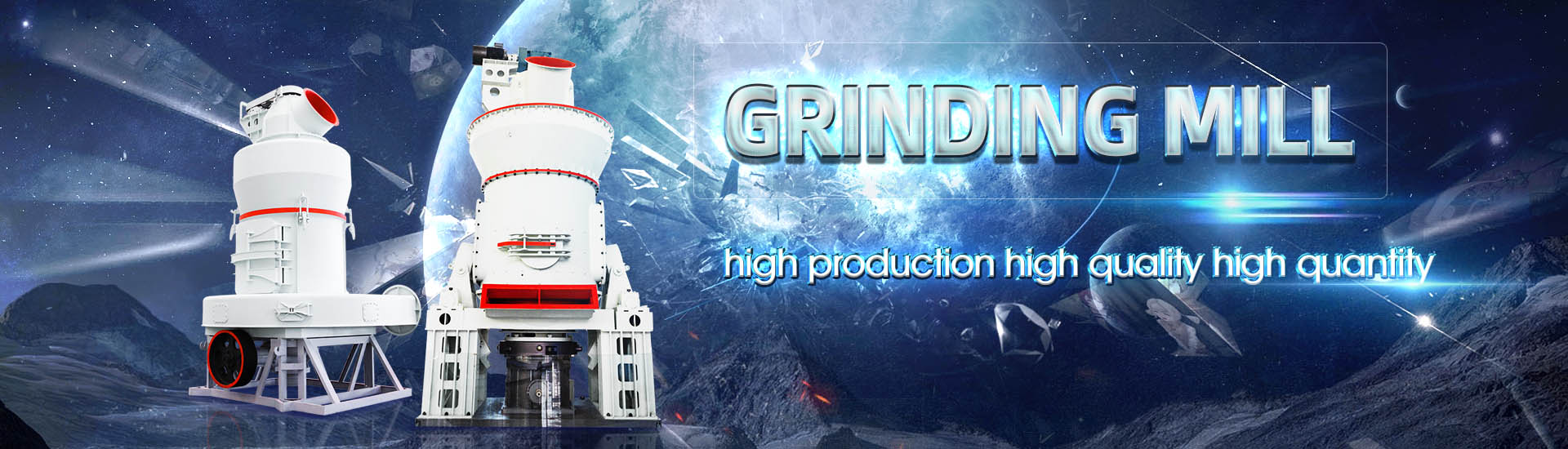
Powder silo feeder discharge port
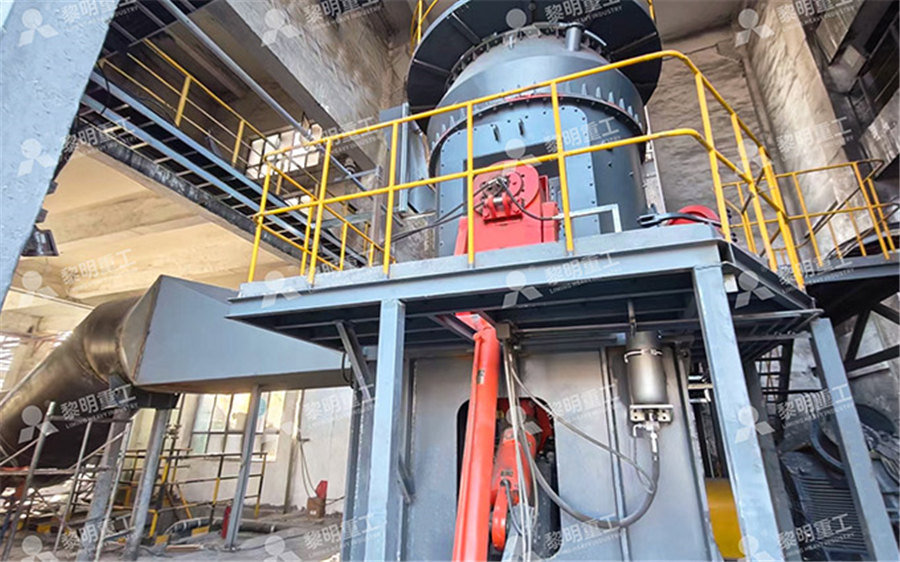
How feeder design impacts silo discharge Processing
2022年12月20日 Reliable bulk solids material flow from a bin or silo requires that the silo hopper is designed to create the correct flow pattern (funnel flow or mass flow) during discharge In funnel flow, material above the hopper outlet This page presents different methods found in the literature allowing to perform hopper discharge flow rate calculation and estimate the bulk mass flow rate of powder from an existing bin, or Hopper and silo bulk discharge flow rate calculationHoppers, silos or dumping stations require discharge equipment to adapt to the varying flow properties of bulk materials and to the given design criteria The bulk materials’ behavior Hopper Discharge Systems AumundGEA supplies bulk storage silos and hoppers for food and dairy products, including powders, sugar, flour, starch, salt, ingredients, mixtures and cerealsPowder Silos GEA Powder Handling

Silo and bin discharger Gericke PDF Catalogs Technical
Gericke: Type RA silo and bin discharger Designed for bulk materials with medium to poor flow characteristics Applications include: n Discharging and feeding from silos and hoppers into It can be used to improve the flow environment and flow area of the powder in the hopper, increase the flow rate of the powder and reduce the overload pressure during discharge Powder silo design and discharge characteristics: a reviewControlled discharge of bulk solids from hoppers and silos is achieved by using a properly designed feeder In many installations the feeder is required to serve an opening size considerably greater than the critical arching dimensions of the Design Considerations for Loads on Feeders bulkonlineInvented, patented and developed by Matcon, the original Cone Valve Manufacturers Our Cone Valve technology allows manufacturers to handle a wide range of powders, bulk materials from cohesive to freeflowing The Valves for Powders and Bulk Materials Matcon IBC
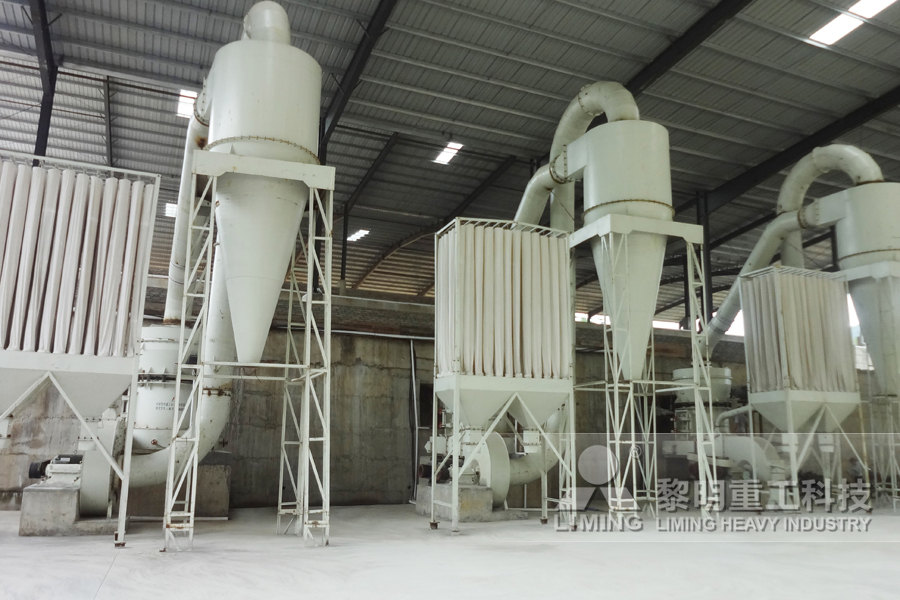
Vacuum Feeder (Negative Pressure Conveying)
