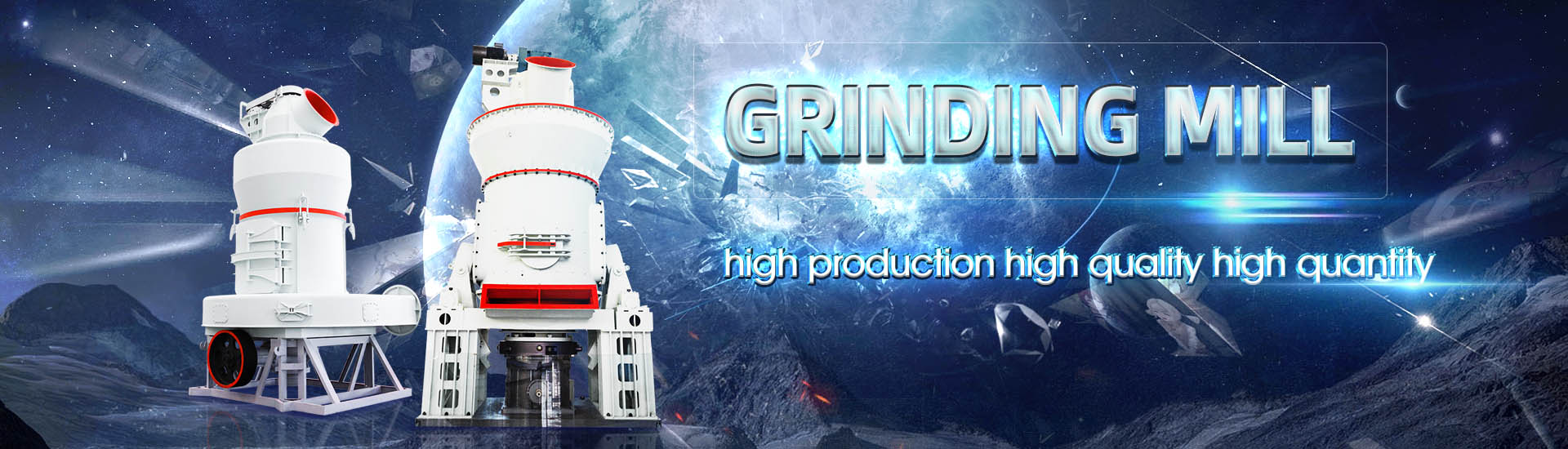
Raw material vertical mill grinding fineness increased from 2O to 22
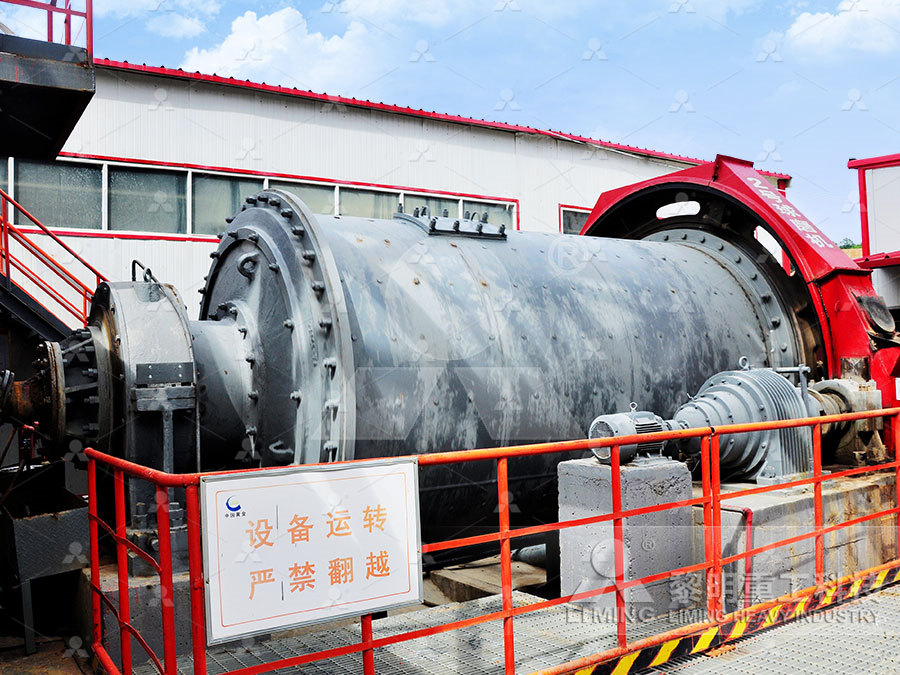
Vertical roller mill for raw Application p rocess materials
Vertical roller mills are adopted in 20 cement plants (44 mills) in Japan In the vertical roller mill which is widely used in the raw material grinding process, raw materials input grinding table Vertical roller mills, (VRM), are widely used for grinding raw materials in factories engaged in the extraction and processing of minerals Any machine used for grinding or crushing consumes Parámetros para el Proceso de Molienda en Molinos Verticales After the cement raw material is crushed, it will be sent into the raw mill for further grinding until a certain degree of fineness is reached, and then enter the clinker calcination process From the production experience of many cement plants, Raw Mill – Raw Mill In Cement Plant AGICO Cement 2023年3月1日 On the other hand, no fineness soft sensing study in grinding circuits considers material analysis in the mill feed, therefore, a particular attention will be addressed to the right choice of parameters that impact raw meal fineness, including material quality characteristics, to build an accurate and reliable longterm modelEfficient machine learning model to predict fineness, in a vertical raw
.jpg)
Modeling Based on the Extreme Learning Machine for Raw Cement Mill
2015年1月1日 Vertical grinding mill is the main grinding equipment for the newtype dry cement raw meal production, raw material grinding process in cement industries accounts for approximately 50#8211;60#160;% of the total energy consumption The dynamic characteristics of the2022年10月3日 Vertical Raw Mill is a main equipment that is used in grinding or refining raw materials at PT Semen Baturaja (Persero) Tbk using a tire roller that can produce raw meal with the standard (PDF) ANALISA KINERJA ALAT VERTICAL RAW MILL PABRIK II PT 2016年6月1日 Raw meal fineness is the percentage content of 80 µm sieving residue after the cement raw material is ground The accurate prediction of raw meal fineness in the vertical mill system is very Modelling of the vertical raw cement mill grinding process 7 // Almost any plant for the grinding of cement raw material is a combination of machines specially adapted to the particular physical properties of the material to be ground As a result, our plants work efficiently without any trouble » Highly efficient grinding, drying, and separating in one unit » Outstanding production capacities exceeding 1,400 t/h in one single millPFEIFFER MILLS FOR THE CEMENT INDUSTRY
