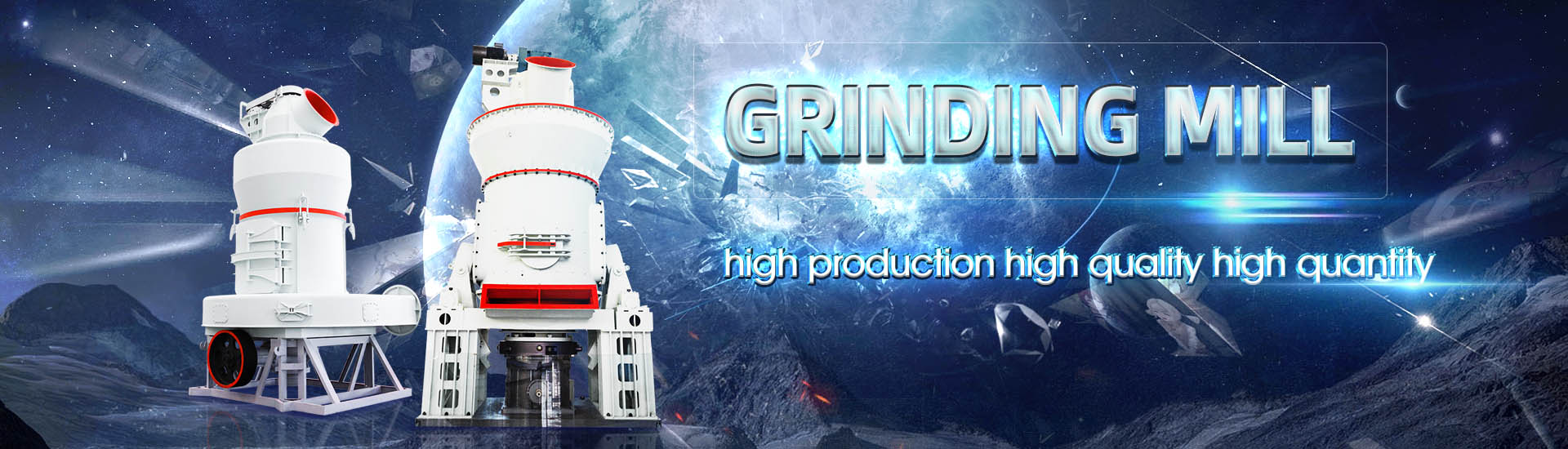
Where to use electrolytic aluminum waste slag mill ore mill
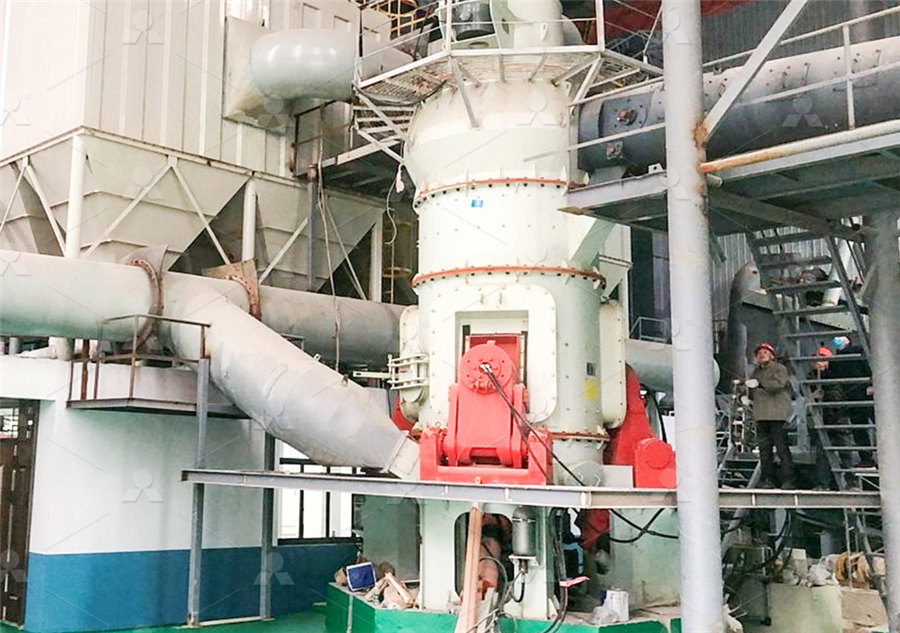
The recycling of carbonrich solid wastes from aluminum
2024年5月23日 Here, we review carbonrich solid wastes with focus on sources and hazards, detoxification, separation, recovery, recycling and disposal Treatment techniques include 2023年4月25日 This article analyzes and summarizes the composition and hazards of the overhaul slag and the current development status of domestic and international electrolytic Research Progress of Electrolytic Aluminum Overhaul Slag Disposal2023年9月22日 To extract lithium from electrolytic aluminum slag, the waste residue must first be dried to reduce its moisture content to less than 5% Then, it is pulverized by an aluminum What kind of mill is best for grinding electrolytic aluminum slag2024年2月1日 The electrolytic aluminum industry generates a large amount lithium (Li)containing electrolytic aluminum slag (EAS) annually, and this can result in severe Efficient lithium recovery from electrolytic aluminum slag via an
.jpg)
Recovery of aluminum from waste aluminum alloy by low
2020年8月1日 Here, we discuss the influence of different processing parameters on electrolytic refining of aluminum alloy and investigate the mechanism of extracting Al from coarse AlSi 2023年9月1日 This study employed hydrometallurgical processes to selectively leach lithium from Licontaining aluminum electrolyte slag, using sodium carbonate solution as the leaching agent A notable leaching efficiency of Clean Process for Selective Recovery of Lithium 2022年10月10日 In this work, electrolytic aluminum carbon anode slag was separated by flotation Using the selectivity index ( SI) as an indicator, the influencing factors of the carbon Recovery of carbon and cryolite from spent carbon anode slag of 2023年4月13日 Aluminium is produced by electrolysis using alumina (Al 2 O 3) as raw material and cryolite (Na 3 AlF 6) as electrolyte In this Hall–Héroult process, the energy consumption A comprehensive review of aluminium electrolysis and the waste
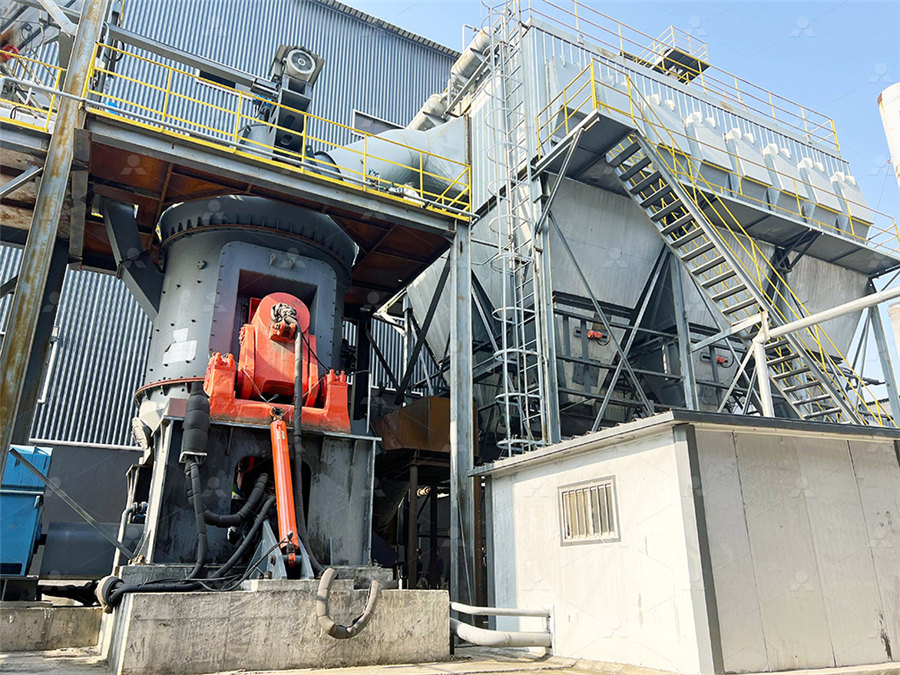
