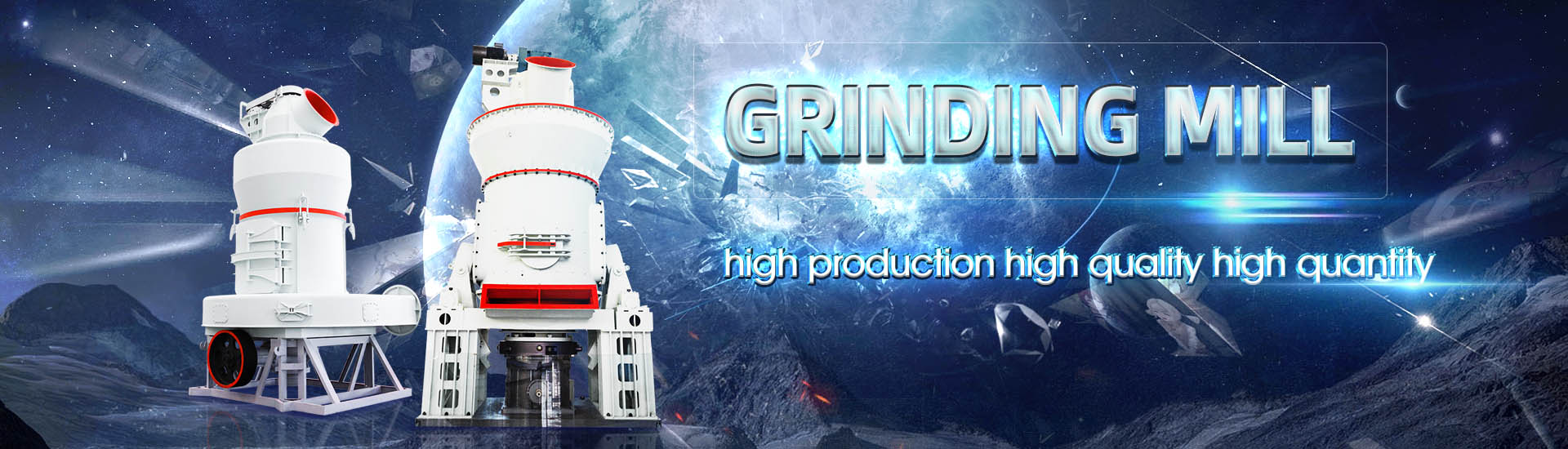
Cement clinker grinding
.jpg)
An Introduction to Clinker Grinding and Cement Storage
Clinker Grinding The cement clinker is ground as finished cement, in a vertical roller mill for cement or in ball mills similar to those normally used for grinding hard raw materials in dry and semidry processes However, the cement 2023年10月19日 Explore the significance of clinker grinding in cement manufacturing, from particle size reduction to improved reactivity and quality control Learn how this integral process transforms clinker into the final Clinker Grinding Techniques in Cement Manufacturing2023年10月23日 Grinding aids can improve production and fineness and decrease energy consumption by reducing the agglomeration of particles and protecting the balls and liners in the mill In this study we(PDF) A study of different grinding aids for lowenergy 2004年11月1日 There is potential to optimise conventional cement clinker grinding circuits and in the last decade significant progress has been achieved The increasing demand for “finer Cement grinding optimisation ScienceDirect
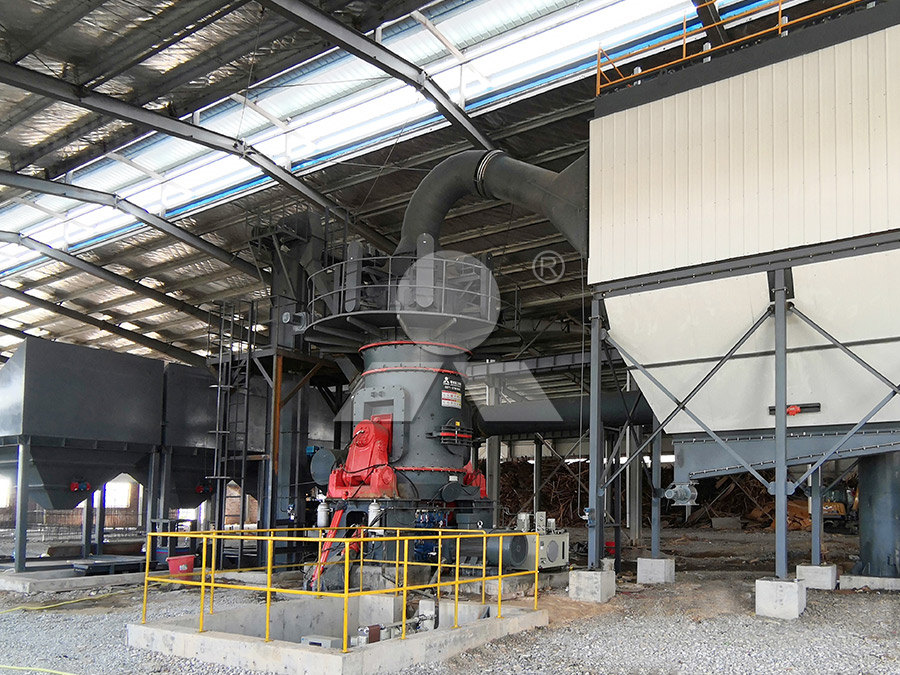
Clinker grinding technology in cement manufacturing
2019年1月3日 Clinker grinding technology is the most energyintensive process in cement manufacturing Traditionally, it was treated as "low on technology" and "high on energy" as grinding circuits use more than 60 per cent of total energy Clinker, the residue formed by hightemperature burning of coal or similar materials, plays an important role in the composition of cement and contributes to the properties of cement in Clinker – MIT Concrete Sustainability Hub2022年2月18日 Cement producers can apply the following measures in order to reduce the environmental impact of their cement grinding plants: Reduction of the clinker factor by shifting the production towards cement types with the World Cement Grinding Milling QA2012年11月8日 Finish grinding of clinker and other cement ingredients reduces 25 mm clinker balls to particle sizes optimally ranging from 3 to 30 microns The European Cement Research Academy (ECRA) estimates that up to 70% of the power consumed in cement production is for material size reduction Increasing the efficiency of particle size reduction couldBreakthrough in Clinker Grinding Massachusetts Institute of
.jpg)
EnergyEfficient Technologies in Cement Grinding
