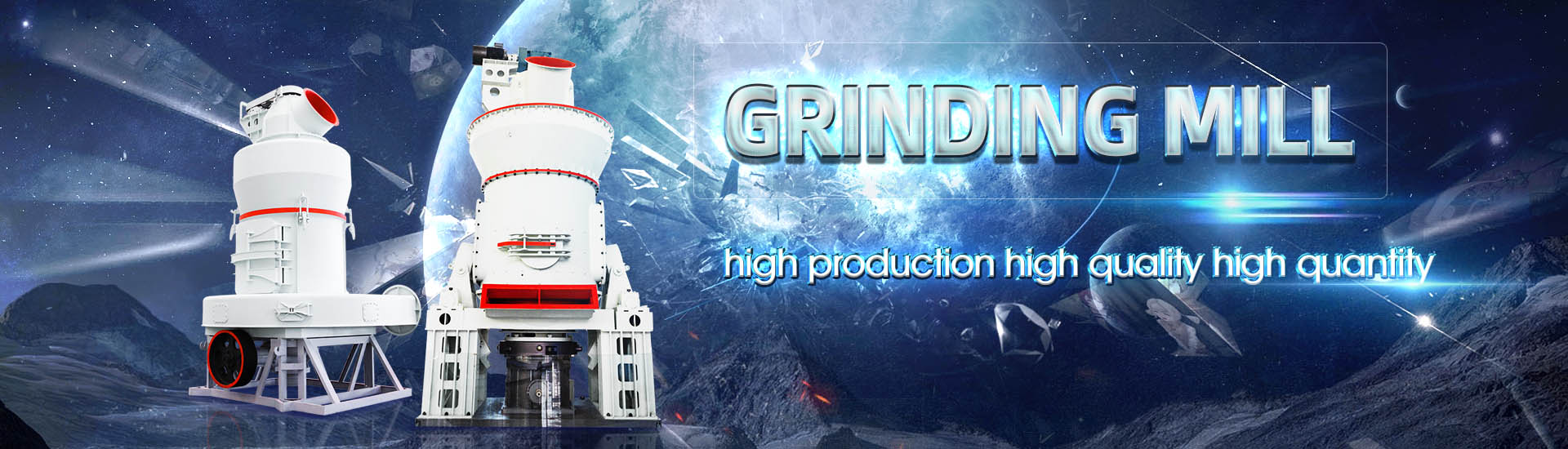
Ore grinding mill Harbin distribution
.jpg)
Ore Grinding MillSBM Industrial Technology Group
We have supplied numberless of wet grinding rod mills for customer in coal chemical industry, to deal with the coal and petroleum coke material and prepare for the coal water slurry making 2018年6月1日 In this article, alternative forms of optimizing the milling efficiency of a laboratory scale ball mill by varying the grinding media size distribution and the feed material particle size Effect of ball and feed particle size distribution on the milling 2017年9月1日 The objective of this work is to assess the influence of fine grinding in ball mills and stirred mills on valuable mineral liberation and particle shape characteristics of UG2 ore, a Fine grinding: How mill type affects particle shape characteristics 2020年1月1日 The present work was used to find the total grinding retention time of each ore in the mill Based on the total retention time of each ore, the optimum grinding time for each ore Estimation of Grinding Time for Desired Particle Size Distribution
.jpg)
Research on prediction model of ore grinding particle
2019年3月28日 The results show that particle size distribution of crushing products under different crushing energies and ore particle sizes is obtained by drop weight test, and the crushing parameters A and b are calculated by fitting 2023年6月1日 The main parameters of grinding and classification process include measurement of millfeeding quantity, mill load measurement, measurement of ore slurry density, Online Measurement and Control for Ore Grinding and Classification2020年12月3日 Crushing and grinding processes are typically used by crushers and mills to liberate minerals, which are energyintensive processes (especially fine grinding by mill) A process mineralogy approach to study the efficiency of milling A simple and novel nonlinear model of a runofmine ore grinding mill circuit, developed for process control and estimation purposes, is validated The model makes use of the minimum Analysis and validation of a runofmine ore grinding mill circuit
