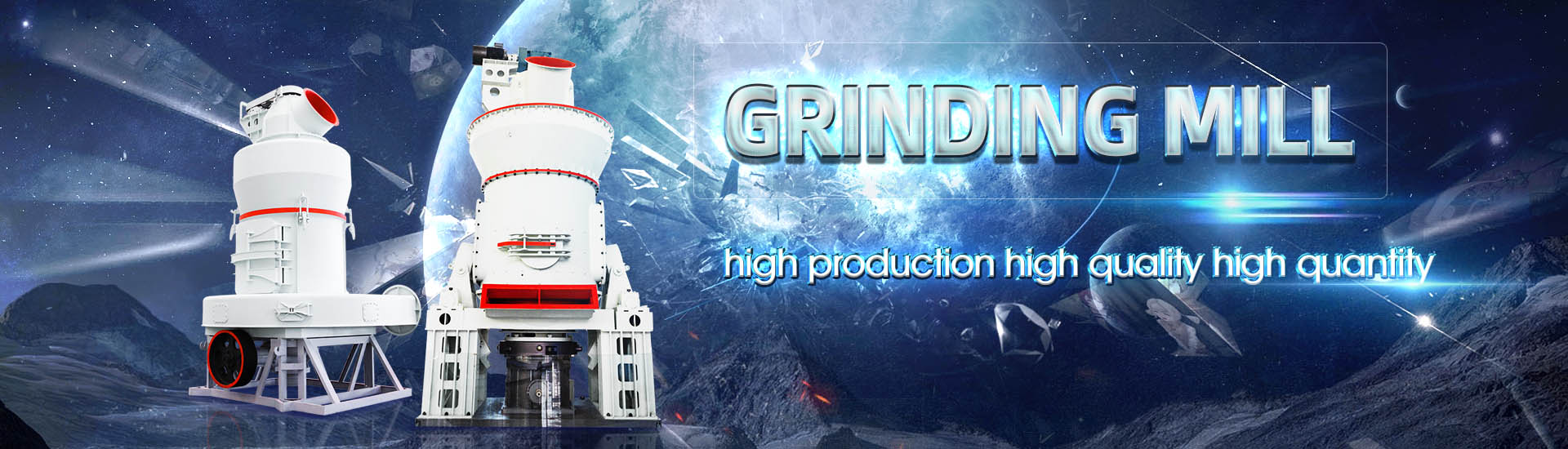
Alkaline Furnace Lining Material Powder Making Process Certification Procedure
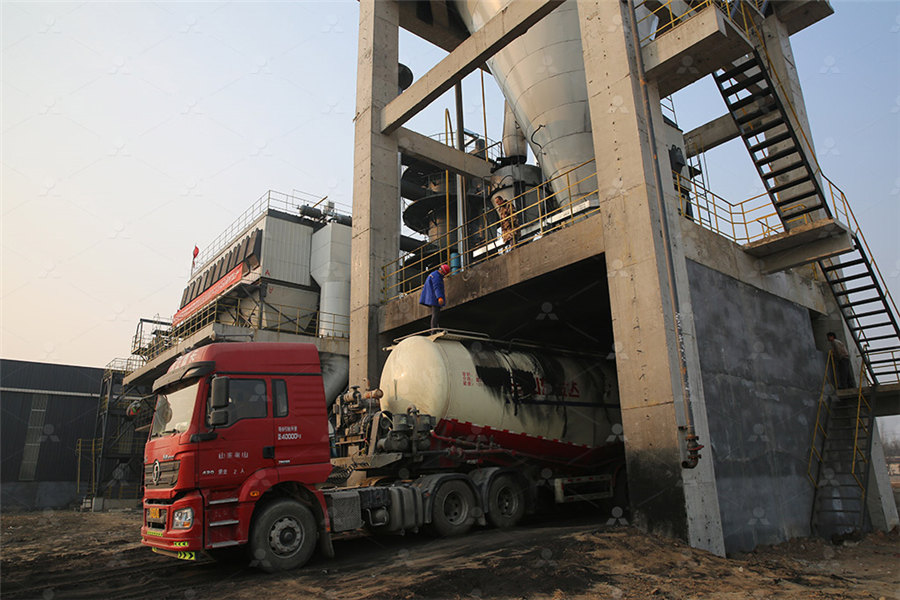
Refractory Lining of Coreless Induction Furnace IspatGuru
2019年9月16日 The lining practice best suited to particular induction furnace depends upon (i) the furnace capacity and design, (ii) raw material used for melting, (iii) quality and temperature 2017年3月14日 To do it right, here are five primary tips for maximum furnace lining efficiency: 1 Use IR thermography to inspect the existing lining — Ensuring lining quality is critical to Ensuring Furnace Lining Efficiency Foundry Managementworking with the metallurgical and thermal process industries for some 50 years and have the majority of UK business for induction furnace linings melting steel We offer a full manufacture, Refractories for Induction FurnacesThis paper will discuss a completely new generation of refractories and address care of structural components, installation, sintering and optimal operation of coreless induction furnaces to Innovative Refractory Technology for Coreless Induction Furnaces
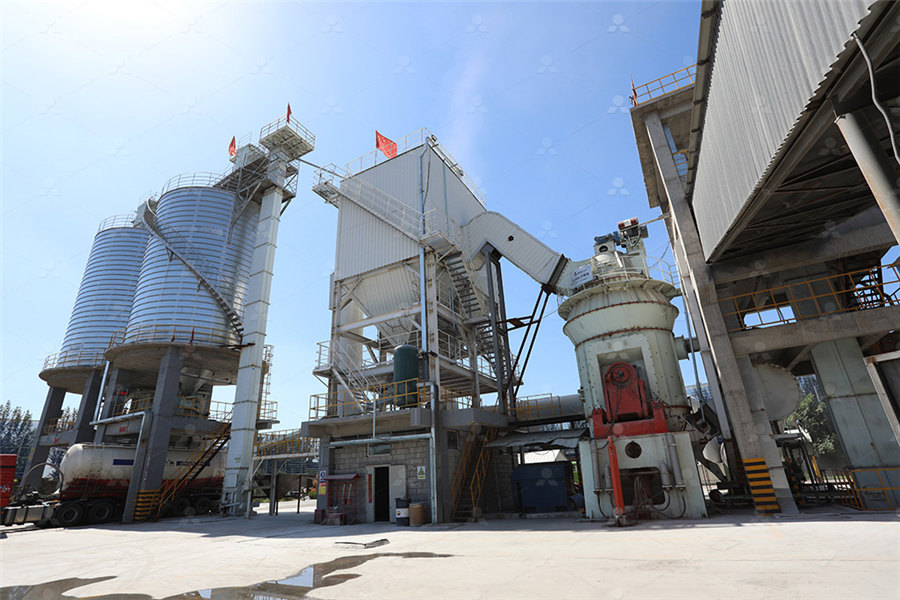
Design, fabrication and properties of lightweight wear lining
2022年3月1日 The design of lightweight wear linings is crucial in terms of the energy and resource efficiency of industrial furnaces and quality of final products This review aims to This means lining concepts and process solutions for any type of primary furnace, slag cleaning furnaces, electric arc furnaces (AC and DC), PS converters, anode furnaces, ladles and Lining Concepts for the Nonferrous Metal Industry RHI MagnesitaThis study aims to characterize alumina (Al2O3) based refractory materials applied on induction furnace lining based on its physical properties such as: the shape and grain size; chemical PHYSICAL CHARACTERIZATION OF ALUMINA (Al2O3) BASED Refractory material lining requires two steps for induction furnaces: Floor portion: Floor material is filled and compacted Wall portion: Liner form is positioned on the bottom refractoryInduction Furnace Lining and Industrial Vibrator Design Theseus
