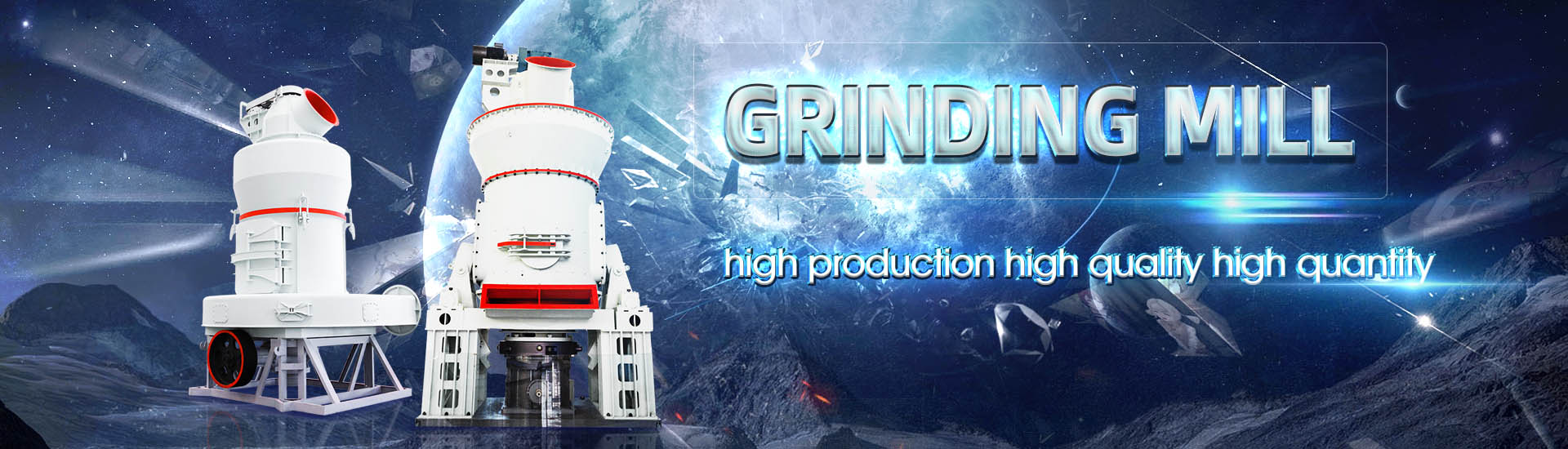
How to control the feed and discharge particle diameter of the reverse ore grinding machine
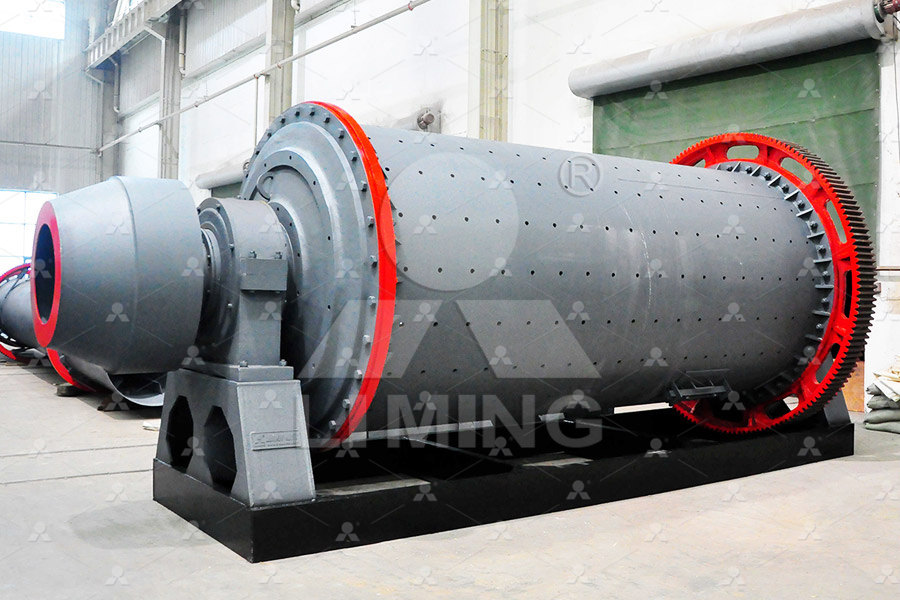
Determining Discharge Rates of Particulate Solids AIChE
The physics of bulk solids is markedly different than the physics of liquids, and these differences have a dramatic impact on the calculation of discharge rate Table 1summarizes some of the more important differences between bulk solids and liquids When liquids are stored in tanks and discharged: 1 the fluid stress is 展开2020年3月1日 In the field of feed manufacturing, grinding is a standard procedure for particle size reduction to make ingredients suitable for animal feeding and digestion The principle of Size reduction in feed technology and methods for determining Grinding in ball mills is an important technological process applied to reduce the size of particles which may have different nature and a wide diversity of physical, mechanical and chemical Grinding in Ball Mills: Modeling and Process Control Sciendo2018年6月1日 Experimental results reported in this article showed that the grinding media diameter should be matched according to the feed and desired product size distributions For Effect of ball and feed particle size distribution on the milling
.jpg)
Cyclones Resource Book
The pipe is extended into the body of the cyclone by a short, removable section known as the vortex finder, which prevents shortcircuiting of feed directly into the overflow The feed is 2016年6月6日 By combining with SAG discharge and screening on the SAG discharge screens, top size control to the ballmill circuit feed is maintained while still unloading the SAG circuit SAG Mill Grinding Circuit Design 911Metallurgist2012年6月1日 As the cylinder starts to rotate, the grinding balls inside the cylinder crush and grind the feed material, generating mechanical energy that aids in breaking bonds, activating Grinding in Ball Mills: Modeling and Process Control ResearchGateIn this paper, an intelligent optimal control method with twolayer hierarchical construction is presented Based on fuzzy and rulebased reasoning (RBR) algorithms, the intelligent optimal Intelligent optimal control system for ball mill grinding process
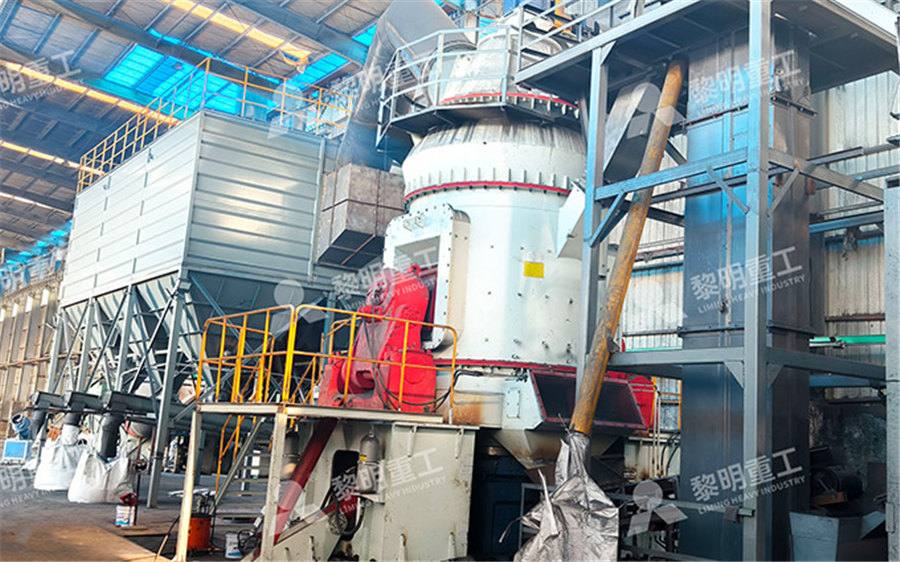
Effect of ball and feed particle size distribution on the milling
