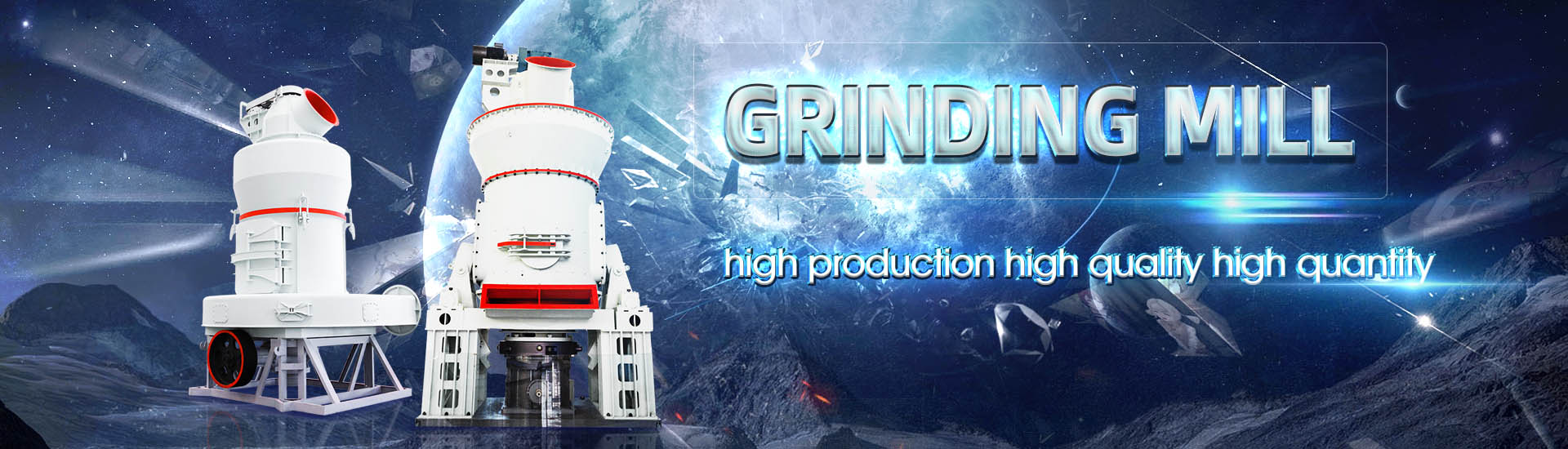
Grinding mill rotating structure
.jpg)
Grinding Mill an overview ScienceDirect Topics
According to the ways by which motion is imparted to the charge, grinding mills are generally classified into two types: tumbling mills and stirred mills In tumbling mills, the mill shell is rotated and motion is imparted to the charge via the mill shellGrinding mills are large rotating cylindrical steel vessels used to grind ore and minerals into finer particles The mills are important parts of the mineral enrichment process and the grinding is Structural Analysis and Condition Monitoring of Grinding Mills: A 2007年1月1日 They have different mechanical structures, which give different grinding performance, and are classified into some typical types such as highspeed rotating disk, Chapter 10 Selection of Fine Grinding Mills ScienceDirectGrinders, also called Hammermills, have a highspeed rotating assembly Grinders cut the materials that pass through a rotating assembly Intermeshing cutters are trapped and sheared Grinding Mill an overview ScienceDirect Topics
.jpg)
Roller Mill Springer
The basic structure of the roller mill includes the grinding roller, the grinding body, the force generation and transmission mechanism, airflow, and the device for easy replacement It can The paper outlines the advantages of shellmounted grinding mills over mills having a conventional trunnionsupported shell The growing use of larger mills in the past decade has The structural design of large grinding mills, with reference to shell There are two kinds of grinding body movements: either they describe an approximately parabolic trajectory, and knock against the material bed in a process known as cataracting; otherwise TUMBLING MILL MECHANICSVertical roller mill is a type of grinder used to grind materials into extremely fine powder for use in mineral dressing processes, paints, pyrotechnics, cements and ceramics It is an energy Vertical roller mill Wikipedia
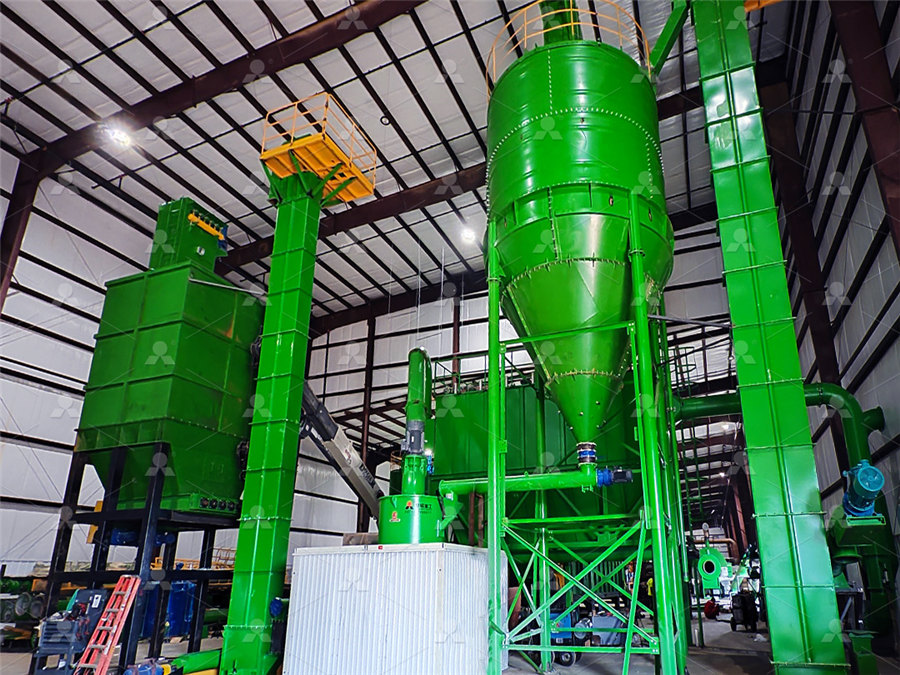
Drawing of the basic structure of a roller mill with two
Drawing of the basic structure of a roller mill with two rotating/counterrotating rollers (crosssection) The paper analyzes the interrelation of: motion, particle size of ground riceA crushing plant delivered ore to a wet grinding mill for further size reduction The size of crushed ore (F 80) was 40 mm and the SG 28 t/m 3 The work index of the ore was determined as 122 kWh/t A wet ball mill 1 m × 1 m was chosen to grind the ore down to 200 micronsGrinding Mill an overview ScienceDirect TopicsIt is evident that the shellsupported mill requires less space than does the conventional mill, and the distance between the bearing reactions is less than that of a conventional mill with the same working length Thus, the bending moment and rotating bending stresses are less for the shellsupported mill of identical shell thicknessThe structural design of large grinding mills, with reference to 2018年8月17日 Wet grinding is generally preferred because of lower power consumption and higher mill capacity Dry grinding must be used where wet grinding is feared to change the physical or chemical structure Grinding Mills — Types, Working Principle
.jpg)