The working principle of the Vacuum Powder Feeding Machine is as follows: Material Suction Process: The machine features a pneumatic valve beneath the silo, allowing only air intake at the feed port A hose connects the air inlet to What are bulk solids feeders? During bulk material handling processes, an amount of the bulk raw material is transferred from one point to another eg, the transfer of the bulk material from a silo to a tank This transfer of the bulk Bulk Solids Feeders – Airlock FeederThe A ishin cross feeder is connected to the hopper, allowing material to flow into it Inside the cross feeder, blades move in an anticlockwise direction, helping to evenly distribute the material This efficient system features a coneshaped structure at the center of the cross feeder, designed to prevent blockages and clogs while ensuring a consistent flow of powder materialCross Feeder Solutions for Powder Slurry Discharge AishinMultiple screw feeders: Thanks to our leading expertise and technical knowhow, our Bin Activator can accomodate multiple feeders, each feeder functioning independently, capable of sustaining a high flow on one side, and a low flow on the other Mechanical extraction of virtually any material, without contamination or variations due to unique ADVANCED DENSITY CONTROLMechanical bin activator Bulk storage silo Screw Feeder
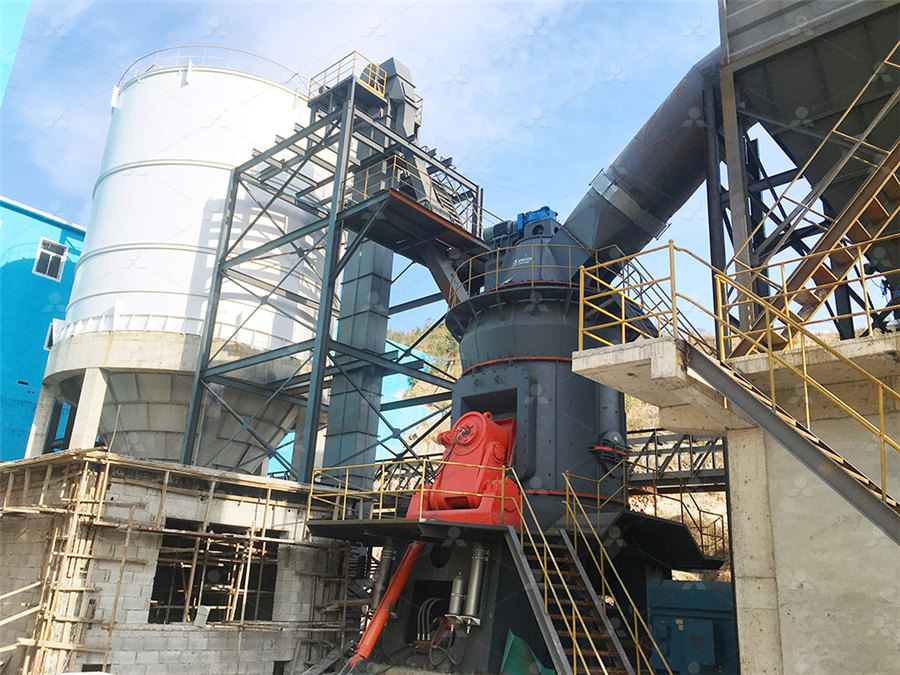
Impeller FeederDAHAN Vibration Machinery
Introduction of Impeller Feeder Impeller feeder, also known as rigid impeller feeder, electric discharge valve, star discharge valve, etc, uses a rotating impeller with compartments to transport powder and small granular materials from the upper storage bin or hopper to the lower dischargeIt is specially designed for storage, feeding powder engineering, quantitative feeding Reliable Hopper, Silo and Bin Discharge AJAX make various types of equipment for discharging from hoppers, including: Bin Activators For stimulating flow Table Feeders For large circular outlets with rigid connections Single Multiple Screw Feeders Multifunctional Bin ActivatorsMethods, techniques and equipment for effective and reliable discharge Powder Silos GEA specializes in the supply of bulk storage silos and hoppers for food products, including dairy powders, sugar, flour, starch, salt and a wide variety of ingredients, mixtures and cereals Discharge equipment using vibratory, aeration and mechanical devicesPowder Silos GEA Powder Handlingdischarge hopper Material discharge hoppers are available in various diff erent heights Discharge blade Table feeder discharge unit Notice: The technical design may diff er from the illustrations 1) Depending on machine confi guration 2) Silo discharge unit version 3) For machines with enclosure: 2500Rotary Table Feeders Eirich