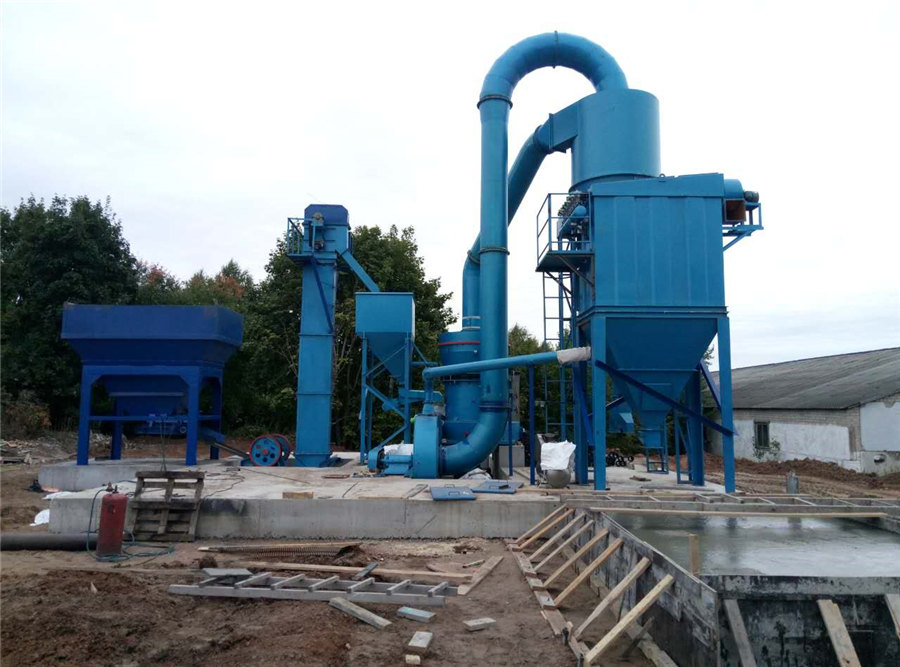
Ore Grinding SpringerLink
2023年7月20日 According to the material transmission methods, ore grinding is divided into dry grinding, wet grinding, and moist grinding Dry grinding relies on pneumatic conveying, in Maintaining the correct particle size and particle size distribution of the regrind product is crucial for downstream process performance solution for fine and ultra fine grinding Outotec Outotec HIGmills; A Fine Grinding Technology1 Population balance model approach to ball mill optimization in iron ore grinding Patricia M C Faria1,2, Luís Marcelo Tavares2 and Raj K Rajamani3 1 Vale SA, Brazil 2 Department of Population balance model approach to ball mill optimization in iron ore 2019年3月28日 In the ball mill, the main grinding method was the impact of the steel ball medium with the finer ore particles, and the Ecs was high because the weight of the single steel ball was significantly Research on prediction model of ore grinding particle size distribution
.jpg)
Population balance model approach to ball mill
2014年1月1日 They rely on the assumption that material breakage characteristics, namely breakage rate and distribution functions, may be estimated from batch grinding tests under controlled conditions, to then 2023年7月20日 Therefore, the rod mill is mostly used for coarse grinding of the previous period of ball mill, or grinding of brittle materials and materials against overcrushing, such as tungsten and tin ore before gravity separation; and (3) autogenous mill – it refers to the materials which themselves are collided and ground mutually to be crushed when the grinding mill rotates, and Ore Grinding SpringerLinkperformance of a large diameter sag mill is shown in Figure 4 page I208 The top