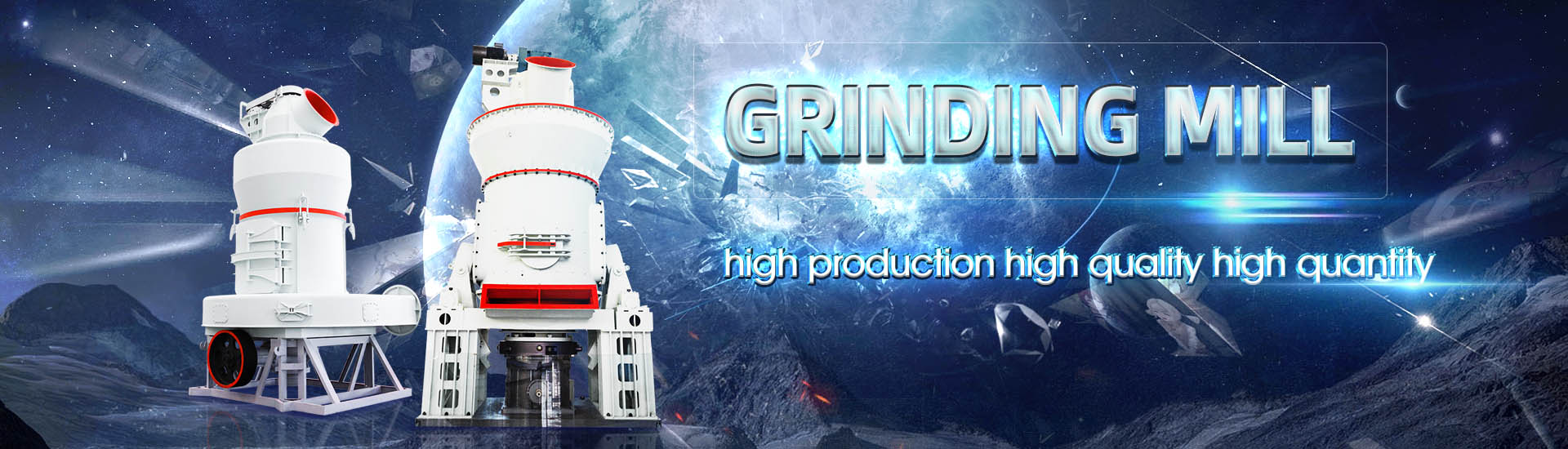
Coking plant ore mill frequency conversion technology
.jpg)
Industrial perspective of the cokemaking technologies
2019年1月1日 The operational efficiency of a coke plant depends on three vital aspects: first, the produced coke should meet the quality standards required for the use of modern blast furnaces; second, the environmental consideration; and third, the cost of the cokeIn cokemaking, Paul Wurth ofers tailormade and stateoftheart solutions for your turnkey construction projects, modernisations, top to stamp charging conversion as well as hot COKEMAKING TECHNOLOGY Paul Wurth2019年7月19日 Many and different technologies have been developed for integrating or substituting the existing ones in order to reduce the coke needing in the traditional integrated Coke Making: Most Efficient Technologies for Greenhouse 2019年1月1日 Assessment of exposure to PCDD/F, PCB, and PAH at a basic oxygen steelmaking (BOS) and an iron ore sintering plant in the UKCoke in the iron and steel industry ScienceDirect
.jpg)
Coke Plant Technologies ThyssenKrupp
complete cement plants and grinding systems of the Polysius brand, as well as machines, plants and systems for mining, extraction, preparation, processing or transshipment of commoditiesThe Yakovlevo MPP implements an ambitious development strategy, gradually increasing the ore production (Fig 5) Since 2023, the production is planned to be four million tons of ore a year, DEVELOPMENT OF THE COKING, SINTERING, AND BLAST 2023年5月2日 The main method of producing coke for blastfurnace ironmaking is laminar coking in batch furnaces A technology that considerably reduces the fraction of coking coals Development of the Coking, Sintering, and BlastFurnace 2011年1月1日 Specific cases on rolling mills promote various cleaner production technologies and practices such as using variable frequency drives in descaler unit (Pavitra and Suchitra, Nonrecovery/heat recovery cokemaking: A review of recent
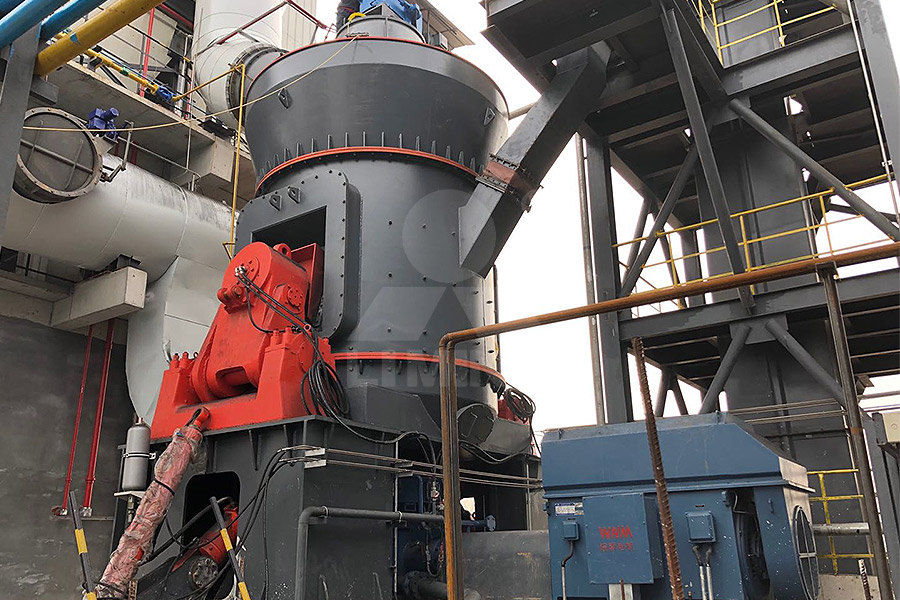
Exergy analysis and optimization of coking process
2017年11月15日 The optimization problem is solved with the practical production data of a coking plant The minimum exergy loss and the optimal design parameters are obtained coking and sinter plants • Ecological benefit Lowest processrelated emission rates • Product quality Hot metal quality suitable for ecological steel applications • CO 2 mitigation potential THE FINEX® PROCESS Primetals Technologies2021年4月21日 HIsarna is a direct bathsmelting reduction technology that combines coal preheating and partial pyrolysis with the smelting reduction vessel working as its core reaction container 18 It can allow noncoking coal and lowcost iron ores (outside BF quality range) to produce iron with 20% less carbon footprint 19 Commercial level successfulness for this Lowcarbon production of iron and steel: Technology options, economic 2016年6月22日 Coke is used as a fuel and a reducing agent in melting iron ore It is produced by baking coal until it becomes carbon by burning off impurities without burning up the coal itself When coke is consumed it generates How does coke and coal play into steel making?
.jpg)
Coking Plant an overview ScienceDirect Topics
Coke production from low rank coals Herbert Richter, André Werner, in LowRank Coals for Power Generation, Fuel and Chemical Production, 2017 1143 Development of the BHTcoking facility in Schwarze Pumpe For the lignite, refinements combine Schwarze Pumpe (later known as gas combine Schwarze Pumpe) and three hightemperature coking plants were planned home products all products blowing hoppers cyclones drag conveyors fluidizing cones gl3v roller mill conversion grain decanters grain heaters hoppers cones hydrators lam roller mill conversion lined hoppers magnetic inspection spouts pickups roll changing carts roller mill belt tensioners slide gates