.jpg)
Hopper and silo bulk discharge flow rate calculation
2 Hopper discharge rate calculation method 1 : using shear cells data In order to estimate the discharge rate of a silo, one of the most reliable method is 1 st to have assessed the flowability of the material that will be stored in the hopper Different methods are available for evaluating the flowability but one of the most reliable, which allows to have quantitative data and not only a Sodimate uses gentle agitation, rather than vibration or fluidization, when discharging and feeding the dry powder Vibrators mounted directly on bins or silos can cause issues such as compacting, bridging, and arching Our silo Bulk storage Handling System Mixing Systemthe powder from any contamination • Easy to install with its rotating flange, adjustable length, flexible or rigid screw feeder Silo Archbreaker Feeder ZDM 400 Powder handling expert The ZDM archbreaker and screw feeder are the components of a mechanical discharging and volumetric feeding system for conical bins and silosSodimate Silo Archbreaker Feeder ZDM 400Easy to install and retrofit to existing silos, hoppers and bins to overcome powder discharge problems Valve sizes ranging from 500mm to 25 metres and acts as both a flow aid and shutoff valve in one The reliability of binandsilo design Material Discharge Valve for Silos and Hoppers
.jpg)
Bulk Silo Systems Powder Storage Sodimate Inc
Bulk storage silos made of steel are the perfect solution to store the powdered reagents like hydrated lime, activated carbon, soda ash, and many other dry chemical powdersThe cylindrical shape and the conical bottom allow a complete discharge of the product when combined with a mechanical arch breaker Silos have a custom design regarding the local constraints related 2023年1月23日 Match the Feeder to the Outlet In most bulk material handling applications, a feeder is used to control discharge from the outlet of the vessel The control involves not only stopping and starting flow but also metering