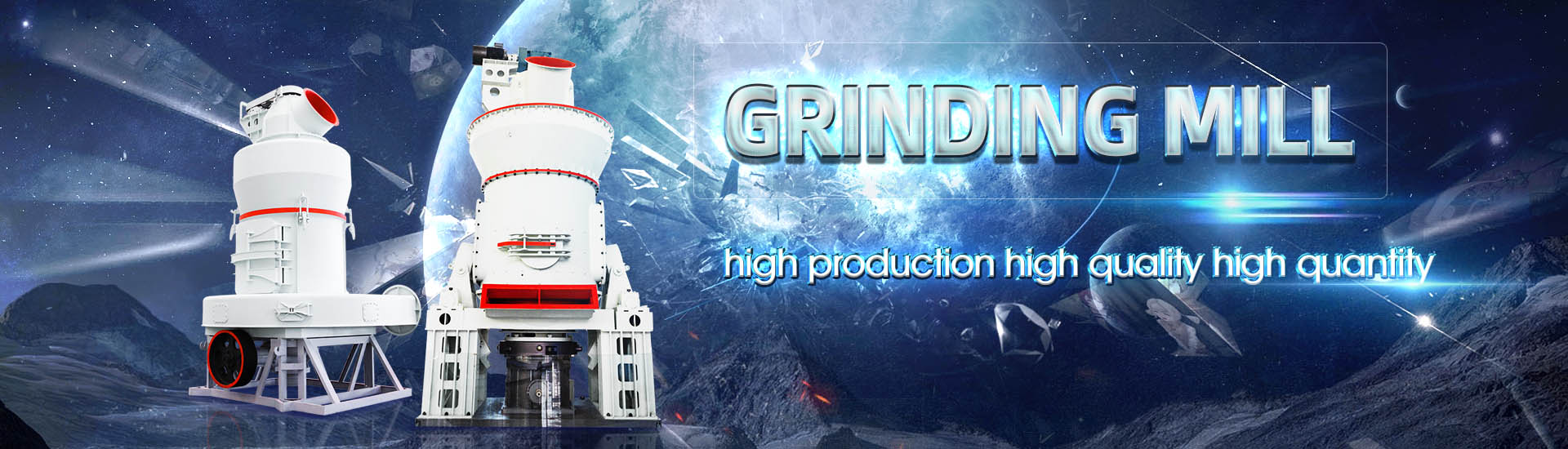
Talk about the clinker calcination of white cement and black cement rotary kiln
.jpg)
Electrification of clinker and calcination treatments in the cement
2024年5月17日 Clinker is the main ingredient and active component of cement, and its production involves the chemical decomposition of CaCO 3 into CaO, releasing CO 2 as by 2020年6月1日 The raw mix is pyroprocessed into clinker in rotary kilns with solid temperatures reaching ≈1500 °C The indurated product, termed clinker, is cooled rapidly to preserve, Thermodynamic data for cement clinkering ScienceDirectThis paper, produced by RILEM TC 282CCL on calcined clays as supplementary cementitious materials (working group 2), focuses on the production of calcined clays, presents an overview Clay calcination technology: stateoftheart review by the RILEM Considerably high false air ingress through the cold clinker discharge system outlet No leakages of CO2–rich during the trials Cooling gas recirculation contributed to a phenomenon of Process characteristics of clinker and cement production SINTEF
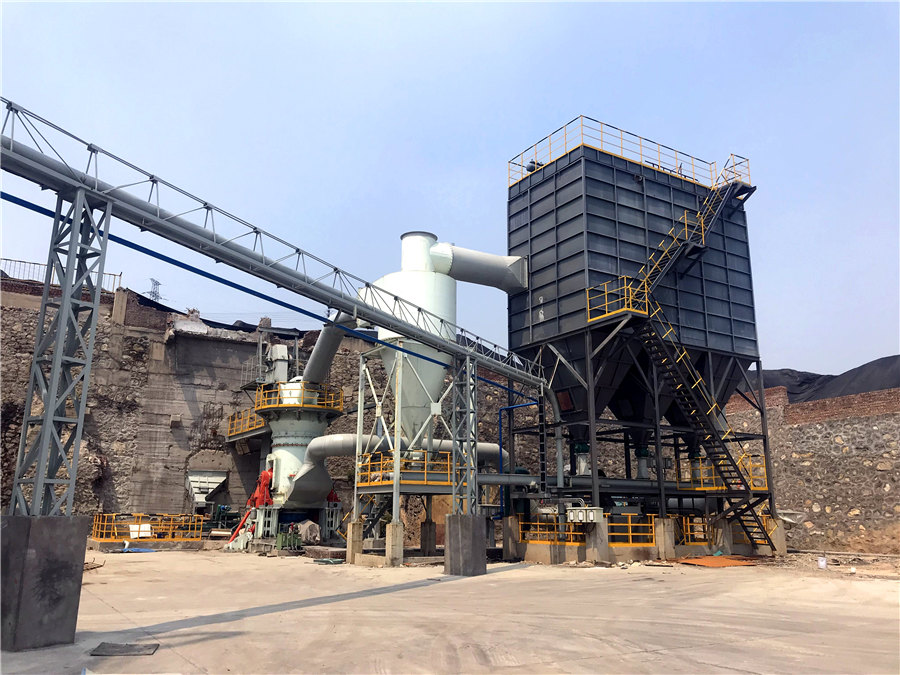
(PDF) Cement Formation—A Success Story in a Black Box: High
Clinker formations by solid state reactions, solid−liquid and liquid−liquid reactions are discussed, as are the influences of particles sizes on clinker phase formation Furthermore, a 2015年8月1日 The study showed that white cement clinker could be made from conventional raw materials by means of intensifiers or by adjusting the process in the stage of clinker cooling(PDF) The key to white cement ResearchGateAbstract: Cement rotary kiln is the core equipment of clinker firing system The system model is very important for understanding the process of cement calcination and optimizing the Firstprinciple modeling and simulation of cement rotary kiln2006年3月17日 Modern dry process plants are a combination of a fourtofivestage cyclone preheater and a precalcination followed by a short rotary kiln The description “dry” or “wet” Wet process rotary cement kilns: modeling and simulation
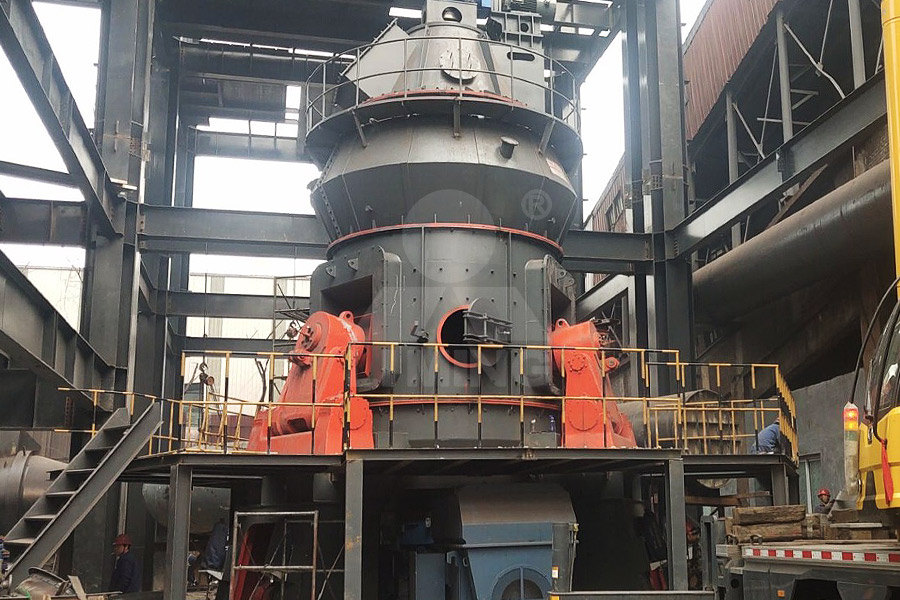
Rotary kiln process: An overview of physical mechanisms, models
