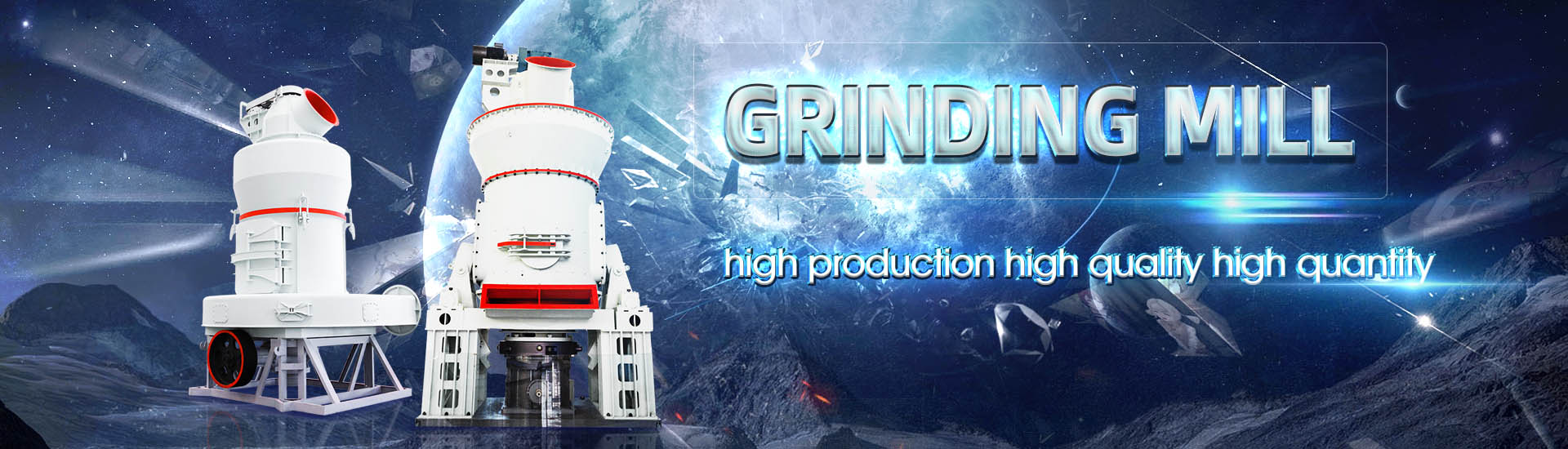
Excellent comprehensive performance of coal mill
.jpg)
An investigation of performance characteristics and
2020年8月12日 To understand the performance of a vertical roller coal mill, the real operational tests have been performed considering three different coal sources Obtained results indicate that2020年8月12日 This study shows the performance of a currently running vertical roller coal mill (VRM) in an existing coalfired power plant In a power plant, the coal mill is the critical An investigation of performance characteristics and energetic The effect of low calorific value coal was observed on mill’s response to match the boiler energy requirements Evaluation of the current operating pulveriser data enabled the determination of Performance optimisation of vertical spindle coal pulverisers2015年11月1日 Coal mills are bottleneck in coal–fired power generation process due to difficulty in developing efficient controls and faults occurring inside the mills In this paper, a dynamic A unified thermomechanical model for coal mill operation

A BranNew Performance Evaluation Model of Coal Mill Based on
2022年3月1日 The proposed KPCA–Bagging–GMR framework for soft sensors using reduced dimensions and ensemble learning has been validated as demonstrating superior predictive Coal quality, that is the properties of coal, has an impact on many parts of a power plant including the coal handling facilities, pulverising mills, boiler, air heater, ESP, ash disposal as well as Expert systems and coal quality in power generation USEAperformance starts in optimizing the inputs, starting at the pulverizer Working in coordination, Storm Technologies and SCEG undertook a project to improve combustion, reliability and Combustion, Reliability, and Heat Rate Improvements through Mill 2020年10月27日 In this paper, various process modeling techniques, ie, MLR, ANN, and LSSVM, are utilized and comprehensively compared for the operational analysis of the generator power production from a 660 MW e supercritical coal Optimization of a 660 MWe Supercritical Power Plant
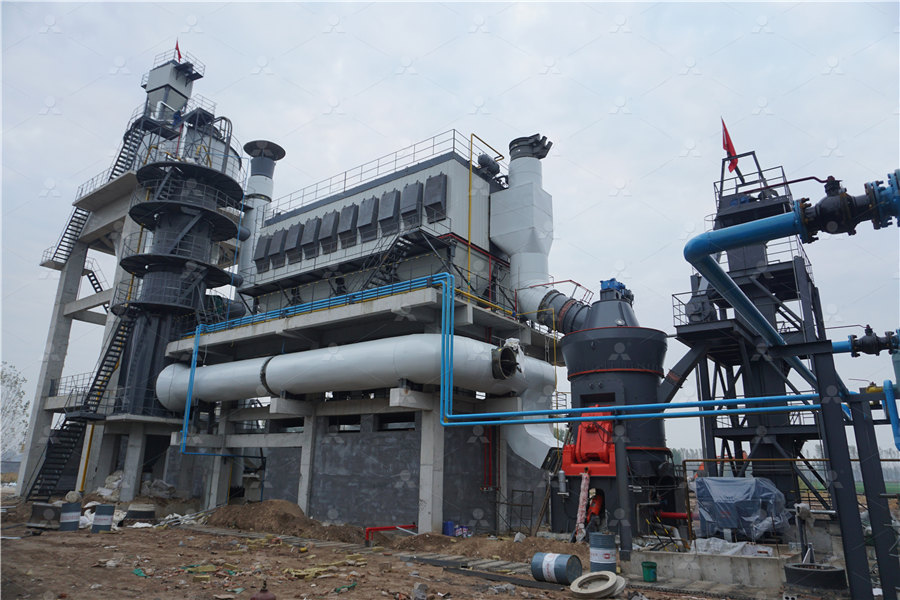
A brannew performance evaluation model of coal mill based on
