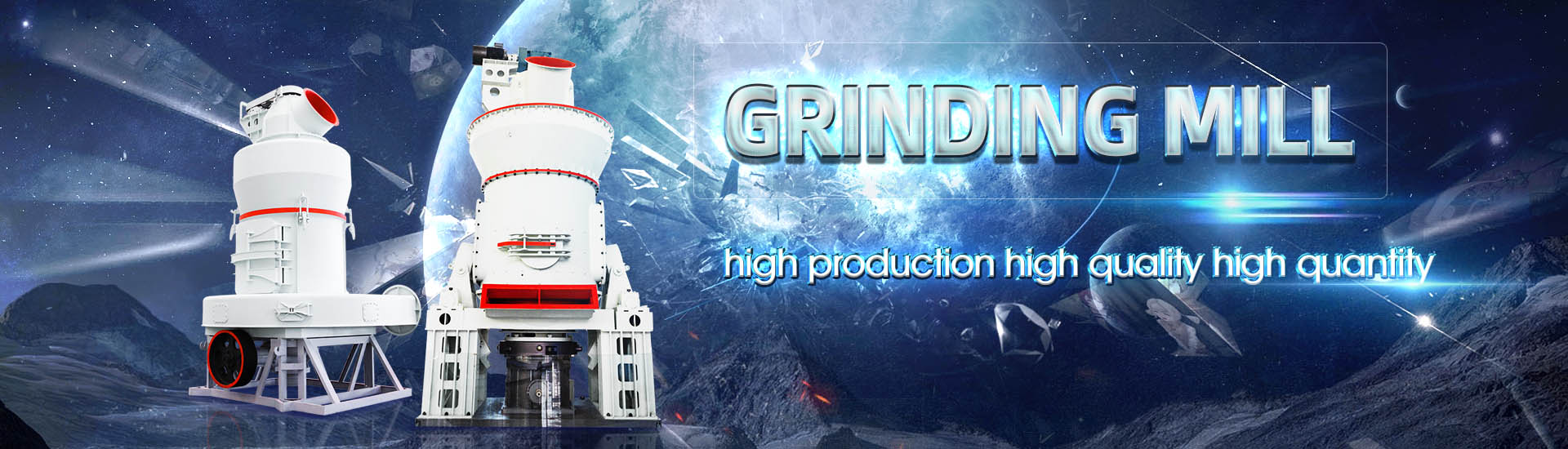
What are the desulfurization limestone price equipment companies
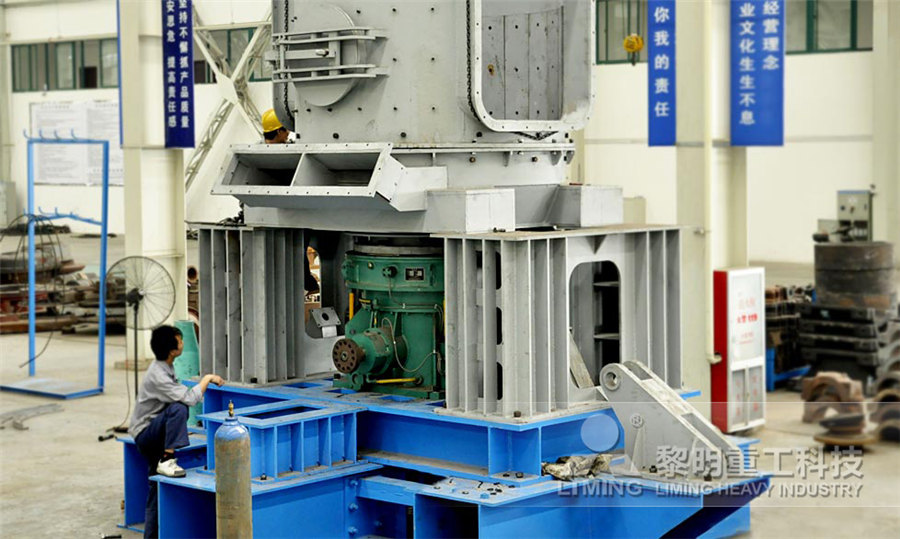
Flue Gas Desulfurization (FGD) Plants Mitsubishi Power
The flue gas desulfurization (FGD) plant removes sulfur dioxides (SO 2) from flue gas produced by boilers, furnaces, and other sources Mitsubishi Power effectively contributes to the prevention of air pollution through its wet limestonegypsum FGD process and seawater FGD process, Through meticulous spray nozzles, we treat flue gases in the FGD wet limestone process Aiming at emissions from burning fossil fuels and coal fired power stations, our system eliminates sulphur dioxide (SO2 emissions) and produces Best Flue Gas de Sulphurization System SolutionA Flue Gas Desulphurisation (FGD) system is majorly available in three variants – Wet Flue Gas Desulphurisation (WFGD), Spray Dryer Absorber (SDA) and Dry Sorbent Injection (DSI), each with distinctive capabilities for emission control Flue Gas Desulphurisation ThermaxWet flue gas desulfurization plants from Steuler Equipment Engineering work using the limestone/gypsum process, as has been standard practice in largescale power stations for decades It is probably the most effective wet DeSO x plants/ flue gas desulfurization plants Steuler
.jpg)
Wet flue gas cleaning, limestone FGD Andritz
Limestone flue gas desulphurization (FGD) units are wellproven and costeffective ANDRITZ provides novel scrubber system (FGDplus) that maximizes SO2 and dust removal while Fluegas desulfurization (FGD) is a set of technologies used to remove sulfur dioxide (SO2) from exhaust flue gases of fossilfuel power plants, and from the emissions of other sulfur oxide Fluegas desulfurization Wikipedia2009年5月1日 In a typical modern installation, the wet scrubber process is based on an aqueous slurry of lime (CaO) and limestone (CaCO3) Passing through the slurry, SO2 in the flue gas is Flue gas desulphurisation – trends and opportunitiesWet scrubbers are used in utilities, paper mills, and chemical plants to remove sulfur dioxide (SO 2) and other pollutants from gas streams Undesirable pollutants are removed by contacting Lime / Limestone Wet Scrubbing System for Flue Gas Desulfurization
.jpg)
Review of Design, Operating, and Financial Considerations in Flue