Solid transport, heat transfer and thermochemical transformation are discussed in detail The heat and mass transfer modeling process in rotary kilns is summarized The commonly used What is Cement Clinker? First, let us know what a clinker is A clinker is a type of material that forms when coal or other organic materials are exposed to high temperatures in a furnace or kiln Now let us see what a cement clinker is Cement clinker is a type of substance formed during the cementmaking processCement Clinker: Types and Uses of Cement Clinker JK CementEach kiln subsystem (including the preheater and clinker cooler) has an important bearing on the time and temperature required for passage through the sintering zone to get clinker that will produce high quality cement KILN Everything you need to know about Kiln System The process of making cement clinker uses a lot of energy and produces a lot of pollution Currently, cement companies use a combination of traditional fossil fuels and alternative fuels (AFFuels Schematics of the clinker calcination process
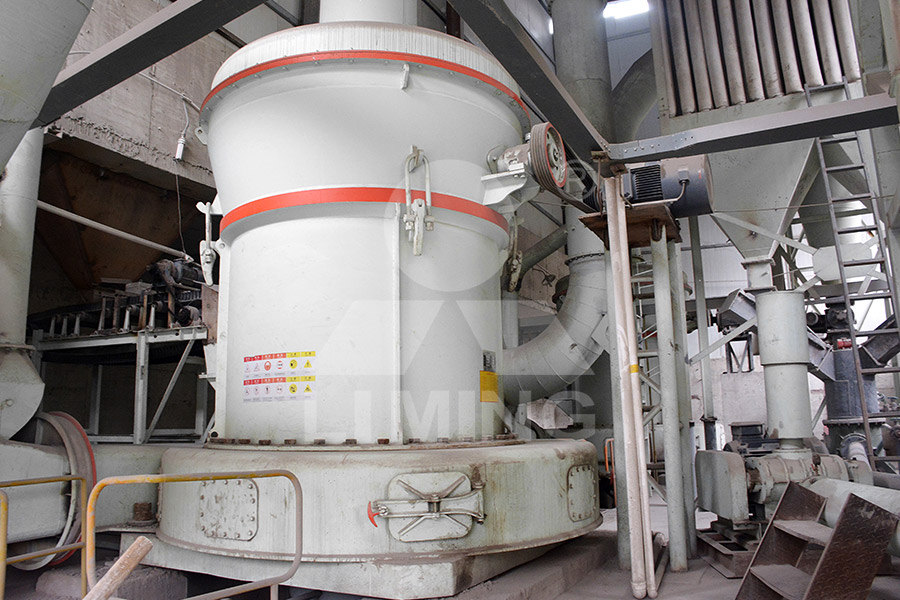
White cement manufacturing process
White cement manufacturing process White cement is a type of special cement, belongs to decoration cementIn general, Portland cement is greyishgreen, as the name suggested, white cement is white In the cement manufacturing process, in order to avoid the mixing of colored impurities, calcination of white cement plant mostly use natural gas or heavy oil as fuel Working Principle: Feeding: Raw materials (cement clinker, fuel, and auxiliary materials) enter the rotary kiln from the feeding port, forming a material layer; Rotary Motion: The rotary kiln begins to rotate, and the material gradually slides down and moves forward under the action of gravity and centrifugal force; Drying, Preheating, Calcination, and Cooling: Fuel is sprayed from the kiln Cement Rotary Kiln Structure Working Features MC2020年5月16日 All things about cement clinker calcination in the cement production process Clinker Calcination Datis Export Group Cement Clinker Production The cement industry is an indispensable basic raw material industry for national economic development, production construction, and people’s livelihoodClinker Calcination Datis Export GroupIn cement plant construction, the cement rotary kiln and vertical shaft kiln is the main cement kiln we adopt They are very different in calcination methods and properties Next, we will look at these two cement kilns in detail What Is Cement Rotary Kiln? Cement rotary kiln can be divided into the dry method rotary kiln and wet method rotary Cement Rotary Kiln Vertical Shaft Kiln Kiln In Cement Plant