the rate of discharge A feeder typically provides the ability to meter or control the throughput rate, often in floodloaded Powder Handling: Silos, Hoppers and Bins, Oh MyContinuous Vacuum Feeding, also known as Negative Pressure Conveying, is a sophisticated material handling system designed to ensure seamless and uninterrupted transfer of powders, granules, and other materials in industrial processes This advanced technology utilizes negative pressure to convey materials through pipelines continuously, offering a reliable and efficient Continuous Vacuum Feeding (Negative Pressure Conveying)LEARN MORE Powder Cone Valve System A superb discharge device, it overcomes all the typical powder handling and flow problems of bridging, blockages, mix segregation, flushing and core flow that are commonly associated with butterfly valvesIt offers automatic and controlled discharge of virtually any powder type, winning where other systems have failedCone Valve Technology Accurate Powder Discharge from IBCs
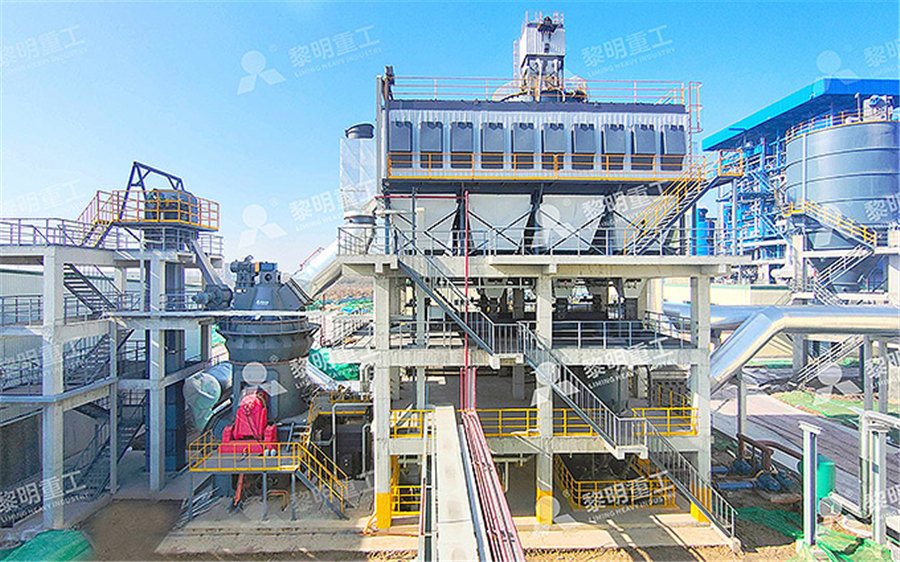
Blockages in silos : arches / bridge, rathole PowderProcess
The flow of powder out of a silo is stopping primarily for 2 reasons ; either formation of arches (arching, bridging) or ratholes Learn in this page what are the root causes of both arches and ratholes and how to avoid them 1 Powder blockage in silosKey Features Discharge mechanism: rotary valve, screw conveyor, and screw feeder systems Screw feeders (or spiral feeders) can be either continuous feeders or batching units Continuous feeding is characterized by releasing a constant amount of product over a set time Over a set time, the batching unit must release a set quantity of product overPowder Feeders – Cosmos Engineering Malaysia2021年9月3日 Discharge devices are well known devices as, for example, belt feeders, apron feeders, enmasse feeders, vibratory feeders, rotary valves, and screw feeders being attached to the outlet of a silo Shutoff devices (eg, slide gates, clamshell gates) can also be regarded as discharge devices since they allow a certain (often poor and accompanied by problems, see Discharge of Bulk Solids SpringerLinkPowder Granular Material Feeder Principles of the Discharge System and Construction Drawing Adjustment of Discharge Rate Feeding and residual material , CIRCLE FEEDER CIRCLE FEEDER solves every problem with powder and granular materials once and for all Construction Drawing Principks of the Dischaege System CIRCLE FEEDER e Hopper, Silo Komachine
