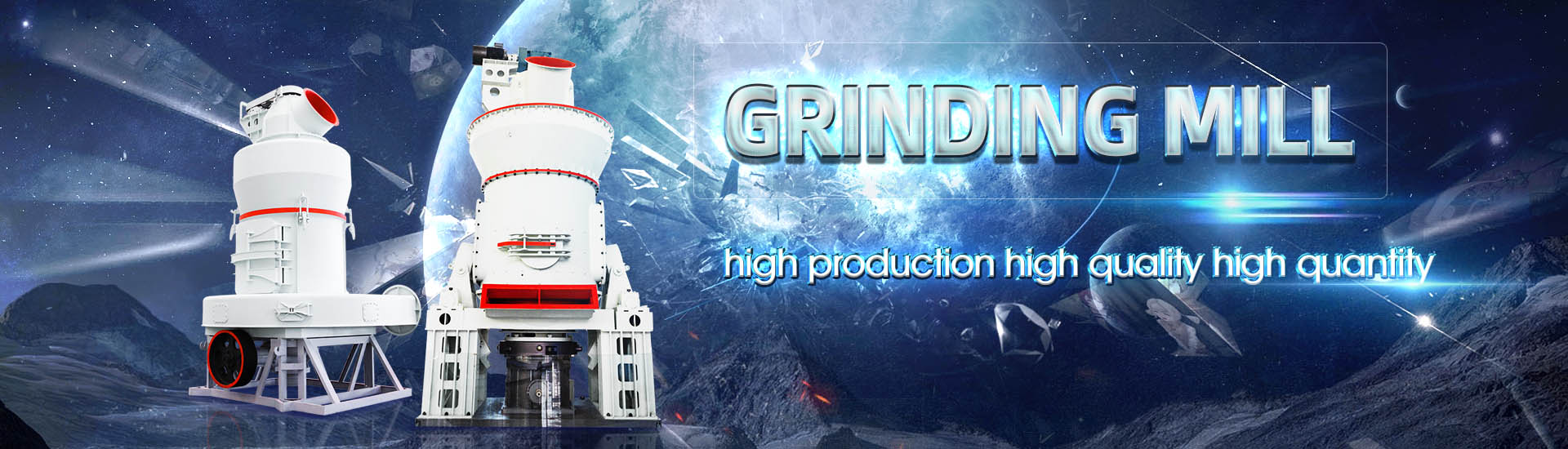
Reasonable configuration of ball mill steel balls
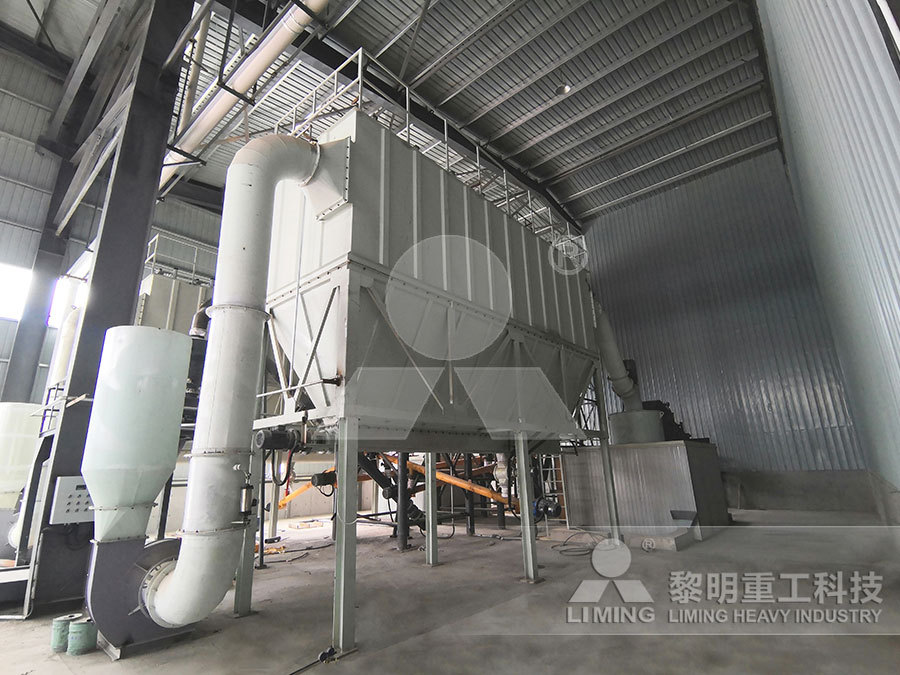
Ball Mill Steel Balls: Quality And Gradation JXSC Mineral
2024年2月19日 Reasonable selection of the gradation of ball mill steel balls is an indispensable measure to improve the output and quality of ball mills Let’s look at how to obtain a reasonable gradation of ball mill grinding body steel This standard applies to steel grinding balls produced by rolling, forging, stamping and used for raw materials and materials grinding in ball mills 2 NORMATIVE REFERENCES STEEL MILLING BALLS FOR BALL MILLS Energosteel Grinding 2013年8月3日 In Grinding, selecting (calculate) the correct or optimum ball size that allows for the best and optimum/ideal or target grind size to be achieved by your ball mill is an important thing for a Mineral Processing Engineer AKA Calculate and Select Ball Mill Ball Size for Optimum This standard is applied to milling balls with diameter of 15120 mm made of low alloy carbon steelor alloy carbon steel using methods of cogging, beating out and pressing and used forSTEEL MILLING BALLS FOR BALL MILLS Specifications
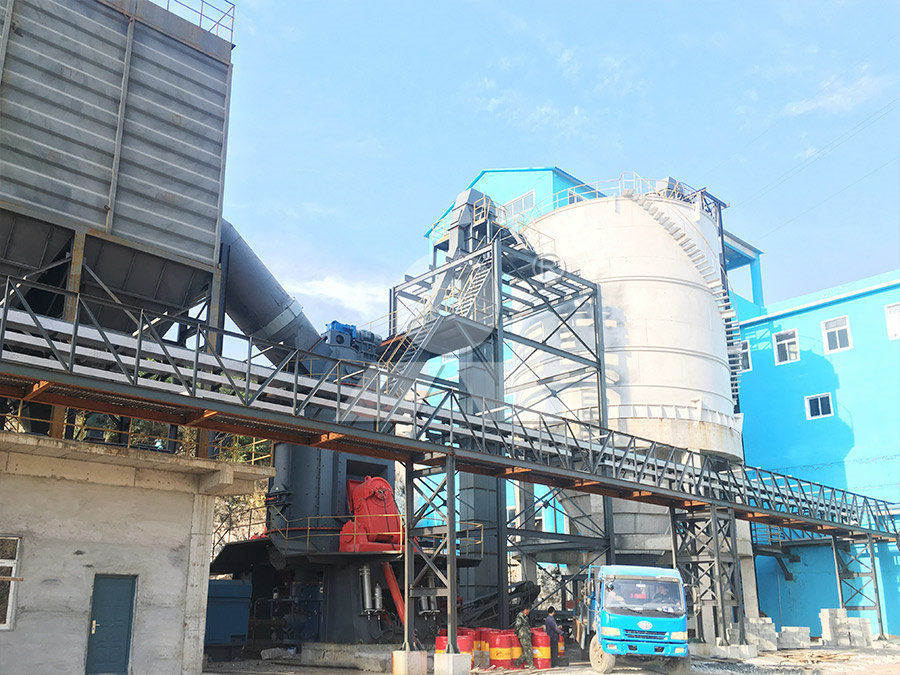
Ball mill steel ball configuration ALPA Powder Equipment
2022年1月13日 Reasonable selection of the gradation of ball mill steel balls is a measure to improve the output and product quality of the ball mill The basic principles of ball mill steel ball The success of a ball milling application depends on the correct selection of accessories and process parameters This includes jar sizes, jar materials, ball sizes, number of balls, particle Three rules for the optimum ball mill setup RETSCHballs depend on the microstructure developed in the steel by carefully selected heat treatment variables, specifically designed for each alloy The control variable of the finished product – MCGBLMIDTS20 Version 20 Ball Milling Technical2013年9月1日 It was found that the optimum composition depends on various factors, including the feed size, the product size, the mill diameter and the breakage parameters In all cases, (PDF) Optimum choice of the makeup ball sizes for

Grinding in Ball Mills: Modeling and Process Control Sciendo
There are three types of grinding media that are commonly used in ball mills: • steel and other metal balls; • metal cylindrical bodies called cylpebs; • ceramic balls with regular or high Ball mill optimisation As grinding accounts for a sizeable share in a cement plant’s power consumption, optimisation of grinding equipment such as ball mills can provide significant cost BALL MILLS Ball mill optimisation Holzinger Consulting2012年6月1日 Steel and other metal balls are the most