.jpg)
Rotary Kiln And Dryer Cement Rotary Kiln Rotary Kiln Dryer
On the contrary, the cement rotary kiln is mainly used for hightemperature applications, the purpose of which is to cause physical changes or chemical reactions of materials Different from the rotary dryer, cement rotary kiln is usually set in the clinker calcination stage of 2021年12月20日 Fig 4 Thin section images of calcined clay mixtures after largescale calcination processing in a rotary kiln; maximum material temperature in the rotary kiln: 750 C( a ) and 930 C( b )[ 41 ]Clay calcination technology: stateoftheart review by the 2018年4月19日 A number of samples from the preburning zone of a wetprocess cement rotary kiln were examined by combined DTA/TG and XRD for estimation of spurrite (2Ca2SiO4CaCO3)Calculation of the formation process of clinker inside the rotary 1971年8月17日 subsequent mechanical processing operations to form gray and white portland cement Gray portland cement is used for structural applications and is the more common type of cement produced White portland cement has lower iron and manganese contents than gray portland cement and is used primarily for decorative purposes116 Portland Cement Manufacturing US EPA
.jpg)
Effect of different calcination temperatures on clinker and
2024年11月2日 The cement industry produces the highest CO 2 emissions after the electricity, iron, and steel industries Among the various types of cement, Portland cement (PC) is the most widely used PC production consumes considerable amounts of natural resources and energy while also accounting for up to 8 % of CO 2 emitted into the atmosphere [4] Cement rotary kiln A cement rotary kiln is a laterally set cement kiln that is inclined to a certain angle with the ground Raw meals in the kiln body will be calcinated in a lowspeed rotation In present cement plants, the new dry Cement Kiln Cement Rotary Kiln AGICO Cement 2002年1月1日 Part 1 of this paper presented a onedimensional model for describing and simulating limestone calcination in rotary kilns The model was successfully validated on a pilot rotary kiln by comparing (PDF) Modeling and simulation of limestone calcination in rotary 2019年7月1日 Cement clinker calcination