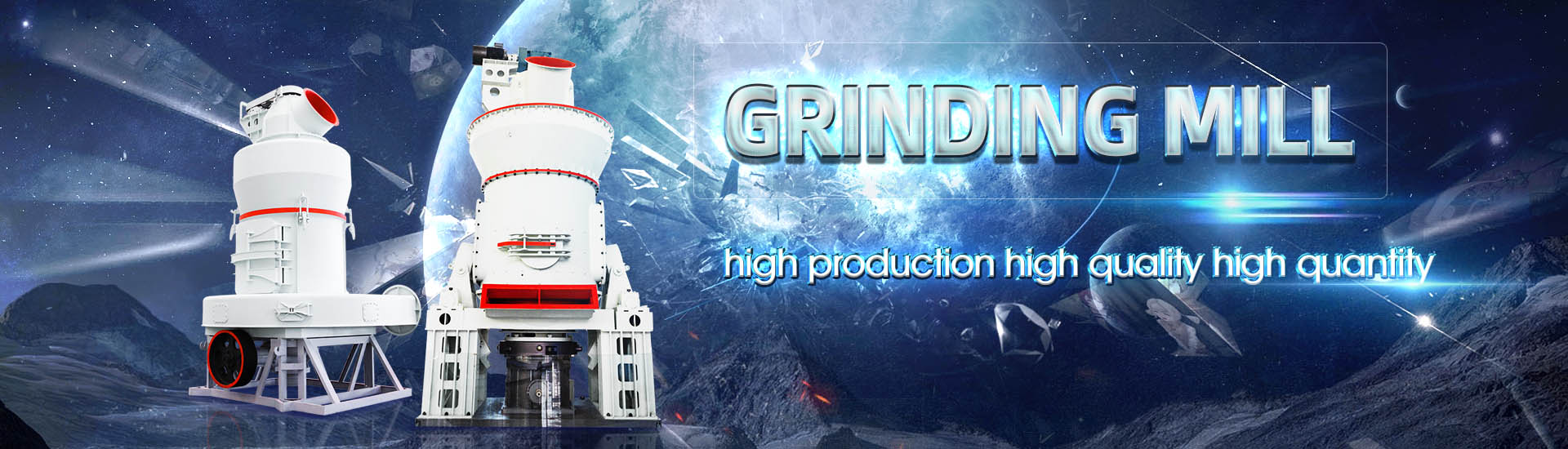
Alkaline furnace lining material grinding project
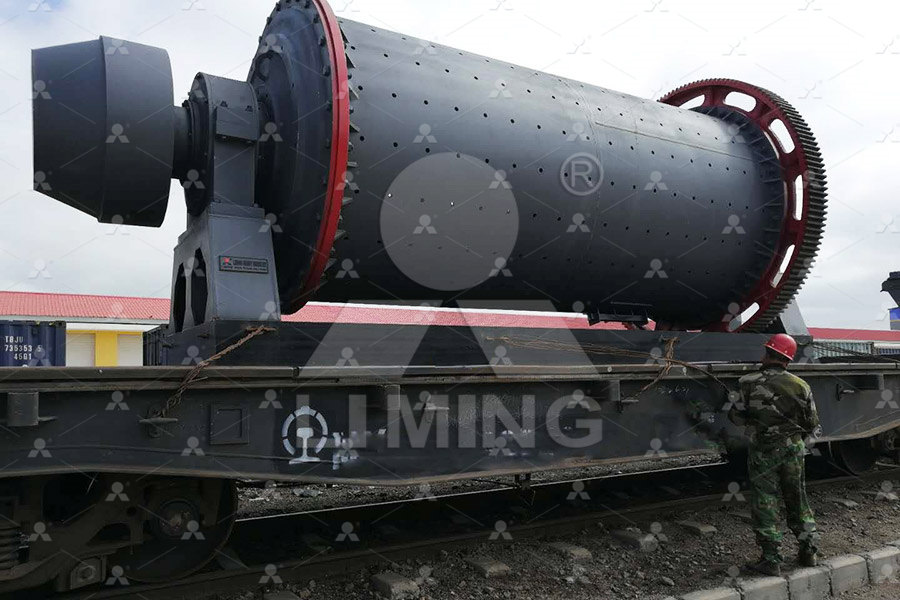
Ensuring Furnace Lining Efficiency Foundry
2017年3月14日 To do it right, here are five primary tips for maximum furnace lining efficiency: 1 Use IR thermography to inspect the existing lining — Ensuring lining quality is critical to protecting the structure from excess heat and This means lining concepts and process solutions for any type of primary furnace, slag cleaning furnaces, electric arc furnaces (AC and DC), PS converters, anode furnaces, ladles and Lining Concepts for the Nonferrous Metal Industry RHI MagnesitaCoreless induction furnace linings for aluminium melting are required to exhibit excellent nonwetting properties and operate successfully over a range of melting and casting Foundry furnace linings: diverse solutions vesuvius Corporate materials such as bricks and concrete, it is the ideal addition to a complete refractory lining Due to its excellent properties, the high temperature insulation wool is particularly energyreducing HIGH TEMPERATURE INSULATION WOOL
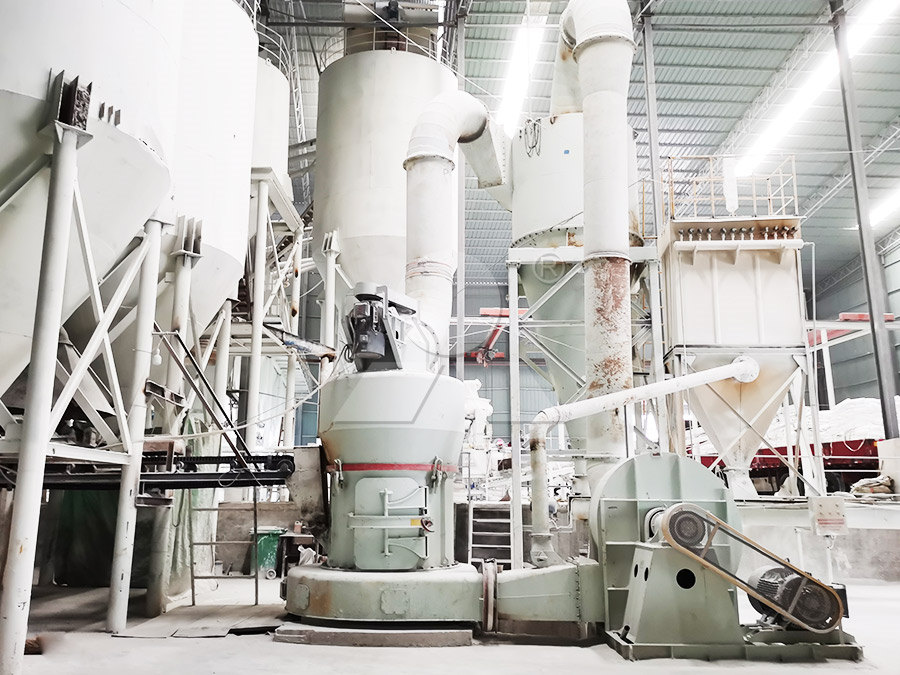
Induction Furnace Lining and Industrial Vibrator Design Theseus
Refractory material lining requires two steps for induction furnaces: Floor portion: Floor material is filled and compacted Wall portion: Liner form is positioned on the bottom refractoryWith many years of experience in furnace lining and proven knowhow in furnace proile definition and cooling concepts, Paul Wurth ofers complete solutions from the bottom and hearth to the BLAST FURNACE TECHNOLOGY Paul Wurth2022年3月1日 The design of lightweight wear linings is crucial in terms of the energy and resource efficiency of industrial furnaces and quality of final products This review aims to Design, fabrication and properties of lightweight wear lining 2015年9月1日 In this paper, we have investigated the advent and nature of alkaline hydrolysis in a refinery plant Innovative remedial measures were successfully implemented to prevent Investigation of Alkaline Hydrolysis in Refractory Linings of Process
