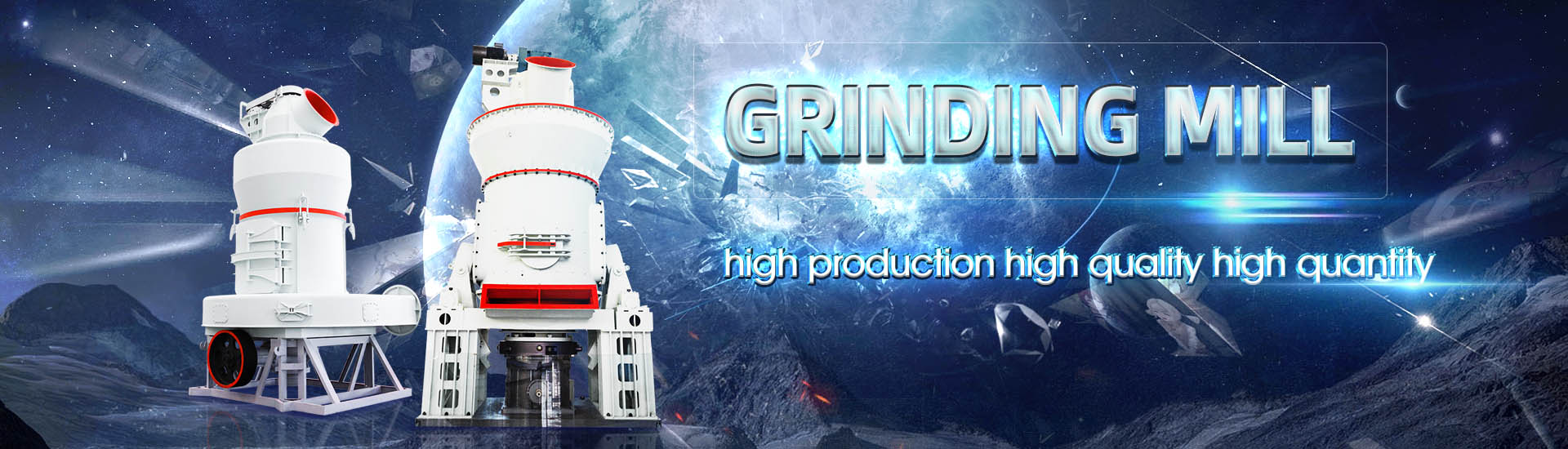
Ratio of steel balls for BBD4060 ball mill
.jpg)
STEEL MILLING BALLS FOR BALL MILLS Energosteel Grinding
GRINDING STEEL BALLS FOR BALL MILLS Specifications Date of validity: 2016 07 – 01 1 FIELD OF APPLICATION This standard applies to steel grinding balls produced by rolling, forging, stamping and used for raw materials and materials grinding in ball mills 2 2013年8月3日 In Grinding, selecting (calculate) the correct or optimum ball size that allows for the best and optimum/ideal or target grind size to be achieved by your ball mill is an important thing for a Mineral Processing Engineer AKA Calculate and Select Ball Mill Ball Size for Optimum The success of a ball milling application depends on the correct selection of accessories and process parameters This includes jar sizes, jar materials, ball sizes, number of balls, particle Three rules for the optimum ball mill setup RETSCH2024年2月19日 The ratio of steel balls in the ball mill depends on the effective length of your mill, whether it has a roller press, the size of the feed particles, the lining and structure used, the expected sieve residue fineness and ratio, how Ball Mill Steel Balls: Quality And Gradation JXSC Mineral
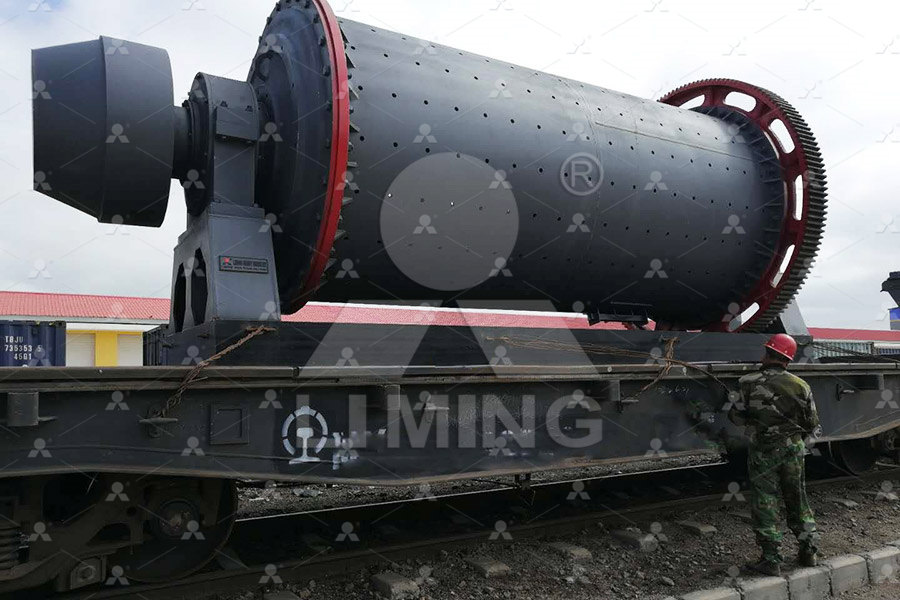
Ball Mill Grinding Process Handbook
This document provides guidance on ball mill grinding processes It covers topics such as ball mill design including length to diameter ratios, percent loading, critical speed, and internals evaluation Methods for assessing ball charge, 2023年4月23日 One of the most used tumbling mills is the ball mill This paper reviews different types of grinding media that have been developed and improved over the years and their properties Also(PDF) Grinding Media in Ball MillsA Review2021年1月22日 Herein, an innovative approach for determining the grinding media system of ball mill based on grinding kinetics and linear superposition principle was proposed The An innovative approach for determining the grinding media 2012年6月1日 Ball mills can grind a wide range of materials, including metals, ceramics, and polymers, and can operate on a variety of scales, from laboratory to industrial (Monov et al Grinding in Ball Mills: Modeling and Process Control ResearchGate