.jpg)
Operational parameters affecting the vertical roller mill
Request PDF On Sep 1, 2016, Deniz Altun and others published Operational parameters affecting the vertical roller mill performance Find, read and cite all the research you need on ResearchGate7 // Almost any plant for the grinding of cement raw material is a combination of machines specially adapted to the particular physical properties of the material to be ground As a result, our plants work efficiently without any trouble » Highly efficient grinding, drying, and separating in one unit » Outstanding production capacities exceeding 1,400 t/h in one single millPFEIFFER MILLS FOR THE CEMENT INDUSTRYVertical raw mill is important equipment widely used in the cement raw meal (cement raw materials) grinding section of the cement production process in cement plantBecause the vertical raw mill is the use of roller grinding principle to crush materials, its vertical raw mill operation is more efficient and energysaving, product output is more stable, so in cement industry, electric Vertical Raw Mill for Cement Raw Meal Grinding in Cement Raw mill is generally called cement raw mill, raw mill in cement plant, it refers to a common type of cement equipment in the cement plantIn the cement manufacturing process, raw mill in cement plant grind cement raw materials into the raw mix, and the raw mix is sent to the cement kiln to make cement clinker, next, clinker and other admixtures will be ground into finished cement by Raw mill Cement Plant
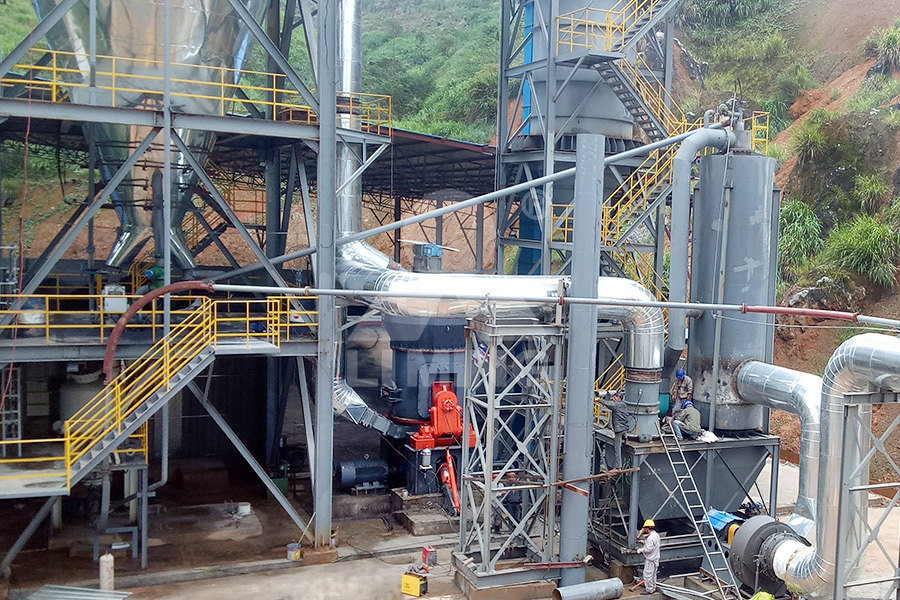
Operational experience from the United States' first vertical roller
OK Roller Mill for Cement GrindingExperience from Operation of Titan Cement's OK274 Mill Increasing Cement Roller Grinding Capacity with vertical Roller Mill Technology Jan 2002 Benetatou2020年10月24日 Raw meal fineness is the percentage content of 80 µm sieving residue after the cement raw material is ground The accurate prediction of raw meal fineness in the vertical mill system is very Prediction of raw meal fineness in the grinding process of cement raw meal that has an arrangement of six rollers on the grinding table This mill, designated the LM 606 has a grinding table with a diameter