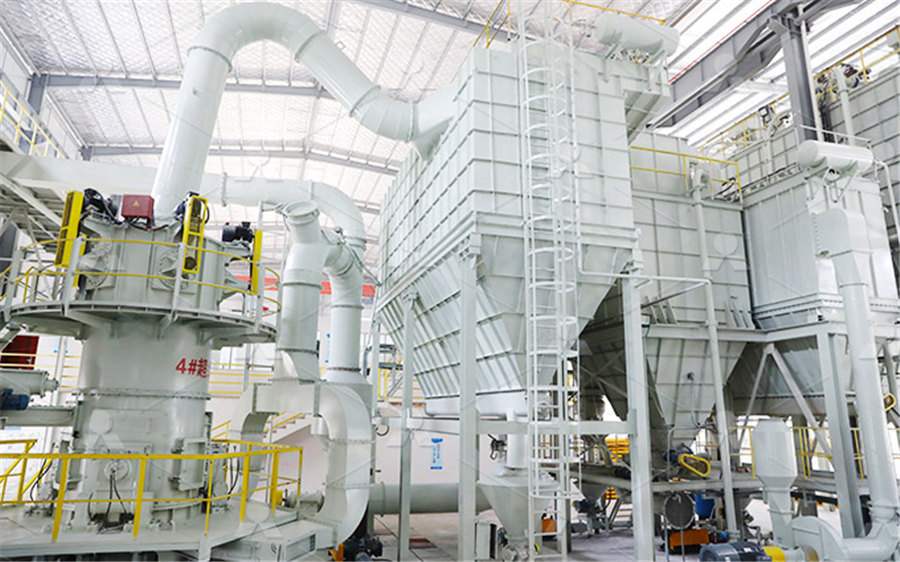
The Cement Plant Operations Handbook 6th Edition from
Fully revised and updated with improved content, the new Sixth Edition of the Cement Plant Operations Handbook is now available Covering some 300 pages, the cement industry’s favourite technical reference book offers indepth information on the various aspects of cement production