.jpg)
Grinding in Ball Mills: Modeling and Process Control Sciendo
The size of a mill is usually characterized by the ratio “length to diameter” and this ratio most frequently varies from 05 to 35 The starting material can be loaded either through a spout 2020年7月2日 In recent research done by AmanNejad and Barani [93] using DEM to investigate the effect of ball size distribution on ball milling, charging the mill speed with 40% small balls and 60% big balls (PDF) Effects of Ball Size Distribution and Mill Speed and Their GRINDING STEEL BALLS FOR BALL MILLS Specifications Date of validity: 2016 07 – 01 1 FIELD OF APPLICATION This standard applies to steel grinding balls produced by rolling, forging, stamping and used for raw materials and materials grinding STEEL MILLING BALLS FOR BALL MILLS Energosteel Grinding Media Ball Ball mill steel balls is an important part of the ball mill, its main function is to carry out the grinding operation in the ball mill, and the material is crushed into the required size Ball mill balls usually have the advantages of high hardness, Ball Mill Balls Manufacturing Of High Quality Ball
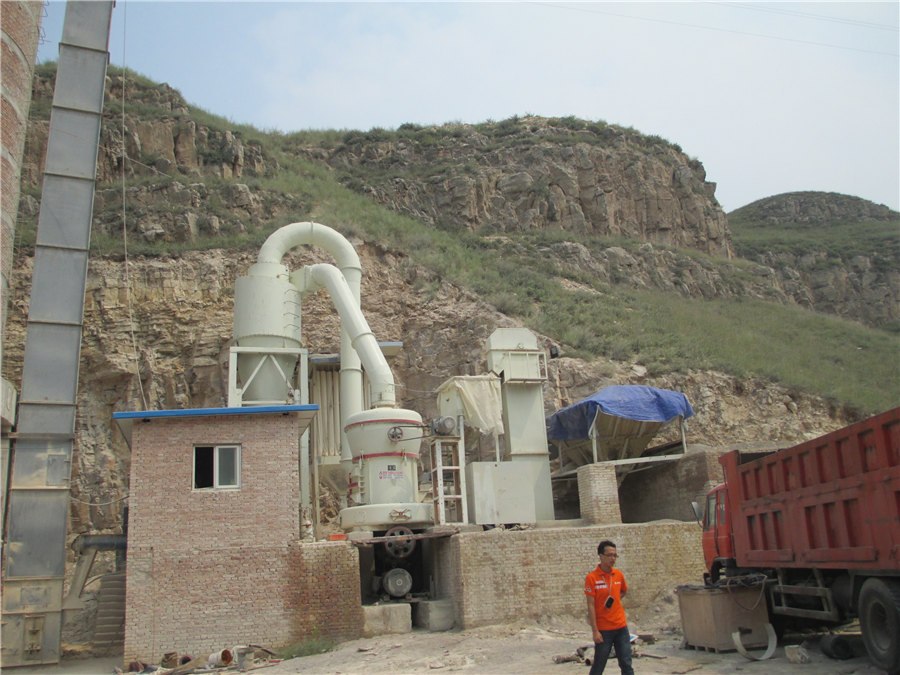
How to choose the ball loading and loading ratio of ball mill?
When the ball mill is used for pulverizing material, the ball milling ratio of the following steel balls is the highest: In production, the twostage ratio and the multistage ratio are more common Generally, the multistage ratio follows the principle of “less at both ends and more in the middle”2023年2月15日 High temperature of the ball mill will affact the efficiency 3 For every 1% increase in moisture, the output of the ball mill will be reduced by 8% 10% 4 when the moisture is greater than 5%, the ball mill will be unable to perform the grinding operation 5 The bearing of the ball mill is overheated and the motor is overloaded Reasons17 Signs of Problems with Ball Mills: Quickly Remove Hidden Troubles2018年11月1日 It increases the milling efficiency of ball milling Tungsten powder and grinding balls were weighed by the precision balance (with the accuracy of 00001 g) respectively to make samples with the BPR (the ratio of milling balls mass to powder mass) of 4:1, 10:1 and 15:1The ball to powder ratio (BPR) dependent