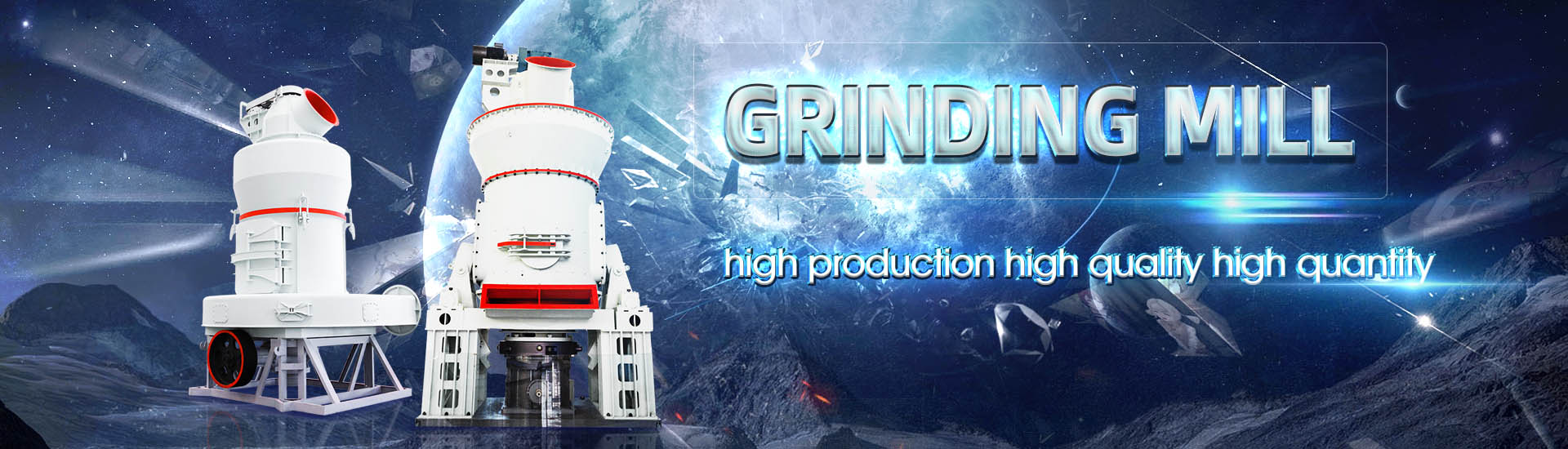
Surface quenching price requirements for large gear of coal mill
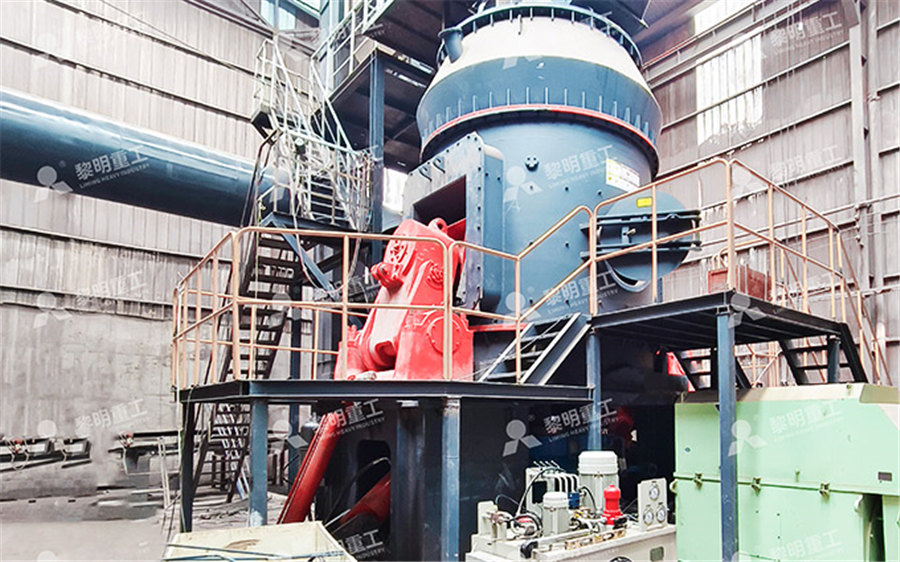
Heat Treatment of Large Components Thermal Processing
Case hardening is normally carried out at temperatures between 880°C to 980°C for carburizing, and 780°C–860°C for hardening The standard procedure is gas carburizing By diffusion of 展开Quenching has three distinctive stages: I Vapor blanket stage Delta temperature creates an insulating vapor in slow cooling 2 Vapor transport stage Liquid breaks through the vapor The Fundamentals of Gear Press QuenchingFor large gears, there is an inevitable compromise between the surface strength required and the core properties of the part To achieve properties similar to case hardened parts, more Manufacturer’s Guide to Heat Treating Gear Technology2021年7月28日 Quenching in QST is an intensive surface cooling technique that uses highpressure water as a coolant for only a few seconds Selftempering is a process of surface A theoretical approach for estimating the effect of waterjet
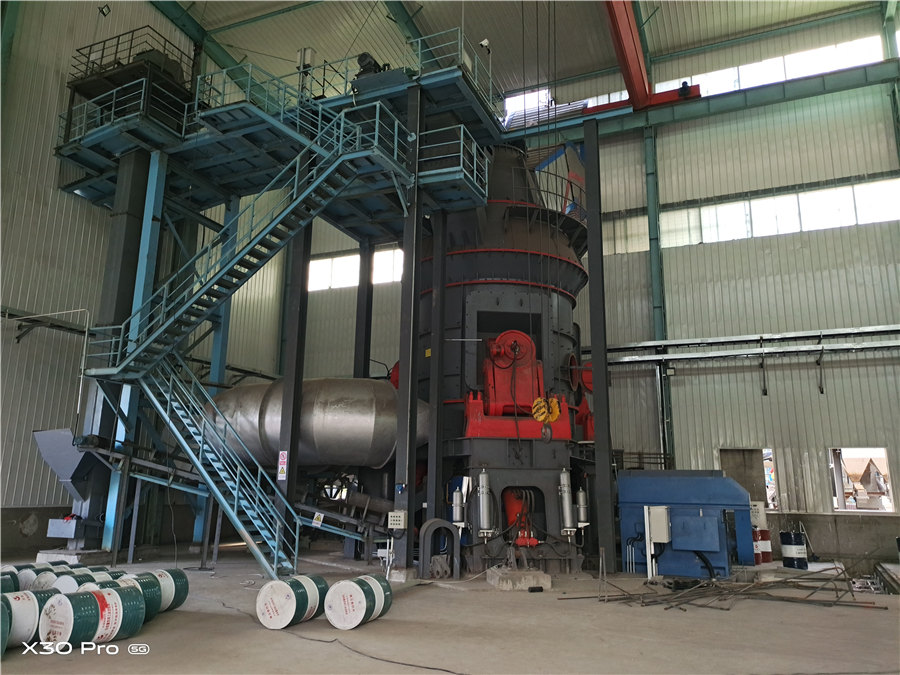
Heat Treat Processes for Gears Gear Solutions Magazine Your
2010年7月1日 The ideal quench is the slowest quench that will uniformly pull heat out of the part, while still fully transforming the surface to martensite and achieving the desired case and There are three types of final heat treatment for the sprocket, with the purpose of improving the mechanical properties such as hardness, wear resistance and strength Quenching includes Industrial sprocket heat treatment method Sprockets and Gears This article provides an overview of common quenching media, the factors involved in the mechanism of quenching, and process variables, namely, surface condition, mass and section Quenching of Steel Steel Heat Treating ASM Digital LibrarySteel selection depends upon features of the gear working conditions, required hardness and cost Lowalloy and mediumcarbon steels with 04 to 055% carbon content (ie AISI 4140, Induction Hardening of Gears: a Review
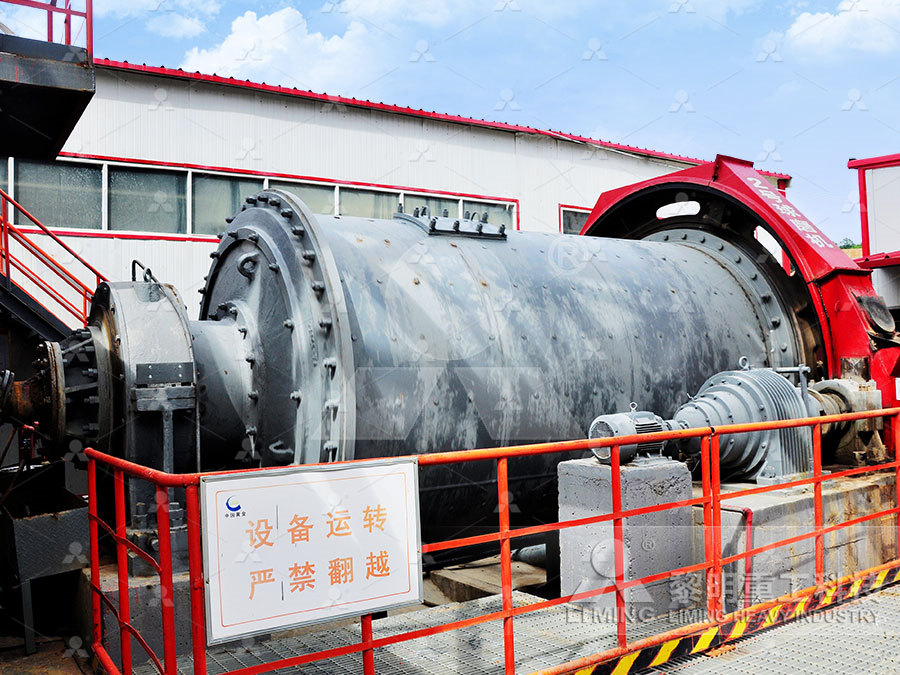