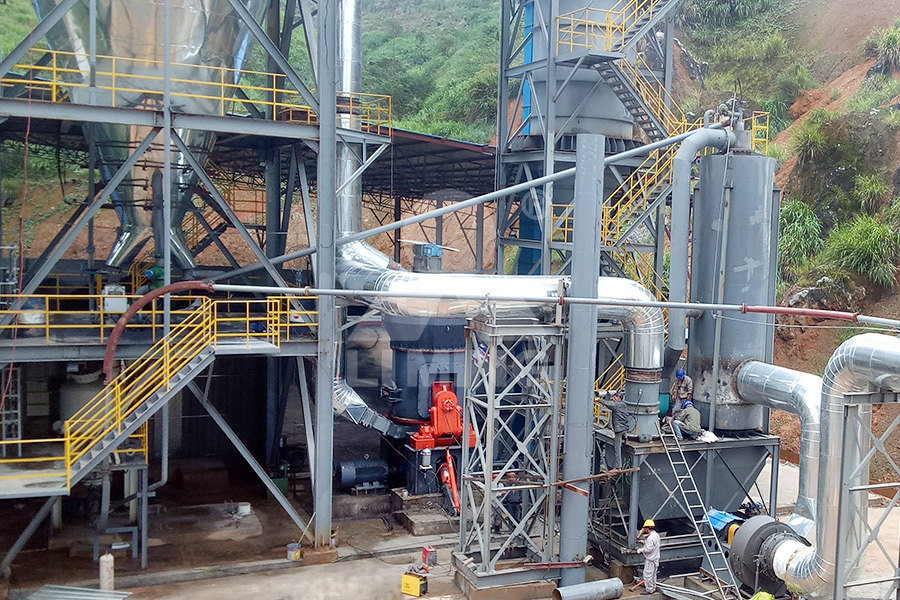
Materials selection of furnace linings with multicomponent
2020年3月1日 In an attempt to generate a systematic approach to select FL ceramic materials, an evolutionary screening procedure (ESP) is proposed in this paper, where a multiobjective This work reports on a new monolithic material with improved performance, compared to existing materials, designed for use in the ramp/hearth area of aluminum furnaces Improved behavior Improved Monolithic Materials for Lining Aluminum Holding2005年11月30日 For graphite refractory, this dissolution is generally assumed to be mass transfer controlled [6,7] , ie, limited by the rate of [C] transport through the diffusion boundary layerWear mechanism for blast furnace hearth refractory lining2021年5月15日 Basic oxygen furnace slag (BOFS) is a waste material generated during the steelmaking process and has the potential to harm both the environment and living organisms when disposed of in a landfillAlkaline Activation of Basic Oxygen Furnace Slag
.jpg)
Refractory lining of a Basic Oxygen Furnace
2013年3月28日 Refractory lining of a Basic Oxygen Furnace satyendra; March 28, 2013; 11 Comments ; charge pad, g carbon converte zones, gunning, slag coting, slag splashing,; Refractory lining of a Basic Oxygen Furnace The 2018年4月19日 Being a low cost material, the cost of lining of the furnace is low Because of dry preparation of the mass, the heating and sintering time needed is short The specific cost of refractory per ton of steel made is low Silica ramming mass can safely be used up to an operating temperature of 1600 deg CInduction Furnace Refractory Lining with Silica Ramming Mass2024年4月25日 The commonly used furnace lining material is metallurgical magnesite with an MgO content of more than 86%, but it is still an alkaline refractory material Neutral Ramming MassHow to choose furnace lining and furnace materials for medium 2022年3月1日 As shown in Fig 1, a conventional refractory lining structure has a wear lining, safety layer, and an insulation layer The wear lining resists erosion, wear, corrosion and thermomechanical loads of molten melts, while the insulation layer reduces the thermal transfer through refractory liningDesign, fabrication and properties of lightweight wear lining