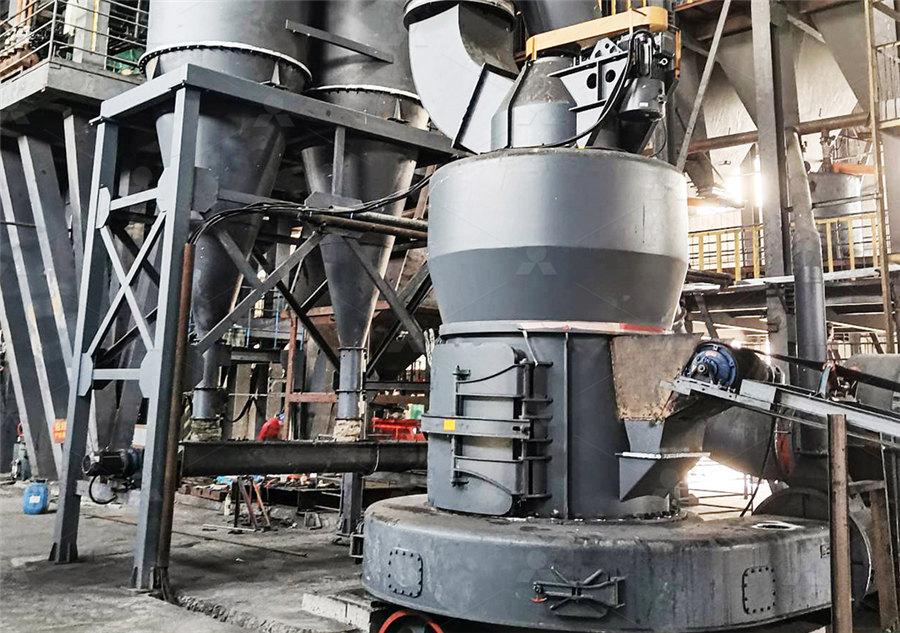
Induction Furnace Melting SpringerLink
2024年1月1日 Induction furnace melting is a process of melting metal by using electromagnetic induction to produce eddy current heating in metal materials in induction furnace, also called Operation and furnace area wise chart of refractories with their Standard Specifications are given below for ready reference: (Methods of Installation, furnace Heating ScheduleREFRACTORY LINING FOR INDUCTION FURNACE IDCOnlineCoral CXL General purpose lining with a wide melting temperature range Coral HB High duty, hard wearing lining suitable for most melting applications Coral SXL High duty for elevated temperatures Coral Vac High duty for high temperatures Coral SMC Incorporates complex chromes for improved slag resistance Coral 85 High performance lining for large furnaces Refractories for Induction Furnacesrequire alkaline cleaners, we will concentrate on this group Alkaline cleaners are specifically formulated (proprietary) chemical blends which consist of alkaline salts, wetting agents, and sequestering (chelating) agents Wetting Agents soap and synthetic detergents The Basics of Alkaline InProcess Cleaning for Metal Substrates
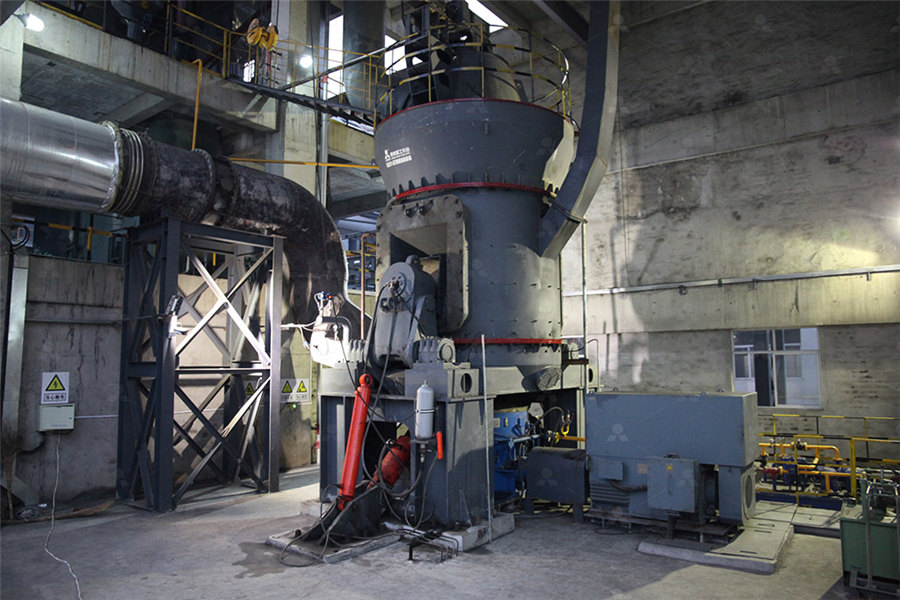
Predictive Furnace Refractory Maintenance Procedures to
2023年1月6日 Reduction of waste and recycling is becoming one of the main focuses in the metal processing industry Approximately, 3 million tons of waste refractory materials are generated annually in the United States by the ferrous, nonferrous, and glass industries []The used refractory linings constitute a major percentage of the industrial waste generated by 2015年3月2日 The term ‘basic’ refers to the refractory linings of the furnace which are made of alkaline materials (dolomite and magnesite) Refractory linings must have specific properties to withstand high temperatures, the corrosive action of the highly oxidized and basic slags, and abrasion during charging and blowingUnderstanding Steel Making Operations in Basic Oxygen Furnace2023年9月5日 