in rotary kiln is an energy intensive process Heat recovery from the kiln shell surface is a potential way to improve energy efficiency to make cement production cleaner and more sustainable In this work, methods were proposed to assess the heat loss through the kiln shell and its influencing factors, using an industrial cement kiln in Improving the sustainability of cement clinker calcination
.jpg)
Electrification of clinker and calcination treatments in the cement
DOI: 101016/jconbuildmat2024 Corpus ID: ; Electrification of clinker and calcination treatments in the cement sector by microwave technology – A review @article{Vermeiren2024ElectrificationOC, title={Electrification of clinker and calcination treatments in the cement sector by microwave technology – A review}, author={Jules 2023年7月20日 We investigated the effects of calcination temperature (950–1 450 °C), steel slag content, and the total chromium content of steel slag on the Cr6+ contents of clinker samples produced using steel slags with different chromium contents Additionally, the reactions of chromium in clinker (produced using steel slag) during calcination were studied It is found that Reactions of Chromium during the Calcination of Cement Clinker Cement rotary kiln is the core equipment of clinker firing system The system model is very important for understanding the process of cement calcination and optimizing the operating conditions In this paper, a detailed firstprinciple model is proposed, which can describe the change of temperature field and material density field in kiln By studying the production Firstprinciple modeling and simulation of cement rotary kiln2021年11月25日 Thus, the application of ANN for rotary kiln identification can be advantageous is this case [4, 10] In this paper, the rotary kiln has been identified by using MLP algorithm of ANN, the input/output variables, as well as the data used in modeling, have been used for the training, testing and validation of the networkIdentification and Modeling of a Rotary Kiln in Cement Plant

Deep decarbonisation of industry: The cement sector Europa