A solidstate electrolysis process for upcycling aluminium scrap
2022年4月13日 Here we propose a solidstate electrolysis (SSE) process using molten salts for upcycling aluminium scrap The SSE produces aluminium with a purity comparable to that of 2023年3月12日 The aluminum electrolysis industry continually and unavoidably produces hazardous solid waste in the form of carbon anode slag Carbon anode slag poses a serious environmental pollution risk, and (PDF) Recovery of Carbon and Cryolite from Spent 2022年10月9日 1 Department of Mining Engineering, Shanxi Institute of Technology, Yangquan, China; 2 Department of Mining Engineering, Balochistan University of Information Technology, Engineering and Management Sciences Recovery of carbon and cryolite from spent carbon 2013年6月1日 Electrolytic manganese residue (EMR) is added into ground granulated blastfurnace slag (GGBS) as an activator to prepare EMR–GGBS cement The effects of chemical activation, mechanical Preparation of electrolytic manganese residue–ground
.jpg)
The recycling and reuse of steelmaking slags — A review
2019年7月1日 Raw iron ore is characterized by the most abundant ironcontaining mineral found in the ore: magnetite (Fe 3 O 4), hematite (Fe 2 O 3), siderites (FeCO 3), and limonites (2Fe 2 O 3 3H 2 O) (Walker, 1986)All the impurities in iron ore (silica, alumina, titania, sulfur, and phosphorus) are collectively known as gangueAll iron ore that is mined has to be crushed, This study collected electrolytic aluminum waste cathodes, anodes, limestone and other materials After grinding the materials with an electric mill, 50 grams of electrolytic aluminum waste samples were sieved to 0075 mm The sample was then dried for 2 hours at a temperature of 110 °C in the dryer, then stored in aResearch on the Coprocessing of Mixed Electrolytic Aluminum Waste 2012年5月30日 Aluminium salt slag is toxic/hazardous waste (production: 200–500 kg/Al tonne) Chemical and mineralogical characteristics are presented Various processes for Al metal recovery and recycling of KCl/NaCl to smelting process are reported Preparation of value added products from