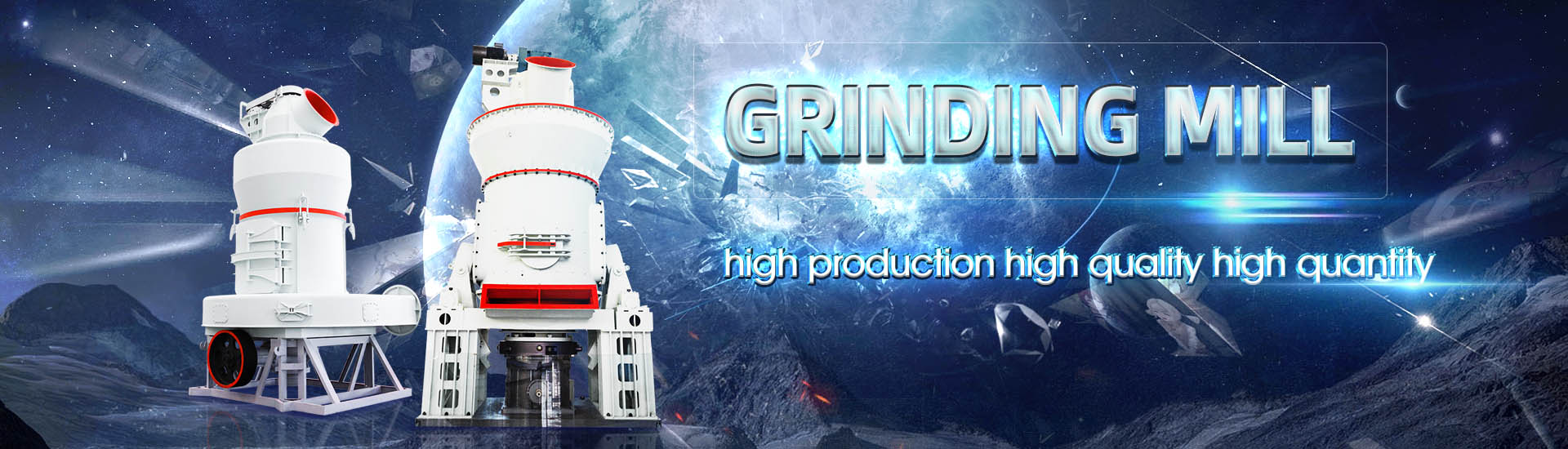
3 8x13m ordinary closedcircuit cement mill
.jpg)
38 * 13m Ball Mill for Cement Plant China Ball Mill and Cement Mill
38 * 13m Ball Mill for Cement Plant, Find Details and Price about Ball Mill Cement Mill from 38 * 13m Ball Mill for Cement Plant Jiangsu Pengfei Group Co, Ltd Print This Page Home 2023年9月1日 Fullscale closedcircuit cement ball milling was modeled using a true unsteadystate simulator (TUSSIM), based on a transient cellbased population balance model (PBM) Modeling of closedcircuit ball milling of cement clinker via a PBM When transferring to closed circuit а mill size 26×13 m at a constant quality cement (3000 cm2pg) capacity grinding unit was increased from 25 to 38 tph while reducing the specific Analysis of the efficiency of the process in closed circuit ball millsOperation and Elements of a ClosedCircuit Ball Mill System Cement ball mills typically have two grinding chambers The first chamber is filled with larger diameter grinding media andlined OPTIMIZATION OF CEMENT GRINDING OPERATION IN BALL MILLS
.jpg)
Comparison of the overall circuit performance in the cement
2011年2月1日 In this study, in order to evaluate and compare the performances of different cement grinding technologies using the ball milling and high compression technology, Abstract Based on a dynamical model of the grinding process in closed circuit mills, efficient efforts have been made to optimize PID controllers of cement milling The process simulation OPTIMIZING THE CONTROL SYSTEM OF CEMENT MILLING: For mills producing several types of cement, we optimize for the main type It is recommended to start first with the coarse grading Mills having non classifying liners should be limited by three Ball charge optimization INFINITY FOR CEMENT EQUIPMENTThe macrostructural models describing the material flows in closed circuit ball mill grinding include the rules of mass flow for steadystate, the nonlinear character of the mill, and the dead time 5 MATERIAL FLOW MODELS OF CLOSEDCIRCUIT GRINDING
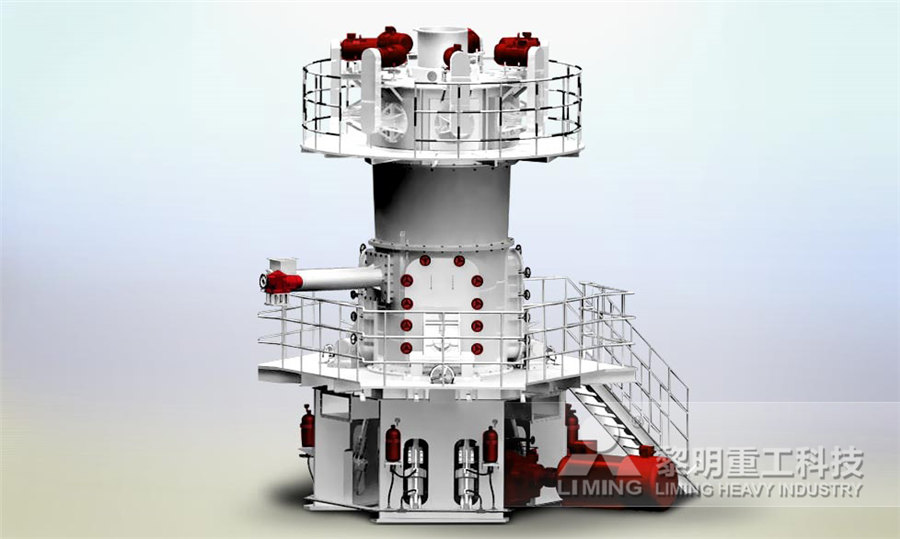
Predictive Control of a Closed Grinding Circuit System in Cement
