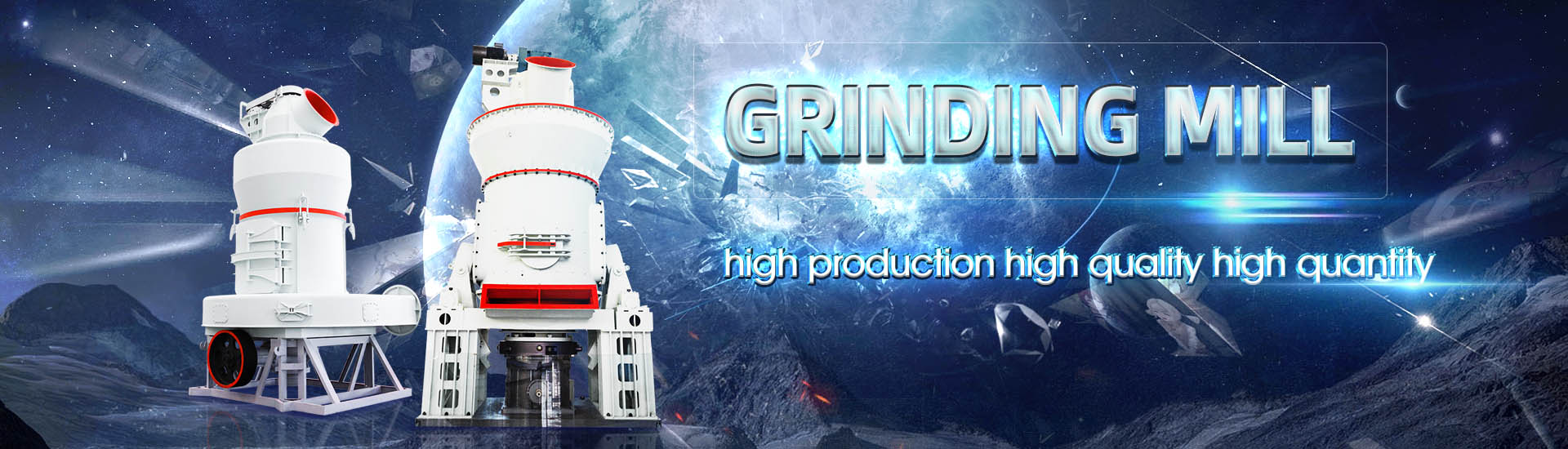
Main distribution of crushing and grinding equipment
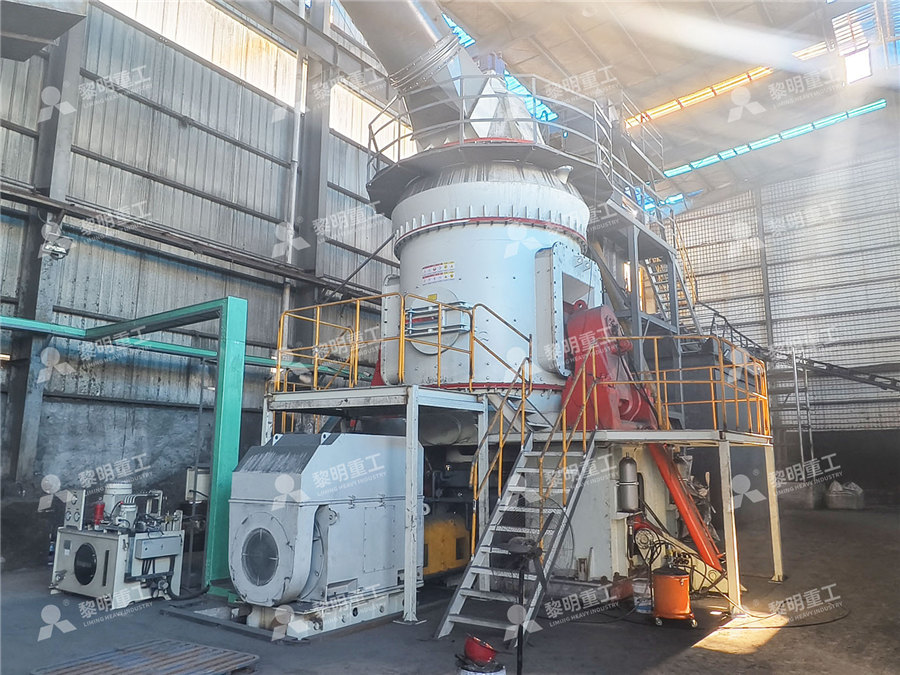
Crushing Plant an overview ScienceDirect Topics
Crushing is the first mechanical stage in the process of comminution in which a principal objective is the liberation of the valuable minerals from the gangue Crushing is typically a dry operation Grinding tools are used in automated or manual settings A life cycle inventory of the grinding process includes nonproduct material (metalworking fluid, tooling), incoming and machined Grinding Equipment an overview ScienceDirect Topics2023年5月5日 Grinding equipment is a type of mineral processing equipment that further reduces the ore particle size of crushed massive or granular ore to powdery material by Grinding Equipment SpringerLinkThe unit operation of the size reduction or comminution of solids by crushers and mills is a very important industrial operation involving many aspects of powder technology It is estimated Size Reduction of Solids Crushing and Grinding Equipment
.jpg)
Crushing Equipment SpringerLink
2023年5月3日 According to the structure and working principle, the commonly used crushing equipment can be divided into jaw crushers, gyratory crushers, cone crushers, roller crushers, As a rule, size reduction (comminution) raw materials are effected in at least two main stages: crushing (primary reduction) and grinding (fine reduction) Generally speaking, crushing Everything you need to know about Crushers in Cement industry2023年6月30日 This article presents a systematic review of the task of improving the energy efficiency of crushing units This is achieved by studying modelling methods and results, the automation ofModeling and Improving the Efficiency of Crushing 2022年6月24日 Grinding is a manufacturing process which significantly contributes in producing high precision and durable components required in numerous applications such as aerospace, (PDF) A comprehensive review on the grinding process:
.jpg)
Selecting the right type of crushing equipment Quarry