Intensive Quenching Processes: Basic Principles, Applications and
2014年5月12日 The paper discusses basics of the intensive quenching (IQ) processes to achieve better part properties and performance characteristics , and outlines specifics of IQ carburizing and quenching, annealing at moderate temperatures can be optionally applied facilitating hard machining such as grinding In recent years increasing application related Metallurgical concepts for optimized processing and properties of 2014年1月1日 The emission factors of kiln end, kiln head, coal mill, crushing and cement mill was 0156 clinker g/t, 3914 clinker g/t, 1538 coal g/t, 0016 stone g/t and 0056 cement g/t respectively, the (PDF) MPS mills for coal grinding ResearchGate2022年5月13日 Backup rolls are the main tool in a fourhigh rolling mill; the rolling forces applied in load cells promote the fatigue of the material due to mechanical contact between backup rolls and work rolls(PDF) Influence of Work Hardening on the Surface of
.jpg)
A Comparison of Three Types of Coal Pulverizers Babcock Power
either high moisture coals, or largesized coals Coal Characteristics Coal characteristics are integral to pulverizer system selection, sizing and performance The production capaci ty for each mill depends upon the following feed properties: In general,the coal entering a mill system should be crushed to a size no larger than2009年9月20日 A control oriented model was then developed by Fan (1994) and Fan and Rees (1994) In 2009, coal flow and outlet temperature of mill were modelled using mass and heat balance equations for startup Modeling and Parameter Identification of Coal Mill2012年11月17日 20 131Fineness Fineness is an indicator of the quality of the pulverizer action Specifically, fineness is a measurement of the percentage of a coal sample that passes through a set of test sieves usually designated at 50, 100, and 200 mesh A 70% coal sample passing through a 200 mesh screen indicates optimum mill performance The mill wear and Coal mill pulverizer in thermal power plants PPT SlideShareone parallel gear drive, one planetary gear drive), 3stage (one spiral bevel gear drive and two planetary gear drives) Speed Ratio: 20 ~ 60 Rated Power: 80 – 9,000 kW Applications Raw material, cement slag, gypsum and coal ash grinding, as well as pregrinding, in building material industries; coal and limestone mill in power and met01 NGC Gears