morphology and microstructure 2023年10月27日 The ball mill is a rotating cylindrical vessel with grinding media inside, which is responsible for breaking the ore particles Grinding media play an important role in the comminution of mineral ores in these mills This work reviews the application of balls in mineral processing as a function of the materials used to manufacture them and the mass loss, as A Review of the Grinding Media in Ball Mills for Mineral
.jpg)
Grinding in Ball Mills: Modeling and Process Control
2012年6月1日 Steel and other metal balls are the most frequently used grinding media with sizes of the balls ranging from 10 to 150 mm in diameter [30] Cylpebs are slightly2021年6月29日 The rotating mill is filled with different steel balls of sizes 25 mm Taking a Φ549 × 883 m ball mill as the filling ratio of 32%; material ball ratio of 10; rotation Effects of Mill Speed and Air Classifier Speed on Performance of 414 Also the balls of the 2nd, 3rd, and 4th groups can be manufactured from low alloy steel and instrument steel in accordance with GOST 5950 415 The balls of the 5th group are manufactured of steel, the carbon equivalent of which shall be no less than: 075% for balls with rated diameter of 1560 mm provided that carbon weight STEEL MILLING BALLS FOR BALL MILLS Specifications2017年4月29日 Miami Copper Co’s plant after the mill had been operating for a year with a ball load of 14,800 lb (6713 kg) which was maintained by the addition of 400 lb (181 kg) of 2in (508mm) steel balls dailyGrinding Media Wear Rate Calculation in Ball Mill

Comparative Study on Improving the Ball Mill Process Parameters
2021年2月19日 The ball mill process parameters discussed in this study are ball to powder weight ratio, ball mill working capacity and ball mill speed As Taguchi array, also known as orthogonal array design, adds a new dimension to conventional experimental design, therefore, Orthogonal array (L9) was carefully chosen for experimental design to understand the effects Steel balls Steel balls are one of the most widely used grinding media in cement ball mills, their diameters can range from 20mm to 150mm according to different grinding requirements In a cement ball mill, generally, φ50100mm steel balls Ball Mill Grinding Media Steel Balls for Ball MillsCompany News; Product News; How to add steel balls to the ball mill, and how to configure the steel balls?