2015年7月27日 The various flue gas desulfurization (FGD) technologies available in the market, for the reduction of sulfur dioxide emissions, are presented The process descriptions are 2022年1月15日 Cui et al proposed a combination of limestonegypsum wet flue gas desulfurization (WFGD) and wet condensation desulfurization technology for enhanced Summary of research progress on industrial flue gas 2021年4月24日 ADesulfurization technology At present, there are dozens of technical process types for flue gas desulfurization and denitrification The special pump for boiler dust removal, desulfurization and denitration is divided into three types: wet, semidry, and dry according to whether water is added to the desulfurization and denitration process and the dry and wet form What are the main methods of desulfurization and denitrification Rehan Jamil, Li Ming, Irfan Jamil, and Rizwan Jamil ISSN : 20289324 Vol 4 No 2, Oct 2013 289 Fig 3 3rd Generation of wetProcess Limestone/LimeGypsum Flue Gas Desulfurization System SchematicApplication and Development Trend of Flue Gas Desulfurization
.jpg)
(PDF) A Review of Desulfurization Technology using
2015年10月30日 A Review of Desulfurization Technology using Limestone in Circulating Fluidized Bed Boiler Type Power Plant October 2015; Journal of the Korean Institute of Resources Recycling 24(5):314;Download scientific diagram Flow diagram of the limestone scrubbing method from publication: Review of Design, Operating, and Financial Considerations in Flue Gas Desulfurization Systems In Flow diagram of the limestone scrubbing methodStrict environmental laws have been put in place around the world to reduce the amount of sulfur in the fuel to reduce the emissions of harmful gases from fuel combustion and improve air quality Therefore, extensive researches have been undertaken to devise effective processes or to improve the desulfurization processes Among the desulfurization processes, the oxidative Insights to the oxidative desulfurization process of fossil fuels The establishment of decentralised power stations, and the provision, installation, and maintenance of related equipment and appliances can create entrepreneurship and employment opportunities on several fronts The DRE system could be of any type – solar, wind (or, even better, a windsolar hybrid), or biomass or biofuelbasedFlue Gas Desulphurisation Thermax
.jpg)
Flue Gas Desulfurization (FGD) Scrubber Systems