the final NMR is discussedAluminium salt slag characterization and utilization – A review2012年5月30日 Aluminium salt slag is toxic/hazardous waste (production: 200–500 kg/Al tonne) Chemical and mineralogical characteristics are presented Various processes for Al metal recovery and recycling of KCl/NaCl to smelting process are reported Preparation of value added products from the final NMR is discussedAluminium salt slag characterization and utilization – A review
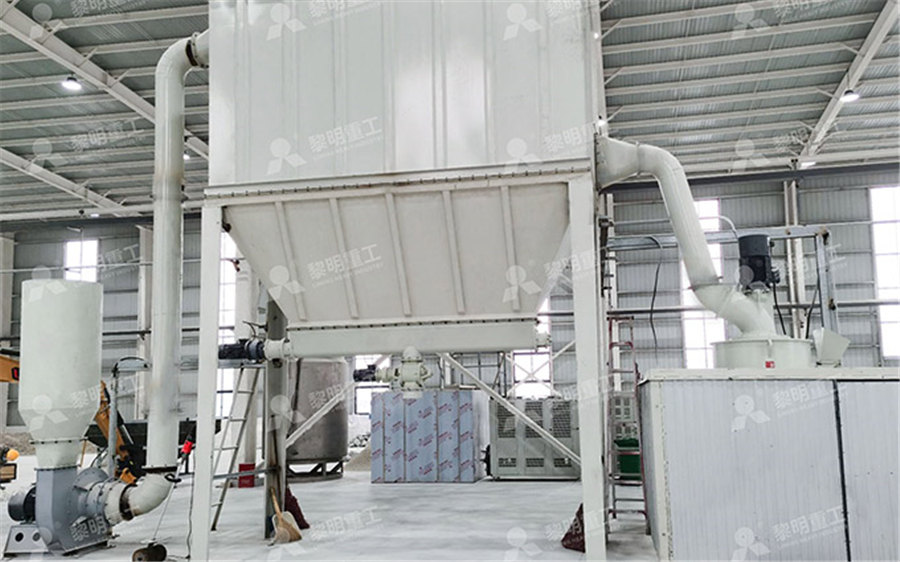
Study on Harmless and Resources Recovery Treatment Technology of Waste
2012年12月31日 During the treatment of spent cathode carbon from electrolytic aluminum, a large amount of fluoride containing wastewater is generated By adding different sodium source and aluminum source 2016年5月16日 Reduce, reuse, and recycle are important techniques for waste management These become significant for improving environmental and economic condition of industries Integrated steel industries are generating huge amounts of steel slag as waste through the blast furnace and Linz–Donawitz (LD) process Presently, these wastes are disposed by dumping in Sustainable Approaches for LD Slag Waste Management in Steel 2022年10月10日 The comprehensive recovery and utilization of electrolytic aluminum spent carbon anode slag (Hereinafter simplified as “carbon anode slag”) are therefore necessary Flotation is a physical separation method used to separate particles by using the difference in surface property of particles ( Chen et al, 2022 ; Ni et al, 2022 )Recovery of carbon and cryolite from spent carbon anode slag of Understanding Mine to Mill is presented in five parts Part A – Setting the Scene provides some definitions of Mine to Mill (M2M) and the historical background A chronology of Mine to Mill developments is followed by brief descriptions of the very wide range of Mine to Mill applications which have been implemented over the last 15 yearsUNDErsTaNDINg MINE TO MILL 911 Metallurgist
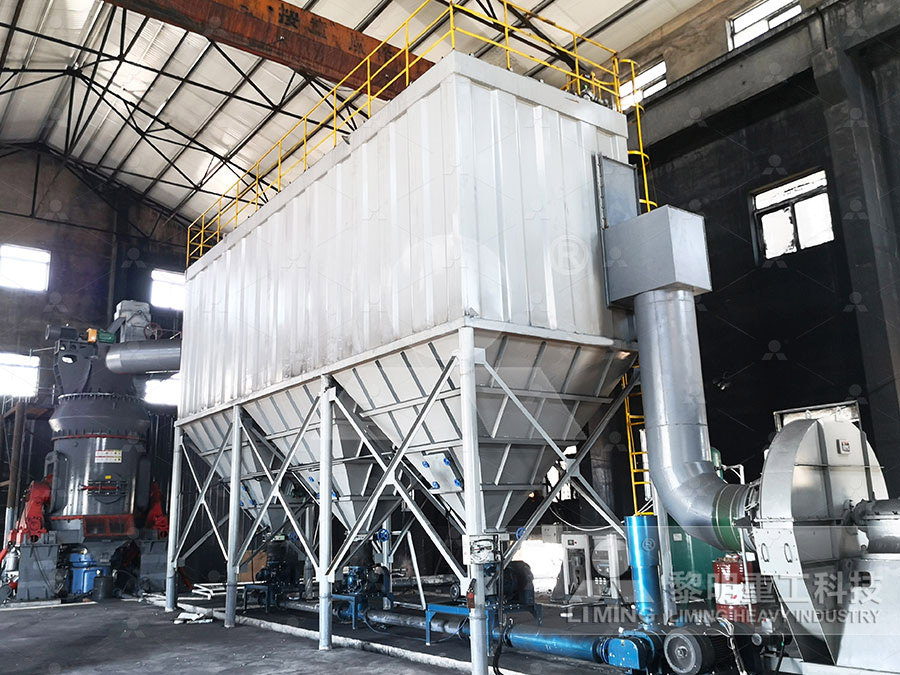
A comprehensive review of aluminium electrolysis and the waste