Abstract—This paper presents the development of a nonlinear model predictive controller (NMPC) applied to a closed grinding circuit system in the cement industry A Markov chain Open and closed circuit dry grinding of cement mill rejects in a pilot scale vertical stirred mill CC Pilevneli*, S Kızgut, I˙ Torog˘lu, D C uhadarog˘lu, E Yig˘itOpen and closed circuit dry grinding of cement mill rejects in a 2021年2月3日 Coarse Return Prediction in a Cement Industry’s Closed Grinding Circuit System through a Fully Connected Deep Neural Network of particles in the milling circuit to control a cement mill betterCoarse Return Prediction in a Cement Industry’s Closed Grinding Of course, even if we set a more appropriate cement fineness, it is difficult to change the current situation that the flow velocity in the opencircuit ball mill is only 1/21/3 of that in the closedcircuit ball mill with the same specification, Ball Mill In Cement Plant Cement Ball Mill AGICO
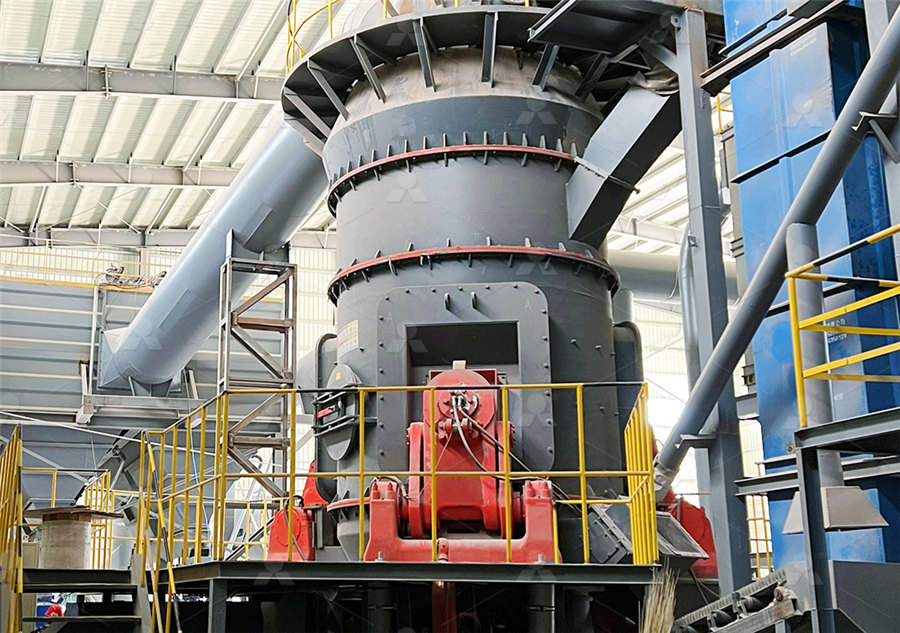
Closed Circuit Grinding VS Open Circuit Grinding
2016年10月12日 Closed circuit grinding system See the advantages of closed circuit grinding The method of installing a bowl classifier to overcome the difficulty is shown in Fig 27 This circuit is usually adopted in modern practice, but with a bowl instead of a straight classifier, if necessary, in the closed circuit of the secondary ball millPredictive Control of a Closed Grinding Circuit System in Cement Industry Luis I Minchala1;3, Member, IEEE, Youmin Zhang2, Senior Member, IEEE, Luis E GarzaCastan˜on´ 3, Member, IEEE Abstract—This paper presents the development of a nonlinear model predictive controller (NMPC) applied to a closed grinding circuit system in the cement Predictive Control of a Closed Grinding Circuit System in Cement Optimization of a Fully Airswept Dry Grinding Cement Raw Meal Ball Mill Closed Circuit Capacity With the Aid Free download as PDF File (pdf), Text File (txt) or read online for free This document discusses optimizing the production capacity of a fully airswept industrial scale twocompartment cement ball mill through simulation The mill has two compartments, with the first Optimization of A Fully AirSwept Dry Grinding Cement Raw Meal Mill Types Diameter x Length(m x m) Support Type Drive Type Motor Power(kW; UDCM 32130: Ø 3,2 x 13,0: Trunnion Bearing: Side Central: 1600: UDCM 38130: Ø 3,8 x 13,0Cement Mill Dal Machinery
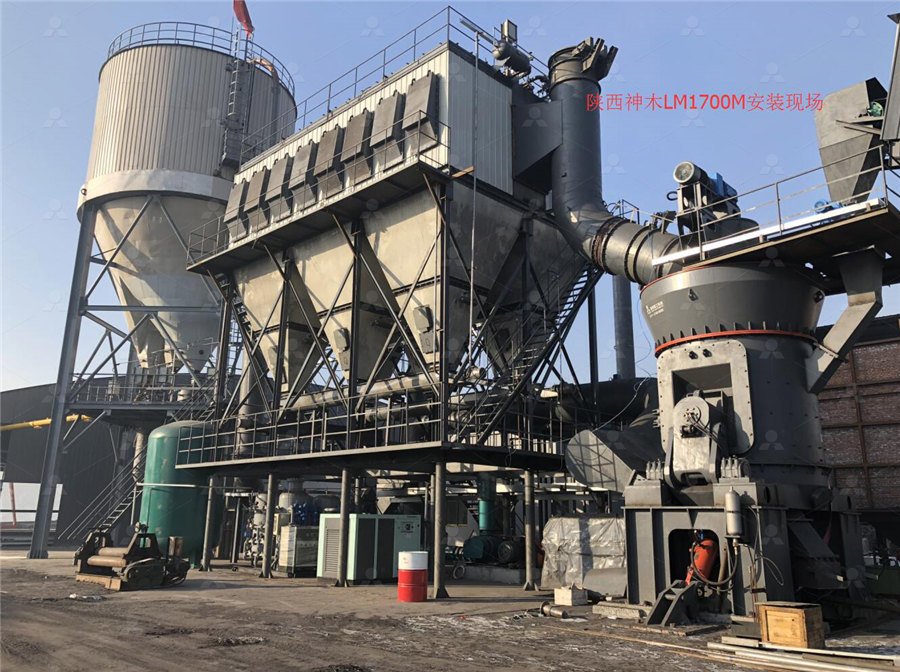
Modeling of closedcircuit ball milling of cement clinker via a