The production of highperformance materials such as rare earth permanent magnets, rare earth hydrogen storage materials, rare earth luminescent materials, rare earth catalysts, hightemperature superconductors, and new metal materials like AlLi alloy, heatresistant Al alloy, superalloy, powder corrosionresistant stainless steel, powder highspeed Powder Metallurgy: A Comprehensive Guide for BeginnersHarper International's Powder Processing Furnaces Continuous High Temperature Kilns Calciners for Powders and Granular Materials Made in the USAPowder Processing Furnaces Thermal Systems From 500 to
.jpg)
Traditional Electric arc furnace steelmaking smelting process
2024年2月19日 The third phase of the smelting process of traditional Electric arc furnace steel making, refining and alloying in one furnace, including the melting period, oxidation period and reduction period In the furnace, the melting of scrap steel, dephosphorization, decarburization, degassing, etc of the molten steel must be completed Remove inclusions and raise 2016 D Ç î ñ Z r î ó Z î ì í ò U v } U Ì Z Z µ o ] U h 81 Table 4 Effect of K on CRI and CSR Sample Property (CRI/CSR) No Added K Medium K Content High K ContentEFFECT OF ALKALINE ELEMENTS ON COKE STRUCTURE UNDER BLAST FURNACE 2024年8月19日 This material has a good effect on a 16ton industrial frequency copper melting furnace in a copper material factory, and the furnace lining life exceeds three years (more than 700 furnaces)Refractory Materials for 30 tons Copper Melting Furnace — Lining Chemical Attack: There could be the possibility of a chemical reaction with the content at high temperatures So, the refractory material selected should be inert against them Installation: The refractory lining material must be easily available and installed The chosen refractory material must be quickly delivered to the required location during repair or maintenance timesWhat is a Refractory Lining? Materials, Selection, and Types of
.jpg)
Design, fabrication and properties of lightweight wear lining