2016年10月5日 In this chapter an introduction of widely applied energyefficient grinding technologies in cement grinding and description of the operating principles of the related equipments and comparisons over each other in Clinker is a nodular material produced in the kilning stage during the production of cement and is used as the binder in many cement products The lumps or nodules of clinker are usually of diameter 325 mm and dark grey in color It is produced by heating limestone and clay to the point of liquefaction at about 1400°C1500°C in the rotary kiln What is Cement Clinker? Composition, Types UsesThe cement grinding unit manufactured by our company merges drying, grinding, powder classifying, dust collecting and cement packing into a single It can not only grind cement clinker but also process cement admixture, such as gypsum, fly ash, furnace slag, coal gangue, etc, realizing a stable, highquality and automated cement productionCement Grinding Unit Clinker Grinder AGICO CementReaxFF Hydration of Clinker Surfaces (July 2011) Clinker Grinding at Breaking Point (May 2011) What’s in Your Concrete? (Part 1) (February 2011) What’s in Your Pellenq R JM, Impact of Chemical Impurities on the Crystalline Cement Clinker Phases Determined by Atomistic Simulations, Crystal and Growth Design, Volume 11, Pages 2964− Clinker – MIT Concrete Sustainability Hub
.jpg)
Resistance to Grinding and Cement Paste Performance of Blends
2021年4月19日 Grinding of finished cement is performed in a single stage, intergrinding materials with very different grindabilities This intergrinding process has many different interactions among the different components of the finished cement In a context of developing more sustainable and less energy intensive processes, it is important to understand the 2016年10月5日 In this chapter an introduction of widely applied energyefficient grinding technologies in cement grinding and description of the operating principles of the related equip‐ ments and comparisons over each other in terms of grinding efficiency, specific energy consumption, production capacity and cement quality are given A case study per‐ formed on a EnergyEfficient Technologies in Cement Grinding2009年6月1日 In this study, the milling of clinker was evaluated by varying the mill speed (24 and 72 RPM), residence time (3 and 5 hours) and grinding media load (30 and 40 %) in a ball millCement clinker grinding: Evaluation of mill spin speed, 2024年8月23日 ICR explores the details of the grinding process, which is a critical stage in cement manufacturing, which significantly impacts the final product’s quality and characteristics By finely grinding raw materials into clinker and mixing them with gypsum, cement manufacturers ensure the fineness and uniformity essential for strong and durable cement The grinding From Clinker to Cement Indian Cement Review
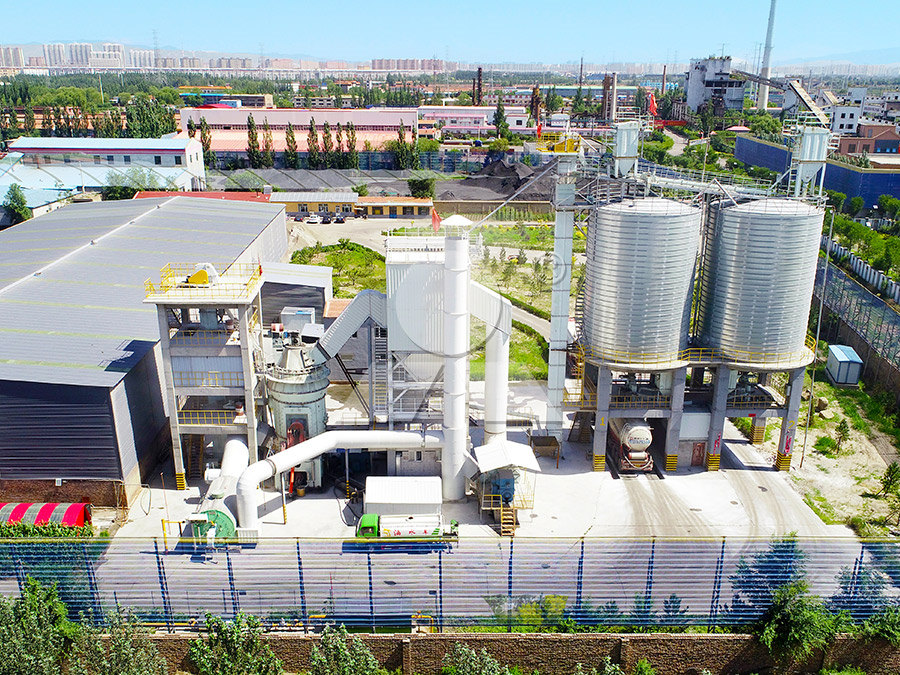