2016年4月7日 Most crushers used for aggregate production can be categorised as one of three main types: Compression crushers – which squeeze the material until it breaks Impact crushers – which use the principle of rapid impact to Mechanical Crushing and Grinding Oleg D Neikov, in Handbook of NonFerrous Metal Powders, 2009 Crushing and Grinding Equipment A major objective of comminution is to liberate minerals for concentration processes Another objective is to Grinding Equipment an overview ScienceDirect TopicsPresented simulation of the crushing and grinding circuit demonstrated the ability to consider many variables simultaneously Throughout the paper, process streams sampling results for particle size distribution were compared to the simulation results and main equipment characteristics used as input for the simulation model were PARISON OF SIMULATION MODEL AND PLANT DATA OF A CRUSHING GRINDING The unit operation of the size reduction or comminution of solids by crushers and mills is a very important industrial operation involving many aspects of powder technology It is estimated that mechanical size reduction of rocks, ores, coals, cement, plastics, grains, etc involves at least a billion tons of material per year in the United States alone The operation ranges in scale, for a Size Reduction of Solids Crushing and Grinding Equipment

Types of Crushers: Choosing the Right One for Each Stage
2024年7月17日 Crushing is a multistage process that includes primary crushing, secondary crushing, and tertiary crushing Different types of crushing equipment are used at each stage to meet various crushing requirements Primary crushing breaks down large raw materials into mediumsized pieces for easier handling in subsequent processes%PDF16 %âãÏÓ 4215 0 obj > endobj 4235 0 obj >/Encrypt 4216 0 R/Filter/FlateDecode/ID[87C03FABF6FB2246BC4F9AB649B4B217>]/Index[4215 26]/Info 4214 0 R/Length 101 AusIMM – Leading the way for people in resources2024年3月12日 The ultrafine grinding machine for dolomite powder has comprehensive mechanical crushing performance such as roller pressing, grinding, and crushing The equipment can form an independent and complete production system with strong systematicity, from the crushing, conveying, and powdermaking to the collection, storage, and packaging of finished Dolomite Crushing Process And Grinding Equipment2023年10月30日 The selection and design of crushing equipment in the mineral processing industry are influenced by several key factors, all of which are critical for achieving efficient and effective ore processing Chief among these factors is the material's inherent characteristics The hardness, abrasiveness, moisture content, and size distribution of the ore significantly impact The selection and design of Crushing equipment Performance