Roller Mill SpringerLink
2023年7月4日 The basic structure of the roller mill includes the grinding roller, the grinding body, the force generation and transmission mechanism, airflow, and the device for easy replacement It can be divided into vertical roller mill, horizontal cylinder roller mill, high pressure roller mill, Raymond mill, and column millThe paper analyzes the interrelation of: motion, particle size of ground rice grains, displacement, and grinding in a roller–plate mill The purpose of the study was to analyze and evaluate Drawing of the basic structure of a roller mill with two rotating The rotary ball mill is a kind of traditional ball mill machineDifferent from the vertical ball mill, it adopts a horizontal barrel type rotating structureThere are two types of rotary ball mill, dry type and wet type, which can be chosen by users according to their actual situationRotary Ball Mill for High Uniformity Grinding of Metallurgy, Glass The components of a SAG mill include a rotating drum filled with steel balls or rods, a stationary structure that houses the motor, gear, reducer, and bearings, and a mill shell lined with steel or rubber plates to protect it from wear caused by the impact of the rock and grinding mediaA Comprehensive Guide to SAG Mill Operation ball mills supplier
.jpg)
Premier™ Horizontal Grinding Mills Metso
A Metso Premier™ horizontal grinding mill is able to meet any projects needs, even if it means creating something novel and unseen before Availability: Maximize availability with our stateoftheart Polymer HSB system and rotating structure design; Downtime: Abstract: The dynamic analysis of grinding mill foundation is a typical problem of soilstructure interaction The substructure method is used to carry out the dynamic analysis and design in DYNAMIC DESIGN FOR GRINDING MILL FOUNDATIONS2023年6月7日 Autogenous mill is a type of grinding equipment that crushes material by mutual impact, grinding and peeling effect among material grains The ore moves along the rotating cylinder and moves up quickly, Wet autogenous mill is also called cascading autogenous mill Its structure is shown in Fig 3Autogenous Mill SpringerLink2023年11月24日 The ball mill is a rotating cylindrical vessel with grinding media inside, which is responsible for breaking the ore particles and the heat treatment processes to determine the effect on the microstructure of the grinding media However, Grinding Media in Ball Mills for Mineral Processing
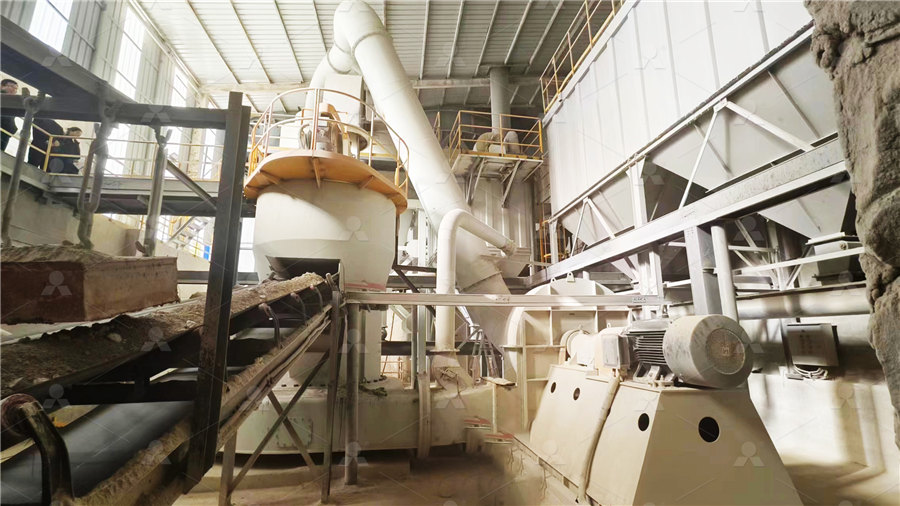
Stirred Mill SpringerLink
2024年1月1日 Stirred mill uses a stirring device to drive the grinding medium to move, generating grinding, shocking, and shearing effect on grinding materials In 1928, American A Szegvari made simple equipment with a handful of pebbles, a metal gasoline drum, and a small drill press, which was used for stirring sulfur to the desired dispersion, and it was the first Grinding Mills: Ball Mill Rod Mill Design PartsCommon types of grinding mills include Ball Mills and Rod Mills This includes all rotating mills with heavy grinding media loads This article focuses on ball and rod mills excluding SAG and AG Grinding Mills 911Metallurgist2024年1月12日 How Overflow Type Ball Mill Works Material Feed: The raw material