product The materials are then fed into a rotary kiln, where they aggregate to form clinker at 1450oC (and flame temperatures reach 2000oC) (6) The clinker is then cooled, ground and blended with other materials to make cement The combustion of fuels to heat cement kilns is responsible for 35% of clinker’s carbon footprint TheThis paper deals with the energy and exergy analysis of a wet type rotary kiln system working in a white cement plant in South India The kiln has a capacity of 120 tonnes of clinker per day The slurry used for this process contains 40% of water The ENERGY AND EXERGY ANALYSIS OF A WHITE CEMENT KILN P 2024年5月1日 The two main CO2 contributors in this process are fossil fuel combustion to heat the rotary kiln and the chemical reaction associated with the calcination process, in the production of the clinker Electrification of clinker and calcination treatments in the cement 2021年5月1日 An ICal 8000 high precision calorimeter provided by Calmetrix was used to measure the heat evolution of the white cement clinker White cement clinkers that passed through the 75 μm sieve were mixed well with 5 wt% gypsum in an agate mortar The 50 g cement was placed into a plastic cup Then, it was mixed well with 25 g water for 30 sEffect of ZnO on the whiteness of white Portland cement clinker

What is Cement Clinker? Composition, Types Uses
Clinker is a nodular material produced in the kilning stage during the production of cement and is used as the binder in many cement products The lumps or nodules of clinker are usually of diameter 325 mm and dark grey in color It is produced by heating limestone and clay to the point of liquefaction at about 1400°C1500°C in the rotary kiln 2007年5月1日 This paper presents an integrated reaction engineering based mathematical model for clinker formation in cement industry Separate models for preheater, calciner, rotary kiln and cooler were Rotary Cement Kiln Simulator (RoCKS): Integrated ResearchGate2023年2月25日 The rotary kiln is used in many solid processes, including drying, incineration, heating, cooling, humidification, calcination and reduction This widespread application can be attributed to factors such as the ability to handle varied loads, with large variations in particle size [1]The rotary kiln is a slightly inclined steel cylinder that rests on supports (bearing rollers) Rotary kiln process: An overview of physical mechanisms, models 2020年4月20日 In this paper, a comprehensive 3D mathematical model for rotary cement kiln including heavy fuel oil combustion, hot flow, zone heat flux model for clinker formation and rotating wall was developedHEAVY FUEL OIL COMBUSTION IN A CEMENT ROTARY KILN