2023年4月13日 The actual consumption of aluminum was calculated based on a statistical analysis of China’s international trade of aluminumcontaining commodities (ACC) from 2008 to 2017 and data regarding 2012年4月1日 Adding mill scale as an ingredient into the iron ore sintering or pelletizing process is the main utilization approach for mill scale because of its high iron content and positional advantages [10 Recycling of steel plant mill scale via iron ore sintering plant2019年7月8日 The electrolytic aluminum waste, which would inevitably be produced from the electrolytic process in the aluminum industry, is harmful to environment and human bodyThermodynamic analysis of waste heat recovery of aluminum Aluminum ash is the slag produced in the production process of electrolytic aluminum or cast aluminum, which is a hazardous solid waste Aluminum ash contains aluminum element, aluminum oxide, aluminum carbide, silicon, fluoride, chloride and other components Among them, alumina accounts for more than 70%, which has a high recycling valueAluminum Ash Processing Aluminum Ash Recovery Aluminum
.jpg)
Utilisation of lead–zinc mill tailings and slag as paste backfill
2020年8月14日 Paste backfilling is an incipient underground mine backfill technology in India It facilitates maximum use of mill tailings with enhanced stability of the underground workings and minimises rehandling of water, as well as provides bulk disposal of mining solid waste Binder type and dosage plays an important role in paste backfill performance This paper highlights 2020年8月1日 Many researchers have studied the refining of aluminum by low temperature aluminium bath system Ali and Yassen (2018) used a different type of dissolvent to recover aluminum from industrial wastes This method was capable of obtaining aluminum of 99% purity by electrorefining of impure aluminum through the use of anhydrous AlCl 3 and NaCl as ionic Recovery of aluminum from waste aluminum alloy by low 2017年3月5日 Normalized CaO (MgO)SiO 2 (Na 2 O,K 2 O)Al 2 O 3 (Fe 2 O 3 ) phase diagram for various types of iron and steel slags Acronyms: blast furnace slag (BFS); basic oxygen furnace slag (BOFS (PDF) Iron and