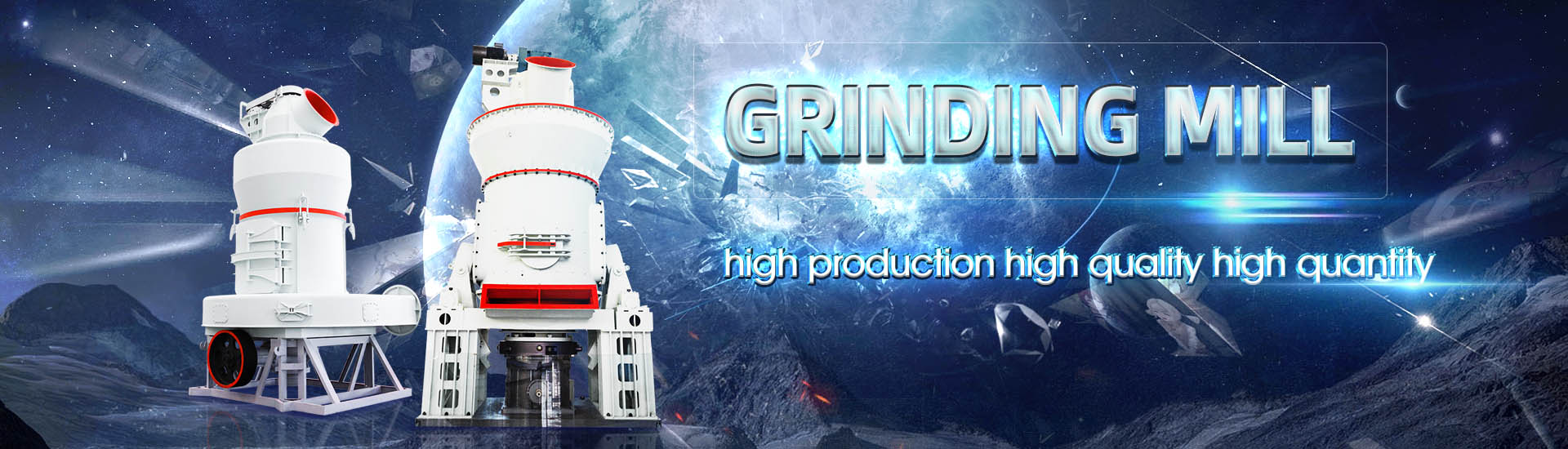
Raw material vertical mill operation method
.jpg)
Operational parameters affecting the vertical roller mill
2016年9月1日 VRM data from a steady plant process operation, such as raw material output, material moisture, kiln hot gas, mill fan flow, grinding pressure, and separator speed, was used Vertical roller mills are adopted in 20 cement plants (44 mills) in Japan In the vertical roller mill which is widely used in the raw material grinding process, raw materials input grinding table Vertical roller mill for raw Application p rocess materials2017年9月11日 In this study, an extensive sampling study was carried out at vertical roller mill of ESCH Cement Plant in Luxemburg Samples were collected from mill inside and around the circuit to(PDF) Performance Evaluation of Vertical Roller Mill in 2017年4月1日 Vertical roller mills (VRM) have found applications mostly in cement grinding operations where they were used in raw meal and finish grinding stages and in power plants Operational parameters affecting the vertical roller mill
.jpg)
Numerical Investigation of Vertical Roller Mill Operation Using
2023年12月4日 This study investigated the effect of table speed (mill speed), roller and table gap, dam ring height, and rolling resistance of material using the discrete element method in 2022年1月23日 There are usually four kinds of VRMs in the cement production line, including raw meal mill, coal mill, Clinker Mill and cement mill, and the vertical mill occupies a large energy consumption unit Therefore, it is Analysis and Optimization of Grinding Performance of Abstract—It is difficult to effectively control the vertical grinding process of raw materials due to its characteristics of strong coupling, nonlinearity and large hysteresis This paper proposes a Intelligent Control System Design for Vertical Mill Based on Data 2024年1月17日 Vertical roller mills, VRMs, are widely used for grinding raw materials in factories engaged in the extraction and processing of minerals Any machine used for grinding or crushing consumesParameters for the Grinding Process in Vertical Mills
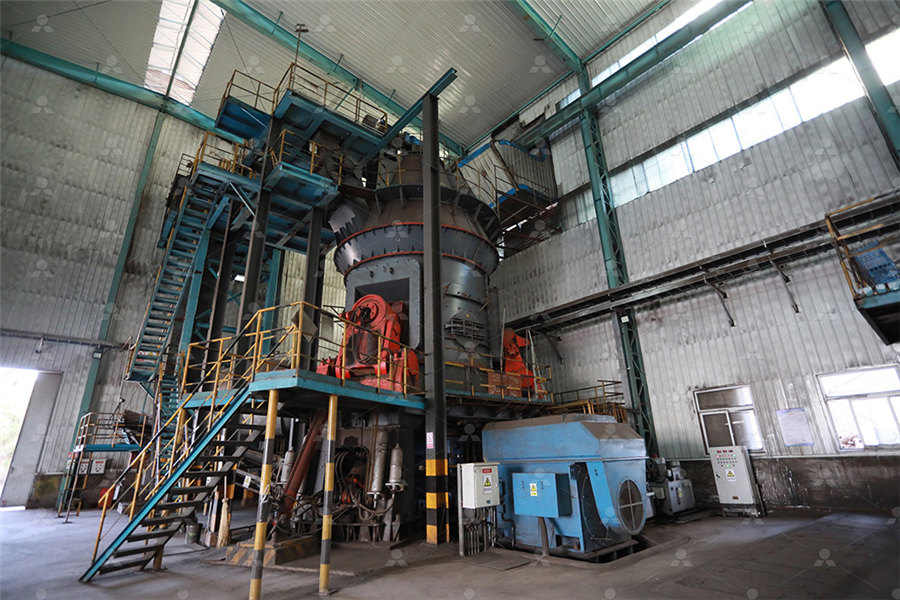
Operation parameters multiobjective optimization method of