The most commonly utilized options in the industry is a flue gas desulfurization limestone wet scrubber and its equivalent based on Ca(OH)₂ In some cases, such as at coalfired power plants with high impurity content, sodium hydroxide (NaOH) solutions may be preferred due to their high reactivity; however, this option can be more costlyRecycle Semidry Flue Gas Desulphurization System Recycle Semidry Flue Gas Desulphurization Equipment For Baotou Power Plant 210MW Unit ESP, WFGD, In wet flue gas desulfurization systems, limestone or service provider you need Find a nearby distributor or reseller Contact the manufacturer to get a quote or a price Desulfurization system, Fluegas desulfurization system All Limestone Market Size Trends The global limestone market size was estimated at USD 7918 billion in 2024 and is expected to grow at a CAGR of 74% from 2025 to 2030 Growing investments in water treatment and purification activities are projected to provide push to the demand of limestone in coming yearsLimestone Market Size, Share, Growth Trends Report 年7月1日 According to the Energy Information Administration, which provides energy statistics for the US Government, power companies are projected to add FGD equipment to 141 gigawatts of capacity in Selecting the Right Pumps and Valves for Flue Gas Desulfurization
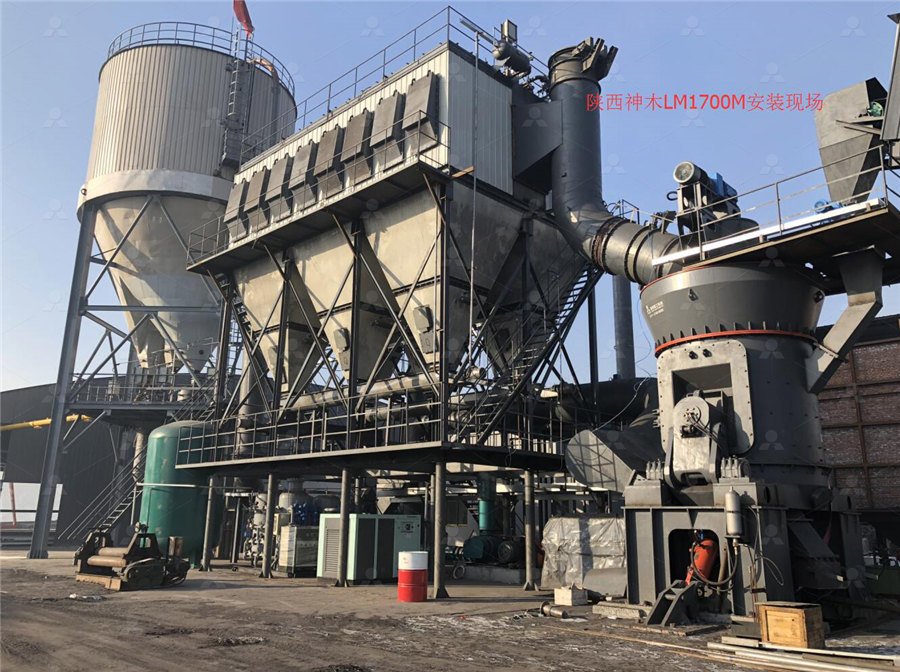
Insights into the desulfurization mechanism of lowgrade limestone
2021年12月1日 From the analysis above, it can be deduced that the desulfurization process by using lowgrade limestone as SO 2 absorbent is divided into three stages: (1) SO 2 dissolves into LGL slurry firstly followed by the formation of SO 3 2−, HSO 3 − and H 2 SO 3 species [21]; (2) continuous dissolution of Cabased compound including CaCO 3 and CaMg equipment, which concentrates the waste From the wastehandling equipment, the concentrated waste is sent for disposal (ponding or stacking) or, alternatively, processed to produce a salable gypsum (calcium sulfate dihydrate) byproduct The practical wet FGD processes are described in the following sections Limestone Forced OxidationFlue Gas Desulfurization: The State of the Art Taylor Francis 2022年1月15日 Global statistics showed in 1998 that wet limestone desulfurization was the main technology used in flue gas desulfurization in power plants, accounting for 83% of flue gas desulfurization systems [89] The limestonegypsum wet desulfurization system mainly involves the absorption section and the oxidation section This includes mud drop Summary of research progress on industrial flue gas desulfurization 2013年10月1日 Limestone slurries are widely utilized in wet flue gas desulfurization (WFGD) processes The evaluation of the reagent's reactivity is fundamental for process design and plant operationModeling Limestone Reactivity and Sizing the Dissolution
