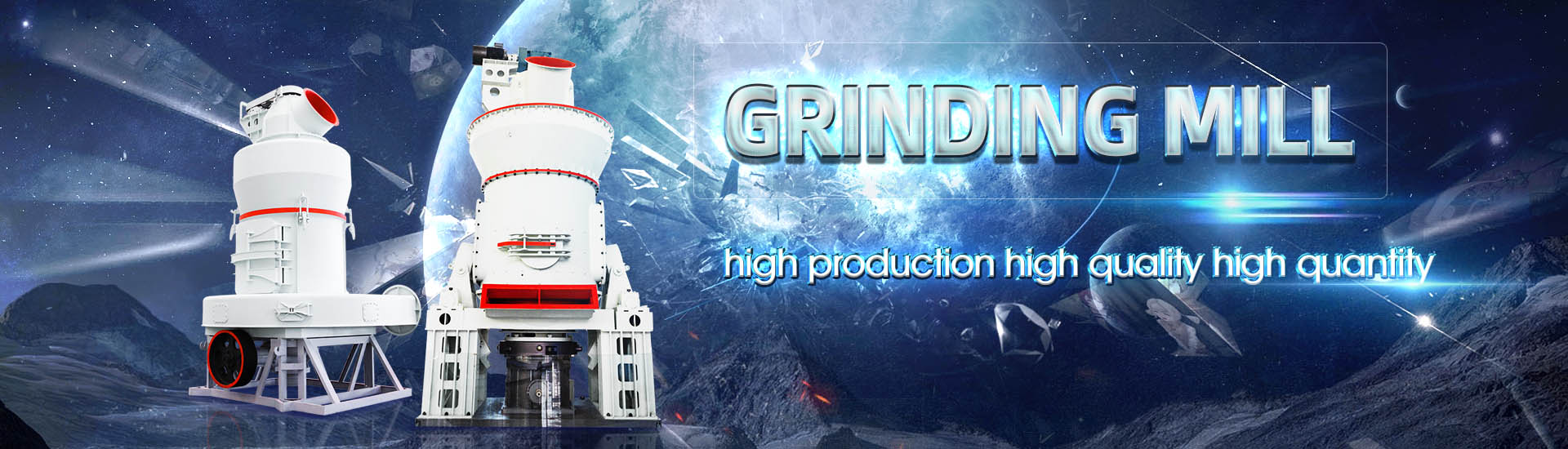
Ore mill design parameters
.jpg)
Ball Mill Design/Power Calculation 911Metallurgist
2015年6月19日 The basic parameters used in ball mill design (power calculations), rod mill or any tumbling mill sizing are; material to be ground, characteristics, Bond Work Index, bulk density, specific density, desired mill These are described in this paper, where complex interactions between key feed, design, and operational variables that may not necessarily be evident in datasets of fullscale mills in SAG Mill Design and Benchmarking Using Trends in the JKTech 2017年10月1日 In this article, we present laboratory scale batch grinding and leaching profiles of a monosized gold ore sample (1700 + 850 μm) The sample was obtained from a runofmine (ROM) ore of one(PDF) Determining optimum wet milling and leaching Pilot plant test results with various ores showed that low energy consumption feature of vertical roller mills is applicable to the ore industry Grinding test results for zinc ore showed that it is (PDF) Operational parameters affecting the vertical roller mill
.jpg)
Assessing the Impact of Surface Blast Design Parameters on the
16 小时之前 Openpit mining remains the dominant method for copper extraction in current operations, with blasting playing a pivotal role in the efficiency of downstream processes such 2021年9月5日 This study aimed to model bauxite grinding and assess the optimum material filling volume in a laboratory ball mill in order to improve mill and overall process efficiency Modeling of Bauxite Ore Wet Milling for the Improvement of 2017年8月10日 Particles breakage in grinding equipment depends on the design and operational parameters (Ghassa et al, 2016) In fact, breakage mechanism determines Effect of design and operational parameters on particle 2019年6月18日 The present work analyzes comminution of a Brazilian iron ore with unusual breakage behavior in batch and pilotscale tests, as well as in an industrial mill, which demonstrated the application of the scaleup approach in Optimization of Solids Concentration in Iron Ore Ball
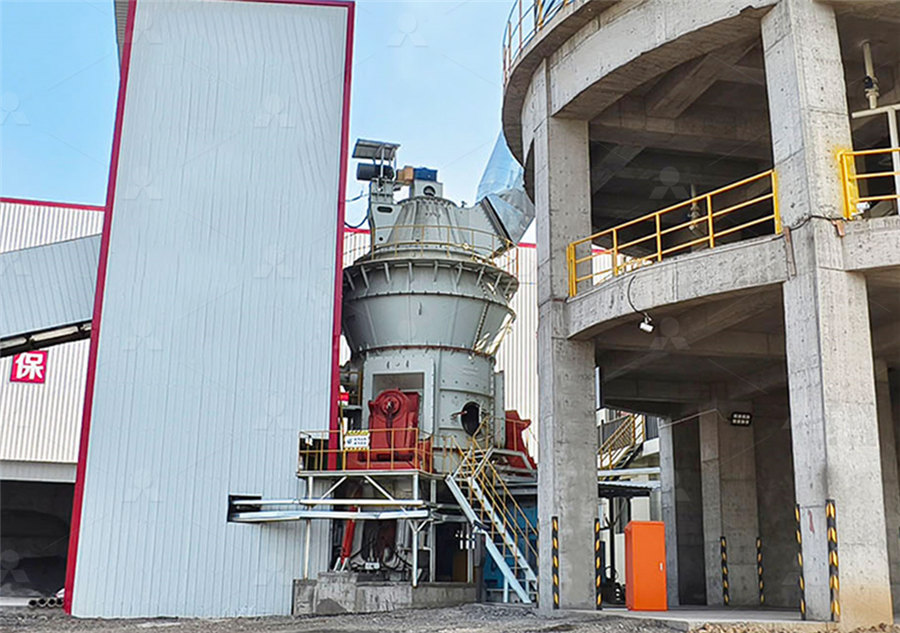
Energy Efficiency Analysis of Copper Ore Ball Mill Drive Systems