The vertical roller mill is an important crushing and grading screening device widely used in many industries Its classification efficiency and the pressure difference determine the entire In the Windrow method, material is deposited from a number of positions With these developments of design and operation, vertical roller mills now have been operated with raw materials Brundick, H, “Drying and grinding of Everything you need to know about cement Materials is recirculated back to the mill [20] In Fig 1, shows a vertical roller mill in which the three sections mentioned above can be easily distinguished The motor, grinding table, rollers and separator are clearly visible The material and hot gas inlet ducts and the material outlet can also be seen Figure 1: Vertical Roller Mill 4 METHODOLOGY Parameters for the Grinding Process in Vertical Mills Using In addition, the raw material grinding process will be supported by a QMR² 48/24 For the 4,000 tons per day kiln line Shiva Cement Ltd contracted a quadropol® vertical roller mill for grinding pet coke with a QMK² 32/16 The same mill size quadropol® Vertical Roller Mill myPolysiusService
.jpg)
Energysaving optimization method of cement raw material vertical mill
(22) 26112019 (43) 02072020 (57) An energysaving optimization method of a cement raw material vertical mill system Safe, convenient and reasonable auxiliary decisionmaking is smartly provided by a machine learning method without changing any structure and principle of a production equipment, adding additional measuring spots and affecting normal production2017年9月11日 Due to the compact design and material transportation system of vertical roller mills (VRM), some important streams (total mill feed and discharge, dynamic separator feed and reject) remain in the (PDF) Performance Evaluation of Vertical Roller Mill inThe cement raw materials (lime, silica and iron ore) enter the circuit through two apron feeders The raw materials are crushed in a hammer crusher to D 95 of 80mm The raw materials are mixed in a certain proportion and fed into a vertical roller mill (LOESCHE mill) The vertical roller mill grinds the marital to D 85 of 90µmModeling and simulation of vertical roller mill using population DOI: 101016/japt2023 Corpus ID: ; Operation parameters multiobjective optimization method of large vertical mill based on CFDDPM @article{Huang2023OperationPM, title={Operation parameters multiobjective optimization method of large vertical mill based on CFDDPM}, author={Rongjie Huang and Yao Ma and Hao Li and Chunya Sun and Jun Liu and Operation parameters multiobjective optimization method of