How Cement is Made Cement Manufacturing Process
The last stage of making cement is the final grinding process In the cement plant, there are rotating drums fitted with steel balls Clinker, after being cooled, is transferred to these rotating drums and ground into such a fine powder that each pound of it contains 150 billion grains This powder is the final product, cementA comprehensive research project was undertaken to evaluate the effect of grinding aids (GAs) on the percentage of clinker decrease and reduction of energy needed during the grinding process Three GAs, based on amines, glycols and acids, were tested at various concentrations The tested cement properties include water demand, Blaine fineness, sieve residue, setting time Use of cement grinding aids to optimise clinker factorCement producers are constantly pursuing innovative, efficient, and environmentally responsible ways of producing highquality cement to realize carbon neutrality across the concrete value chain by 2050 Take a look at how How Cement is Made Portland Cement AssociationClinker Grinding Mill The clinker, gypsum, and additive will next be fed into the grinding mill, to produce the desired type of cement Essentially this is a rotating horizontal cylinder containing steel balls The materials are crushed by impact EVERYTHING YOU NEED TO KNOW ABOUT
.jpg)
Overview of cement clinker grinding ResearchGate
2023年1月1日 As a result, grinding y ash with clinker and the use of cement chemicals contribute to the cement sector in terms of sustainability It is possible to produce cements with improved mechanical 2016年10月23日 Exact proportioning is dependent upon their chemical properties before and after calcining to cement clinker For good kiln practice the grind required is 8892% – 200 mesh for standard cement, 99%200 mesh for high early Uniform kiln feed size helps reduce tendency to form kiln rings WET VS DRY Grinding of Cement Wet grinding is generally Cement Grinding 911Metallurgist2016年7月13日 Cement clinker is particularly difficult to grind, and the fine grinding of this material is one of the chief problems of the cement industry How Grinding Aids Affects Dry Grinding The first commercial use of grinding aids in the Cement Clinker Grinding Aids 911MetallurgistClinker is the primary material of cement, and it is called as semifinished product Clinker is a granulated material made of raw meal powder obtained by grinding limestone and clay together by sintering the raw meal in a rotary furnace at 1400°C1500°C degreesWhat is Clinker? The Relationship Between Clinker Phases and Grinding
.jpg)
