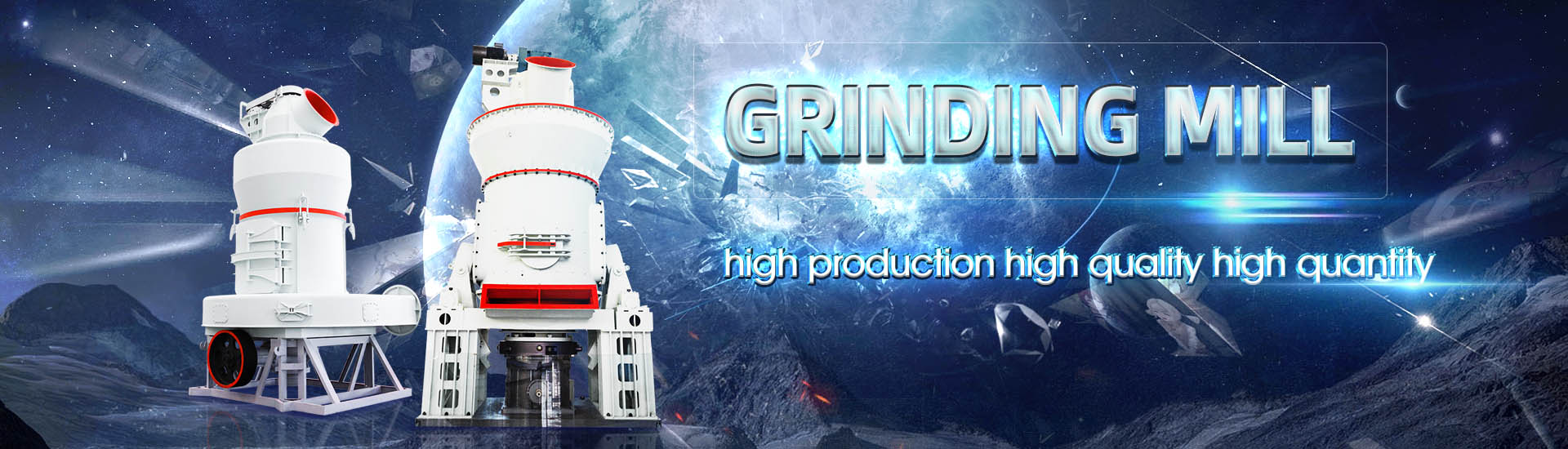
Lignite grinding machinery process flow
.jpg)
Selective grindability of lignites and their application for
2003年3月1日 The grindability of the xylitic component of the lignite significantly differs from that of the mineral matter So there is a promising possibility for the appropriate dry processing of the advanced fuel or other products with low ash and high humic acid contents by the selective This study presents design considerations and an evaluation of a fullscale process chain for methanol and advanced dropin fuel production derived from lignite/solid recovered fuel (SRF) feedstock The plant concept consists of a Process Analysis and Design Considerations of a Low 2000年10月18日 A numerical algorithm is developed for a detailed 3D simulation of the twophase flow field in fluidenergy mills used for pulverization and drying of fossil fuels in large Numerical Simulation of Grinding and Drying Performance of a 1997年7月1日 A numerical investigation is presented for a twodimensional simulation of the gas flow field and of the dynamic behavior of lignite particles inside Beater Wheel mills with Numerical Investigation of the Grinding Process in a Beater Wheel
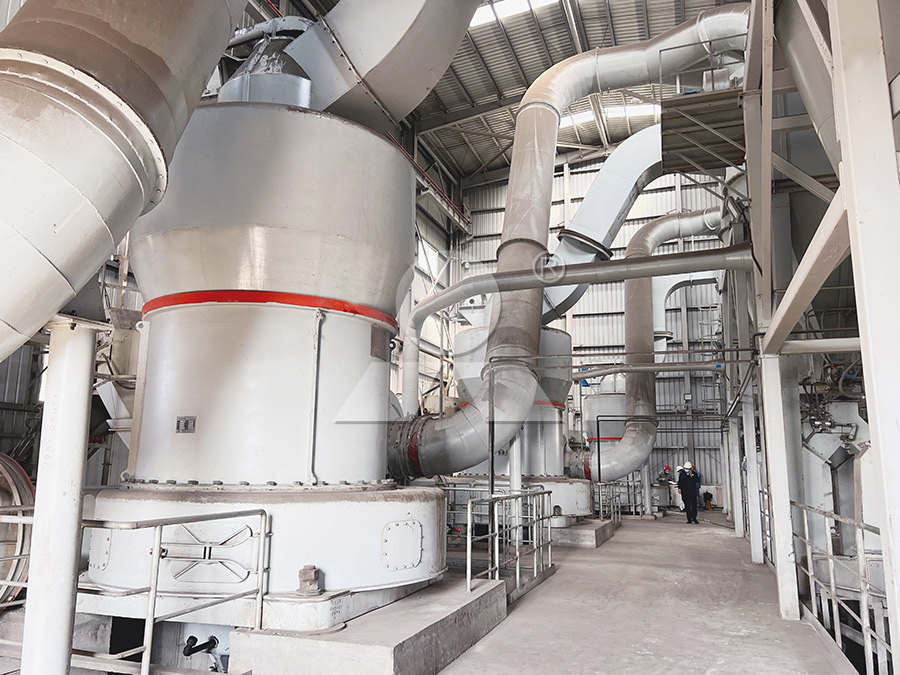
Numerical Simulation of Grinding and Drying Performance of a
2001年6月1日 The flow and the operation characteristics of a recently developed lignite mill are measured, and the numerical algorithm is used to predict the mill performance under various 2023年9月9日 This study aims to investigate the variations in the morphology of lignite samples under different grinding conditions such as grinding time and powder/grinding media ratio (U) The Effects of BallMill Grinding Parameters on Lignite 2024年1月27日 The results demonstrate that lignite ground for 50 min follows monolayer adsorption, characterized by minimal pore size and reduced diffusion rates, thereby extending Preparation and NH4+ Adsorption Performance of Ultrafine 2022年9月30日 Aiming to explore the limitation of Hardgrove Grindability Index (HGI) and broken behavior of lignite, coal samples were ground for different minutes in the Hardgrove Research on the grinding characteristics of lignite based on
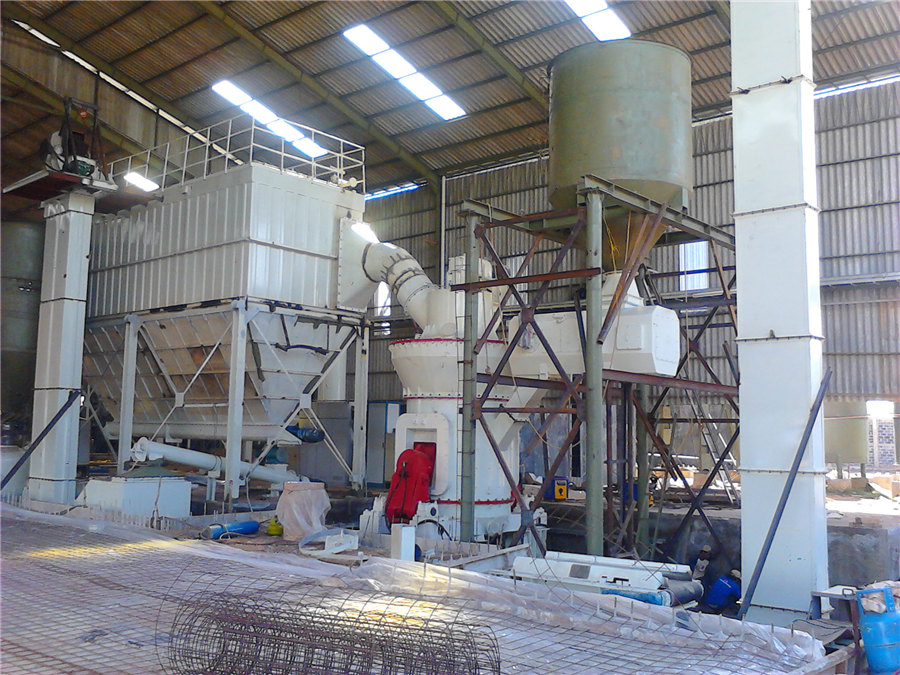
Effects of different drying methods on the grinding characteristics
