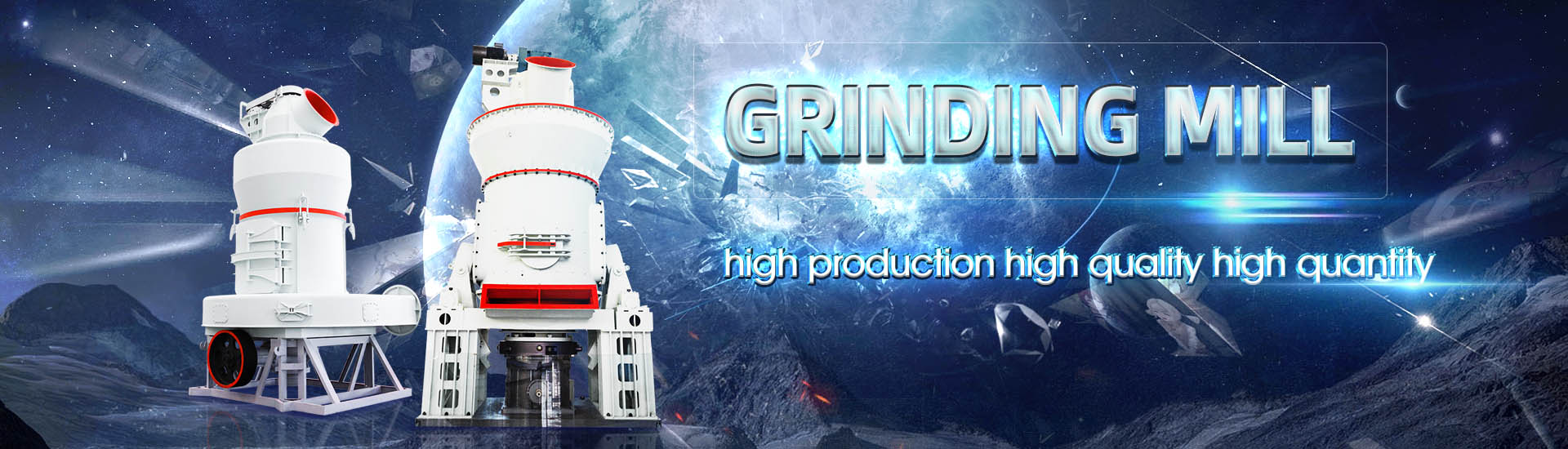
Can the roller ore mill control the shape of the material
.jpg)
Operational parameters affecting the vertical roller mill
2017年4月1日 The control of the circulating load is achieved by adjusting the pressure drop over the mill comprising out of the gas flow and the solid loading inside the mill Higher classifier roller mill operator can control the particle size by widening or narrowing the roll gap For most roller mills, the roll gap is automatically adjusted through a PLC that’s programmed to change Roller mills: Precisely reducing particle size with greater efficiencyIn this paper, Taguchi optimization technique is used to predict the best results for the given inputs such as roller diameter, friction value, velocity of the rollers and percentage reduction to Optimize the Rolling Process Parameters for Material AA1100 Rolling is the most important metal forming process More than 95% of ferrous and nonferrous metals and alloys are processed to their usable shapes by rolling Usable shapes of rolled Introduction to Rolling Process Cambridge University Press
.jpg)
Rolling operation in metal forming: Process and principles
2020年6月17日 The present article aimed to access rolling techniques in metal forming operation, or as part of the industrial manufacturing process Comparison in performance of 2020年1月1日 At least, more than 95% of the ferrous and nonferrous metals are processed to desired shapes through rolling These desired metal shapes include plates, foil, strip and Rolling operation in metal forming: Process and principles – A brief The simulation results showed that VCR configuration can significantly enhance the control efficiency of the work roll bending force and increase the transverse stiffness of rolling mill Improvement in shape control performance of finishing mills in Controlling grain size through the crosssection Controlling size and distribution of precipitates in the hot band Sheet hot rolling mills begin with a continuously cast steel slab Slabs must be Principles of Hot Rolling AIST
.jpg)
Optimization of Metal Rolling Control Using Soft Computing
2019年11月25日 Through rotating rolls, the continuous plastic deformation of the metal leads to a change in size and shape, while at the same time improving the metal structure and material 2022年11月30日 Crackers – A mill used to crack grain or other types of friable materials; Flakers – Mills used to flake grains or other materials; Grinders (Rollers mill grinders) – Roller mills that are used to grind in a feed mill Roller Mill: Components, Designs, Uses, Advantages Investigation on the particle size and shape of iron ore pellet feed using ball mill and HPGR grinding methods Armin Abazarpoor, Mohammad Halali Materials Science Engineering Department, Sharif University of Technology, Azadi Street, PO box 1136511155, Tehran, Iran, Corresponding author: f (Armin Abazarpoor)Investigation on the particle size and shape of iron ore pellet feed 2013年5月30日 Fig 4 Roll configurations in rolling mills Twohigh mill roll configuration – This is the most commonly used rolling mill configuration In this configuration, there are two horizontally mounted rolls The rolling mill motor Basics of Rolling and Rolling Mills – IspatGuru
.jpg)
Analysis of vertical roller mill performance with changes in material