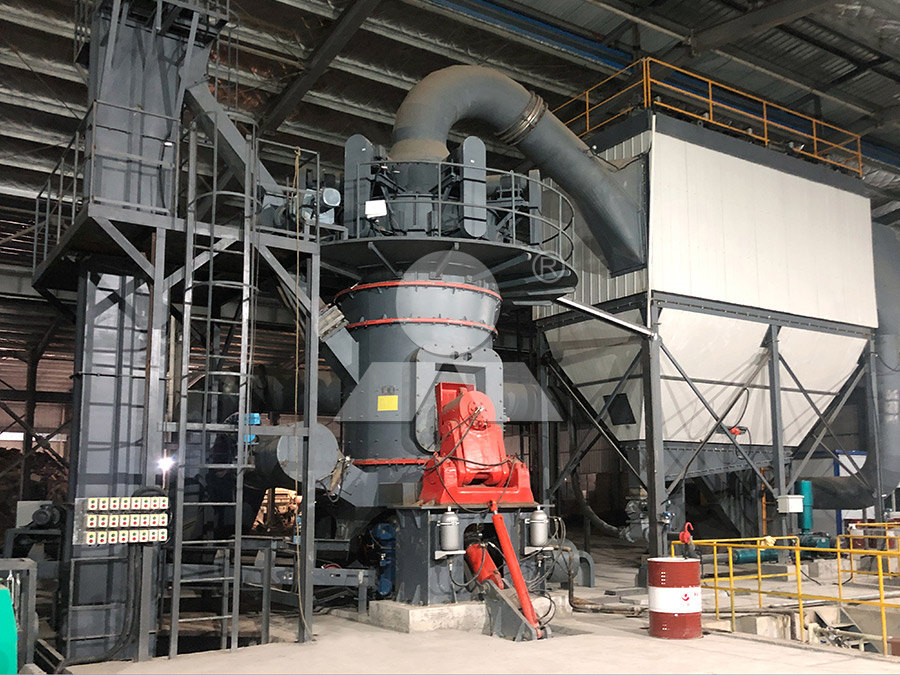
LaboratoryScale Integrated Coke Dry Quenching System for Coal
requirement is 125 kg of testing size coke and corresponding 20 kg coal blend; therefore capacity was considered as 20 kg according to following calculations: VM in coal = 19–37% Coke yield = 100 VM coal? VM coke Considering VM coke =1% Coke yield = 82–64% Therefore minimum coal requirement for single test ¼ ðÞ12:5=64 100 ¼ 19:5kg2024年3月1日 The large specific surface area of nanomaterials determines that surface defects significantly affect the properties of nanomaterials However, the complexity of surface defects makes it difficult to investigate the surface quenching mechanism theoretically, and the small size and highly sensitive growth characteristics of nanomaterials pose a challenge in revealing their Surface quenching mechanism and optimal coating shell 2021年6月22日 Quenching and cooling is the key to ensure that the effective hardening layer depth and the hardness of the center are enough after carburizing and quenching of large gear and gear shaft, and also an important means to control gear deformation and increase residual pressure stress on the tooth surfaceEquipment requirements for developing deep carburizing large heavy surface the temperature distributions are very different and much less varied There is also adelay in the features created by the delay in heat dif fusing from between surface and roll bulk The average temperature at all depths is the same when the roll is running in equilibrium The very large temperature gradients throughdepth give rise GENERAL ASPECTS OF ROLL COOLING FOR HOT COLD
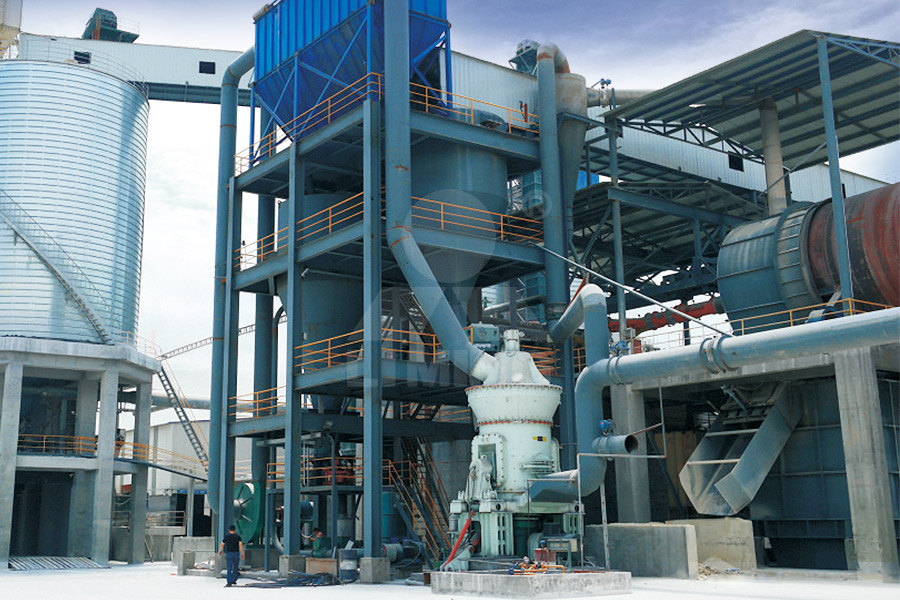
Custom Large Girth Ring Gear for Ball Mill / Rotary Kiln