2015年12月15日 Ximeng lignite (XL) was treated by using different drying methods, namely, conventional, microwave, and combination, to investigate their effects on the grinding 2014年8月23日 The objectives of this study are as follows: (1) to propose a highefficiency lignite predrying system with lowgrade heat integration for a 1,000 MW modern lignitefired power A novel lignite predrying system with lowgrade heat integration GypLignite dryer process flow ZONEDING Lignite Coal Dryer ZONEDING’s lignite coal rotating dryer adopts a lowtemperature fourstage drying process to ensure the quality of lignite coal remains unchanged, Our product range also Lignite Coal Dryer Machine Zoneding Mining Machine2021年5月5日 It is also known as the Abrasive Grinding Machining Process Why Abrasive Grinding Machining Process? Because the abrasives are placed on the surface to do the finishing process with much more accuracy The grinding Grinding Machine: Definition, Parts, Working
.jpg)
Analyzing process parameters for industrial grinding circuit based
2023年9月1日 Based on the machine learning method, this study analyzed the full process parameters (ie, ball mill power, fresh ore feed rate, hydrocyclone feed pump power, hydrocyclone pressure, mill feed water flow rate, dilution water flow rate, and sump level) for industrial grinding circuit2012年6月1日 As the cylinder starts to rotate, the grinding balls inside the cylinder crush and grind the feed material, generating mechanical energy that aids in breaking bonds, activating the catalyst, and Grinding in Ball Mills: Modeling and Process ControlProcess of Raw Mill The proportioned raw material is feed first to a grinding mill In the mill, particles ground in to very fine sizes In the grinding unit, drying, grinding and mixing takes place simultaneously Hot gas from clinker burning unit is passed into the grinding unit to assist the drying and grinding processCement Manufacturing Process INFINITY FOR CEMENT EQUIPMENTThe grinding machine provides high accuracy and fine surface finish with minimum tolerances The machining process is done by the abrasive action of the grinding wheel; the abrasives are embedded over the periphery of the rotating wheel In Grinding machine grinding wheel is work as a cutting tool and responsible for all machining processesGrinding Machining Process : Complete Notes Mech4study
.jpg)
Grinding Machines SpringerLink
2015年1月1日 As grinding machines belong to the class of machines for the material removal with geometrically nondefined cutting edges, those machines can be classified in correlation to the classification of the different process technologies with geometrically nondefined cutting edges as it is given in DIN 8589, parts 11, 12, and 13 (DIN 858911 2003; DIN 858912 2003; 2018年2月6日 Grinding is the material removal and a surface finish process in which the material is removed from the work surface in the phase of small chips by process of tiny abrasive particles of grinding (PDF) A Review of Cylindrical Grinding