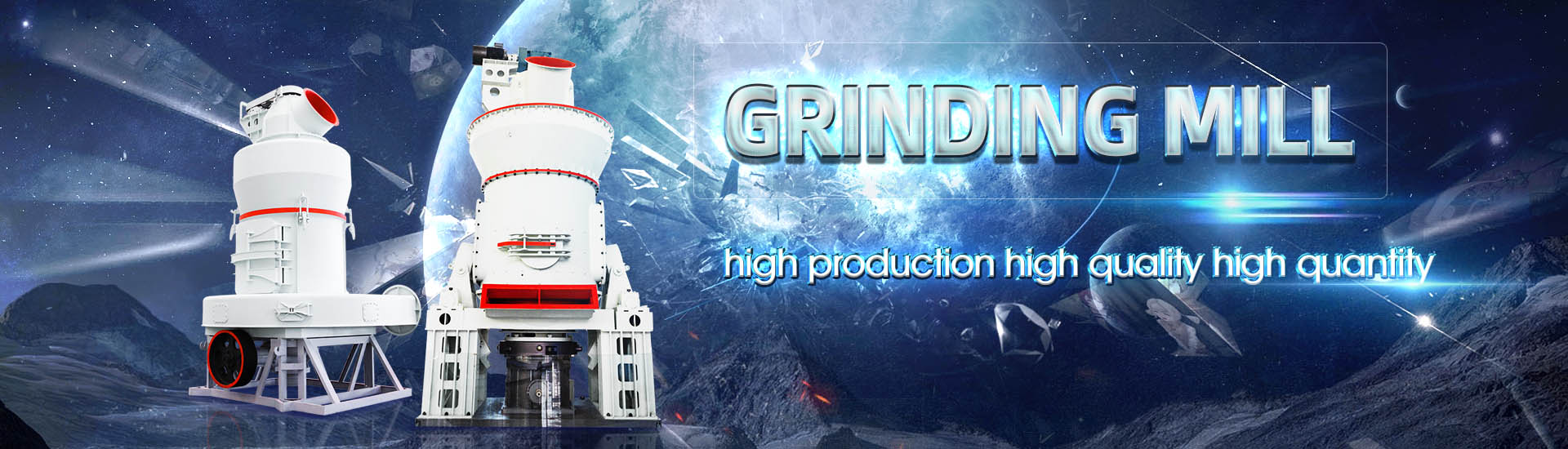
How to Change the Shaft of Grinding Mill
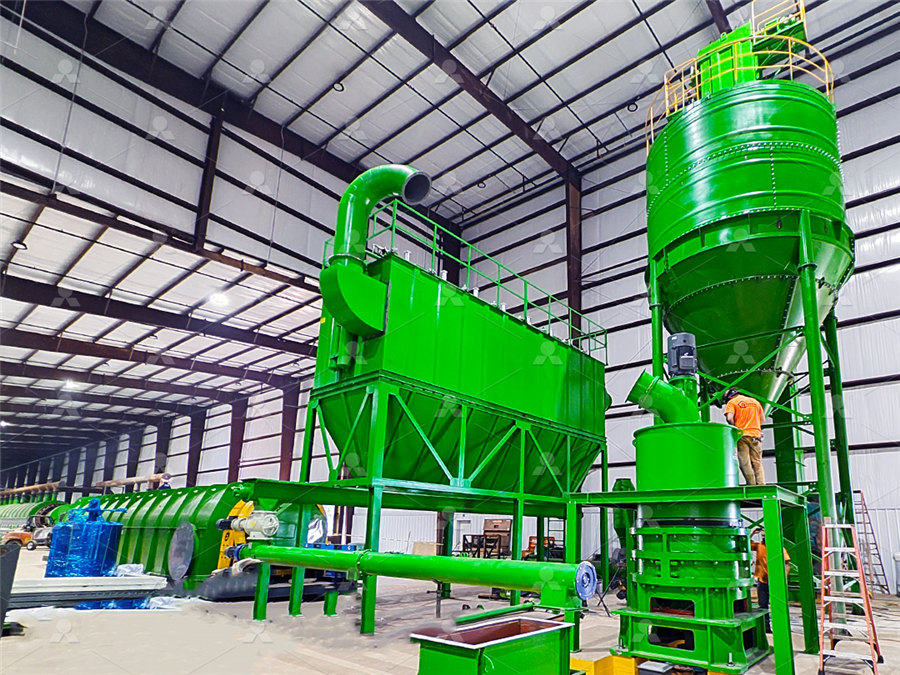
Wiener Ball Mill Generation 7 Replace grinding shaft
2022年5月3日 Wiener Ball Mill Generation 7How to replace the grinding shaft Chocolate and Compound process line The ball mill is easy to maintain as all parts are m2016年10月20日 Establish vertical and horizontal centerline of mill and pinion shaft against the effects of this, we recommend that the trunnion bearing sole Ball Mill Maintenance Installation Procedurechange the hammer pattern by adding more hammers to prevent excessive hammer pin hammer hole wear Always consult with the hammermill manufacturer when increasingHammermill Maintenance CPMWhen the ball mill machine is running normally, the temperature of transmission bearing shaft and reducer should not exceed 55℃ The feed part should be repaired in time for the serious wear Ball Mill Maintenance Procedure Guide

Hammermill and roll crusher maintenance and operation
2023年6月22日 Changing all rolls at once is usually the most efficient use of the time and effort required to make a roll change Rolls must be operated in a way to avoid having the material pile up in the nip when the mill is running at full simply done by replacing the bearing and no changes being necessary to the actual spindle design Some sections include a useful tip like the one shown below, these tips are based on MACHINE TOOL SPINDLE BEARING SELECTION MOUNTING 2015年7月28日 We will begin with the mill’s bull gear assembly and work towards the motor, The BULL GEAR, sometimes called the RING GEAR is designed to turn the mill transforming the energy of the motor into motion for Grinding Mill Gear Assembly 911Metallurgist2016年6月6日 SemiAutogenous Grinding (SAG) Mills The shell liner profile possible is primarily determined by the chordal dimension The profile must minimize packing and plate wear but give sufficient lift for proper grinding SAG Mill Liner Design 911Metallurgist

Practical Roll Techniques Grinding Balancing Valmet