Steel Slags ResearchGate2023年8月2日 With global science and technology development, natural resources are gradually consumed and the demand for industrial materials is also gradually increasing []The recovery and recycling of limited resources have become an important topic that must be considered in the future development trend []Aluminum, as an important material, is particularly widely used in Sustainable Recovery of Fluorine from Waste Aluminum
.jpg)
Novel process for the extraction of lithium carbonate from spent
2020年12月1日 The rapid development of the electrolytic aluminum industry in China and the increasing demand for aluminum products have led to the development of many lowgrade bauxite mines with an average Li 2 O content of at least 058% (Wang et al, 2013)Due to the use of this lowgrade bauxite in the electrolytic aluminum process, the content of lithium in the ore operations consist of an open pit mine and an in siru leach operation, a lined leach pile containing ore mined from the open pit, and a solvent extraction/electrowinning facility The sulfide ore operations consist of an underground mine, a mill facility for copper and molybdenum flotation, and a smelter and electrolytic refinerySlag reprocessing: Magma Copper Company's San Manuel Facility2021年7月30日 Aluminum is the second mostconsumed metal in the world, only outranked by steel Primary aluminum is produced through the HallHeroult process1 In this process, alumina dissolves in a sodium cryolite melt, and aluminum is reduced at the aluminum liquid cathode pool while the anode products are significant amounts of \({\mathrm{CO}}{2}\) and other A Review of Secondary Aluminum Production and Its Byproductsaluminum processing, preparation of the ore for use in various products Aluminum, or aluminium (Al), is a silvery white metal with a melting point of 660 °C (1,220 °F) and a density of 27 grams per cubic cm The most abundant metallic element, it constitutes 81 percent of Earth’s crust In nature it occurs chemically combined with oxygen and other elementsAluminum processing History, Mining, Refining, Facts
.jpg)