(2) Ball mill steel ball adding skills The ball mill steel ball ratio should be based on the effective length of your mill, whether it is equipped with a roller press, the size of the feed, what liner and structure to use, the expected sieve fineness and ratio, how many chromium balls to How to add steel balls to the ball mill, and how to configure the steel 2017年2月13日 If finer grinding is wanted two or three stage grinding is advisable as for instant primary rod mill with 75—100 mm (3″—4″) rods, secondary ball mill with 25—40 mm(1″—1½”) balls and possibly tertiary ball mill with 20 mm (¾”) balls or cylpebsBall Mills 911Metallurgist
.jpg)
Guidance of Ball Mill Steel Balls Miningpedia
Steel balls of different sizes in the bin have different proportionsFor example, when the ball mill is used for the first time, three kinds of ball proportions of large, medium and small are required for proportioning, and when adding ball mill steel balls for the first time, the steel balls should be added according to 80% of the maximum ball capacity given by the manufacturer2024年2月28日 1 Mill Volume Analysis The volume of your ball mill sets the stage for efficient milling Calculate it by multiplying the total mill volume, accounting for void spaces, by the fraction filled by the balls Typically, aim for a filling fraction between 30% and 50% 2 Ball Mass Computation The mass of the balls is a critical parameterBall Mill Efficiency Guide: Calculating Optimal Number Of Balls The ball mill is a cylindrical drum (or cylindrical conical) turning around its horizontal axis It is partially filled with grinding bodies: cast iron or steel balls, or even flint (silica) or porcelain bearings Spaces between balls or bearings are occupied by the load to be milledBall Mill an overview ScienceDirect Topics2024年8月15日 a, Illustration of a mill and the relevant parameters that contribute to the effective impact velocity v effective in Equation 4 Angular velocity of planetary disk, ω p; angular velocity of jar, ω j; transmission ratio i=1+(r p /r j) 1/2 b, Impact energy map relative to the planetary ball mill geometry with variable radii for r p and r jNavigating Ball Mill Specifications for TheorytoPractice