frequently used grinding media with sizes of the balls ranging from 10 to 150 mm in diameter [30] Cylpebs are slightlyGrinding in Ball Mills: Modeling and Process Control2021年6月29日 The rotating mill is filled with different steel balls of sizes 25 mm, 40mm mill configurations like vertical mils and high speed Taking a Φ549 × 883 m ball mill as the research Effects of Mill Speed and Air Classifier Speed on
.jpg)
(PDF) Failure of Steel Grinding Balls ResearchGate
PDF On May 1, 2019, N A Shaburova published Failure of Steel Grinding Balls Find, read and cite all the research you need on ResearchGate414 Also the balls of the 2nd, 3rd, and 4th groups can be manufactured from low alloy steel and instrument steel in accordance with GOST 5950 415 The balls of the 5th group are manufactured of steel, the carbon equivalent of which shall be no less than: 075% for balls with rated diameter of 1560 mm provided that carbon weight STEEL MILLING BALLS FOR BALL MILLS SpecificationsGRINDING STEEL BALLS FOR BALL MILLS Specifications Date of validity: 2016 07 – 01 1 FIELD OF APPLICATION This standard applies to steel grinding balls produced by rolling, forging, stamping and used for raw materials and materials grinding STEEL MILLING BALLS FOR BALL MILLS Energosteel Grinding Media Ball 2017年4月29日 Miami Copper Co’s plant after the mill had been operating for a year with a ball load of 14,800 lb (6713 kg) which was maintained by the addition of 400 lb (181 kg) of 2in (508mm) steel balls dailyGrinding Media Wear Rate Calculation in Ball Mill
.jpg)
Wearresistant Forged Steel Ball and Casting Steel Ball of Ball Mill
Ball Mill Steel Balls Diameter:20150mm(+2mm/1mm tolerance) Certificates:ISO 9001:2000, ISO 9001:2008, ISO9001, ISO14001, ISO18001 Customized: Customizable Hardness: HRC6065(forged steel ball), 45HRC58HRC(casting steel ball) Breakage rate: 1%max in normal and correct operating conditions Production capacity:150, 000 Mt/Yearball mill and ball charging systems australia Grinding is the process of achieving particle size reduction through attrition and compressive forces at the granular level The grinding media in a ball mill is typically steel or ceramic balls of varying sizes, depending on the feed size, work index of the ore and the size reduction and distribution required in the dischargeBALL MILL AND BALL CHARGING SYSTEMS AUSTRALIAReason: This is a common problem mining ball mills face, resulting in low productivity and low ore processing efficiency One reason may be the improper design of the grinding chamber, which affects the flow of materials and reduces grinding efficiency Additionally, worn or damaged liners can hinder the grinding process by reducing the effective