2022年5月31日 In this paper, a brannew GAIFCMIDHGF assessment method is proposed Genetic algorithm (GA) is first applied to optimize initial parameters, which is fundamental and Download scientific diagram Technical specifications of vertical roller coal mill from publication: An investigation of performance characteristics and energetic efficiency of vertical roller Technical specifications of vertical roller coal millet al 2017) In a coalfired power plant, one of the main equipment is the coal mill, whose effectiveness influences mainly the whole power plant performance (Shah, Vuthaluru, andAn investigation of performance characteristics and energetic Download scientific diagram The layout of the coal mill with a rotary classifier from publication: An investigation of performance characteristics and energetic efficiency of vertical roller The layout of the coal mill with a rotary classifier
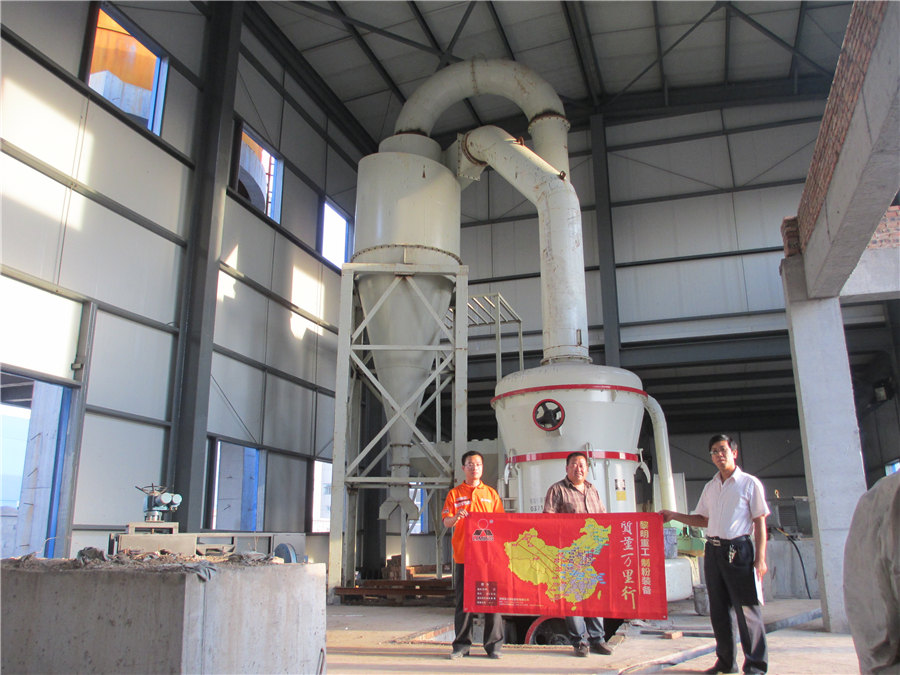
CFD Modeling of MPS Coal Mill for Improved Performance and Safety
2009年1月1日 Air flow distribution at the mill throat, as well as inside the mill, significantly influences the mill performance in terms of separation, drying, coal/air flow uniformity at the mill outlet (HGI), at a given raw coal sizing entering the mill and at a given coal moisture content Throughput alone is NOT a definition of pulverizer capacity! Please read on Comprehensive Performance Optimization Performance optimization includes a thorough process of evaluating the existing performance, Pulverizer Capacity is not simply “tons throughput per hour!”According to the running characteristics of vertical coal mill, KINGCERA has designed different wearresistant lining plates for coal mill barrel and coal mill shell The coal mill liner can be installed onsite, or on the curved steel plate in the factory and then welded to the mill barrelMediumspeed coal mill wearresistant ceramic liner Composite 2023年5月17日 Disadvantages of Coal Hammer Mill Wear and Maintenance: In a coal hammer mill, the hammers or blades can deteriorate significantly with time, particularly when grinding abrasive materials To guarantee optimal operation and prevent performance degradation, we require routine maintenance, including hammer replacement and inspectionWhat Is Coal Hammer Mill? SBM Mill Crusher