2013年9月13日 This paper provides practical tips on roll inspections, balancing, grinding and grooving In addition, we discuss proper roll handling during removal, storage, transport, and 2022年11月28日 Grinding is a type of finishing process in mechanical processing, with less machining and high precision It is widely used in the machinery manufacturing industry The heattreated and quenched carbon What is Grinding Process How It Works Different drive assembly, basically consisting of a drive shaft within a drive shaft, which reduces the mill’s overall height (Other drive types are covered in the next section) You can also equip the mill with vibration and bearingtemperature sensors to monitor the bearing housing’s condition; this allows you to perform maintenance beforeHow to operate an air classifier mill to meet your fine grinding 2024年6月18日 To begin, locate the spindle or shaft on your grinding machine This is the part that the grinding wheel will attach to Slide the new wheel onto the spindle, making sure it fits snugly How often should I change the grinding wheel on my bench grinder?How to Change a Grinding Wheel on a Bench Grinder: A
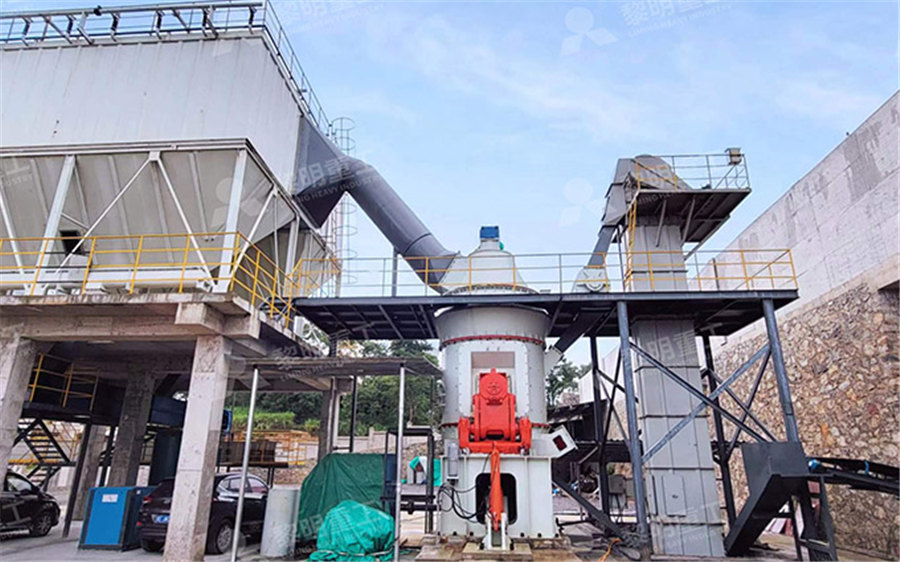
How to use a Milling Machine Instructions American Machine
QuickChange Tooling The quickchange adapter mounted on the spindle nose is used to speed up tool changing Tool changing with this system allows you to set up a number of milling operations such as drilling, end milling, and boring without changing the setup of 2017年1月17日 Excessive mill speeds caused more power consumption but resulted in reduced grinding rate Based on the simulation data, two scaleup models were proposed to predict power draw and grinding rateBreaking down energy consumption in industrial grinding millsThe Basket Mill is a wet mill that combines dispersion and grinding It is a continuous batch processing system The entire grinding process is carried out in the same container Can achieve ultrafine grinding Suitable for mass production, very suitable for different colors, easy to change colors and change productsBasket Mill Wet Grinding Mills ELE100 HP hammermill grinding corn, #8 screen will achieve 15 TPH = $029 per ton @ $006 KwH With worn parts, grinding 10 TPH = $045 per ton Normal wear Excessive wear As the screen wears, less material is able to pass through; hammermill capacity and efficiency decrease The particle does notHammermill Maintenance CPM
.jpg)
All About Grinding Quills The Meister Toolbox