.jpg)
State of the art desulfurization technology arrives in North America
well as equipment that takes desulfurization knowledge and improvements to a new level Not only can tailormade injection blends be supplied for the most effective desulfurization processes, the company also owns a long reference list of desulfurization facilities that have been built, run and serviced The group has the discretion to call2012年3月1日 Strategies for heavy oil desulfurization were evaluated by reviewing desulfurization literature and critically assessing the viability of the various methods for heavy oil The desulfurization methods including variations thereon that are discussed include hydrodesulfurization, extractive desulfurization, oxidative desulfurization, biodesulfurization Desulfurization of heavy oil Applied Petrochemical Research2020年8月15日 Postcombustion flue gas desulfurization and denitrification technologies are essential in achieving the full compliance of fine particulate matter (PM25, aerodynamic diameter less than 25 μm) air quality standards by 2030 in China as sulfur dioxide (SO2) and nitrogen oxides (NOX) are the main precursors of PM25 Some studies have addressed the Comprehensive evaluation of flue gas desulfurization and Before flue gas desulfurization was installed, the emissions from the Four Corners Generating Station in New Mexico contained a significant amount of sulfur dioxide The G G Allen Steam Station scrubber (North Carolina) Fluegas desulfurization (FGD) is a set of technologies used to remove sulfur dioxide (SO 2) from exhaust flue gases of fossilfuel power plants, and from the Fluegas desulfurization Wikipedia
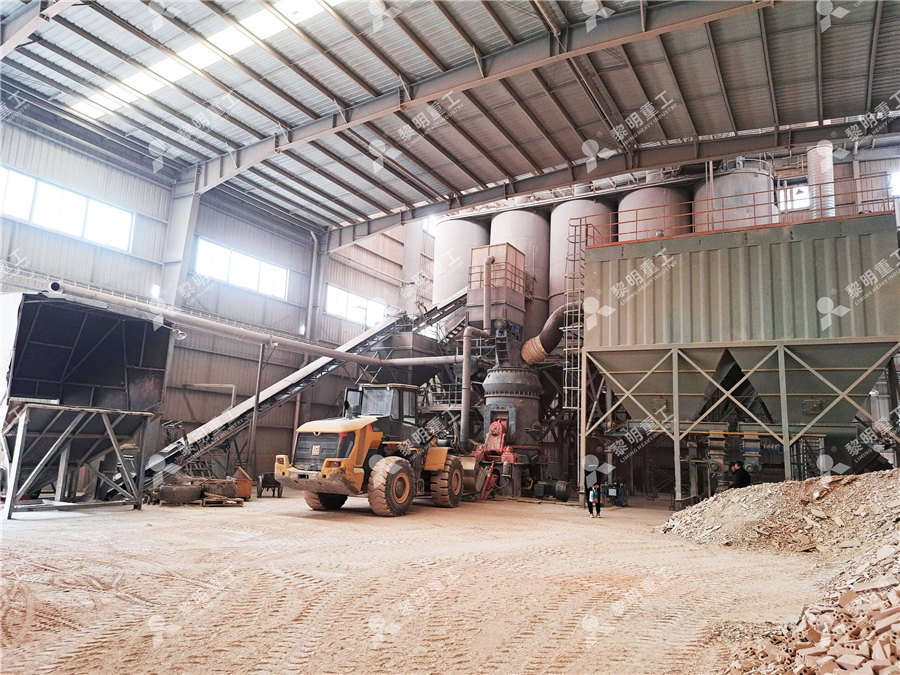
Desulphurization mechanism and engineering practice of carbide