size data has been plotted in both raw and smoothed form It clearly shows that as top size increases the mill weight increases as the mill finds it increasingly difficult to break down the bigger rocks Power responds to the increased mill weight by also increasingI203 I204 INTRODUCTION SMC Testing2022年8月31日 The order of influencing factors of the two ores is as follows: grinding time > filling ratio > grinding concentration For Tongkeng ore, the optimized grinding conditions are grinding time 54 min, grinding concentration 67% and filling ratio 35% For Gaofeng ore, the optimized grinding conditions are grinding time 38 min, grinding Grinding Modeling and Energy Efficiency in Ore/Raw Material
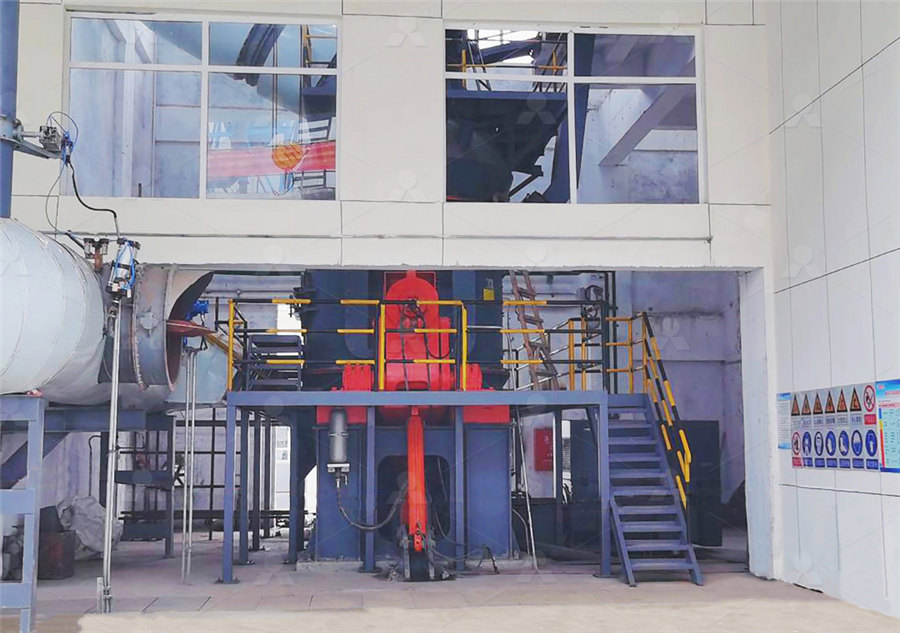
Investigation on Iron Ore Grinding based on Particle Size Distribution
2020年5月28日 The feed samples of X, Y, and Z iron ores were ground in the BBM (ball mill refers to a BBM of size 300 mm × 300 mm with smooth liners) to identify the PSD, BWI, and RT of each ore Grinding experiments were conducted according to Bond’s standard test procedure []For each iron ore sample, the RT taken to produce 250% circulating load in the BBM was 2012年12月28日 A comparative study was carried out to investigate the effect of highpressure grinding rolls (HPGR) comminution on agitation leaching of gold ore in comparison with the conventional jaw crusher Optimizing the performance of highpressure grinding roll based ore Keywords: iron ore; ball mill; modeling; simulation; population balance model; slurry density 1 Introduction It has been well over half a century since Austin and Gardner [1], followed by Reid [2], applied the concept of firstorder breakage kinetics to steadystate continuous grinding in a mill The grindingOptimization of Solids Concentration in Iron Ore Ball Milling 2023年12月12日 Ore can have various properties, such as hardness, density, moisture content, etc, which can affect the ore’s productivity and grinding efficiency Discover the world's research 25+ million members(PDF) Control of ball mill operation depending on ball load and ore
