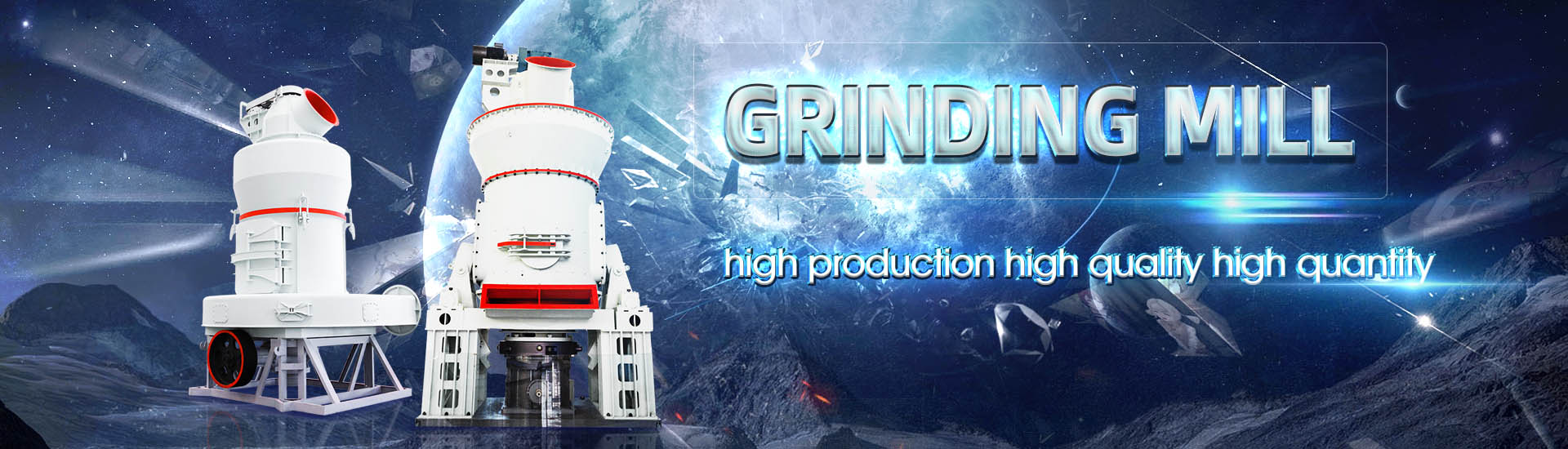
Ore mill net 150*125 Ore mill net 150*125 Ore mill net 150*125
.jpg)
Stripping Ratios, Pit Limits Cutoff Grade Optimization
In order to determine transition depth from openpit to underground mining on the basis of the allowable and economically feasible overall stripping ratios, an economicmathematical Mine to Mill, which links aspects of mining and mineral processing in order to optimise the combined mining and processing stages, has been under development and use for the last 20 UNDErsTaNDINg MINE TO MILL 911 Metallurgist2018年3月12日 Cutoff grade is defined as the grade that is used to distinguish between ore and waste within a given ore body It also differentiates between various types of ore for different(PDF) Comparison of cutoff grade models in mine ResearchGateThis study was aimed at increasing mine output and profit margin by controlling fragment size distribution, managing grade variability, and ensuring that broken ore reaches the mill plant Monitoring ore loss and dilution for minetomill integration in
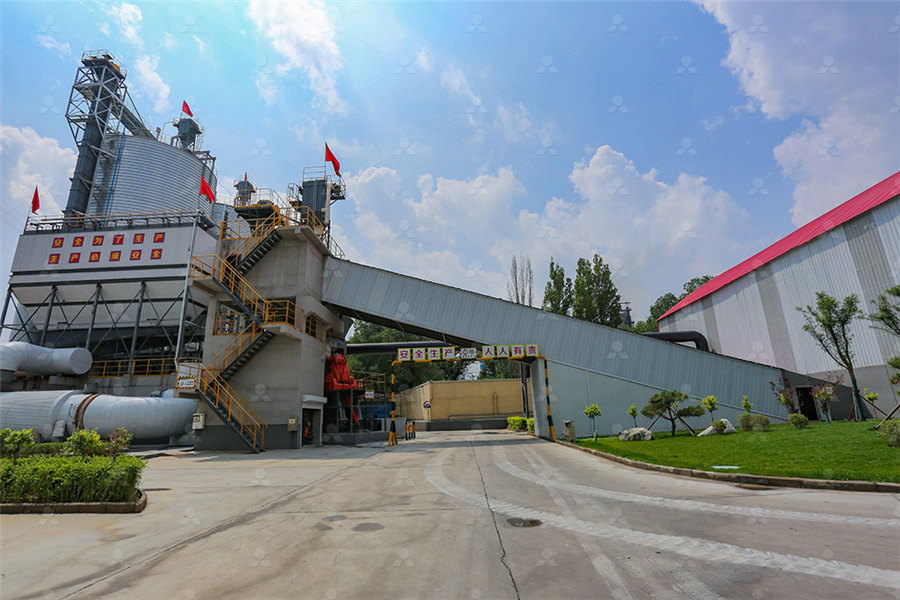
Bond Work Index Procedure and Method 911Metallurgist
2015年6月6日 This Grindability Test or Bond Ball Mill Work Index Procedure is used to determine the Bond Work Index of minus six mesh or finer feed ore samples These equation How to estimate the power required for a grinding mill ? What is the work index ? What is the power required to mill an ore ?Grinding power : step by step calculation PowderProcess2018年11月21日 Effort and insights from mineralogical and processing characterisation (eg ore hardness) of subore body domains allows sequencing for processing to ensure consistency Dynamic concepts for mine to mill operation and optimisationIn particular, ball milling is one of the important unit operations in the iron ore pelletizing process The mill product, due to its physical properties, determines the efficiency ofPopulation balance model approach to ball mill optimization in
.jpg)
Development of ore sorting and its impact on mineral processing