2023年9月1日 Closedcircuit ball mills have been operated for cement milling for decades [[7], [8], [9]]Fig 1 shows the process flow of a closedcircuit, twocompartment cement ball mill The closedcircuit operation helped to reduce overmilling of particles [10], resulting in lower specific power consumption [11] in comparison with opencircuit operation, where the ball mill is Cement Ball Mill Description: MQ series ball mills are mainly used in grinding operations in mining, cement, refractory, chemical and other industries According to the discharging method, 8 closed circuit: 163: 224: YRKK9008: 3150: MFY320: 47 : Cement Ball Mill StructureBall Mill for Cement Grinding Process2017年10月12日 Some investigations observed that VRM installation in grinding saves 30% of cement mill energy with ease of control and reduces the mill startup/shut down durations [1,2,3,4, 5] Predictive Control of a Closed Grinding Circuit System in Cement Cement ball mill is a cement grinding machine used in the cement production line for cement clinker grinding Ordinary Portland Cement Manufacturing; Sulphate Resisting Cement Manufacturing; closecircuit: 28~32: ≤25: 183: 80: 1000: Cement Ball Mill Cement Grinding Machine
.jpg)
EnergyEfficient Technologies in Cement Grinding
2016年10月5日 In this chapter an introduction of widely applied energyefficient grinding technologies in cement grinding and description of the operating principles of the related equipments and comparisons over each other in Request PDF On Apr 1, 2013, Alex Jankovic and others published Closed circuit ball mill – Basics revisited Find, read and cite all the research you need on ResearchGateClosed circuit ball mill – Basics revisited Request PDFPredictive Control of a Closed Grinding Circuit System in Cement Industry Luis I Minchala1;3, Member, IEEE, Youmin Zhang2, Senior Member, IEEE, Luis E GarzaCastan˜on´ 3, Member, IEEE Abstract—This paper presents the development of a nonlinear model predictive controller (NMPC) applied to a closed grinding circuit system in the cement Predictive Control of a Closed Grinding Circuit System in Cement 3 CASE STUDY A 15 mio t/a cement plant is having a closed circuit ball mill for cement grinding: The mill has been operating with satisfactory performance interms of system availability and output, however power consumption was on higher side 31 System Description Mill Rated capacity 150 t/h OPC at 2800 blaine I chamber linersPROCESS DIAGNOSTIC STUDIES FOR CEMENT MILL