Specific energy consumption during the milling process depends on the geomechanical parameters of the raw material and on the design parameters of the mill [9,10] The energy Powder Technology 208 (2011) 121–127 Contents lists available at ScienceDirect Powder Technology j o u r n a l h o m e p a g e : w w w e l s ev i e r c o m / l o c a t e / p ow t e c Optimization of some parameters of stirred mill for ultrafine (PDF) Optimization of some parameters of stirred 2018年4月17日 Ore Testing for AG SAG Grinding Mill Design The application of autogenous and semiautogenous grinding circuits in recent years has contributed toward substantial savings in capital and operating costs compared to conventional circuits, particularly for large scale copper and molybdenum operationsAutogenous and SAG SemiAutogenous Mill Design Calculations2019年10月1日 Nomenclature a B selection function parameter calculated for the Bond design mill [min −1] a k selection function parameter measured for a monosized media charge of diameter d k [min −1] a L selection function parameter calculated for the laboratory design mill [min −1] a T selection function parameter corresponding to the reference ball diameter d T [mm]Assessing the dependency of selection function parameters with
.jpg)
Crushing Plant Design and Layout Considerations 911 Metallurgist
design parameters At virtually all mines, ore characteristics change over time, and it can be costly to “design in” the optimal flexibility required to handle such changes Some owners stipulate that initial capital investment be kept to a minimum, with design modifications paid for out of the operating budget This is not always easy to Optimization of stirred mill parameters for fine grinding of PGE bearing chromite ore, Particulate Science and Technology, DOI: 101080/2020 To link to this article: https://doi Optimization of stirred mill parameters for fine grinding of PGE 2021年1月18日 relates to the 19mm F80 of the ore charge fed to the SAGDesign test and to the test procedure which includes a Bond Ball Mill Work Index test on SAG ground ore from the first stage of the test The ratio of SAG pinion energy to Bond BM Wi is a key parameter in a SAG mill grinding circuit design, becauseImpact on Grinding Mill Design of Recent New Discoveries2021年2月26日 Milling is among the most energyconsuming technological stages of copper ore processing It is performed in mills, which are machines of high rotational masses The start of a mill filled to capacity requires appropriate solutions that mitigate the overloading One method for increasing the energy efficiency of ball mills is to optimize their drive systems This article Energy Efficiency Analysis of Copper Ore Ball Mill Drive