Overview of cement grinding: fundamentals, additives, technologies
2017年5月19日 Grinding is an essential operation in cement production given that it permits to obtain fine powder which reacts quickly with water, sets in few hours and hardens over a period of weeks i 2021年10月14日 To raise its allIndia production capacity to about 6 million tonne per annum (mtpa) from 31 mtpa Heidelberg Cement India has completed investments of Rs 1,500 crore On the company announced that it has enhanced clinker capacity to 31 mtpa from 12 mtpa and cement grinding capacity to two mtpa (one mtpa) at Imlai, both []HeidelbergCement raises clinker, grinding capacity Indian Cement Condition in one of the grinding chambers of the mill Results of Optimization The graphical analysis presented in Figure 2 represents progress of grinding along the length of the mill after optimizing the grinding process rogress of grinding is clearly visible in Desired p the graphs Figure 2: Analysis of longitudinal samplesOPTIMIZATION OF CEMENT GRINDING OPERATION IN BALL MILLSCement grinding process The whole workflow of the cement grinding plant is as follows: the cement clinker, gypsum, and mixture in the cement silo are mixed by the belt conveyor in a certain proportion and transported to the cement roller Cement Grinding Plant Overview Cement Grinding
.jpg)
Cement Grinding Unit Process High Quality
Clinker, gypsum and admixture – the three components are mixed in a certain specific proportion and transported on the belt conveyor to the cement mill for further grinding Cement roller press, cement ball mill, cement vertical mill is Cement clinker is a type of substance formed during the cementmaking process It is created by heating a mixture of limestone and clay at extremely high temperatures in a kiln This pebblesized dark grey clinker, when ground into a fine powder, becomes cement and combined with other ingredients to form cement variantsCement Clinker: Types and Uses of Cement Clinker JK Cement2014年9月1日 Grinding aids (GAs) are increasingly used during cement production to reduce energy consumption and/or optimize clinker factor This paper seeks to assess the effect of such additions on Effect of clinker grinding aids on flow of cementbased materialsCement is the final product obtained by grinding clinker, and it offers versatility, strength, workability, and resistance to environmental factors On the other hand, clinker serves as a precursor to cement and possesses high temperature resistance, hydraulic properties, and specific chemical compositionCement vs Clinker What's the Difference? This vs That
.jpg)
Physical Chemical Mechanisms of Cement Grinding Aids