.jpg)
Modeling and Parameter Identification of Coal Mill
2009年9月20日 A control oriented model was then developed by Fan (1994) and Fan and Rees (1994) In 2009, coal flow and outlet temperature of mill were modelled using mass and heat balance equations for startup PDF On Jan 1, 2021, 增澳 董 published Research Progress on Comprehensive Utilization and Resourceful Treatment of Coal Gangue Find, read and cite all the research you need on ResearchGateResearch Progress on Comprehensive Utilization and Resourceful 2014年10月1日 Request PDF Numerical and experimental analysis of pulverized coal mill classifier performance in the Soma B Power Plant Coal particle separation in a classifier after the pulverization Numerical and experimental analysis of pulverized coal mill 2020年4月14日 22 Experiment The chemical composition measured by Bruker S8 TIGER XRF analysis; the mineralogical composition measured via Bruker D8 ADVANCE XRD analysis; thermal analysis conducted with Mettler Toledo analyzer in a temperature range of 30–1000 °C at a heating rate of 10 °C/min and N 2 or O 2 atmosphere Mortar strength test: prismatic mortar Identification and Activation of Coal Gangue and Performance
.jpg)
Development overview of paste backfill technology in China’s coal
2021年10月12日 After years of development, paste backfill technology has become an important part of China’s green safety mine construction and coal green mining technology system in the new era In this paper, the research status of paste backfill technology in China’s coal mines is expounded from the aspects of paste backfill materials, strata control theory, and paste backfill Download scientific diagram Effect of mill outlet temperature on the coal volatile matter from publication: An investigation of performance characteristics and energetic efficiency of vertical Effect of mill outlet temperature on the coal volatile matter2014年3月1日 This study shows the performance of a currently running vertical roller coal mill (VRM) in an existing coalfired power plant In a power