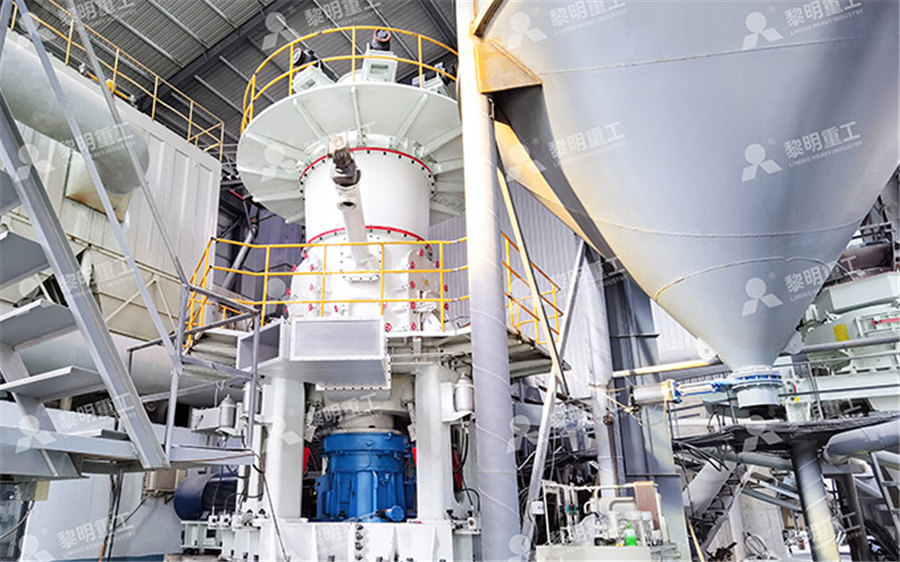
Effect of design and operational parameters on particle
2017年6月1日 Request PDF Effect of design and operational parameters on particle morphology in ball mills Different factors involving in grinding of ore cause various breakage mechanisms These different 2017年10月1日 PDF The comminution and leaching unit operations play a vital role in the extraction process of valuable minerals from ores Historical research Find, read and cite all the research you (PDF) Determining optimum wet milling and leaching parameters for drive system to be overloaded when the mill filled with copper ore is started For this reason, the mill is stopped only in the case of a failure or planned maintenance work The aim is to minimize the potential number of startups, as the mill at a standstill must be later started under full load In the case of a prolonged downtime, the Energy Efficiency Analysis of Copper Ore Ball Mill Drive Systems2016年4月22日 In all ore dressing and milling processes, including flotation, cyanidation, gravity concentration, and amalgamation, it is necessary to crush and grind, often with rob mill ball mills, the ore in order to liberate the Ball Mill Rod Mill Design 911Metallurgist
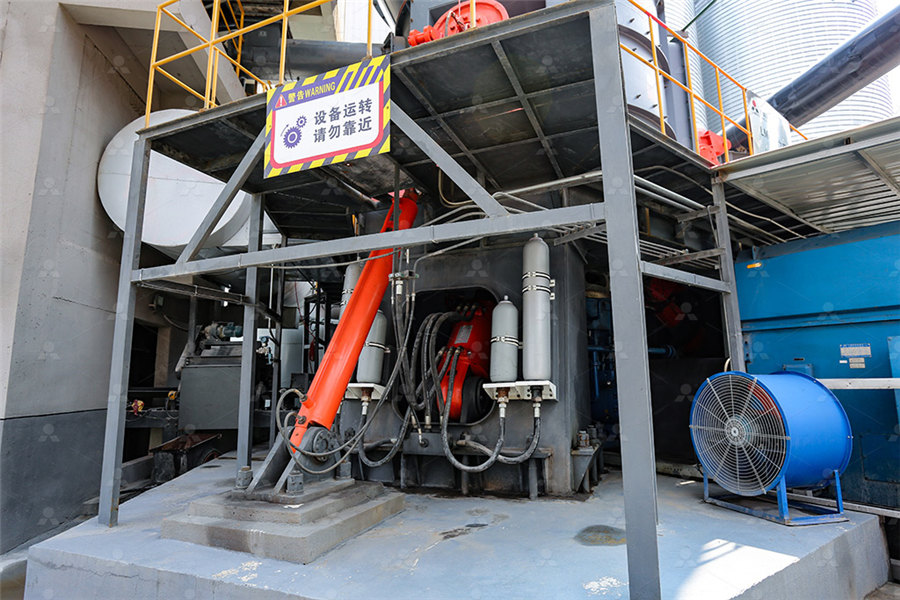
Optimization of stirred mill parameters for fine
2020年7月23日 Optimization of stirred mill parameters for fine grinding of PGE bearing chromite ore, Particulate Science and Technology, DOI: 101080/2020 To link to this article: https://doi 2020年7月23日 Abstract The depletion of highgrade ores has forced the utilization of lowgrade ores The small liberation sizes in the lowgrade ores require fine grinding which is an energy intensive operation In the present study, lowgrade chromite ore bearing platinum group of elements (PGE) was used as an experimental material The previous study concluded the Optimization of stirred mill parameters for fine grinding of PGE 2018年4月5日 Explore essential rod mill design calculations with 911 