Process ResearchGateDownload scientific diagram WTA process for lignite drying from publication: A Critical Assessment of Industrial Coal Drying Technologies: Role of Energy, Emissions, Risk and Sustainability WTA process for lignite drying Download Scientific DiagramThe wheat grinding process is crucial as it determines the texture and quality of the flour Advanced wheat grinding machinery and technology play a significant role in this phase, ensuring precision and consistency Following grinding, the process of sifting separates the fine flour from the bran and other coarse particlesUnderstanding Wheat Processing Steps: From Grain to Flour

System optimization and selection of lignite coal
2015年7月1日 7 Benefits and issue with lignite coal drying • Mechanism of inhibition of spontaneous combustion of lignite By destroying or reducing the structure with lower activation energy; Coal surface is inerted by covering with Download scientific diagram Typical cement manufacturing process flow diagram [4] from publication: Model Development for CO2 Capture in the Cement Industry Climate change has become a Typical cement manufacturing process flow 2018年7月27日 For the necessary direct fine grinding of the runofmine lignite coal, RWE has developed a special process with two grinding stages connected in series for the reduction of the grain size of the raw lignite coal from around less than 80 mm to the desired value of less than 2 mm Fig 3b shows the overall process of finegrain WTA process WTA technology for drying of lignite coal – IspatGuru2020年6月29日 Belt grinding has become an important production process, in some cases replacing conventional grinding operations such as the grinding of camshafts Belt speeds are usually in the range of 2,500 to 6,000 ft/min Machines for abrasivebelt operations require proper belt support and rigid construction to minimize vibrationChapter 17: Grinding Methods and Machines American Machinist
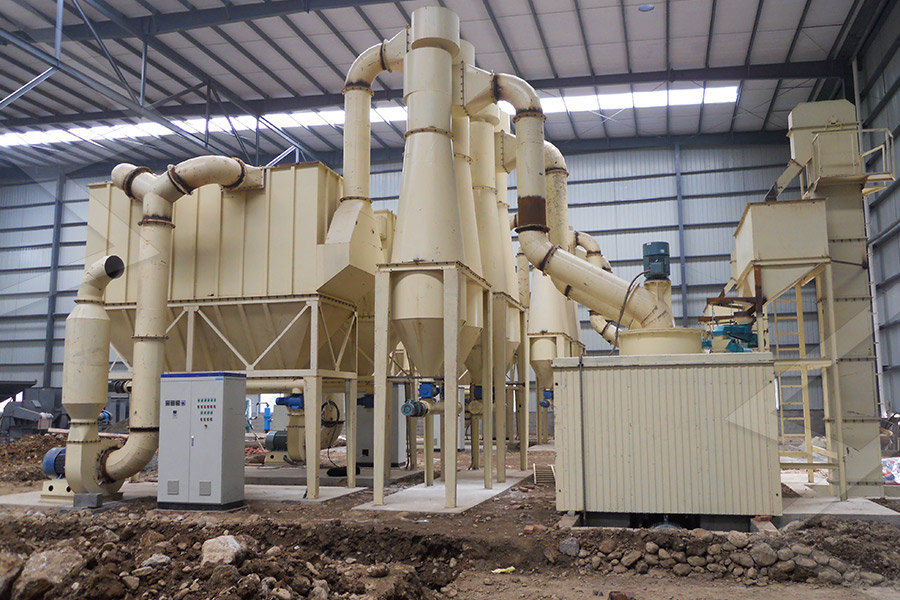
Types of Machining Process: Classifications and Differences
2022年11月30日 Grinding is one of the types of machining process ideal for improving the finish on a machined part’s surface and tightening its tolerance Furthermore, the process produces parts with identical shapes, finishes, and sizes It is also the first step in further finishing operations like honing, lapping and superfinishing2 Lignite power station fleet, fuel quality, technology and legislation 13 21 Lignite power stations 1950‒2015 13 22 Lignite fuel resources and consumption 14 23 Lignite fuel quality: energy content, water and ash 16 24 Lignite power plant boiler technology 17 25 International commitments