.jpg)
Soft Constrained MPC Applied to an Industrial Cement Mill Grinding Circuit
and cement mill grinding circuits (Sahasrabudhe et al, 2006; Stadler et al, 2011; Samad and Annaswamy, 2011) In the following, we review the approaches to control cement mill grindFigure 3: Cement mill grinding circuit ing circuits van Breusegem et al (1994, 1996); Van Breusegem et al (1996) and de Haas et al (1995) developed an LQG conIn 1904, Krupp produced a selfcontained cement mill using a ball mill and their version of the Askham separator in closed circuit, but I think this was never used in Britain However, from the mid 1890s, ball mills were used in combination with tube mills (see below) and this setup became the normal cement milling installation until 1920Cement Kilns: Size Reduction and Grinding2023年9月1日 A recently developed process simulator, TUSSIM, for a fullscale cement ball mill [4] was augmented with a variable Tromp curve model [14] for simulating closedcircuit ball milling For the sake of brevity, only key aspects of the model are described here The readers are referred to [5] for derivation of the cellbased PBM within TUSSIM [5]Modeling of closedcircuit ball milling of cement clinker via a 1972年6月1日 RECYCLING FLOW l%] ELEVATOR 100 ,I I AIR SLIDE FINlSHED 90 PROD SEPARATOR REJECTS 80 BALL MILL CLINKER FEED 70 Figure 1 Closed Circuit Ciment Mill 60 Broyeur en circuit fermEi 50 40 30 EXPERIMENTAL HIGH ORDER MODEL 20 LOW ORDER DISCRETE MODELe 85 90 95 100 CLINKER FEED [~] 007 Figure 2Control of a Closed Circuit Cement Mill ScienceDirect
.jpg)
Predictive Control of a Closed Grinding Circuit System in Cement
Predictive Control of a Closed Grinding Circuit System in Cement Industry Luis I Minchala1;3, Member, IEEE, Youmin Zhang2, Senior Member, IEEE, Luis E GarzaCastan˜on´ 3, Member, IEEE Abstract—This paper presents the development of a nonlinear model predictive controller (NMPC) applied to a closed grinding circuit system in the cement Download scientific diagram Closed circuit grinding system from publication: Optimizing the control system of cement milling: Process modeling and controller tuning based on loop shaping Closed circuit