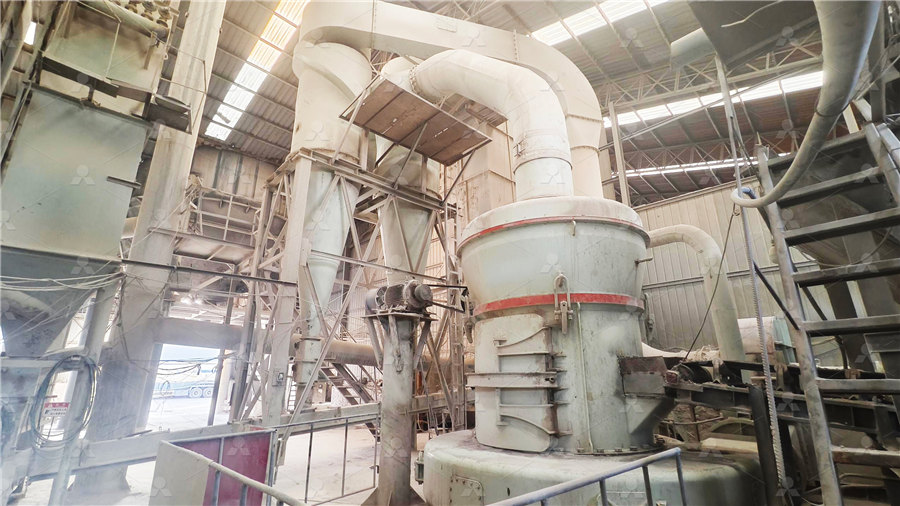
Modeling and application of stirred mill for the coarse grinding
2022年5月23日 Grinding experiments were conducted in a laboratoryscale stirred mill on a lowgrade PGE bearing chromite ore HighPressure Grinding Rolls (HPGR) product of −1 mm was used as feed material to This mill accepts grinding set weights of up to 30 kg, the largest grinding jar has a volume of 2,000 ml chemical industry, etc, it has two ore grinding Compare this product Remove from comparison tool ball grinding mill horizontal for ore ball grinding mill Final grain size: 74 µm Ore mill, Ore grinding mill All industrial manufacturersore and corresponds to the scheme, including medium and small stage ball grinding provides a comparative analysis of a wide range of ore processing steps and requires 515% energy in a selfgrinding mill [3] 1 Figure 2 Ball mill process control system using ACS (Adaptable Control System) Figure 2 shows that the input and output signalsControl of ball mill operation depending on ball load and ore 2018年6月1日 A number of researchers (Deniz, 2012; Bwalya et al, 2014; Petrakis et al, 2016) carried out studies about the effect of feed particle size and grinding media size on the grinding kinetics of different oresKhumalo et al, 2006 postulated that generally larger sized grinding media would break larger particles quicker but a finer product would be obtained by use of Effect of ball and feed particle size distribution on the milling
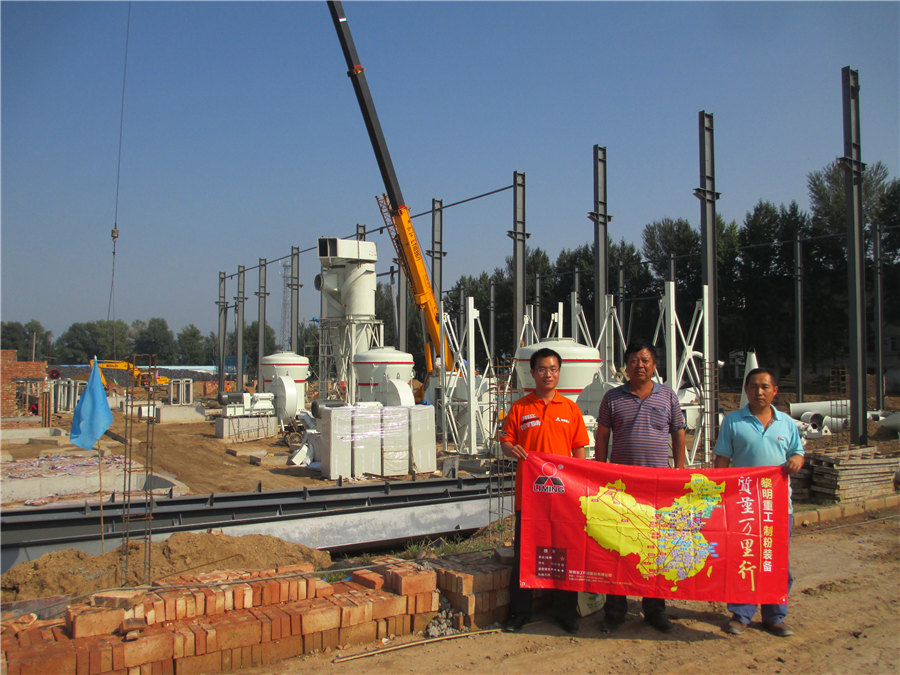
Ore Pretreatment Methods for Grinding: Journey and Prospects