.jpg)
Cement Silos MEKA Concrete Plants
CRUSHING SCREENING PLANTS Feeders Grizzly Feeder Pan Feeders with Grizzly Scalper Vibrating Feeder Apron Feeder MEKA offers a wide range of storage silos for powder products like, Lime, Fly Ash, Microsilica, Bentonite 2024年5月15日 Electrostatic discharge in powder silos poses a significant safety hazard due to the risk of fire or explosion However, the underlying discharge mechanisms are not fully understood This study aims to improve the comprehension of electrostatic discharge dynamics and mechanisms by introducing a fluid discharge model for charged powder silosElectrostatic discharge mechanisms and dynamic characteristics of To control or throttle the feed rate to the downstream process, a feeder or discharge valve is typically installed at the outlet of the bin or hopper However, some feeders, such as screw feeders and belt feeders, are not able to stop the uncontrolled discharge of powders out of bins caused by floodingDetermining Discharge Rates of Particulate Solids AIChERotary feeder placed under the silo, hopper or other container system is used to control the bulk solid (in powder or granule form) discharge from these units and feed equipments like conveyor, screw feeder, mixer etc Skip to content [ protected] EN DE TR HOME PAGE; ABOUT US;Rotary Feeder Applications polimak
.jpg)
Bulk solids handling Engineering Feeder and Conveyor Design
The use of trim gates (not recommended) if used in between silo outlets and feeders needs to be treated with caution Settings can block product flow, and lead to erratic discharge due to funnelling and high wear and energy requirements Flow control must only be achieved by the feeder, and not any other meansA feeder must provide an equal discharge over the area of the opening If this is not the case then the feeder will cause funnel flow, even if the silo has build for mass flow This is illustrated in the following situation from practice: Case: screw feeder A silo for wood dust and gypsum powder regularly gave flow problemsSilo design bulk solidsEN19914:2006 Eurocode 1: Actions on Structures Part 4: Silos and Tanks McGee, E, McGlinchey, D: Using Wall Friction Data to design Hoppers PARTEC 2004 Nuremberg 2004 Schulze, D: Silo Design and Bulk Solids Flow Properties From Powder to Bulk, IMechE Conference 2001Design Considerations for Loads on Feeders bulkonlineThe main equipment of positivepressure dilutephase pneumatic conveying includes rotary feeder device, pneumatic screw conveying pump, roots blower, China 5×800m³ Gypsum Powder Silos Project closed storage yard, and bulk material port handling project for cement, clinker, fly ash, coal, slag powder, sand and gravel aggregate Pneumatic Conveying Systems for Dry Bulk SRON® Silo
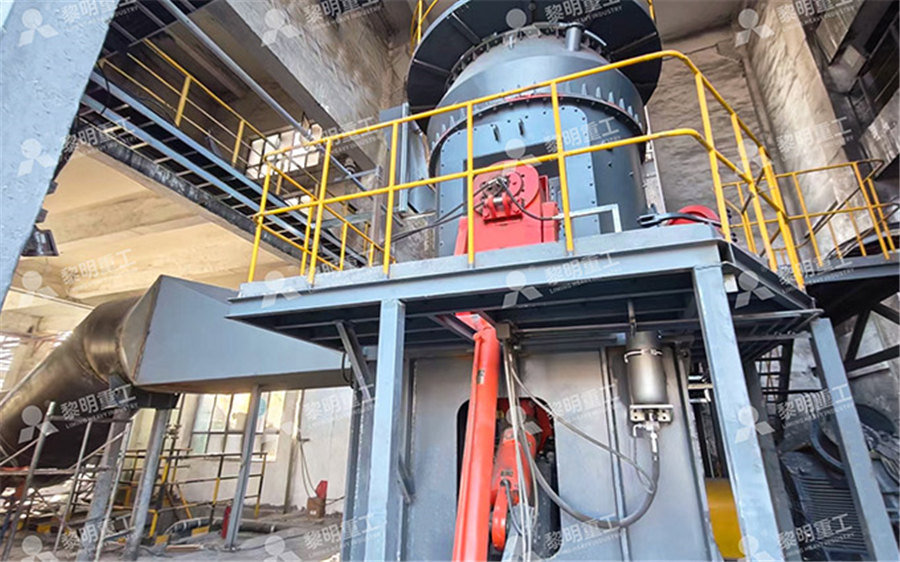
New PAC Feed System Acrison
The system utilizes two Model W105Z Volumetric Feeders sharing a common hopper, with each feeder equipped with its own Wetting Cone assembly The operator supplies both feeder systems with product from a single loading pointpositive discharge of material, on demand Conditions the material to a constant bulk density The Vibra Screw Bin Activator is specifically designed and sized to ensure that the material contained in the silo will flow freely into the feeder system below Bin vent to assure proper air venting when refilling the silo Dry and wet transfer either POWDER ACTIVATED CARBON SYSTEMS Vibra ScrewSiletta® MultiFunction Feeder Type RM for raw materials in mining and process industries, and high rate of flow Handles lumps up to 200 mm Simultaneous discharge over the entire outlet area Live bottom; Trimming valve; Shut off valve; For outlets:Bulk Handling Global Bulk solids and powder flow solutionsPressure in a silo filled with a fluid (imaginary); b vertical stress after filling the silo with a bulk solid; c vertical stress after the discharge of some bulk solid The stresses acting in a hopper are different from those in the vertical section Just after fillingStorage of Powders and Bulk Solids in Silos
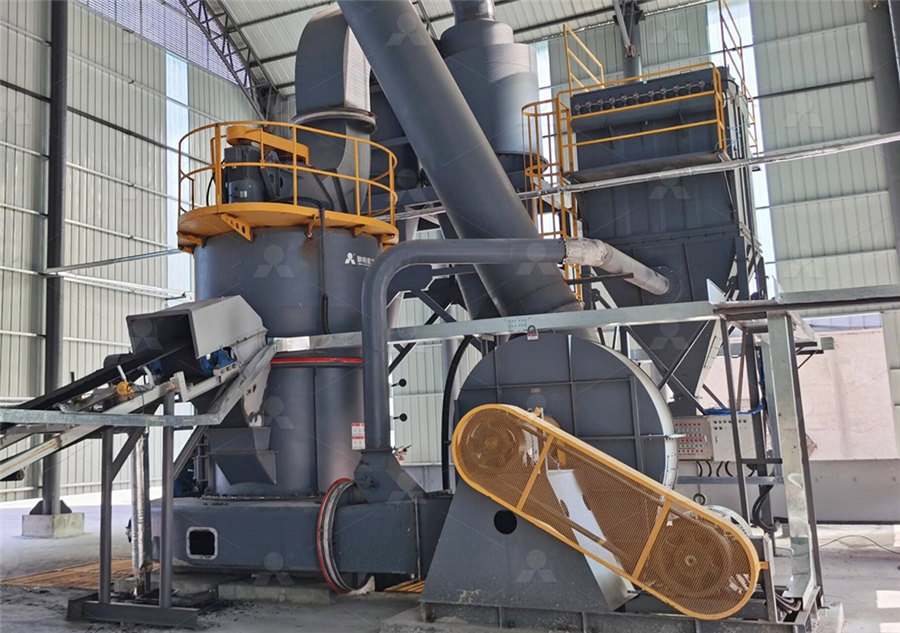
Investigation of discharging flow behavior of powder in the