Guide to Modern Smelting Processes CED Engineering
An ancient retort (see image above), used in ancient smelting processes, served several important purposes: 1 Ore Concentration: Retorts were used to concentrate the desired metal from ore The retort allowed for the separation of valuable metals 2023年3月12日 Aluminum has a variety of uses in the building, transportation, electric power, packaging, national security, and hightech industries due to its unique chemical and physical properties []Cryolitealumina molten salt electrolysis is mainly applied in modern industrial aluminum production [2,3]As the aluminum production process continues, a large amount of Recovery of Carbon and Cryolite from Spent Carbon Anode Slag2024年11月1日 Based on the above analysis, the following improvement suggestions were put forward: (1) In terms of electrode research, the use of inexpensive graphite electrodes had a good effect on steel slag treatment, and hightemperature ceramic electrodes and iron erosionresistant electrodes (ZrB 2) were gradually being exploited; (2) In terms of equipment, the existing Recent research progress on recycling metallurgical waste slag 2022年2月19日 It is estimated that the amount of the REEs lost in the waste molten salt slag accounts for 5% of the total amount of that used in the electrolysis process Rareearth molten salt slag generally contains about 20–60% of REEs, which is much higher than the rareearth content in other industrial wastes, such as phosphogypsum, bauxite residue (red mud), mine tailings, Recovery of RareEarth Elements from Molten Salt Electrolytic Slag
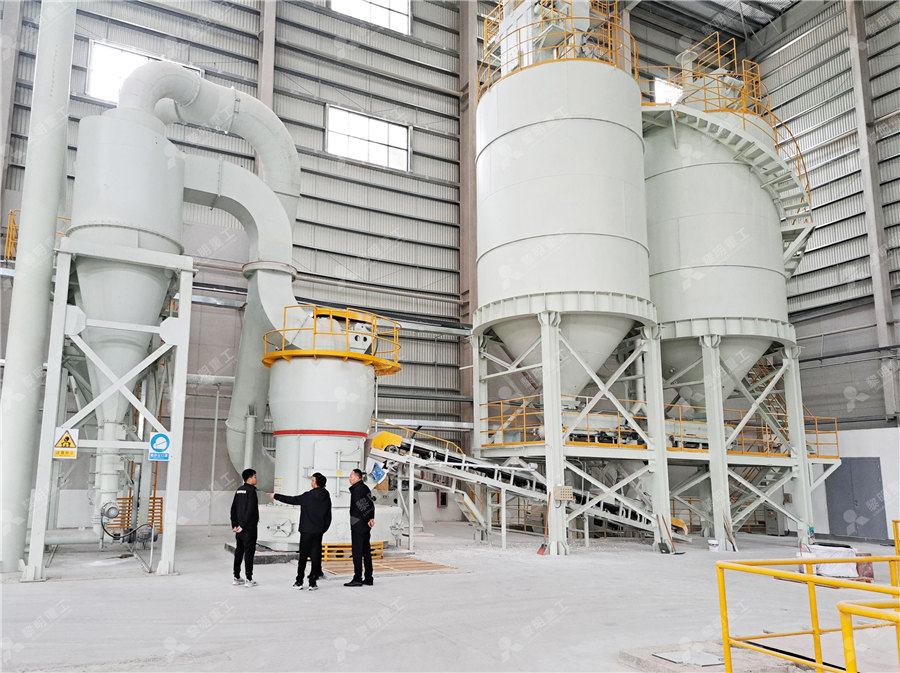
Stepwise extraction of lithium and potassium and recovery of
2024年6月29日 Aluminum electrolyte is a necessity for aluminum reduction cells; however, its stock is rising every year due to several factors, resulting in the accumulation of solid waste Currently, it has become a favorable material for the resources of lithium, potassium, and fluoride In this study, the calcification roasting–twostage leaching process was introduced to extract 2024年3月21日 at a ratio of 3:7 Beata Figiela et al [20] used mining