2022年5月31日 Mineral crushing is the main source of energy consumption in mineral processing According to statistics, this consumption accounts for about 35–50% of the total cost of the mine (Curry et al, 2014), or even higherIt may also account for 18% of the global electrical energy consumption (NapierMunn, 2015)More efficient crushing equipment needs to be 2001年9月1日 Since the 1960s, the computer control systems have been installed in hot strip mills Nowadays, the control area covers reheating furnace combustion control, roughing mill setup, finishing mill setup, dimensional control (thickness, width and profile), temperature control (finishing mill delivery temperature, coiling temperature), etc Various kinds of sensors are State of the art in hot rolling process control ScienceDirectAt a rolling mill, blooms and slabs are further rolled down to intermediate parts such as plate, sheet, strip, coil, billets, bars and rods Many of these products will be the starting material for subsequent manufacturing operations such as forging, sheet metal working, wire drawing, extrusion, and machiningMetal Rolling2023年2月11日 Angular rolling technology can overcome the size limitation of plate mill equipment and product heavy steel plate with large unit weight or improve the production efficiency of small width spreading ratio product With the DEFORM software, the numerical simulation study of the angular rolling process was carried out, and the relation laws of the Research and application of the angular rolling technology for plate mill
.jpg)
Investigation on contact pressure of backup roll with parabolic
2023年7月18日 The work rolls of CVC rolling mill usually adopt Sshaped roll profile curve in the rolling process of plate, which changes the contact between the rolls and causes the contact pressure distribution between the rolls to be uneven The peak of the contact pressure between the rolls appears at the end of the roll, which leads to peeling or “meat loss” at the end of the 2015年11月21日 In a broader sense, a rolling mill is an automatic system or line of roll stands along with a series of equipments that performs both rolling and auxiliary operations: transport of the original billet/bloom/slab from the stock to the heating furnaces and the mill rolls, transfer of the rolled material from one roll stand to another, turning or twisting in case of some mills, Basics of Rolling of Steel – IspatGuruMill control system monitoring picture contains raw ingredients system, roller mill system, tran sportation and storage system of raw material the running state ofthe equipment and operation pa Design and Realization Of Roller Mill Control System2023年5月31日 The gear train, therefore, rotates the work rolls in a circular motion, and through the motion; the metal material is passed between the rolls You can control the whole process using the planetary gear train designed for A Definitive Guide to Rolling Mills: All You Need to
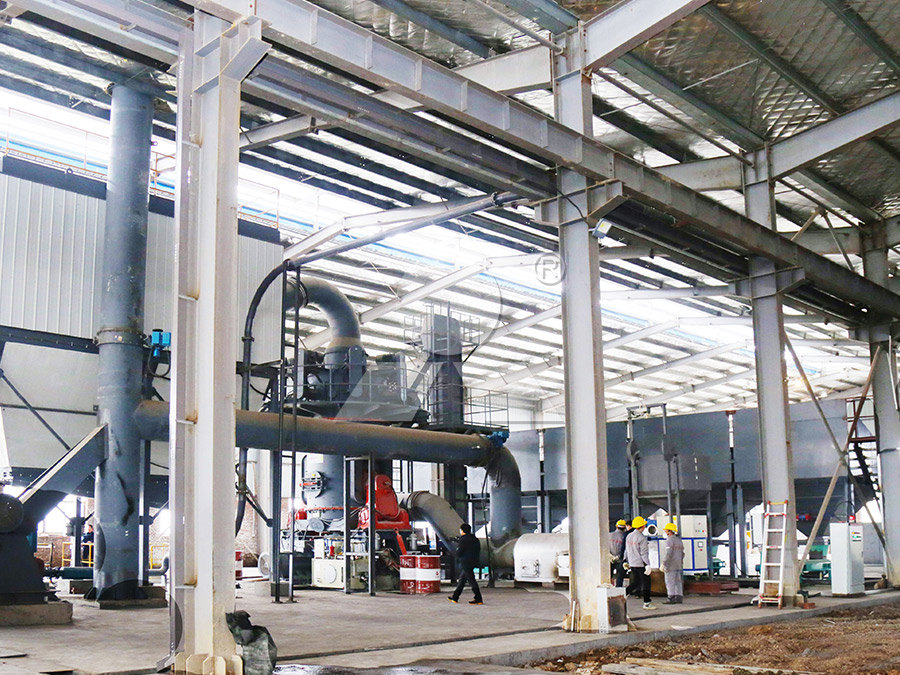
Improvement in shape control performance of finishing mills in