impact between the ball and the Inventory Of Common Faults And Solutions Of Mining Ball MillBall mill steel balls is an important part of the ball mill, its main function is to carry out the grinding operation in the ball mill, and the material is crushed into the required size Ball mill balls usually have the advantages of high hardness, high wear resistance, high precision, high strength, and high tensile strength, and can withstand greater impact force and pressure in the high Ball Mill Balls Manufacturing Of High Quality Ball Mill Ball
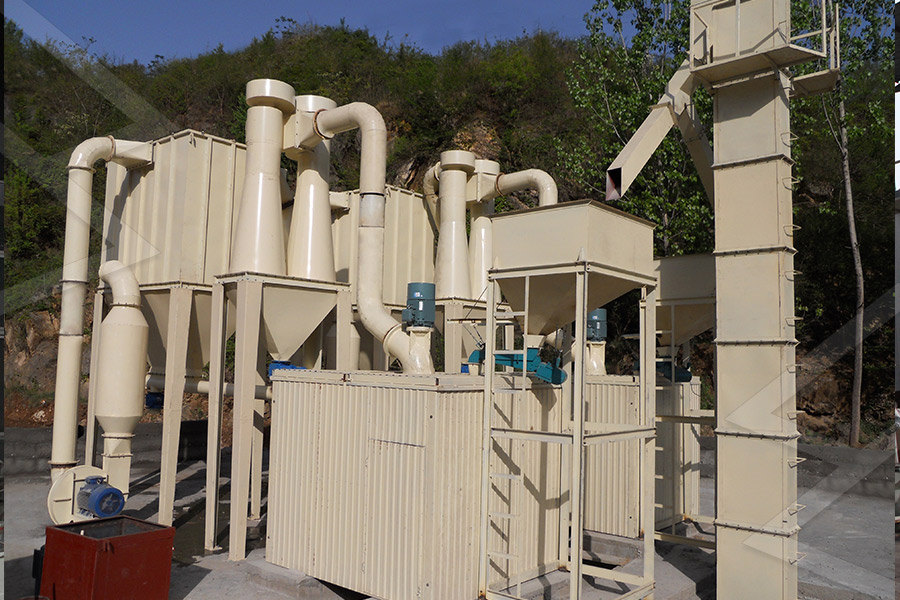
Across International Stainless Steel Grinding Balls for Lab Ball Mill
Across International Stainless Steel Grinding Balls for Lab Ball Mill Grinding Media available in different size and Polished stainless steel grinding balls for planetary and high energy ball mills Grinding jar ball configuration 50ml 100ml 250ml 500ml 1000ml Ball size/qty (pcs) 6mm 50 100 280 500 1000 10mm 8 16 40 100 2024年2月27日 In addition, the ball mill steel ball also has high chromium cast iron, high carbon and highmagnesium alloy steel, and other materials Processing of ball mill balls The ball mill balls on the market can be divided How To Choose Steel Balls For Ball Mill? Grinding 2024年7月9日 Significance of ball mill balls The ball mill steel balls are crucial consumables for the grinding plant They need replenishing at intervals to maintain grinding quality and rate The number of balls in a ball mill Different sizes of mill balls2022年1月13日 Reasonable selection of the gradation of ball mill steel balls is a measure to improve the output and product quality of the ball mill The basic principles of ball mill steel ball grading are: (1) Under normal circumstances, the larger the diameter of the mill, the larger the impact force, so the diameter of the steel ball is relatively small;Ball mill steel ball configuration ALPA Powder Equipment
.jpg)
Method of Steel Grinding Ball Proportioning and Example
2023年2月15日 A beneficiation plant in Singapore loads balls into a ϕ 1500mm×3000mm wet grid type ball mill, determines the filling rate ϕ = 50%, and selects cast steel grinding balls δ = 45 t/m 3 The ball mill processes the mediumhard ore 1 See Table 1 for the sieving analysis results of all the ore samples from a ball mill Table 1duction technology Significant increase in ball quality requires the creation of specialized rolling systems The fundamental principles to be adopted in creating such systems are reviewed Keywords: grinding balls, ball mills, ball production, ball quality, ballrolling systems DOI: 103103/S20115Improving the Quality of Steel Grinding Balls2021年6月9日 Grinding balls for ball mill, mainly includes High, medium , low chromium alloy steel balls and High, medium , low aluminum ceramic ballsetcThe diameter of the steel balls is has 100mm , No need to add too small balls The How to add load steel balls of ball mill ? Reduce wear damageUnderstanding Mill Ball Materials 1 Steel Balls Steel balls are the most common type of mill balls used in ball milling processes They are made of steel and come in different sizes and shapes, depending on the application Steel balls are very durable, have high density, and are resistant to What are Mill Balls Made of? ball mills supplier
.jpg)
Optimization and transformation of 300MV units steel ball coal mill
best proportion of adding balls is ø60:ø40:ø30=4:3:3, in order to ensure the filling coefficient of the steel ball in the coal mill, the steel ball is preliminarily added 58T to carry out the appropriate areas The internal load, for the original and current configuration, is represented schematically in Fig (3) 90º 270º 180º 0º θ T θS = 51° = 217° 90º 270º 180º 0º θ T θS = 29° = 252° (a) current configuration (b) original configuration Figure 3 Load schemes for the current and original configurations of the STRUCTURAL INTEGRITY EVALUATION OF A BALL MILL2019年11月7日 Comprehensive treatment,we should have a test on the 300 MV unit steel ball coal mill pulverizing systemAt the same time,analyze the main operating parameters before modificationTransform the Optimization and transformation of 300MV units steel ball coal mill RoM ball mill is pebble ported most of the steel balls can discharge through the pebble ports and cause logistic problems of separating steel balls from rocks prior to sending the pebbles for RoM BALL MILLS A COMPARISON WITH AG/SAG MILLING
.jpg)
Ball Mill Design/Power Calculation 911Metallurgist
2015年6月19日 The basic parameters used in ball mill design (power calculations), rod mill or any tumbling mill sizing are; material to be ground, characteristics, Bond Work Index, bulk density, specific density, desired mill 2023年1月2日 1 To deal with ore with large hardness and coarse particle size, a greater impact force is required, and larger steel balls need to be loaded, that is, the harder the material, the larger the diameter of the steel ball; 2 The larger the diameter of the mill, the greater the impact force, and the smaller the diameter of the selected steel ball; 3How to add steel balls to the ball mill is suitable, and how to For ball mill, reasonable ball loading not only affects the improvement of grinding efficiency and productivity, If the maximum diameter of a billiard ball mill is 100 mm in the multistage ball distribution, steel balls with diameter of 90 mm should be selected when twostage ball distribution is