2018年6月18日 Ore pretreatment methods for grinding: journey and prospects, Mineral Processing and Extractive Metallurgy Review, DOI: 101080/2018 To link to this article: https://doior g/10 2020年10月18日 An iron ore concentrate sample was ground separately in a pilotscale HPGR mill in multiple passes and a dry opencircuit ball mill to increase the specific surface area of particlesThe effects of iron ore concentrate grinding methods (HPGR and 2017年3月20日 An effect of a grinding method, that is ball mill and high pressure grinding rolls (HPGR), on the particle size, specific surface area and particle shape of an iron ore concentrate was studiedPhysicochemical Problems of Mineral Processing Investigation HGM ultrafine grinding mill can process nonmetallic ores with Mohs hardness less than 7 The equipment has stable operation, simple operation, long service life, low carbon and environmental protection There are 5 models of HGM ultrafine grinding mill, SBM Ore Ultrafine Grinding Mill
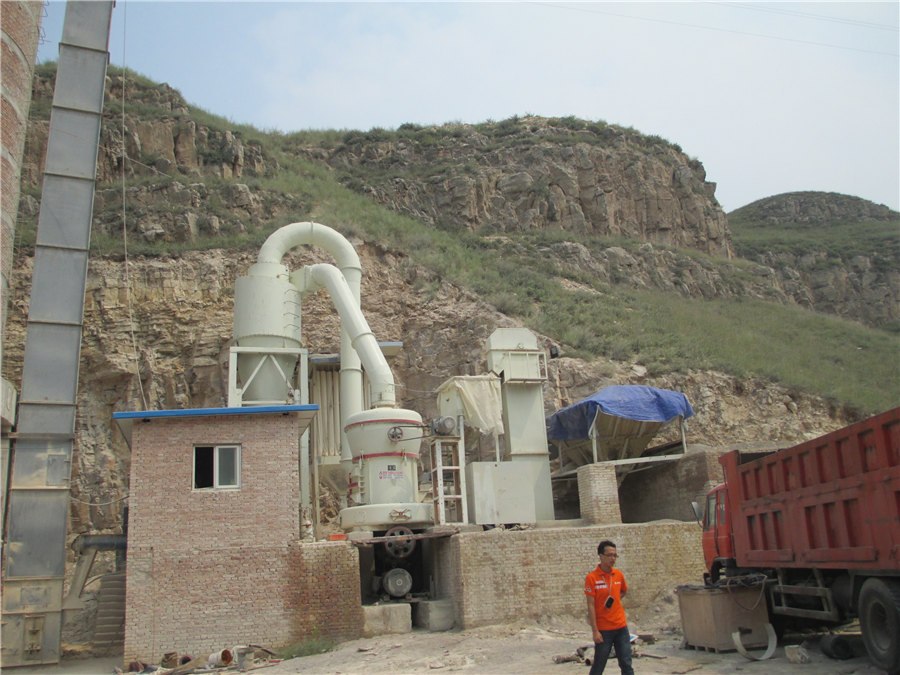
Estimation of Grinding Time for Desired Particle Size Distribution
from the ores The grinding of ore is a highly energyintensive process [1–4] In this process, the size of the particle obtained depends on the energy consumption of the ball mill The major challenge encountered in the process of iron ore grinding is to maintain the desired product particle size distribution (PSD) with sufficientTable 1 Chemical composition of typical grinding media (% wt) Adapted from [24] 211 Cast Iron Cast iron can be grey cast iron or white cast iron, but white cast irons are commonly used in Grinding Media in Ball MillsA Review ResearchGate2020年1月3日 Iron ores obtained from different sources differ in their chemical and physical properties These variations make the process of grinding a difficult task The work carried out in this context focuses on three different samples of iron ore, viz, high silica high alumina, low silica high alumina, and low silica low alumina The grinding process for all the three iron ores is Estimation of Grinding Time for Desired Particle Size Distribution 2013年4月16日 ABSTRACT In this study, ultrafine grinding of a refractory silver ore tailings was studied A laboratory scale pintype vertical stirred mill and ceramic beads were employed for the grinding testsInvestigation of some parameters affecting the Ultrafine grinding