Donghua steel continuous casting–rolling (DSCCR) production line is an endless rolling production line independently integrated and developed by a Chinese enterprise To solve the problem of outofcontrol shape caused by insufficient adjustment ability of work roll bending force of DSCCR finishing mills, the backup roll contours of the finishing mill were optimized FINISHING MILL BackUp Roll (Undriven) Work Roll (Driven) Looper (Interstand Tension Control) Entry Side Guide (Strip Centering in Roll Bite) 0125” 0094” (248%) 0080” (149%) 650 fpm 890 fpm 1380 fpm Making, Shaping and Treating of Steel: 101 Mill Configuration FINISHING MILL Work Rolls BackUp Roll FM Stand 39 40Principles of Hot Rolling AIST2024年1月8日 The roll deformation model of the sixhigh rolling mill is one of the core models of the strip shape control theory The influence function method (IFM) is a numerical method applied to solve the roll deformation problem This study aims to address the problems of slow calculation speed and insufficient calculation accuracy of IFM in calculating the roll deformation of the six An improved method for calculating roll deformation of sixhigh 2002年10月10日 In addition, mills can control the gap profile by bending these huge rolls or by expanding them with hydraulic pressure like a huge steel balloon Figure 5 Camber is an edgetoedge length differential defect You've probably seen the pictures of the mill control pulpit with all its of the material and destroy the coil shape in Everything you need to know about flatteners and levelers for coil
.jpg)
Roll Forming AHSS Guidelines
Roll Forming takes a flat sheet or strip and feeds it longitudinally through a mill containing several successive paired roller dies, each of which incrementally bend the strip into the desired final shape The incremental approach can minimize strain localization and 2022年6月1日 This control input can also be adjusted while the plate moves through the roll gap two CMOS cameras are installed at the entry and exit side of the mill stand, above the roller table neither the upstream lateral position nor the upstream shape of the plate can be accurately measured with the entryside cameraAre edger rolls useful to control the plate motion and camber in a 2012年9月27日 Mill design, which follows engineering rules, design concepts, and past design experiences, provides a fundamental blueprint of a mill The mill design innovation focuses on performance On the Optimization Procedure of Rolling Mill Design• Thickness feedback control • Thickness feedforward control • Mass flow control • Speed feedforward control • Roll eccentricity control • Tension feedforward control Thickness feedback control The basic control strategy is thickness feedback (monitor control) based on the measured thick ness deviation at the exit side of the millMETALS Improving quality and costefficiency in cold rolling ABB
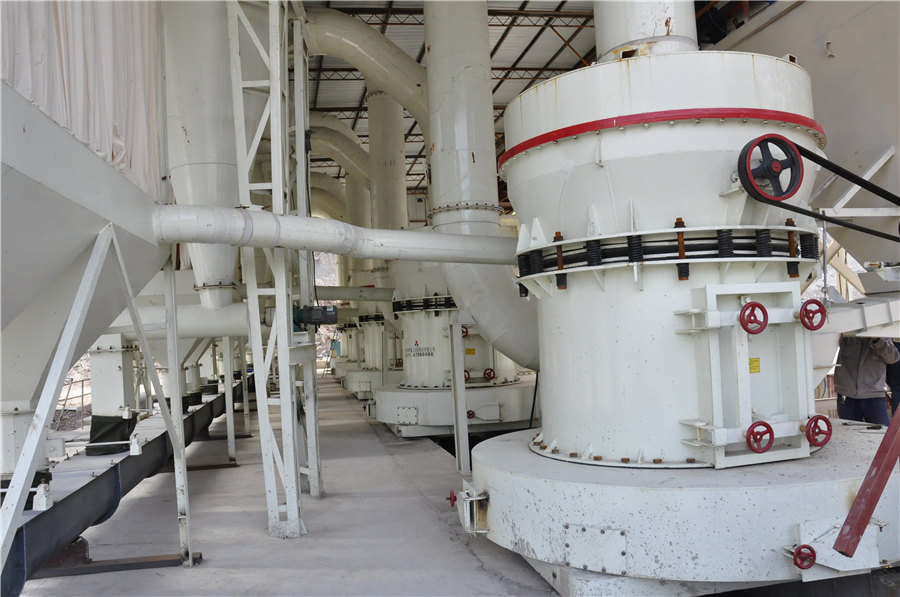
Modeling and validation of bending force for 6high tandem cold
2022年9月28日 As shown in Fig 3, the UCM 6high cold rolling mill is based on the ordinary 4high cold rolling mill with the addition of an intermediate roll that can shift laterally between the work roll and the backup rollThrough the hydraulic roll bending system, applying a variable bending force to the end of the work roll or intermediate roll instantaneously changes the The control methods to enhance the shape control ability and improve the shape quality are mainly divided into three aspects: the configuration and design of work roll contours and backup rolls contours, the accuracy of the shape control model, and the rolling process system [4] Through investigation and research on the production line, it isImprovement in shape control performance of finishing mills in 2015年4月9日 autogenous grinding, ball mill, grinding mills, hammer mill, rod mill, roller mill, SAG, Grinding Mills and Their Types In various fields of the process industry, reduction of size of different materials is a basic unit Grinding Mills and Their Types – IspatGuru2012年12月31日 So roller mill control system present has be com e the bottleneck of vertical grinding rapid clay, ir on ore, fl uorite, slag as material, USES the belt says realization of automatic Design and Realization Of Roller Mill Control