2013年12月13日 Anyone who does CNC grinding knows what a grinding quill is, but few actually understand the important contribution the quill makes to optimized abrasive machining processes In the rush to fine tune their grinding operations, abrasive machinists turn their attention to such things as feeds speeds, abrasive wheel shapes and materials, dressing options and 55 known as the distribution function [45, 46]) describes the distribution of fragment sizes obtained after a breakage of particles of size xjThus, b1j, b2j, , bnj are the mass fractions of particles in size classes 1, 2, , n after a breakage of particles in size class j The mechanism of breakage is illustrated in [23] by a diagram shown in Fig 3Grinding in Ball Mills: Modeling and Process Control Sciendo1 Material is fed into the mill, typically by gravity 2 Inside the grinding chamber, the material is repeatedly struck by flailing ganged hammers which are attached to a shaft that rotates at a specified speed The material is crushed by a combination of hammer blows, collision with the walls of the grinding chamber and particle on particle Intro to Size Reduction Schutte Hammermill2017年5月8日 A lifter mill of 6 ft diameter, revolving at 187 rpm, is grinding coal The body of the mill is divided into two sections: one section, 75 ft long, being charged with 5 tons of steel balls, of 2 in average diameter, and the Grinding Mill Power 911Metallurgist
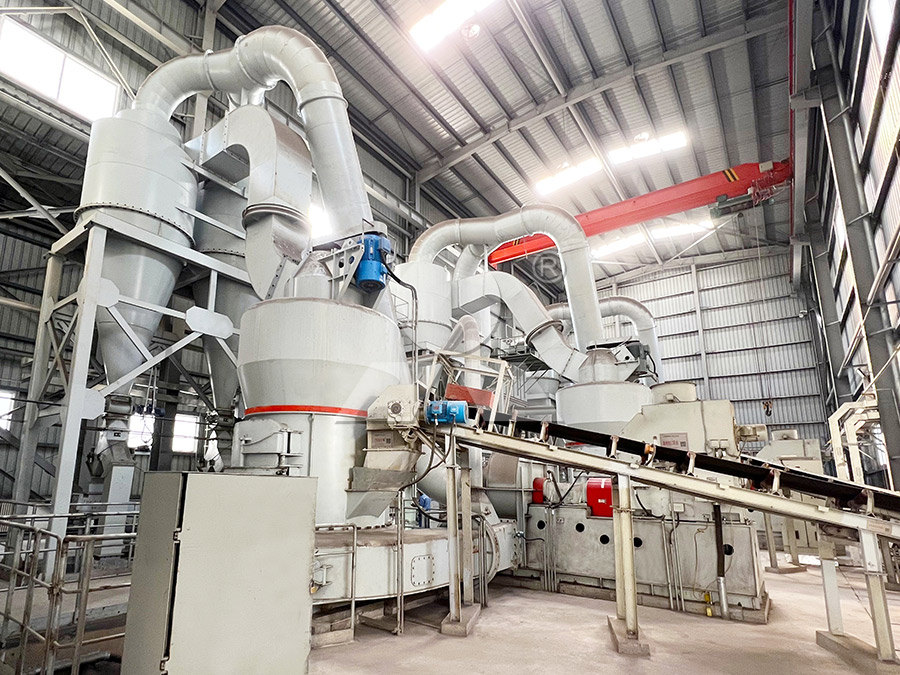
Ten Ways to Improve the Grinding Efficiency of Your
2019年4月22日 Here are ten ways to improve the grinding efficiency of ball mill 1 Change the original grindability another way is to reduce the shaft height of the spiral classifierHigh performance bearings developed specifically for internal grinding or highspeed motor applications under spring preload › Bore size range: ø6–25 mm, contact angle: 15˚ › Ball material: steel (S type), ceramic (H and X type) › Non separable type › Universal combinations (DU and SU) BSR SeriesMACHINE TOOL SPINDLE BEARING SELECTION MOUNTING 2016年10月27日 Replacing Hammer Mill Wear Parts Any machine that has moving or rotating parts requires routine maintenance to ensure that it performs at optimal capacity This is especially true of size reduction equipment which has grinding elements that will wear over time Inspecting and Replacing Wear Parts:Routine Hammer Mill Maintenance Schutte Hammermill2022年5月31日 Mineral crushing is the main source of