.jpg)
Selection and application of nine different refractory materials for
2024年3月14日 Refractory materials for induction furnaces need to be selected based on the furnace type, furnace structure, type of steel being smelted, smelting process and operating conditions At the same time, the phase and physical properties of the refractory material from room temperature to working temperature should also be consideredinterrupted to repair or replace refractory lining Replacement of the lining increases furnace downtime Refractory material lining requires two steps for induction furnaces: Floor portion: Floor material is filled and compacted Wall portion: Liner form is positioned on the bottom refractory Then linerInduction Furnace Lining and Industrial Vibrator DesignTherefore, in all our projects, we install a layer of specialized material as the first lining layer at the bottom of the furnace This ‘stop layer’ ensures that if the main bulk of the furnace lining material fails, gas and liquid metal are prevented from penetrating through to Furnacing lining materials ELMON™ ElkemBlast Furnace Lining and Cooling Technology Page 5 of 16 B–2–023 4 Design Features of the Danieli Corus Blast Furnaces Figure 3 Installation of the lining of Blast Furnace No 6 in 1985BLAST FURNACE LINING AND COOLING TECHNOLOGY
.jpg)
Refractory lining of blast furnace – IspatGuru
2014年8月15日 Different types of BF refractories Different types of refractories which are used in blast furnace lining are described below Baked carbon blocks – Micro porous carbon block, semi graphitic carbon block, and micro porous 2003年1月20日 Thermal shock resistance The mm test specimens were heated to 1100uC, under a reducing atmosphere, at a rate of 125 K h–1, and kept at this temperature for 3 hAfter this soaking step Wear mechanism for blast furnace hearth refractory liningAlkaline Lining Materials includes mainly metallurgical magnesia with more than 92% magnesium oxide and fused magnesia,suitable for melting low silicon alloy steel and alkaline steel。 