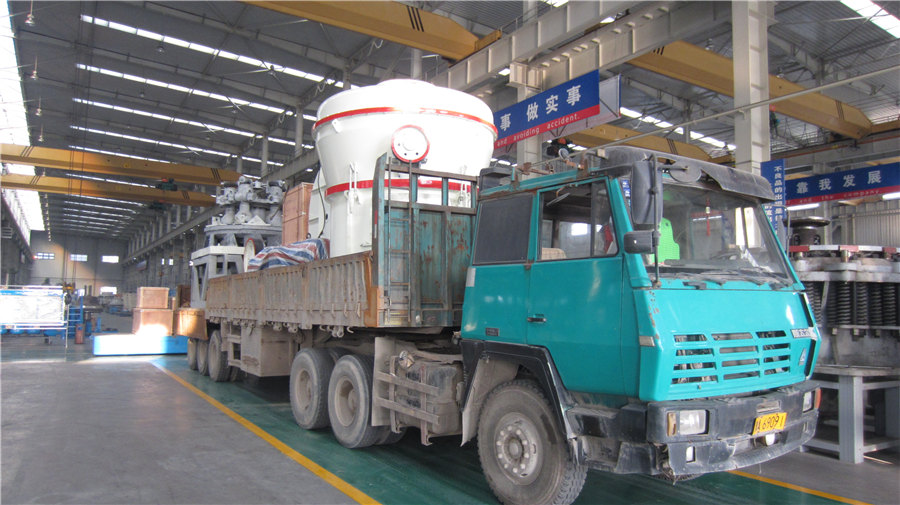
PLANETARY BALL MILL Laarmann
• Speed ratio (speed sun wheel : grinding jar) Laarmann Group BV Op het Schoor 6 6041 AV The Netherlands info@laarmann laarmann webshoplaarmann +31 6 23 40 00 33 LM PBM PLANETARY BALL MILL Counter weight with 1 jar can be expanded for 14 positions PBM Planetary ball mill closed 1 Movement planetary mill2023年4月28日 The ratio of balls to powder affects both how the milling works and how good the powder is that comes out of it By changing the ratio of balls to powder, you can find the best ratio to get the particle size and distribution The milling process and the size distribution of the particles can be affected by how fast the ball mill turnsParametric study on four station ball mill for synthesis of ultrafine 2019年12月4日 steel balls Ceramic balls As the name implies, this grinding media are made of ceramic which is energysaving and environmentally friendly The ceramic ball has a Mohs hardness of 90, which is second only to 3 Types of Grinding Media for Ball Mills FTM 2017年1月1日 An increase of over 10% in mill throughput was achieved by removing the ball scats from a single stage SAG mill These scats are non spherical ball fragments resulting from uneven wear of balls (PDF) Performance optimization of an industrial ball
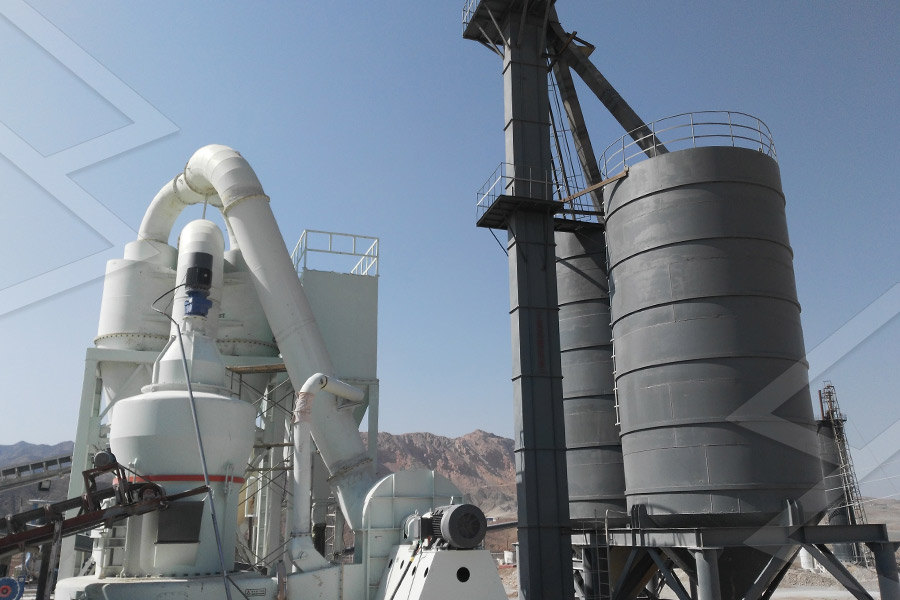
Friction and wear characteristics and simulation study of NM500
2024年9月12日 Friction and wear test equipment, scanning electron microscope, abrasion balls made of CGr15 high carbon chromium bearing steel, and liners made of NM500 steel were used for wear simulation and friction–wear experiments The variation trends of friction coefficient, wear amount, and subsurface characteristics under dry friction and slurry conditions were studied 2014年4月28日 Energies of the balls at different milling intensities and ball to powder weight ratios for Ti 50 Ni 50 (3 balls) Planetary Ball Mill Process in Aspect of Milling Energy2023年4月23日 of cement clinkers was higher with cylpebs grinding media than with steel balls in a ball mill Table 2 Adapted from [51] Ball filling ratio also affects the grinding rate(PDF) Grinding Media in Ball MillsA Review ResearchGate2022年11月9日 Therefore, under normal circumstances, there is no need to add a small ball The steel balls in the ball mill are constantly worn out during the operation To maintain a reasonable ratio of the ball charge filling rate and the balls, The Role of Ball Mill Steel Balls JXSC Mineral