.jpg)
Shenyang Sanland Crushing And Grinding Equipment
Shenyang Sanland Crushing And Grinding Equipment Manufacture Co, Ltd China Manufacturer with main products:Crusher Jaw Crusher ,Cone Crusher ,Impact Crusher ,Ball Mill ,Gyratory Crusher a production distribution company for largesize crushers, mineral processing, art of treating crude ores and mineral products in order to separate the valuable minerals from the waste rock, or gangue It is the first process that most ores undergo after mining in order to provide a more concentrated material for the procedures of extractive metallurgyThe primary operations are comminution and concentration, but there are other Mineral processing Metallurgy, Crushing Grinding Britannica2024年1月1日 It mainly includes crushing process control, crushing appliance fault diagnosis, and automatic distributing control Crushing Process Control To ensure the continuous, stable, and safe operation of the ore crushing production process, it is necessary to monitor the running state and parameters of key equipment (such as crusher and belt conveyor) in real time for MeasurementControl for Crushing and Screening Process2022年10月4日 21 Energy Rock drilling, blasting, and comminution (crushing and grinding) consume a vast amount of energy in hard rock mines As mentioned in Sect 1, statistics from hard rock mines indicates that drilling and blasting consumes 2% and comminution does 53% of the total energy input in the whole production chain from mining to mineral processing (Spathis Reduction of Fragment Size from Mining to Mineral Processing: A
.jpg)
Crushing and grinding (Mineralogy) Fiveable
Particle size distribution is critical in determining how effectively minerals can be separated during processing, making crushing and grinding essential steps The choice of equipment for crushing and grinding depends on the type of material being processed and the desired particle size for subsequent processing stepsMechanical parts for Metso® and Sandvik® crushing machines and grinding equipment Quality parts for impact and cone crushers, screens, conveyor belts Experts in distribution of multibrand parts and services for quarrying and mining installations Phone : +33 