The commonly used wet desulfurizer is limestone, which is expensive (Xu et al 2019) The carbide slag has the advantages of wide sources, low price, and similar active ingredients with limestone, so that the carbide slag can be used for replacing the traditional limestone desulfurization to reduceThermal power plant desulfurization equipment Limestone powder for desulfurization generally requires a particle size of 250 mesh or 325 mesh, and 325 mesh limestone powder has better desulfurization effect The preparation of this fineness limestone powder is basically a vertical mill or a European millWhat are the desulfurization processes in thermal power plants?However, when it comes to this process, it’s essential for companies to ensure they are selecting the proper seal, as this is critical in maximizing the operational performance of equipment Below is an explanation of slurry types, as well as Slurry Applications in The Flue Gas Desulfurization Wet FGD system using limestone as the sorbent Most wet FGD systems use a limestone sorbent that is prepared by first crushing the limestone into a fine powder using a ball mill and then mixing the powder with water in the slurry preparation tank Particle size of the limestone impacts the efficiency of SO2 removal In theA review wet flue gas desulfurization by the use of limestone
.jpg)
What are the process flows of desulfurization and denitrification
The absorbent uses seawater, so there is no absorbent preparation system The absorption system does not scale or block No desulfurization slag is generated after absorption, which eliminates the need for desulfurization ash treatment facilities The desulfurization rate can be as high as 90%, and the investment and operating costs are low2009年5月1日 In a typical modern installation, the wet scrubber process is based on an aqueous slurry of lime (CaO) and limestone (CaCO3) Passing through the slurry, SO2 in the flue gas is removed, via a complex series of chemical reactions, to produce calcium sulphate (gypsum) and sulphite salts – what is known as the limestone gypsum processFlue gas desulphurisation – trends and opportunities2001年5月19日 A detailed process model of the wet limestone flue gas desulfurization system has been presented This model can be used to calculate indispensable parameters for estimating costs and next to minimize capital and operating costs The process model describes most important stage of SO2 removal running in an absorber and a holding tank It includes Model of the Wet Limestone Flue Gas Desulfurization Process 2020年11月11日 Wet flue gas desulfurization was simulated to improve gypsum production using lowgrade limestone Highgrade limestone with 94 wt% CaCO3 content is used for producing gypsum with 93 wt% purity, but owing to the resource depletion of highgrade limestone, lowgrade limestone should be replaced as an alternative However, lowgrade Modeling of the wet flue gas desulfurization system to utilize low
