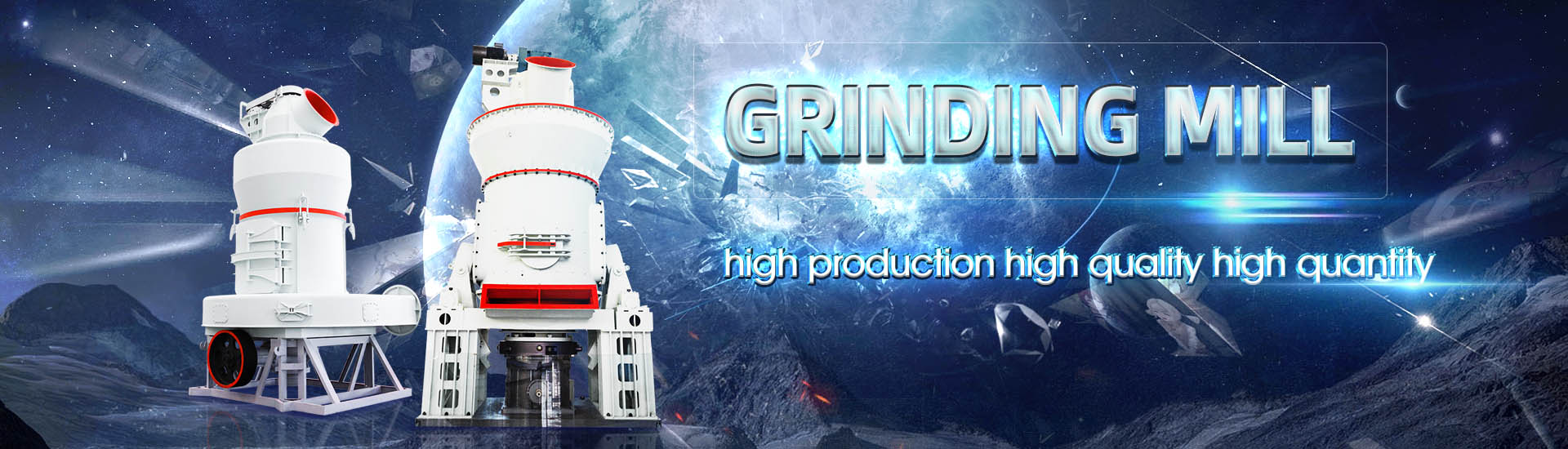
Coal particles Manufacturing process

Industrial perspective of the cokemaking technologies
2019年1月1日 Solid particles entrained with COG during the carbonization process reported as quinoline insoluble particles (QI), and they are concentrated in the coal tar QI contains coal 1 天前 The conventional graphite manufacturing process usually involves a series of stages: the pulverization of needletype coke, the granulation of pitch and coke premix Due to our A Shortened Process of Artificial Graphite Manufacturing for 2015年7月1日 Coal preparation is an indispensable stage in coal production, during which runofmine coal is transformed into products (clean coal) suitable for the market Byproducts A review of stateoftheart processing operations in coal Coal preparation, which may also be called washing, cleaning or processing, is the methodology by which coal feedstocks are upgraded in order to reduce freight costs, improve utilization Coal Preparation SpringerLink
.jpg)
Mineral Beneficiation and Processing of Coal SpringerLink
2021年5月11日 The prime objective of the coal preparation is to separate the clean coal at the coarsest possible size Conventional gravity separators, such as Jigs and dense media 2021年2月8日 Pitch extracted from coal, a byproduct of the carbonization process during the production of metallurgical coke, constitutes a valuable aromatic hydrocarbon source essential Influence of coal properties on coal conversion processescoal 2022年11月26日 For the first time, mass and energy changes of coal tar pitch occurring during the primary carbonization process can be estimated by applying the present thermodynamickinetic model Model estimations on mass losses Modeling the Coal Tar Pitch Primary Carbonization 2023年2月20日 Stircasting techniques are currently the simplest and most commercially viable method of manufacturing metal matrix composites This method entails mechanicallyTaguchi optimization and modelling of stir casting process
.jpg)
(PDF) The Origin and Classification of Coal
2019年12月31日 This chapter describes the process of coalification, which gradually turns plant debris into coal, involving heat, pressure and the effects of time Chemical changes during peatification andThe extraction of coal is a critical stage in the processed coal manufacturing process, as it determines the quality and quantity of coal available for processing and conversion The efficient and sustainable extraction of coal is essential to ensure a stable supply of raw materials for various industries and meet the growing global energy demandThe Processed Coal Manufacturing Process: A Comprehensive 2021年9月1日 Recent advancement in coal tar pitchbased carbon fiber precursor development and fiber manufacturing process Author links open overlay panel Chandrachur Banerjee, Vimal Kumar Chandaliya, Pratik Fiber from slurry oil could not be drawn due to the presence of mesophase particles in it However, both PFO and coal tar produced Recent advancement in coal tar pitchbased carbon fiber 2023年9月1日 If coal is heated the gases and residues produced can be used in manufacturing plastics, explosives, dyes, pitch, ammonia A mechanical shear is used to crush the coal into small particles, releasing water that was held in Coal Geoscience Australia
.jpg)
Development of a Binder Manufacturing Process for Molded Coal