energy consumption in mineral processing According to statistics, this consumption accounts for about 35–50% of the total cost of the mine (Curry et al, 2014), or even higherIt may also account for 18% of the global electrical energy consumption (NapierMunn, 2015)More efficient crushing equipment needs to be Analysis of vertical roller mill performance with changes in
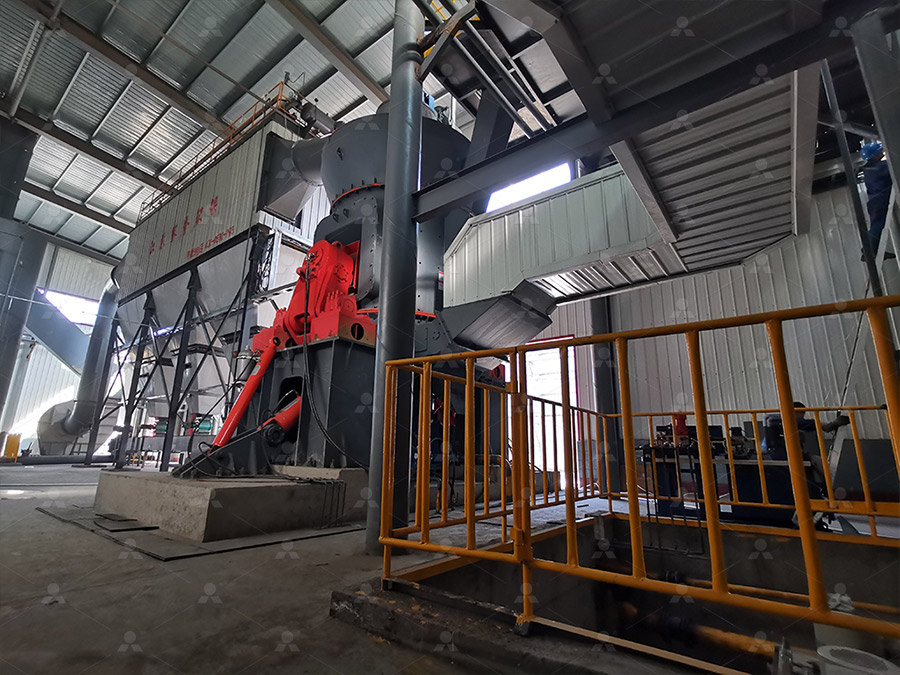
Scaleup of Agitator Bead Mills Grinding Dispersing
tion scale is only possible if no changes are made to operating parameters such as grinding media size, agitator shaft peripheral speed, grinding media density and, thus, the stress energy of the grinding first crushed in the same mill with identical grinding media in recirculation mode with four different agitator tip speeds of 5 m 2020年6月3日 The design of such grinding mills is extremely critical, requiring sophisticated software tools, proprietary calculation worksheets, and experienced technical engineers and drafters This blog will review how the mill design process has changed over the last 30 years While most of the changes have been positive, new issues and problems have risen in the How grinding mill design changed over the last 30 yearsSHAFT DIMENSION Roller crush capacity = 2945194tons/day, Power (P) = 47485KW, Roller speed (N) = 4 rpm Roller diameter = 920mm, Shaft diameter at roller= 500 mm, Torque =1133KNm, Shaft diameter at bearing support= 430 mm, Shaft diameter at pinion = 470 mm, Selfweight = 131Ton, Total length = 4430mm L1= 475 mm, L2= 1700mm, L3= 520 mm, L4= 271 (PDF) DESIGN AND ANALYSIS OF ROLLER SHAFTS FOR SUGAR2017年6月2日 Buhrstone mills are one of the oldest types of mills used for grinding grains and hard materials Disk attrition mills are modern versions of the ancient Buhrstone mill Vertical shaft mills work on the same principal as VSI crusher, with a rotor on a vertically mounted shaft using centrifugal force to throw the media against a wear plateHow it Works: Crushers, Grinding Mills and Pulverizers
.jpg)
(PDF) Grinding Media in Ball MillsA Review