First, the detection frequency quenching, the hardness after tempering ring gear cogging meets the requirements of the drawings; secondly, to detect whether the maximum outer diameter larger size D6944 as the deformation \ 3mm, the 2020年4月2日 The mill main gear b ox l ubricant co nsists o f th e main Coal mill motor power (kW) 0 4171 4548 Due to increase in fuel price and demand in more energy requirement in Analysis of the Coal Milling Operations to the Boiler 2024年7月3日 Various methods of hardening of machine parts and mechanisms are considered Volumesurface quenching of steels with reduced hardenability is analyzed The structure, hardness and toughness of steels subjected to different types of quenching are investigated It is shown that volumesurface quenching ensures a uniform distribution of hardness from the Prospects of Application of VolumeSurface Quenching for Station capacity determines the quantum of coal to be handled by coal handling plant and thus the capacity of coal unloading system, crushers, coal conveying system etc Generally for unit size of 500 MW and above, one coal handling plant is provided to cater for two units Coal conveying system may cater to maximum three units to limitSTANDARD DESIGN CRITERIA/ GUIDELINES FOR BALANCE OF
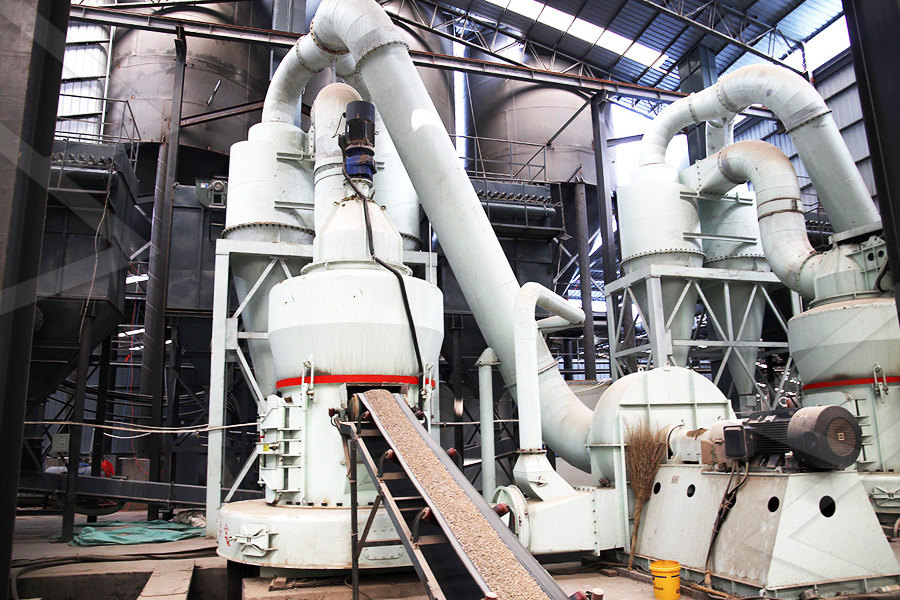
Factors affecting the service life of mill girth gear
The girth gear is the main transmission component of the rotary kiln and ball mill As the rotary kiln and the ball mill are largescale equipment, the girth gear often wears during operation, and is one of the accessories that need to be replaced regularly The poor lubrication conditions in operation, the harsh working environment, and the mixture of dust, sand, and other impurities in the 2007年7月1日 Mechanisms of Heat Removal During Quenching The mechanism of cooling a gear in liquid is largely dependent on geometry for a given material which dictates the requirements of the quench system There are three distinct stages of cooling (Figure 1) Stage A is called the “vapor blanket” (or “film boiling”) stageOil Quenching Technologies For Gears Gear Solutions Fig 1 Schematic of the coal pulverizer mill shaft N Parida