of 600 m and an installed drive rating of 4 650 kW Even with poor grindability of the raw material this mill is expected to produce an output of 640 t/h at a raw meal fineness corresponding to a residue of Redundancy and interchangeability – large vertical roller mills 2020年10月24日 A twodimensional convolutional neural network method is proposed that is used to predict raw meal fineness during the grinding process of raw material and is proved to be very effective by comparing with the stateoftheart methods Raw meal fineness is the percentage content of 80 µm sieving residue after the cement raw material is ground The Prediction of raw meal fineness in the grinding process of cement raw
.jpg)
Vertical Grinding Mill: How it Works, Application And Advantages
Read this indepth blog to learn about the working principle of Vertical Grinding Mill, its application, and its advantages +91 226796 9655 The grounded raw material is then carried through the air from the blower into the Analyzer Machine for screening Higher the RPM, higher the fineness and lower the productionA vertical roller mill, also known as a vertical grinding mill or vertical mill, is a comprehensive grinding equipment integrating crushing, drying, grinding, grading, and conveying Vertical grinding mills can be widely used in electric power, metallurgy, construction, chemical industry, and other industries to make powder, especially for materials such as cement clinker, coal Energysaving and Efficient Vertical Roller Mill Fote Machinery2021年1月1日 Stacking Reclaiming of Raw material: Swing type stacker Reclaimer: Limestone other raw material are stored in open area into a longitudinal storage unit called stockpile through Stacker These are then extracted transversely from the stockpile through reclaimer: 3: Raw Meal Grinding Homogenization: Grinding Mill Vertical Roller Mill Review on vertical roller mill in cement industry its High quality Gold Mines Vertical Grinding Mill For Raw Material Low Wear Fineness Adjustable from China, Gold Mines Vertical Grinding Mill For Raw Material Low Wear Fineness Adjustable vertical roller mill 1400/22: NBY800/YNS62090: 56/90: Ф38x75: 90 : 17: 103: 1600: JDX900? Ф46x10+35: 190 : 15: 278:Gold Mines Vertical Grinding Mill For Raw Material Low Wear Fineness
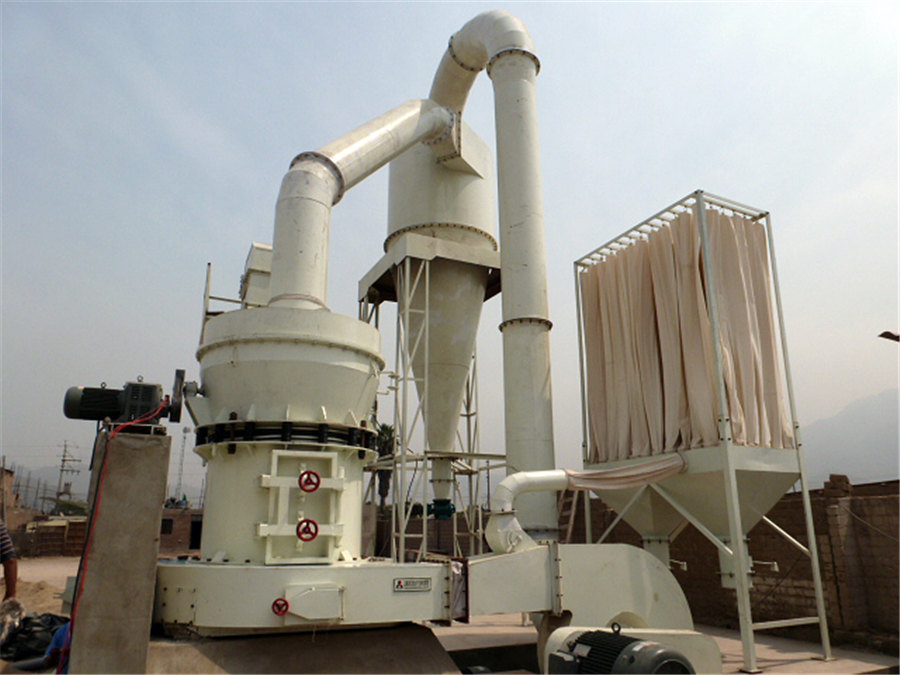
BALL MILLS Ball mill optimisation Holzinger Consulting