Molded coal is made of blended coal, pitches and heavy tar They are mixed while heated in a mixer Then, they are pressed and molded in a briquetting machine producing the molded coal When molded coal is used as raw material for coke, coal particles easily attach to one another, and the Development of a Binder Manufacturing Process for Molded 2022年11月26日 The properties of the carbon materials obtained as the final product of coal tar pitch carbonization process are a consequence of the type of chemical and physical phenomena occurring through the process A new simplified approach for modeling of the primary carbonization is presented to provide the semiquantitative knowledge about the process Modeling the Coal Tar Pitch Primary Carbonization Process2010年5月18日 The process of coal manufacturing from petroleum derivates (coke) generates polluting particles that are released by the plant’s chimney The magnetic spheres formed in the furnace have different sizes, and they also contain smaller particles than Air pollution caused by manufacturing coal from petroleum coke An introduction to the nature of coal J Groppo, in Coal Combustion Products (CCP's), 2017 13 Coal beneficiation 131 Coal beneficiation processes Coal beneficiation, or coal preparation as it is also termed, refers to the processes through which inorganic impurities are separated from raw mined coal, thereby providing improved combustion characteristics to the fuel producedCoal Beneficiation an overview ScienceDirect Topics
.jpg)
Industrial perspective of the cokemaking technologies
2019年1月1日 To do this, it must wet the surface of the coal particles during the manufacturing process and remain in the briquette during carbonization at least until the coal particles soften Briquette blending technology of coal has been relatively popular in the 1980s, particularly in Japanese steel plants ( Amakatsu et al, 1978 , Nakamura et al, 1979 )• Brick shrink during the manufacturing process as measures to reduce plant emissions Most brick are used vitrification occurs Brick will vary in size due to the within 500 miles of a brick manufacturing facility INTRODUCTION The fundamentals of brick manufacturing have not changed over time However, technological advancementsManufacturing of Brick Brick Industry Association2023年1月1日 Sizing coal is the process of segregating coal lumps that are similar in size Coal passes over one or more vibrating screens/grates and the larger sizes not passing through each screen are separated Coal is usually separated using grates of three sizes: coarse, intermediate, and fine Each size follows a different path through the plantCoal beneficiation: theory and practice ScienceDirect2021年11月1日 The selective separation of hydrophobic coal particles from hydrophilic gangue minerals by froth flotation dates back to the 1920s Prior to this, commercial applications of froth flotation were limited only to ores and minerals finer than 100 µm in size (Nguyen and Schulze, 2003)In coal flotation, particles finer than 500 µm are commonly employed due to their natural A review on flotation of coal using mixed reagent systems
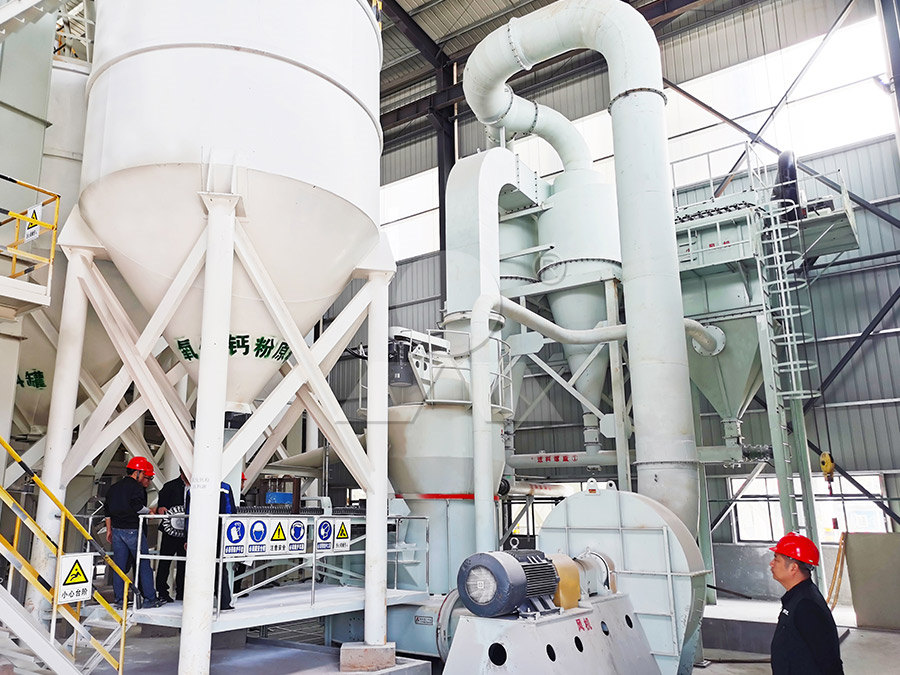
Application of Statistical Process Control for Coal Particle Size