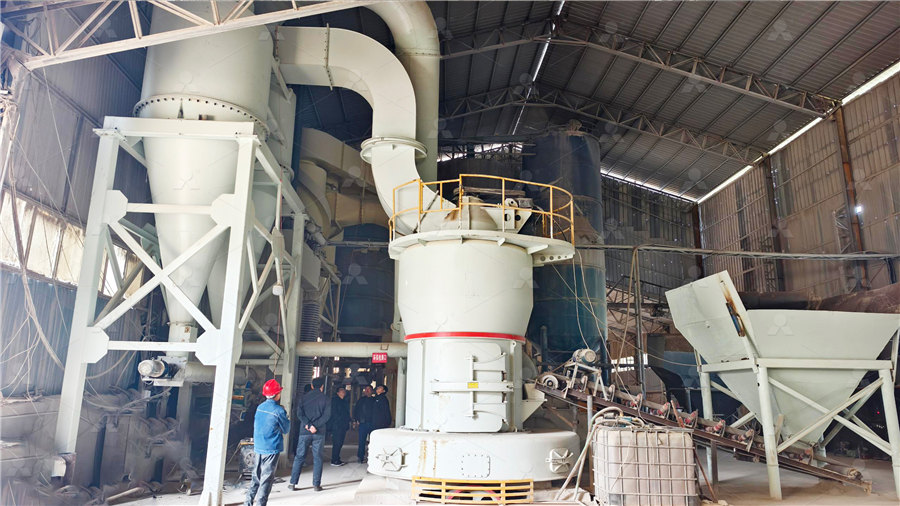
Cement Clinker Uses, Attributes, and Important Facts You Need
Cement clinker is a byproduct of cement production This material is obtained through a chemical process that produces cement clinker The byproduct is then converted into a usable material for the manufacturing of Portland cement Further, this material can be processed in different ways to produce the cement clinker Cement ProductionMujumdar KS, Ranade VV (2006) Simulation of rotary cement kilns using a onedimensional model Chem Eng Res Des 84(3):165–177 Article Google Scholar Mujumdar KS et al (2007) Rotary Cement Kiln Simulator (RoCKS): integrated modeling of preheater, calciner, kiln and clinker cooler Chem Eng Sci 62(9):2590–2607Clay calcination technology: stateoftheart review by the 2015年8月1日 Properties, manufacture and prospects of white cement were discussed Development of the methods of bleaching white cement, effect of intensifiers on clinker firing and methods of firing the white (PDF) The key to white cement ResearchGate2024年4月8日 The clinker produced in the rotary kiln is cooled and finely ground into a powder This grinding process is essential for achieving the desired fineness and consistency of the white cement Step 6: Addition of GypsumWhite Cement: Composition, Uses, and Application
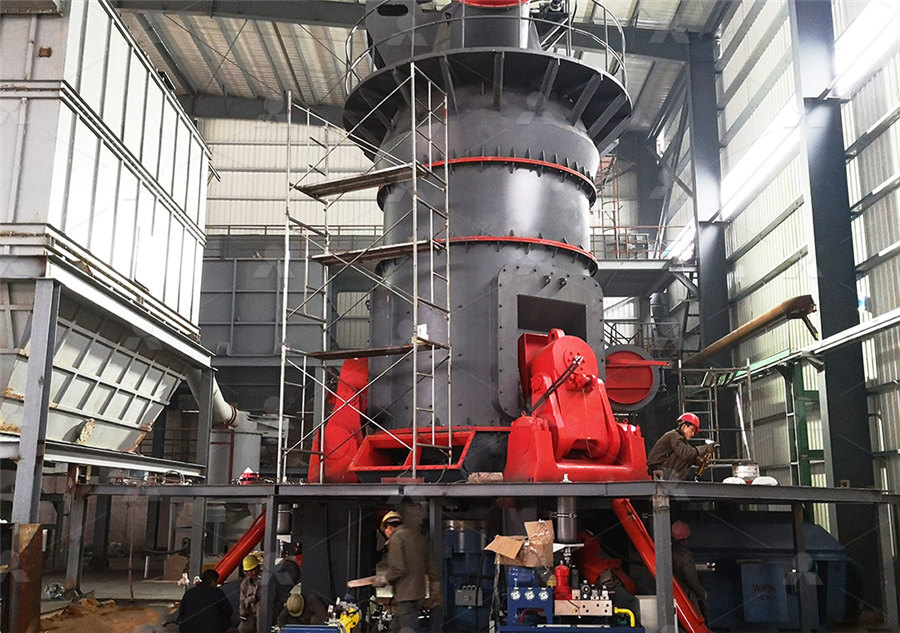
Rotary Kiln In Cement Plant Cement Rotary Kiln
People who know a little about the cement industry know that rotary kiln is the important cement equipment for processing cement clinker from raw materials It can be divided into dry process cement rotary kiln and wet process cement 2021年11月1日 Limestone calcined clay cement (LC 3) is one such recently developed ternary blended cement in which the alumina from the calcined clay and the carbonate from the limestone also react with each other, along with the traditional pozzolanic reaction of calcined clay and the filler effect of limestone, creating a synergy between the three primary components (clinker, Limestone calcined clay cement and concrete: A stateoftheart Combined calcination and CO 2 capture in cement clinker production by use of electrical energy A gastogas heat exchanger (“CO 2 HEX”) is installed toCOMBINED CALCINATION AND CO2 CAPTURE IN CEMENT CLINKER