2014年10月15日 The goal of ore sorting is to reduce the total amount of material sent to the high energy milling circuit, while not significantly impacting total metal recovery In general, ore 2014年1月1日 The mill product, due to its physical properties, determines the efficiency of subsequent stages of classification, filtration and pelletizing, thus impacting the quality of iron ore pelletsPopulation balance model approach to ball mill 3 BALL MILL MODEL The population balance model may be expressed by Equation (1): > @ ¦ i1 1 i b ij m j j i j i S Ht dt d H m t (1) where: S i (t) is the size discretized selection function for Population balance model approach to ball mill optimization in iron ore 2017年3月20日 Investigation on the particle size and shape of iron ore pellet feed using ball mill and HPGR the disaggregation method is based on passing the minus of 1 mm samples from the 0150 mm sievePhysicochemical Problems of Mineral Processing
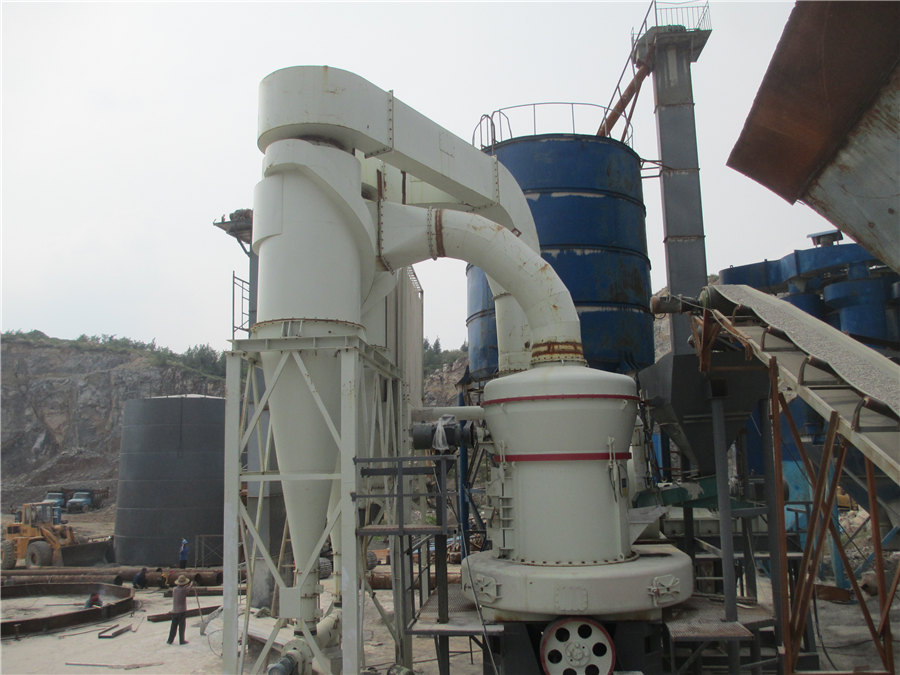
Simulation of industrial PGM and iron ore ball milling circuits from
2023年4月20日 As such, the present work applies a phenomenological ball mill model in integrated process simulations to describe the performance of an industrial ball milling and classification circuit for 2013年7月15日 For any circuit, whether a crushing circuit, a rod mill, or a closed ball mill circuit, the Work Index always means the equivalent amount of energy to reduce one ton of the ore from a very large size to 100 um The sample was received crushed appropriately for the ball mill testBond Work Index FormulaEquation 911Metallurgist2017年7月26日 Soft ore Work Index 13 = 100,000/90,000 = 11 kwh/t Hard ore Work Index 16 = 100,000/65,000 = 154 kwh/t For the purposes of this example, we will hypothesize that the the crushing index of the hard ore with the increased energy input of 154 kw/t reduces the ball mill feed size to 6,500 micrometersHow Ball Mill Ore Feed Size Affects Tonnage Capacity2013年7月15日 A methodology is described for equipment sizing and selection for a circuit closed with screens, and the laboratory testing requirements are described for low grade base metal ores and magnetite ores(PDF) Energy Efficient Ball Mill Circuit – Equipment Sizing
.jpg)
A Review of Alternative Procedures to the Bond Ball Mill
2021年7月12日 G —net weight of undersize product per unit revolution of the mill, Bond mill or a reference ore for comparison in each test usually 50, 100, or 150), 2013年12月31日 The present investigation focuses on utilizing the calculated retention time of the iron ore as a standard grinding reference time to the laboratory ball mill for optimizing the grinding time of A developed approach based on grinding time to determine ore 2018年8月8日 15 0075 150 20 01 200 25 0125 The article presents research