The intermediate frequency furnace magnesium material has the advantages of high refractoriness, good resistance to alkaline slag and stability against physical and chemical effects, but its Lining Material (Refractories Material) Huaxin Electric Melting Abrasives and Grinding Media Diesel Particle Filters and Gas Particle Filters Glass Technology Main lining: Topping patching material: Coil coat: HeatKing ™ Product Solutions: VA1173 (10MT) TA1211: CA337: Sponge Iron Melting : Furnace Zone : Main lining:Monolithic Lining Solution Steel Melting Induction Furnaces
.jpg)
The Study of AlkalineActivated Magnesium Slag Cementitious Material
2012年6月1日 Download Citation The Study of AlkalineActivated Magnesium Slag Cementitious Material Magnesium slag cementitious material was prepared successfully using the magnesium slagfurnace slag 2 Ironmaking and Steelmaking 2005 VOL 32 NO 6 Ironmaking and Steelmaking irs19243d 23/8/05 12:51:31 The Charlesworth Group, Wakefield +44(0)1924 Rev 751n/W (Jan 20 2003) 3 Schematic section through apparatus used to expose specimens to alkaline steam Silva et al Wear mechanism for blast furnace hearth refractory lining 4 Layout of trays (silicon Wear mechanism for blast furnace hearth refractory liningWhether new construction, lining replacement or lining repair, MegaBRIX® Precast Furnace Linings provide superior lining performance, ease of installation and quick turnaround TURNKEY INSTALLATIONS, REPAIR MAINTENANCE Extensive Project management experience within the aluminum industry Material zoning from furnace to breach BREACH Furnace Linings – Wahl Refractory SolutionsDevelopment of a SmallScale Oil Fired Furnace for Refractory Lining The geometric dimensions and density data used in constructing the furnace metal casing and refractory material wall lining are as follow: Furnace March, 2021 displayed in Fig 14 using a hack saw They were subsequently polished using grinding wheel and Development of a SmallScale Oil Fired Furnace for Refractory Lining