to lower greenhouse gas emissions 18Retrofitting lignite plants to improve efficiency and performance2019年2月18日 However, with the addition of 5% lignite, the grinding duration was 60 min, accounting for 419% of particles (d ≤ 10 μm) and 854% of particles (d ≤ 10 μm) This was the optimal activation effect on the particles obtained by adding 3% lignite to PR powder in an appropriate grinding duration (20 min)Enhanced Phosphorus Release from Phosphate Rock Activated with Lignite 2021年3月12日 So far, the biggest mill for lignite coal grinding will be delivered to Cemindo’s Bayah plant in Indonesia This MPS 4500 BK has been ordered for grinding lignite with a maximum moisture of 37% and it is able to produce a throughput rate of minimum 100 t/h at a residue of 15% R009 mm The installed power for the mill main drive is 1300 kWMPS mills for coal grinding AYS Engineering
.jpg)
Grinding Process SpringerLink
During a machining process with a trackbound cutting edge engagement, the cutting edge of the grain penetrates the workpiece upon a flat path and, after a phase of elastic deformation, triggers plastic flow of the workpiece material (Fig 3)Due to the shape of the cutting edge, the angle between the cutting edge contour and the workpiece surface is very small at the beginning of 2018年7月20日 Drying Technologies of Lignite Coals satyendra; July 20, 2018; 0 Comments ; bituminous coal, Coldry process, drying of coal, Fliessner process, Lignite, MTE process, PristineM process, Thermal dewatering, WTA Drying Technologies of Lignite Coals – IspatGuru2022年11月12日 Cocoa nibs are ground using a colloid mill In the process of grinding the sauce, the large particles of cocoa crumbs will become particles of only about 015mm under the highspeed shearing and friction of the colloid Cocoa Processing Flow Chart (From Bean To Powder)2018年10月28日 For RWE’s lignitefired power plants, the focus for mercury control is on an innovative entrained flow process and adsorption by activated lignite, called HOK®, produced from Rhenish lignite HOK® is injected into the flue gas stream, adsorbs both elemental and oxidised mercury and is removed from the flue gas in the electrostatic precipitator together How Rhenish lignite can reduce power plant mercury emissions
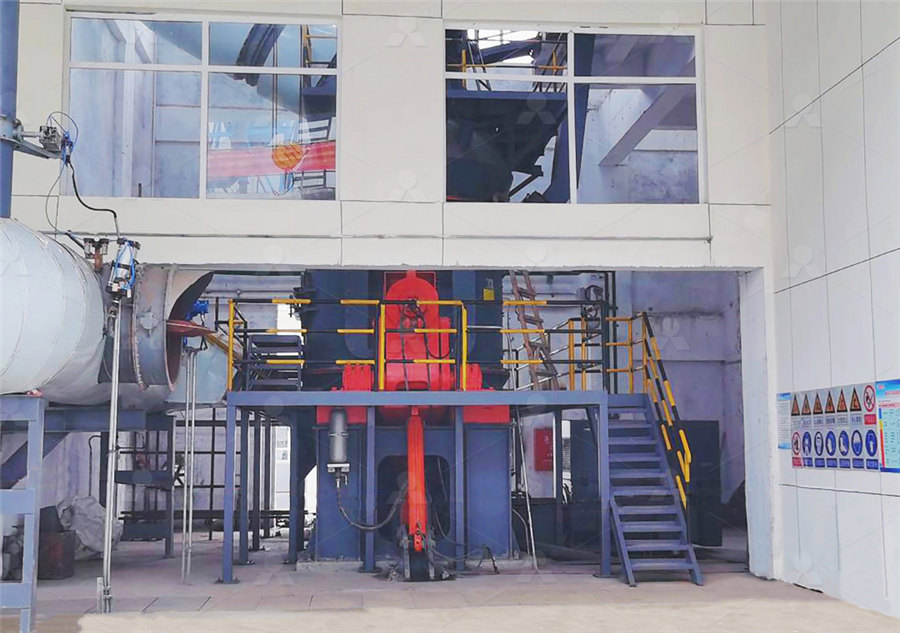
Briquetting Process an overview ScienceDirect Topics