on the comminution of copper ore in a selfconstructed mill using highpressure it is especially appropriate for (PDF) Grinding Kinetics Adjustment of Copper Ore Grinding in 2017年1月1日 Thus, the performance of an industrial ball mill can be adequately described using the orespecific breakage distribution function together with the systematic variation of the material transport (PDF) Performance optimization of an industrial ball
.jpg)
Standard Bond Ball Mill Grindability Test MethodProcedure
2015年12月14日 Net Product = Product – weight of undersize in Mill Feed; Net grams of product per revolution = Net Product/No of Rev Add new feed to Screen Oversize (circulating load) to bring up to original weight of Material Charge using split samples Calculate No of Revolutions for next period No Rev =The final fineness of the grinding materials can be adjusted between 150 meshes and 3000 mesh (745 micron) Application of ultrafine grinding mill – in ore field Ring Mill For Ultrafine Grinding Calcium Carbonate A ring mill, also known as Ultra Fine Grinding Mill SBM Ultrafine Powder 2022年10月1日 The grindability of raw material is generally determined by Bond’s standard ball mill grindability test (developed by the Allis Chalmers company) The ball mill grindability test is used for describing ore hardness and it is so widespread that the Bond Work Index generated from the test is often referred to as an ore characteristicA new methodology to obtain a corrected Bond ball mill work Understanding Mine to Mill is presented in five parts Part A – Setting the Scene provides some definitions of Mine to Mill (M2M) and the historical background A chronology of Mine to Mill developments is followed by brief descriptions of the very wide range of Mine to Mill applications which have been implemented over the last 15 yearsUNDErsTaNDINg MINE TO MILL 911 Metallurgist

Vertical mill simulation applied to iron ores ResearchGate
2014年11月1日 The sample of coarse iron ore was characterized in laboratory tests carried out in a small batch ball mill Selection and breakage function parameters were determined from the laboratory tests2015年6月6日 Riffle one 500 gram charge of ore down to splits of 125 grams each Record the exact weight of one split; identify it as Feed No 1 Wet screen through a 150 mesh screen Filter and dry the +150 mesh and screen through the 6150 mesh screen deck Record the weight of each size fraction on