Additionally, a viewpoint was that the process capabilities were inadequate The reason for this might be the different feeder and bin discharge problems of coal and the careless behaviors of laborers Keywords: coal, coal particle size, control charts, process capability, statistical process control, vertical roller mill 12023年6月5日 The mechanism of highintensity conditioning (HIC) has not been thoroughly revealed, and therefore this work investigates the effect of HIC on the surface hydrophobicity of coal with different particle sizes and the possible Changes in Surface Hydrophobicity of Coal Particles 2015年7月1日 The United States currently operates 268 coal preparation plants in 14 states according to the latest annual census of coal processing plants conducted by Coal Age [3] The facilities, which are primarily located in West Virginia (80), Kentucky (56), and Pennsylvania (44), represent a total installed feed capacity of over 200,000 tons per hourA review of stateoftheart processing operations in coal preparation coal particles Ian Moore 26th February 2019 Contributors • Zushu Li a • Stephen Spooner a • Colin Atkinson b • Jan van der Stelc • Stefan Bornc • Seetharaman Sridhard a) Warwick Manufacturing Group b) Materials Processing Institute c) Tata Steel d) Colorado School of Mines Content • Coal properties important for steel industryDirect observation of swelling coal particles
.jpg)
Labscale Production of Coalderived Graphene Particle Bonded
Labscale Production of Coal derived Graphene Particle Bonded Filaments DEFE Kelvin Fu Assistant Professor Center for Composite Materials University of Delaware The main goal of this project is to develop a labscale manufacturing process to fabricate filaments containing coalderived graphene for 3D printing use2019年12月31日 This chapter describes the process of coalification, which gradually turns plant debris into coal, involving heat, pressure and the effects of time(PDF) The Origin and Classification of Coal ResearchGate2023年5月10日 Particle size distribution should be carefully taken into account for considerable operational benefits Nevertheless, the particle size should fall between 335 and 14 millimetres when utilizing AC for the adsorption of minerals like gold (0132–0055 in) It would not be appropriate to elute AC with particles smaller than 1 mm 41Activated Carbon: Fundamentals, Classification, and Properties2023年6月9日 Coal gasification is recognized as the core technology of clean coal utilization that exhibits significant advantages in hydrogenrich syngas production and CO2 emission reduction This review briefly discusses the recent research progress on various coal gasification techniques, including conventional coal gasification (fixed bed, fluidized bed, and entrained bed Recent Progress on HydrogenRich Syngas Production from Coal
.jpg)
Eliminating environmental impact of coal mining wastes and coal
2024年10月1日 Coal processing byproducts mainly include coal gangue and coal A CFB boiler operates with a much higher fluidisation air velocity so that smaller coal particles are entrained into the upper section of the furnace where majority of combustion chemical plants and ammonia manufacturing where pure H 2 in large quantities is 2024年1月5日 Waste coalderived isotropic pitch was produced via a direct coal liquefaction (DCL) process [[12], [13], [14]] in tetralin (1,2,3,4tetrahydronaphthalene), followed by pressure filtration and distillation of the resultant coal extract to render an isotropic pitchDCL of coal in tetralin (1:3 by weight) was carried out in a 2 L autoclave at 410 °C for 30 minutes under Isotropic pitchderived carbon fiber from waste coalFixed Bed Combustion: In fixed