is fed into the mill at one end and travels through the mill by rotation The feed enters the mill at a specific rate, ensuring a controlled grinding process; Grinding Process: As the mill rotates, the grinding media crushes and grinds the material into a fine powder The wet conditions enhance the Wet Overflow Type Ball Mill and ApplicationsIndustrial vertical grinding mill is an ideal largescale grinding equipment, integrating crushing, drying, Structure of Industrial Vertical Grinding Mill 1 Grinding disc: including guide ring, wind ring, Dynamic powder classifier This is a highspeed rotating cage When dusty gas passes through the cage, Industrial Vertical Grinding Mill
.jpg)
FLS High Pressure Grinding Rolls – Efficient grinding
It weakens rock structure and exposes ore particles, The rotating sideplates improve the material feed into the rolls By eliminating the socalled “edge effect”, or as pebble crushers in semiautogenous grinding (SAG)–ball mill circuits2015年6月1日 In the 1970’s and early 1980’s mills experienced “overall” structural failures Over time, analysis and design methods have improved, and the vast majority of failures we see today are “local” failures on the mill structure These are often caused by stress concentrations of the geometry, such as atTypes of Grinding Mill Structural Failures Vytas LLC2013年12月23日 The two main character of an Autogenous Mill eg size reduction which occurs through the detachment of material from the surface of larger particles (referred to as 'abrasion') and the grinding Design of a typical Autogenous Mill: PartII ResearchGateThe cylinder has a length and a diameter, which determines the capacity of the ball mill The inner surface of the cylinder is usually lined with wearresistant materials such as rubber, ceramic, or metal to extend the lifespan of the mill 2 Balls: Balls are the grinding media used in a ball millThe structure and construction of a ball mill
.jpg)
A New Conical Stone Soybean Milk Machine with Double Thread Grinding
The outer stone mill rotates with side type motor Structures are shown in Figure5(A) The whole set of structure is placed in a sealed enclosure, shown in Fig5(B) Pour beans and water from the funnel Soymilk flow out from the bottom left A B Figure 5 Conical stone mill structure (The outer (2) and inner (3) stone mill on the chassis (1)This mill is designed with a modular impeller that has removable discs and spacers Slurry enters at the bottom, travels upward through the mill chamber, and overflows through a media retention screen at the top The rotating polyurethane discs activate inert ceramic grinding media inside the milling chamberFlexible, efficient grinding systems – FLS2024年1月1日 The basic structure of the roller mill includes the grinding roller, the grinding body, the force generation and transmission mechanism, airflow, and the device for easy replacement It can be divided into vertical roller mill, horizontal cylinder roller mill, high pressure roller mill, Raymond mill, and column millRoller Mill SpringerLink2023年10月27日 The ball mill is a rotating cylindrical vessel with grinding media inside, which is responsible for breaking the ore particles Grinding media play an important role in the comminution of mineral A Review of the Grinding Media in Ball Mills for