the Bond Feed Screen Analysis WorksheetBond Work Index Procedure and Method 911Metallurgist2012年4月1日 Adding mill scale as an ingredient into the iron ore sintering or pelletizing process is the main utilization approach for mill scale because of its high iron content and positional advantages [10 Recycling of steel plant mill scale via iron ore sintering plant2015年6月19日 The basic parameters used in ball mill design (power calculations), rod mill or any tumbling mill sizing are; material to be ground, characteristics, Bond Work Index, bulk density, specific density, desired mill tonnage capacity DTPH, operating % solids or pulp density, feed size as F80 and maximum ‘chunk size’, product size as P80 and maximum and finally the type of Ball Mill Design/Power Calculation 911Metallurgist

(PDF) Uranium Mill Tailings: Geochemistry, Mineralogy, and
2006年12月1日 Worldwide, the mining of uranium has generated 938 × 106 m3 of mill tailings The radioactivity of these tailings depends on the grade of ore mined and varies from less than 1 Bq/g to more than 2010年10月26日 First use of Sinamics SL150 cycloconverters for grinding mills: Siemens to modernize ore mill drive for copper producer Quadra FNX Quadra FNX Mining Ltd, a Canadian mining company, has commissioned Siemens to modernize the drive in an SAG mill in its Robinson opencast copper mine in Nevada, USAFirst use of Sinamics SL150 cycloconverters for grinding mills: Siemens Representative sample: The only ore blend a SAG mill will never see Critical size: Ore component that is harder than the mill has power to grind at the specified rate When a SAG mill is too small, pebble crushing allows the critical size to be eliminated and throughput is increased Conversely, critical size pebbles occur when hard oreDesign SAG mill production when you need it most: In day 1 and 2014年10月20日 Rio Paracatu regrind circuit Santos Júnior et al (2011) presented some data on the Paracatu Vertical Mill circuit process, as well as its comparison to the plant's conventional ball millRegrind of metallic ores with vertical mills: An
.jpg)
Chilean Mill 911Metallurgist