2018年2月1日 In this article, alternative forms of optimizing the milling efficiency of a laboratory scale ball mill by varying the grinding media size distribution and the feed material particle sizeGas cyclone separators are grouped into two main categories, reverseflow and axialflow Reverse flow cyclone separators are cone shaped Gas enters the top of the separator body, flows downwards, then flows back upwards and is Cyclone Separator Working Principle (Dust Separator)Keywords: Ball mills, grinding circuit, process control I Introduction Grinding in ball mills is an important technological process applied to reduce the size of particles which may have different nature and a wide diversity of physical, mechanical and chemical characteristics Typical examples are the various ores, minerals, limestone, etcGrinding in Ball Mills: Modeling and Process Control Sciendo2018年2月1日 In this article, alternative forms of optimizing the milling efficiency of a laboratory scale ball mill by varying the grinding media size distribution and the feed material particle size Effect of ball and feed particle size distribution on
.jpg)
A GUIDEBOOK TO PARTICLE SIZE ANALYSIS University of Iowa
describe the nonspherical particle seen in Figure 1 using the longest and shortest diameters, perimeter, projected area, or again by equivalent spherical diameter When reporting a particle size distribution the most common format used even for image analysis systems is equivalent spherical diameter on the x axis and percent on the y axis2022年3月9日 A sustainable feed industry is constantly looking for the best way to process feed, to have the best yield with use of lowest amount of energy and lowest amount of raw materials In this article we focus on the ways how to optimize the particle size in Importance and optimization of particle size in animal feed 2017年10月26日 The following are factors that have been investigated and applied in conventional ball milling in order to maximize grinding efficiency: a) Mill Geometry and Speed – Bond (1954) observed grinding efficiency to be a function of ball mill diameter, and established empirical relationships for recommended media size and mill speed that take this factor into Factors Affecting Ball Mill Grinding Efficiency2015年8月7日 To increase the overflow requires either a higher volume fed to the cyclone or a smaller underflow discharge opening As the pressure in the cyclone climbs the amount of coarser material in the overflow increases The reason that this pressure is generated is because the volume of the feed is greater than apex discharge capacityHydrocyclone Working Principle 911Metallurgist