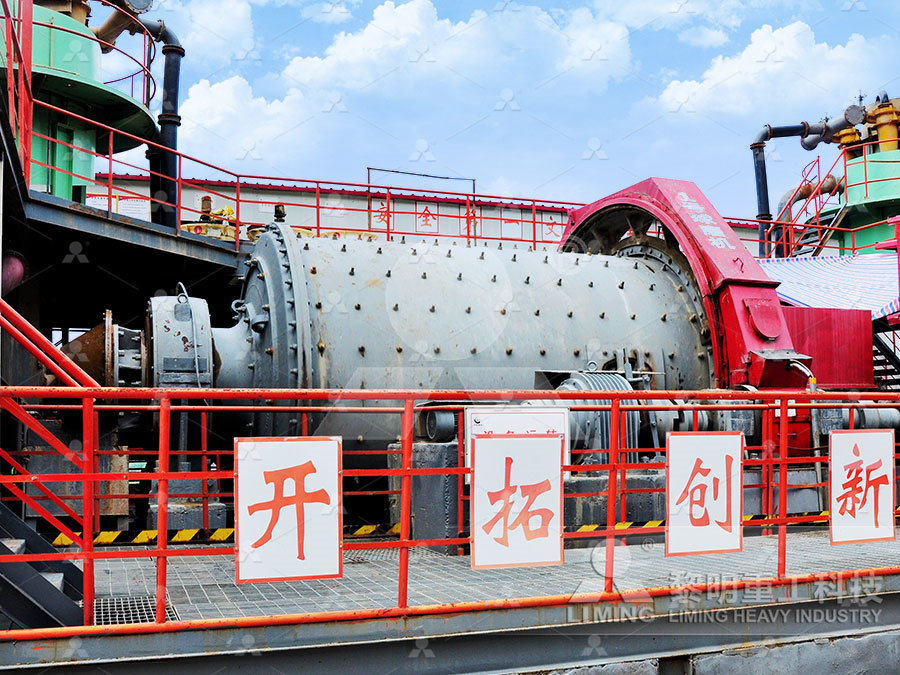
Rolling Process for Steel – IspatGuru
2014年3月27日 Fig 3 Rolling of thick plate in a plate mill Prediction of stresses and rollseparating force – Once the spread (the boundary of the deformation zone) has been calculated, this information can be used to predict the stresses and the rollseparating force The computerized procedure used here is in principle the same as the method described for 2023年8月5日 Terminology Used In Rolling Process Common Terminologies in Rolling: Ingot: The initial metal input provided to the rolling process, extracted from casting with various defects Bloom: The first rolled product of an ingot, having a crosssectional area greater than 230 \(cm^2\); Billet: A product obtained by further rolling of a bloom with a crosssectional area Rolling Metal FormingWorking, Types, Advantages and HGM ultrafine grinding mill can process nonmetallic ores with Mohs hardness less than 7 The equipment and the ground powder has high whiteness and good shape CLUM vertical roller mills are very popular in the production of highend non Limestone Ultrafine Vertical Grinding Mill – Case in Mali Material: limestone Fineness: 500meshSBM Ore Ultrafine Grinding Mill2014年1月1日 Conference: Proceedings of the 23rd International Mining Congress and Exhibition of Turkey IMCET 2013; At: Kemer, Antalya, Turkey, April 1619, 2013, pp 293301Factors affecting the performance of crushing plant operations
.jpg)
Analysis of Shape Control Characteristics for UCMW Cold Rolling Mill
2020年8月7日 In order to analyze the flatness control characteristics for a certain UCMW (Universal Crown Mill with Work roll shifting) cold rolling mill, combined with the actual parameters in the field, a 2021年1月29日 In order to help the Vertical Roller Mill (VRM) working stably with higher automation level and lighter labor intensity, an intelligent automatic control system is designed by analyzing the Increase productivity of vertical roller mill using seven QC tools2020年8月7日 In order to analyze the flatness control characteristics for a certain UCMW (Universal Crown Mill with Work roll shifting) cold rolling mill, combined with the actual parameters in the field, a static simulation model of the quarter roll systems of the UCMW cold rolling mill was established by the ANSYS finite element software The bearing roll gaps under the factors of Research on Shape Control Characteristics of Nonoriented2020年3月1日 The miller must control compression to avoid damage to the flour and prevent excessive flaking of endosperm particles Flaked endosperm can reduce flour yield, because overtails from the top sieves during reduction ends up in the mill's overtails streams and, subsequently, the bran stream (stock that has gone over a sieve is known as ‘overs’)Stone milling versus roller milling: A systematic review of the
.jpg)
Rolling mill control: architecture and applications IEEE Xplore