plant, the coal mill is the critical equipment, whose Breakage and separation mechanism of ZGM coal mill based 2020年5月15日 Coal ganguebased geopolymer (CGGP) is one of the hot spots existing in the recycling of coal gangue resources due to its good comprehensive mechanical properties(PDF) Experimental Study on the Characteristics of Activated Coal
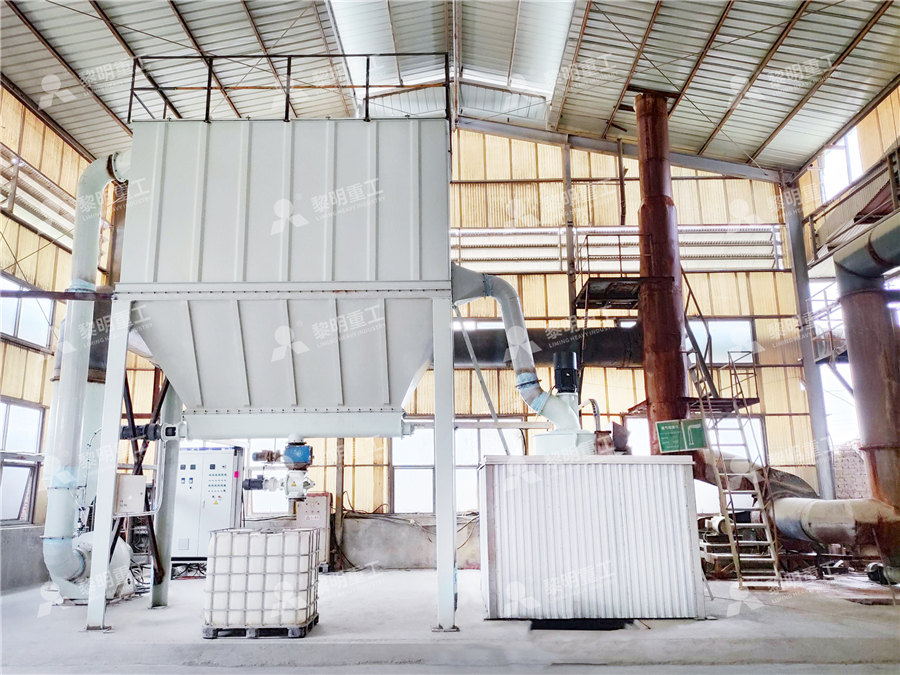
Effect of Coal Quality and Performance of Coal pulverisers / Mills
2021年3月31日 24 mill performance monitoring using non iso kinetic technique • dirty pitot testing to be carried out before and after mill overhaul • non iso kinetic sampling to be used for routine checking of fineness • pf fineness data to be trended mill wise • sample to be collected from each pipe in case of major degradation2019年10月1日 Request PDF Wet and dry grinding of coal in a laboratoryscale ball mill: Particlesize distributions In this study, experimental data for wet and dryground coal samples under wet and dry Wet and dry grinding of coal in a laboratoryscale ball mill: Particle A simple energy balance model of the coal mill is derived in (Odgaard and Mataji 2006), this model is based on a more detailed model found in (Rees and Fan 2003)In this model the coal mill is seen as one body with the mass m mThe following variables are defined: T(t) is the temperature in the coal dust flow in the mill, ṁ PA (t) is the primary air mass flow, T PA (t) is Coal Mill an overview ScienceDirect Topics2024年1月2日 This paper presents an investigation into the optimization of petroleum coke mill or petcoke mill processes, to improve efficiency and reduce waste in the heavy industry within the cement plant where our study is conducted Our mission was to create a robust algorithm that could properly anticipate the mill’s performance and improve its operations To accomplish Development of a kiln petcoke mill predictive model based on a
.jpg)
CoCombustion Characteristics of Typical Biomass and Coal