Metallurgist Our comprehensive guide provides formulas and techniques for optimizing rod mill performance and ensuring effective mineral processingRod Mill Design Calculations 911MetallurgistPowder Technology 208 (2011) 121–127 Contents lists available at ScienceDirect Powder Technology j o u r n a l h o m e p a g e : w w w e l s ev i e r c o m / l o c a t e / p ow t e c Optimization of some parameters of stirred mill for ultrafine grinding of refractory Au/Ag ores Oktay Celep a, Nevzat Aslan b, İbrahim Alp a,⁎, Gökhan (PDF) Optimization of some parameters of stirred mill for ultra
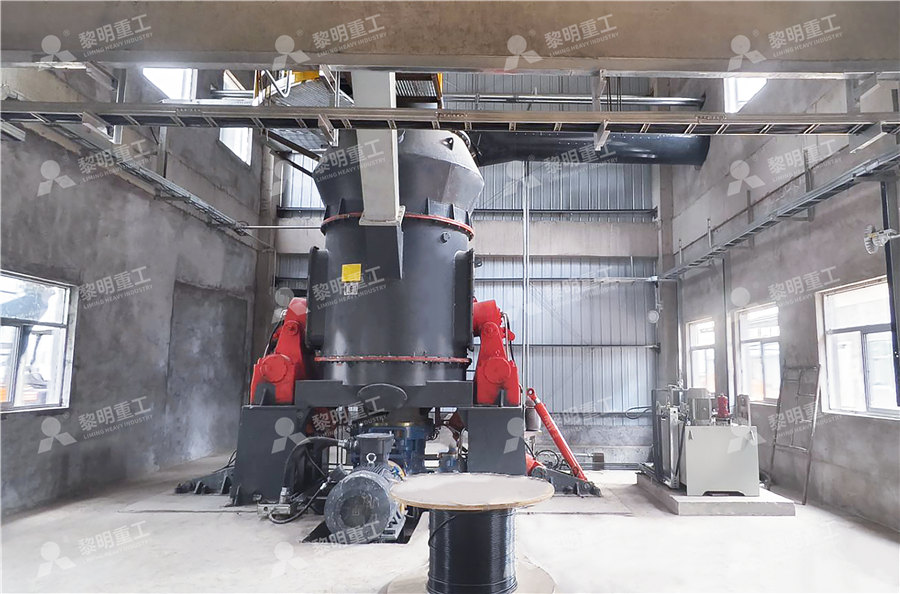
Factors for Ball Mill DesignSizing Calculator Formula
Grinding Mill Sizing Parameters leftpanel 0 SITUATION : Ore Work Index, kWh(net) /metric ton : Based on Net Power Available Feed Size, F80, microns : Capacity Correlation Ideally, design value should not exceed 13 psi If higher, increase # of Cyclones or Cyclone Diameter Mill Feed (incl Recycle) Flow Number :The SAG mill was designed for monzonite ore, with allowance in the mine schedule for reduced throughput when treating the harder volcanics Design parameters chosen for the Cadia SAG mill are shown the following table Table 2 : Cadia SAG Mill Design Parameters Diameter – inside liners (m) (ft) 1204 40Design of the 40 foot SAG Mill Installed at the Cadia Gold Copper 2012年6月1日 Typical examples are the various ores, minerals, The design of a ball mill can vary significantly depending on the size, In both cases the main parameters of the model are Grinding in Ball Mills: Modeling and Process ControlThe SAG mill was designed for monzonite ore, with allowance in the mine Table 2 : Cadia SAG Mill Design Parameters Diameter – inside liners (m) (ft) 1204 40Design of the 40 foot SAG Mill Installed at the Cadia
.jpg)
AG and SAG Mill Circuit Selection and Design by Simulation
mented with results from full scale mill data in cases where the pi lot mill data base contained little or no variation in the parameter of interest eg mill speed To indicate the extent of the pilot mill data base, Table 1 summarises its details Table 1: Pilot Mill Data Base Details New Feed F,, (mm) Ball load (%) Recycle load (%)2017年8月10日 Every year, billions tons of metal ores, minerals, Particles breakage in grinding equipment depends