common solution to grind raw materials and cement Roller presses are used mainly in combination with a ball mill for cement grinding applications and as finished product grinding units, as well as raw ingredient grinding equipment in mineral applications This paper will focus on the ball mill grinding process, its tools and optimisation2024年9月1日 Fine grinding is a milling method of crushing materials to less than −01 + 001 mm by using grinding, impacting, shearing and other forces within the mill (Kumar et al, 2023)The purpose of grinding is not only to provide a suitable feed size for further processing but also to release valuable minerals from the gangue, which is tightly combined in the oreEffect of different mills on the fine grinding characteristics and In addition, the raw material grinding process will be supported by a QMR² 48/24 For the 4,000 tons per day kiln line Shiva Cement Ltd contracted a quadropol® vertical roller mill for grinding pet coke with a QMK² 32/16 The same mill size quadropol® Vertical Roller Mill myPolysiusServiceFor drying the wet raw material it is necessary that prior to the mill start up the grinding plant isheated for some timeOtherwise the cold grinding plant would take away too much heat from the drying process and the finish product would PROCESS TRAINING for operators of Vertical RAW Mills
.jpg)
Optimizing Raw Mills Performance ; the Materials
2019年6月22日 Specific power consumption of a raw mill is primarily dependent upon raw materials hardness and harder the material more will be the power required to grind the material to the desired fineness For the cement industry the ball mill was really an epochmaking breakthrough as for almost 80 years it was the predominant mill for grinding of raw materials and coal, and still today is the most used mill for cement grinding Over the last three decades the vertical roller mill has become the preferred mill for grinding of raw materialsCement grinding Vertical roller mills VS ball mills2022年2月28日 Comparing dry and wet grinding curves in a ball mill in the same condition (an equal amount of materials and grinding media has been used on each pair of wetdry experiments) (Fig 17) indicated two significant differences at higher power values of wet grinding, specifically when speed exceeded 06 critical speed and for higher ω Pmax in the Grinding SpringerLinkIf the fineness exceeds the fine rules, the mill output will decrease and the power cent result of the raw material fineness per hour according to the laboratory The speed of the separator is such that the fineness is controlled within the range of R 008≤14~16%How to Improve Grinding Efficiency of Vertical Roller Mill