spouting trimmingbeading machine services all services consulting custom LAM ROLLER MILL CONVERSION CETEC Cereal Technologies2022年12月1日 Biogas to electricity conversion technology Biogas has long time established applications in direct combustion for cooking and lighting and is currently increasingly being used for power (PDF) Technologies for biogas to electricity conversionA coking plant is used to produce coke (coking coal) from metallurgical coal Coking plants consist of coke ovens (aka coking ovens, coke furnaces, coking furnaces) Coal is used to reduced iron ore to produce pig iron (aka hot metal) in the blast furnace (BF)However, it cannot be burned directly in the furnace because it contains numerous harmful byproducts that gets generatedCoking plant Global Energy Monitor
.jpg)
Process optimization of a chrome ore gravity concentration plant
2020年4月1日 The aim of this study was to optimize the recovery of chromite from the chrome plant tailings of the South African Middle Group chromite seams using a Wilfley shaking table2019年8月1日 By comparison, the point load on the particles in ball mills is conducive to the attrition process (Bu et al, 2019b;Bu et al, 2020a) Abrasion and attrition result in rounder (more spherical Differences in dry and wet grinding with a high solid 2016年3月30日 In book: Encyclopedia of Iron, Steel, and Their Alloys (pppp 10821108) Chapter: i) Direct Reduced Iron: Production; Publisher: CRC Press, Taylor and Francis Group, New York(PDF) i) Direct Reduced Iron: Production ResearchGateCoke’s role in steelmaking is to provide the heat needed to melt the ore, whose natural state is iron oxide, the rust you see on iron after it has been exposed to the atmosphere Coke also ‘steals’ the oxygen from the iron ore, so that it can become iron In the coking plant, coal is heated to 1250c in the absence of oxygen, removing impurities and creating coke, a porous Coking plant ArcelorMittal
.jpg)
Research and development of the intelligent control of iron ore
2016年3月21日 Research and development of the intelligent control of iron ore sintering process based on fan frequency conversion X H Fan School of Minerals Processing and Bioengineering, Central South University, Changsha, Hunan, China2023年5月2日 The main tasks of coking, sintering, and ironmaking processes at Severstal in 2017–2022 are specified The operation of the production complex until 2020 as part of “traditional” units of classical designs is described The assimilation of new facilities based on an essentially different technology in 2020 to 2022 is shown The results of blastfurnace Development of the Coking, Sintering, and BlastFurnace 2023年11月1日 Residue conversion by combining catalytic hydrotreating and delayed coking has been evaluated comparatively with both the wellknown mature delayed coking technology is also a possibility for combination with The evaluation of the DC plant (Case 2) considered only the feed flows and the CCR concentration of Combination of hydrotreating and delayed coking technologies 2023年8月12日 After the VFD (Variablefrequency Drive) ball mill uses frequency conversion speed regulation, the starting current can be more than 5 times smaller than the original one (for example, the Application of Sunwoele VFD (Variablefrequency Drive) on ball mill
.jpg)
Intelligent Optimization and Control of Coking Process