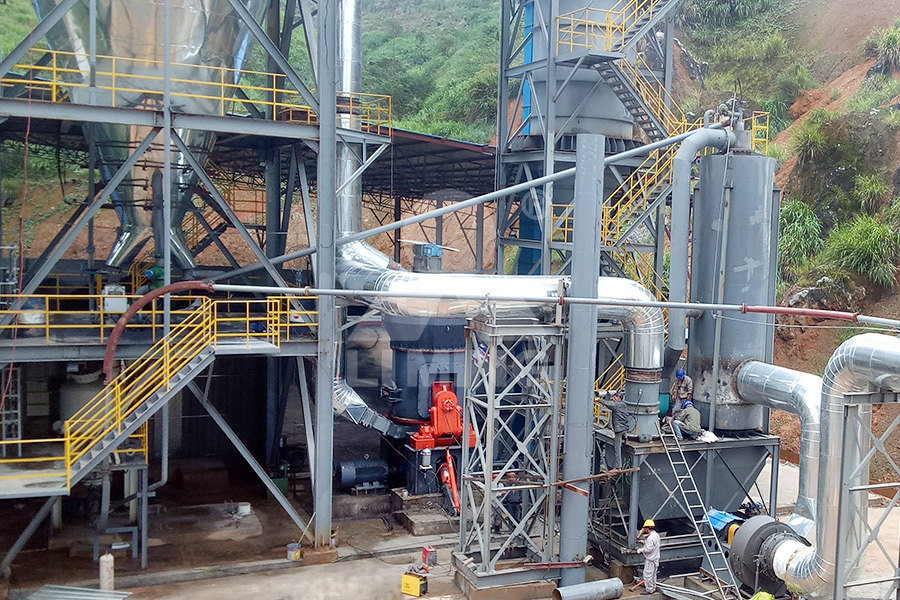
SAG Mill Grinding Circuit Design 911Metallurgist
2016年6月6日 By combining with SAG discharge and screening on the SAG discharge screens, top size control to the ballmill circuit feed is maintained while still unloading the SAG circuit (Mosher et al, 2006) A variant of this method is to direct pebblecrushing circuit product to the ballmill sump for secondary milling: while convenient, this has the disadvantage of not 2015年1月1日 Figure 2 also shows the equations representing the classical force balance acting on a spherical particle with diameter d, at a position r in the cyclone, ie, at equilibrium, the centrifugal force in the cyclone is equal to the drag force and the buoyancy forces acting on the particle, or F C − F B − F D = 0Hydrocyclones ScienceDirectParticle Size Reduction and Enlargement JF RICHARDSON, JR BACKHURST, in Chemical Engineering (Fifth Edition), Volume 2, 2002 The rod mill In the rod mill, high carbon steel rods about 50 mm diameter and extending the whole length of the mill are used in place of ballsThis mill gives a very uniform fine product and power consumption is low, although it is not suitable Rod Mill an overview ScienceDirect Topics2018年6月1日 A number of researchers (Deniz, 2012; Bwalya et al, 2014; Petrakis et al, 2016) carried out studies about the effect of feed particle size and grinding media size on the grinding kinetics of different oresKhumalo et al, 2006 postulated that generally larger sized grinding media would break larger particles quicker but a finer product would be obtained by use of Effect of ball and feed particle size distribution on the milling
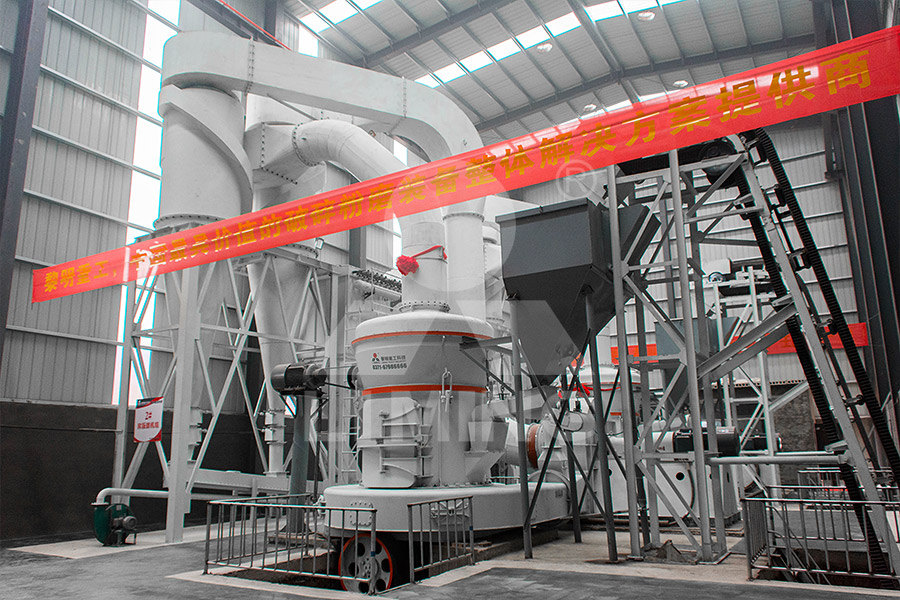
Closed Circuit Grinding VS Open Circuit Grinding