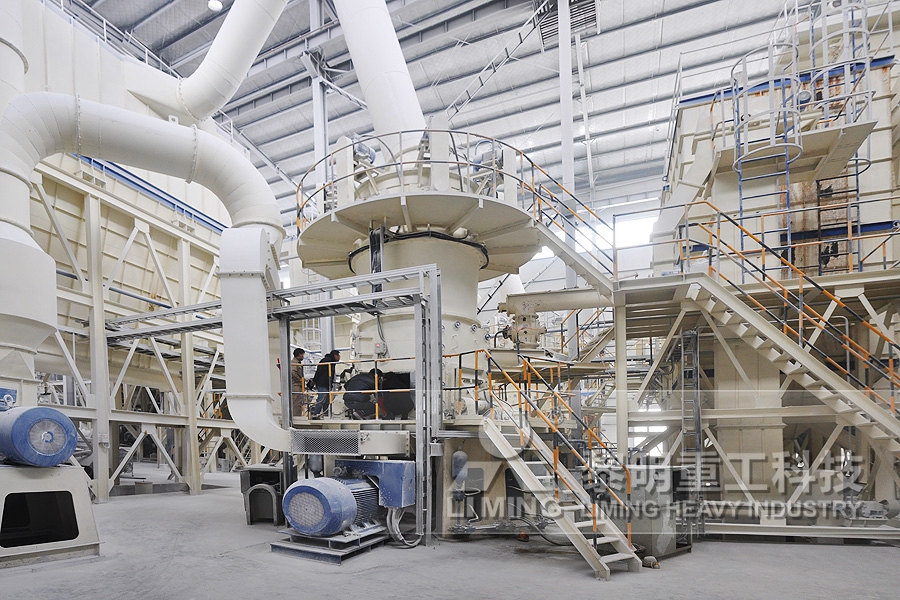
Research of iron ore grinding in a verticalrollermill
Request PDF On Mar 15, 2015, Mathis Reichert and others published Research of iron ore grinding in a verticalrollermill Find, read and cite all the research you need on ResearchGate27–61%, and feed size distribution at range of 12–30 mm Results showed that the lowest grinding efficiency was occurred at solid content of 44 wt% and deviation from this optimum amount had Effects of flow rate, slurry solid content, and feed size distribution 2020年1月3日 Request PDF Estimation of Grinding Time for Desired Particle Size Distribution and for Hematite Liberation Based on Ore Retention Time in the Mill Iron ores obtained from different sources Estimation of Grinding Time for Desired Particle Size Distribution and CLUM series of ultrafine gypsum powder vertical grinding mills are a new type of ultrafine industrial ore grinding equipment that integrates grinding, grading, powder collection and conveying +17CLUM Ultrafine Vertical Grinding Mill
.jpg)
Effect of grinding media shape on the particle size distribution of
2024年5月20日 The ball mill lifts the grinding media by rotation of its horizontal cylindrical part which then falls back impacting the ore particles The grinding action is then achieved by attrition, abrasion, and impact between the ore and the grinding media 3 Spherical media has been commonly used in ball mills; however, different shapes of grinding media have different 2023年6月1日 The main parameters of grinding and classification process include measurement of millfeeding quantity, mill load measurement, measurement of ore slurry density, Online analysis of particle size distribution