et al / Engineering Failure Analysis 10 (2003) 733–744 735 Fig 2 Failure surface of a pulverizer mill shaft showing fatigue beach marks Fig 3 Failure surface of a pulverizer mill shaft, which has been subjected to rubbing during operation 3Failure analysis of coal pulverizer mill shaft AcademiaPrevious Post Next Post Contents1 COAL PREPARATION AND FIRING11 INTRODUCTION12 2COAL RESERVES13 CHARACTERISATION OF COALS BY CHEMICAL131 31 Major components132 32 Minor Components14 4CHARACTERISATION BY PHYSICAL AND MECHANICAL PROPERTIES141 41 Coal Storage142 42 Variation of Physical and COAL PREPARATION AND FIRING INFINITY FOR CEMENT EQUIPMENT
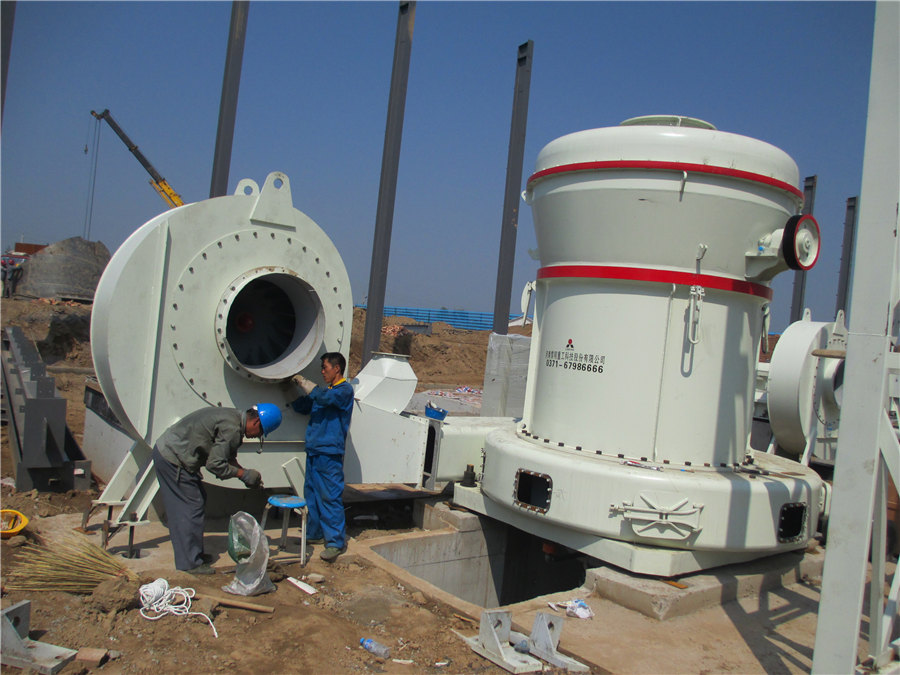
(PDF) Drives for large vertical roller mills ResearchGate
2017年1月1日 Experiments using the commonly used aluminum alloy 6061T651 on a MAKINOA55 machine tool is then designed and conducted to verity the surface roughness and to find the process parameters for best 2023年3月2日 The production of grinding balls is large, and it is usually processed by method of continuous quenching The production process of forged grinding ball is shown as Fig 1a, the round steel bar is heated by a natural gas heating furnace, heated to about 1050–1150°C and is sheared into segments, and the air hammer is used for rough forging and precision forging into Effect of Water Spray Quenching on Microstructure and Wear requirement at the mill table Fig 1 shows a schematic of a threestage bevelplanetaryplanetary gearbox The bevel gear stage changes the direction from horizontal to vertical, with the two planetary stages transmitting the drive torque to the grinding table The big design challenge for these gearboxes is mainly theDRIVE SELECTION FOR LARGE LOESCHE VERTICAL ROLLER MILLS2018年3月23日 We synthesized and characterized a set of ultrasmall hexagonalphase NaGdF4: 20% Yb3+, 2% Er3+ upconversion nanoparticles with core diameters of 37 ± 05 nm In order to assess passivation effects and the influence of possible core–shell intermixing and to identify optimum particle structures for combined imaging in the visible and nearinfrared Quantum Yields, Surface Quenching, and Passivation Efficiency