.jpg)
Effects of Mill Speed and Air Classifier Speed on Performance of
2021年6月29日 Nowadays, ball mills are widely used in cement plants to grind clinker and gypsum to produce cement The research focuses on the mill speed as well as air classifier speed effect on the two 2016年11月8日 The grinding process of vertical mill raw meal in cement industry features nonlinear, strong coupling and long timedelay, which is difficult to model precisely and implement stable control for Adaptive dynamic programming in raw meal fineness control of vertical SINOMALY produces cement raw material grinding mills in various specifications These machines are suitable for grinding mill production lines with an output of 2500t/d, 3200t/d, 4000t/d, 5000t/d, 6000t/d and 8000t/d The vertical grinding mill is utilized for the grinding of raw materials, mixed cement, and slag powderVertical Roller Mill for Cement Raw Material SINOMALYThe document discusses optimization and operation of vertical roller mills (VRMs) Key points include: 1) Continuously monitor and adjust process parameters to find the optimum operating conditions of highest capacity and lowest power consumption 2) Relevant process parameters to monitor include product rate, fineness, classifier speed, grinding force, power consumption, air Optimization of Vertical Raw Mill Operation PDF
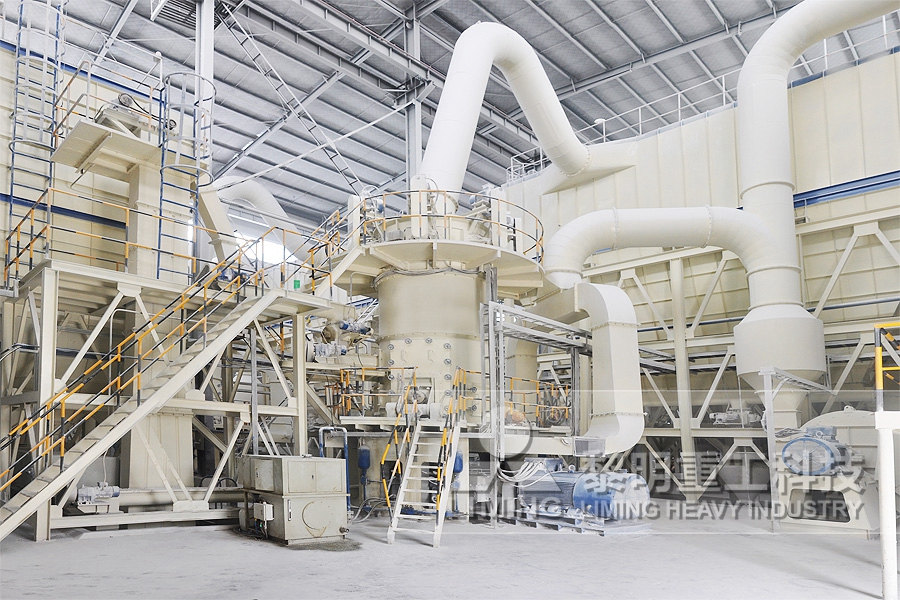
Operating experience with a vertical roller mill for
2012年3月1日 Vertical roller mills are the mills traditionally used for processing granulated blastfurnace slag and for grinding composite cements From the energy aspect they are superior to grinding plant Vertical Raw Mill: A vertical raw mill is mainly used in cement plants for raw material grinding Simple process flow, providing for drying, grinding and classifying all in one equipment; Minimum floor space requirement, compact layout and low investment in civil works; High grinding efficiency, low energy consumption and low wear on metal partsVertical Roller Mills LNV TECHNOLOGY2017年4月1日 Vertical roller mills (VRM) have found applications mostly in cement grinding operations where they were used in raw meal and finish grinding stages and in power plants for coal