on the design and operational parameters (Ghassa et al, 2016) Effect of ball charge distributions and mill types on parameter of particles circularity for fine and coarsegrained feed are shown in Fig 6 Effect of design and operational parameters on particle morphology 2010年12月21日 In this study, optimization of some parameters of stirredmill on ultrafine grinding of refractory Au/Ag ores was performed A threelevel Box–Behnken design combining a response surface Optimization of some parameters of stirred mill for ultrafine 2020年10月9日 That is, we implemented a Design of Experiment (DoE) method to systematically calibrate the simulation parameters to the physical laboratory tests, and we supported this through observations Operation Analysis of a SAG Mill under Different
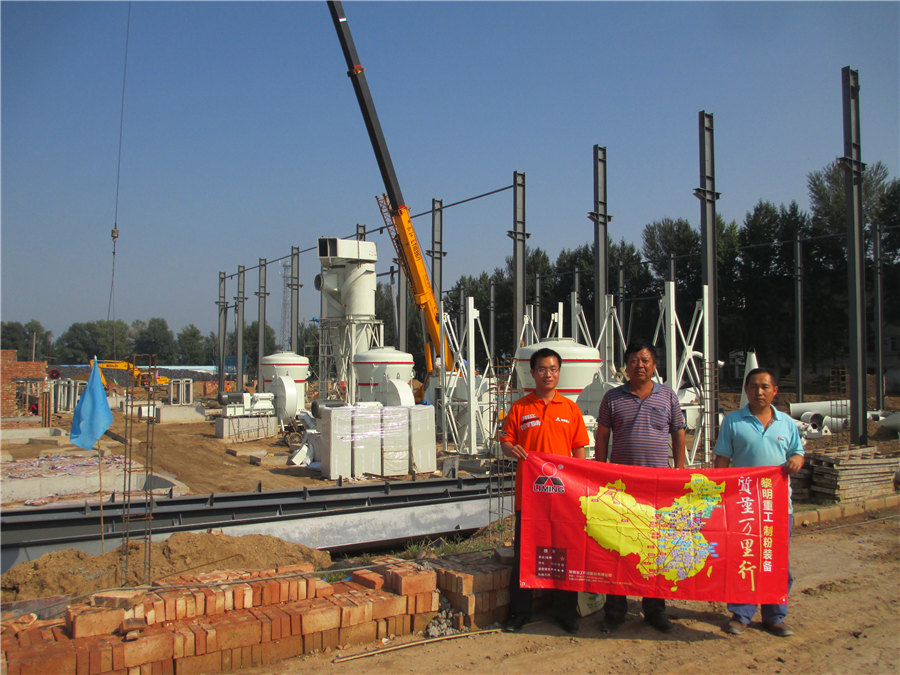
How Ball Mill Ore Feed Size Affects Tonnage Capacity
2017年7月26日 Soft ore Work Index 13 = 100,000/90,000 = 11 kwh/t Hard ore Work Index 16 = 100,000/65,000 = 154 kwh/t For the purposes of this example, we will hypothesize that the the crushing index of the hard ore with the increased energy input of 154 kw/t reduces the ball mill feed size to 6,500 micrometers2017年4月1日 For the modelling of the grinding operation, breakage rates of the particles are correlated with design parameters and material characteristics Research of iron ore grinding in a verticalrollermill Miner Eng, 73 (2015), pp 109115 View PDF View article View in Scopus Google Scholar Roy, 2002Operational parameters affecting the vertical roller mill 2011年1月1日 Request PDF JK drop weight parameters: A statistical analysis of their accuracy and precision and the effect on SAG mill comminution circuit simulation The JK Drop Weight test was developed at JK drop weight parameters: A statistical analysis of their accuracy 2014年1月1日 An analysis of the kinetics of dolomite grinding in a dry ball mill reveals that the following approximations apply for the parameters of the batch grinding model: the size discretized selection Population balance model approach to ball mill optimization in iron ore
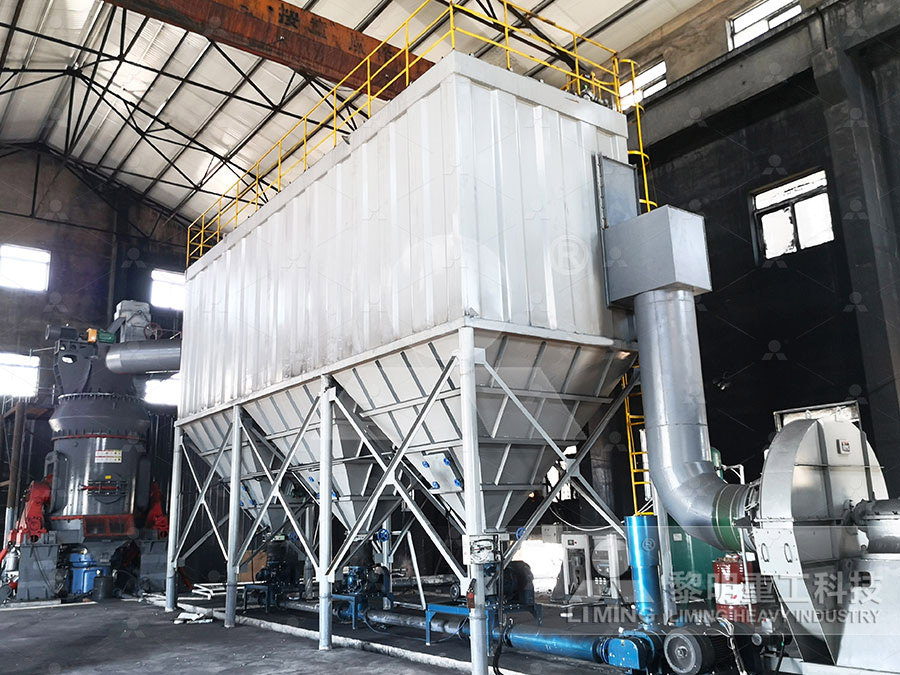
SAGDesignTM – Using Open Technology for Mill Design and