2023年4月23日 According to Kelsall et al [17] changes in media (quantity, density, size, shape) High mill filling reduces the grinding rate because the collision zone would be saturated2022年11月8日 How to change the mesh screen sieve working videohttps://fmixer/pinmillgrinderhtmlPin Mill grinding machine is the famous universal size reductioHow to change the mesh screen sieve of the pin mill 2016年6月6日 Grinding Mill Shell Design The design incorporates a circumferential transition plate welded in place between the end of the shell cylinder and the shell flange – Liner handling equipment and procedures in SAG Mill Liner Design 911Metallurgist2017年9月1日 The first stirred mill was installed in the platinum industry in 2002, and by the year 2010, forty stirred mills had been installed at various platinum operations in South Africa, and these led to a step change in flotation recoveries (Rule, 2011, Rule, 2010)Over the last decade, approximately 200 Automated Scanning Electron Microscopy (AutoSEMEDS) systems have Fine grinding: How mill type affects particle shape characteristics
.jpg)
10 tips to improve the grinding efficiency of ball mill
2022年4月19日 Summary:The low grinding efficiency, low processing capacity, high production energy consumption, and unstable product fineness of the ball mill are the problems that most of the users in the industry will encounterHow to effectively improve the grinding efficiency of the ball mill is an important issue The low grinding efficiency, low processing capacity, high 2017年8月5日 The installed power in the primary mill is generally much greater than in conventional circuits Since the semiautogenous or autogenous mill is dependent at least in part, if not entirely, on the ore to grind itself, a small change in ore grinding characteristics can produce a relatively large change in the grinding capacity of the millHow to Control a SAG Grinding Mill Circuit 911MetallurgistMill performance is based on mill diameter and length only increases or decreases capacity The Slice Mill is simply a mill of the same diameter as the production mill but much shorter A Slice Mill of 72” diameter by 12” wide would replicate the result of Variables in Ball Mill Operation Paul O AbbeDIFFERENT MILLS REQUIRE DIFFERENT AMOUNTS OF MEDIA •BASED UPON WORKING VOLUME OR TOTAL VOLUME •Mills such as the Immersion Mill have a fixed amount determined by size of the basket •Steel Ball Mill 333% •Open Head Sand Mill 3545% •Ceramic Pebble Ball Mill 50% •Dry Grind Batch Attritor 4560% •Wet Grind Batch Attritor 3845% •Continuous How to Choose the Correct GRINDING MEDIA PCI Mag