2023年11月25日 In the fluidization process of nylon powder, maintaining a uniform flow of powder in the feed silo is crucial to reduce powder agglomeration and facilitate the fluidization process In this study, BINSERT was applied to improve the flow properties of powder in the feeding silo The discharge process of nylon powder in silos equipped with different dip angles Gericke: Type RA silo and bin discharger Designed for bulk materials with medium to poor flow characteristics Applications include: n Discharging and feeding from silos and hoppers into dense phase and lean phase pneumatic conveying systems n Fast loading of lossinweight feeders with integral outlet valve for complete product flow isolation n Component feeding into weigh Silo and bin discharger Gericke PDF Catalogs Technical Solutions for bulk solids and powder flow problems in all industries Bulk solids and powder flow properties testing, shear testing, bulk materials handling equipment, Silo discharge and feeder technology for cohesive and difficult to manage products Guaranteed controlled mass flow discharge of high moisture (65%), cohesive, Bulk solids Powder flow properties testing Bulk materials Silo Unlock the secrets of powder flow, solids properties, and silo design with our indepth knowledge base Learn to enhance powder flowability, tackle flow issues, Hopper and silos discharge rate calculation Learn how to calculate hopper discharge flow rates for bulk solids, a critical task for Mastering Powder Flow: A Comprehensive Guide to Solids
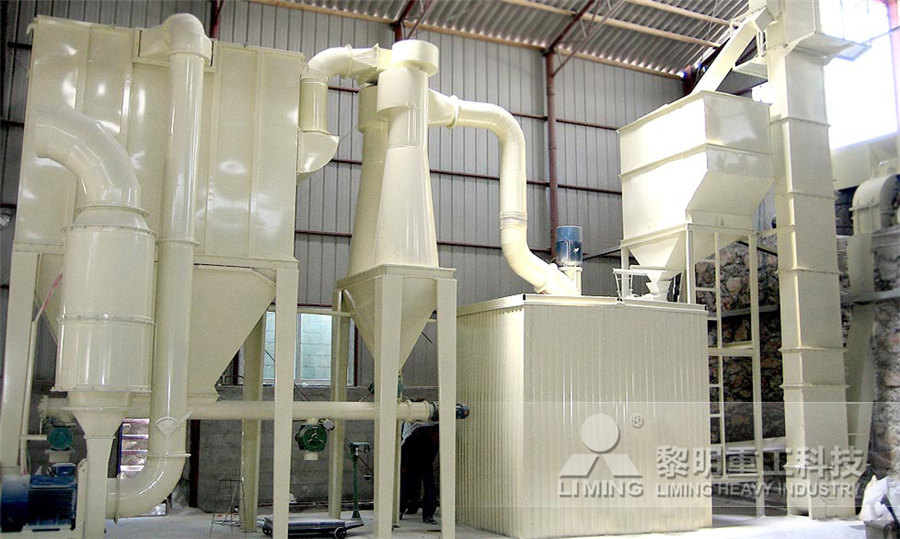
Mass Flow Feeder LCI Corp
When a large quantity of bran is stored in a silo, it is difficult to discharge because the material's high pressure causes bridging at the lower part of the silo This is aggravated by bran's low bulk density Our mass flow feeder is ideal for discharging bran from large silos due to its large inlet diameter which prevents bridgingThe use of trim gates (not recommended) if used in between silo outlets and feeders needs to be treated with caution Settings can block product flow, and lead to erratic discharge due to funnelling and high wear and energy requirements Flow control must only be achieved by the feeder, and not any other meansBulk solids handling Engineering Feeder and Conveyor DesignWAM Microbatch Feeders MBF The WAM MBF range of Microbatch feeders provide accurate volumetric feeding of powder and granular materials Stainless steel body, Agitator tool and Feeder screw Available with Horizontal or Vertical spout outlets Available with foodgrade and ATEX zone versions Throughputs of up to 6m³ / hrHopper / Silo Discharging Filquip