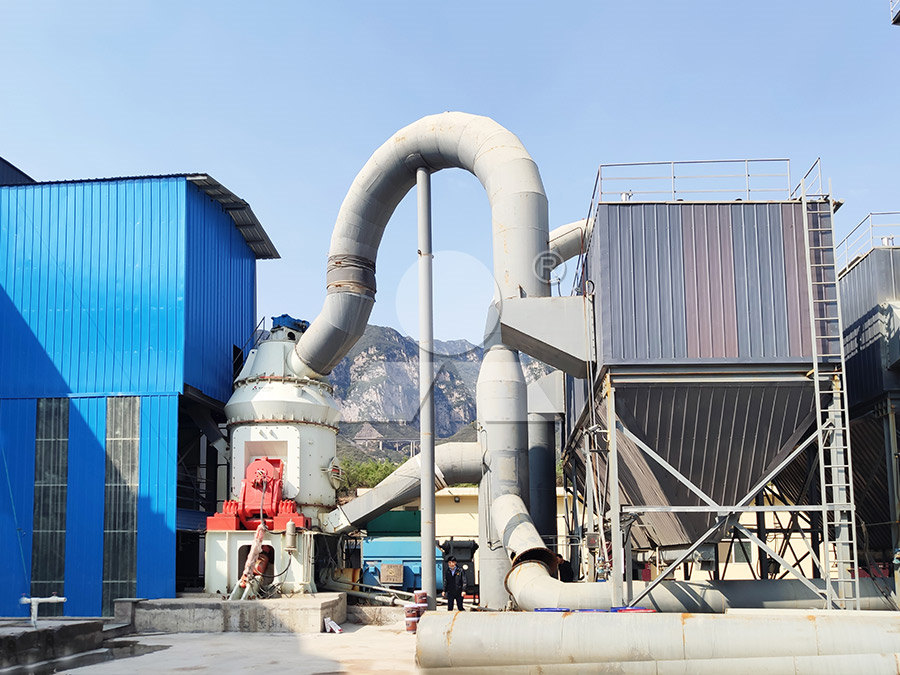
Induction Furnace Refractory Lining: Properties and Base Materials
2023年3月10日 That concludes the explanation of induction furnace lining, beginning with the properties of lining, the basic material and binder material of lining, the main principles of lining, and the criteria for selecting a lining material If you have any questions or need more information, please leave them in the comments section or contact our teamChemical Attack: There could be the possibility of a chemical reaction with the content at high temperatures So, the refractory material selected should be inert against them Installation: The refractory lining material must be easily available and installed The chosen refractory material must be quickly delivered to the required location during repair or maintenance timesWhat is a Refractory Lining? Materials, Selection, and Types of 2020年10月19日 According to the raw materials and smelting furnace need different acid and alkaline divided into lining, our factory is using acidic lining Play lining, is to use the material such as quartz sand, the furnace wall do a layer How to improve the induction furnace lining lifeIn addition to significant furnace downtime, such lining systems also typically lead to hydrogen pickup in the aluminium melt for the initial period following furnace installation The INSURAL furnace lining system, combining highly insulating Foundry furnace linings: diverse solutions vesuvius
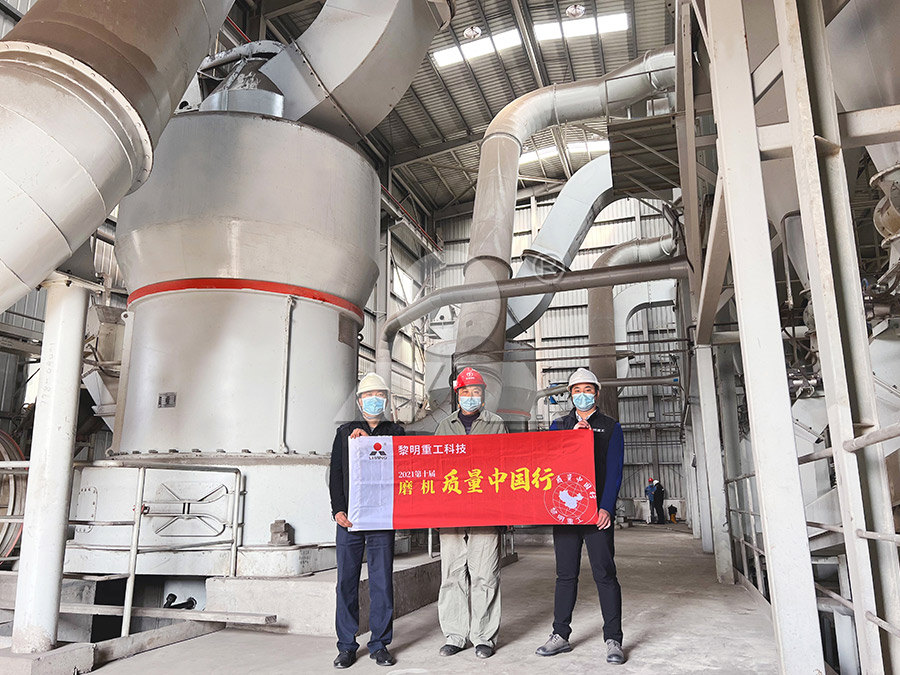
Electric Arc Furnace Refractory Material
There are also unburned magnesia alkaline bricks and asphalt combined with magnesia and dolomite ramming mass materials or your electric arc furnace project is about to start or rebuild, please contact us Exclusive customer 2 Ironmaking and Steelmaking 2005 VOL 32 NO 6 Ironmaking and Steelmaking irs19243d 23/8/05 12:51:31 The Charlesworth Group, Wakefield +44(0)1924 Rev 751n/W (Jan 20 2003) 3 Schematic section through apparatus used to expose specimens to alkaline steam