grinding system Download Scientific Ø The OPC equivalent fineness must be calculated for every cement type ground in the mill being studied Ø The ball charge will be chosen from table 1 or 2 (closed or open circuit mill) according to the smallest OPC equivalent fineness Everything you need to know about clinker/cement Every 100 cm²/g increase in cement fineness increases the mill power consumption by 12 kWh/t for a closed circuit mill 23 kWh/t for an open circuit mill, a sheer waste if this is not required by the market! Equipment design: Improvements in New Existing Cement Grinding
.jpg)
OpenCircuit Mill an overview ScienceDirect Topics
Overview of cement clinker grinding Vipin Kant Singh, in The Science and Technology of Cement and Other Hydraulic Binders, 2023 9713 Influence on grinding efficiency Some of the admixtures allow fineness to be increased in open circuit mills, whereas in closed circuit mills, considerable production increase can be achieved at the same fineness1927 First Loesche coal mill delivered for the Klingenberg power station in Berlin 1953 500th coal mill plant sold worldwide 1961 Introduction of hydraulic spring assembly system 1965 Construction of first pressure mill (LM 122 D) 1980 Delivery of first modular coal mill (LM 263 D) 1985 Delivery of first selfinerting coal grinding plant (LM 212 D) for the steel industry (PCI LOESCHEMILLSIMPROVED CEMENT QUALITY AND GRINDING EFFICIENCY BY MEANS OF CLOSED MILL CIRCUIT MODELING A Dissertation by GLEB GENNADIEVICH MEJEOUMOV Submitted to the Office of Graduate Studies of Texas AM University in partial fulfillment of the requirements for the degree of DOCTOR OF PHILOSOPHY December 2007 Major Subject: Civil EngineeringIMPROVED CEMENT QUALITY AND GRINDING EFFICIENCY BY MEANS OF CLOSED MILL Modeling And Simulation Of A Closed Loop Ball Mill Grinding Circuit Proceedings of IRF International Conference, Chennai, India, 20th April 2014, ISBN: 978938 10 II DYNAMICS OF THE BALL MILL GRINDING CIRCUIT product Blaine measured in cm²/g and the rejects Fig1 In a continuous ball mill grinding circuit, the ball millMODELING AND SIMULATION OF A CLOSED LOOP BALL MILL GRINDING CIRCUIT
.jpg)
Open and closed circuit dry grinding of cement mill rejects in a