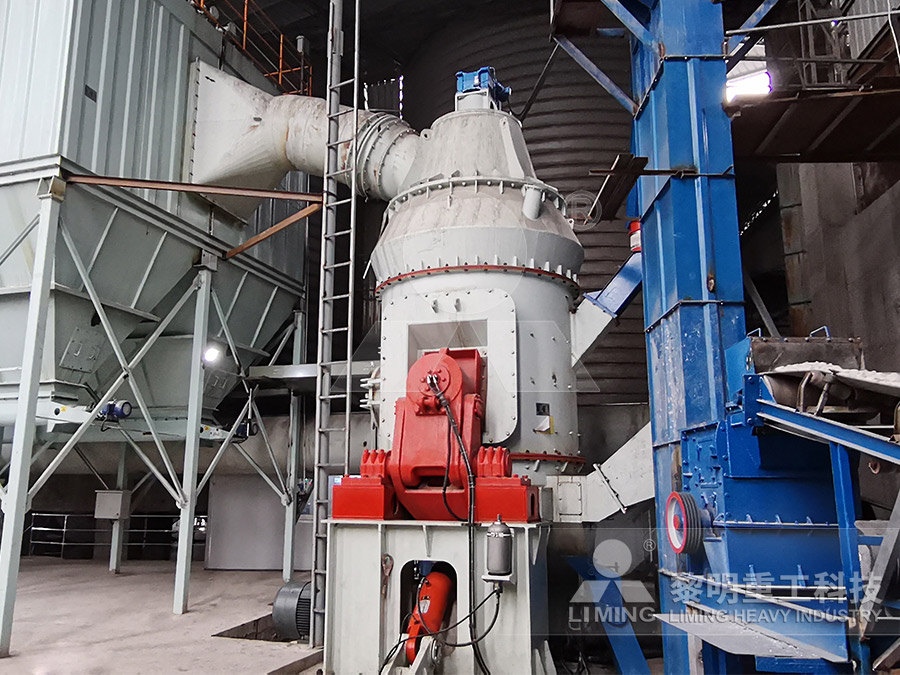
EnergyEfficient Technologies in Cement Grinding IntechOpen
2016年10月5日 In this chapter an introduction of widely applied energyefficient grinding technologies in cement grinding and description of the operating principles of the related equipments and comparisons over each other in terms of grinding efficiency, specific energy consumption, production capacity and cement quality are given A case study performed on a 2024年5月17日 A SAG (SemiAutogenous Grinding) mill is a giant rotating cylinder filled with grinding media and the ore being reduced As the mill rotates, the grinding media lifts and the impact crushes the feed material SAG mill control refers to the practice of managing the mill load, which is the amount of material inside the mill at any given timeA guide to SAG Mill managementInstall the short key into the slot of the drive shaft (See photo to the right) Slide the rotating burr onto the drive shaft ensuring the key way on the burr slides over the key in the groove of the shaft Install 2 washers on the shaft Screw the Reassembly Instructions – Country Living Grain Mills2022年10月26日 The stirring shaft can be classified into three types based on its structure and shape: mill size The size can vary from 015mm to 30 mm The grinding result is directly influenced by the size and type of grinding dyno mill DYNO MILL – A DYNAMIC WAY TO GRIND EASIER
.jpg)
Practical Roll Techniques Grinding Balancing Valmet
2013年9月13日 The correct way to measure concentricity on a grinding machine is 180º from wheel (back side), if the roll is supported on grinding seats For example, if the grinding seat is out of round this form will be transferred to the roll shell by the grinding wheel Runout will not be seen on the wheel side but when a2021年8月20日 This can happen in more aggressive grinding or when grinding certain metals that tend to stick to the grinding wheel In these applications, scrubber nozzles might need to be implemented Scrubber nozzles are typically highpressure (5001,000 psi), lowflow rate devices that are targeted after the grinding zone to remove chips from the wheel structure5 Grinding Considerations for Improving Surface FinishRelatively small slowly varying shaft position and velocity variations superimposed on the normal running speed of