4 90 39 39 55 Email : clientshms@haladjian The Group The Haladjian Mechanical parts for mining, crushing and grinding equipment2019年10月8日 The crushing and grinding operations are an important part of the processing of mineral resources, and it is also operation with high investment and high energy consumption In the case of metal mines, equipment investment in crushing operations accounts for 65% to 70% of the total plant value, power consumption is about 50% to 65%, and steel consumption is as Crushing and Grinding Process JXSC Machine2023年5月5日 Grinding equipment is a type of mineral processing equipment that further reduces the ore particle size of crushed massive or granular ore to powdery material by medium (such as steel ball, steel bar, and gravel) and the impact, shearing, and grinding effects of oreGrinding Equipment SpringerLink
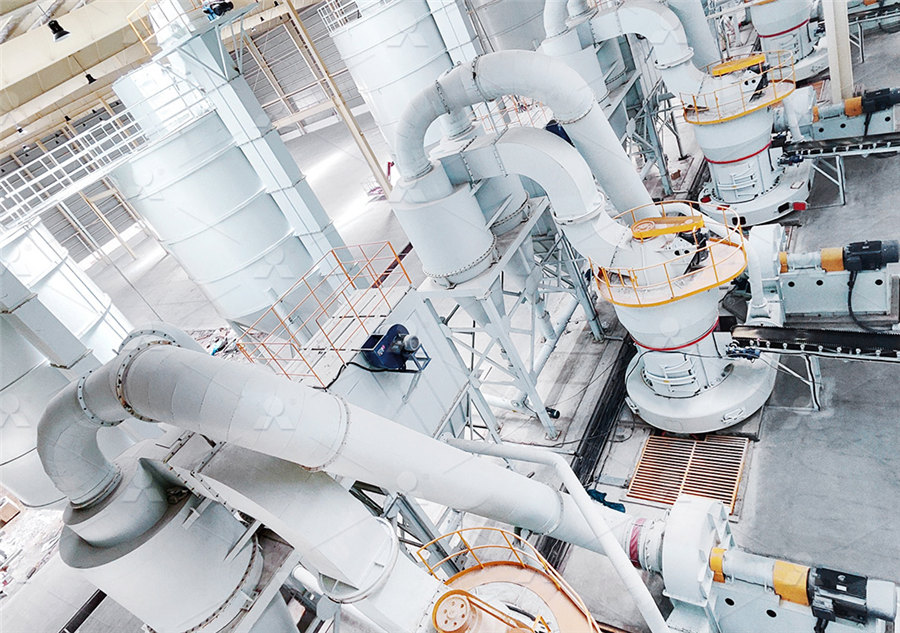
Impact of HPGR operational pressing force and material moisture
2024年9月1日 The paper concerns investigations on potential energy savings and breakage effectiveness, resulting from the application of HPGR device into ore mineral processing circuit A series of laboratory experiments in HPGR for sulphide copper ore was carried out at four values of pressing force in the press and four levels of moisture of the feed material (according to 2018年11月19日 This can be taken under the consideration of unique method of extractive metallurgy in which main steps are known 5Crushing and grinding equipment Figure 3 2 Size distribution of (PDF) Comminution in mineral processing ResearchGatecrushing, and then describes the working principle and structure of straw slimer, and discusses the research status of fine grinding mill, and the main problems of the crusher equipment are discussed, and finally prospects the development trend of agricultural straw fine crushing equipment II Straw Principle and Structure of Fine Crusher The research progress of agricultural straw crushing machinery 2022年4月20日 Medium and fine crushing: The coarsely crushed limestone is then subjected to medium and fine crushing We can choose impact crusher for equipment Some stones use cone crusher for secondary crushing, but the hardness of limestone is not high Considering the problem of investment cost, we choose impact crusher Crusher is more costeffectiveLimestone crushing and grinding production line SBM Ultrafine