.jpg)
Cement Grinding myPolysiusService
3 Cement Production Technology –Cement Grinding –Mechanical Design and Function of Separator Contents Topic 1 Separators –General Topic 2 Separators –Structure Topic 3 Separators –Mode of Functioning Topic 4 Separators –Installation Examples Topic 5 Separators –Assembly Topic 6 Separators –Maintenance and Wear ProtectionThe first example of using an agitated vessel and grinding media for comminution was in 1922 when Szegvari stirred a gallon can full of pebbles to rapidly disperse a sulphur suspension [19]This was developed into the first ‘stirred ball mill’ by Klein and Szegvari in 1928 [20]This prototype was refined into the Attritor mill, a low tip speed (3–5 m/s [21]) vertical pin mill which Semi Autogenous Grinding Mill ScienceDirect TopicsStructure and Principle HCH ultrafine grinding mill consists of main mill, classifier, high pressure fan, cyclone collector, pipes, electromagnetic vibrating feeder, electrical distribution cabinet and etc The large pieces of materials are crushed into small particles by the crusher and then sent to the storage bin by the elevator, and then sent to the tray on the turntable through the Best HCH Ultrafine Grinding Mill Manufacturer and Factory2015年1月1日 Table 2 Fourth level classification of grinding with rotating tools according to DIN 858911 Figure 2 takes into account that especially the surfaces to be manufactured strongly define the structure and axes configuration of grinding machines and thus can directly be used as classification scheme end mill on one machineGrinding Machines SpringerLink
.jpg)
Literature Review: Gearless Motor Failures – A Mill Designer’s
2014年9月10日 The rotating element (the shell, heads and trunnions) of a mill is a slowly rotating tube Its structural design is often analysed using a simple, linear, twodimensional finite element model and there is no need to undertake a dynamic analysis of the mill structureATTRITOR BALL MILL STRUCTURE The attritor ball mill is mainly composed of a grinding cylinder, agitator, lining plate, grinding media, driving system, The motor and reducer drive the agitator in the grinding cylinder rotating rapidly Multi metal rods are vertically and spirally arranged on the agitatorAttritor Ball Mill Wet Dry Grinding Stirred Ball Mill AGICO Ball MillFor a mill speed of 90%, the lowest specific power consumption occurs with the new lifters As the lifter wears, the power increases with the peak occurring for a face angle of 458 The mill performance then drops off as the lifter wears further The change in power consumption between the best and worst lifter shapes is now 84%Charge behaviour and power consumption in ball mills: sensitivity 2020年3月15日 In the present study, the fluid structure interaction (FSI) between slurry and mill structure and between slurry and grinding media is modelled using a partitioned (or staggered) approach In a partitioned approach, the fluid and solid equations are uncoupled, allowing the use of different computational codes for the fluid and the solid domains, respectivelyA novel approach for modelling of physical interactions between
.jpg)
Grinding in Ball Mills: Modeling and Process Control