This disintegration is sometimes referred to as relaxation characteristic The briquetting process may be responsible for briquette relaxation Drying may be accompanied by shrinkage; expansion (increase in a briquette's length or width) is also possible The briquetting process primarily involves drying, grinding, sieving, compacting, and cooling2022年7月1日 Lignite samples (LS) were prepared by grinding the lignite to particles 05 mm in diameter, passing them through a 35mesh sieve, and autoclaving them at 121 °C for 30 min A fungal strain was isolated from newly exposed lignite and identified as Fusarium (fungus named Fusarium sp NF01, accession No MN) by Shanghai Majorbio BioPharm Technology Proteomic analysis of Fusarium sp NF01 revealed a multilevel Such a simplified relation was successfully employed on a fullsize, lignitefired steam boiler for a determination of the coal's massflow distribution [7, 17] among the burner nozzles receiving Thermal power plant's coal grinding and transport system to 2020年11月18日 Manufacturing Process: Grinding Previous blog; Next blog; Huyett Marketing Department 11/18/2020 Grinding, also called surface grinding, is a machining operation in which material is removed using a powered abrasive wheel, stone, belt, paste, sheet, compound, etc to realize fine finish tolerances and surface finishesManufacturing Process: Grinding Huyett
.jpg)
Grinding Processes SpringerLink
Grinding is the common collective name for machining processes that utilize hard, abrasive particles as the cutting medium The grinding process of shaping materials is probably the oldest in existence, dating from the time prehistoric humans found that they could sharpen their tools by rubbing them against gritty rocks2024年4月21日 The process flow of lignite upgrading mainly includes the following steps: First, the coal mine sends the raw lignite ore to the washing plant for the washing processProcess flow of lignite upgrading by Jiutian Mediumyear prior to selection of a process This allows for the effects of spring floods, highand lowwater periods, and other river activity to be included in the final determination If a process is based upon samples drawn from summer production, lignite By Rick Yelton New machinery for doityourself lignite removalNew machinery for doit yourself lignite removal Concrete 2015年12月1日 Ximeng lignite (XL) was treated by using different drying methods, namely, conventional, microwave, and combination, to investigate their effects on the grinding characteristics of XLEffects of different drying methods on the grinding characteristics
.jpg)
17 Lignite Combustion US Environmental Protection Agency