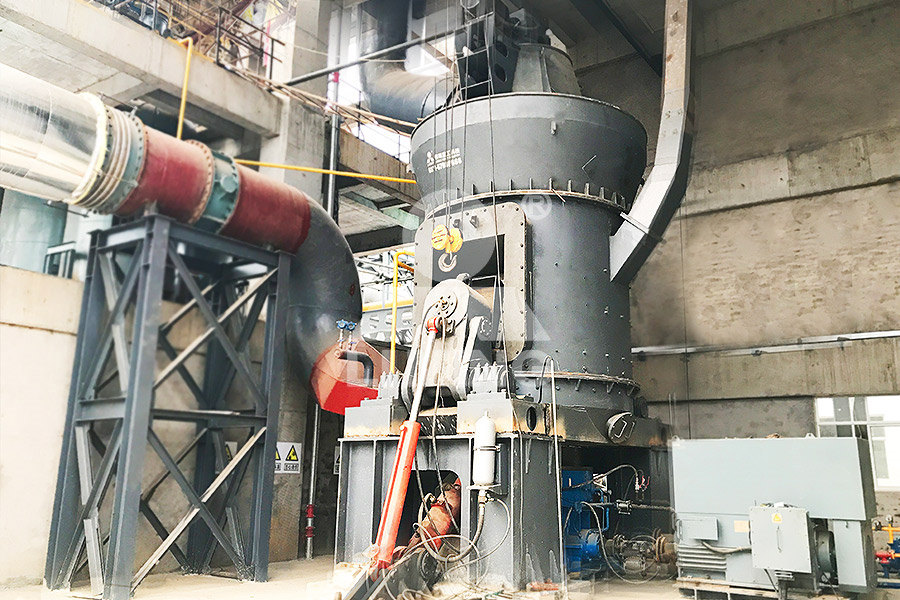
(PDF) A comprehensive review on the grinding process:
June 2022; ARCHIVE Proceedings of the Institution of Mechanical Engineers Part C Journal of Mechanical Engineering Science 19891996 (vols 203210) 236(2):年10月1日 The crushing roller is one of the main parts of a highpressure grinding roller, which is a type of highly efficient ore crushing equipment In the work reported in this paper, a kind of assembled 3D design and analysis of the crushing roller of a highpressure This paper does not examine quantitatively other beneficial results of improved blasting However, these exist and they include: 1 Increased productivity in crushing and grinding 2 More undersize that bypasses stages of crushing 3 Reduced consumable wear The Effects of Blasting on Crushing and Grinding Efficiency and 2021年7月22日 (1) The density, diameter, and filling amount of the medium The density and particle size of the medium affect the particle size of the product and the energy utilization rate of the mill Studies have shown that when using a stirring mill to grind talc, the highdensity zirconia balls (631g/cm3) have a higher crushing efficiency than the lowdensity glass balls (25g/cm3)Characteristics and Application of Wet Superfine Crushing

SIZE REDUCTION BY CRUSHING METHODS By ResearchGate
Crushing and grinding are the two primary comminution processes Crushing is normally carried out on the "runofmine" ore The grinding process which is normally carried out after crushing, may 2024年4月26日 The main objectives of screening are to classify the ore into different size ranges and remove any oversize or Advances in technology have led to the development of more efficient and specialized crushing and screening equipment, enabling finer control over the size distribution of the crushed ore and improving overall process Iron Ore Processing: From Extraction to Manufacturing2017年8月24日 Comminution commonly involves crushing and grinding The distribution of particles according to their size can then be indicated as the proportion of the particle population Moreover, they are also encouraged in the quarry industry due to the improved product shape There are two main impact crusher equipments: hammer Mineral Processing SpringerLink2023年6月3日 It mainly includes crushing process control, crushing appliance