wastes such as gangue to prepare geopolymers, exploring the possibility that these solid wastes could be used as materials in the wider construction industry Liet al [21] calcined electrolytic manganese slag mixedSynthesis of Electrolytic Manganese Slag Solid WasteBased 2022年9月1日 To better solve the waste pollution problem generated by the electrolytic manganese industry, electrolytic manganese slag as the main raw material, chromium iron slag, and pure chemical reagents (PDF) A study of the solidification and stability mechanisms of 2021年2月8日 The aluminum dross skimming from the smelting furnace is called primary aluminum dross, which is graywhite in appearance, mainly composed of a mixture of metallic aluminum and aluminum oxide, and the aluminum Here's what No One tells you about Comprehensive
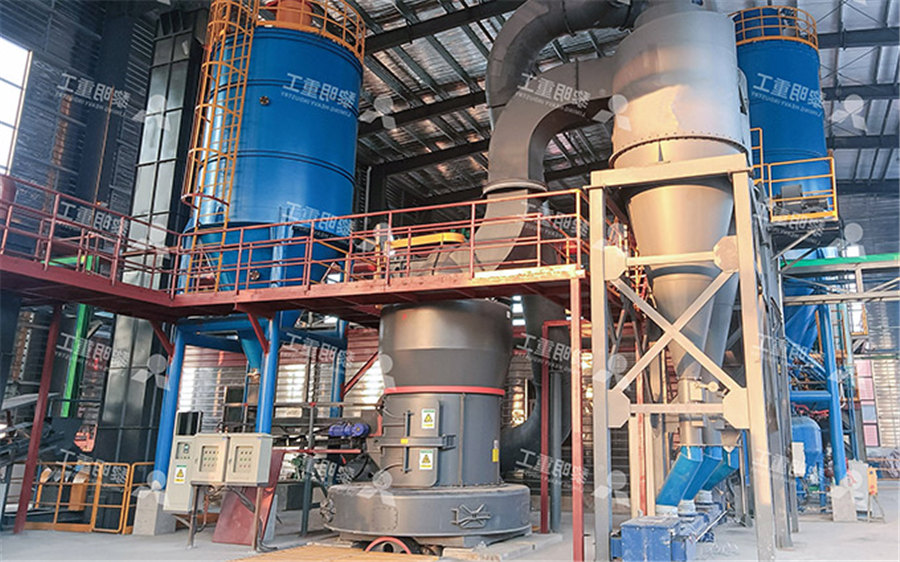
Enhancing concrete properties with steel waste: a comprehensive
2024年9月23日 This critical review systematically explores the innovative utilization of ground granulated blastfurnace slag (GGBS), steel slag (SS), and other steel waste in concrete, addressing a crucial research gap in predicting concrete properties with these materials By analyzing 97 publications, this review offers a comprehensive understanding of how these HCM’s HC1700 vertical pendulum Raymond mill, HLM series manganese carbonate vertical mill and other equipment have a high reputation in manganese ore enterprises all over the world market share, the following two types of electrolytic manganese powder grinding mill equipment will be introduced to youNews How to choose the electrolytic manganese powder grinding mill 2024年5月23日 The aluminum electrolysis industry continually and unavoidably produces hazardous solid waste in the form of carbon anode slag Carbon anode slag poses a serious environmental pollution risk, and The recycling of carbonrich solid wastes from aluminum electrolytic 2023年12月29日 Steel plants use mill scale in two ways: as an auxiliary material for sintering to improve sinter layer permeability and enhance wear resistance of ceramic materials; and as briquetted slagmaking agent for direct use in steelmaking to aid in slag removal, temperature regulation, and cost reductionHow to Turn Waste Mill Scale into Valuable Briquettes?