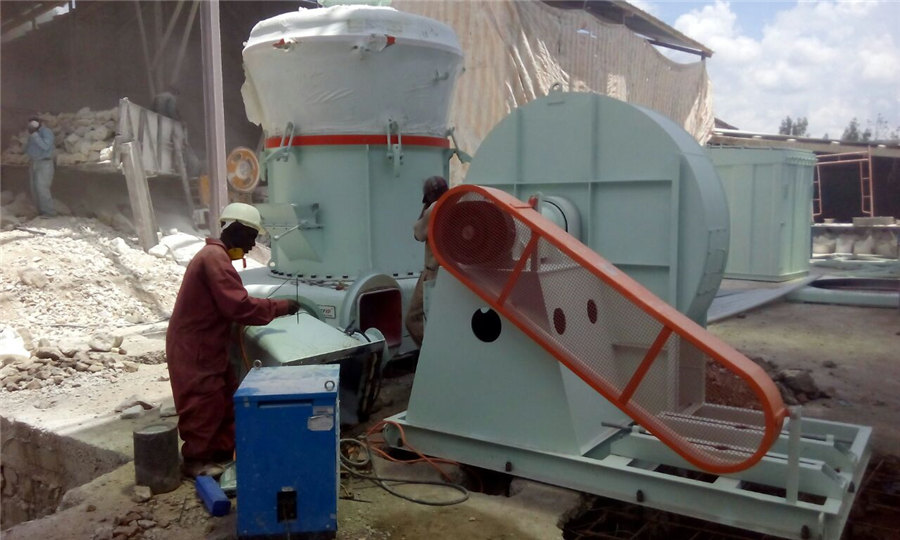
Global optimization of reliability design for large ball mill gear
2013年11月1日 The Φ55 m × 85 m large ball mill gear transmission of Shenyang North Heavy Industry (shown in Fig 3) uses a single helical gear transmission The main motor power is P = 4500 kW, the motor speed is n = 200 r/min, and the gear ratio is i = 1457 The pinion is made of 37SiMn2MoV; table quenching is 45 ~ 50 HRCVertical Coal Mill (VCM) is equipment for grinding and pulverizing coal into micron size Rotary kilns then use the powders as fuel burners The VCM has a housing section equipped with a lining The layout of the coal mill with a rotary classifierneed improvement to achieve milloptimal performance Coal feed to the mill is important, this was observed to be a limiting constraint on mill capacity when the coal required exceed nominal load requirement KEYWORDS: Air fuel ratio; pulverised fuel distribution; classifier; elutriation; heat balance; isokineticPerformance optimisation of vertical spindle coal pulverisers2021年11月4日 The rolling mill gear shaft with grinding cracks is made of 17CrNiMo6 steel, the modulus Mn is 18mm, the carburizing and quenching process requirements are that the carburizing layer depth is 330 ~ 370mm, and the surface hardness is 580 ~ 620hrcCase of gear grinding crack caused by carburizing and quenching
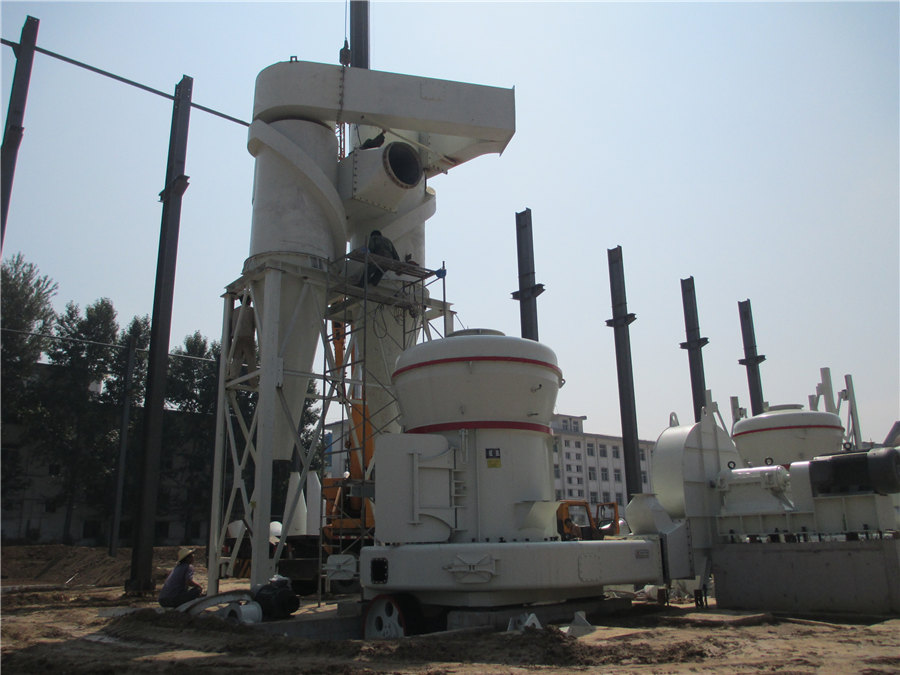
A unified thermomechanical model for coal mill operation
2015年11月1日 As presented by Andersen et al (2009) and Odgaard, Stoustrup, and Mataji (2007), coal moisture imposes limit on the maximum load at which a coal mill can be operated and the load gradient (how fast the mill may change its operating point), if it is desired that the pulverized coal entering the furnace has moisture content less than or equal to a certain value carburizing and quenching, annealing at moderate temperatures can be optionally applied facilitating hard machining such as grinding In recent years increasing application related demands towards case carburized components