carried out (2) How to choose the ball loading and loading ratio of ball mill?2024年8月8日 Unlock the secrets to ball mill efficiency with our comprehensive guide on choosing the right grinding media Learn how material composition, size, shape, Steel balls, recognized for their robustness, are better suited for heavyduty milling tasks where material hardness is a significant factorBall Mill Success: A StepbyStep Guide to Choosing the Right
2FD{P}PC]854]XQ.jpg)
Recommended Ball Mill Speed Liner Configuration
2017年10月25日 In practical terms, one must assume some mill diameter, usually about 150 mm (6 inches) less than the mill inside shell or nominal diameter, that allows for the difference between the mill inside diameter and the location of the centre of gravity of the ball, as well as an assumed liner condition midway between new and fullyworn2022年3月14日 Is the grinding efficiency of the ball mill high?The key is to see the steel ball configuration!#ballmill: https://bitly/3w7EHDe#ballginder【Contact JXSC getBall mill grinding efficiency lies in the configuration of the steel ballsThe Technique Of Adding Steel Balls To The Ball Mill in The Beneficiation Equipment Call Us: 86 : grindingballsmedia@163 Language English; it is necessary to carry out reasonable ball compensation and low wear compensation Previous: Forged Steel Balls Production Process Next: Select The Quality Index Of Grinding The Technique Of Adding Steel Balls To The Ball Mill in The 2024年8月1日 Common choices for ball mill media include ceramic balls, flint pebbles, and stainless steel balls Each type of media has different properties and advantages depending on the specific needs of the black powder production process Highquality ball mill media for black powder is essential for achieving the best resultsEffective Ball Mill Media for Superior Black Powder Production
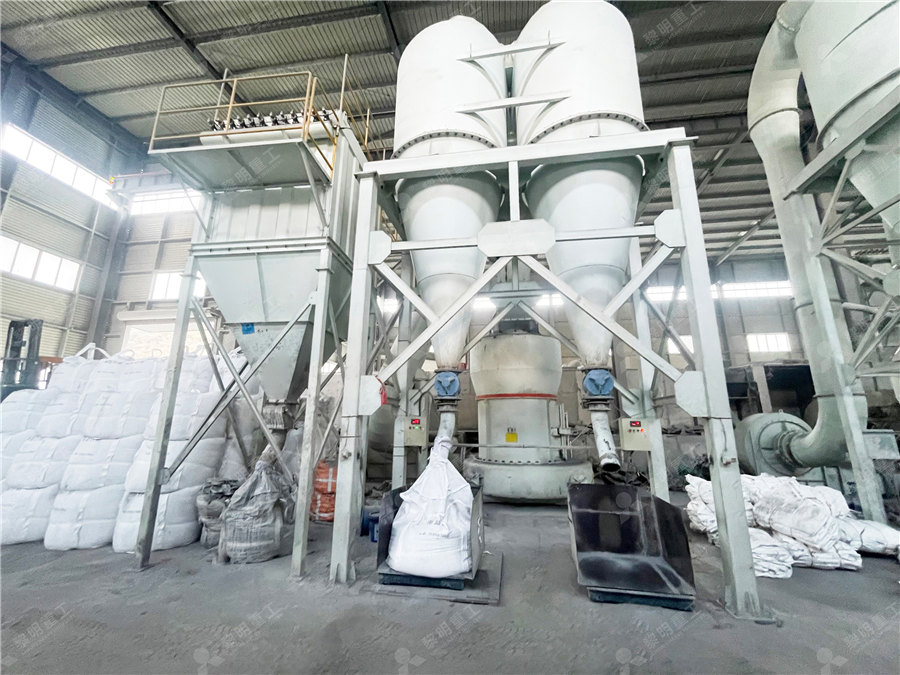
(PDF) Grinding Media in Ball MillsA Review
2023年4月23日 In the ball mill, friction is formed due to the difference between surfa ces of adjacent grinding balls in the abr asion zone, whilst impact is due to rockball impact and ba llball impact in the 2019年12月19日 Ball mill steel balls mainly include: cast iron balls, forged steel balls, rolled steel balls, and the diameter of ball mill steel balls usually is Φ20mm ~ Φ120mm, and the maximum steel ball diameter used by super large ball mill How Many Balls in a Ball Mill? JXSC MachineSteel balls Steel balls are one of the most widely used grinding media in cement ball mills, their diameters can range from 20mm to 150mm according to different grinding requirements In a cement ball mill, generally, φ50100mm steel balls Ball Mill Grinding Media Steel Balls for