2019年11月14日 Coking is a complex process It features a large time constant, strong nonlinearities, and timevarying characteristics To achieve good control performance, it is important to obtain a precise COT in a realtime fashion; but this is difficult owing to restrictions imposed by the structure of a cokeoven and operating costsThe Yakovlevo MPP implements an ambitious development strategy, gradually increasing the ore production (Fig 5) Since 2023, the production is planned to be four million tons of ore a year, including 10% blastfurnace ore The mass fraction of iron is 605% in sintering ore and more than 45% in blastfurnace ore Features of the 2020–2022 DEVELOPMENT OF THE COKING, SINTERING, AND BLAST COOKING AND NOVEL FIBERLINE TECHNOLOGY LABORATORY RESULTS AND A COMPARISON TO MILL RESULTS Authors*: 1Hannu Råmark 2Janne Vehmaa ABSTRACT Sulfite cooking has dominated the production of dissolving pulp in the past For environmental reasons, production with sulfite cooking has decreased and been replaced by prehydrolysis MANUFACTURING OF DISSOLVING PULP WITH CONTINUOUS COOKING 2024年3月17日 Coal: Specifically the coking variety, is transformed into coke, serving as both a fuel and a reducing agent in the blast furnace to facilitate the conversion of iron ore into molten iron Limestone: Acts as a flux in the blast furnace It helps to remove impurities by combining with them to form slag, which can be separated from the molten ironA Visual Guide: Steel Making Process Chart Cabaro Group
.jpg)
Conversion of Sponge Iron From Low Grade Iron ore And Mill
mill scale represent about 2% of steel produced and it available as a secondary material due to its richness in iron (about 72 % Fe) More than 14 million tons of mill scales are generated yearly in India and is expected to reach about 30 million tons by 2020 In an integrated steel plant, almost 85% of the mill scale, generated isfootprintImpact of Cokemaking Technology on a Steel Plant’s Carbon 2017年6月5日 FINEX® is based on the direct use of iron ore fines and noncoking coal while eliminating the cokemaking and sintering processes, The FINEX® Process combines coking plant, [Great Conversion to Lowcarbon Discover the Technology that is Making Steel In 1976, we constructed the first CDQ plant at the Yawata Works of NIPPON STEEL CORPORATION, with a capacity of 56 t/h Since then, we have not only recorded a large number of construction achievements, but we have also Coke Dry Quenching (CDQ) System Nippon Steel

Conversion of Sponge Iron From Low Grade Iron ore And Mill
The case studies of processing of low grade iron ore fines from iron ore mines, processing of iron ore beneficiation plant tails have been discussed where in the pellet grade concentrate and cement grade iron concentrate were produced at 75 wt% of ROM and 50 wt% yield of plant tailings equivalent to 125 wt% yield of ROM 2021年7月22日 plant is to treat the coke oven gas sufficiently so that it can be used as a clean, environmentally friendly fuel Top Coke oven / byproduct plant interface In a byproduct coke oven the evolved coke oven gas leaves the coke oven chambers at high temperatures approaching 2000()()FSteelmaking: The Coke Oven ByProduct Plant accci2021年3月8日 BFBOF operation relies almost entirely on coal products, emitting ~70% of CO2 in the integrated plant (BF iron making) Hot iron is then charged to BOF to make steel HM (BOF steel making) An integrated BFBOF production plant also include process plants for coking, pelletizing, sinter, finishing, and associated power productionLowCarbon Production of Iron Steel: Technology Options, 2017年11月15日 Taking a typical coking plant as an example, the optimization model is solved and analyzed with the practical production data The dosages of 1/3 coking coal (m coal,1), gas coal (m coal,2), fat coal (m coal,3), lean coal (m coal,4) and coking coal (m coal,5) in five coal storage rooms are optimizedExergy analysis and optimization of coking process

Energy Utilization in Coking Process SpringerLink