in slurry, measurement of sump liquid level, pulp flow measurement, and so onMeasurement and Control for Ore Grinding and Classification2014年10月1日 In a test performed in the Loesche test center in Germany, copper slag grinding saved 229% energy in an airswept model and 344% energy in an overflow model [13,14]Copper Ore Grinding in a Mobile Vertical Roller Mill Pilot Plant2023年4月23日 grinding media in a grinding mill with about 2630 wt% chrome by Chen et al [37] using a phosphate ore in a modified ball laboratory ball mill whose electrochemical potential could be controlled(PDF) Grinding Media in Ball MillsA Review ResearchGate
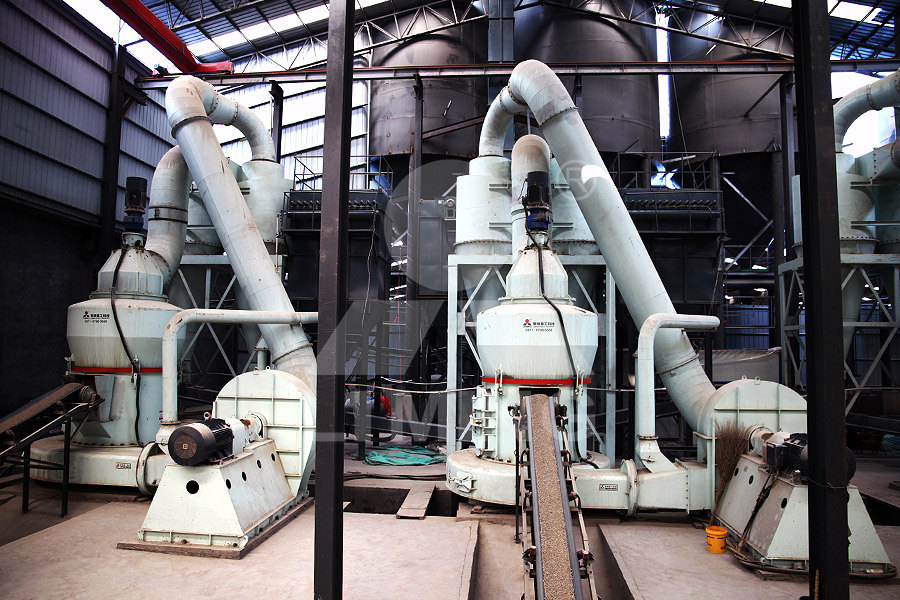
Rod Mill Grinding 911Metallurgist
2017年7月4日 As already discussed, if the breakage rate functions, ki, i = l, n, are dependent on the size distribution of the material in the mill, the batch grinding model (Equation 1) is nonlinear and the convenient analytic solutions and analysis that apply for linear grinding systems (see, for example, 11, 12, 18) are not valid in this case2016年7月7日 The recovery of gold by ore leaching is influenced by the size of the particles and the chemical environment The effect of particle size on the dissolution of gold is usually studied using mono Effect of Particle Size and Grinding Time on Gold 2013年12月31日 The grinding process for all the three iron ores is carried out individually in Bond’s ball mill and the total retention time taken by each iron ore sample is calculatedA developed approach based on grinding time to Investigation on the particle size and shape of iron ore pellet feed using ball mill and HPGR 909 areas of 500–1600 cm2 g1The concentrate must therefore be reground in order toInvestigation on the particle size and shape of iron ore pellet feed
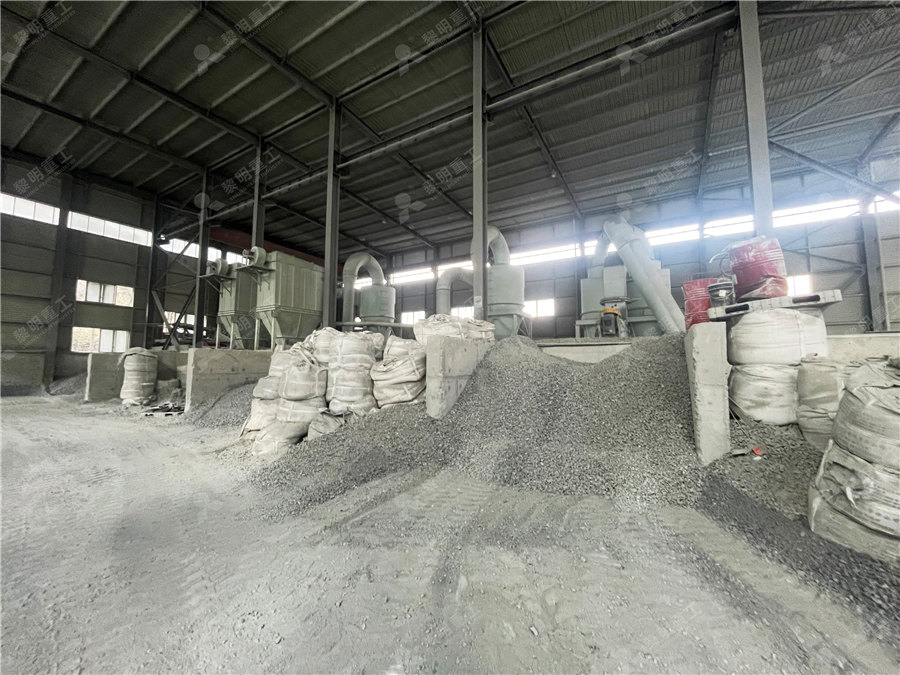
Grinding Kinetics Adjustment of Copper Ore Grinding in an