.jpg)
LimestoneGypsum FGD Wet Desulphurization
Limestonegypsum desulfurization process is one of the most widely used desulfurization technologies in the world About 90% thermal power plants in Japan, Germany, and the United States adopted this technology for the flue gas desulfurization Part2 2 Working PrincipleChina Biogas Desulfurization wholesale Select 2024 high quality Biogas Desulfurization products in best price from certified Chinese Biogas Plant manufacturers, Biogas Engine suppliers, wholesalers and factory on MadeinChina your Biogas Desulfurization MadeinChinaparticles formed during the desulfurization is CaSO 4 With the increase in SO 2 concentration, the fine particle emission has little difference The fine particles formed during desulfurization are mainly from the entrainment and evaporation of desulfurization slurry Keywords Limestone–gypsum desulfurization Fine particles Characteristic Fine Particle Characteristics from Limestone– Gypsum Desulfurization The picture provides a simplified flowchart of such a plant, in this case the twostage KRC flue gas desulfurization process With this process, the sulfur dioxide (SO2) contained in the flue gas is absorbed chemically in an aqueous washing suspension of limestone (CaCO3), quicklime (CaO), or slaked lime (Ca(OH)2) according to the simplified Flue Gas Desulfurization EKATO
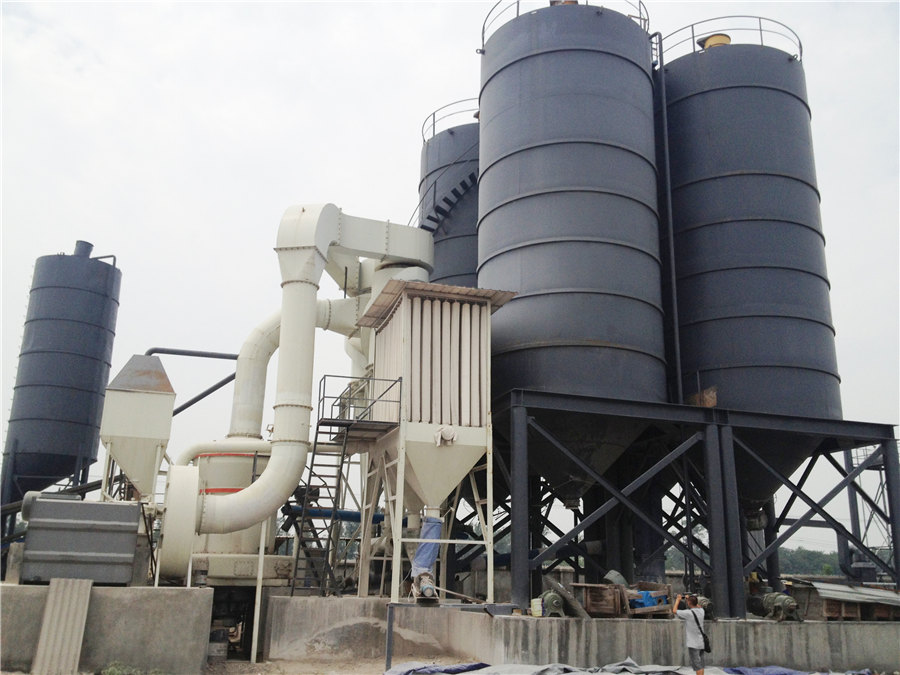
Application of the Lime/Limestone Flue Gas Desulfurization Process
equipment for SO2, acid mist or stack fume control Air Pollution Control Equipment To control both the particulate and the SO2 emissions from the air pollution sources in nonferrous metal smelting, PPSI has developed three different equipment configurations The October 1980 Volume 30, No 10 年5月11日 Limestone surry scrubbing with production of CaSOâ/CaSOâ waste solids is the dominant commercial technology for fluegas desulfurization The rate of limestone dissolution directly determines Limestone dissolution in flue gas desulfurization ResearchGate2002年1月1日 Further, of the wet limestone processes, limestone forced oxidation (LSFO) has been used most often in recent applications The SO2 removal performance of scrubbers has been reviewedFlue Gas Desulfurization: The