indicated some shortcomings of existing alloys [2] For instance, large gearMetallurgical concepts for optimized processing and properties of 2009年1月1日 below shows the particle tracks colored by the particle velocity magnitude for particles with a diameter size of 58 μm Fine particles of such a size are easily entrained in the flow and follow a CFD Modeling of MPS Coal Mill for Improved Performance and SafetyPractice has proved that the application of microcomputer control system, the worker operation is simple, the worker wants to input steel code only, the hardening layer depth and the surface carbon content of the requirement, its everything is completed automatically by the computer control, when the hardening layer depth and the surface carbon content reach the 20Cr2Ni4 Steel Gear Carburizing and Quenching Process Study
.jpg)
ATOX® Coal Mill FLSmidth Cement
Our ATOX® Coal Mill is a compact vertical roller mill that can grind almost any type of raw coal The coal mill utilises compression and shear force generated between the large rollers and the rotating table to crush and grind raw coal, Mill Feeders: Feeders for coal mill are generally installed directly under hoppers with rod gate in between The feeders are generally 2 to 3 m long and discharge on to conveyor or feeding chute to mill For coal mill feeding, table feeders, belt feeders, Coal Grinding Cement Plant Optimization520 P Niemczyk et al / Control Engineering Practice 20 (2012) 519–530 Nomenclature Dpmill mc mpc mcair mass of unground coal on the table (kg) mass of pulverized coal on the table (kg) mass of pulverized coal carried by Derivation and validation of a coal mill model for 2020年7月1日 The external surface of the coal mill shaft had been welded, and the poor welding process resulted in a large number of welding defects such as cracks, slag inclusions and lack of fusion in the Fracture failure analysis of coal mill shaft ResearchGate
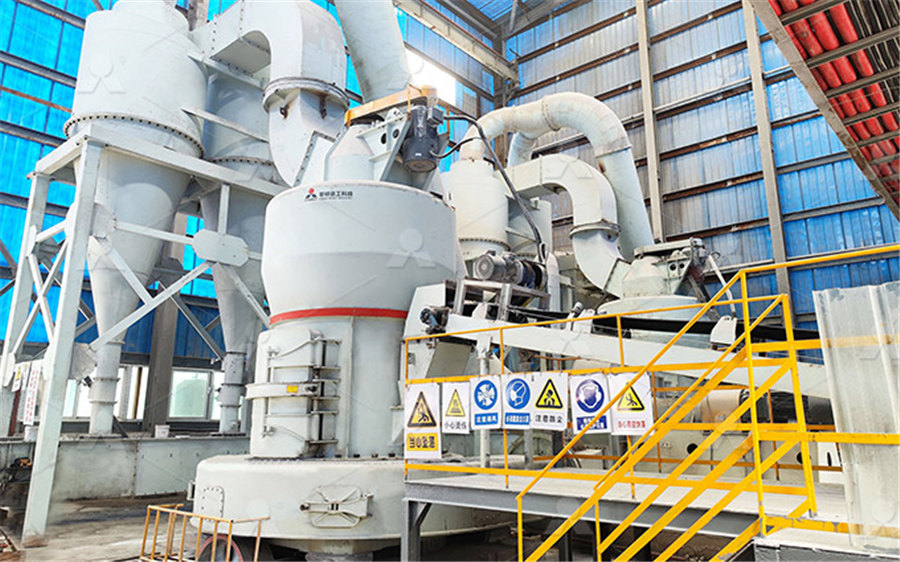
The 6 Main Process Fans in Cement factory