Finally, to achieve a comprehensive evaluation of ignition and combustion performance of coal and biomass blends, two combustion indices as a function of biomass blending ratio are shown in Figure 4 The trend of S and C increased first, then declined, and rose again when the percentage of biomass exceeded 80%, overall exhibiting an “N” curve shape2019年12月1日 The classification performance of model coal mill classifiers with different bottom incoming flow inlets was experimentally and numerically studiedClassification performance of model coal mill classifiers with 2021年11月4日 Technique to Investigate Pulverizing and Abrasive Performance of Coals in Mineral Processing Systems November 2021; Energies 14(21):7300; wear process in a ballonrace type of coal millTechnique to Investigate Pulverizing and Abrasive Performance of Coals 2023年9月15日 As the significant ancillary equipment of coalfired power plants, coal mills are the key to ensuring the steady operation of boilers In this study, a fault diagnosis model was proposed on the Fault Diagnosis of Coal Mills Based on a Dynamic Model
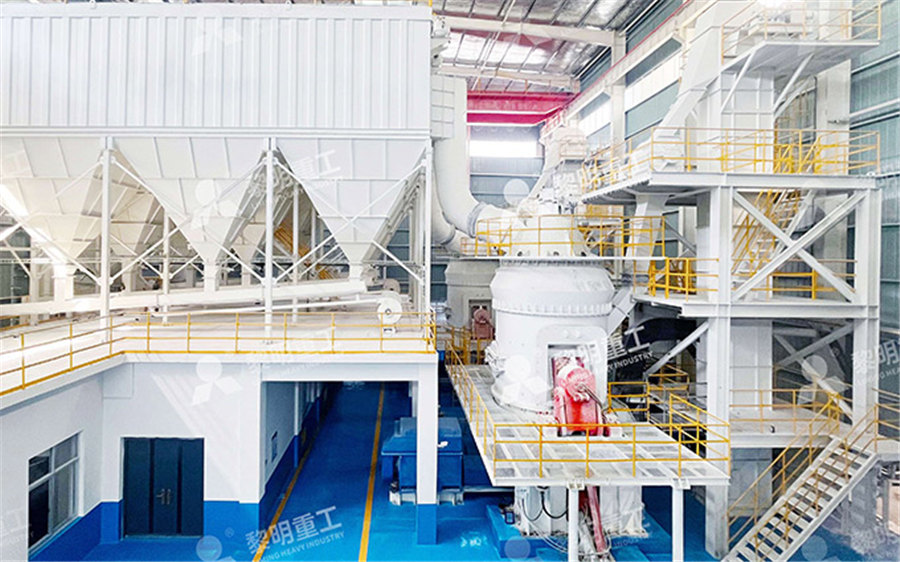
(PDF) Modeling and Control of Coal Mill Academia
Modeling and Control of Coal Mill The book comprises essays on four ways of working since the early 1990s: researchbased art, performance exhibitions, interventions, and invocations of modernist architecture and design The introduction offers a critique of the attention/distraction binary and proposes that today, Coal Mill: The heart of the system, where raw coal is pulverized into a fine powder Various types of mills, such as ball mills, vertical roller mills, and hammer mills, can be used depending on the specific requirements of the application Storage Bin/Silo: Pulverized coal is temporarily stored in a bin or silo before being fed into the furnaceIndirect Firing Coal Grinding Systems: Enhancing Efficiency and 2020年1月1日 Coal mills have a significant influence on the reliability, efficiency, and safe operation of a coalfired power plant Coal blockage is one of the main reasons for coal mill malfunctionEarly Warning of Critical Blockage in Coal Mills Based on Operators can adjust grinding variables, such as coal flow and mill rotation speed, in realtime to achieve the desired coal fineness and optimize mill performance Copper Ball Mill: A Comprehensive Guide; Coal Mill Pulverizer in Thermal Power Plants; Contact Info Phone: +86 +86 : Mill in Thermal Power Plant: Enhancing Efficiency and