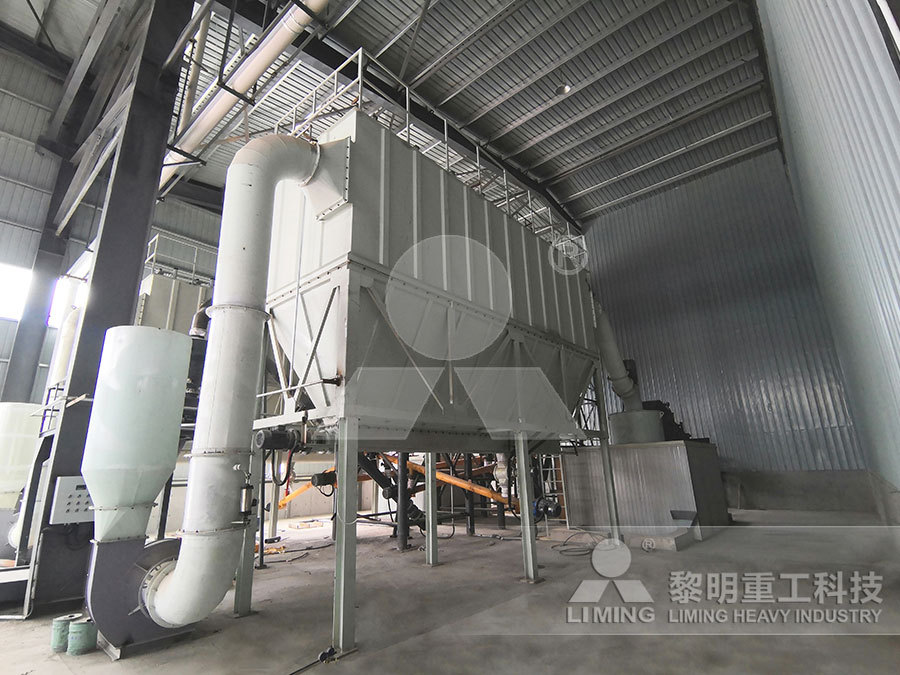
Raw Material DryingGrinding Cement Plant Optimization
Dry Grinding: Open circuit Ball mill, closed circuit Ball mill, vertical roller mill, Roll Press or Roll press in circuit with ball mill However, it would be seen that the most significant process and types used for raw material grinding operations in modern cement industry are: Process: Dry Closed circuit drygrinding Type of mill: Ball and accurately establish the model of raw material grinding process in vertical mill to optimize the control of key parameters during the process[5] The model of raw material grinding process for vertical mill has been studied indepth both at home and abroad Cai X[6] established a soft sensing model of the materialIntelligent Control System Design for Vertical Mill Based on Data 2018 In this chapter an introduction of widely applied energyefficient grinding technologies in cement grinding and description of the operating principles of the related equip‐ ments and comparisons over each other in terms of grinding efficiency, specific energy consumption, production capacity and cement quality are given(PDF) CEMENT RAW MATERIAL GRINDING ; VERTICAL ROLLER MILL OPERATION This depends on the particle size of the material The choice of haulage method depends primarily on considerations of economy This temperature is used to drying material in vertical raw mill The transport is based on the well Cement Manufacturing Process INFINITY FOR
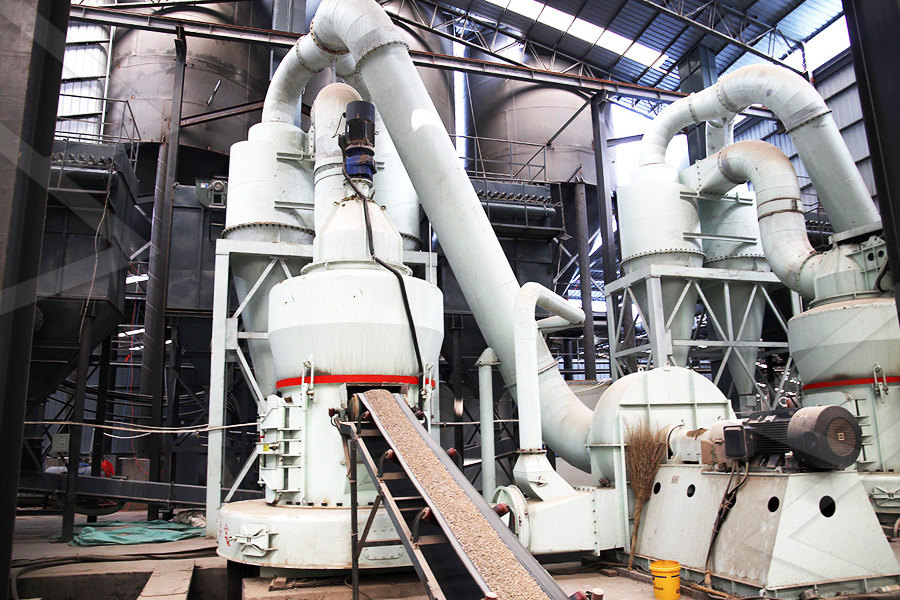
Raw Mill – Raw Mill In Cement Plant AGICO Cement
AGICO Cement Vertical Mill AGICO Cement Ball Mill Cement Vertical Mill Grinding System Cement vertical mill, also called roller mill, is another raw mill commonly used in cement pared with the cement ball mill, it has a 2019年8月4日 Raw Materials Unit Operations Equipment There are four main methods of apply ing paint: 1by spreading, Vertical ball mill; Paints Industry: Raw materials unit operationsOptimizationofVerticalRawMillOperationpdf Free download as PDF File (pdf), Text File (txt) or view presentation slides online The document discusses optimization