2012年6月1日 A typical structure of a closedloop circuit for wet grinding consists of a ball mill, sump and classifier [10, 13, 33, 39] and it is schematically shown in Fig 4Material grinding process motor through reducer rotating drive disc, the material falls from the mill under the central entrance and exit, under the action of centrifugal force to the disc edge by the roller to move and the crushing, grinding out lap after the material was speed up the flow to and vertical mill with one of the separator, after the meal by the separator back to the mill, the re Vertical roller mill WikipediaThe mill itself consists of a rotating disk with 4 grinding pins at its periphery and an impeller wheel classifier integrated into the top section of the mill chamber The diameter of the grinding disk is 200 mm and the one of the classifier is 100 mm Both parts rotate with a variable speed of up to 11,000 rpm After the particles are fed to (PDF) Grinding in an air classifier mill AcademiaRing Motor drive a grinding mill without contact between rotating and fixed parts This concept avoids girth gear and pinions, which are used for conventional mill drives The stator of the Ring Motor is wrapped around the mill as a ring Due to the large size, the stator is fabricated and transported in segments At site, the stator segments areDesign and dynamic behavior of large Ring Motors for grinding
.jpg)
An investigation of performance characteristics and energetic
2020年8月12日 As one of the three major forces of coal mills, the grinding force exerts a significant impact on the working process of coal mills and parameters like mill current and outlet temperatureEffect of Grinding Media Density on Mill Perfomance In order to increase the efficiency of the grinding mill, Stoimenov et al [82] suggested that the grinding media density should be increased The author discovered that lowdensity balls are less efficient than highdensity balls when grinding material is subjected to the ultrasonic milling methodGrinding Media in Ball MillsA Review AcademiaThe mill proposals include the rotating mill structure, startup set of lining, and induction drivetrain Select™ horizontal grinding mill proposals also offer additional components and special tools, including feed chutes or spouts, discharge trommels, jacking cradles, hydraulic jacking systems, hydraulic torque wrenches, and UT bolt tension measuring systems to name just a fewSelect™ Horizontal Grinding Mills MetsoA bead mill is a type of equipment used for ultrafine grinding and dispersing of particles It operates on the principle of impact and attrition: grinding media (beads) made of glass, ceramic, or steel are agitated inside a vessel or a chamber by a rotating shaft with impellers, causing the particles to break into smaller sizes due to collision and shear forcesBead Mills for ultrafine grinding RETSCH
.jpg)
The Working Principle and Structure of Rod Mill
2019年10月17日 In this post, we're going to learn more about rod mill We'll cover it from two aspects: 1 Working principle 2 Structure Let's dive right in! 1 Working Principle of Rod Mill Rod mill is a common equipment for grinding operation in mineral concentrator, which is mainly suitable for rough grinding operation