2016年10月12日 Stockpiling of ore ahead of the mill can aid in smoothing out some of the fluctuations although it must be stored in such a manner that no segregation occurs In operating a grinding circuit, like any other unit process, d50 versus 95% finer: Line graphs representing feed, underflow, and overflow [image 14523] Particle size distributions of the feed, underflow and overflow streams d 95 (overflow) = 95 microns d 95 (underflow feed) = 750; Due to AMIT 145: Lesson 2 Classifying Cyclones2015年8月15日 Cyclone separators are considered one of the most common and widely used method of separating solid particles from fluids The focus of this paper was to design a separator that could effectively Design and fabrication of cyclone separator ResearchGate2022年1月1日 High pressure grinding rolls (HPGR) technology was introduced to the minerals processing industry in the mid 1980s and has rapidly (for the mining industry) established itself as the convention in the comminution of cement, clinker, slag, iron ore, iron ore Comminution and classification technologies of iron ore
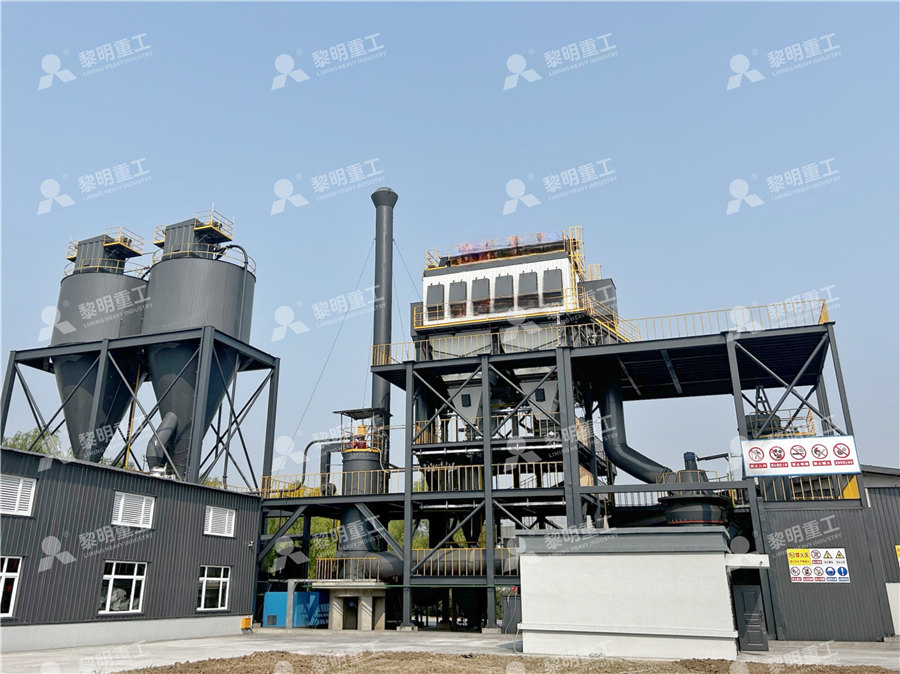
Hydrocyclone System Design SpringerLink
2021年10月14日 1011 Pulp Feeding Tank In general, the hydrocyclone feed is conveyed by a pumping system coupled to the pulp discharge from a mill The pumping system consists of a tank that receives the pulp discharge from the grinding mill, a centrifugal pump driven by an electric motor, a transmission system of pulleys and trapezoidal belts and a piping system2019年1月1日 It has another disadvantage in that wear will take place if the machine is run without any feed, because no clearance is maintained between the grinding heads and the bull ring Originally used for the preparation of pulverised coal, the pendulum mill is now used extensively in the fine grinding of softer materials such as sulphur, bentonite, and ball clay as Particle Size Reduction and Enlargement ScienceDirect1 A properly designed pneumatic discharge system can increase production as much as 300400% over gravity discharge mills when grinding light materials to a fine particle size 2 Without air, dusty material will take the path of least resistance, typically out the feed chute In a pneumatic system, dust is controlledIntro to Size Reduction Schutte HammermillThe terminal velocity of a particle in the "free" settling zone is a function of its diameter, the density difference between the particle and the fluid, and the fluid viscosity The equipment employed for gravity separation for waste treatment is normally either a rectangular basin with moving bottom scrapers for solids removal or a circular tank with a rotating bottom scraperWater Handbook Wastewater Treatment Veolia Water