Ball Mills2023年3月8日 6 Control the speed of the ball mill Under the condition that the steel balls of the ball mill are configured and practical, the rotating speed of the ball mill increases, and the steel balls of the cylindrical bearings will drop into piles; When the speed of rotation increases as necessary, the power exceeds the maximum, the grinding effect is the best, and the ball Steel Balls Consumption Ball Mill Effect JXSC Machine
.jpg)
Analyzing the influence of lifter design and ball mill speed on
2023年10月30日 Ball mills are the foremost equipment used for grinding in the mineral processing sector Lifters are placed on the internal walls of the mill and are designed to lift the grinding media (balls 2023年10月27日 The ball mill is a rotating cylindrical vessel with grinding media inside, which is responsible for breaking the ore particles Grinding media play an important role in the comminution of mineral ores in these mills This work reviews the application of balls in mineral processing as a function of the materials used to manufacture them and the mass loss, as A Review of the Grinding Media in Ball Mills for Mineral 2018年2月1日 In another study to investigate ball size distribution on ball mill efficiency by Hlabangana et al [50] using the attainable region technique on a silica ore by dry milling, a threeball mix of Effect of ball and feed particle size distribution on the milling Rotation: The ball mill rotates around a horizontal axis, partially filled with the grinding mediumAs the mill rotates, the grinding media cascade and tumble over each other, impacting the material being processed Impact and Attrition: The grinding media in the ball mill impact and grind the material, causing it to reduce in sizeThe impact of the balls creates a lot of heat which can be China Ball Mill Manufacturers Suppliers Factory Customized Ball Mill
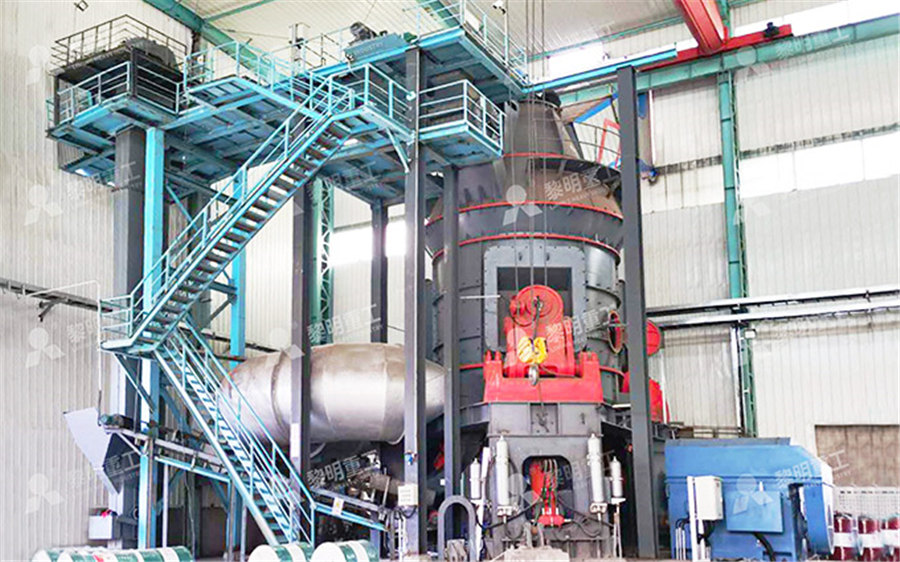
How to Determine the Ratio of Grinding Balls in a Ball Mill
2023年10月23日 Learn about weight configurations, ideal diameters, and mass ratios for efficient grinding processes Home Polyethylene ball mill + zirconia / alumina / agate grinding balls 3 Nylon ball mill + stainless steel / zirconia / alumina / agate grinding balls 4 Polyurethane ball mill + zirconia /alumina / agate grinding balls 52023年6月19日 The overflow type ball mill belongs to the nonforced high material level ore discharge, and the discharge speed is slow The mineral material stays in the machine for a long time, so its overgrinding phenomenon is serious 6 Different motion state of the steel ball The speed of the gridtype ball mill is high, and the steel balls are droppedBattle of the Mill Grid Ball Mill VS Overflow Ball Mill