most stoker units, the grate on which the lignite is burned gradually moves from one end of the furnace to the other The lignite is spread on the grate in such a fashion that at the end of the grate only ash remains (ie, all of the lignite has been burned to the final ash product) When the ash reaches the end of the2019年11月1日 Recently, Magalhaes et al [78] compared the combustion behaviors of three biomass (raw and torrefied) and two lignite coals in a drop tube furnace using pyrometry techniques, and found that biomass particles and Tuncbilek lignite ignited homogeneously forming volatiles envelope flame and a distinguishable char combustion, while Soma lignite exhibited Biomass torrefaction: properties, applications, challenges, and 2024年4月22日 Process flow of lignite upgrading Lignite is a type of coal that contains relatively high amounts of moisture and ash The utilization value of lignite is relatively low, but through upgrading processes, lignite can be converted into fuels with more economic value Process flow of lignite upgrading Jiutian Machinery PRLog2018年5月25日 'Grinding Parameters' published in 'CIRP Encyclopedia of Production Engineering' In general, the material removal rate can be calculated by the actuating cross section A w, which is the cross section between tool and workpiece orthogonal to the feed directionA general overview on the process parameters and the calculation of the material removal rate Grinding Parameters SpringerLink
.jpg)
Machining 101: What is Grinding? Modern Machine Shop
2021年7月3日 Grinding process control balances these three interactions to achieve the desired parameters These interactions feed into three major commercial grinding processes: rough grinding, precision grinding and ultraprecision grinding Rough grinding maximizes the metal removed at the cost of surface finish2022年6月24日 Grinding is a manufacturing process which significantly contributes in producing high precision and durable components required in numerous applications such as aerospace, Li C, Zhang Q, Wang S, et al Useful fluid flow and flow rate in grinding: an experimental verification Int J Adv Manufacturing Tech 2015; 81(5): 785–794A comprehensive review on the grinding process: Advancements Lignite mining refers to the extraction of lignite, which causes pollution of land, air, and water, resulting in ecological damage Efforts are being made to reclaim the minedout land and convert it into agricultural fields, afforestation areas, orchards, herbal gardens, and an Eco Park to maintain ecological balance and minimize the negative impacts of the mining activitiesLignite Mining an overview ScienceDirect Topics2019年8月26日 What is Zircon Sand? Zirconium sand, also known as zircon sand, is a mineral composed mainly of zirconium silicate Pure zircon sands are colorless transparent crystals, often dyed yellow, orange, red, and brown due to different origins and impuritiesZircon Processing Equipment, Process Flow, Cases JXSC Machine