Silva et al Wear mechanism for blast furnace hearth refractory lining 4 Layout of trays (silicon Wear mechanism for blast furnace hearth refractory liningThe furnace lining built with silica sand as the basic refractory material is often called acid furnace lining Silica sand has many advantages: firstly, it has abundant resources and low prices; moreover, the crucible made of silica sand as the basic refractory material still has good strength at the high temperature close to its melting point and has good resistance to quench and heatLining material and particle size gradation of cast steel in Hydraulically bonded, high alumina induction furnace coil screed with a very smooth surface 1: Hydraulic: 1700: Capscreed: Hydraulically bonded, high alumina high strength induction furnace coil screed for pushout furnaces 1: Hydraulic: 1680: Capscreed 96C: A high fluidity, selfflowing, high alumina castable: 1 / 3: Hydraulic: 1800: Capgrout GCoreless Induction Furnace Linings Capital Refractories

Ladle Furnace Slag: Synthesis, Properties, and Applications
2023年11月23日 The bottom of the ladle furnace consists of a pipeline through which argon gas is pumped for the homogeneous stirring of liquid steel in the furnace It also has a porous refractory plug connected to the argon pipeline, an addition hopper mounted on the cover used to extract fumes generated during the process, and a lance for injecting desulfurizing agents 17 , (3)Protective furnace lining: the acidic substance Fe ₂ O ₃ in the residue and SiO ₂ can easily react with the alkaline substance MgO in the furnace lining material to erode the furnace lining Adding calcium oxide, these acidic substances preferentially react with calcium oxideNews What is the use of lime in steelmaking production?2019年9月16日 Refractory lining material can be shaped or unshaped (monolithic material) Dry monolithic refractory material is normally used for the lining of induction furnace Life of refractory lining depends on dryness of refractory material and also compaction ratio For the lining of induction furnace, refractory materials