grinding The mill combines crushing, grinding, classification and if necessary drying operations in one unit and enables to decrease number of equipment in grinding circuitsOperational parameters affecting the vertical roller mill 2021年1月22日 In the whole process of cement production, the electricity consumption of a raw material mill accounts for about 24% of the total Based on the statistics of the electricity consumption of the raw A Survey and Analysis on Electricity Consumption of Raw Material Mill
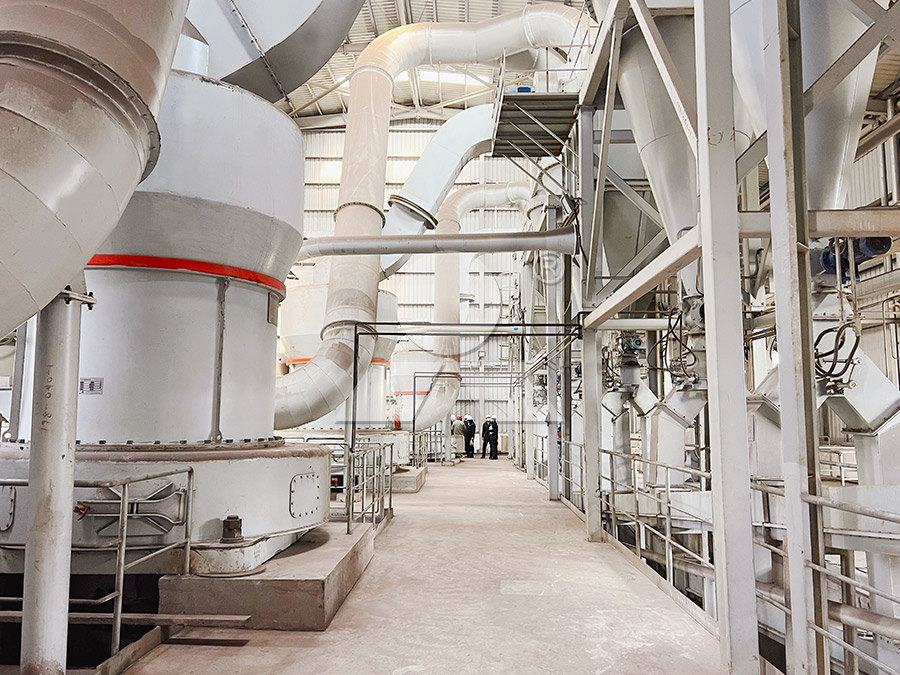
(PDF) Case studies and operational results of modern MVR vertical
2017年1月1日 For decades vertical roller mills have been in use in the cement industry for the grinding of cement raw material and coal Since the 1980's this mill type has also been used for combined or 2023年11月1日 Grinding operation is the last preparation stage before beneficiation In this stage, the material undergoes the combined action of impact and grinding, so that the ore particle size is diminished and the qualified materials is provided for succeeding beneficiation operations [1, 2]Generally, the quality of the grinding product is also an important factor to determine the Energy conservation and consumption reduction in grinding 2022年1月23日 This work concentrates on the energy consumption and grinding energy efficiency of a laboratory vertical roller mill (VRM) under various operating parametersAnalysis and Optimization of Grinding Performance of Vertical 2020年10月24日 The accurate prediction of raw meal fineness in the vertical mill system is very helpful for the operator to control the vertical mill However, due to the complexity of the industrial environment, the process variables have coupling, timevarying delay and nonlinear characteristics in the grinding process of cement raw materialPrediction of raw meal fineness in the grinding process of cement raw
.jpg)
Efficient machine learning model to predict fineness, in a vertical raw
2022年12月1日 Soft sensor enables computing parameters that can be physically impossible to measure This work aims to develop a soft sensor for raw meal fineness in a vertical roller mill of a cement plantraw material grinding, a modular vertical roller mill with 5 m table diameter and 4 rollers was added The existing kiln systems were partly modernized, one kiln system was replaced by new system Grinding Process Optimization Featuring Case Studies and