2022年11月16日 Coking (coking chemistry) process is the production and energy conversion process of converting primary energy coking coal into secondary energy resources (coke, coke oven gas, coal tar, etc) through hightemperature carbonization Its energy consumption accounts for about 20% of the total energy consumption of ferrous metallurgyWe present photonic frequency conversion technology for generation, transmission, and reception of 5G radio signal in the millimeterwave band Photonic upconversion technology using a stable radiooverfiber system is presented for generation of low phase noise radio signal Simple photonic downconversion technology is proposed for simultaneous detection and down Photonic Frequency Conversion Technology for 5G Advanced 2024年4月29日 The ball mill’s drag system has been modified using variable frequency speed regulation technology, which satisfies the ball mill’s characteristics of lowspeed operation and large starting Application of Sunwoele VFD (Variablefrequency Drive) in ball mill 即时翻译文本完整的文档文件。为个人和团队提供准确的翻译。每天有数百万人使用DeepL进行翻译。DeepL翻译:全世界最准确的翻译 DeepL Translate
.jpg)
Technology of Producing Petroleum Coking Additives to Replace Coking
world is delayed coking; this process makes it possible to extent petroleum processing to produce commodities at the oil refinery plant up to 98%4,5 In 2021, the total crude material capacity of the delayed coking units in Russia was about 136 million tons6,7 Using this process, the light petroleum product2005年2月1日 An Aspen Plus modeling platform was developed to evaluate the performance of the conversion process of degermed defibered corn (DDC) to ethanol in 15 and 40million gallons per year (MGPY) dry Enhancing Profitability of Dry Mill Ethanol Plants: Process Modeling 2023年12月11日 The traditional ironmaking technologies (including coking, sintering, pelletizing, and BF ironmaking process) are carbonintensive, which makes the industry a significant contributor to global CO2 emissions Hydrogen replacement of carbon in steelmaking processes is a sustainable way to reduce CO2 emissions First, the reduction thermodynamics and HydrogenBased Reduction Technologies in LowCarbon 2018年7月11日 Lundgren et al (2013) assume a constant cost of 224 €/MWh for COG, while BFG and BOFG are assumed to be free Yildirim et al (2018) assume that COG will be replaced by natural gas within the Chemical Conversion of Steel Mill Gases to Urea: An Analysis of Plant
.jpg)
Application of frequency conversion technology and energy
Inverter technology for its energy saving, safe, easy to control, easy operation, etc, is widely used in oilfield production It becomes one of the pumping electric drive system control technology In light of work characteristics of the beam pumping unit, it pointed out the advantages of the variable frequency drive, discussed the work characteristics of the beam pumping unit inverter 2023年11月10日 All content in this area was uploaded by Hassan Z Harraz on Nov 10, 2023DIRECT REDUCED IRON ORE: Production ResearchGateFor the last decade, most of the research works have been oriented towards effective treatment of coking wastewater with proper integration of biological treatment with advanced treatment techniques (Liu et al 2016; Kumar et al 2017; Xue et al 2017; Wang et al 2019)Investigation towards enhancing the biodegradability of coking wastewater has also been in the limelight of Advances in treatment of coking wastewater IWA Publishing2022年8月5日 Currently, conventional oil is used as the main source for the petrochemical industry However, conventional oil’s capacity is declining, and that source will probably be exhausted in the near future Heavy oil and petroleum residues have become a suitable alternative source to meet global energy demand However, heavy oil and oil residues require Coking IntechOpen
.jpg)
Selection of a Delayed Coking Technology at Predesign Initial
2023年12月6日 In the newgeneration Russian delayed coking plants [1, 3], formation of the secondary feedstock and, consequently, control of the recirculation ratio are accomplished in an additionally installed column, to which the preheated feedstock and the recycle, for which heavy coking gas oil or what is called still gas oil is used, are fed from the bottom of the main