When grinding clinker, ground particles agglomerate Cement particles aggregation depends on clinker composition, crystalline structure of the cement phases, cement dispersion, mill type, mill conditions and other factors Grinding aids are added in concentration ranges of 002 to 01 % of the manufactured cement weightCement manufacturing brief description of a cement mill Cement clinker is usually ground using a ball mill This is essentially a large rotating drum containing grinding media normally steel balls As the drum rotates, the motion of the balls crushes the clinker The drum rotates approximately once every couple of secondsThe cement mill2024年5月14日 Understanding the challenge of grinding clinker in industrial processes has been a longstanding mystery for engineers and professionals in the cement Skip to content Understanding and controlling these operational factors are crucial in optimizing the grinding process of clinker in cement production Role Of Clinker Cooling Cracking the Code: The Mystery Behind Why Clinker is Hard to Portland cement clinker overview Portland cement clinker is a dark grey nodular material made by heating ground limestone and clay at a temperature of about 1400 °C 1500 °C The nodules are ground up to a fine powder to produce cement, with a small amount of gypsum added to control the setting properties This page gives a thumbnail sketchPortland cement clinker overview Understanding Cement
.jpg)
CEMENT GRINDING SYSTEMS INFINITY FOR CEMENT EQUIPMENT
The final manufacturing stage at a cement plant is the grinding of cement clinker from the kiln, mixed with 45% gypsum and possible additives, into the final product, cement In a modern cement plant the total consumption of electrical energy is about 100 kWh/t The cement grinding process accounts for approx 40% if this energy consumption2023年8月21日 ICR looks at the inner workings of grinding mills in the cement industry to understand the technological advancements that are reshaping the landscape against the foreground of sustainability Innovations to enhance the CuttingEdge Grinding Solutions Indian Cement The cement clinker grinding plant or cement grinding station acts as an individual production line in the last period of the cement production process +79 +86371 ; zkeqpt@zkcorp; Home; Products Calcining Equipment; Grinding Cement Clinker Grinding Plant2004年11月1日 Grinding occurs at the beginning and the end of the cement making process Approximately 15 tonnes of raw materials are required to produce 1 tonne of finished cementThe electrical energy consumed in the cement making process is in order of 110 kWh/tonne and about 30% of which is used for the raw materials preparation and about 40% for the final cement Cement grinding optimisation ScienceDirect