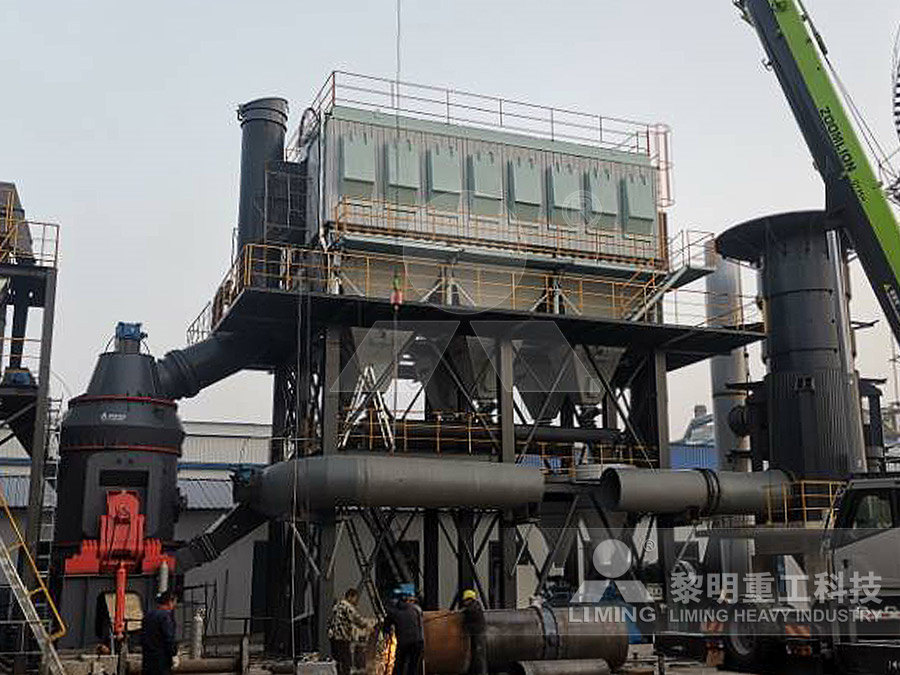
Hazardous aluminum dross characterization and recycling
2018年10月1日 In general, industrial production is accompanied by issues such as generation of waste and depletion of natural resources as well Industrial wastes accumulate over time bringing about critical environmental and public health detriments (Xiao et al, 2005)One of the most important and strategic industries producing hazardous wastes, is the aluminum production 2024年3月21日 manganese slag–solid wastebased geopolymer (SWGP) was evaluated by analyzing the mineral phase, morphology , and leaching concentration of the geopolymer 2Synthesis of Electrolytic Manganese Slag–Solid WasteBased 2024年2月1日 The electrolytic aluminum industry generates a large amount lithium (Li)containing electrolytic aluminum slag (EAS) annually, and this can result in severe environmental pollution and wasting of Li resources This paper proposes a method for recovering Li from the slag using AlCl 3 as the leaching agent The effects of the leaching temperature, AlCl 3 Efficient lithium recovery from electrolytic aluminum slag via an 2023年5月20日 Due to chemical corrosion and erosion by molten aluminum liquid and electrolyte, the carbon anode of the aluminum electrolytic cell would fall off into the electrolyte during the primary aluminum electrolysis process to produce spent anode carbon (SCA), which has been listed as one of the typical hazardous solid wastes in the National Hazardous Waste Regeneration of raw materials for aluminum electrolysis from
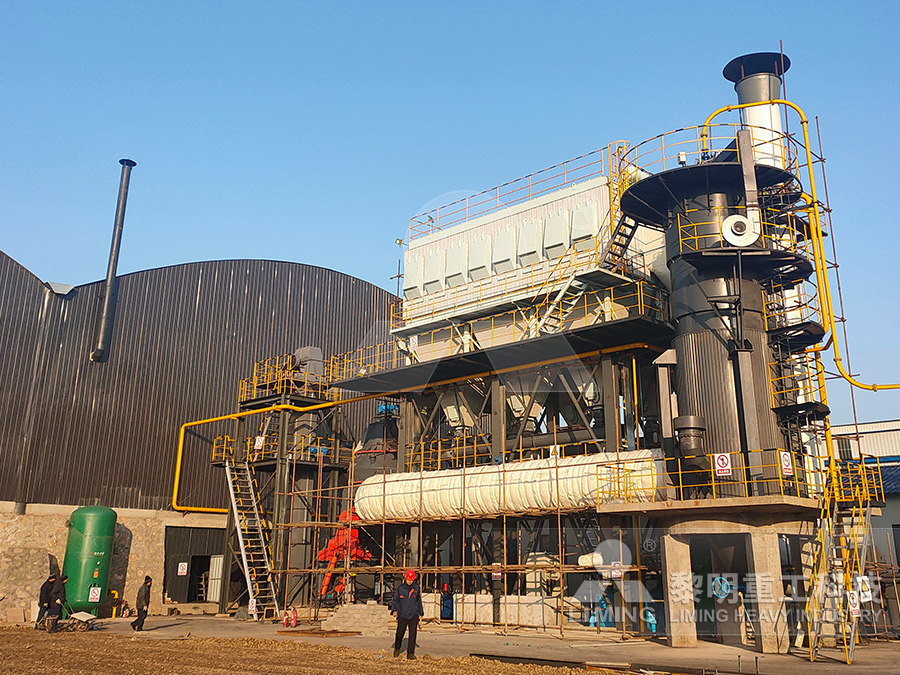
Fine Grinding as Enabling Technology – The IsaMill
Mill Diameter Mill Length Installed Power Mill Volume Power Intensity (m) (m) (kW) m3 (kW/m3) Autogenous Mill 10 45 6400 353 18 Ball Mill 5 64 2600 126 21 Regrind Ball Mill 32 48 740 39 19 Tower Mill 25 25 520 12 42 IsaMill 13 3 1120 3 280 3 3) 23/m) Ball Mill Tower Mill IsaMill (m Power Intensity Media Size No Balls / m Surface Area