Coal mill fans: In cement industry coal mill fans are used to supply required air for burning coal and remove the exhaust gases produced after burning These fans help in effective burning of coal inside the mill For a large clinker line there are usually 2 2018年2月15日 Gears can be fairly large when hardening large gears and pinions (for example, mill, marine, and large transportation gears, etc), with outside diameters easily exceeding 3 m and can weigh several tons Gears used in wind turbines are typical examples where toothbytooth induction hardening is effectively usedInduction Gear HardeningA simple energy balance model of the coal mill is derived in (Odgaard and Mataji 2006), this model is based on a more detailed model found in (Rees and Fan 2003)In this model the coal mill is seen as one body with the mass m mThe following variables are defined: T(t) is the temperature in the coal dust flow in the mill, ṁ PA (t) is the primary air mass flow, T PA (t) is Coal Mill an overview ScienceDirect Topics2023年10月2日 Carburizing and quenching can endow the gear with a hardening depth, improving the part's hardness and contact fatigue strength while distorting the part, resulting in increased or uneven subsequent grinding allowances and reduced part precision Therefore, cooperative control of hardening depth and distortion is critical Here, the temperature, phase Optimization Method for Gear Heat Treatment Process Oriented
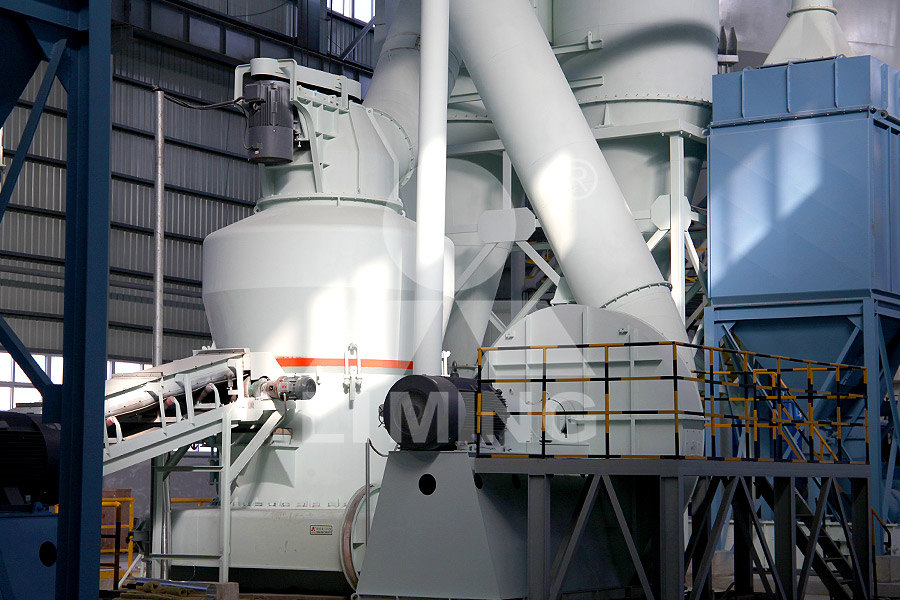
Surface Laser Quenching as an Alternative Method for
2020年4月1日 Before and after thermal treatment, all samples were ground with SiC sandpaper (grit numbers from 120 up to 600) in order to obtain surfaces with a roughness of 01 ± 003 µm measured using a roughness tester Mitutoyo SJ400 22Loesche has been involved in processing solid fuels since 1925 Some key events include delivering their first coal mill in 1927 and introducing hydraulic systems in 1961 Their mills are distinguished by grinding without metal contact, suitability for combustible dust, and low vibration even at partial load Loesche designs complete grinding plants that operate efficiently and 132 Loesche Mills For Solid Fuels Coal Mill E 2016