.jpg)
Rod Mills: Efficient Grinding Solutions for Mining
2016年6月1日 Historically there has been three basic ways of grinding ore, hammer mills, rolls, or wet tumbling mills Hammer mills and rolls are not used that often and then usually only for special applications as in lab work or chemical preparation The type of mill that is used for grinding ore in a modern concentrator is the wet tumbling mill2017年11月1日 Size of feed particles is strongly reduced during pelleting process Consequently, digestibility of nutrients in pig feed could be improved On the other hand, presence of high quantities of fine particles in pig feed (both mash and pelleted) negatively affects the health of gastrointestinal tract (GIT) leading to higher incidence of stomach ulceration and Importance of feed structure (particle size) and feed form Google 提供的服務無須支付費用,可讓您即時翻譯英文和超過 100 種其他語言的文字、詞組和網頁。Google 翻譯2020年10月1日 The test rig was a 75mm hydrocyclone with a 15mm apex diameter and 254mm vortex finder diameter The geometric characteristics are presented in Fig 1 and the values are enumerated in Table 1The setup consisted of a hydrocyclone, a mono pump, a feed control valve, a pressure gauge and a mixing tank; the experimental setup is shown in Fig 2Influence of the feed particle size distribution on roping in
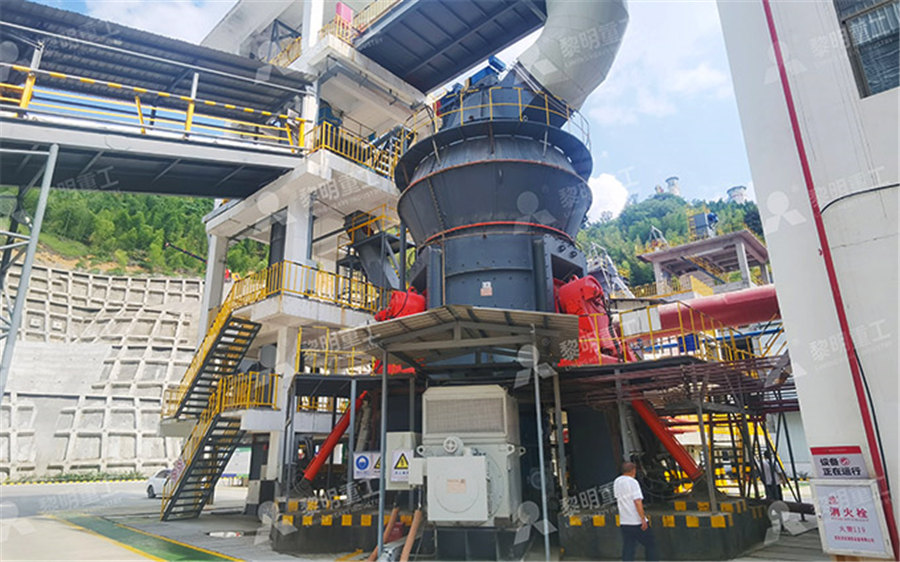
Precise control of discharge of spherical particles by cone valve
2024年1月15日 1 Introduction One of the recent focal points in granular mechanics has been the comprehension and control of particle flow under realworld process conditions [1]The movement of particles through a converging channel is a fundamental aspect of various handling and processing operations within the field of granular technology2015年6月19日 The basic parameters used in ball mill design (power calculations), rod mill or any tumbling mill sizing are; material to be ground, characteristics, Bond Work Index, bulk density, specific density, desired mill tonnage capacity DTPH, operating % solids or pulp density, feed size as F80 and maximum ‘chunk size’, product size as P80 and maximum and finally the type of Ball Mill Design/Power Calculation 