2022年3月1日 As shown in Fig 1, a conventional refractory lining structure has a wear lining, safety layer, and an insulation layerThe wear lining resists erosion, wear, corrosion and thermomechanical loads of molten melts, while the insulation layer reduces the thermal transfer through refractory lining2019年11月1日 The article presents the procedure for qualifying brazing technology in a vacuum furnace on the example of stainless steel elements joined with copper filler material from the FNo group 105, in (PDF) Qualification of brazing procedure for furnace 2023年10月10日 Overview of Atomizing Metal Powder Production Atomization is a process used to produce metal powders with precise particle sizes and distributions for use in manufacturing Check furnace lining integrity: Annual: Training operators on proper startup ISO certification, established QC testing procedures, lot traceability The Atomizing Metal Powder Industry Additive Manufacturing Material2021年6月21日 Powder detergent spray drying process explained Modern powder detergents comprise a lightweight, freeflowing, puffed mass In those terms, compared to dry mixing and agglomeration processes, spray drying delivers a superior productPowder Detergent: Ingredients Manufacturing Process Explained
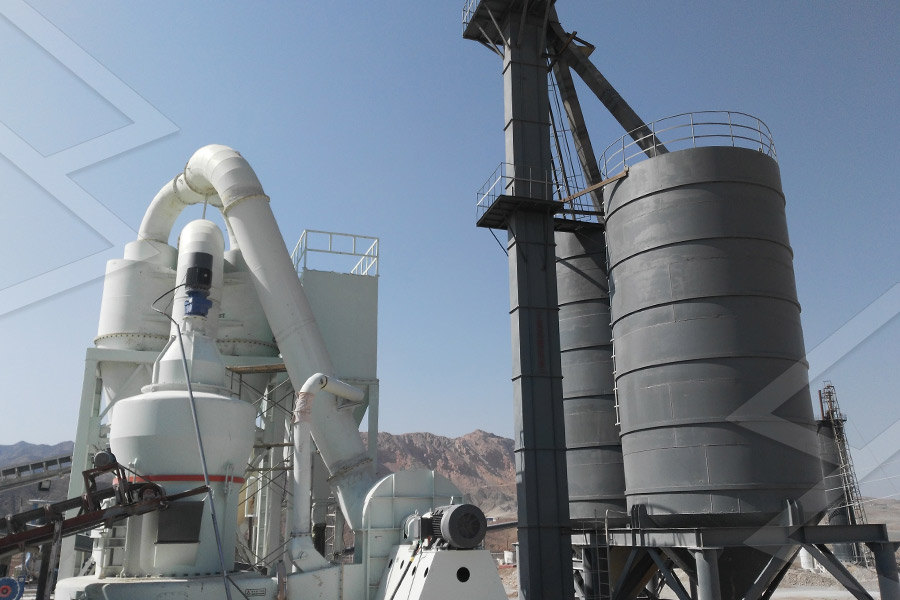
Five Tips for Achieving Furnace Lining Efficiency
Thermal Ceramics is a business of Morgan Advanced Materials Five Tips for Achieving Furnace Lining Efficiency By Steve Chernack, Morgan Advanced Materials lining without the proper expansion joints, the brick could grow and end up pushing the entire lining off the furnace wall Tip 5 – Proper installation is key to success2020年4月15日 Assuring that the furnace lining remains within the manufacturer specified limits requires careful usage of the lining during operation as well as inspection and monitoring procedures(PDF) Causes of the Quartzite Lining Destruction during Operation Use Case: Used in basic oxygen furnaces (BOF) and other alkaline steelmaking processes Key Features: • Superior resistance to alkaline slags • Wellsuited for environments with high basicity Applications: • Basic ramming mass is