and operation of vertical roller mills (VRMs) Key points include: 1) Continuously monitor and adjust process parameters to find the optimum operating conditions of highest capacity and lowest power consumptionOptimization of Vertical Raw Mill Operation PDF2024年7月16日 From transforming raw materials into desired shapes, milling operation plays Get Quote Services Can be performed on both horizontal and vertical milling Precision CNC milling is widely recognized as the most accurate milling operation This method combines advanced CNC technology with highprecision tools to produce parts 23 Types of Milling Operations: Learn About Milling Processes
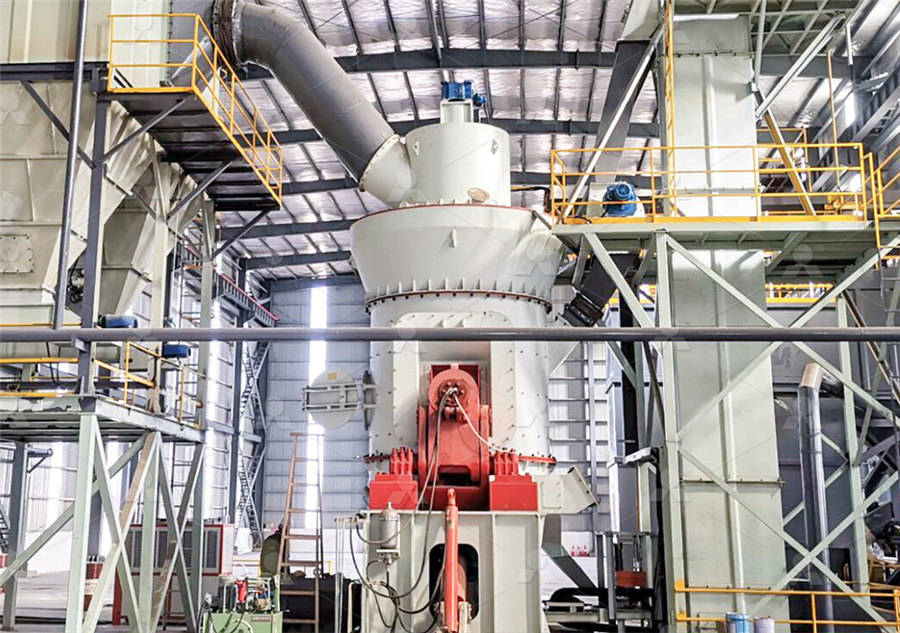
Vertical raw mill Cement Plant
Vertical raw mill is one kind of raw mill, generally used to grind bulk, granular, and powder raw materials into required cement raw meal in the cement manufacturing plantVertical raw mill is an ideal grinding mill that crushing, drying, grinding, grading transfer set in one It can be widely used in cement, electric power, metallurgy, chemical industry, nonmetallic ore, and other industries2016年6月1日 Raw meal fineness is the percentage content of 80 µm sieving residue after the cement raw material is ground The accurate prediction of raw meal fineness in the vertical mill system is very Modelling of the vertical raw cement mill grinding process based 2023年12月4日 A vertical roller mill (VRM) is a grinding equipment used for the size reduction of minerals, cement, and ceramics The capacity of the VRM depends not only on the grinding material properties but Numerical Investigation of Vertical Roller Mill Operation Using Vertical roller mill is a type of grinder used to grind materials into extremely fine powder for use in mineral dressing processes, alternative for a ball mill [1] Overview The vertical roller mill is a kind of grinding machine for cement, raw material, cement clinker, slag and coal slag Vertical roller mill Wikipedia
.jpg)
PROCESS OPTIMISATION FOR LOESCHE GRINDING PLANTS