applied sciences Article Grinding Kinetics Adjustment of Copper Ore Grinding in an Innovative Electromagnetic Mill Marta WołosiewiczGłab˛ 1,*, Paulina Pieta˛ 1, Dariusz Foszcz 1, Szymon Ogonowski 2 ID and Tomasz Niedoba 1 1 Department of Environmental Engineering and Mineral Processing, Faculty of Mining and Geoengineering, AGH University of Science and 2022年12月31日 OPTIMIZATION OF LATERITE ORE GRINDING PROCESS USING BALL MILL WITH RESPONSE SURFACE METHOD December 2022; Metalurgi 37(3):119126; The size distribution of laterite ore in grinding OPTIMIZATION OF LATERITE ORE GRINDING PROCESS USING BALL MILL 2015年3月10日 DOI: 101016/JMINPRO201410002 Corpus ID: ; Copper ore grinding in a mobile vertical roller mill pilot plant @article{Altun2015CopperOG, title={Copper ore grinding in a mobile vertical roller mill pilot plant}, author={Deniz Altun and Carsten Gerold and Hakan Benzer and Okay Altun and Namık A Aydogan}, journal={International Journal of Copper ore grinding in a mobile vertical roller mill pilot plantA crushing plant delivered ore to a wet grinding mill for further size reduction The size of crushed ore (F 80) was 40 mm and the SG 28 t/m 3 The work index of the ore was determined as 122 kWh/t A wet ball mill 1 m × 1 m was chosen to grind the ore down to 200 micronsGrinding Mill an overview ScienceDirect Topics
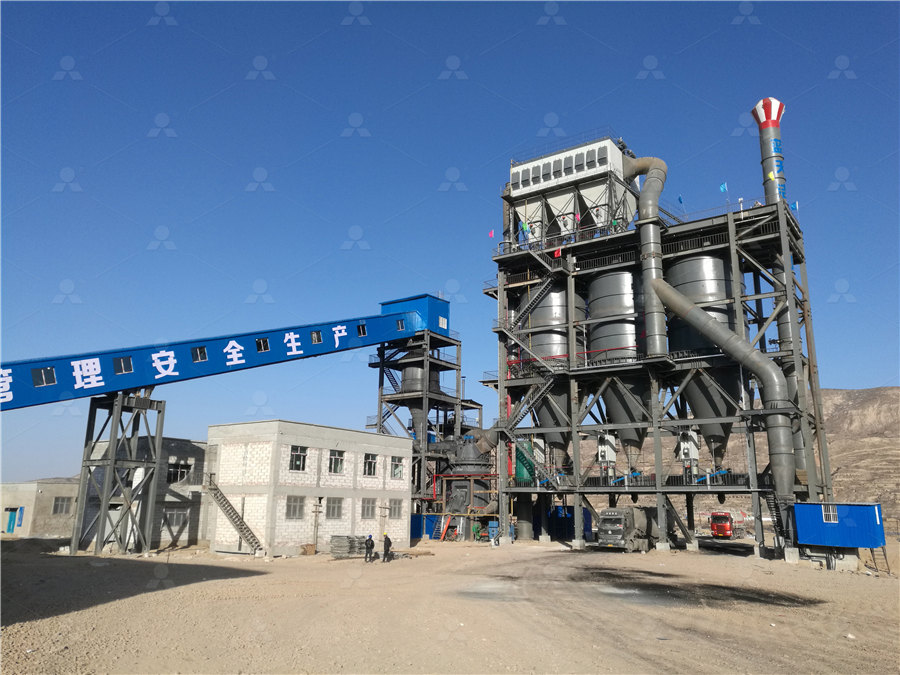
Use of the Swebrec Function to Model Particle Size Distribution in
Size distribution of the ore particles of the fresh feed to the mill The region of the experimental distribution between sizes below 6 8 mm behaves very differently, howeverCopper ore of 05% was tested using batchgrinding tests Samples were carried out using three reconstructed feed size distributions in an experimental ball mill The size distribution was reconstructed using the double Weibull formula, and modeled using the selection and breakage functions Copper ore samples were grinding up to 15 minExploring ball size distribution in coal grinding mills