are normally monolithic Refractory Lining of Coreless Induction Furnace IspatGuruWe offer Ceramic Fiber Furnace Lining, Vacuum Formed Ceramic Fiber, ceramic fiber blanket, Vacuum Formed Ceramic Fibre shapes is made from high quality polycrystalline ceramic fiber raw material, [ protected] or call us on + to discuss your projects Features: Operating temperature up to 1800 o C; Light weight, Ceramic Fiber Furnace Lining, Vacuum Formed Ceramic Fibre,
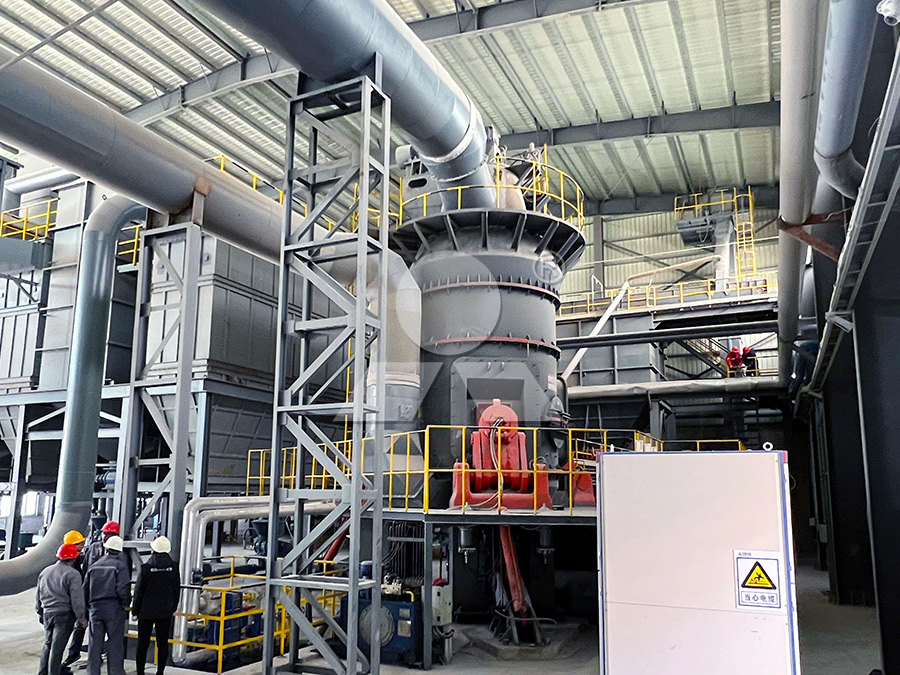
Ensuring Effective Furnace Lining Efficiency Thermal
2017年5月30日 Not only does this protect furnace parts from extreme heat caused by smelting, but it also prevents excessive heat loss and can lead to greater overall energy efficiency However, identifying the need for new and other effects, the metallic housing of the furnace is fitted with a refractory lining In the past, refractory bricks were used as the primary material for fabrication of the lining At the present time, monolithic furnace linings are being used all the more frequently owing to rapid development of the technology of refractoryconcrete FURNACES WITH A REFRACTORYCONCRETE LINING2020年5月21日 Whether from the shape of the material or the thermal insulation performance of the lining, they are essentially made of carbon material lining A new furnace lining, the use and maintenance of good furnace lining life can be as long as more than 10 years, the use and maintenance is not good, furnace lining life less than a year or even just a Analysis of 6 causes of lining damage in hot furnace of downtime Follow the five tips below to keep your furnace lining running efficiently Tip 1 – Evaluate the furnace liner by using infrared (IR) thermography inspection Infrared (IR) thermography scans are an essential step for evaluating the quality of the furnace lining Lining quality is critical to protecting the steelFive Tips for Achieving Furnace Lining Efficiency
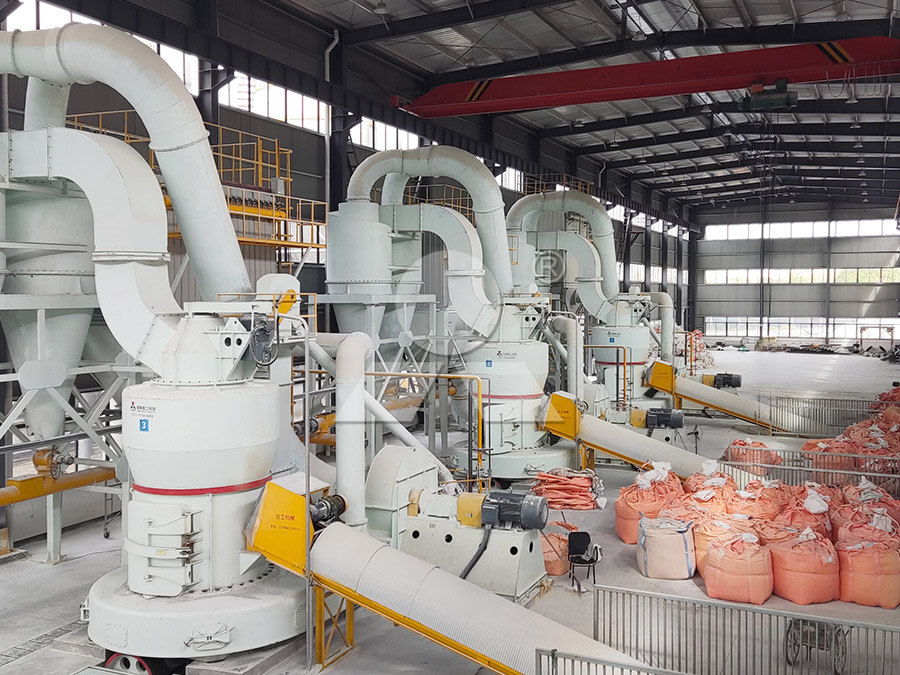
Review in application of blast furnace dust in wastewater