2004年1月14日 Mill capacity and the stirring speeds were the investigated parameters for the open circuit tests, whereas closed circuit tests were carried out at a constant stirring speed but variable discharge rate Five speed levels used in the open circuit grinding tests are 200, 400, 600, 800 and 1000 rpm The capacities were determined to obtain product 2009年5月15日 Grinding of clinker is the last and most energyconsuming stage of the cement manufacturing process, drawing on average 40% of the total energy required to produce one ton of cement During this stage, the clinker particles are substantially reduced in size to generate a certain level of fineness as it has a direct influence on such performance characteristics of the Improved cement quality and grinding efficiency by means of closed mill 2015年1月7日 3 ~ Nael Shabana 20103~ 60 Ventilation 70 Grinding and Generation of Heat 71 Heat Generation in Tube Mills 72 Cooling Procedures During Finish Grinding 73 Heat Balance for Mill Cooling 80 Cement Mill Specific Power Consumption 81 Calculation of Cement Mill Power Consumption 82 Calculation of the Specific Consumption of Energy per Ton of Cement mill notebook PDF Free Download SlideShareWith builtin air separators these mills grind in closed circuit, almost always as dryinggrinding mills Roller mills are now operated with throughput capacities of more than 500 tons per hour of cement raw mix (Loeschemill, Polysius Roller mills INFINITY FOR CEMENT EQUIPMENT
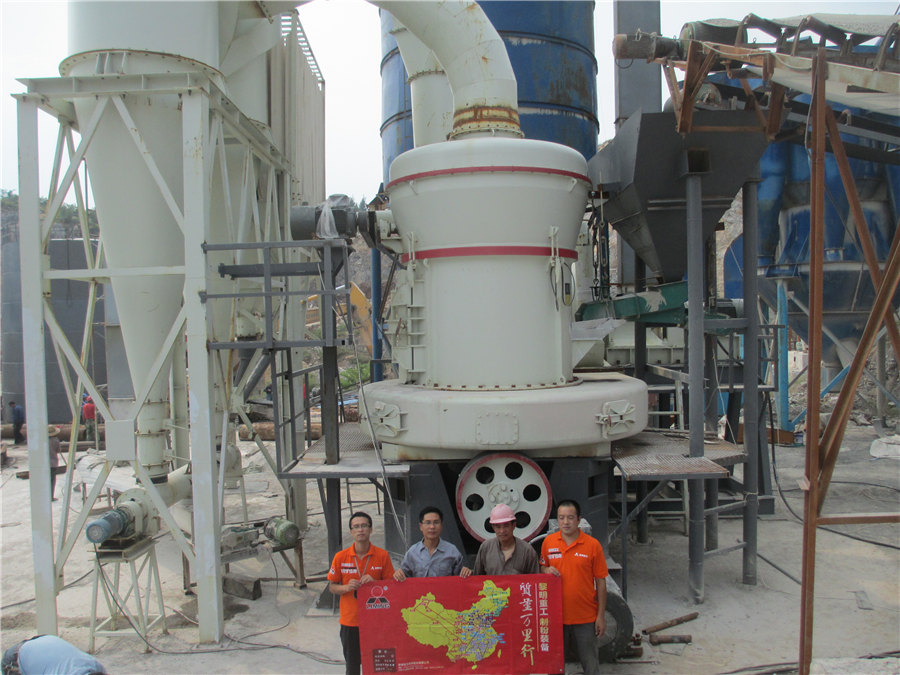
Cement Mill Dal Machinery
Mill Types Diameter x Length(m x m) Support Type Drive Type Motor Power(kW; UDCM 32130: Ø 3,2 x 13,0: Trunnion Bearing: Side Central: 1600: UDCM 38130: Ø 3,8 x 13,0The operational controls are also reviewed for optimized mill operation Every element of a closed circuit ball mill system is evaluated independently to assess its influence on the system Figure 1 below is a typical example of inefficient grinding indicated by analysis of the longitudinal samples taken after a crash stop of the millOPTIMIZATION OF CEMENT GRINDING OPERATION IN BALL MILLS2018年7月1日 Among the industries, the nonmetallic industry was reported as the third largest energy user and accounted for about 12% of the global energy use [1]Within this portion, cement industry had the majority of the utilization with 85–12% [1], [2]US Energy Information Administration (EIA) [7] named cement industry as