1998年3月4日 Considers some of the distributed aspects of the control of modern metal rolling mills Such mills have a range of ever more ambitious targets, for example product quality, yield, metallurgy and throughput These aims are supported by high levels of mill sophistication, in terms of plant equipment, instrumentation, actuators and control hardware In spite of this roll bite and in a typical Cold Tandem Mill, work roll temperatures normally fall in the range of 55oC – 70oC with strip recoil temperatures and interstand strip temperature rarely exceeding 160 oC depending on product Roll Bite temperatures in slower heavily drafted stands can peak in the region of 300oC, diminishing with theFundamentals of Roll Cooling and Control of Flatness at Lechler2019年11月13日 Metallurgy of Rolling mill Rolls satyendra; November 13, 2019; 2 Comments ; Back up roll, Cast roll, Chilled iron rolls, Forged rolls, Roll barrel, Roll neck, Roll wear, rolls, Work roll,; Metallurgy of Rolling mill Rolls Rolls are implements or tools used in rolling mills to reduce the cross section of the material being rolledMetallurgy of Rolling mill Rolls – IspatGuruThe Pfeiffer pilot mill used in this study is a semiindustrial vertical roller mill of type MVR with a table diameter of 400 mm The mill can be equipped with different classifiers for specific applications The process layout of the plant (Figure 2) corresponds to that of an industrial plantVertical Roller Mills used for the comminution of mineral ores
.jpg)
1 Hot rolling and rolling defects: 11 Front and back tensions
Fig 171: Rolling mill control From the above curves, we could understand the control of rolling mill The solid curve, called plastic curve, represents the variation of rolling load with rolled thickness As thickness reduces, roll force increases This was shown earlier The solid line represents the elastic deformation of the roll2021年2月8日 The technologies used for the shape control of the plates are continuous variable crown (CVC) along with work roll bending and backup roll bending The shape control technology also makes use of software/ sensors consisting of (i) a highaccuracy crown model which considers 3dimensional deformation of the rolling material, (ii) proximate Rolling of Steel Plates in a Plate Rolling Mill – IspatGuru2023年12月4日 21 Vertical Roller Mill The VRM shall have three or four rollers and a table The rollers were pressed against the ore and table using hydraulic cylinders during operation The table is rotated by an external drive train, and rollers are counterrotated due to the friction between the roller and materialNumerical Investigation of Vertical Roller Mill Operation Using There is a distinct cooling system for every roller A pressure blade is there for roller gaps, hydraulic control, etc Three roller mill of this type is overall equally userfriendly in nature If you are interested in, you can read Graphene Sheet Films Applications SG Roll Mills They are the improved versions of the S triple rollThree Roll Mill and The Potential Applications
.jpg)
Rolling Mills: What They Are How They Work What is a Rolling Mill?
2021年4月19日 Rolling mills can be designed with specialty tooling to impart patterns on the material – this is known as an embossed mill Additionally, grooved mills can be used to reduce round and bar stock by reducing the overall area of the material but maintaining the shape