conceived as a way to avoid problems caused by designing a grinding mill through simulations derived from indirect measurement methods, where subtle differences in the ore properties can create a less than optimal design due to the lack of operating parameters which do not exist for a new mill at the design stage2021年3月23日 PDF Milling is among the most energyconsuming technological stages of copper ore processing It is performed in mills, which are machines of high Find, read and cite all the research you Energy Efficiency Analysis of Copper Ore Ball Mill Drive Systems2024年9月26日 The present article focuses on incorporating mill scale, a steel plant solid waste, into the iron ore pelletization process The characterization results indicated that the mill scale contained about 71% of Fe and predominantly consists of magnetite and wustite mineral phases A detailed pelletization study is conducted using the mill scale at different proportions (0%, Evaluation of Quality Parameters and Mineralogy of Iron Ore SGS MINERALS SERVICES 2011 TECHNICAL PAPER 201108 SAG MILL TESTING AN OVERVIEW OF THE TEST PROCEDURES AVAILABLE TO CHARACTERIZE ORE GRINDABILITY AUTHOR: FO VERRET, G SAG Mill Testing Test Procedures to Characterize
.jpg)
Quantifying variability of ore breakage by impact ScienceDirect
2018年10月1日 The JKDWT approach is used by industry as one of the standard approaches to design, operate and optimise SAG mill circuits Abrasion ore parameter Table 5 Parameters that were used in SAB WJ, 1983 Breakage characteristics of ores for ball mill modelling In: Proceedings AusIMM, vol 286, June, pp 31–39 Google In the past, most of the mill scaleup work was based, directly or indirectly, on the empirical Bond energy size reduction equation This approach was used extensively in the minerals industry and in accordance to some researchers (Austin, Klimpel and Luckie [1]) Bond work index may be useful for mill design, but not for optimization ofPOPULATION BALANCE MODEL APPROACH TO BALL MILL OPTIMIZATION IN IRON ORE Mill Type Overview Three types of mill design are common The Overflow Discharge mill is best suited for fine grinding to 75 – 106 microns; The Diaphram or Grate Discharge mill keeps coarse particles within the mill for additional grinding and typically used for grinds to 150 – 250 microns; The CenterPeriphery Discharge mill has feed reporting from both ends and the product AMIT 135: Lesson 7 Ball Mills