essential for furnaces where the steelmaking process involves the use of alkaline materials 3 Neutral Ramming Mass in Steel Industries Enhancing Melting Processes2017年5月30日 4 Select the right material for furnace rebuilds Some repairs identified by infrared thermology scanning can be too large to address online, and instead, the unit must be shut down for a furnace reline or process heater reline In this scenario, it is important to select the right refractory materials to facilitate a successful furnace rebuildEnsuring Effective Furnace Lining Efficiency Thermal Processing
.jpg)
ALKALINE CARBONATES IN BLAST FURNACE PROCESS
pact and alkali content in a selected blast furnace ALKALINE CARBONATES IN THE BLAST FURNACE PROCESS Alkalis enter blast furnaces in all parts of the blast furnace charge, but mainly in manganese ore and in metallurgical waste materials A large part of alkalis is brought by coke In operating conditions, the amountin induction furnace lining that are monolithic This dry powder must be compacted with homogenous density Because lining material’s lifetime, depends on this fact Refractory ramming process has been done by pneumatic vibrators operated manually so far Doing this process by hand cannot guarantee homogenous ramming which willInduction Furnace Lining and Industrial Vibrator Design2024年1月1日 In order to ensure electromagnetic induction efficiency, the wall of the crucible is thin, and the inner side bears the erosion and pressure of hightemperature molten steel The furnace lining of coreless induction furnace (crucible) has two types: acidic and alkaline Acid furnace lining is made of quartz sand with silica content more than 98%Induction Furnace Melting SpringerLinkHigh duty lining developed to withstand elevated temperatures and retain a good level of powder at the back face Ceramic: 1700* 1750† Coral SMC: Incorporates complex chromes for improved slag resistance Ceramic: 1700* 1750† Coral Coreless Induction Furnace Linings Capital
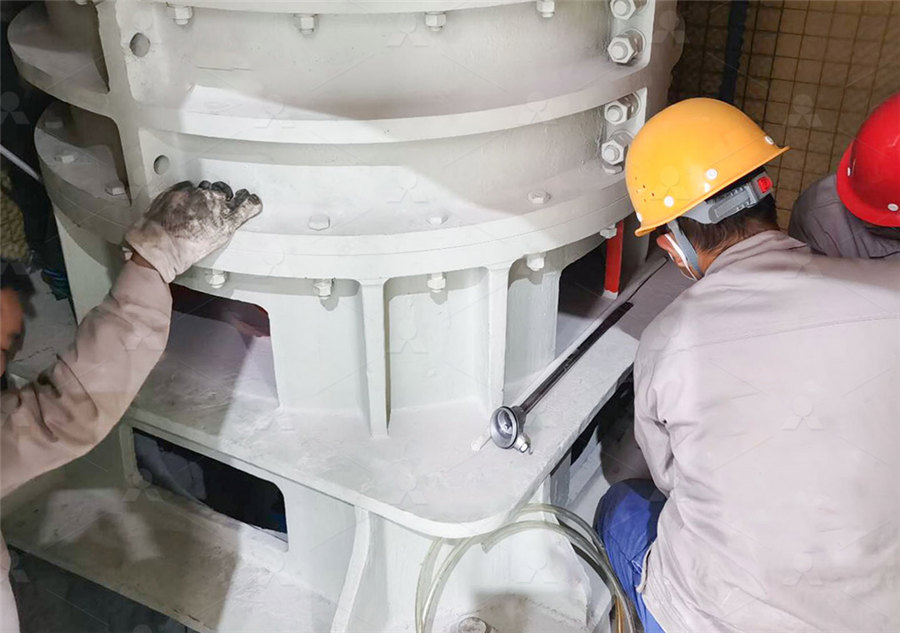
Refractory Lining of the Electric Arc Furnace –