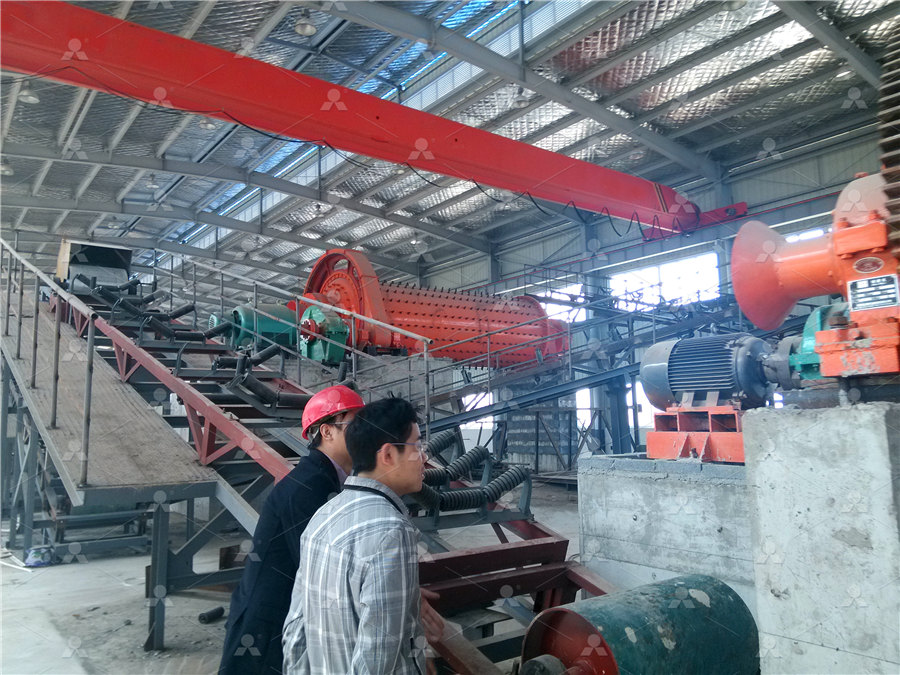
A brannew performance evaluation model of coal mill
2022年3月1日 Download Citation A brannew performance evaluation model of coal mill based on GAIFCMIDHGF method Adopting a more scientific and precise assessment method to evaluate the current running 2014年1月1日 The emission factors of kiln end, kiln head, coal mill, crushing and cement mill was 0156 clinker g/t, 3914 clinker g/t, 1538 coal g/t, 0016 stone g/t and 0056 cement g/t respectively, the (PDF) MPS mills for coal grinding ResearchGate2024年4月8日 The comprehensive performance evaluation index system of ultrasupercritical coal fired units is constructed by examining the boiler performance, turbine performance, plant power performance Dynamic Comprehensive Evaluation of a 660 MW UltraSupercritical Coal 2019年5月8日 7 Maintenance Strategy Maintenance Significant Item Inspection / Execution Task Coal Measure HGI (hard grove index), moisture content, abrasiveness and size of coal fed to mill Pulverised fuel (PF) Measure particle TPS Coal Mills and Fan Performance PPT SlideShare
.jpg)
Utilization of Rejected Coal Through Blending Techniques in
2023年12月16日 Effect on Mill Performance Due to Rejected Coal The presence of rejected coal in a thermal power plant's coal mill significantly impacts its performance Rejected coal, consisting of noncombustible impurities, harms the mill in several ways: Reduced Efficiency: Impurities in rejected coal damage grinding elements, lowering grinding efficiency2023年11月30日 Coal fly ash (CFA) is an increasingly prevalent byproduct that necessitates more resourceful and ecofriendly processing methods Extracting aluminum from CFA is a crucial aspect of promoting sustainable development in the alumina industry In this paper, a technique for comprehensive extraction of silica and alumina from circulating fluidized bedbased CFA is Comprehensive Extraction of Silica and Alumina from Coal Fly 2017年11月1日 As the present study is focused on coalfired power plants, the performance of these kinds of power plants based on the energy and exergy viewpoints