Circuits – Mining Mill Operator 2018年1月19日 The parameters relating to mill hardness consist of and grindability blast design for mill feed; ore blending decisions The empirical ‘engineering’ models for blast fragmentation at present are predicting the mean fragmentation under a set of assumptions and do not attempt to predict the full size distributionPredicting Mill Ore Feed Variability Using Integrated Geotechnical
.jpg)
SAG Mill Liner Design 911Metallurgist
2016年6月6日 Once the process metallurgist has thoroughly tested the ore body and determined the optimum method of mineral recovery; and the plant designer has efficiently and economically laid out the circuit, instrumentation, equipment installation, and building design; and the mill manufacturer has completed his stress analysis and reliability engineering for mill design, the 2020年10月1日 These include mill power draft calculations, shell lifter design, lifter wear prediction, pulp lifter simulation and ore particle breakage in grinding mills The status of advancement in each of A Review on Current Mill Liner Design and Performance2021年10月21日 The economic and technical values of the hydrometallurgical or leaching processing are a function of its reaction rates and these reaction rates are enhanced by mechanical activation (MA) in hydrometallurgical processing This study presents a novel derived theoretical model for MAassisted leaching in investigating the effects of ball mill parameters Effect of Ball Mill Parameters’ Variation on the Particles of a PROCESSING AND COMPLEX USAGE OF MINERAL RAW MATERIALS EURASIAN MINING 2022 No 2 pp 54–57 55 kWh/t; M ia is the Morrell index for coarse ore treatment in tumbling mills to the size P 80 > 750 μm , kWh/t; Mic is the M orrell index for ore treatment in cone and jaw crushers, kWh/t; Mih is the Morrell index for ore treatment in HPGR circuits, kWh/t; Mib is the ORE HARDNESS PROPERTIES EVALUATION BASED ON
.jpg)
Grinding Media in Ball Mills for Mineral Processing
2023年11月24日 Factors that influence the grinding efficiency include mill design, liner design, mill speed, mineralogical composition of the ore, charge ratio, and grinding media properties The grinding efficiency of a ball mill is determined by the product size distribution, energy consumption, and the grinding costs