2015年7月14日 The Quartz Mill AKA Chilean Mill is one of the more popular types of the original Chilean millStill used for certain grinding problems, this mill employs the convexconcave principle of crushing ores, resulting in a product surprisingly low in slime content and which has its particles, such as sulfides and gold, well polished and free of recovery retarding tarnish2016年7月8日 * Crushing provides for two 7hour shifts, eighth and sixteenth hours are for cleanup Rod and Ball Milling each provide for three 8hour shifts of continuous operation By referring to equipment manufacturer’s bulletin on crushers, Fig 1, a crusher producing 80% passing 3/4″ requires a close side setting of approximately 5/8″Equipment Sizing: Crusher or Grinding Mill 911Metallurgist2016年6月6日 Interlock mill drive motor(s) with new ore feed supply so that mill, (36 in) in length In a reversible 97 m (32 ft) mill using up to 8% charge of 100125 mm (45 in) Table II gives a comparison of liner materials in semiautogenous grinding of copper and iron oresSAG Mill Liner Design 911Metallurgist2011年1月1日 This investigation deals with the effect of replacing some amount of Baharia high barite iron ore concentrate by mill scale waste which was characterized by high iron oxide content on the (PDF) Recycling of mill scale in sintering process Science of
.jpg)
Kinetic grinding test approach to estimate the ball mill work
2015年7月31日 The article discusses the study of the possibility of applying nonstandard mill MSL14K for the Bond ball mill test As a result of ore grinding experiments, the Bond ball mill work index was 2024年4月1日 This work aims to optimize the grinding parameters for an Egyptian feldspar ore that ensures maximum production of size −250 þ 45 mm and minimum % − 45 mm Grinding was performed using a Some Aspects on Grindability of Feldspar Ore Using Ball MillFind out all of the information about the Dec Group product: jet mill MC DecJet® 100 Contact a supplier or the parent company directly to get a quote or to find out a price or your closest point of saleJet mill MC DecJet® 100 Dec Group vertical / for ore / January 2007, two complete grinding circuit surveys were performed followed by a SAG mill crash stop and grindout After stopping the mill, a SAG mill feed sample was also collected from Conveyor parison of SAG mill feed size throughputs
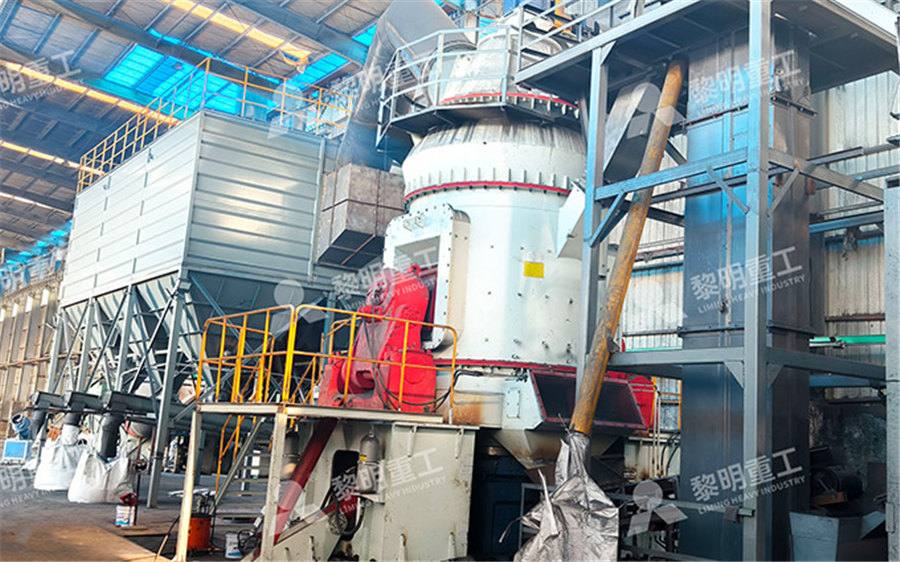
Buy Ore Ball Mill for Mineral Processing Iron Gold