State of the Art [J]2020年5月16日 Numerous mitigation techniques have been incorporated to capture or remove SO2 with flue gas desulfurization (FGD) being the most common method Regenerative FGD method is advantageous over other methods due to high desulfurization efficiency, sorbent regenerability, and reduction in waste handling The capital costs of regenerative methods are Sulfur dioxide removal: An overview of regenerative flue gas
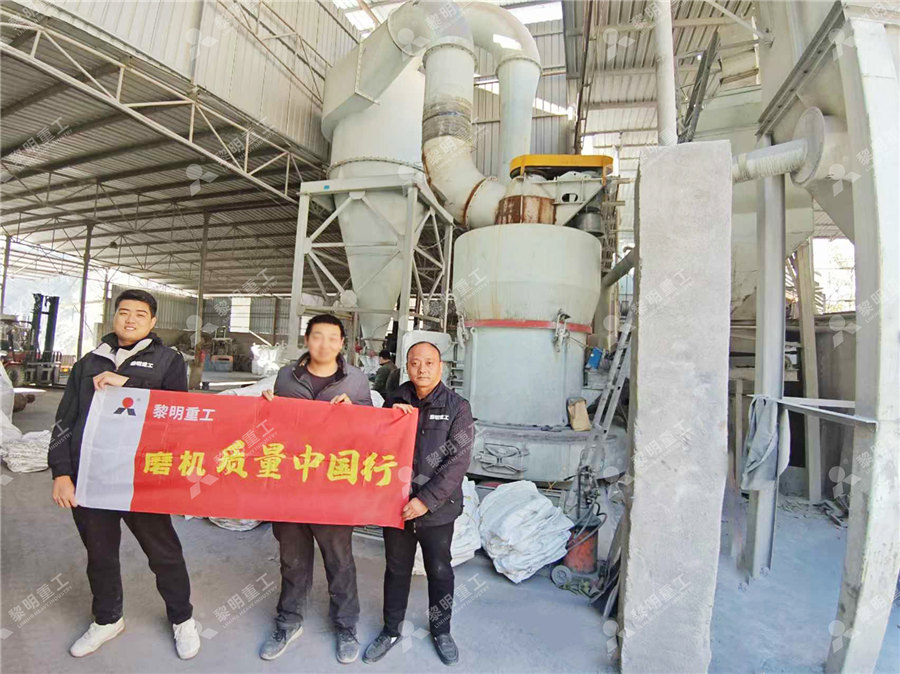
Flue Gas Desulfurization System Market MarketsandMarkets
2024年8月22日 The demand for chemicals has experienced severe shocks across end markets, with global supply chains being disrupted Due to this, the stock prices revenue of major chemical companies have taken significant hits, thus delayed investment on new FGD systems installation Flue Gas Desulfurization Systems Market DynamicsRequest PDF Impacts of the desulfurization price subsidy policy on SO2 reduction: Evidence from China's coalfired power plants Administrative and orderbased environmental regulation policies Impacts of the desulfurization price subsidy policy on SO2 2022年7月11日 Desulfurization techniques process and future challenges for commercial of crude oil products: Review(PDF) Desulfurization techniques process and future challenges 2022年7月14日 The carbide slag has the advantages of wide sources, low price, and similar active ingredients with limestone, so that the carbide slag can be used for replacing the traditional limestone desulfurization to reduce the desulfurization cost and solve the problem of a large amount of carbide slag stacking; and meanwhile, the carbide slag can also capture CO 2 Desulphurization mechanism and engineering practice of carbide
.jpg)
Recent advances in process and materials for dry desulfurization
(2) Furnace injection technology is the most popular source control technique of sulfur owing to its simple crafts/equipments and low costs of limestone/lime, and the optimization of injection process (eg, location, powder spray equipments), reduction of limestone/lime particle size, addition of additives with catalytic function may further enhance the removal efficiency of sulfur 2006年8月1日 A generic wetlimestone flow diagram is outlined in Figure 1 (The diagram also applies for systems using hydrated limeCa(OH 2)as the reagent, where equipment and vessel sizes are smaller)Wet WetLimestone Scrubbing Fundamentals Power Engineering