• Cement raw material • Clinker / granulated slag • Industrial minerals, and a vertical roller mill (VRM) ously for realtime optimisation • The key to mill optimisation is stable operation of the plant Only with stable operation can greater performance be achieved and thus added value be2024年3月17日 Milling is a popular machining process Milling is a machining operation in which a revolving cutter removes material from a workpiece in a controlled manner This method of subtractive manufacturing seeks to give the 16 Types of Milling Operations Explained [with PDF]2023年6月1日 This study aims to improve the output and production efficiency of a large vertical mill by optimizing its operational parameters This paper takes a large vertical mill in LGM as the object, a numerical calculation method of particle–fluid coupling system in large vertical mill based on CFDDPM theory, and a multiobjective optimization method of operating parameters of Operation parameters multiobjective optimization method of 2011年3月1日 In order to reduce the larger pressure resistance (pressure difference between inlet and outlet) of a vertical roller mill, the flow field in the vertical roller mill is numerically simulated by CFD technology Based on the simulation results, the reasons that led to the larger pressure resistance of the vertical roller mill is studied, offering the theory guide for the Numerical Study of the Flow Field in a Vertical Roller Mill
.jpg)
Commissioning theory and practices of vertical mill for raw material
The paper described initial commissioning method of vertical mill for cement raw material from the view of theory and practice,and discussed the controlled points during commissioning of vertical mill after cement kiln runningIt also analyzed the problems occurring during operation,and proposed specific treatment approachesThe raw vertical mill of CHAENG has stable operation, high output and convenient replacement of parts It has been recognized and purchased by customers in South Asia, Africa and other markets: 1 A 5000t/d cement production line EPC turnkey project in South Africa adopts GRMR5341 raw material vertical mill of CHAENG 2Vertical Raw Mill CHAENG2022年5月31日 Consequently, a numerical simulation method of Discrete Element Method (DEM) coupled with MultiBody Dynamics (MBD) is proposed in this work to study Kisen Vertical Mill (KVM), an external circulation vertical roller mill developed by Sinoma International Intelligent Technology Co, Ltd, for a deeper understanding of grinding process in the VRM, in which Analysis of vertical roller mill performance with changes in material Feeding