2020年5月6日 Refractory Lining of the Electric Arc Furnace satyendra; May 6, 2020; 0 Comments ; AC EAF, DC EAF, EAF, EBT, Fettling, guniting, hearth, magnesite, Monolithic lining, roof, Taphole,; Refractory Lining of the Electric Lining materials for coretype induction furnace The cored or channel induction furnace lining should be made of refractory castables that are resistant to corrosion, and erosion resistance and have high chemical stability Usually, lowcement refractory castables are made from fused corundum aggregate, added with an appropriate amount of sintered alumina fine powder, and Induction Furnace Refractory AGRM Refractories2023年7月5日 Coreless induction furnace is one of the most widely used equipment in the steelmaking sector, while the lining refractory are the key factors in determining the lifetime of the induction furnace The multiphysics field dominates the operating conditions of the lining refractory which can be wellstudied using numerical simulation techniques Based on the Effects of induction furnace conditions on lining refractory via 2024年5月16日 To learn more about the manufacturing process of detergent powder, refer to our article on detergent powder manufacturing process Production Process for Detergent Powder The production process for detergent powder involves several methods to create highquality products that effectively clean and remove stainsUnderstanding the Detergent Powder Manufacturing Process
.jpg)
Materials selection of furnace linings with multicomponent refractory
2020年3月1日 Materials selection of multicomponent systems is a challenging task, which is usually not properly tackled in furnace linings (FL) design In an attempt to generate a systematic approach to select FL ceramic materials, an evolutionary screening procedure (ESP) is proposed in this paper, where a multiobjective genetic algorithm coupled with a finite element model 2013年12月1日 In FY20, India’s steel production was 109 MT, and it is the secondlargest steel producer on the planet, after China India’s per capita consumption of steel was around 75 kg, which has risen Technological Changes