bed, coal particles are supported on a grate in the combustion chamber The combustion air is allowed to flow through the coal bed in upward direction either by a chimney draft or by a fan Coal may be fed to the bed in Combustion of Coal National Institute of Technology, Srinagar2021年8月2日 Respirable coal mine dust represents a serious health hazard for miners Monitoring methods are needed that enable fractionation of dust into its primary components, and that do so in real time Near the production face, a Demonstration of Optical Microscopy and Image
.jpg)
How Is Plastic Made? A Simple StepByStep Explanation
The vast majority of plastic in use today is synthetic because of the ease of manufacturing methods involved in the processing of crude oil However, the growing demand for limited oilreserves is driving a need for newer plastics from renewable resources such as waste biomass or animalwaste products from the industry2024年7月23日 Prior to the casting process, the brown pumice and coal ash particles underwent a preheating treatment for 2 h at 500 °C based on the recommendation of previous studies by Kumar et al 31 Development, modelling and optimization of process parameters 2016年7月1日 The coal briquette manufacturing process layout is shown in Figure 1 Optimal results were obtained using a fine coal particle size (00530103 mm), a high heating rate, FACTORS IDENTIFICATION FOR COAL BRIQUETTES MANUFACTURING When it comes to effective coal processing, our operators at RPM Solutions bring a deep wealth of mining and machining experience to every project Call : 18002703102; info@rpmsolve; Most cleaning processes involve washing coal in order to separate coal particles from stone particles Coal can be charred, Coal Processing Coal Preparation Coal Handling RPM Solutions
.jpg)
Monitoring, Process Control, Simulation, and Optimization in Coal
The rapid desorption of gas in coal is an important cause of gas overlimit and outbursts In order to explain the causes of coal and gas outbursts induced by vibration, this paper studies the gas desorption experiments of tectonic coal with different particle sizes and different adsorption equilibrium pressures under 0~50 Hz vibration2017年6月1日 Laboratory Scale Studies have shown that the combustion of high amount of coal particles may increase porosity proportion in fired bricks, leading to high water The impact of the addition of coal wastes was assessed by testing the required parameters related to the manufacturing process such as; firing shrinkage, flexural Coal mine wastes recycling for coal recovery and ecofriendly 2024年7月15日 Factors such as coal’s physical and chemical properties (coal type, coal rank, particle size) and process parameters, specifically activation method, temperature, and activation agents, could impact AC production This may assist in identifying ways of enhancing the quality of the AC from the coalbased manufacturing processReview of the effects of coal properties and activation parameters a mixture of coal and petroleum coke Gasification process convert the solid combustible mixture into a gas that is subsequently depured to separate sulphur and dust particles The cleaned gas composed by 60% CO, 22% H 2, 10% N 2, 4%H 2O and 4% CO 2, is then burned with high efficiency in a combined cycle electricitygenerating unit[2]Production of Lightweight Aggregates from Coal Gasification
.jpg)
Fly ash properties, characterization, and applications: A review