Amount Control of Verticle Roller Mill Mainteining material laye thicknessr is the main content of the operation control The stability of the material layer is a prerequisite for safe operation of the verticle roller mill The amount of feed in the mill can be tested by 3 methods: Grinding roller limit device clearance;How to Improve Grinding Efficiency of Vertical Roller Mill
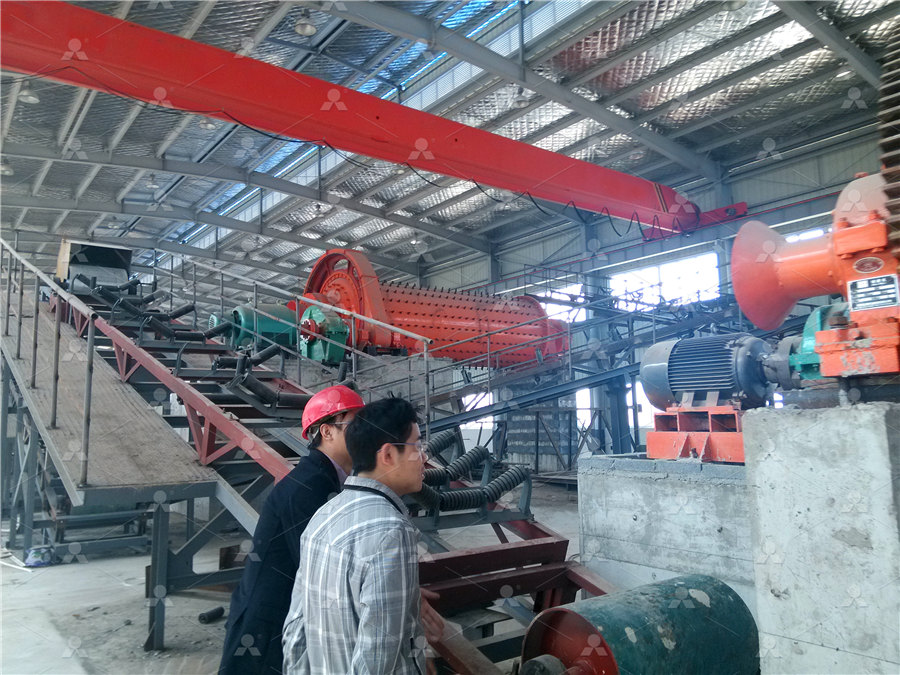
VRM Operation and Optimization PDF Mill (Grinding)
VRM operation and optimizationppt Free download as Powerpoint Presentation (ppt / pptx), PDF File (pdf), Text File (txt) or view presentation slides online The document discusses vertical mills used for grinding clinker, raw materials, coal, and cement Vertical mills can be used for both pregrinding and finish grinding They comprise rollers that are hydraulically pressed onto a 2018年9月10日 The simulator was used for the thermodynamic performance of a raw mill (RM) and raw materials preparation unit in a cement plant in Nigeria using actual operating data The raw mill has a capacity (PDF) Thermodynamic Analysis of Raw Mill in Cement2022年1月23日 This work concentrates on the energy consumption and grinding energy efficiency of a laboratory vertical roller mill (VRM) under various operating parametersAnalysis and Optimization of Grinding Performance of Vertical 2020年7月2日 An energysaving optimization method of a cement raw material vertical mill system Safe, convenient and reasonable auxiliary decisionmaking is smartly provided by a machine learning method without changing any structure and principle of a production equipment, adding additional measuring spots and affecting normal production The method comprises: ENERGYSAVING OPTIMIZATION METHOD OF CEMENT RAW MATERIAL VERTICAL MILL
)D`ERF`389RMI4.jpg)
A datadriven decisionmaking framework for online control of vertical
2020年5月1日 Vertical roller mill (VRM) is a type of heavyduty and energyintensive grinding equipment for many industries, such as cement, steel and chemical industries It is used to grind slag, nonmetallic ore and other block and granular raw materials into required powder materials The fine powders can be used as raw materials for cement production2021年1月22日 In the whole process of cement production, the electricity consumption of a raw material mill accounts for about 24% of