dual drive grinding mill motors can cause individual motor torque variations which disturb load sharing The magnitude of load or torque unbalance is a function of the magnitude of the mechanical variation, the type of motors used, ie, induction or synchronous, Load Sharing of Dual Motor Grinding Mill Drives IEEE Xplore2023年1月9日 1 The temperature of the slurry at the pre scattered stage is not high, but once the horizontal sand mill began, the temperature of the slurry in the grinding cavity exceeds the protection temperature, so that the sand mill was stopped In the case, we can appropriately increase the speed of the feed pump, thereby shortening the stay of the slurry in the grinding How to choose the right vertical sand mill horizontal sand mill?
.jpg)
Millstone Create Wiki Fandom
The Millstone is a more basic equivalent of the Crushing Wheels, and is most likely the first of the two that the Player will construct It is capable of applying milling recipes to any valid items inserted from above There are 2 variables that effect the processing speed of the Millstone: RPM and recipe duration The recipe duration is a number assigned to each recipe to determine is 2021年1月11日 Choosing a SAG Mill To Achieve Design Performance John Starkey1, Principal Consulting Engineer Sami Hindstrom2, Manager, Grinding Travis Orser2, Project Manager, Grinding 1 Starkey Associates Grinding Design and Process Engineering 336 – 268 Lakeshore Rd E Oakville, Ontario L6J 7S4 PH: (905) 4657512 Fax (905) 8445297Choosing a SAG Mill to Achieve Design PerformanceRead this indepth blog to learn about the working principle of Vertical Grinding Mill, its application, and its advantages +91 226796 9655 sales@macawberindia 130131, Hindustan Kohinoor Complex Supports for the bracket are also provided on the top to secure the cast iron bracket in between, while the main shaft, made of alloy Vertical Grinding Mill: How it Works, Application And AdvantagesYour grain mill is designed to be easily motorized The flywheel is grooved for use with a standard ½” A or V belt We advise using a gearreduced motor that will drive the mill at 75 rpm's or less The motor and the mill should be securely fastened to a substantial surface The mill handle MUST be removed before motorized operationGrain Mill Owner’s Manual – Country Living Grain Mills