in Blast Furnace Iron Making in India 2021年1月26日 (3) The lining material is required to have a low thermal conductivity and small thermal expansion, so that the tundish lining has a certain degree of heat preservation and good integrity (4) It is required that the lining material has little pollution to the molten steel during the pouring process to ensure the quality of the molten mon problems of steelmaking tundish refractory material 2024年9月25日 ISI Mark Certification is mandatory to manufacture and sell products that are listed in the Product Certification Scheme of BIS Check the mandatory Products List, Benefits, Procedure, Documents, cost and more Get BIS certified by ISI Mark Certification Benefits Procedure, Documents, Fees Aleph INDIA
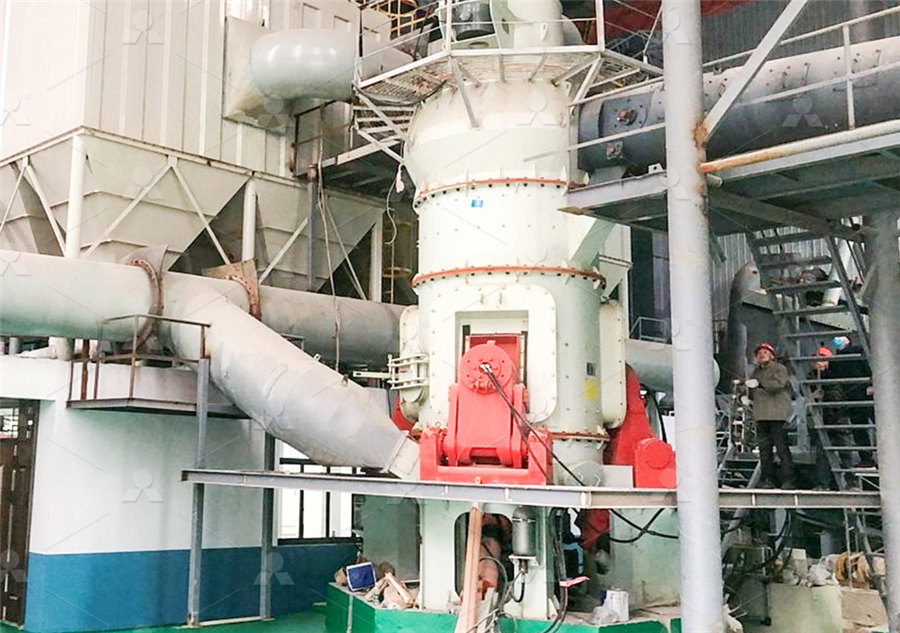
How to improve the induction furnace lining life
2020年10月19日 According to the raw materials and smelting furnace need different acid and alkaline divided into lining, our factory is using acidic lining Play lining, is to use the material such as quartz sand, the furnace wall do a layer 2019年7月19日 Carbon may also be introduced to a much smaller extent from fluxing materials and other process additives that are charged to the furnace Using the default values in the IPCC Guidelines for iron (004) and steel (001) for the fraction of carbon gives an emission factor of 011 tCO 2 /tcs for carbon removed from the iron as CO 2 Basic Oxygen Furnace: Most Efficient Technologies for Greenhouse 2021年5月15日 Basic oxygen furnace slag (BOFS) is a waste material generated during the steelmaking process and has the potential to harm both the environment and living organisms when disposed of in a landfillAlkaline Activation of Basic Oxygen Furnace Slag Modified 2019年6月15日 Material losses caused by having a powder bed can be avoided by using blown powder processes (reviewed by Thompson et al [20]), which deposit the powder at the same time as it is being melted These also have material losses because not all the powder reaches the melt pool, but the process only uses the material incorporated into the workpieceEnergy and material efficiency of steel powder metallurgy