2021年9月1日 As shown in Fig 1, the byproducts of coal ash combustion include fly and bottom ash, boiler slag, and flue gas FA particles, the main byproduct, are fine powdery particles, and heterogeneous During coal combustion, FA particles were carried usually aside by the aid of flue gas and detained by precipitators either electrostatic or mechanical2023年2月20日 It was observed at 25 wt% of pumice particles, 25 wt% of carbonated coal particles, 700 °C processing temperature, 200 rpm stirring speed, and 5 min stirring time, the optimum percentage of Taguchi optimization and modelling of stir casting processA coke oven at a smokeless fuel plant, Abercwmboi, South Wales, 1976 The industrial production of coke from coal is called coking The coal is baked in an airless kiln, a "coke furnace" or "coking oven", at temperatures as high as 2,000 °C (3,600 °F) but usually around 1,000–1,100 °C (1,800–2,000 °F) [2] This process vaporises or decomposes organic substances in the coal, Coke (fuel) Wikipedia2019年9月5日 Compared with coalfired power, biomass directfired power plant can reduce 528287 kg CO2 emissions during the process of generating 104 kWh power, which plays a positive part in mitigating Life Cycle Assessment of Straw Solid Particle Molding Fuel
.jpg)
Advances in Coal Processing, Utilization, and Process Safety
Simulation and predictive modeling of coal seam gas outbursts and rock bursts; New technologies in coal processing and their implications for process safety; Research on coal utilization and its safety impacts; Environmental and safety considerations in coal–gas extraction and utilization; The coal spontaneous combustion mechanism Dr Feng Du2023年1月5日 Understanding the role of coal particle shape in the flotation process is helpful in achieving a clean usage of coal slime flotation In this investigation, the anthracite coal surface was modified using a chlorinated salt solution containing Na +, Ca 2+, or Fe 3+Coal particles with four surface shapes were prepared: angular coal particles (ARPs), prismatic coal particles Influence of particle shape on the interaction processes of coal 2024年3月15日 Studying the fragmentation characteristics of coal particles is important for enhancing furnace gasification efficiency Based on the processing method of visualization imaging technology, this study investigated the proportion of particle fragmentation, fragmentation mode, surface temperature, and other characteristics of the Fuhua Indonesian Coal (FIC) Experimental study on the fragmentation behavior of coal particles Cement Manufacturing Process by TIZITA MOGES , The particles are thus flung radically outwards to the wall of the cyclone from where they fall into dust hopper External Thermal Efficiency is using the recovered heat for other process; Raw mill, Coal Mill and Cement mill drying; Heating and power generation; Speed of Clinker CoolingCement Manufacturing Process INFINITY FOR CEMENT EQUIPMENT
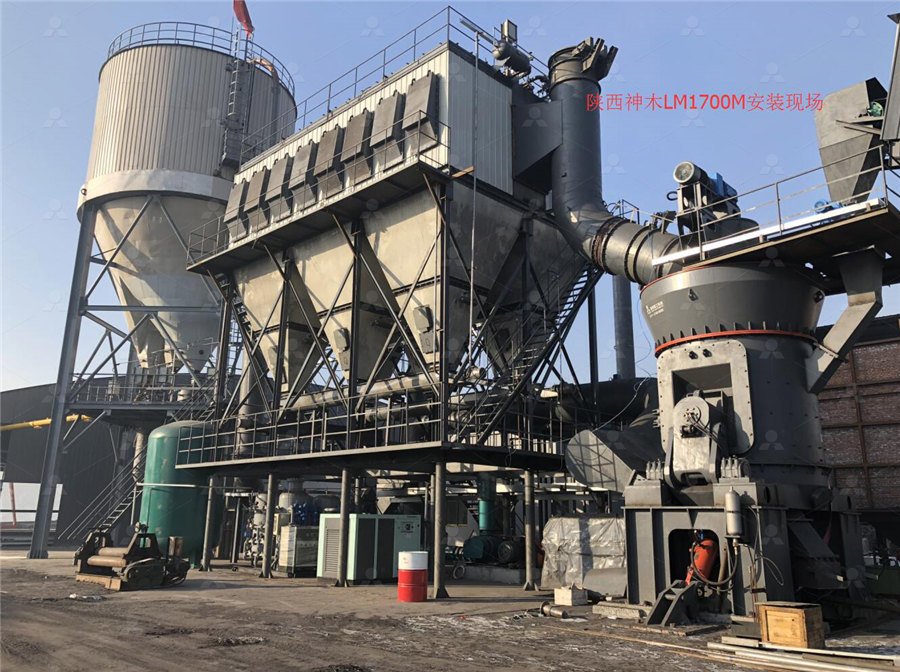
Firstrate manufacturing process of primary air fan (PAF) coal
2022年5月1日 Additive manufacturing (AM) has become one of the most revolutionary technology applications in manufacturing in the past decades The process uses the principle of adding layer by layer of material using a 3D digital solid model [[1], [2], [3], [4]]Conventional manufacturing technology involves a broader selection of raw materials in the production