.jpg)
Ball Mill an overview ScienceDirect Topics
Ball mills tumble iron or steel balls with the ore The balls are initially 5–10 cm diameter but gradually wear away as grinding of the ore proceeds The feed to ball mills (dry basis) is typically 75 vol% ore and 25% steel The ball mill is operated in closed circuit with a particlesize measurement device and sizecontrol cyclones2024年8月8日 In a ball mill of diameter 2000 mm, 100 mm dia steel balls are being used for grinding Presently, for the material being ground, the mill is run at 15 rpm At what speed will the mill have to be run if the 100 mm balls are replaced by 50 mm balls, all the other conditions remaining the same?FCMO: Ball Mill Operating Speed MSubbu Academy2021年11月1日 However, the measurement results are easily affected by the wear of steel balls,other grinding media and liners The filling ratio, ratio of particle to ball and mineral weight were varied to control the mill load The initial ratio of grading ball was 30 mm: 40 mm: 50 mm: 70 mm = 30: 20: 30: 20Assessing load in ball mill using instrumented grinding mediaEach FOX Forged Steel grinding ball is solid from surface to center These sturdy, well built, shockabsorbing steel balls are the perfect hardness for ball mill grinding Whether you are grinding raw materials in ball mills, or using Forged Steel Ball FOX Forged Steel Grinding Ball
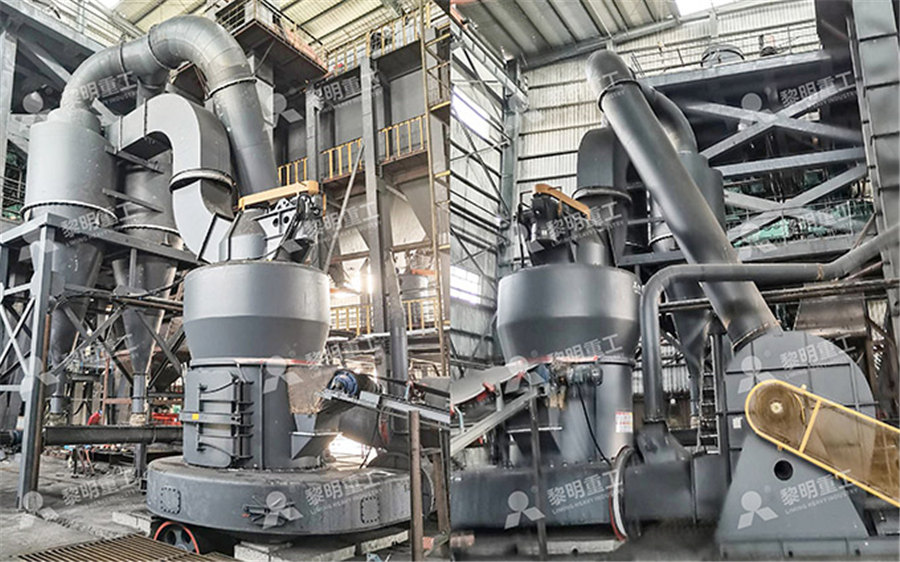
Operation Analysis of a SAG Mill under Different
2020年10月9日 The mill speed, fill level ratio, and steel ball ratio can significantly affect mill operation, F Modeling on the E ff ect of Coal Loads on Kinetic Energy of Balls for Ball Mills Energies 2016年1月1日 The wear of balls used during a grinding process is considered one of the losses that cause an increase in the operating cost allocated to the ball mill [21]A comparison of wear rates of ball mill grinding I want to ball mill 60 gm of Al powder in steel jar with 10mm diameter ball size How can I determine the best