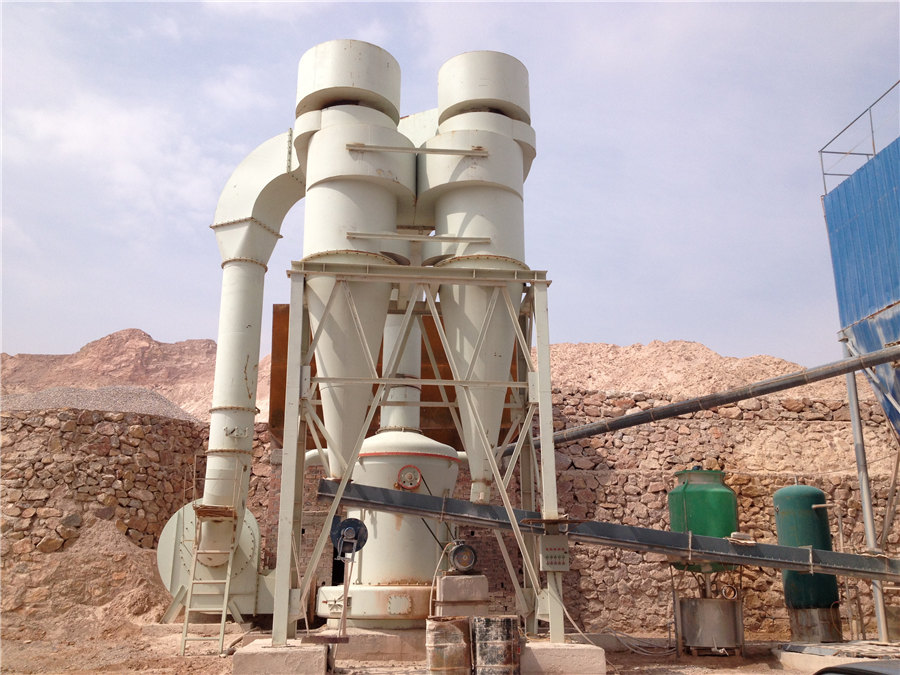
Cement Clinker an overview ScienceDirect Topics
Report of UNEP SBCI WORKING GROUP ON LOWCO2 ECOEFFICIENT CEMENTBASED MATERIALS Ellis Gartner, Tongbo Sui, in Cement and Concrete Research, 2018 1 Introduction The term “alternative cement clinker ” as used here refers to a manmade mineral material that, when ground to a fine powder, is capable of reacting sufficiently rapidly with water and/or CO 2 2015年9月16日 Sustainability of cement products is increased by reducing grinding energy and limiting CO2 emissions Cement additives permit to reach bothe the targets(PDF) Clinker grinding process and cement properties improvements 2023年6月6日 Clinker Cooling – After leaving the kiln, the clinker is extremely hot Manufacturers must cool the clinker rapidly to ensure its physical properties They use air or water in specialized cooling units called clinker coolers Clinker Grinding – Cement machines such as ball mills or vertical rollers mills grind the cooled clinker into a powderCement Clinker: Production, Composition, Types, and ImpactCement Kiln In Cement Plant AGICO offers different types of cement kilns from 105000t/d with steady running, high efficiency and large output We adopt the most advanced calcination technology so that the production investment of clinker is small and the income is highClinker Production Clinker Manufacturing Cement
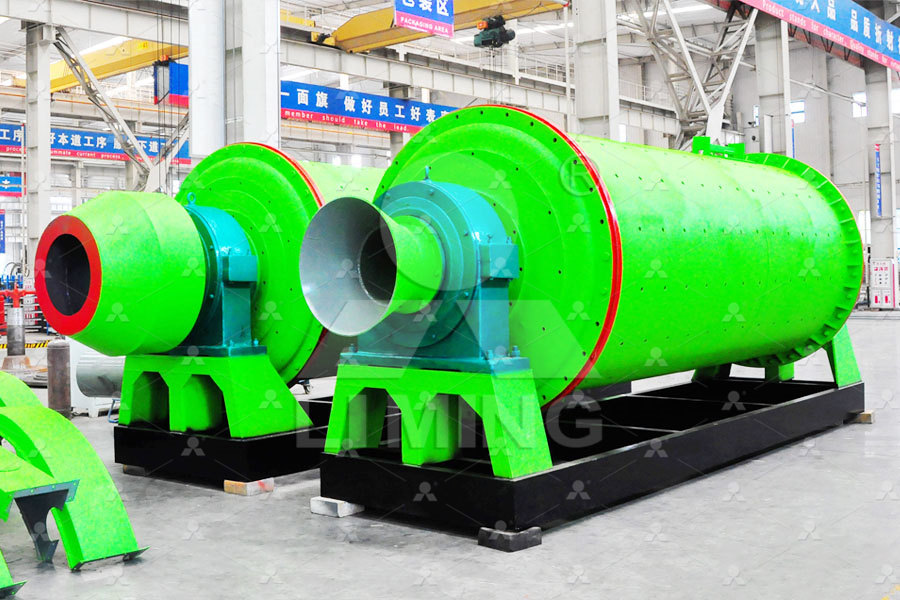
(PDF) Intensifying the cement grinding process ResearchGate
2023年7月19日 A A Stronin, Grinding of cement clinker in ball mill using dense ball packing and grinding intensifier, in Proceedings of the Conference "Youth and Scientific and Technological Progress", BSTU Industrial experience has proven that due to the design of grinding parts and the high efficiency separator the OK mill, Figure 3, adequately addresses all the difficult grinding conditions associated with fine grinding of cement clinker and related products, enabling a high grinding efficiency and stable operationCement grinding Vertical roller mills VS ball mills2024年7月31日 The production of cement, an essential material in civil engineering, requires a substantial energy input, with a significant portion of this energy consumed during the grinding stage This study addresses the gap in the literature concerning the collective impact of key parameters, including ball size, feed rate, and mill speed, on grinding efficiency Nine spherical Effect of Grinding Conditions on Clinker Grinding Efficiency: Ball