.jpg)
Rotary Furnaces: Advanced Materials Processing and Applications
Inert atmospheres prevent oxidation or chemical reactions during the heat treatment process Advantages of Rotary Furnaces Compared to conventional furnaces, rotary furnaces offer several advantages, including: High Production Capacity: Rotary furnaces can process large volumes of material, making them suitable for highvolume production The lining practice best suited to a particular furnace depends upon the capacity and design of the furnace, operation practice adopted during making of a heat, and furnace output For successful and consistent performance of the lining, the important aspects are (i) use of proper grade and quality of the lining material, (ii) careful and systematic lining practice, and (iii) consistency in Induction Furnace and Steelmaking IspatGuru2020年6月10日 Globally, steel products have been mainly manufactured via primary steelmaking process that constitutes two major routes These are integrated Blast Furnace–LD Process/Basic Oxygen Furnace Route (BF–LD/BOF) and Directly Reduced Iron–Electric Arc Furnace (DRI–EAF) steelmaking practiceIron and SteelMaking Process SpringerLink2024年3月4日 Blast furnace dust (BFD) is the solid powder and particulate matter produced by dust removal process in ironmaking industry The element composition of BFD is complex, and a direct return to sintering will lead to heavy metal enrichment and blast furnace lining corrosion In recent years, the application of BFD in wastewater treatment has attracted widespread Review in application of blast furnace dust in wastewater
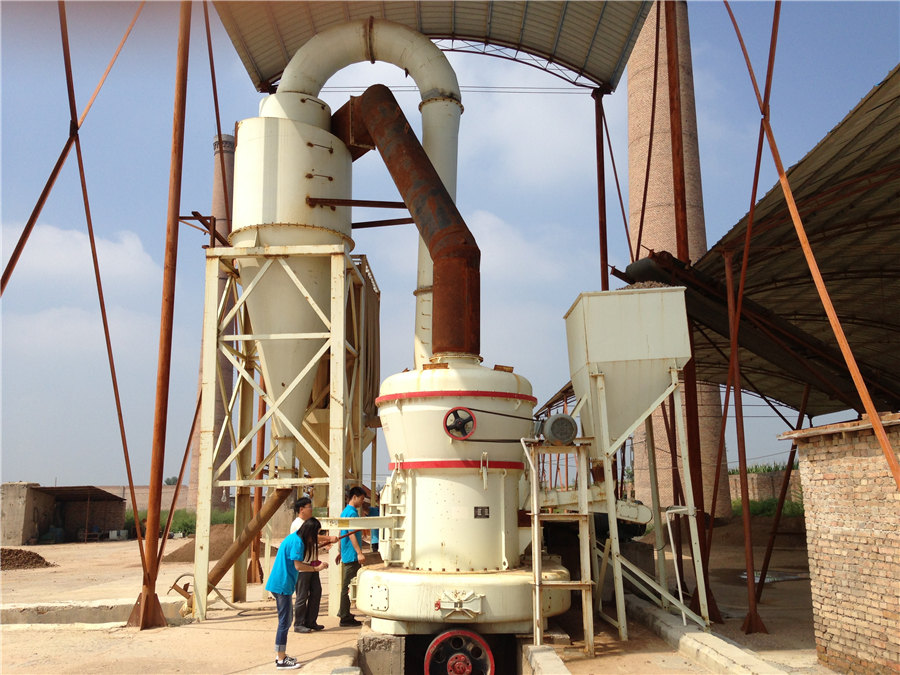
Effects of induction furnace conditions on lining refractory via
boundary conditions are shown in Table 1 The furnace lining material in the model is based on quartz ramming material and the furnace material is based on steel Specic parameters are shown in Table 2 Some of the parameters in Table 2 are taken from other works [7 , 19–21] The global setup of mesh for the solution domain is free