are sought in more detail here (Ali et al The optimum performance of the combined cycle power plant: A 2022年2月24日 Curves of mill productivity, power consumed, specific surface of coal dust in terms of the relative rotational speed of the ball drum mill Composition of the balls loading the mill with a standard Improving the efficiency of the coal grinding process in ball drum
.jpg)
MultiObjective Optimization of Coal Mill Outlet Temperature
Multiobjective Optimization of Coal Mill Outlet Temperature Control Using MPC Zengji Zhang1, Yicheng Zhang2, Wei Shen2, BOE Xukang Lyu3,∗ 1Sinoma International Engineering Co, Ltd, Nanjing, Jiangsu, China 2College of Computer Science and Technology, Zhejiang SciTech University, Hangzhou, Zhejiang, China 3Zhejiang New Rise Digital Technology Co, Ltd, CFD Modeling of MPS Coal Mill for Improved Performance and Safety Kamalesh S Bhambare, Dr Zhanhua Ma, and Dr Pisi Lu RMT Inc, 744 Heartland Trail, Madison, WI 53717 AbstractCFD Modeling of MPS Coal Mill for Improved Performance and 2019年5月10日 17 Classifiers • The flow of coal particles through a classifier is several times the amount of coal flowing to the burners because of the large amount of coal recirculated within a pulverizer For example, if a pulverizer is operating at 100,000 lb/hr coal feed to the burners, as much as 300,000 lb/hr or more may be flowing through the classifier for regrindingMonitoring Coal mill Performance PPT SlideShareKey words: Coal mill classifier, Cut size, Nonswirling inlet, Particle image velocimetry, Impeller rotational speed 摘要: The classification performance of model coal mill classifiers with different bottom incoming flow inlets was experimentally and numerically studiedThe flow field adjacent to two neighboring impeller blades was measured using the particle image velocimetry techniqueClassification performance of model coal mill classifiers with
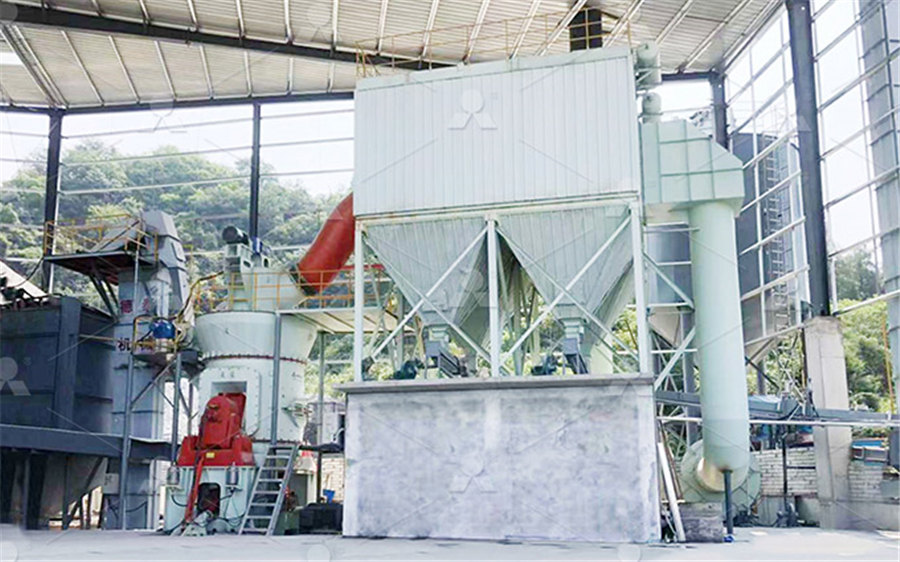
Analysis of the Coal Milling Operations to the Boiler Parameters
2020年4月2日 Wen, (2010) concludes that the mill performance in term of coal end product is th e major factor can cause th e Coal mill motor power (kW) 0 4171 4548 4390 4586 4562