fault diagnosis, and automatic distributing control Crushing Process Control To ensure the continuous, stable, and safe operation of the ore crushing production process, it is necessary to monitor the running state and parameters of key equipment (such as crusher and belt conveyor) in real time for MeasurementControl for Crushing and Screening Process
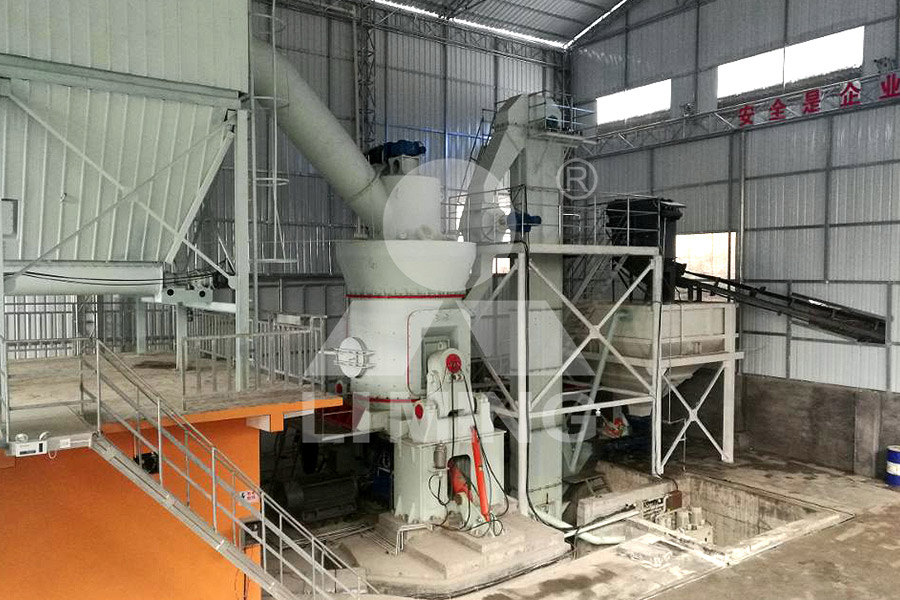
Crushing and Grinding Semantic Scholar
Semantic Scholar extracted view of "Crushing and Grinding" by L Work Skip to search form Skip to main content Skip to account menu Semantic with special attention paid to the approximation of the particle size distribution of crushing products by means of Weibull, lognormal, and logistic functions Expand 6 [PDF] Save2023年11月21日 Amid the sweeping advance of Industry 40 and Smart Manufacturing, the deployment of large rotating machinery equipment, including semiautogenous mills, ball mills, and coal mills, is expanding across a multitude of sectors 1 This expansion has concurrently amplified the focus on the health and performance monitoring of these substantial apparatusAdvances in vibration analysis and modeling of large rotating 2017年2月17日 When making comparisons of the efficiencies of different grinding and crushing machines it is desirable to be able to estimate the work actually done in crushing the ore from a given size of feed to a given size of product, the screen analysis of both feed and product being determined Messrs Klug and Taylor, in a paper on this subject, published in the monthly Difference between Crushing and Grinding 911MetallurgistIn this context, the term average size depends on the method of measurement In the industry, screening or sieving is widely used to evaluate particle size distribution in granular materials and powders In case of coarse crushing the Size Reduction1: Grinding – Unit Operations in Food
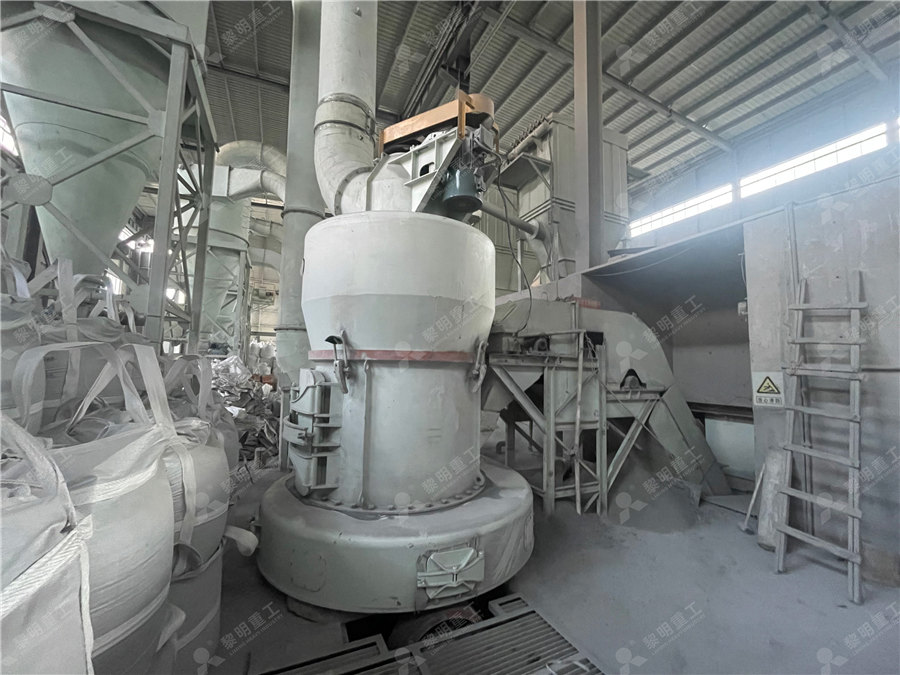
Comminution SpringerLink
2015年2月2日 In crushing circuits sensors are implemented to measure bins and chute levels, frequency of feeders, lubrication flow rate and temperature, crusher power draw, mass flow rate, particle size distribution (not common), etc In grinding circuits the sensors measure parameters such as: pulp density, volumetric flow rate, sump levels, cyclone 2014年8月21日 There are three main steps in designing a