911Metallurgistinstance, accelerating chutes are employed to feed bulk materials from slow moving belt or apron feeders onto conveyor belts In other cases, transfer chutes are employed to direct the flow of bulk material from one conveyor belt to another, often via a three dimensional path TheCHUTE DESIGN CONSIDERATIONS FOR FEEDING AND TRANSFER2020年3月1日 Effect of differently expressed feed particle size on the feed conversion ratio of weaned pigs and fitted linear equations (data from Ohh et al, 1983) Download: Download highres image (157KB) Download: Download fullsize image; Fig 9Size reduction in feed technology and methods for determining
.jpg)
Size reduction in feed technology and methods for determining
2019年11月1日 In conclusion, the determination, expression and prediction of particle size can be a new direction for controlling the grinding process in the feed mill to better explain its relationship with Google 提供的服務無須支付費用,可讓您即時翻譯英文和超過 100 種其他語言的文字、詞組和網頁。Google 翻譯rougher head feed is a combination of multiple ball mill hydrocyclone overflows and, therefore, does not represent the performance of any individual ball mill circuit Thus, the rougher head stream samples cannot be used in a ball mill control strategy for realtime particle size controlGrind process control using realtime tracking of +150um coarse What diameter of cyclone do we need to treat 0:177 m3s 1 of feed, given: I f = 1:8 10 5 Pas I ˆ f = 1:2 kgm 3 I ˆ S = 2500 kgm 3 I P = 1650 Pa I x 50 desired is 08 m I Eu = 700 I Stk 50 = 6:5 10 5 Hint: if we use 1 cyclone, the pressure drop will be too high; so we must split the feed into multiple, parallel cyclones So then, howSeparation Processes: Cyclones
.jpg)
Cyclones Resource Book
discharge hopper or speeding up the cyclone feed pump) will also change the pressure Within limits, an increase in operating pressure will cause the cut point to drop (finer overflow) This is because the centrifugal force on the particles is increased, forcing more fine particles to2017年9月1日 With the continual depletion of high grade simple ore bodies, more complex, finely disseminated ore bodies are being processed, which has led to an increase in the prevalence of fine grinding (Sinnott et al, 2006)This has been evident in the platinum group element (PGE) industry in South Africa, where the Bushveld Complex hosts 70% of