PRODUCTION BY White Cement Plant The production process of white Portland cement is quite different from ordinary Portland cement It is unique in both process flow and cement equipment selection In white cement plants, the main manufacturing process includes six steps: raw material crushing, raw material grinding, clinker calcination, clinker cooling, cement grinding, and cement packingWhite Cement Manufacturing – White Cement Plant AGICO Cement
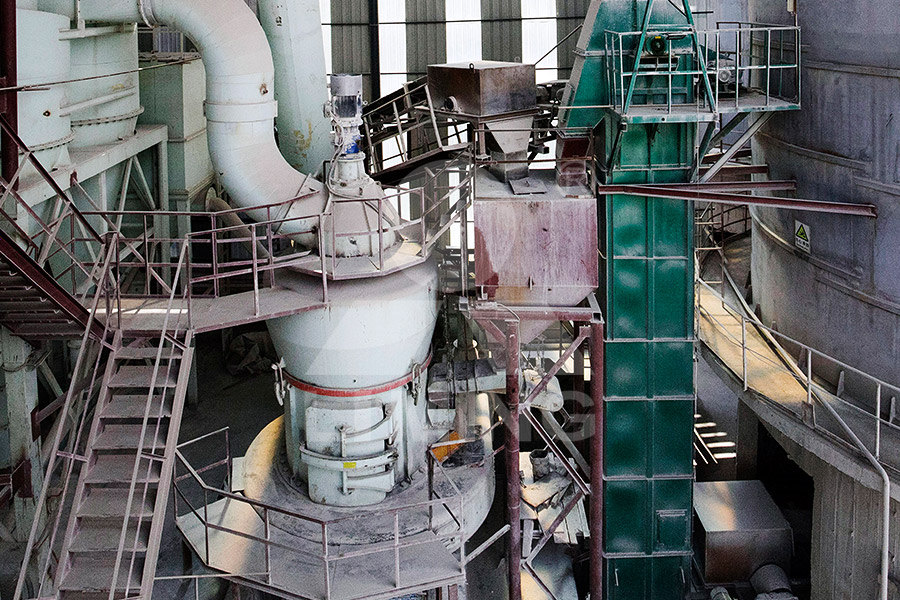
Reversephase extraction and separation of minerals in cement clinker
2021年2月8日 The emission of SO2 during cement production will lead to environmental pollution, but cement clinker has a certain effect on sulfur fixation To study the mechanism of sulfur fixation of cement clinker, we have separated the sulfurcontaining minerals in cement clinkers by the threestep method of reversephase extraction, separation and enrichment In 2013年1月1日 Studies on cement production optimisation have been carried out on clinker simulation using AspenTech [36], cement raw materials blending using a general nonlinear timevarying model [37], cement Modelling the cement process and cement clinker quality2023年7月10日 The cement manufacturing process involves the extraction and processing of raw materials, such as limestone, clay, and shale, which are then heated in a kiln at high temperatures to form clinkerCement Manufacturing Process and Its Environmental ImpactRotary cooler is one kind of cement cooler applied for cement manufacturing plantsAs an essential part of the cement kiln system, a rotary cooler is used to cool the clinker discharged from the cement rotary kilnThe rotary cooler also helps air to absorb the large amounts of heat carried by clinker, heating the combustion air up to the high temperature, strengthen the calcination, Rotary Cooler Clinker Cooler In Cement Plant AGICO CEMENT
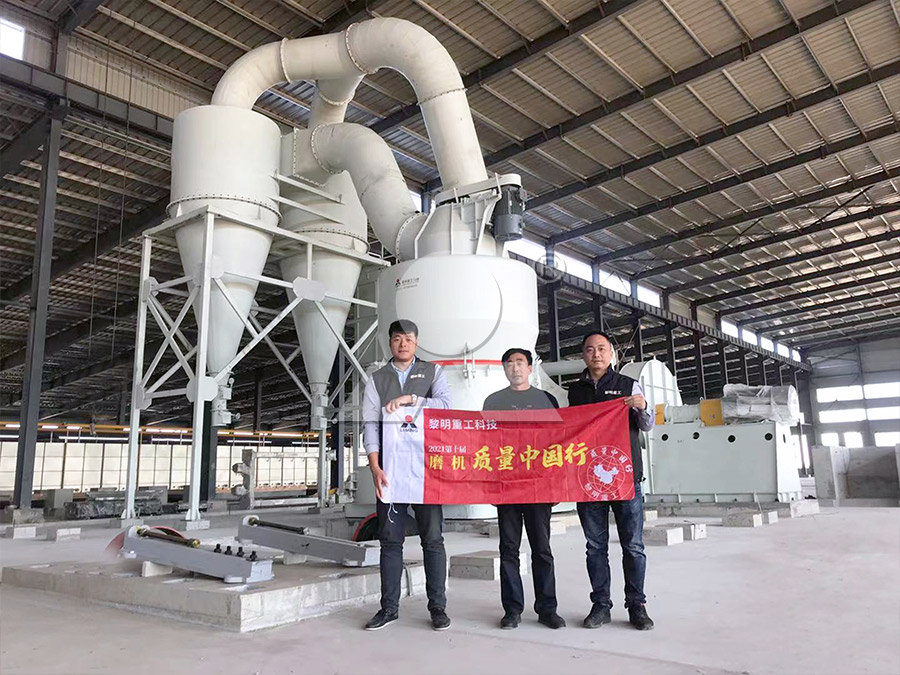
Cement Kiln, Cement Plant Kiln, Kiln In Cement Plant Shaft Kiln
AGICO CEMENT supplies cement plant kiln with high quality and competitive prices, both shaft kilns and rotary kilns are applied to the cement plant of AGICO, as a professional cement kiln manufacturer from china, we always both work on cement rotary kilns and shaft kilns, you can choose suitable types of cement kiln according to your real needs(how to buy costeffective