RPM and balls to powder ratio for wet Ball Milling? Question 4 answersHow to calculate ball to powder ratio? ResearchGate2015年4月24日 2 Ball mill consist of a hollow cylindrical shell rotating about its axis Axis of the shell horizontal or at small angle to the horizontal It is partially filled with balls made up of Steel,Stainless steel or rubber Inner surface of the shell is lined with abrasion resistant materials such as Manganese,Steel or rubber Length of the mill is approximately equal to its diameter Ball mill PPT Free Download SlideShare
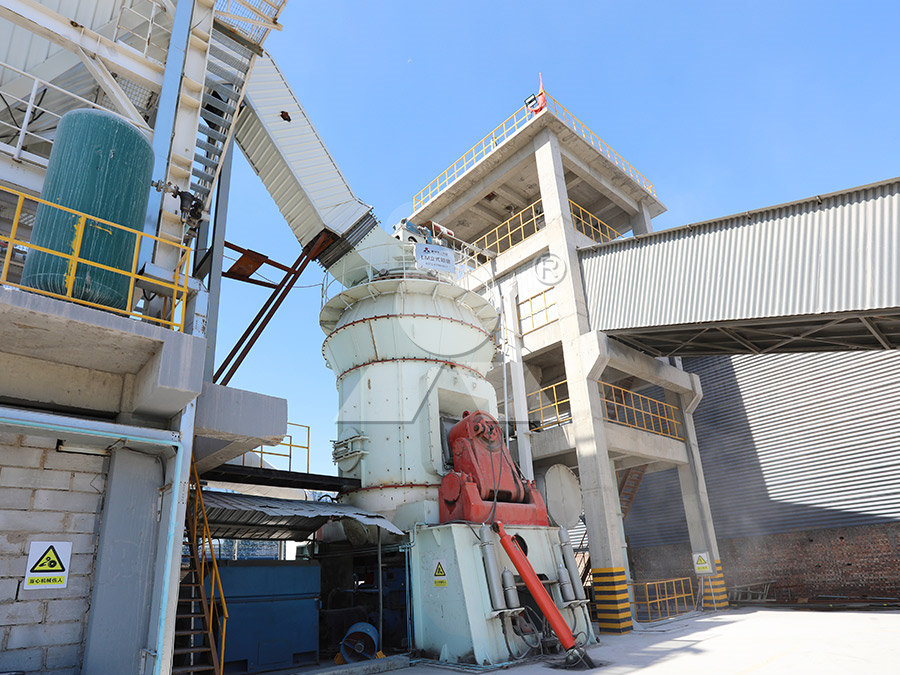
An investigation of the corrosive wear of steel balls in grinding
2015年6月1日 In wet grinding practice, highstress abrasion occurs over a small region when ore particles are trapped between the grinding balls and the mill liner, and the load is sufficient to fracture 2024年5月7日 Forged steel grinding balls are primarily used in ball mills or rod mills to crush and grind materials into finer particles In the mining industry, they are used to extract precious metals from ore Cement manufacturing utilizes these balls to grind clinker, limestone, and other materials into a fine powder, a crucial step in the production processForged Steel Grinding Balls by ENERGOSTEEL2016年9月1日 Nkwanyana and Loveday (2017) used batch grinding experiments in a 06 m diameter mill to test partial replacement of steel balls (375 mm) for secondary grinding, by partly rounded pebbles (19 Addition of pebbles to a ballmill to improve grinding efficiency2022年1月1日 Effects of balltopowder diameter ratio and powder particle shape on EDEM simulation in a planetary ball mill Author links open overlay panel KyongChol Kim a b, When the planetary ball mill operates at high speed, the balls and powder perform irregular and complex movements in the vial, Effects of balltopowder diameter ratio and powder particle
.jpg)
How do you calculate ball mill grinding media?
2023年6月16日 From steel balls to ceramic beads, the choice of grinding media can significantly impact the efficiency and effectiveness of your milling process The Importance of Proper Grinding Media Keep in mind factors such as ball diameter, balltomaterial ratio, and mill speed, as these can affect the grinding kinetics and efficiency