the most energy intensive among the Energy and cement quality optimization of a cement grinding circuitChemical process industries are running under severe constraints, and it is essential to maintain the endproduct quality under disturbances Maintaining the product quality in the cement grinding process in the presence of clinker heterogeneity is a challenging task The model predictive controller (MPC) poses a viable solution to handle the variability This paper addresses the Predictive Controller Design for a Cement Ball Mill Grinding
.jpg)
Optimization of a fully airswept dry grinding cement raw meal
2015年4月1日 Request PDF Optimization of a fully airswept dry grinding cement raw meal ball mill closed circuit capacity with the aid of simulation Production capacity of a fully airswept industrial IMPROVED CEMENT QUALITY AND GRINDING EFFICIENCY BY MEANS OF CLOSED MILL CIRCUIT MODELING A Dissertation by GLEB GENNADIEVICH MEJEOUMOV Submitted to the Office of Graduate Studies of Texas AM University in partial fulfillment of the requirements for the degree of DOCTOR OF PHILOSOPHY December 2007 Major Subject: Civil EngineeringIMPROVED CEMENT QUALITY AND GRINDING EFFICIENCY BY MEANS OF CLOSED MILL 2020年3月1日 Eq (18), representing the scaleup effect on the degree of size reduction, is examined with the cement mill data for both open and closed circuitsIn Fig 6, the left side of Eq (18), the degree of size reduction, is plotted on the ordinate against the right side of Eq (18), the scaleup variables, on the abscissaOnly the reference particle size x r = 75 μm is examined in A scaleup and design basis of continuous tube mills in cement 1996年6月1日 There are a variety of control strategies that one may consider for cement mill circuit control and often several methods for implementing each strategy(PDF) An industrial application of multivariable linear quadratic
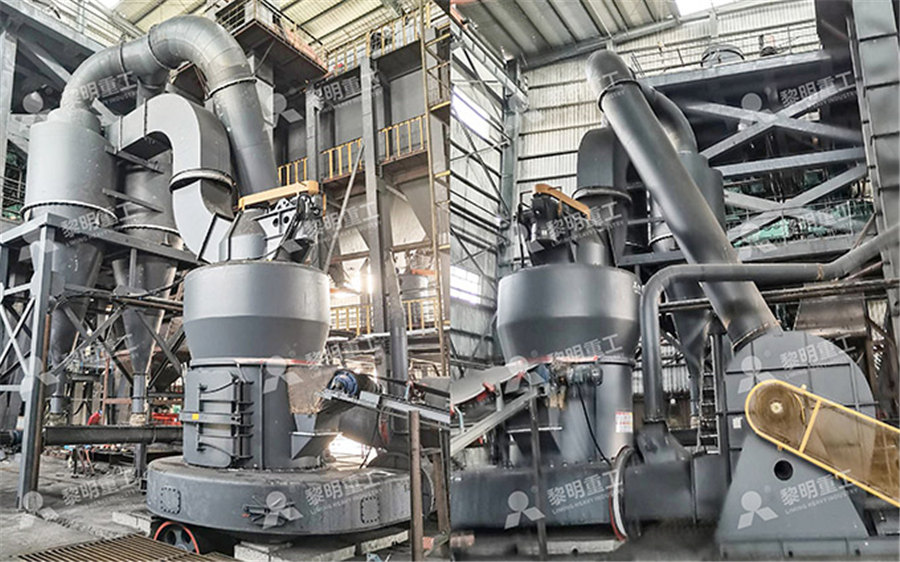
DESIGN AND ANALYSIS OF BALL MILL INLET CHUTE FOR ROLLER PRESS CIRCUIT
Additional tools required It will increase the plant off time Increasing Man hours and manpower Liner replacement, bolt tightening will be complicated 31 Inlet Chute Design Considerations The following parameters are considered while designing the mill inlet chute for powdery materials UMS ø46m Cement mill It is the mostly sold mill in FLS