the total Based on the statistics of the electricity consumption of the raw A Survey and Analysis on Electricity Consumption of Raw Material Mill 2023年6月8日 of 1025 vertical raw mill plant operational data were use d i n this study based on this method Thre e subse ts of this data set are availa ble: 717 for training, 154 for valida tion, and 154 for Assessment of the thermodynamics efficiency of a cement vertical raw 2019年6月22日 This was claimed to improve kiln operation In authors experience at one of the plants using vertical raw mill; In house method to determine the raw materials Grindability:Optimizing Raw Mills Performance ; the Materials WAY
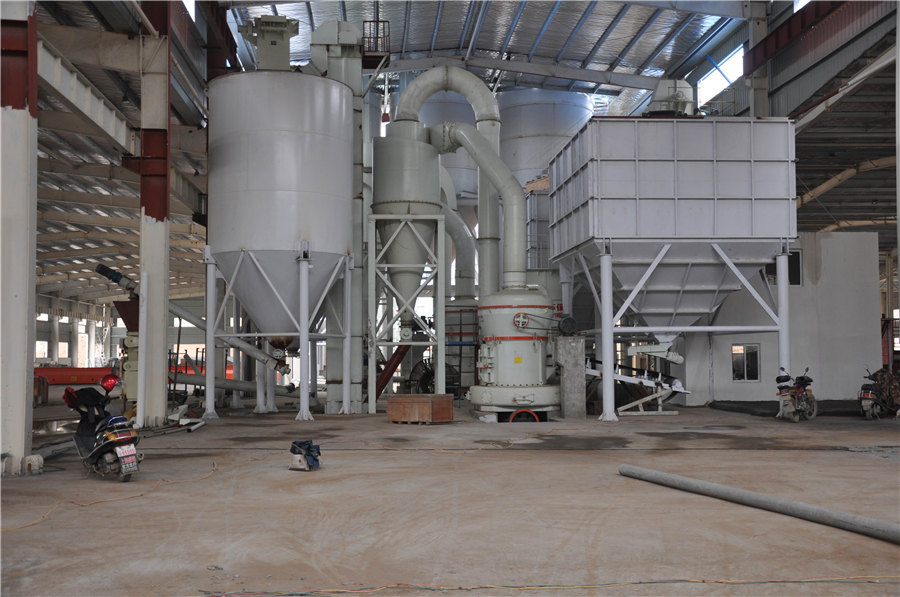
OK™ Raw and Cement Mill
The OK™ Mill was originally designed for cement grinding In 2017 we released the OK™ vertical roller mill for raw materials grinding The OK™ Mill’s modular design comes with unique flexibility, showcasing parts commonality, where spare parts can be shared between vertical roller mills regardless of size and applicationThe advantages of the modular vertical roller mill technology are evident in the results from a case study about a modular vertical roller mill 5000 – 4 roller raw material mill in operation in Grinding Process Optimization Featuring Case Studies and 2015年1月1日 Vertical grinding mill is the main grinding equipment for the newtype dry cement raw meal production, raw material grinding process in cement industries accounts for approximately 50#8211;60#160;% of the total energy consumption The dynamic characteristics of theModeling Based on the Extreme Learning Machine for Raw Cement Mill 2024年1月17日 Vertical roller mills, VRMs, are widely used for grinding raw materials in factories engaged in the extraction and processing of minerals Any machine used for grinding or crushing consumes around Parameters for the Grinding Process in Vertical Mills Using

Analysis of vertical roller mill performance with changes in material
2022年5月31日 Mineral crushing is the main source of energy consumption in mineral processing According to statistics, this consumption accounts for about 35–50% of the total cost of the mine (Curry et al, 2014), or even higherIt may also account for 18% of the global electrical energy consumption (NapierMunn, 2015)More efficient crushing equipment needs to be