2024年3月4日 Blast furnace dust (BFD) is the solid powder and particulate matter produced by dust removal process in ironmaking industry The element composition of BFD is complex, and a direct return to sintering will lead to heavy metal enrichment and blast furnace lining corrosion In recent years, the application of BFD in wastewater treatment has attracted widespread 2022年12月2日 Materials with a basicity of more than 1% have an alkaline character Materials with a basicity of 1% have an acidic nature Simply put, an alkalinecharacteristic lining material contains more MgO2 The lining material with an acidic character has a higher SiO2 content Can’t acid lining be used in cast steel smelting? Or is it the other way 8 Differences Between Cast Steel and Cast Iron Faz Foundry2021年3月20日 The CP is a good raw material for preparing graphitiferous cathode carbon block, cathodic pastes, and the carbon block for furnace lining for which the ash content is required to be ≤ 2%–8% (Ministry of Industry and Information Technology of the People’s Republic of China, 2012), ≤ 3–7% (Ministry of Industry and Information Technology of the Recycling and utilization of spent potlining by different high 2016年1月21日 During the circulation process, alkali steam will inevitably contact with the metallurgical raw material and furnace lining of the blast furnace, which will have negative effects on production [7 Behavior of Alkalis in Blast Furnaces Request PDF ResearchGate
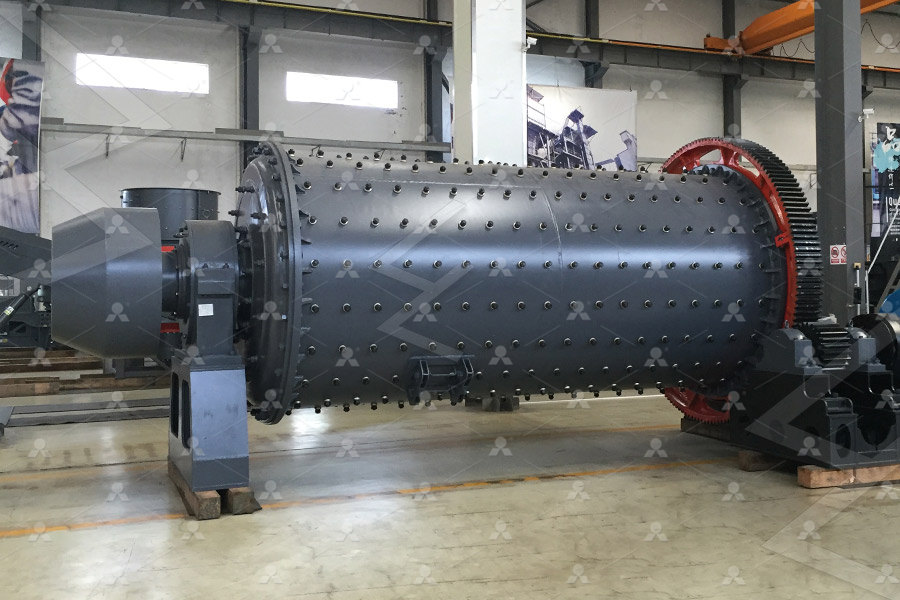
(PDF) Blast furnace lining and cooling technology ResearchGate
2004年11月1日 The developments of a blast furnace lining and cooling concept are discussed The blast furnace can reliably be driven to the unknown limits of production and pulverized coal injection (PCI 2024年5月21日 Once the new lining is installed, the furnace undergoes a baking process in which the lining material is solid baked to form a monolithic structure Putting the furnace into operation Once relining is completed, the furnace is put into operation and the process of heating to operating temperature starts in order to return to productionBlast Furnace Relining: From Project to Implementation M