The ore ball mill designed by our company, which is represented by gold ore ball mill and iron ore ball mill, is manufactured with highquality materials and advanced technology They have the characteristics of high efficiency, energy 2019年9月24日 There are numerous examples in the literature, some of which are quantifying the effect of Mine to Mill Grundstrom et al, 2001;Hart et al, 2001;Scott et al, 2002;Burger et al, 2006;Jankovic et al Simulating the Impact of Ore Competence Variability The liberation studies based on the P80 passing percentage were discussed BBM and LBM were used to perform the grinding The BBM was used to calculate the total retention time taken for each ore in the mill The estimated retention time of the iron ore in the mill was used as a standard grinding reference time to the LBM(PDF) Estimation of Grinding Time for Desired Particle Size 2020年1月3日 Iron ores obtained from different sources differ in their chemical and physical properties These variations make the process of grinding a difficult task The work carried out in this context focuses on three different samples of iron ore, viz, high silica high alumina, low silica high alumina, and low silica low alumina The grinding process for all the three iron ores is Estimation of Grinding Time for Desired Particle Size Distribution
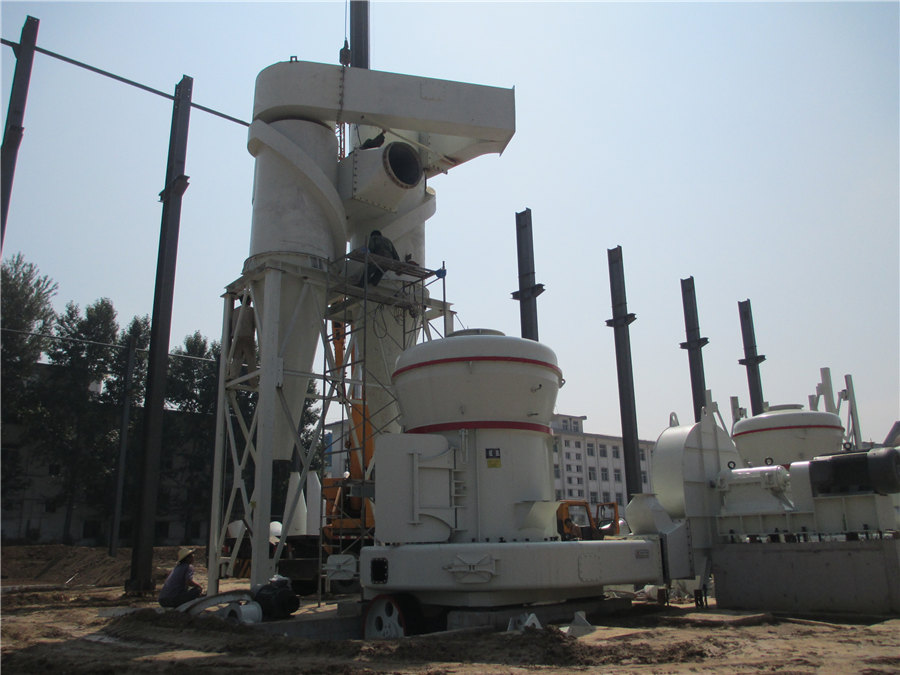
Winning the Metal: Ore Mills of the West Western Mining History
It is the chore of the mill manager to decide what methods or techniques will be used to obtain the valuable commodity Treating ore by milling is generally a twostep process, first the ore must be crushed, then the crushed ore must be treated to separate 2019年6月30日 All content in this area was uploaded by Grace OforiSarpong on Oct 06, 2020(PDF) Geometallurgical Studies on Gold Ore for EnhancedThe approach developed takes into account the ore characteristics is the mill net power, [kW] M F 80 = 110,000 µm and a target grind P 80 = 125 µm A SAG mill of 13 MW with D= 36 ft and (PDF) Toward a Simple Approach Determining Single Stage SAG mill 2018年3月12日 Comparison of cutoff grade models in mine planning for improved value creation based on NPV(PDF) Comparison of cutoff grade models in mine ResearchGate
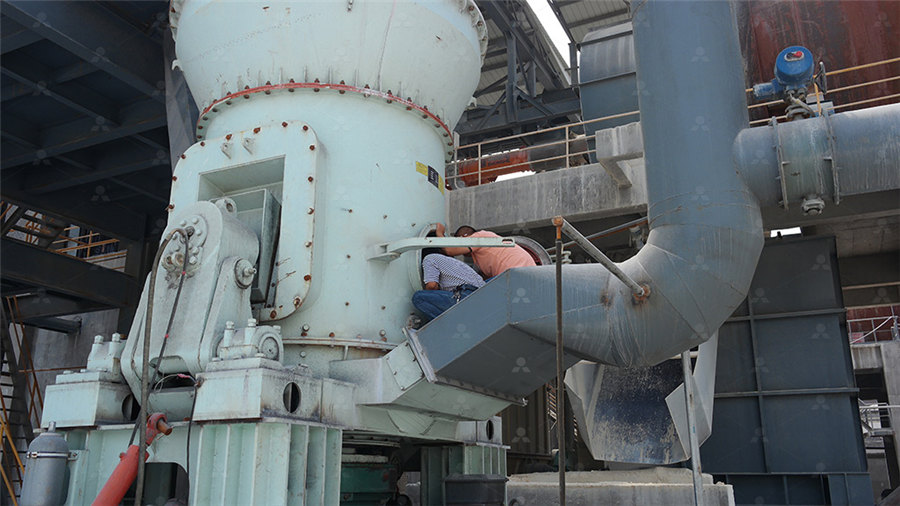
AMIT 135: Lesson 7 Ball Mills Circuits – Mining Mill Operator
Mill Type Overview Three types of mill design are common The Overflow Discharge mill is best suited for fine grinding to 75 – 106 microns; The Diaphram or Grate Discharge mill keeps coarse particles within the mill for additional grinding and typically used for grinds to 150 – 250 microns; The CenterPeriphery Discharge mill has feed reporting from both ends and the product