good crushing plant: process design, equipment selection, and layout The first two are dictated by production requirements and design parameters, but the layout can reflect the input, preferences and operational experience of a number of partiesSetting up of crushing plant: design and layout considerations2021年7月6日 Crushing and grinding are known as comminution procedure where the major operations are intensively related to liberation and reduction of particle size by means of different minution a Heart of Mineral Processing ResearchGate2022年1月1日 An additional crushing effect occurs between the compressed particles, resulting in less wear of the liners This is also called interparticular crushing The gyratory and cone crushers are equipped with the setting adjustment system, which adjusts css and thus affects product size minution and classification technologies of iron ore
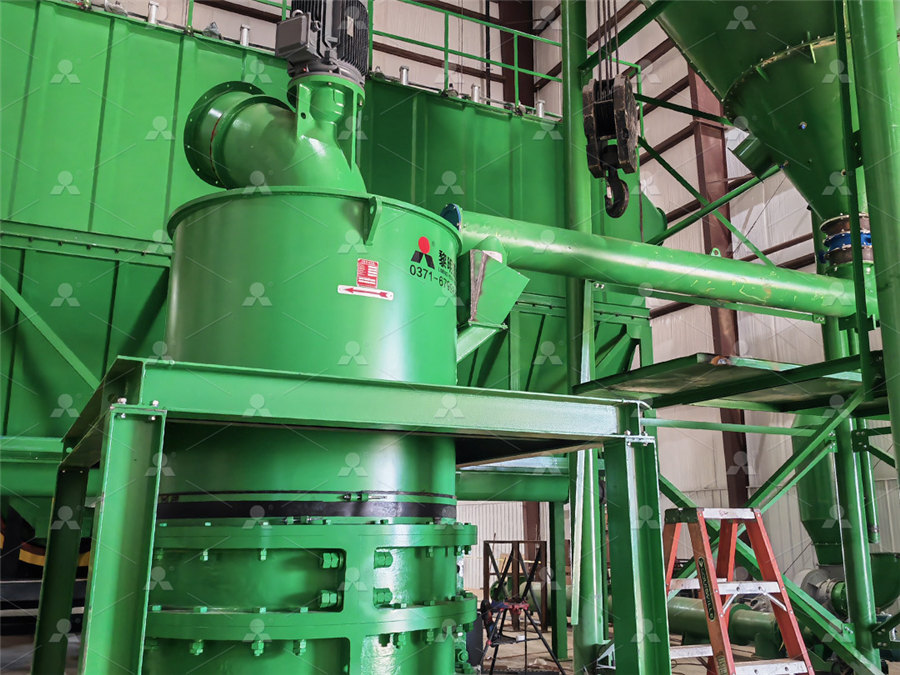
Gold Extraction Recovery Processes 911Metallurgist
2016年2月29日 SAG mills, rod mills and ball mills are the classical pieces of grinding equipment employed in gold recovery plants There is an increasing trend to employ SAG mills (semiautogenous mills) in place of secondary and tertiary crushing and primary grinding The most common type of rod mill is the overflow mill There are two typed of ball mills used32 Crushing of Bauxite The equipment selected for the crushing area is chosen based on the physical characteristics of the raw bauxite and the capacity rates required Typical crusher types evaluated for a specific project include Jaw Crushers, Cone Crushers, highspeed ImpactorsorHammermills,andlowspeedSizersThecrushingareamayalsoincludePhysical Bauxite Processing: Crushing and Grinding of Bauxite2023年4月26日 Work, improve equipment operation efficiency, and increase efficiency and income for mining enterprises This article briefly analyzes the causes of crushing and grinding equipment failures Crushing Equipment Currently, the commonly used crushing equipment includes jaw crushers, cone crushers, and impact crushersCrushing and Grinding Equipment Common Faults and Solutions2003年1月1日 and the crushing and grinding equipment employed, Four main objectives involving operational costs, effects of each size distribution parameter on crushing performance were discussed(PDF) The Effects of Blasting on Crushing and Grinding