global Fine grinding: How mill type affects particle shape characteristics Mill Type Overview Three types of mill design are common The Overflow Discharge mill is best suited for fine grinding to 75 – 106 microns; The Diaphram or Grate Discharge mill keeps coarse particles within the mill for additional grinding and typically used for grinds to 150 – 250 microns; The CenterPeriphery Discharge mill has feed reporting from both ends and the product AMIT 135: Lesson 7 Ball Mills Circuits2017年3月4日 Ball mills are used for wet grinding iron ore, g old/copper ore, nickel ore and other ores, as wel l as lime/limestone for flue gas desulphurisat ion systems, coal and other raw materials Rod mill :SIZE REDUCTION BY GRINDING METHODS ResearchGate
36.jpg)
5 Ways to Improve the Ball Mill Efficiency Fote Machinery(FTM)
2020年1月11日 Screen the specific ore and group them according to particle size; Analyze the ore crushing resistance, and calculate the exact ball diameters required by each group of ore with the ball diameters semitheoretical formula; Guide the grinding media refilling with the principle of crushing statistical mechanics on the particle composition Keywords: Intelligent optimal control; Fuzzy control; Rulebased reasoning; Grinding process; Particle size 1 Introduction The grinding process is a runofmine ore size reduction operation used in the mineral industry to liberate the valuable minerals to be recovered by subsequent beneficiation processesIntelligent optimal control system for ball mill grinding process2007年10月1日 Size is usually defined as the average particle size distribution of individual components of feed or as the fineness of feed grinding [9] Wolf et al [22] described the specific size as coarse Feed particle size: Implications on the digestion and performance 2020年8月4日 By optimizing grinding and particlesize reduction, feed milling processes can be ma de more efficient , leading to im proved feed qu ality and overall producti vity 21 Ha mm ermills(PDF) Optimizing Feed Milling Processes for Enhanced Efficiency
.jpg)
The impact of feed treatment on the performance of broilers: A review
2017年12月1日 Commonly used treatments of poultry feed, such as pelleting, expanding or extrusion increase the physical density of the feed and lead to increased feed intake, reduced time spent feeding